Самый простой пескоструйный аппарат
Как видно – это немаленькие изделия, как по весу, так и по стоимости. Можно ли сделать пескоструйное приспособление на 1-2 литра из подручных материалов, затратив минимум денег? Это вполне возможно, особенно если под рукой есть пистолет от краскопульта.
В быту их можно будет использовать для очистки заржавевшего металлического инструмента и деталей, элементов металлических ворот перед окраской, удаления загрязнений с поверхностей придомовых и садовых дорожек, выложенных плиткой или зацементированных.
Процесс изготовления простого пескоструйного аппарата
Приводим пошаговую инструкцию по изготовлению пескоструйной самоделки, работающей по принципу эжектора (пульверизатора).
Шаг 1. Необходимо купить или позаимствовать пневматический пистолет, рассчитанный на давление до 4 МПа, пластиковую 0,5- или 1-литровую бутылку, штуцер, шланги и сверла. О других материалах и инструментах будем упоминать по мере их применения на соответствующем шаге.
Шаг 2. Скручиваем с бутылки пробку, а оставшийся на горлышке поясок разрезаем столярным ножом и удаляем. Крышку плотно закручиваем на место.
Шаг 3. С помощью электродрели и сверла на 5 мм просверливаем горлышко бутылки по диаметру с обеих сторон прямо под самой крышкой.
Шаг 4. В просверленные отверстия аккуратно вставляем трубочку из комплекта к пневматическому пистолету. Определяем на ней место, где будет располагаться бутылка с песком. Оно должно быть ближе к пневматическому пистолету. Это обеспечит большую надежность конструкции, лучшую балансировку и удобство в работе.
Шаг 5. Вытаскиваем трубочку из отверстий в бутылке и отмечаем с помощью маркера на трубочке место, где будет пропилено продолговатое отверстие для поступления из емкости песка.
Шаг 6. С помощью напильника по металлу выполняем на трубочке продолговатое неширокое отверстие, аккуратно зачищая его края.
Шаг 7. Вновь возвращаем трубочку на место, причем выпиленное напильником отверстие должно быть направленно вниз, а над ней вертикально вверх будет располагаться бутылка.
Шаг 8. Места входа трубочки в бутылку и выхода из нее заливаем подходящим клеем, во-первых, для обеспечения прочности соединения, во-вторых, для герметизации, чтобы во время работы пескоструйного приспособления воздух, подаваемый компрессором, не выходил наружу.
Дождавшись полного отвердевания клея, можно приступать к испытанию пескоструйного аппарата, предварительно засыпав в бутылку сухой песок крупностью не более 0,5 мм, а пистолет с помощью шланга, соединив с компрессором, который в состоянии обеспечивать давление в 4 МПа (бар).
Шаг 9. Направляем трубочку пистолета на загрязнения садовой дорожки, регулируя давление воздуха, а значит и расход песка, с помощью ручки на инструменте. Эффективность очистки очевидна.
Шаг 10. Попытаемся очистить от ржавчины пассатижи, которые долгое время лежали где-то, подвергаясь воздействию воды или влажного воздуха. Направляя на ржавые места инструмента, струю воздуха вперемешку с песком, добиваемся его полной очистки. Поверхность металла после такой обработки приобретает благородный матовый оттенок.
Для информации: в качестве источника сжатого воздуха использован бытовой воздушный компрессор, на щитке управления которого расположена ручка регулировки расхода воздуха, расходомер, штуцеры для подключения шлангов и манометр, показывающий давление в системе.
В качестве средства очистки, наряду с мелким песком, можно использовать мелко раздробленную скорлупу грецких орехов.
Безопасность работы
Частицы песка или его заменителя вылетают из сопла пескоструйного устройства со скоростью в десятки метров в секунду и, отражаясь от очищаемой поверхности, могут повредить незащищенные части тела, особенно глаза и руки.
Поэтому при работе с пескоструйным аппаратом необходимо пользоваться средствами индивидуальной защиты: очками или щитком, респиратором, перчатками, одеждой с длинными рукавами. Работу желательно проводить на открытом воздухе или в помещении с эффективной приточно-вытяжной вентиляцией.
