- ΠΠΎΠ²ΠΊΠ°. ΠΠΎΠ²ΠΊΠ° ΠΌΠ΅ΡΠ°Π»Π»Π°. Π’Π΅Ρ Π½ΠΎΠ»ΠΎΠ³ΠΈΡ ΠΊΠΎΠ²ΠΊΠΈ. ΠΠΏΠ΅ΡΠ°ΡΠΈΠΈ ΠΊΠΎΠ²ΠΊΠΈ.
- ΠΠΎΠ²ΠΊΠ° ΡΠ²ΠΎΠ±ΠΎΠ΄Π½Π°Ρ 89, 103 β Π’Π΅Ρ Π½ΠΎΠ»ΠΎΠ³ΠΈΡ
- Π’Π΅Ρ
Π½ΠΎΠ»ΠΎΠ³ΠΈΡ Ρ
ΡΠ΄ΠΎΠΆΠ΅ΡΡΠ²Π΅Π½Π½ΠΎΠΉ ΠΊΠΎΠ²ΠΊΠΈ ΠΈ ΡΠ»Π΅ΡΠ°ΡΠ½ΠΎΠ³ΠΎ ΠΈΡΠΊΡΡΡΡΠ²Π°. Π§Π°ΡΡΡ 1.
- ΠΡΠ·Π½Π΅ΡΠ½ΡΠΉ ΠΈΠ½ΡΡΡΡΠΌΠ΅Π½Ρ ΠΈ ΠΎΠ±ΠΎΡΡΠ΄ΠΎΠ²Π°Π½ΠΈΠ΅
- ΠΡΠ½ΠΎΠ²Π½ΡΠ΅ ΡΠΏΠΎΡΠΎΠ±Ρ Π΄Π΅ΡΠΎΡΠΌΠΈΡΠΎΠ²Π°Π½ΠΈΡ ΠΊΠΎΠ²ΠΊΠΎΠ³ΠΎ ΠΆΠ΅Π»Π΅Π·Π°.
- ΠΠ°Π³ΡΠ΅Π²
- ΠΡΠΎΡΡΠΆΠΊΠ°
- Π‘ΠΊΡΡΠ³Π»Π΅Π½ΠΈΠ΅ Π³ΡΠ°Π½Π΅ΠΉ
- ΠΡΠΎΡΠΌΠ»Π΅Π½ΠΈΠ΅ ΡΡΡΡΠΏΠΎΠ²
- ΠΡΡΠ°Π΄ΠΊΠ°
- ΠΠΈΠ±ΠΊΠ°
- ΠΡΠΎΠ±ΠΈΠ²ΠΊΠ°
- Π ΡΠ±ΠΊΠ°
- ΠΡΠΎΠ΄Π΅Π²Π°Π½ΠΈΠ΅
- Π‘ΠΊΡΡΡΠΈΠ²Π°Π½ΠΈΠ΅-ΡΠΎΡΡΠΈΡΠΎΠ²Π°Π½ΠΈΠ΅
- Π¨ΠΈΡΠΊΠΈ
- ΠΠΎΠ»ΡΡΡ-ΡΠΏΠΈΡΠ°Π»ΠΈ
- Π‘Π²Π΅ΡΡΠΊΠ° ΠΊΠΎΠ»Π΅Ρ
- ΠΠ΅ΡΠ΅ΡΠ΅ΡΠ΅Π½ΠΈΠ΅ Π²Π½Π°Ρ Π»Π΅ΡΡ
- Π Π°ΡΡΠ΅ΠΊΠ°Π½ΠΈΠ΅
- Π‘ΠΊΠΎΠ±Ρ
- ΠΠΎΠ²Π°Π½Π°Ρ Π·Π°Π³ΠΎΡΠΎΠ²ΠΊΠ°: ΠΡΠ½ΠΎΠ²Ρ ΠΊΠΎΠ²ΠΊΠΈ ΠΌΠ΅ΡΠ°Π»Π»Π°
- ΠΠΎΠ»Π΅Π·Π½ΡΠ΅ ΡΡΠ°ΡΡΠΈ β Π’Π΅Ρ Π½ΠΎΠ»ΠΎΠ³ΠΈΡ ΠΊΠΎΠ²ΠΊΠΈ
- Π’Π΅Ρ Π½ΠΎΠ»ΠΎΠ³ΠΈΡ ΠΊΠΎΠ²ΠΊΠΈ
- Π’Π΅Ρ
Π½ΠΎΠ»ΠΎΠ³ΠΈΡ ΡΡΡΠ½ΠΎΠΉ ΠΊΠΎΠ²ΠΊΠΈ
- Π‘ΠΎΠ΄Π΅ΡΠΆΠ°Π½ΠΈΠ΅.
- ΠΠ»Π°Π²Π° I. ΠΡΠ°ΡΠΊΠΈΠ΅ ΡΠ²Π΅Π΄Π΅Π½ΠΈΡ ΠΎ ΠΊΡΠ·Π½Π΅ΡΠ½ΠΎΠΌ ΠΏΡΠΎΠΈΠ·Π²ΠΎΠ΄ΡΡΠ²Π΅
- ΠΠ»Π°Π²Π° II. ΠΠ±ΡΠΈΠ΅ ΡΠ²Π΅Π΄Π΅Π½ΠΈΡ ΠΎ Π½Π°Π³ΡΠ΅Π²Π΅ ΠΌΠ΅ΡΠ°Π»Π»ΠΎΠ²
- ΠΠ»Π°Π²Π° III. ΠΠ°Π³ΡΠ΅Π²Π°ΡΠ΅Π»ΡΠ½ΡΠ΅ ΡΡΡΡΠΎΠΉΡΡΠ²Π°
- ΠΠ»Π°Π²Π° IV. ΠΠ½ΡΡΡΡΠΌΠ΅Π½ΡΡ ΠΈ ΠΏΡΠΈΡΠΏΠΎΡΠΎΠ±Π»Π΅Π½ΠΈΡ Π΄Π»Ρ ΡΡΡΠ½ΠΎΠΉ ΠΊΠΎΠ²ΠΊΠΈ
- ΠΠ»Π°Π²Π° V. ΠΡΠ·Π½Π΅ΡΠ½ΡΠ΅ ΠΎΠΏΠ΅ΡΠ°ΡΠΈΠΈ
- ΠΠ»Π°Π²Π° VI. Π‘Π²Π΅Π΄Π΅Π½ΠΈΡ ΠΈΠ· ΡΠ΅ΠΎΡΠΈΠΈ ΠΎΠ±ΡΠ°Π±ΠΎΡΠΊΠΈ ΠΌΠ΅ΡΠ°Π»Π»ΠΎΠ² Π΄Π°Π²Π»Π΅Π½ΠΈΠ΅ΠΌ
- ΠΠ»Π°Π²Π° VII. Π‘ΠΎΡΡΠ°Π²Π»Π΅Π½ΠΈΠ΅ ΡΠ΅ΡΡΠ΅ΠΆΠ° ΠΏΠΎΠΊΠΎΠ²ΠΊΠΈ ΠΈ ΡΠ²Π΅Π΄Π΅Π½ΠΈΡ ΠΎ Π΄ΠΎΠΏΡΡΠΊΠ°Ρ , ΠΏΡΠΈΠΏΡΡΠΊΠ°Ρ ΠΈ Π½Π°ΠΏΡΡΠΊΠ°Ρ Π² ΠΊΡΠ·Π½Π΅ΡΠ½ΠΎΠΌ ΠΏΡΠΎΠΈΠ·Π²ΠΎΠ΄ΡΡΠ²Π΅
- ΠΠ»Π°Π²Π° VIII. Π’Π΅Ρ Π½ΠΈΠΊΠ° Π±Π΅Π·ΠΎΠΏΠ°ΡΠ½ΠΎΡΡΠΈ, ΡΠ»Π΅ΠΊΡΡΠΎΠ±Π΅Π·ΠΎΠΏΠ°ΡΠ½ΠΎΡΡΡ ΠΈ ΠΏΡΠΎΡΠΈΠ²ΠΎΠΏΠΎΠΆΠ°ΡΠ½ΡΠ΅ ΠΌΠ΅ΡΠΎΠΏΡΠΈΡΡΠΈΡ
- ΠΠ»Π°Π²Π° IX. ΠΠΎΠ΄Π³ΠΎΡΠΎΠ²ΠΊΠ° ΠΈΡΡ ΠΎΠ΄Π½ΡΡ ΠΌΠ°ΡΠ΅ΡΠΈΠ°Π»ΠΎΠ²
