- ленточный и дисковый, схемы, изготовление, компоненты
- Гриндер своими руками: нюансы изготовления
- Общий | Сверлильный станок своими руками | Практик-механик
- 10 способов использования аккумуляторной дрели-шуруповерта
ленточный и дисковый, схемы, изготовление, компоненты
Наверняка, если вы увлекаетесь шлифовальными и другими подобными работами, уже слышали про такие полезные вещи, как ленточная шлифовальная машина, орбитальная, шлифовальная вибромашина и так далее. Но вполне возможно, что вам не встречалась такое приспособление , как роторная шлифовальная машина. Ее отличием считается то, что тут шлифовальным элементом являет не ремень и не диск, это вал! Такая машина отличается простотой, а ее эффективность можно вполне сопоставить с ленточным шлифовальным станком, если вам, конечно, не нужна в совершенстве идеальная плоскость. Впрочем, точность тут не проблема, все зависит от качества сборки.
Суть машины следующая, она состоит из вала, на котором закреплена наждачная бумага. Шлифовальный ротор, назовем его так, приводится в действие дрелью. Напротив ротора находится рабочая плоскость, она регулируется по высоте. Работает все очень просто, берем брусок или доску, которую нужно отшлифовать, и регулируем рабочий столик по высоте так, чтобы доска не заходила между ротором и столиком с зазором в пару миллиметров.

При желании вы удобно можете обрабатывать любые по ширине плоскости (учитывая максимальную ширину станка), вы запросто можете обрабатывать торцы материала. Рассмотрим подробнее, как же сделать это чудо техники.
Материалы и инструменты, которые использовал
Список материалов:
— наждачная бумага;
— фанера;
— дрель;
— длинный резьбовой стержень;
— два подшипника;
— гайки, барашки, шайбы и другие мелочи;
— два длинных винта с гайками и шайбами;
— саморезы;
— дверные петли;
— клей по дереву, эпоксидный клей, суперклей.
Список инструментов:
—
—
—
— электролобзик;
— гаечные ключи;
— зажимы.
Процесс изготовления станка:
Шаг первый. Изготовление рабочей плоскости
Основным элементом станка можно считать рабочую плоскость, именно благодаря ней можно регулировать расстояние до шлифовального вала. Рабочая плоскость должна иметь возможность подниматься и опускаться. Сделать ее очень просто. Берем лист фанеры и вырезаем из него основание, к основанию крепим два прямоугольника из фанеры. Садим их на клей по дереву, а с другой стороны дополнительно заворачиваем саморезы.
Теперь будет нужен еще один кусок фанеры, это будет непосредственно рабочая плоскость. Берем дверные петли и прикручиваем ее на них. В итоге плоскость сможет подниматься и опускаться.
Шаг второй. Установка крепежных винтов
По бокам рабочей плоскости установлены два винта, они предназначены для фиксирования стола на нужной высоте. Под них нужно просверлить отверстия между двумя половинками фанеры, более подробно о чем я, смотрите на фото. Потом открутите планку фанеры, между которой сверлились отверстия и положите в канавку болт. Легкими ударами молотка утопите шляпку до половины диаметра в фанеру, аналогично нужно сделать и на другой стороне. В итоге у вас получатся отличные пазы для шляпок винтов.
Шаг третий. Установка боковых стенок
Боковые стенки автор также делает из фанеры. Они двойные, самая широкая стенка предназначена для поддерживания рабочей плоскости, а узкая нужна для надежного крепления шлифовального ротора.
В широкую боковую стенку должны заходить стержни винтов, которые устанавливаются в рабочем столе. Берем карандаш и рисуем линию, по которой эти винты будут двигаться при поднятии и опускании столика. Сверлим в начале и конце линий отверстия, а затем вырезаем пазы при помощи электролобзика.
Установите винты на свои места в рабочем столе, желательно фанеру склеить и потом скрутить саморезами. Теперь установите боковые стенки, а с другой стороны на винты установите шайбы и гайки барашки. С помощью этих гаек вы сможете быстро фиксировать рабочую плоскость в нужном положении.
Шаг четвертый. Прикручиваем основу
Чтобы скрепить всю конструкцию, вам понадобится лист фанеры, из которого изготавливается основа. Первым делом приклейте к боковым стенкам короткие стенки, предназначенные для установки подшипников.
Шаг пятый. Устанавливаем подшипники для оси ротора
Настало время установить подшипники. Для них нужно рассверлить посадочные места, в этом деле вам поможет дрель с соответствующей битой. Потом просверлите отверстия для оси ротора, которой выступает длинный болт или резьбовой стержень.
Шаг шестой. Изготовление и установка шлифовального ротора
Установите подшипники на свои места, не забыв хорошо смазать, а также подготовьте гайки с шайбами. Ротор изготавливается из кругляков фанеры, которые вырезаются на сверлильном станке. Разводим эпоксидную смолу и поочередно надеваем кругляки на ось, между каждой деталью наносим эпоксидный клей! Когда соберете всю эту гирлянду, хорошенько ее сожмите и дайте клею полностью высохнуть.
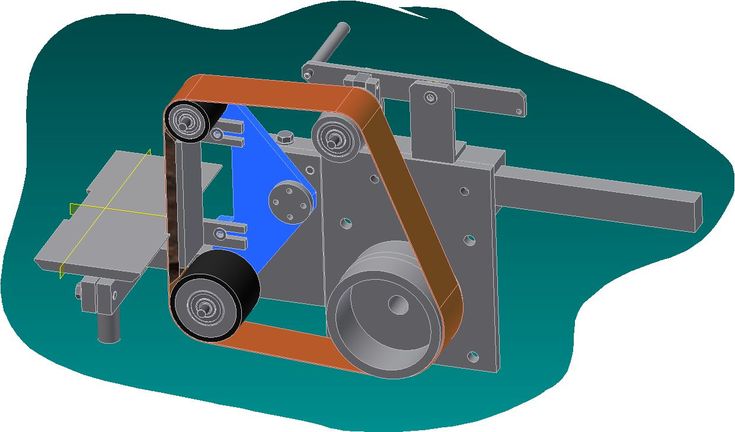
Когда клей высохнет, зафиксируйте и отрегулируйте шлифовальный ротор. Это делается с помощью гаек. Закрутите их так, чтобы люфт вала был минимальным, но подшипники не должны быть перетянутыми! Зафиксируйте гайки с помощью суперклея, или просто ставьте по две гайки.