Смотрите видео
Original article in English
Пескоструй своими руками из баллона: подробное описание с фото
Изготовление пескоструйного аппарата своими руками от автора самоделки: фото изготовления с подробным описанием.
Для начала хочу показать схему моего самодельного пескоструя.
Итак, был куплен компрессор (в гараже штука нужная, но такой мощный брался для пескоструя) 2-х поршневой, с ресивером на 100 литров, ременной передачей, принудительным охлаждением поршней и двигателя мощностью 3кВт и производительностью 500л\мин — самый мощный однофазный компрессор из представленных у нас на рынке.
Хочу уточнить.
Для нормальной производительной пескоструйки этот компрессор слабоват, и по этому если кто надумает делать пескоструй мощнее того, которым песочат свечи, минимальная производительность компрессора должна быть от 500 л/мин и выше!
Ещё один важный момент — диаметр шланга должен быль в 3-4 раза больше диаметра сопла, шланг должен иметь как можно меньше соединений и изгибов, все сгоны не должны понижать внутреннее проходное сечение, длина шланга не должна превышать требуемую.
Если нужен длинный шланг, то нужно отыграться на удлинении воздушной части, а не той в которой будет транспортироваться песок, её я сделал всего 3 м, а воздушную часть — около 8-ми метров, что позволяет компрессору находится подальше от пескоструйки, и втягивать меньше пыли.
Шланг был взят с внутренним сечением 18 мм. При этом сгоны подошли на 1/2 (16мм) и 3/4 дюйма (20 мм).
Большое сечение должно сохраняться на всем трубопроводе, начиная от компрессора, и заканчивая соплом. По этому, быстросъемные соединения применяемые для краскопульта и пр. неприменимы для пескоструя в виду того, что на быстросъемных соединениях диаметр внутреннего сечения всего 5 мм.
По этому пришлось выкрутить заглушку на ресивере, и ввернуть на ее место шаровой кран, так как сечение заглушки 16 мм. На кран устанавливается накидная гайка, именуемая у сантехников «американкой», чтобы можно было легко отсоединять пескоструй от компрессора. Опять же подбираем сгоны так, чтобы не уменьшать проходное сечение
Подачу воздуха организовал, но столкнулся с еще одной проблемой — когда в бачке заканчивается песок, то основная его масса остается на краях сосуда, а в центре — пустота.
Решение простое — нужно сделать дно конусным. Понеслась: срезаю старое дно, из бляхи 1 мм делаю конус и привариваю его к ёмкости, снизу ввариваю резьбу 16 мм, перевариваю ножки на конус.
Теперь нужно сделать крючки для шлангов, чтобы их можно было удобно сматывать. Кроме того хочу сказать, что подавать воздух в баллон сверху оказалось лишним, более того без него все работает даже лучше, поэтому оставил только кран, при помощи которого можно стравливать давление с баллона, в том случае если в конусе забивается песок.
А это общий вид пескоструя в собранном виде — получилось довольно компактно, не смотря на длинный и толстый шланг)
Теперь осталось самое главное — сопло. Во первых должен быть кран для удобной работы, во вторых быстросъемный (ну или хотя бы чтоб снимался без инструментов) держатель сопла, и собственно само сопло из износостойкого материала.
Кран был взят на 3/4 дюйма (20 мм), по тому как его внутреннее сечение всего 18 мм. Вся рукоятка в сборе вместе с соплом выглядит так:
Держатель сопла сделал из накидной гайки на 3/4-ти и переходной муфты с 16 мм на 12 мм, которую накидной гайкой прикручиваем к крану.
В получившийся держатель вставляется керамическое сопло, а его несоответствие по диаметру устраняется подбором резинки нужного диаметра
Касательно сопла — его не трудно изготовить из свечи зажигания — была взята свечка от бензопилы, так как у нее электрод тоньше, и соответственно диаметр будущего сопла — 4 мм. Из свечи от классики получается сопло в 5 мм, что для моего компрессора очень много — слишком стремительно падает давление и компрессор не успевает его восполнять.