- ΠΠ»Π°Π²Π° X. Π‘Π²Π΅Π΄Π΅Π½ΠΈΡ ΠΎ ΡΡΡΡΠΊΡΡΡΠ½ΡΡ ΠΏΡΠ΅Π²ΡΠ°ΡΠ΅Π½ΠΈΡΡ Π² ΡΠΏΠ»Π°Π²Π°Ρ ΠΏΡΠΈ Π½Π°Π³ΡΠ΅Π²Π΅ ΠΈ ΠΊΠΎΠ²ΠΊΠ΅
- ΠΠ»Π°Π²Π° XI. Π’Π΅Ρ Π½ΠΎΠ»ΠΎΠ³ΠΈΡΠ΅ΡΠΊΠΈΠΉ ΠΏΡΠΎΡΠ΅ΡΡ ΡΡΡΠ½ΠΎΠΉ ΠΊΠΎΠ²ΠΊΠΈ
- ΠΠ»Π°Π²Π° XII. ΠΠ°Π²Π΅ΡΡΠ°ΡΡΠΈΠ΅ ΠΎΠΏΠ΅ΡΠ°ΡΠΈΠΈ ΠΏΡΠΎΠΈΠ·Π²ΠΎΠ΄ΡΡΠ²Π° ΠΏΠΎΠΊΠΎΠ²ΠΎΠΊ
- ΠΠ»Π°Π²Π° XIII. ΠΠΏΠ΅ΡΠ°ΡΠΈΠΈ ΠΌΠ°ΡΠΈΠ½Π½ΠΎΠΉ ΠΊΠΎΠ²ΠΊΠΈ
- ΠΠ»Π°Π²Π° XIV. ΠΡΡ ΠΎΠ΄Π½ΡΠ΅ ΠΌΠ°ΡΠ΅ΡΠΈΠ°Π»Ρ
- ΠΠ»Π°Π²Π° XV. ΠΠ½ΡΡΡΡΠΌΠ΅Π½Ρ Π΄Π»Ρ ΠΌΠ°ΡΠΈΠ½Π½ΠΎΠΉ ΠΊΠΎΠ²ΠΊΠΈ
- ΠΠ»Π°Π²Π° XVI. ΠΠΎΠ²ΠΎΡΠ½ΠΎΠ΅ ΠΎΠ±ΠΎΡΡΠ΄ΠΎΠ²Π°Π½ΠΈΠ΅, Π΅Π³ΠΎ Π²ΡΠ±ΠΎΡ ΠΈ ΠΏΡΠ°Π²ΠΈΠ»Π° ΡΠΊΡΠΏΠ»ΡΠ°ΡΠ°ΡΠΈΠΈ
- ΠΠ»Π°Π²Π° XVII. Π‘Π²Π΅Π΄Π΅Π½ΠΈΡ ΠΎ ΠΏΡΠΎΠΈΠ·Π²ΠΎΠ΄ΡΡΠ²Π΅ ΠΏΠΎΠΊΠΎΠ²ΠΎΠΊ ΠΌΠ΅ΡΠΎΠ΄ΠΎΠΌ Π³ΠΎΡΡΡΠ΅ΠΉ ΡΡΠ°ΠΌΠΏΠΎΠ²ΠΊΠΈ.
- ΠΠ»Π°Π²Π° XVIII. ΠΠΎΠ²ΠΊΠ° ΡΠ²Π΅ΡΠ½ΡΡ ΡΠΏΠ»Π°Π²ΠΎΠ² ΡΠΏΠ»Π°Π²ΠΎΠ²
- Π§ΡΠΎ ΡΠ°ΠΊΠΎΠ΅ ΠΊΠΎΠ²ΠΊΠ°? Π Π°Π·Π»ΠΈΡΠ½ΡΠ΅ Π²ΠΈΠ΄Ρ ΠΏΠΎΠΊΠΎΠ²ΠΎΠΊ Π² ΠΏΠΎΠ΄Π΅ΡΠΆΠ°Π½Π½ΠΎΠΌ ΠΏΡΠΎΠΈΠ·Π²ΠΎΠ΄ΡΡΠ²Π΅
- ΠΠ»Ρ ΡΠ΅Π³ΠΎ Π½ΡΠΆΠ½Π° ΠΊΠΎΠ²ΠΊΠ°?
- ΠΠ°ΠΊΠΈΠ΅ Π±ΡΠ²Π°ΡΡ Π²ΠΈΠ΄Ρ ΠΊΠΎΠ²ΠΊΠΈ?
- ΠΠ°ΠΊΠΈΠ΅ ΡΡΡΠ΅ΡΡΠ²ΡΡΡ ΠΏΡΠΎΡΠ΅ΡΡΡ ΠΊΠΎΠ²ΠΊΠΈ?
- ΠΠ°ΠΊΠΎΠ΅ ΠΎΠ±ΠΎΡΡΠ΄ΠΎΠ²Π°Π½ΠΈΠ΅ ΠΈΡΠΏΠΎΠ»ΡΠ·ΡΠ΅ΡΡΡ Π΄Π»Ρ ΠΊΠΎΠ²ΠΊΠΈ?
- Π‘Π²ΠΎΠ΄ΠΊΠ°
- ΠΡΡΠΎΡΠ½ΠΈΠΊΠΈ
- ΠΠΎΠ»ΡΡΠ΅ ΠΎΡ Custom Manufacturing & Fabricating
- Π΄ΠΎΡΡΠΈΠΆΠ΅Π½ΠΈΠΉ Π² ΡΠ΅Ρ Π½ΠΎΠ»ΠΎΠ³ΠΈΠΈ ΠΊΠΎΠ²ΠΊΠΈ Π΄Π»Ρ ΡΡΠΆΠ΅Π»ΠΎΠΉ ΠΏΠΎΠ΄Π²ΠΈΠΆΠ½ΠΎΠΉ ΠΊΠΎΠ½ΡΡΡΡΠΊΡΠΈΠΈ Stru
- ΠΠΎΠ²Π°Π½ΡΠ΅ ΠΠΠ | GKN Sinter Metals
- ΠΠΎΠ²ΡΠ΅ ΡΠ΅Π½Π΄Π΅Π½ΡΠΈΠΈ Π² ΠΊΡΠ·Π½Π΅ΡΠ½ΡΡ ΡΠ΅Ρ Π½ΠΎΠ»ΠΎΠ³ΠΈΡΡ : ΠΠ°ΡΠ΅ΡΠΈΠ°Π»Ρ ΠΊΠΎΠ½ΡΠ΅ΡΠ΅Π½ΡΠΈΠΈ AIP: Π’ΠΎΠΌ 1353, β 1
- ΠΠΎΡΡΡΠ°Ρ ΡΡΠ°ΠΌΠΏΠΎΠ²ΠΊΠ° — ΠΎΠ±Π·ΠΎΡ
- ΠΡΠ΄ΡΡΠ΅Π΅ ΠΊΡΠ·Π½Π΅ΡΠ½ΠΎΠΉ ΠΎΠ±ΡΠ°Π±ΠΎΡΠΊΠΈ — ΠΠ°ΠΌΠ΅Π½ΠΈΡ Π»ΠΈ ΠΊΠΎΠ²ΠΊΠ° Π½ΠΎΠ²ΡΠΌΠΈ ΠΏΡΠΎΡΠ΅ΡΡΠ°ΠΌΠΈ?
- Π§ΡΠΎ ΡΠ°ΠΊΠΎΠ΅ ΠΏΡΠΎΡΠ΅ΡΡ ΠΊΠΎΠ²ΠΊΠΈ, ΠΎΠΏΠ΅ΡΠ°ΡΠΈΡ, ΡΠΈΠΏΡ, ΠΏΡΠΈΠΌΠ΅Π½Π΅Π½ΠΈΠ΅, ΠΏΡΠ΅ΠΈΠΌΡΡΠ΅ΡΡΠ²Π° ΠΈ Π½Π΅Π΄ΠΎΡΡΠ°ΡΠΊΠΈ?
ΠΠΎΠ²ΠΊΠ°. ΠΠΎΠ²ΠΊΠ° ΠΌΠ΅ΡΠ°Π»Π»Π°. Π’Π΅Ρ Π½ΠΎΠ»ΠΎΠ³ΠΈΡ ΠΊΠΎΠ²ΠΊΠΈ. ΠΠΏΠ΅ΡΠ°ΡΠΈΠΈ ΠΊΠΎΠ²ΠΊΠΈ.