Шаг седьмой. Устанавливаем дрель
Для установки дрели понадобится изготовить небольшой «столик» с кронштейном. Этот столик делается из фанеры. Закрепите патрон дрели на валу и вырежьте детали по высоте. Скрутите «столик», используя саморезы.
Теперь можно изготовить крепежный кронштейн, для этого понадобится фанера или деревянный брус. Делаем необходимые замеры и распиливаем фанеру вдоль на две части. Далее между двумя половинками положите не толстую планку и просверлите на сверлильном станке отверстие такого диаметра, чтобы в него могла потом зайти носовая часть дрели.
Вот и все, кронштейн почти готов.

Электрическая дрель – это универсальный инструмент. Помимо использования по прямому назначению (сверлению отверстий), ее можно задействовать для множества видов работ. Ведь патрон дрели позволяет зажимать не только сверла, но и фрезы, шлифовальные элементы и даже деревянные заготовки для токарной обработки. Поэтому из этого инструмента можно сделать несколько видов полноценных домашних станков для обработки и изготовления различных материалов и деталей.
Особенности применения станков
Работа дрелью на весу при удержании инструмента только руками существенно ограничивает ее возможности. Вес инструмента и вибрация не позволяют жестко зафиксировать дрель в нужном положении. Но если продумать и сконструировать специальную станину, где она будет устойчиво крепиться, то обыкновенная ручная дрель превратится в профессиональное, почти промышленное оборудование.
Из дрели можно самостоятельно сделать такие виды станков:
- сверлильный;
- токарный;
- фрезерный;
- шлифовальный.
Причем после замены рабочего или режущего элемента станки становятся взаимозаменяемыми. Предусматривают функцию два в одном, например, сверлильный и фрезерный станок, токарный и шлифовальный. Все зависит от условий монтажа и потребностей владельца.
Мощность станков и их возможности будут зависеть от вида дрели (мощности ее электродвигателя), способу крепления, так как именно она в этом случае выступает главной рабочей частью оборудования.
Виды станков
Несмотря на самодельную сборку, каждый станок позволяет изготавливать широкий спектр деталей различной сложности и конфигурации. При правильном монтаже агрегата, он практически не будет уступать профессиональным заводским аналогам по точности и скорости работы.
Если же задействовать и дрель высокой мощности, рассчитанную на длительную бесперебойную эксплуатацию, то на таком станке возможно наладить и серийное производство или обработку разнообразных элементов.
В домашних условиях такие станки способны полностью удовлетворить бытовые нужды по ремонту мебели, автомобиля, велосипеда и многих других вещей повседневного обихода. Они помогут реализовать множество дизайнерских решений без необходимости обращаться в профильные мастерские.
Каждый вид станка предусматривает выполнение разных работ и имеет свои особенности.
Сверлильный
Сверлильный станок необходим для формирования отверстий в различных поверхностях – как плоских, так и многогранных элементах из дерева, металла, пластика, стекла. Диаметр отверстия и материал детали определяется типом используемого режущего элемента – сверла.
Принцип работы агрегата основан на том, что механизм, обеспечивающий крутящий момент режущего элемента (в нашем случае – дрель) располагается прямо перпендикулярно относительно обрабатываемой поверхности на специальной станине – закрепленном на стойке шпинделе. При опускании шпинделя сверло входит в поверхность и проделывает в ней отверстие.
Главное преимущество работы на станке перед ручной обработкой – отверстие получается более точным . Закрепленную дрель можно четко сфокусировать и направить в нужное место.
Можно закрепить дрель на дополнительной продольной планке, размещенной перпендикулярно опускающему/поднимающему шпинделю на его корпусе – это позволит перемещать закрепленный инструмент не только в вертикальном, но и в горизонтальном направлении.
Токарный
Обработка деталей на токарном станке происходит за счет быстрых оборотов заготовки вокруг своей оси, которые обеспечиваются вращающимся от электродвигателя шпинделем, в данном случае – это патрон дрели. Режущий элемент подается вручную сбоку, перпендикулярно вращающейся заготовке, или же проникает внутрь, в зависимости от вида выполняемых работ.
Токарный станок используется для внутренней и наружной обработки металлических, деревянных или пластиковых деталей:
- нарезания резьбы;
- винторезных работ;
- подрезки и обработки торцов;
- зенкерования;
- развертывания;
- расточки.
Заготовка зажимается в станке между обеспечивающим крутящий момент элементом (насадкой в патроне дрели) и прижимной направляющей втулкой. Прижимная втулка размещается на специальных полозьях, и фиксируется в нужном положении гайкой. От длины полозьев будет зависеть размер заготовки, которую можно установить в агрегат .
В данном случае, при самостоятельном изготовлении станка, длина полозьев определяется индивидуально по желаниям и потребностям владельца.
Дрель же фиксируется в станине «намертво».
Фрезерный
Фрезерный станок используется для обработки металлических и деревянных заготовок с помощью фрезы – инструмента со специальными резцами, зубьями. Во время работы фреза, оборачиваясь вокруг своей оси, снимается с заготовки часть наружного слоя, придавая ей необходимую форму.
С помощью фрезы производят точильные и другие работы:
- резку;
- заточку;
- торцевание;
- зенкерование;
- развертку;
- нарезание резьбы;
- изготовление зубчатых колес.
В случае с самодельным мини-агрегатом, фрезеровочная насадка зажимается в патрон дрели, закрепленной на станине. Заготовка подается вручную или также фиксируется в специальном зажимном устройстве.
Шлифовальный
При помощи шлифовального станка производят зачистку различных поверхностей, делая их гладкими. Также шлифовка помогает менять форму заготовки, придавать ей нужный конструкционный вид, например, в деревообрабатывающей версии оборудования.
В качестве шлифующего элемента, как правило, используется наждачная бумага . В патрон дрели зажимается специальная насадка, которая имеет шероховатую поверхность – шлифблок.
Существуют насадки, предусматривающие замену шлифующего материала – лист наждачной бумаги фиксируется на их плоскую рабочую поверхность при помощи специальных «липучек», расположенных с тыльной стороны.
Процесс шлифовки производится за счет обработки заготовки вращающейся в патроне дрели насадкой со шлифующим покрытием. Благодаря абразивному напылению на наждачной бумаге она снимает с обрабатываемой заготовки часть ее поверхности.
При изготовлении станка дрель зажимается и фиксируется в станине в одном положении, а заготовка подается вручную.
В качестве упора для заготовки может использоваться дополнительная подставка – для удобства ее так же, как и в случае с токарным станком, можно разместить на полозьях.