Чтобы получить из свечи сопло, нужно слезать с нее юбку и вообще весь металл. Затем алмазным диском (диск по камню, плитке керамической и т.п.) отпилить от керамического изолятора свечи нижнюю часть, ту которая находилась в юбке. Затем нужно выкрутить электрод из будущего сопла, а если не выкручивается, то необходимо высверлить его сверлом соотвественного диаметра. При наличии сверл с алмазным наконечником не плохо было бы сделать конус на сопле, со стороны крана, но в принципе и так все работает.
Самодельное сито тоже оказалось неудобным, да и камешки через него проскакивали, по этому было найдено металлическое сито для муки которое отлично себя зарекомендовало)
При пескоструйке пыль стоит непроглядная, по этом нужно использовать респиратор, желательно с «выхлопом» вниз.
Для защиты лица и глаз можно использовать маску из оргстекла, но она довольно быстро матуется — это уже вторая… Кстати, «выхлоп» вниз для того чтоб эта маска не потела.
Проверяем работу пескоструя на чашке задней пружины.
После обработки.
Ну и в заключение хочу сказать, что пескоструйный аппарат система комплексная, и при несоответствии хотя бы одной его части нормально работать не будет. Здесь можно провести аналогию — крепость цепи определяется крепостью ее самого слабого звена. По этому, для тех, кто решит делать пескоструй своими руками подведу итог, на что нужно обратить внимание чтобы создать рабочий аппарат:
1. Компрессор с производительностью от 500 л/мин и выше, с принудительным охлаждением, большим ресивером (50л минимум) и желательно с ременной
передачей, так как они не так греются, а при пескоструйке компрессор не выключается.
2. Диаметр внутреннего сечения всех шлангов и сгонов, начиная от компрессора и до сопла не должен быть меньше 16 мм, или хотя бы быть в 4 раза больше диаметра сопла, но тут кашу маслом не испортишь) Так же по возможности (а это возможно) нужно избегать изгибов на сгонах и шлангах уже при работе.
3. Баллон должен иметь конусное дно, с как можно более острым углом.
4. Сопла должны быть как можно тверже, к примеру сопло из закаленной стали проживет около часу — двух. Из керамики — около 100. Из карбида вольфрама — около 900-та часов. Боковое сечение сопла может быть как обычное прямолинейное, так и конусное (сопла Вентури). Последние дают прибавку в производительности, так как разгоняют частицы на последок до около 700 км/час (в прямолинейных соплах скорость приблизительно 300 км/час), но сопла Вентури дома пожалуй не изготовить, так как керамику нечем обрабатывать…
5. Песок. Он должен быть сеяный, желательно дважды, или даже трижды ситом, в котором размер ячейки меньше чем диаметр сопла. Кроме того песок должен быть полностью сухим, таким, чтобы он высыпался из кулака. Песок может быть речной серый, или желтый, или кварцевый, или любой как я понял, главное чтоб пескоструйный аппарат был красный, и абразив сухой и просеянный) Так же используют электрокорунд, стружку чугуна и прочие абразивы, но я думаю в гараже можно обойтись и без них.
6. Приведу некоторые показатели уже рабочего аппарата, что думаю облегчит постройку нового. И так: производительность компрессора — 500 л/мин, ресивер — 100 л, диаметр сопла — 4 мм, диаметр шлангов — 18 мм, Давление при пескоструйке — стремительно падает с 8 атм. до 1,5 и держится в этом диапазоне +/-0,5 атм. в зависимости от того, сколько времени открыт кран у сопла. Даже при таких низких давлениях успешно песочится краска и неглубокая ржавчина. Для случаев потяжелее приходится закрывать кран и немного ждать, пока нагноится давление повыше, но в принципе работать можно.
7. Бюджет. Если учится на чужих ошибках, и не наступать на те же грабли, то можно смастерить аппарат за примерно 50 у.е., если делать самому и уже иметь в наличии баллон и сварку с компрессором. Если включать в цену компрессор, тогда конечно цена другая будет, но я его не включал, по тому как в любом случае бы покупал его в гараж, и помощнее, чтобы в будущем пользоваться пневмоинструментом.