ΠΠΎΠ²ΠΊΠ° ΠΌΠ΅ΡΠ°Π»Π»Π°
ΠΠΎΠ²ΠΊΠ° β ΡΠΏΠΎΡΠΎΠ± ΠΎΠ±ΡΠ°Π±ΠΎΡΠΊΠΈ Π΄Π°Π²Π»Π΅Π½ΠΈΠ΅ΠΌ, ΠΏΡΠΈ ΠΊΠΎΡΠΎΡΠΎΠΌ Π΄Π΅ΡΠΎΡΠΌΠΈΡΠΎΠ²Π°Π½ΠΈΠ΅ Π½Π°Π³ΡΠ΅ΡΠΎΠ³ΠΎ (ΡΠ΅ΠΆΠ΅ Ρ ΠΎΠ»ΠΎΠ΄Π½ΠΎΠ³ΠΎ) ΠΌΠ΅ΡΠ°Π»Π»Π° ΠΎΡΡΡΠ΅ΡΡΠ²Π»ΡΠ΅ΡΡΡ ΠΈΠ»ΠΈ ΠΌΠ½ΠΎΠ³ΠΎΠΊΡΠ°ΡΠ½ΡΠΌΠΈ ΡΠ΄Π°ΡΠ°ΠΌΠΈ ΠΌΠΎΠ»ΠΎΡΠ° ΠΈΠ»ΠΈ ΠΎΠ΄Π½ΠΎΠΊΡΠ°ΡΠ½ΡΠΌ Π΄Π°Π²Π»Π΅Π½ΠΈΠ΅ΠΌ ΠΏΡΠ΅ΡΡΠ°.
Π€ΠΎΡΠΌΠΎΠΎΠ±ΡΠ°Π·ΠΎΠ²Π°Π½ΠΈΠ΅ ΠΏΡΠΈ ΠΊΠΎΠ²ΠΊΠ΅ ΠΏΡΠΎΠΈΡΡ ΠΎΠ΄ΠΈΡ Π·Π° ΡΡΠ΅Ρ ΠΏΠ»Π°ΡΡΠΈΡΠ΅ΡΠΊΠΎΠ³ΠΎ ΡΠ΅ΡΠ΅Π½ΠΈΡ ΠΌΠ΅ΡΠ°Π»Π»Π° Π² Π½Π°ΠΏΡΠ°Π²Π»Π΅Π½ΠΈΡΡ , ΠΏΠ΅ΡΠΏΠ΅Π½Π΄ΠΈΠΊΡΠ»ΡΡΠ½ΡΡ ΠΊ Π΄Π²ΠΈΠΆΠ΅Π½ΠΈΡ Π΄Π΅ΡΠΎΡΠΌΠΈΡΡΡΡΠ΅Π³ΠΎ ΠΈΠ½ΡΡΡΡΠΌΠ΅Π½ΡΠ°. ΠΡΠΈ ΡΠ²ΠΎΠ±ΠΎΠ΄Π½ΠΎΠΉ ΠΊΠΎΠ²ΠΊΠ΅ ΡΠ΅ΡΠ΅Π½ΠΈΠ΅ ΠΌΠ΅ΡΠ°Π»Π»Π° ΠΎΠ³ΡΠ°Π½ΠΈΡΠ΅Π½ΠΎ ΡΠ°ΡΡΠΈΡΠ½ΠΎ, ΡΡΠ΅Π½ΠΈΠ΅ΠΌ Π½Π° ΠΊΠΎΠ½ΡΠ°ΠΊΡΠ½ΠΎΠΉ ΠΏΠΎΠ²Π΅ΡΡ Π½ΠΎΡΡΠΈ Π΄Π΅ΡΠΎΡΠΌΠΈΡΡΠ΅ΠΌΡΠΉ ΠΌΠ΅ΡΠ°Π»Π» β ΠΏΠΎΠ²Π΅ΡΡ Π½ΠΎΡΡΡ ΠΈΠ½ΡΡΡΡΠΌΠ΅Π½ΡΠ°: Π±ΠΎΠΉΠΊΠΎΠ² ΠΏΠ»ΠΎΡΠΊΠΈΡ ΠΈΠ»ΠΈ ΡΠΈΠ³ΡΡΠ½ΡΡ , ΠΏΠΎΠ΄ΠΊΠ»Π°Π΄Π½ΡΡ ΡΡΠ°ΠΌΠΏΠΎΠ².
ΠΠΎΠ²ΠΊΠΎΠΉ ΠΏΠΎΠ»ΡΡΠ°ΡΡ ΡΠ°Π·Π½ΠΎΠΎΠ±ΡΠ°Π·Π½ΡΠ΅ ΠΏΠΎΠΊΠΎΠ²ΠΊΠΈ ΠΌΠ°ΡΡΠΎΠΉ Π΄ΠΎ 300 Ρ.
ΠΠ΅ΡΠ²ΠΈΡΠ½ΠΎΠΉ Π·Π°Π³ΠΎΡΠΎΠ²ΠΊΠΎΠΉ Π΄Π»Ρ ΠΏΠΎΠΊΠΎΠ²ΠΎΠΊ ΡΠ²Π»ΡΡΡΡΡ:
ΠΠΎΠ²ΠΊΠ° ΠΌΠΎΠΆΠ΅Ρ ΠΏΡΠΎΠΈΠ·Π²ΠΎΠ΄ΠΈΡΡΡΡ Π² Π³ΠΎΡΡΡΠ΅ΠΌ ΠΈ Ρ ΠΎΠ»ΠΎΠ΄Π½ΠΎΠΌ ΡΠΎΡΡΠΎΡΠ½ΠΈΠΈ.
Π₯ΠΎΠ»ΠΎΠ΄Π½ΠΎΠΉ ΠΊΠΎΠ²ΠΊΠ΅ ΠΏΠΎΠ΄Π΄Π°ΡΡΡΡ Π΄ΡΠ°Π³ΠΎΡΠ΅Π½Π½ΡΠ΅ ΠΌΠ΅ΡΠ°Π»Π»Ρ β Π·ΠΎΠ»ΠΎΡΠΎ, ΡΠ΅ΡΠ΅Π±ΡΠΎ, Π° ΡΠ°ΠΊΠΆΠ΅ ΠΌΠ΅Π΄Ρ. Π’Π΅Ρ
Π½ΠΎΠ»ΠΎΠ³ΠΈΡΠ΅ΡΠΊΠΈΠΉ ΠΏΡΠΎΡΠ΅ΡΡ Ρ
ΠΎΠ»ΠΎΠ΄Π½ΠΎΠΉ ΠΊΠΎΠ²ΠΊΠΈ ΡΠΎΡΡΠΎΠΈΡ ΠΈΠ· Π΄Π²ΡΡ
ΡΠ΅ΡΠ΅Π΄ΡΡΡΠΈΡ
ΡΡ ΠΎΠΏΠ΅ΡΠ°ΡΠΈΠΉ: Π΄Π΅ΡΠΎΡΠΌΠ°ΡΠΈΠΈ ΠΌΠ΅ΡΠ°Π»Π»Π° ΠΈ ΡΠ΅ΠΊΡΠΈΡΡΠ°Π»Π»ΠΈΠ·Π°ΡΠΈΠΎΠ½Π½ΠΎΠ³ΠΎ ΠΎΡΠΆΠΈΠ³Π°.
ΠΠΎΡΡΡΠ°Ρ ΠΊΠΎΠ²ΠΊΠ° ΠΏΡΠΈΠΌΠ΅Π½ΡΠ΅ΡΡΡ Π΄Π»Ρ ΠΈΠ·Π³ΠΎΡΠΎΠ²Π»Π΅Π½ΠΈΡ ΡΠ°Π·Π»ΠΈΡΠ½ΡΡ ΠΈΠ·Π΄Π΅Π»ΠΈΠΉ, Π° ΡΠ°ΠΊΠΆΠ΅ ΠΈΠ½ΡΡΡΡΠΌΠ΅Π½ΡΠΎΠ²: ΡΠ΅ΠΊΠ°Π½ΠΎΠ², Π·ΡΠ±ΠΈΠ», ΠΌΠΎΠ»ΠΎΡΠΊΠΎΠ² ΠΈ Ρ.ΠΏ.
ΠΠ°ΡΠ΅ΡΠΈΠ°Π»ΠΎΠΌ Π΄Π»Ρ Π³ΠΎΡΡΡΠ΅ΠΉ ΠΊΠΎΠ²ΠΊΠΈ ΡΠ²Π»ΡΡΡΡΡ ΠΌΠ°Π»ΠΎΡΠ³Π»Π΅ΡΠΎΠ΄ΠΈΡΡΡΠ΅ ΡΡΠ°Π»ΠΈ, ΡΠ³Π»Π΅ΡΠΎΠ΄ΠΈΡΡΡΠ΅ ΠΈΠ½ΡΡΡΡΠΌΠ΅Π½ΡΠ°Π»ΡΠ½ΡΠ΅ ΠΈ Π½Π΅ΠΊΠΎΡΠΎΡΡΠ΅ Π»Π΅Π³ΠΈΡΠΎΠ²Π°Π½Π½ΡΠ΅ ΡΡΠ°Π»ΠΈ. ΠΠ°ΠΆΠ΄Π°Ρ ΠΌΠ°ΡΠΊΠ° ΡΡΠ°Π»ΠΈ ΠΈΠΌΠ΅Π΅Ρ ΠΎΠΏΡΠ΅Π΄Π΅Π»Π΅Π½Π½ΡΠΉ ΠΈΠ½ΡΠ΅ΡΠ²Π°Π» ΡΠ΅ΠΌΠΏΠ΅ΡΠ°ΡΡΡ Π½Π°ΡΠ°Π»Π° ΠΈ ΠΊΠΎΠ½ΡΠ° ΠΊΠΎΠ²ΠΊΠΈ, Π·Π°Π²ΠΈΡΡΡΠΈΠΉ ΠΎΡ ΡΠΎΡΡΠ°Π²Π° ΠΈ ΡΡΡΡΠΊΡΡΡΡ ΠΎΠ±ΡΠ°Π±Π°ΡΡΠ²Π°Π΅ΠΌΠΎΠ³ΠΎ ΠΌΠ΅ΡΠ°Π»Π»Π°.