Необходимые материалы и инструменты
Создающим крутящий момент элементом, а соответственно главной рабочей частью в каждом виде станка является дрель. Тип обработки будет в большей степени зависеть от установленной в ее патрон насадки. Поэтому для их сборки понадобятся идентичные материалы.
Для сборки токарного, шлифовального станка:
- прямоугольное металлическое или деревянное основание, станина;
- прижимная втулка;
- прижимная бабка, которая будет крепиться на патрон дрели;
- полозья для прижимной втулки;
- посадочное место для фиксации дрели.
Материалы для сборки сверлильного, фрезерного станка:
- квадратная станина;
- металлическая стойка, на которой будет перемещаться шпиндель с закрепленной дрелью;
- пружина, соответствующая диметру стойки;
- столик для заготовки;
- штифт для крепления столика.
Из инструментов понадобятся:
- отвертка;
- плоскогубцы;
- ножовка по дереву или металлу;
- крепежные элементы – болты, саморезы, гайки;
- сварочный аппарат.
Если планируется изготавливать металлический станок, то необходимым условием будет наличие сварочного аппарата.
Так как станок предназначается больше для домашнего использования, его чертежи и размеры составляющих элементов устанавливаются индивидуально.
Алгоритм изготовления
Учитывая, что по типу обработки домашние станки будут взаимозаменяемыми, а решающую роль будет играть установленная в дрель насадка, рассмотрим два основных варианта самодельных агрегатов – горизонтального и вертикального.
Порядок сборки вертикального станка таков.
- Вырезать из куска металла или дерева квадратную основу 50 на 50 см, толщиной от 10 до 20 мм.
- Точно по центру на расстоянии 1-2 см от края высверлить в ней отверстие для монтажа стойки. Диаметр стойки должен быть не менее 5 см.
- Установить стойку, отцентровать ее при помощи уровня и приварить сварочным электродом. Если изготавливается деревянный станок и стойка будет деревянной, то жестко зафиксировать ее саморезами.
- Дрель при помощи металлических хомутов закрепить на подвижном элементе, который будет надеваться на стойку, образуя опускающий/поднимающий шпиндель.
- Надеть пружину на стойку. Ее длина должна быть не менее 2/3 стойки.
- Насадив дрель на стойку, отметить место, куда будет попадать сверло при опускании шпинделя.
- Соответственно этому месту вырезать в станине крест-накрест две сквозные ложбины.
- В ложбину на штифте с резьбой устанавливается столик, на котором будет крепиться заготовка. С нижней стороны на штифт накручивается гайка, она будет фиксировать столик в нужном положении. С наружной стороны прикрепить столик к штифту можно также гайкой, утопив ее в поверхность столика, чтобы она не мешала укладке заготовок.
- Важно, чтобы после фиксации гайкой длина наружной части штифта была заподлицо с верхней поверхностью столика.
На столик укладывается заготовка (при необходимости фиксируется струбцинами) и по ложбинкам перемещается в нужном направлении. Дрель опускается вручную, обратно поднимается за счет пружины. Чтобы переоборудовать станок во фрезерный или шлифовальный, достаточно заменить сверло соответствующей насадкой – фрезой или шлифблоком.
Алгоритм сборки горизонтального станка выглядит так.
- Вырезать прямоугольную станину – размеры определяются индивидуально.
- На одном краю закрепить посадочное место для дрели с ложбиной в верхней части соответствующей размерам инструмента.
- Зафиксировать на нем дрель хомутом.
- Вдоль станины вырезать сквозную ложбину для штифта, а по краям установить два металлических уголка, по которым будет перемещаться прижимная втулка.
- Ширина прижимной втулки должна точно соответствовать расстоянию между направляющими уголками (полозьями). Снизу в нее вкручивается штифт с резьбой, который будет перемещаться в ложбине.
- Переместив втулку вплотную к патрону дрели, определить место, где будет установлена специальная бабка для фиксации заготовок.
- Прикрепить к втулке бабку с размещенным по центру металлическим конусообразным штырем.
- Втулка фиксируется в нужном положении (для зажима заготовки) гайкой, накручиваемой снизу на штифт.
Самодельный дисковый шлифовальный станок, сделанный умельцем своими руками: подробные фото изготовления с описанием.
Решил сделать себе в гараж — шлифовальный станок. В закромах нашёл старый двигатель советского производства, мощность около 1 кВт, 1420 об/мин.
Значит полностью разобрал этот электродвигатель и очистил от ржавчины, наждачной бумагой и надфилями.
На распределительной коробке была утеряна гайка, пришлось поставить гайку от переходника на пластиковую трубу.
Полировал корпус пастой ГОИ.
Затем почистил и покрасил кожух, использовал грунтовку, краску и лак.
У токаря заказал план-шайбу. Наружный диаметр — 100 мм, 4 отверстия и одно по центру, все диаметром 4 мм, толщина самой шайбы 4 мм. Однако, выяснилось, что на вал двигателя план-шайба одевается хоть с небольшим усилием, но от руки, а нужно, что бы с небольшим натягом. Фольга не влазит, слишком плотно, поэтому нанёс слой грунтовки.
Затем изготовил рабочую поверхность — диск из ДСП. Купил 2 куска ДСП толщиной 16 мм, для крупной наждачки и мелкой. По кругу нанесено 5 или 6 слоёв лака ПФ-170.
Чтобы точно установить диск, сделал так: по центру план-шайбы (в заранее просверленное отверстие при изготовлении) вбил коротыш из гвоздя, и совместил с просверленным отверстием в центре диска, разметил и просверлил в диске 4 отверстия под крепление.
Шляпки винтов утопил и посадил на эпоксидную смолу, чтоб не проворачивались при затягивании гаек.
Станину сделал из двери старого шкафа.
Поставил конденсаторы.
К диску приклеил наждачную бумагу № 60 на клей ПВА. Максимальный размер диска который можно использовать — 330 мм.
А еще шлифовальный станок называют гриндером, которая переводится с английского grinder как дробилка.
Дробилки бывают для камней, дробилки для мяса – у нас мясорубки, бывают садовые дробилки, выпускающие щепу. Но если слово употребляется самостоятельно – просто гриндер, имеется в виду только одно: шлифовальный станок в сфере обработки металлов.
Гриндер хорош и полезен везде, в том числе в домашнем хозяйстве – от грамотной заточки ножа высокого качества или портновских ножниц до шлифовки сложной детали из металла или другого «трудного» материала. Иными словами, инструмент нужный, в хозяйстве пригодится.