Ну вот вроде и все, вывалил на изнанку все что знал, но за то теперь есть статься, где собрано все что нужно для того, чтобы собрать аппарат в гаражных условиях.
Автор самоделки: Евгений Иримия. источник
Сделай сам: 5 простых шагов для установки временного ограждения для взрывных работ
Мы часто видим транспортные контейнеры, используемые на стройплощадках для создания временных площадок для взрывных работ. Это может быть тот случай, когда у вас есть проект с небольшим количеством клапанов и других деталей, требующих пескоструйной обработки, и вы можете вывести их из эксплуатации для пескоструйной обработки и покраски.
У других людей может возникнуть ситуация, когда им требуется помещение для дробеструйной очистки всего на 1-2 дня в месяц, и они хотят сделать это в месте, скрытом от глаз и содержащем абразив и пыль, которые распространяются повсюду.
Примечание 1: Эта установка не является зоной дробеструйной обработки, которая позволяет вам перерабатывать абразив, если это ваша цель, вам будет полезно иметь подходящее помещение для дробеструйной обработки. Мы можем помочь вам с этим, но обычно это включает в себя обсуждение, чтобы удовлетворить ваши потребности.
Примечание 2: Это относится исключительно к зоне пескоструйной обработки, свяжитесь с нами, если вам нужна установка для окраски, зона покраски должна быть взрывобезопасной и требует некоторых других соображений
Есть несколько важных факторов, которые следует учитывать
1. ВЕНТИЛЯЦИЯ
Если бластер не видит, что он делает, то у вас будет очень низкое качество работы и вам часто придется переделывать работу. Это также представляет угрозу безопасности, если бластер не может видеть, что он пытается сделать.
Если из-за плохо обустроенного участка вам придется делать переделки, вы потеряете много времени и денег, просто занимаясь погрузочно-разгрузочными работами. Часто обработка материалов является одной из самых дорогостоящих частей проекта. Так что подберите правильное оборудование, и вы опередите своих конкурентов.
2. Воздушный поток
Вы хотите, чтобы воздушный поток проходил непосредственно мимо бластера и вентилировался через дверцы контейнера сзади.
Как правило, если воздуховод действительно используется, он размещается на переднем отверстии контейнера. Как и в нашем предыдущем видео внутри резервуара, если в этом воздуховоде работает всасывающий вакуум, он просто вытягивает свежий поступающий воздух. Если это вентилятор, дующий внутрь и создающий положительное давление, то, скорее всего, он раздувает вздымающиеся облака пыли, застрявшие в дальнем конце.
Чтобы эффективно улавливать пыль и свести к минимуму выход абразива наружу, мы рекомендуем вам установить перегородку, которая проходит от верхней части контейнера до 18 дюймов от пола. Поместите эту фальшстену примерно в 12 дюймах от задней части контейнера.
Вырежьте отверстие диаметром 12–20 дюймов в задней части контейнера по направлению к верху и прикрепите к нему вентиляционный канал и воздуховод.
Для создания сквозняка вы можете использовать простой черный макс или синий волшебник, который создаст хороший поток. Если это более постоянная установка или вам нужно больше удаления пыли, вы можете арендовать пылесборник для проекта.
4. Освещение
Очень важно иметь отличное освещение, так как это позволяет бластеру четко видеть, во что он стреляет. Установите 4-5 ламп вокруг верхнего края под углом к центру контейнера, это создаст много света и сведет к минимуму количество повторений
5. Предотвратите выход абразива
Мы рекомендуем вам установить несколько простых дверей, таких как куриный сарай с куриной сеткой и простым фильтровальным листом или затеняющей тканью, чтобы предотвратить выход абразива из области. Фильтрующая пленка над дверями по-прежнему будет способствовать хорошему притоку воздуха и естественному освещению помещения.
Вы можете просто полностью убрать двери и использовать вместо них эти двери.