ΠΠΏΠ΅ΡΠ°ΡΠΈΠΈ ΠΊΠΎΠ²ΠΊΠΈ
Π Π°Π·Π»ΠΈΡΠ°ΡΡ ΠΊΠΎΠ²ΠΊΡ ΠΏΡΠ΅Π΄Π²Π°ΡΠΈΡΠ΅Π»ΡΠ½ΡΡ ΠΈ ΠΎΠΊΠΎΠ½ΡΠ°ΡΠ΅Π»ΡΠ½ΡΡ. ΠΡΠ΅Π΄Π²Π°ΡΠΈΡΠ΅Π»ΡΠ½Π°Ρ ΠΊΠΎΠ²ΠΊΠ° (ΠΈΠ»ΠΈ ΡΠ΅ΡΠ½ΠΎΠ²Π°Ρ) ΠΏΡΠ΅Π΄ΡΡΠ°Π²Π»ΡΠ΅Ρ ΡΠΎΠ±ΠΎΠΉ ΠΊΡΠ·Π½Π΅ΡΠ½ΡΡ ΠΎΠΏΠ΅ΡΠ°ΡΠΈΡ ΠΎΠ±ΡΠ°Π±ΠΎΡΠΊΠΈ ΡΠ»ΠΈΡΠΊΠ° Π΄Π»Ρ ΠΏΠΎΠ΄Π³ΠΎΡΠΎΠ²ΠΊΠΈ Π΅Π³ΠΎ ΠΊ Π΄Π°Π»ΡΠ½Π΅ΠΉΡΠ΅ΠΉ Π΄Π΅ΡΠΎΡΠΌΠ°ΡΠΈΠΈ ΠΏΡΠΎΠΊΠ°ΡΠΊΠΎΠΉ, ΠΏΡΠ΅ΡΡΠΎΠ²Π°Π½ΠΈΠ΅ΠΌ ΠΈ Ρ.ΠΏ. ΠΠΊΠΎΠ½ΡΠ°ΡΠ΅Π»ΡΠ½Π°Ρ ΠΊΠΎΠ²ΠΊΠ° (ΡΠΈΡΡΠΎΠ²Π°Ρ) ΠΎΡ Π²Π°ΡΡΠ²Π°Π΅Ρ Π²ΡΠ΅ ΠΌΠ΅ΡΠΎΠ΄Ρ ΠΊΡΠ·Π½Π΅ΡΠ½ΠΎΠΉ ΠΎΠ±ΡΠ°Π±ΠΎΡΠΊΠΈ (ΠΎΡΠ°Π΄ΠΊΡ ΠΈ Π²ΡΡΠ°Π΄ΠΊΡ, ΠΏΡΠΎΡΡΠΆΠΊΡ ΠΈ ΡΠ°ΡΠΊΠ°ΡΠΊΡ Π½Π° ΠΎΠΏΡΠ°Π²ΠΊΠ΅, ΠΏΡΠΎΡΠΈΠ²ΠΊΡ, Π³ΠΈΠ±ΠΊΡ ΠΈ ΡΠΊΡΡΡΠΈΠ²Π°Π½ΠΈΠ΅), Ρ ΠΏΠΎΠΌΠΎΡΡΡ ΠΊΠΎΡΠΎΡΡΡ ΠΈΠ·Π΄Π΅Π»ΠΈΡ ΠΏΡΠΈΠ΄Π°ΡΡ ΠΎΠΊΠΎΠ½ΡΠ°ΡΠ΅Π»ΡΠ½ΡΡ ΡΠΎΡΠΌΡ.
ΠΠΎΠ²ΠΊΠ° ΡΠ²ΠΎΠ±ΠΎΠ΄Π½Π°Ρ 89, 103 β Π’Π΅Ρ Π½ΠΎΠ»ΠΎΠ³ΠΈΡ
ΠΠ»ΠΈΡΠ½ΠΈΠ΅ Π½Π° ΠΊΠ°ΡΠ΅ΡΡΠ²ΠΎ Π΄Π΅ΡΠ°Π»ΠΈ 90 ΠΠΎΠ²ΠΊΠ° ΡΠ²ΠΎΠ±ΠΎΠ΄Π½Π°Ρ 89, 103 β Π’Π΅Ρ Π½ΠΎΠ»ΠΎΠ³ΠΈΡ 109 β[c.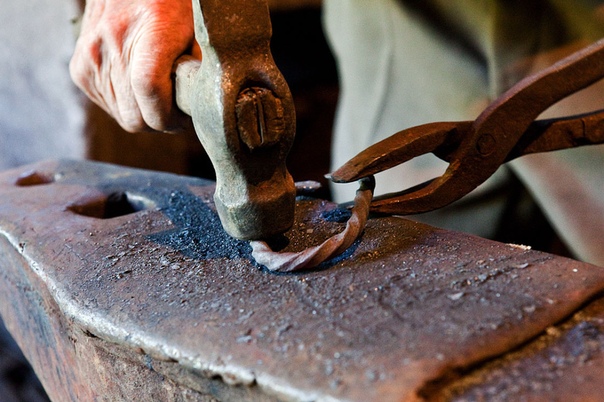
Π₯Π°ΡΠ°ΠΊΡΠ΅ΡΠΈΡΡΠΈΠΊΠ° ΠΏΠΎΠΊΠΎΠ²ΠΎΠΊ, ΠΈΠ·Π³ΠΎΡΠΎΠ²Π»ΡΠ΅ΠΌΡΡ ΠΌΠ΅ΡΠΎΠ΄ΠΎΠΌ ΡΠ²ΠΎΠ±ΠΎΠ΄Π½ΠΎΠΉ ΠΊΠΎΠ²ΠΊΠΈ, ΠΈ ΡΠ΅Ρ Π½ΠΎΠ»ΠΎΠ³ΠΈΡ ΠΈΡ ΠΈΠ·Π³ΠΎΡΠΎΠ²Π»Π΅Π½ΠΈΡ β[c.284]
Π’Π΅Ρ Π½ΠΎΠ»ΠΎΠ³ΠΈΡ ΠΊΠΎΠ²ΠΊΠΈ ΠΈ ΡΡΠ°ΠΌΠΏΠΎΠ²ΠΊΠΈ Π΄ΠΎ 1928 Π³. ΠΊΠ°ΡΠ΅ΡΡΠ²Π΅Π½Π½ΠΎ Π½Π΅ ΠΈΠ·ΠΌΠ΅Π½ΠΈΠ»Π°ΡΡ ΠΏΠΎ ΡΡΠ°Π²Π½Π΅Π½ΠΈΡ Ρ Π΄ΠΎΡΠ΅Π²ΠΎΠ»ΡΡΠΈΠΎΠ½Π½ΡΠΌ ΠΏΠ΅ΡΠΈΠΎΠ΄ΠΎΠΌ. Π‘Π²ΠΎΠ±ΠΎΠ΄Π½Π°Ρ ΠΊΠΎΠ²ΠΊΠ° ΡΠ³Π»Π΅ΡΠΎΠ΄ΠΈΡΡΠΎΠΉ ΠΈ Π»Π΅Π³ΠΈΡΠΎΠ²Π°Π½Π½ΠΎΠΉ ΡΡΠ°Π»ΠΈ Π² Π³Π»Π°Π΄ΠΊΠΈΡ ΠΈ Π²ΡΡΠ΅Π·Π½ΡΡ Π±ΠΎΠΉΠΊΠ°Ρ ΠΈ Π² ΠΏΠΎΠ΄ΠΊΠ»Π°Π΄Π½ΡΡ ΡΡΠ°ΠΌΠΏΠ°Ρ , ΠΊΡΠΎΠΌΠ΅ ΡΠ²ΠΎΠ΅Π³ΠΎ ΠΎΠ±ΡΡΠ½ΠΎΠ³ΠΎ ΠΏΡΠΈΠΌΠ΅Π½Π΅Π½ΠΈΡ Π² ΠΈΠ·Π³ΠΎΡΠΎΠ²Π»Π΅Π½ΠΈΠΈ ΡΠΈΠΏΠΎΠ²ΡΡ Π΄Π΅ΡΠ°Π»Π΅ΠΉ ΠΌΠ°ΡΠΈΠ½ΠΎΡΡΡΠΎΠ΅Π½ΠΈΡ, Π±ΡΠ»Π° Π²Π½Π΅Π΄ΡΠ΅Π½Π° Π² ΠΏΡΠΎΠΈΠ·Π²ΠΎΠ΄ΡΡΠ²Π΅ ΠΏΡΡΡΠΊΠΎΠ² Π±ΡΡΡΡΠΎΡΠ΅ΠΆΡΡΠ΅ΠΉ ΡΡΠ°Π»ΠΈ Π΄Π»Ρ ΠΏΠΎΡΠ»Π΅Π΄ΡΡΡΠ΅Π³ΠΎ ΠΈΠ·Π³ΠΎΡΠΎΠ²Π»Π΅Π½ΠΈΡ ΠΈΠ· Π½ΠΈΡ ΡΠ΅ΠΆΡΡΠ΅Π³ΠΎ ΠΏ Π΄ΡΡΠ³ΠΎΠ³ΠΎ ΡΠ°Π±ΠΎΡΠ΅Π³ΠΎ ΠΈΠ½ΡΡΡΡΠΌΠ΅Π½ΡΠ°. β[c.107]