Тем более, что смастерить его своими руками вполне реально. Для этого вовсе необязательно иметь специальное оборудование и солидный профессиональный опыт.
Повозиться, конечно, придется, но зато вы сделает именно то, что вам нужно и, что весьма немаловажно, сэкономите серьёзную сумму денег вплоть до нескольких тысяч американских долларов.
Делаем с диском или с лентой?
Чертеж гриндера.
По широте продуктовой линейки с шлифовальными станками могут поспорить разве что токарные . Гриндеров на рынке предлагается огромное количество – всех мастей и размеров.
Самый известный и примитивный в виде знаменитого наждака – пары кругов из шлифовального камня с прикрученным мотором. Продаются эти станки с самыми разнообразными схемами и принципами действия.
Но если вы планируете сделать самодельный шлифовальный , лучше остановиться и выбрать между двумя вариантами: дисковым или ленточным.
- Дисковый гриндер шлифовальный слой из абразива наносится на диск, который во время включения вращается.
- Ленточный станок, в котором абразив нанесен на ленту, намотанную на ролики.
Какой из них лучше – рассуждать неправильно. Правильным будет критерий «какой нужнее». Выбор должен зависеть от того, что именно вы собираетесь шлифовать. Если это относительно простые детали из, скажем, дерева, вам больше подойдут дисковые самодельные шлифовальные станки по дереву.
Если же у вас впереди серьёзные шлифовальные работы по точной финишной доводке со сложными деталями, выбирайте ленту.
Нужно брать во внимание разницу между иском и лентой не только по их функциональных особенностях. Еще один важный фактор – мощность привода. Шлифуете деревянные зеготовки небольшого размера – вам хватит мощности в пределах 160 – 170 Вт.
Такую спокойно выдаст элементарный мотор от стиральной машины или даже от старой дрели.
Для ленточного гриндера старые бытовые моторы не подойдут никоим образом. Там понадобится движок с мощностью не менее 400 – 500 Вт, и не простой, а трехфазный с пусковыми и рабочими конденсаторами.
Для шлифовки массивных и габаритных деталей мощность будет нужна повыше: до 1200 Вт. Сразу заметим, что покупка конденсаторов к станку обойдется вам ненамного дешевле самого мотора.
Выбираем ленту
Станок с лентой универсальнее с точки зрения функциональности: он делает все, что дисковые модели, плюс еще много чего. Сразу заметим, что вариантов самодеятельных моделей ленточных шлифовальных станков великое множество.
Дело в том, что природа данного станка очень пластичная, позволяющая использовать самые разные подручные материалы, вплоть до находок на свалках металлолома.
Главное – знать и придерживаться трех правил:
- Абразивная сторона ленты должны быть настроена очень четко, чтобы ее касалась только заготовка, которая шлифуется.
- Лента должны быть равномерное натянута в любой момент времени и вне зависимости от вида работ.
- Скорость движения должна быть разной и должна зависеть только от одного: вида детали и характера шлифовки.
Конструирование самодельного ленточного шлифовального станка
Устройство шлифовального станка.
Главные следующие:
- Мотор или двигатель с приводом, работающий на электричестве.
Привод лучше устанавливать рядом с ведущим роликом главного диаметра. - Основание или станина.
Часто фиксируется прямо на полу, иногда эта штука ездит на колесиках – это как вам удобнее и нужнее. - Два натяжных катка – ведущий и ведомый.
Делать из металла или очень прочной древесины с тонким слоем прокладочной резины для предупреждения проскакивания ленты на роли или барабан. - Пружина и рычаг для системы натяжки ленты.
Пружина прижимная, а рычаг крепится к основанию и ведомому катку. - Основание для размещения мотора с приводом.
- Для ленты с абразивом нужно использовать бумагу или ткань.
Ее ширина может быть самой разной – в диапазоне от 5-ти до 30-ти см. Уровень зернистости – от 80-ти. - Металлические трубы толщиной от 2-х мм и больше.
- Металлические уголки в соответствии с размерами станка.
- Специальная магнитная подставка для металлических деталей.
- Направляющие типа рельсовых.
Схема устройства шлифовального станка.
Этапы работы:
- Делаем каркас основания или станины.
– режем уголки по размерам станины;
– свариваем каркас и уголки;
– фиксируем внизу рамы плиту из ДСП для снижения вибрации при работе. - Мастерим рабочую поверхность.
– вырезаем по размеру стальной лист и привариваем его прямо к основанию;
– привариваем рельсовые направляющие к верхней части каркаса;
– делаем каретку из уголков с колесиками для передвижения по направляющим станины;
– с обеих сторон рабочей поверхности монтируем и фиксируем опоры из подшипников;
– фиксируем винт с ручкой на каретке; - Фиксируем электрический двигатель систему подъема рабочей зоны.
- Закрепляем опоры передач.
- Устанавливаем ленту с абразивным покрытием.
– отрезаем ленту с запасом в несколько сантиметров под углом в 45°;
– склеиваем ее внахлест с промазкой клеем стороны со смытым водой абразивом;
– сушим место склеивания феном; - Готовимся к тестовому пуску станка.
– обрабатываем все детали станка машинным маслом;
– подводим электрическое питание;
– делаем пробным запуск.
Техника безопасности при работе на шлифовальном гриндере
Как и любая другая работа на любых других станках, шлифовка на самодельном ленточно шлифовальном станке подпадает под довольно жесткие правила безопасности, которых нужно строго придерживаться.
Принцип работы гриндера.
Эти правила следующие:
- Категорически запрещено трогать руками все, что движется и рабочей поверхности.
- Пользоваться защитными очками во время работы для защиты от раскалённых абразивных частиц.
- Тщательно проверять, крепки ли соединения и крепления всех движущихся частей гриндера.
- Следить за состоянием оплетки электрических проводов.
- Защитных кожух обязателен, даже несмотря на то, что он немного сужает угол обзора.
Шлифовальный станочек из дрели. Вариант предложен Павлом Ивановым из г. Томск.
Спроектирована эта шлифовалка по памяти (в интернете наткнулся однажды на аналогичную конструкцию), и собрана при первой же возможности — оказался в гостях у друга в мебельном цеху, натаскал обрезков и скрутил прям на месте.
В основе — жесткий короб с подстольем, в котором размещается дрель. Короб собирается на конфирматах. Сам инструмент фиксируется своеобразным зажимом.
Рассмотрим данный зажим подробнее, поскольку он является самым сложным элементом конструкции. Он представлен парой деталей: нижней, жестко закрепленной в П-образном коробе и верхней подвижной, которая притягивается к нижней парой винтов с барашками.