6. Извлечение абразива
Чтобы облегчить сбор абразива, который течет вместе с воздушным потоком, большая его часть будет выпадать, когда он начнет возвращаться обратно в область задней перегородки, поэтому добавьте кусок фанеры под углом 45 градусов. , и это заставит абразив стекать обратно в зону дробеструйной обработки, что упрощает его сбор лопатой для утилизации.
Вы также можете вырезать место в боковой части контейнера и сделать небольшой навес для пескоструйной установки и места для легкой утилизации.
ПЛОХАЯ ВЕНТИЛЯЦИЯ
Обычно на входе в эти контейнеры размещают воздуховоды. Если воздуховод использует всасывание, он в основном улавливает потоки свежего воздуха, которые в противном случае могли бы попасть в контейнер. Если они дуют под положительным давлением, они, как правило, создают вздымающиеся облака пыли, которые не могут покинуть заднюю стенку и, таким образом, расширяются, ограничивая видимость бластера. Для любого процесса (положительного или отрицательного давления) это крайне неэффективная установка.ПРАВИЛЬНО ОСУЩЕСТВЛЕННАЯ ВЕНТИЛЯЦИЯ
Присоединение воздуховода к задней части контейнера и использование отрицательного давления (вакуумная экстракция) является наилучшей установкой для этого конкретного сценария.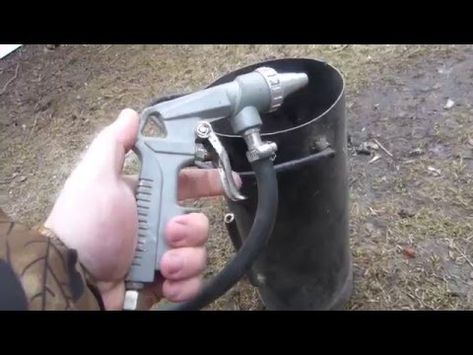
Опять же, эти рекомендации являются общими обходными путями, дающими вам общее представление о том, как избавиться от пыли в контейнере с одним входом. Тем не менее, мы настоятельно рекомендуем обратиться к опытному специалисту, который поможет в вашей конкретной ситуации.
Если у вас есть какие-либо сомнения или вопросы относительно предстоящего проекта покраски, позвоните в нашу сервисную службу. Мы всегда здесь, чтобы помочь!
Обращайтесь в BlastOne со своими вопросами!
К сожалению, многие подрядчики считают вентиляцию просто затратами на соблюдение требований, тогда как на самом деле ВЕНТИЛЯЦИЯ ОПЛАЧИВАЕТ СЕБЯ ЧЕРЕЗ БОЛЕЕ БЕЗОПАСНУЮ И ПРОИЗВОДИТЕЛЬНУЮ СРЕДУ. Мы предлагаем эти принципы и рекомендации, чтобы помочь в охране здоровья, безопасности и производительности вашей рабочей силы.
4 ПРИНЦИПА:
- Хорошая вентиляция помогает поддерживать качество воздуха в зоне дыхания оператора на уровне, позволяющем респиратору оператора эффективно справляться с любыми оставшимися атмосферными загрязнителями.
- Хорошая вентиляция помогает поддерживать хорошую видимость за счет удаления пыли и освещения рабочей зоны.
- Хорошая вентиляция обеспечивает приток свежего воздуха для разбавления любых загрязняющих веществ в рабочей зоне, предотвращая их взрывоопасность. Всегда используйте газоанализаторы.
- Хорошая вентиляция также защищает от вредной пыли или примесей свинца, выбрасываемых из корпуса для пескоструйной обработки и загрязняющих окружающую среду.
3 ПРАВИЛА, которым необходимо следовать при проектировании системы вентиляции:
- Воздух должен поступать вверх, а вытягиваться вниз. Причина этого двояка:
- Во-первых, пары растворителей и пыль тяжелее воздуха. Извлечение от высокого до низкого использует гравитацию , для помощи в их удалении и .