Π Π°ΡΡΠΈΡΠ΅Π½ΠΈΠ΅ ΠΏΡΠΎΠΈΠ·Π²ΠΎΠ΄ΡΡΠ²Π° Π°Π²ΠΈΠ°ΡΠΈΠΎΠ½Π½ΡΡ ΠΈ Π°Π²ΡΠΎΠΌΠΎΠ±ΠΈΠ»ΡΠ½ΡΡ Π΄Π²ΠΈΠ³Π°ΡΠ΅Π»Π΅ΠΉ Π½Π΅ ΠΌΠΎΠ³Π»ΠΎ Π½Π΅ ΠΎΠΊΠ°Π·ΡΠ²Π°ΡΡ Π²Π»ΠΈΡΠ½ΠΈΡ Π½Π° ΡΠΎΠ²Π΅ΡΡΠ΅Π½ΡΡΠ²ΠΎΠ²Π°Π½ΠΈΠ΅ ΡΠ΅Ρ Π½ΠΎΠ»ΠΎΠ³ΠΈΠΈ ΡΠ²ΠΎΠ±ΠΎΠ΄Π½ΠΎΠΉ ΠΊΠΎΠ²ΠΊΠΈ. ΠΡΠ»ΠΈ ΡΠ°Π½Π΅Π΅ ΠΊΠΎΠ»Π΅Π½ΡΠ°ΡΡΠ΅ Π²Π°Π»Ρ ΡΡΠ°ΡΠΈΠΎΠ½Π°ΡΠ½ΡΡ Π΄Π²ΠΈΠ³Π°ΡΠ΅Π»Π΅ΠΉ ΠΊΠΎΠ²Π°Π»ΠΈ ΠΈΠ· ΠΏΡΠΎΡΡΠΎΠΉ ΡΠ³Π»Π΅ΡΠΎΠ΄ΠΈΡΡΠΎΠΉ ΡΡΠ°Π»ΠΈ, ΡΠΎ Π² ΠΏΠ΅ΡΠΈΠΎΠ΄ ΠΏΠ΅ΡΠ²ΡΡ ΠΏΡΡΠΈΠ»Π΅ΡΠΎΠΊ ΠΊΠΎΠ»Π΅Π½ΡΠ°ΡΡΠ΅ Π²Π°Π»Ρ Π°Π²ΠΈΠ°ΡΠΈΠΎΠ½Π½ΡΡ Π΄Π²ΠΈΠ³Π°ΡΠ΅Π»Π΅ΠΉ Π² ΠΊΡΠ·Π½Π΅ΡΠ½ΡΡ ΡΠ΅Ρ Π°Ρ ΡΡΠ°Π»ΠΈ ΠΊΠΎΠ²Π°ΡΡ ΠΈΠ· Ρ ΡΠΎΠΌΠΎΠ½ΠΈΠΊΠ΅Π»Π΅Π²ΠΎΠΉ ΡΡΠ°Π»ΠΈ, Π² ΠΊΠΎΡΠΎΡΡΡ Π²Ρ ΠΎΠ΄ΠΈΠ»ΠΈ Π‘ (0,25β0,35%), Π‘Π³ (0,8β1,0%), Ni (3,00β 3,25%), ΠΠΏ (0,40-0,60%), Si (0,20-0,30%), Π ΠΈ S (Π½Π΅ Π±ΠΎΠ»Π΅Π΅ 0,03%).

Π‘Π²ΠΎΠ±ΠΎΠ΄Π½Π°Ρ ΠΊΠΎΠ²ΠΊΠ° ΠΏΡΠΈΠΌΠ΅Π½ΡΠ»Π°ΡΡ ΡΠ°ΠΊΠΆΠ΅ Π΄Π»Ρ ΠΈΠ·Π³ΠΎΡΠΎΠ²Π»Π΅Π½ΠΈΡ ΠΌΠ½ΠΎΠ³ΠΈΡ
Π΄ΡΡΠ³ΠΈΡ
Π΄Π΅ΡΠ°Π»Π΅ΠΉ Π΄Π²ΠΈΠ³Π°ΡΠ΅Π»Π΅ΠΉ β ΠΊΠ»Π°ΠΏΠ°Π½ΠΎΠ², ΡΠ΅ΡΡΠ΅ΡΠ΅Π½, ΡΠ°ΡΡΠ½ΠΎΠ² Π½ Π΄Ρ. ΠΡΠΏΠΎΠ»ΡΠ·ΠΎΠ²Π°Π½ΠΈΠ΅ ΠΏΡΠΈ ΡΡΠΎΠΌ Π·Π½Π°ΡΠΈΡΠ΅Π»ΡΠ½ΡΡ
ΠΏΡΠΈΠΏΡΡΠΊΠΎΠ² Π²ΡΠ·ΡΠ²Π°Π»ΠΎ Π±ΠΎΠ»ΡΡΠΎΠΉ ΠΎΡΡ
ΠΎΠ΄ ΠΌΠ΅ΡΠ°Π»Π»Π° Π² ΡΡΡΡΠΆΠΊΡ. ΠΠ°ΡΠ°Π»Π»Π΅Π»ΡΠ½ΠΎ ΡΠΎ ΡΠ²ΠΎΠ±ΠΎΠ΄Π½ΠΎΠΉ ΠΊΠΎΠ²ΠΊΠΎΠΉ ΠΏΠΎΠ»ΡΡΠΈΠ»Π° ΡΠ°ΡΠΏΡΠΎΡΡΡΠ°Π½Π΅Π½ΠΈΠ΅ ΡΠ΅Ρ
Π½ΠΎΠ»ΠΎΠ³ΠΈΡ Π³ΠΎΡΡΡΠ΅ΠΉ ΡΡΠ°ΠΌΠΏΠΎΠ²ΠΊΠΈ, ΡΠΎΡΠ΅ΡΠ°Π²ΡΠ°Ρ ΡΠ²ΠΎΠ±ΠΎΠ΄Π½ΡΡ ΠΊΠΎΠ²ΠΊΡ Π·Π°Π³ΠΎΡΠΎΠ²ΠΊΠΈ Π²Π½Π°ΡΠ°Π»Π΅ ΠΈ ΠΏΠΎΡΠ»Π΅Π΄ΡΡΡΡΡ ΡΡΠ°ΠΌΠΏΠΎΠ²ΠΊΡ, ΠΈΠ·Π²Π΅ΡΡΠ½ΡΡ ΠΏΠΎΠ΄ Π½Π°Π·Π²Π°Π½ΠΈΠ΅ΠΌ Π΅Π²ΡΠΎΠΏΠ΅ΠΉΡΠΊΠΎΠΉ, ΠΊΠΎΡΠΎΡΠ°Ρ ΠΏΡΠΈΠΌΠ΅Π½ΡΠ»Π°ΡΡ Π΅ΡΠ΅ Π² Π΄ΠΎΡΠ΅Π²ΠΎΠ»ΡΡΠΈΠΎΠ½Π½ΠΎΠ΅ Π²ΡΠ΅ΠΌΡ.