По центру, с помощью корончатого сверла (можно фрезой Форстнера подходящего диаметра) выбрано отверстие под редуктор дрели (фиксация осуществляется за площадку для крепления рукояти).
В нижней детали просверлены пара отверстий диаметром 10 мм, которые Т-образно соединяются с вертикальными каналами для шпилек от «барашков». В них вставлены гайки М10 с парой шайб. Думаю, что и как понятно из фотографии.
В собранном виде получилось вот так:
Что надо было сделать по-другому:
1. Вместо гаек М10 и шайб лучше использовать цилиндрические мебельные гайки «бочонки».
2. Ось вращения надо пониже, вровень со столом. (Ошибся в расчетах).
3. Нужен «задник» для дрели — при длительной работе от вибрации ее перекашивает малость, что очень заметно на толстых деталях.
В планах:
1. «Задник» (дощечка-подпорка).
2. Хочу накрыть область от «зажима» до стола кожухом, закрыть передний торец и сделать патрубок под пылесос.
3. «Направляшка»-ограничитель. Пока что обхожусь рейкой и струбцинками.
Точил на этой шлифовалке ножи кухонные, доску разделочную (фанера 12 мм), ДСП 16 мм, пластик. Нужно подбирать наждачку сообразно работе.
У меня ударная дрель (как и на фото в первом посте про такие шлифовалки). Минусы такого варианта — большой люфт патрона, трудно точить мелкие детали. Плюсы применения дрели — регулировка оборотов, меньше шансов «спалить» деталь.
При наличии фрезера можно сделать регулировку высоты дрели над столом. А это уже и долбежник, и мелкая циркулярка-болгарка (вместо шлифовалки можно поставить тонкий диск отрезной и резать профиля, трубы, пластик, кабель-каналы, пороги, плинтуса).
Еще один существенный минус такой шлифовалки — большая и тяжелая, на «шабашку» не потаскаешь 🙂
Гриндер своими руками: нюансы изготовления
Что это такое? Гриндер, сделанный своими руками, – незаменимый инструмент в любой мастерской. Он позволяет шлифовать изделия из дерева, пластика, металла, а также обрабатывать любые поверхности. В зависимости от выбора абразива можно работать с разными видами материалов.
Как сделать? Конструкций самодельных гриндеров множество. Кто-то делает их с применением двигателя от устаревшей стиральной машины, а кто-то – из старой болгарки или дрели. Но объединяют все эти модели одни и те же технические детали.
Вопросы, рассмотренные в материале:
- Принцип работы гриндера
- Особенности сборки гриндера своими руками
- Как сделать гриндер своими руками
- Из чего сделать гриндер своими руками
- Как склеить ленту для гриндера
- Из чего сделать ролики, шкив и поворотный стол для гриндера
Принцип работы гриндера
Гриндер – специальное шлифовальное устройство, в котором рабочим элементом является лента с абразивным напылением. Данное приспособление оснащается электрическим приводом. Предназначено оно для финальной обработки поверхности изделий из дерева, металла и различных полимеров. Такой прибор можно собрать своими руками, при этом особое внимание нужно уделить:
- точному следованию чертежам;
- последовательности осуществления работы;
- выбору подходящих материалов.
Особенностью гриндера является весьма несложная конструкция, воспроизвести которую можно даже в домашних условиях своими руками. Вам понадобятся электродвигатель, натяжные ролики и абразивная лента с нужной зернистостью.
Для корректной сборки данного устройства нужно представлять принцип его работы. При замыкании цепи активируется электромотор. Его вал стыкуется с ведущим катком. Вращаясь, ролик крутит абразивную ленту, а та в свою очередь – ведомые катки. Заготовка прикладывается к движущейся абразивной ленте и шлифуется. Для того чтобы в процессе использования оборудования лента не соскочила, следует ориентироваться на положение рабочей полосы.
Ленточный гриндер, изготовленный своими руками с соблюдением всех норм по размерам, позволит осуществлять обработку деталей, созданных из различных материалов. С его помощью можно эффективно устранять дефекты поверхности металлических заготовок, деревянных предметов, а также изделий, созданных из стекла. Регулируя катки, можно проводить обработку на различную глубину.
Длительное пользование шлифмашиной приводит к тому, что шлифовальная полоса изнашивается и растягивается. Устраняется данная проблема просто: при помощи механизма, расположенного на одном из роликов (между основным и второстепенным катком устройства), лента подтягивается и закрепляется в новом положении.
Особенности сборки гриндера своими руками
При изготовлении шлифовального устройства самостоятельно полезно изначально принять во внимание нюансы аналогичных изделий заводской сборки. К примеру, в стандартную комплектацию обязательно должен входить опорный столик для фиксации заготовки при обработке.
Шлифовальные агрегаты заводского изготовления оснащены столиками, которые могут поворачиваться на 90° по одной оси. Это дает возможность осуществлять шлифовку двух плоскостей заготовки подряд, не снимая ее с фиксации на данной поворотной поверхности. Если вам не нужна высокая точность обработки, то достаточно и статичного стола. С одной стороны, это упростит конструкцию, но с другой – шлифовальный станок потеряет долю функциональности.
В конструкцию шлифовального станка входят и другие элементы:
- катки;
- основание;
- лента;
- натяжной механизм;
- защитная стенка.
Эти детали можно приобрести, но вполне возможно сделать их своими руками. При работе шлифмашины возникает много пыли и искр. Во многом интенсивность распространения пыли зависит от материала, из которого сделаны заготовки. Поэтому в правила техники безопасности при пользовании данным станком входит обязательное использование защитных очков. Кроме того, в комплектацию устройства должно входить защитное акриловое стекло, которое будет отгораживать зону шлифовки от оператора (его глаз).
Обычно даже переносные шлифовальные станки комплектуются стальными корпусами. Это необходимо для придания всей конструкции достаточной жесткости. Стойки гриндера должны иметь отверстия, которые необходимы для фиксации агрегата на деревянной поверхности (например, на верстаке) с помощью болтов. Чем больше производительность шлифовального устройства, тем длиннее должна быть абразивная лента и, соответственно, мощнее приводной электродвигатель.