- Это помогает ограничить воздействие этих загрязняющих веществ в зоне дыхания операторов. Вентиляция вверх естественным образом поднимает загрязняющие вещества и увеличивает вероятность компрометации оборудования СИЗ и/или зрения операторов.
- Система должна обеспечивать правильный поток воздуха для достижения правильного количества воздухообменов (ИЗМЕРЯЕТСЯ В ЧАСОВЫХ ИЗМЕНЕНИЯХ ИЛИ СКОРОСТИ ВОЗДУХА В РАБОЧЕЙ ЗОНЕ) — и это зависит от следующих трех факторов:
- Тип сбрасываемых загрязняющих веществ
- Вид работы
- Размер пространства
- Опасная пыль или пары должны быть надлежащим образом собраны или безопасно удалены, чтобы соответствовать экологическим нормам или нормам OSHA.
- Если рабочая зона герметизирована, площадь поперечного сечения должна быть как можно меньше.
Рекомендации по проектированию локализации и вентиляции
СКАЧАТЬ БЕСПЛАТНО!
Загрузить отчет
Пескоструйная обработка и покраска в сравнении с покраской
От администратора Опубликовано 6 сентября 2018 г. Медиа взрыв Без комментариев
Надлежащая отделка проекта по изготовлению металла имеет решающее значение для его защиты и эстетики. Функция всегда должна быть важнее формы, поэтому вам нужно найти тип и метод покраски, которые помогут ей противостоять нагрузкам и износу, а также придадут ей завершающий штрих, который вы ищете.
Покраска проекта по изготовлению металла включает распыление краски на водной основе или на основе растворителя на поверхность, как и любой другой проект покраски. Помимо грунтовки и верхнего слоя, которые часто объединяются в один, покраска проста и понятна.
Пескоструйная обработка и покраска требуют немного больше работы и включают в себя предварительную обработку, нанесение и отверждение. Пескоструйная обработка очищает поверхность проекта от любого мусора, жира или предыдущего лакокрасочного покрытия с использованием абразивной среды. Этот метод создает небольшие царапины на поверхности, что помогает краске покрыть и сцепиться с материалом. Без пескоструйной обработки краска может быть более склонна к сколам и трещинам. Пескоструйная обработка также удаляет ржавчину со стали, давая ей чистый лист для следующего защитного покрытия.
После этого абразивного процесса с помощью электростатического пистолета наносится грунтовка и порошок на основе цинка, что позволяет краске равномерно и быстро покрывать поверхность. Он также предотвращает чрезмерное распыление и толстые слои, которые склонны к сколам, поскольку отталкивает избыток.
После пескоструйной обработки и окраски детали отправляются в печь для отверждения, где грунтовка затвердевает и превращается в гель. Когда этот процесс завершен, наносится последний слой краски. Окончательный слой наносится так же, как и грунтовка, но именно тогда появляется желаемый цвет или текстура. После завершения окрашенная деталь возвращается в печь для затвердевания.
Преимущества пескоструйной обработки и покраски Основными преимуществами пескоструйной обработки и покраски по сравнению с покраской являются прочность и долговечность. Это больше, чем просто слой краски, этот процесс подготавливает поверхность, грунтует изделие и наносит последовательные слои краски, а также отвердевает изделие, чтобы максимизировать защитные эффекты надлежащей отделки.
Вот некоторые другие преимущества пескоструйной обработки и окраски:
- Стойкость к коррозии: Благодаря точному нанесению грунтовки и краски один слой обеспечивает защиту нескольких слоев традиционной краски без риска появления сколов и трещин. Из-за этого обработанная пескоструйной обработкой и окрашенная деталь может лучше противостоять экстремальным внешним условиям, чем традиционная краска.
- Экономичность: продуманная система пескоструйной обработки и окраски предотвращает избыточное распыление, поэтому вы получаете больший выход краски и меньше отходов.
- Скорость: Детали, подвергнутые пескоструйной обработке и окрашенные, сохнут быстрее, чем влажная краска, поэтому весь процесс происходит быстрее. После того как детали остынут, они также готовы к обработке или обработке, что сокращает время простоя.