β
ΠΠ΄Π½Π°ΠΊΠΎ Π² ΡΠ²ΡΠ·ΠΈ ΡΡΠ΅ΠΌ, ΡΡΠΎ ΡΠ²ΠΎΠ±ΠΎΠ΄Π½Π°Ρ ΠΊΠΎΠ²ΠΊΠ° ΡΠ²ΡΠ·Π°Π½Π° Π½Π΅ ΡΠΎΠ»ΡΠΊΠΎ Ρ Π±ΠΎΠ»ΡΡΠΎΠΉ Π·Π°ΡΡΠ°ΡΠΎΠΉ ΠΌΠ°ΡΠ΅ΡΠΈΠ°Π»ΠΎΠ², Π½ΠΎ ΠΈ Ρ Π±ΠΎΠ»ΡΡΠΎΠΉ ΡΡΡΠ΄ΠΎΠ΅ΠΌΠΊΠΎΡΡΡΡ ΠΌΠ΅Ρ Π°Π½ΠΈΡΠ΅ΡΠΊΠΎΠΉ ΠΎΠ±ΡΠ°Π±ΠΎΡΠΊΠΈ Π·Π°Π³ΠΎΡΠΎΠ²ΠΎΠΊ, ΠΎΡΠ½ΠΎΠ²Π½Π°Ρ Π·Π°Π΄Π°ΡΠ° ΡΠ΅Ρ Π½ΠΎΠ»ΠΎΠ³ΠΎΠ² Π² ΡΡΠ»ΠΎΠ²ΠΈΡΡ ΠΌΠ΅Π»ΠΊΠΎΡΠ΅ΡΠΈΠΉΠ½ΠΎΠ³ΠΎ ΠΏΡΠΎΠΈΠ·Π²ΠΎΠ΄ΡΡΠ²Π° ΡΠΎΡΡΠΎΡΠ»Π° Π² ΡΠΎΠΌ, ΡΡΠΎΠ±Ρ ΡΠ΄Π΅Π»Π°ΡΡ ΡΠΊΠΎΠ½ΠΎΠΌΠΈΡΠ΅ΡΠΊΠΈ ΡΠ΅Π»Π΅ΡΠΎΠΎΠ±ΡΠ°Π·Π½ΡΠΌ ΠΏΡΠΈΠΌΠ΅Π½Π΅Π½ΠΈΠ΅ ΡΡΠ°ΠΌΠΏΠΎΠ²ΠΎΠΉ ΠΎΡΠ½Π°ΡΡΠΊΠΈ ΠΈ ΠΏΡΠΈ ΠΌΠ΅Π»ΠΊΠΈΡ ΡΠ΅ΡΠΈΡΡ . ΠΡΠΎ ΠΏΠΎΠ²Π»Π΅ΠΊΠ»ΠΎ Π·Π° ΡΠΎΠ±ΠΎΠΉ Π½Π΅ΠΎΠ±Ρ ΠΎΠ΄ΠΈΠΌΠΎΡΡΡ ΠΏΡΠ΅Π΄ΡΡΠ²Π»Π΅Π½ΠΈΡ ΠΊ ΠΊΠΎΠ½ΡΡΡΡΠΊΡΠΈΠΈ ΡΡΠ°ΠΌΠΏΠΎΠ²ΠΎΠΉ ΠΎΡΠ½Π°ΡΡΠΊΠΈ Π½ΠΎΠ²ΡΡ , Π΄ΠΎΠΏΠΎΠ»Π½ΠΈΡΠ΅Π»ΡΠ½ΡΡ ΡΡΠ΅Π±ΠΎΠ²Π°Π½ΠΈΠΉ. β[c.268]
Π₯ΠΎΡΡ ΠΠ ΠΌΠ΅ΡΠ΅ ΡΠ°Π·Π²ΠΈΡΠΈΡ ΡΠ°Π·Π»ΠΈΡΠ½ΡΡ
ΡΠΏΠΎΡΠΎΠ±ΠΎΠ² Π³ΠΎΡΡΡΠ΅ΠΉ ΡΡΠ°ΠΌΠΏΠΎΠ²ΠΊΠΈ ΡΠΏΠΎΡΠΎΠ± ΡΠ²ΠΎΠ±ΠΎΠ΄Π½ΠΎΠΉ ΠΊΠΎΠ²ΠΊΠΈ ΠΏΠΎΡΡΠ΅ΠΏΠ΅Π½Π½ΠΎ ΡΡΠ°Π½ΠΎΠ²ΠΈΡΡΡ ΡΠΎΠ»ΡΠΊΠΎ Π²ΡΠΏΠΎΠΌΠΎΠ³Π°ΡΠ΅Π»ΡΠ½ΡΠΌ, ΡΠ»ΡΠΆΠ°ΡΠΈΠΌ Π΄Π»Ρ Π²ΡΠΏΠΎΠ»Π½Π΅Π½ΠΈΡ Π·Π°Π³ΠΎΡΠΎΠ²ΠΈΡΠ΅Π»ΡΠ½ΡΡ
ΠΎΠΏΠ΅ΡΠ°ΡΠΈΠΉ, Π½Π΅ΠΎΠ±Ρ
ΠΎΠ΄ΠΈΠΌΠΎ Π²ΡΠ΅ ΠΆΠ΅ ΠΎΡΠΌΠ΅ΡΠΈΡΡ, ΡΡΠΎ Π·Π°ΠΌΠ΅Π½Π° ΡΠ²ΠΎΠ±ΠΎΠ΄Π½ΠΎΠΉ ΠΊΠΎΠ²ΠΊΠΈ ΡΡΠ°ΠΌΠΏΠΎΠ²ΠΊΠΎΠΉ Π²ΡΠ΅ Π΅ΡΠ΅ ΡΠ²Π»ΡΠ΅ΡΡΡ ΠΎΠ΄Π½ΠΎΠΉ ΠΈΠ· Π²Π°ΠΆΠ½Π΅ΠΉΡΠΈΡ
Π·Π°Π΄Π°Ρ ΠΏΡΠΎΠ³ΡΠ΅ΡΡΠΈΠ²Π½ΠΎΠΉ ΡΠ΅Ρ
Π½ΠΎΠ»ΠΎΠ³ΠΈΠΈ ΠΊΡΠ·Π½Π΅ΡΠ½ΠΎ-ΠΏΡΠ΅ΡΡΠΎΠ²ΠΎΠΉ ΠΎΠ±ΡΠ°Π±ΠΎΡΠΊΠΈ.
ΠΠ»Π°Π²Π° II. Π’Π΅Ρ Π½ΠΎΠ»ΠΎΠ³ΠΈΡ ΠΊΡΠ·Π½Π΅ΡΠ½ΠΎ-ΡΡΠ°ΠΌΠΏΠΎΠ²ΠΎΡΠ½ΠΎΠ³ΠΎ ΠΏΡΠΎΠΈΠ·Π²ΠΎΠ΄ΡΡΠ²Π° ΠΎΡ Π²Π°ΡΡΠ²Π°Π΅Ρ ΠΊΠ°ΠΊ ΠΎΠ±ΡΠΈΠ΅ ΡΠ΅ΠΎΡΠ΅ΡΠΈΡΠ΅ΡΠΊΠΈΠ΅ ΠΎΡΠ½ΠΎΠ²Ρ ΠΊΠΎΠ²ΠΊΠΈ-ΡΡΠ°ΠΌΠΏΠΎΠ²ΠΊΠΈ, ΡΠ°ΠΊ ΠΈ ΠΏΡΠ°ΠΊΡΠΈΠΊΡ ΡΠ²ΠΎΠ±ΠΎΠ΄Π½ΠΎΠΉ ΠΊΠΎΠ²ΠΊΠΈ ΠΈ ΡΡΠ°ΠΌΠΏΠΎΠ²ΠΊΠΈ Π½Π° ΡΠ°Π·Π»ΠΈΡΠ½ΡΡ ΠΌΠ°ΡΠΈΠ½Π°Ρ -ΠΎΡΡΠ΄ΠΈΡΡ . β[c.558]
ΠΠΏΡΠ΅Π΄Π΅Π»ΡΡΡΠ΅Π΅ Π²Π»ΠΈΡΠ½ΠΈΠ΅ Π½Π° ΡΡΡΡΠΊΡΡΡΡ ΠΈ ΡΠ²ΠΎΠΉΡΡΠ²Π° ΠΊΠΎΠ²ΠΊΠΎΠ³ΠΎ ΡΡΠ³ΡΠ½Π° ΠΎΠΊΠ°Π·ΡΠ²Π°Π΅Ρ ΠΎΡΠ½ΠΎΡΠ΅Π½ΠΈΠ΅ ΡΠΎΠ΄Π΅ΡΠΆΠ°Π½ΠΈΡ ΠΌΠ°ΡΠ³Π°Π½ΡΠ° ΠΈ ΡΠ΅ΡΡ Π² Π½Π΅ΠΌ. Π£ΡΡΠ°Π½ΠΎΠ²Π»Π΅Π½ΠΎ, ΡΡΠΎ ΠΏΡΠΈ ΠΎΡΠ½ΠΎΡΠ΅Π½ΠΈΠΈ ΠΠΏ S ΠΌΠ΅Π½ΡΡΠ΅ΠΌ 1,7 ΠΎΡΠ»ΠΈΠ²ΠΊΠΈ ΠΈΠ· Π±Π΅Π»ΠΎΠ³ΠΎ ΡΡΠ³ΡΠ½Π° Π΄Π°ΠΆΠ΅ Π² Π²Π΅ΡΡΠΌΠ° ΠΌΠ°ΡΡΠΈΠ²Π½ΡΡ