Как сделать гриндер своими руками
Наиболее ответственным моментом при осуществлении сборки гриндера своими руками является подготовительный этап. Он включает:
- Составление чертежа ленточного гриндера с размерами. Схема должна соответствовать требуемым эксплуатационным условиям. Можно «отрисовывать» чертеж своими руками. Другим разумным решением является использование готового варианта, который можно взять в Интернете. Чертеж должен быть подробным и содержать описание отдельных элементов конструкции станка с указанием всех размеров. В Сети можно найти схемы самых разных вариантов гриндеров (например, станок, сделанный из болгарки) любой производительности.
- Подготовку деталей и инструментов. Понадобятся: электролобзик, дрель и болгарка.
Конструкция шлифовального устройства подразумевает использование преимущественно металлических деталей и элементов. Поэтому некоторые узлы невозможно изготовить без токарного станка. Если у вас нет соответствующих навыков, можно заказать необходимые детали у профессионального токаря или же купить. Гриндер должен давать возможность обрабатывать как горизонтальные, так и вертикальные поверхности. Еще лучше, если будет предусмотрена возможность шлифовки под разными углами.
Из чего сделать гриндер своими руками
Привод – наиболее ответственная часть станка. Вам понадобится электромотор с частотой вращения якоря 1 500–3 000 об/мин. Требуемая мощность – 0,75–1 кВт. От того, насколько двигатель может держать обороты, зависит производительность оборудования. Удобно, если мотор оснащен регулятором частоты вращения якоря – тогда с помощью одного гриндера можно решать множество задач по обработке различных поверхностей.
Вам подойдут следующие типы электромоторов:
От стиральной машины
Использование данного силового агрегата многим представляется весьма сомнительной затеей. Дело в том, что при работе гриндера возникает много пыли и отходов шлифовки различных фракций. Мотор стиральной машины совершенно точно не рассчитан на работу в таких условиях, поэтому он может быстро выйти из строя. Впрочем, у некоторых мастеров, которые собрали гриндеры своими руками, подобные двигатели служили долгие годы (например, потому что в конструкции шлифстанка предусмотрена эффективная защита мотора от пыли).
От болгарки
Болгарка в рабочем состоянии – это практически готовый привод для шлифовального станка. Ее электродвигатель выдает нужные обороты для процесса качественной шлифовки. С помощью данного гриндера можно производить, например, заточку ножей и ножниц.
От шлифмашинки
Если по каким-то причинам заводская шлифовальная машинка потеряла функциональность, но при этом силовая часть осталась рабочей, то имеет смысл использовать ее электродвигатель. Достаточно закрепить электродвигатель в корпусе на верстаке и упорядочить систему включения/отключения.
Как склеить ленту для гриндера
Ленту для гриндера можно склеить из листов наждачной бумаги, имеющих стандартные размеры (длина – 1 830, 1 600, 1 230, 915 и 610 мм; ширина – 100 и 50 мм). Главное, чтобы получающаяся шлифовальная лента соответствовала следующим характеристикам:
- тканевая основа;
- способность выдерживать высокие скорости вращения;
- стойкость к абразивному воздействию;
- возможность удлинения на 10–15 % без разрыва ленты;
- незначительный нагрев даже при длительной работе.
При конструировании самодельного станка шлифовальная лента не должна быть длиннее 1 230 мм. В противном случае придется увеличивать габариты станка, что влечет дополнительные требования к размещению данного оборудования.
Алгоритм склейки абразивной ленты в домашних условиях:
- Из листов наждака нужно вырезать полосы требуемой ширины.
Края ленты следует делать диагональными разрезами.
- Края необходимо соединить и склеить малярным скотчем с абразивной стороны (временно).
- Срез зафиксировать парой капель суперклея.
- Место среза обработать и при помощи шелковой ленты соединить полосы между собой, плотно прижав друг к другу.
- Место склейки следует обернуть бумагой и положить под пресс на ночь.
Из чего сделать ролики, шкив и поворотный стол для гриндера
Ролики
Эти элементы (чтобы ролики не были слишком инертными) должны быть сделаны из легких металлов и сплавов. В противном случае при запуске двигателя слишком тяжелые ведомые колесики станут набирать скорость вращения медленнее, чем ведущий. То есть лента будет прокручиваться, что может ее повредить. Если другого металла, кроме стали, для создания ролика нет, можно хотя бы сделать его полым (впрочем, такие работы обойдутся дорого). Затем, чтобы абразивная лента не соскакивала с него, на ролике нужно выточить торцевую канавку.
Рекомендуем статьи
- Для чего нужен гидравлический пресс: виды, сферы применения
- Чем резать трубу: инструменты, способы, приемы
- Как сделать наковальню: простые советы и идеи
Шероховатость поверхности роликов не должна превышать значения 1,25-2,5 Ra. В противном случае абразивная лента будет быстро изнашиваться. Но слишком гладкими колесики также не следует делать, так как лента станет проворачиваться (скользить).
Шкив
Его можно изготовить из мотоциклетного колеса, фанеры и других листовых древесных материалов.
Поворотный стол
Если требуется обработка деталей с высокой точностью, без поворотного стола в конструкции станка не обойтись. Столик должен поворачиваться на 90°, при этом на нем должен присутствовать механизм крепления заготовки. Удобнее всего изготавливать подобную поверхность из дюралюминиевых листов толщиной не менее 1,5 см (если меньше, то велика вероятность, что стол не выдержит нагрузки).
Итак, собрать гриндер в домашних условиях, то есть своими руками, достаточно просто, особенно если подойти к делу с умом. Начните с выбора подходящего чертежа ленточного гриндера (в Интернете), а затем определитесь с функционалом. Это даст возможность понять, какая именно производительность шлифовального оборудования необходима.
Общий | Сверлильный станок своими руками | Практик-механик
ослепление
Нержавеющая сталь
- #1
Здравствуйте,
Я хочу иметь возможность затачивать сверла диаметром до 30 мм, чтобы покрыть свой диапазон.
Я хочу построить точилку для 4/6 фасонных сверл по принципу работы, показанному на этом сайте. Точилка для сверл своими руками. Это инструмент для любителей размером до 10 мм. Я хочу масштабировать дизайн, чтобы покрыть большие биты. Я уже купил двигатель приличного размера с большей мощностью.
Точилка этого типа требует, чтобы бита была зажата в центре блока инструментов. Я полагаю, что один держатель насадок не сможет охватить весь диапазон размеров насадок. Инструментальный блок на основе ER16 выдержит до 10 мм. Мне понадобится другой блок инструментов для более широкого диапазона сверл.
Я рассматриваю возможность использования дешевого китайского патрона, такого как этот, с шестью кулачками и наклонными кулачками, но мне интересно, есть ли лучший способ. Проблема с этим патроном заключается в том, что диаметр отверстия составляет всего 26 мм, и они, похоже, не продают кулачки с длинным наклоном с патронами большего размера. Другая проблема заключается в том, что спираль на моих больших сверлах достигает 80 мм. Челюсти должны иметь длину не менее 80 мм, чтобы контактировать как минимум с двумя лезвиями, чтобы сверло удерживалось по центру.
Я думал об использовании двух противоположных V-образных блоков длиной 100 мм, но не могу придумать простого способа изменить диаметр зажима.
Есть предложения по самоцентрирующемуся зажиму?
Стивен Томас
Алмаз
- #2
Возможно, я упускаю что-то очевидное, но если вы все равно собираетесь, как вы говорите, «увеличить масштаб», почему бы не увеличить патрон (шпиндель) до ER32 или ER40?
смт
L Vanice
Алмаз
- #3
В шлифовальном станке SRD производства США используется патрон с блокирующими V-образными блоками, два патрона для охвата диапазона размеров шлифовального станка модели 80B. Сложный в изготовлении, но дизайн работает очень хорошо.
Если вам необходимо заточить фаску, обратите внимание на шлифовальную машину Champ производства США, которая просто укладывает биты в кусок стального уголка, поэтому сложный патрон не нужен. Они очень быстро работают из-за простого держателя сверла.
Я видел на eBay 6-кулачковые патроны, некоторые китайские, некоторые польские, которые имеют один набор длинных кулачков и предназначены для использования на точилках для сверл.
Ларри
ослепление
Нержавеющая сталь
- #4
Стивен Томас сказал:
Возможно, я упускаю что-то очевидное, но если вы все равно собираетесь, как вы говорите, «увеличить масштаб», почему бы не увеличить патрон (шпиндель) до ER32 или ER40?
Нажмите, чтобы развернуть…
Цанги ER будут слишком короткими, чтобы захватить спиральные кромки насадок большого размера.
EPAIII
Алмаз
- #5
Я еще не строил, но задумался над дизайном. Одна идея, которую я придумал, заключалась в том, чтобы использовать один или, в вашем случае, два или три размера цанги, например, 12 мм, 25 мм и, возможно, 75 мм. Затем сделайте отдельные втулки для бит каждого размера. Втулки могут быть длиннее, чем цанги, и для них потребуется только пара прорезей, по одной на каждом конце и перекрывающихся в центре. Если втулки сделаны аккуратно, в цангах, на токарном станке, центрирование должно быть хорошим. Рукава большего размера могут быть длиннее, чтобы удерживать флейты.
Я думаю, вы могли бы сделать втулки с большим количеством прорезей, как цанга ER, которые охватывают диапазон размеров, возможно, в диапазоне 1 мм каждый.
ослепление
Нержавеющая сталь
- #6
Привет
Мне нравятся чередующиеся блоки Vee.
Они компактны, и один комплект может охватывать широкий диапазон размеров.
Единственное, что мне не нравится, так это цена, по крайней мере этих https://www.drill-grinder.com/storefront/scripts/prodView.asp?idproduct=23.
За такое количество золота я бы сделал набор.
Стивен Томас
Алмаз
- #7
Цанги ER будут слишком короткими, чтобы захватить спиральные кромки лагерных насадок.
Нажмите, чтобы развернуть…
Я не считаю это правдой. На самом деле фаски примерно такой же длины или даже длиннее, чем цанги 5ST, которые сделаны специально для захвата сверл, разверток и даже больших метчиков за фаски для заточки концов.
https://www.maritool.com/Collets-ER…/ER40-COLLET-1.1875-Special/product_info.html
Все сверла я затачиваю в магазине, кроме центровочных и ступенчатых, вручную. Но я делаю и затачиваю множество других инструментов (метчики, развертки, специальные сверла, концевые фрезы и т. д.) в различных приспособлениях, и поэтому я понимаю необходимость небольшого «захвата» с радиальным профилем с хорошей центровкой. Я вижу, что, несмотря на то, что они компактны по сравнению с другими вариантами, ER40 все еще немного массивны после добавления гайки. Гайки можно немного подрезать и использовать с помощью гаечного ключа, но диаметр все равно останется.
Я использовал рукава, описанные EPA. В моем пневматическом подшипнике Weldon используются втулки. Они могли быть как с носиком 5с, так и с прямым носом с рукавами. Они не считаются неточными. Hardinge, еще один сторонник тонких инструментов, использует втулки во многих вариантах крепления, хотя, конечно, они изобрели и являются лучшими производителями цанг -c (1c, 3c, 4c, 5c, 16c и т. д.).
Самой маленькой готовой и быстрой в сборке системой, которую я могу придумать, если не считать использования рукавов, будет либо 5ST, предназначенная для этой цели; или 5c с удлиненными носами, которые могут увеличивать внутреннюю длину за счет удлинения носа для захвата канавок. К сожалению, ни один из них не проходит через отверстие более чем на 1 дюйм. Я просверлил несколько отверстий для специальных целей, которые могут быть примерно 26,5 мм (1-1 / 32+ дюйма), но для этого размера осталось не так много резьбы. Преимущество цанг 5ST/5c в том, что они приводятся в действие вытяжной трубой, поэтому носик шпинделя может быть немного больше, чем диаметр носика цанги.
Цанги Ericson DA идеально подходят для сверл диаметром до 20 мм, очень малого диаметра на размер рукоятки; но это настолько велико, насколько они идут. Я использовал их на своих револьверных станках для сверл.
Последний вздох для готовых инструментов: у меня есть пара наборов цанг 6H, которые были стандартом Hendey. Они вроде как 5с, но длиннее и немного большего диаметра. Они проходят через приклад 1-1/8 дюйма, и я уверен, что их можно расточить до 30 мм, и все будет в порядке. Как и 5c, они приводятся в действие вытяжной трубой, поэтому диаметр носика немного больше, чем рабочий. Часть конуса можно даже затачивать меньшего размера, чтобы просто затачивать сверла.0007
Вы могли бы использовать такую систему. Устройство пройдет 32 мм в Vee-блоке/без цанги. Высота центра задается над мерными блоками, поэтому центрирование происходит довольно быстро. У меня есть, но обычно использую более дешевые варианты для средней работы, чтобы не запачкать
http://www.subtool. com/st/mg5cvs1_master-grind_spin_index_fixture.html
Удачи.
смт
ослепление
Нержавеющая сталь
- #8
Здравствуйте,
Это, безусловно, хорошее приспособление, и я вижу его преимущества, но цена делает его нерентабельным. За эту цену я мог бы купить пожизненный запас сверл.
Китайский 6-кулачковый патрон выглядит намного лучше (дешевле).
Я знаю, что мне потребуется как минимум два приспособления, чтобы охватить диапазон до 35 мм. ER16 подойдет до 10 мм. Магазин сделал чередующиеся блоки Vee, которые выглядят как хороший кандидат на диапазон +10 мм.
Макгайвер
Алмаз
- #9
дазз сказал:
Я хочу иметь возможность затачивать сверла до 30 мм, чтобы покрыть мой диапазон.
Я хочу построить шлифовальный станок с 4/6 гранями
Нажмите, чтобы развернуть…
Каждое утро, когда я смотрю в зеркало, я вижу, как моя самодельная шлифовальная машина
умная задница отвечает в сторону, у меня есть несколько идей для вас, чтобы построить то, что хорошо сработало. Я часто делаю ручную заточку до нескольких дюймов, но также хорошо иметь точный способ сделать это и сверла, которые я затачиваю с помощью моей заточки с точностью до пары тысяч желание перейти от крошечного к огромному. цанговые идеи и т. д. Мне не нравится, что недостаточно контакта с периферийной землей, особенно по мере увеличения размера.
Мой представляет собой V-образный блок, предназначенный для T&CG, он также хорошо работает на плоскошлифовальном станке. Я бы рекомендовал один из них в качестве основы; добавляет тонны возможностей, и вам не нужно строить шпиндели большого диаметра и т. д. В любом случае, мой используется на небольшом настольном T&CG и точно выполняет все размеры
Вот базовая установка. У меня есть три разных концевых упора для сверления любого размера. Блок V закален. Торцевые упоры и упор для зубьев крепятся к корпусу с помощью разрезных шплинтов, поэтому их можно быстро отрегулировать и сделать прочными.
Необходимы регулировки концевого упора сверла и опоры зуба. Я решил индексировать сверло для идеальной концентричности …. вместо шпинделя с огромным отверстием и патрона или цанги. Вот фото регулируемого по микрометру зубчатого упора.
Я также сделал универсу, на которой он стоит, наверное, не стоит сейчас, когда вокруг есть дешевые оффшорные
Работает действительно очень хорошо, почти без компромиссов — подходит практически для любого размера, легко устанавливается и индексируется.
10 способов использования аккумуляторной дрели-шуруповерта
Фото: CGardner
Некоторым может понравиться их мокрая пила для резки плитки, в то время как другие не могут расстаться со своим фрезером или рейсмусовым станком, но я готов держу пари, есть по крайней мере один электроинструмент, который каждый достойный домашний мастер имеет в пределах досягаемости и использует по крайней мере раз в неделю — аккумуляторную дрель и шуруповерт. Он портативный, полезный для всего, от подвешивания картин до обрамления дома, а для тех, кто в курсе, и для множества других задач. Вращающийся двигатель и регулируемый патрон означают, что вы можете вставлять любые предметы, чтобы они вращались — эта гибкость, как оказалось, может быть весьма полезной. Вот десять моих любимых способов использования аккумуляторной дрели-шуруповерта:
Дух. Я знаю, ты знаешь. Но подумайте о том, чтобы использовать его не только для того, чтобы просто забить базовое сверло. Сверление направляющих и зенкерных отверстий имеет важное значение для качественной отделки, поэтому рассмотрите специальный набор конических сверл только для этой задачи, например, со встроенным зенкером. Если вы не получаете качественные отверстия без разрывов, которые вы ищете, вы, вероятно, выбрали не те биты. Большинство простых спиральных сверл, продаваемых в хозяйственных магазинах, на самом деле предназначены для сверления металла на низкоскоростном сверлильном станке, поэтому подумайте о переходе на набор сверл с острием, предназначенных для дерева.
Фото: CGardner
2. Сделайте большие отверстия.Помимо стандартного набора сверл от 1/16″ до 1/2″, существуют всевозможные варианты для создания больших идеально круглых отверстий. Если ваша выемка должна быть круглой, специальная фреза всегда обеспечит более качественный разрез, чем пила для замочной скважины или электролобзик. Рассмотрите возможность использования его при создании места для встроенного освещения или при создании места для сантехнических труб в балках пола, шкафах, столешницах или, если вы амбициозны, в душе на открытом воздухе.
3. Водите все.Большинство дрелей поставляются со стандартными плоскими и крестовыми насадками, которые необходимы для заворачивания винтов и болтов. Также подумайте о приобретении набора шестигранных отверток, которые могут ускорить сборку мебели в разобранном виде и помочь разобрать предметы домашнего обихода для обслуживания и ремонта.
4.
В хозяйственных магазинах продаются специальные насадки для смешивания нескольких банок с краской для получения однородного цвета, подобно ручному миксеру на вашей кухне. Они также производят миксеры для взбивания яиц для бетона, строительных растворов, растворов и растворов.
Фото: CGardner
5. Отшлифуйте контуры и изогнутые поверхности.Плоская наждачная бумага и шлифовальные блоки отлично подходят для плоских поверхностей, но когда вам нужно отшлифовать кривые и дуги, вам нужна криволинейная шлифовальная поверхность. Используйте аккумуляторную дрель и шлифовальный барабан, чтобы придать гладкую поверхность даже самым неправильным формам.
6. Отшлифовать металл и удалить ржавчину. Если у вас нет ручной угловой шлифовальной машины, вы можете использовать насадку, которая вставляется в аккумуляторную дрель и позволяет использовать круги, предназначенные для угловых шлифовальных машин. В качестве альтернативы возьмите «насадку-щетку», чтобы использовать ее с дрелью для удаления ржавчины с железных и стальных инструментов и предметов домашнего обихода.
Фото: CGardner
7. Скрутите провода.Если вы хотите проложить несколько проводов одинаковой длины, вы можете поместить каждый из них в сверлильный патрон и вращать его, чтобы получился аккуратный пучок надежно переплетенных проводов. Этот метод также работает для скручивания стального троса, который вы можете использовать для подвешивания предметов к потолку, например, хранения или освещения в вашем гараже или подвале.
8. Выпрямите изогнутые или согнутые провода и кабели.Точно так же можно использовать дрель на низкой скорости для выпрямления изогнутых проводов и кабелей. Проверьте этот совет от 1953 Испанская версия Popular Mechanics :
Фото: mimecanicapopular.com
Говорят: «Закрепив проволоку в отверстии, потяните, чтобы она оставалась натянутой, и медленно вращайте сверло.