ΡΠ΅ΡΠ΅Π½ΠΈΡΡ
ΡΠ²ΠΎΠ±ΠΎΠ΄Π½Ρ ΠΎΡ Π²ΡΠ΄Π΅Π»Π΅Π½ΠΈΠΉ ΠΏΠ΅ΡΠ²ΠΈΡΠ½ΠΎΠ³ΠΎ Π³ΡΠ°ΡΠΈΡΠ°. Π‘ΠΊΠΎΡΠΎΡΡΡ ΡΠ°ΡΠΏΠ°Π΄Π° ΡΠ²ΡΠ΅ΠΊΡΠΈΡΠ΅ΡΠΊΠΈΡ
ΠΊΠ°ΡΠ±ΠΈΠ΄ΠΎΠ² Π½Π° ΠΏΠ΅ΡΠ²ΠΎΠΉ ΡΡΠ°Π΄ΠΈΠΈ ΠΎΡΠΆΠΈΠ³Π° ΠΎΡ ΠΎΡΠ½ΠΎΡΠ΅Π½ΠΈΡ ΠΌΠ°ΡΠ³Π°Π½ΡΠ° ΠΊ ΡΠ΅ΡΠ΅ Π·Π°Π²ΠΈΡΠΈΡ Π½Π΅Π·Π½Π°ΡΠΈΡΠ΅Π»ΡΠ½ΠΎ. ΠΡΠΈ ΠΎΡΠ½ΠΎΡΠ΅Π½ΠΈΠΈ ΠΠΏ S = 0,8β1,2 ΠΏΠ΅ΡΠ»ΠΈΡΠ½Π°Ρ ΡΡΡΡΠΊΡΡΡΠ° ΡΠΎΡ
ΡΠ°Π½ΡΠ΅ΡΡΡ Π½Π΅Π·Π°Π²ΠΈΡΠΈΠΌΠΎ ΠΎΡ Π΄Π»ΠΈΡΠ΅Π»ΡΠ½ΠΎΡΡΠΈ Π²ΡΠΎΡΠΎΠΉ ΡΡΠ°Π΄ΠΈΠΈ Π³ΡΠ°ΡΠΈΡΠΈΠ·Π°ΡΠΈΠΈ, Π° ΡΠΎΡΠΌΠ° ΡΠ³Π»Π΅ΡΠΎΠ΄Π° ΠΎΡΠΆΠΈΠ³Π° ΠΏΠΎΠ»ΡΡΠ°Π΅ΡΡΡ ΡΠ°ΡΠΎΠ²ΠΈΠ΄Π½ΠΎΠΉ. Π‘ ΠΏΠΎΠ²ΡΡΠ΅Π½ΠΈΠ΅ΠΌ ΠΎΡΠ½ΠΎΡΠ΅Π½ΠΈΡ ΠΠΏ S Π½Π°Π±Π»ΡΠ΄Π°Π΅ΡΡΡ ΠΏΠ΅ΡΠ΅Ρ
ΠΎΠ΄ ΠΊ ΠΏΠ΅ΡΠ»ΠΈΡΠΎ-ΡΠ΅ΡΡΠΈΡΠ½ΠΎΠΉ ΠΈ ΡΠ΅ΡΡΠΈΡΠ½ΠΎΠΉ ΡΡΡΡΠΊΡΡΡΠ΅ ΠΌΠ΅ΡΠ°Π»Π»ΠΈΡΠ΅ΡΠΊΠΎΠΉ ΠΎΡΠ½ΠΎΠ²Ρ ΠΈ ΡΠΌΠ΅Π½ΡΡΠ΅Π½ΠΈΠ΅ ΠΊΠΎΠΌΠΏΠ°ΠΊΡΠ½ΠΎΡΡΠΈ Π²ΡΠ΄Π΅Π»Π΅Π½ΠΈΠΉ ΡΠ³Π»Π΅ΡΠΎΠ΄Π° ΠΎΡΠΆΠΈΠ³Π°. ΠΠ·ΠΌΠ΅Π½Π΅Π½ΠΈΠ΅ ΠΎΡΠ½ΠΎΡΠ΅Π½ΠΈΡ ΠΠΏ S ΠΎΡ 1,0 Π΄ΠΎ 3,0 ΠΏΠΎΠ·Π²ΠΎΠ»ΡΠ΅Ρ ΠΏΠΎΠ»ΡΡΠΈΡΡ Π²ΡΡ Π³Π°ΠΌΠΌΡ ΡΡΡΡΠΊΡΡΡ (ΠΎΡ ΠΏΠ΅ΡΠ»ΠΈΡΠ½ΠΎΠΉ Π΄ΠΎ ΡΠ΅ΡΡΠΈΡΠ½ΠΎΠΉ) ΠΈ ΠΌΠ΅Ρ
Π°Π½ΠΈΡΠ΅ΡΠΊΠΈΡ
ΡΠ²ΠΎΠΉΡΡΠ² ΠΊΠΎΠ²ΠΊΠΎΠ³ΠΎ ΡΡΠ³ΡΠ½Π° ΠΏΠΎ ΠΠΠ‘Π’Ρ 1215β59, Π±Π΅Π· ΠΈΠ·ΠΌΠ΅Π½Π΅Π½ΠΈΡ ΡΠΎΠ΄Π΅ΡΠΆΠ°Π½ΠΈΡ Π΄ΡΡΠ³ΠΈΡ
Ρ
ΠΈΠΌΠΈΡΠ΅ΡΠΊΠΈΡ
ΡΠ»Π΅ΠΌΠ΅Π½ΡΠΎΠ² ΠΈ ΡΠ΅Ρ
Π½ΠΎΠ»ΠΎΠ³ΠΈΠΈ ΠΏΡΠΎΠΈΠ·Π²ΠΎΠ΄ΡΡΠ²Π°.
Π 1928 Π³. ΠΠΠ’Π£ ΡΠΆΠ΅ Π³ΠΎΡΠΎΠ²ΠΈΠ»ΠΎ ΡΠΏΠ΅ΡΠΈΠ°Π»ΠΈΡΡΠΎΠ² Π½ΠΎΠ²ΠΎΠ³ΠΎ ΠΏΡΠΎΡΠΈΠ»Ρ Π»ΠΈΡΠ΅ΠΉΡΠΈΠΊΠΎΠ², ΠΊΡΠ·Π½Π΅ΡΠΎΠ², ΠΏΡΠΎΠΊΠ°ΡΡΠΈΠΊΠΎΠ², ΡΠ΅ΡΠΌΠΈΡΡΠΎΠ², ΡΠΏΠ΅ΡΠΈΠ°Π»ΠΈΡΡΠΎΠ² ΠΏΠΎ ΠΎΠ±ΡΠ°Π±ΠΎΡΠΊΠ΅ ΡΠ΅Π·Π°Π½ΠΈΠ΅ΠΌ, ΡΡΠΎΠ»Ρ Π½Π΅ΠΎΠ±Ρ ΠΎΠ΄ΠΈΠΌΡΡ Π΄Π»Ρ ΡΡΡΠΎΡΡΠΈΡ ΡΡ Π·Π°Π²ΠΎΠ΄ΠΎΠ² ΠΈ ΡΠ°Π±ΡΠΈΠΊ. ΠΡΠΊΠΎΡΠ΅ ΡΠ°ΠΊΠΎΠ³ΠΎ ΡΠΎΠ΄Π° ΡΠΏΠ΅ΡΠΈΠ°Π»ΠΈΡΡΠΎΠ² ΡΡΠ°Π»Π° Π²ΡΠΏΡΡΠΊΠ°ΡΡ ΠΠΎΡΠΊΠΎΠ²ΡΠΊΠ°Ρ Π³ΠΎΡΠ½Π°Ρ Π°ΠΊΠ°Π΄Π΅ΠΌΠΈΡ. Π ΡΠ΅ Π³ΠΎΠ΄Ρ ΠΊΡΠ·Π½Π΅ΡΠ½ΠΎΠ΅ ΠΏΡΠΎΠΈΠ·Π²ΠΎΠ΄ΡΡΠ²ΠΎ ΠΏΡΠ΅Π΄ΡΡΠ°Π²Π»ΡΠ»ΠΎ Π² ΠΎΡΠ½ΠΎΠ²Π½ΠΎΠΌ ΡΠ²ΠΎΠ±ΠΎΠ΄Π½ΡΡ ΠΊΠΎΠ²ΠΊΡ. ΠΠΎΡΡΡΠ°Ρ ΡΡΠ°ΠΌΠΏΠΎΠ²ΠΊΠ° Π² ΠΌΠ½ΠΎΠ³ΠΎΡΡΡΡΠ΅Π²ΡΡ ΡΡΠ°ΠΌΠΏΠ°Ρ , ΠΊΠΎΡΠΎΡΠ°Ρ Π² Π½Π°ΡΡΠΎΡΡΠ΅Π΅ Π²ΡΠ΅ΠΌΡ ΡΠΈΡΠΎΠΊΠΎ ΡΠ°ΡΠΏΡΠΎΡΡΡΠ°Π½Π΅Π½Π° Π½Π° Π·Π°Π²ΠΎΠ΄Π°Ρ , ΡΠΎΠ³Π΄Π° ΠΏΡΠΈΠΌΠ΅Π½ΡΠ»Π°ΡΡ ΠΌΠ°Π»ΠΎ. ΠΡΠ°Π²Π΄Π°, ΠΈΠΌΠ΅Π»Π° ΠΌΠ΅ΡΡΠΎ ΡΡΠ°ΠΌΠΏΠΎΠ²ΠΊΠ° Π² ΠΏΠΎΠ΄ΠΊΠ»Π°Π΄Π½ΡΡ ΡΡΠ°ΠΌΠΏΠ°Ρ , ΠΏΠΎ ΠΎΠΏΡΡΠ° ΠΏΠΎ ΡΠ΅Ρ Π½ΠΎΠ»ΠΎΠ³ΠΈΠΈ Π³ΠΎΡΡΡΠ΅ΠΉ ΠΈ Ρ ΠΎΠ»ΠΎΠ΄Π½ΠΎΠΉ ΡΡΠ°ΠΌΠΏΠΎΠ²ΠΊΠΈ Π½Π΅ Π±ΡΠ»ΠΎ. ΠΡΠ·Π½Π΅ΡΠ½ΠΎΠ΅ ΠΎΠ±ΠΎΡΡΠ΄ΠΎΠ²Π°Π½ΠΈΠ΅, Π·Π° ΠΈΡΠΊΠ»ΡΡΠ΅Π½ΠΈΠ΅ΠΌ ΠΏΡΠΈ- β
Π’Π΅Ρ
Π½ΠΎΠ»ΠΎΠ³ΠΈΡΠ΅ΡΠΊΠΈΠ΅ ΠΎΡΠ½ΠΎΠ²Ρ ΠΊΠΎΠ½ΡΡΡΡΠΈΡΠΎΠ²Π°Π½ΠΈΡ Π΄Π΅ΡΠ°Π»Π΅ΠΉ, ΠΈΠ·Π³ΠΎΡΠΎΠ²Π»ΡΠ΅ΠΌΡΡ
ΡΠ²ΠΎΠ±ΠΎΠ΄Π½ΠΎΠΉ ΠΊΠΎΠ²ΠΊΠΎΠΉ. ΠΠΎΠ½ΡΡΡΡΠΊΡΠΈΡ Π΄Π΅ΡΠ°Π»ΠΈ, ΠΏΠΎΠ»ΡΡΠ°Π΅ΠΌΠΎΠΉ ΠΈΠ· ΠΏΠΎΠΊΠΎΠ²ΠΊΠΈ, ΠΈΠ·Π³ΠΎΡΠΎΠ²Π»Π΅Π½Π½ΠΎΠΉ ΡΠ²ΠΎΠ±ΠΎΠ΄Π½ΠΎΠΉ ΠΊΠΎΠ²ΠΊΠΎΠΉ, Π΄ΠΎΠ»ΠΆΠ½Π° Π±ΡΡΡ ΡΠΎΠ³Π»Π°ΡΠΎΠ²Π°Π½Π° Ρ ΡΠ΅Ρ
Π½ΠΎΠ»ΠΎΠ³ΠΎΠΌ Π² ΡΠ΅Π»ΡΡ
ΠΎΠ±Π΅ΡΠΏΠ΅ΡΠ΅Π½ΠΈΡ ΠΌΠ°ΠΊΡΠΈΠΌΠ°Π»ΡΠ½ΡΡ
ΠΌΠ΅Ρ
Π°Π½ΠΈΡΠ΅ΡΠΊΠΈΡ
ΠΊΠ°ΡΠ΅ΡΡΠ², ΠΌΠΈΠ½ΠΈΠΌΠ°Π»ΡΠ½ΡΡ
ΠΎΡΡ
ΠΎΠ΄ΠΎΠ² ΠΈ ΡΡΡΠ΄ΠΎΠ΅ΠΌΠΊΠΎΡΡΠΈ ΠΊΠ°ΠΊ Π² ΠΏΡΠΎΡΠ΅ΡΡΠ΅ ΠΊΠΎΠ²ΠΊΠΈ, ΡΠ°ΠΊ ΠΈ Π² ΠΏΡΠΎΡΠ΅ΡΡΠ΅ ΠΏΠΎΡΠ»Π΅Π΄ΡΡΡΠ΅ΠΉ ΠΌΠ΅Ρ
Π°Π½ΠΈΡΠ΅ΡΠΊΠΎΠΉ ΠΎΠ±ΡΠ°Π±ΠΎΡΠΊΠΈ.
ΠΠΎΠ²ΠΊΠ° Ρ ΠΏΡΠΈΠΌΠ΅Π½Π΅Π½ΠΈΠ΅ΠΌ ΠΏΠΎΠ΄ΠΊΠ»Π°Π΄Π½ΠΎΠ³ΠΎ ΡΡΠ°ΠΌΠΏΠ° β Π’Π΅Ρ Π½ΠΎΠ»ΠΎΠ³ΠΈΡ β ΠΡΠΈΠΌΠ΅ΡΡ 64 —ΡΠ²ΠΎΠ±ΠΎΠ΄Π½Π°Ρ β ΠΠΏΠ΅ΡΠ°ΡΠΈΠΈ β Π’Π΅Ρ Π½ΠΎΠ»ΠΎΠ³ΠΈΡ 61 β[c.442]
Π€ΠΎΡΠΌΠ° Π·Π°Π³ΠΎΡΠΎΠ²ΠΊΠΈ, ΠΏΠΎΠ»ΡΡΠ΅Π½Π½ΠΎΠΉ ΡΠ²ΠΎΠ±ΠΎΠ΄Π½ΠΎΠΉ ΠΊΠΎΠ²ΠΊΠΎΠΉ, ΠΎΠ±ΡΡΠ½ΠΎ Π·Π½Π°ΡΠΈΡΠ΅Π»ΡΠ½ΠΎ ΠΎΡΠ»ΠΈΡΠ°Π΅ΡΡΡ ΠΎΡ ΡΠΎΡΠΌΡ ΠΈ ΡΠ°Π·ΠΌΠ΅ΡΠΎΠ² Π΄Π΅ΡΠ°Π»ΠΈ. Π’Π΅Ρ Π½ΠΎΠ»ΠΎΠ³ΠΈΡ ΠΊΠΎΠ²ΠΊΠΈ ΡΡΠ΅Π±ΡΠ΅Ρ ΠΈΡΠΏΠΎΠ»ΡΠ·ΠΎΠ²Π°Π½ΠΈΡ ΠΏΡΠΎΡΡΡΡ , ΠΏΠ»Π°Π²Π½ΡΡ , ΠΏΠΎ Π²ΠΎΠ·ΠΌΠΎΠΆΠ½ΠΎΡΡΠΈ ΡΠΈΠΌΠΌΠ΅ΡΡΠΈΡΠ½ΡΡ ΡΠΎΡΠΌ. ΠΠΎΠ²Π΅ΡΡ Π½ΠΎΡΡΠΈ ΠΏΠΎΠΊΠΎΠ²ΠΎΠΊ Π½Π΅ΡΡΡ Π½Π° ΡΠ΅Π±Π΅ ΡΠ»Π΅Π΄Ρ ΠΊΠΎΠ²ΠΎΡΠ½ΡΡ ΡΠ΄Π°ΡΠΎΠ² ΠΈ ΠΌΠ΅ΡΡΠ½ΡΡ Π²ΠΌΡΡΠΈΠ½ ΠΈ ΠΏΠΎΠΊΡΡΡΡ Π·Π½Π°ΡΠΈΡΠ΅Π»ΡΠ½ΡΠΌ ΡΠ»ΠΎΠ΅ΠΌ ΠΎΠΊΠ°Π»ΠΈΠ½Ρ. Π’ΠΎΠ»ΡΠΈΠ½Π° Π΄Π΅ΡΠ΅ΠΊΡΠ½ΠΎΠ³ΠΎ ΡΠ»ΠΎΡ Ρ ΠΊΡΡΠΏΠ½ΡΡ ΠΏΠΎΠΊΠΎΠ²ΠΎΠΊ ΠΏΡΠΈ Π½Π΅ΡΠΊΠΎΠ»ΡΠΊΠΈΡ Π½Π°Π³ΡΠ΅Π²Π°Ρ Π΄ΠΎΡΡΠΈΠ³Π°Π΅Ρ Π²Π΅Π»ΠΈΡΠΈΠ½Ρ 5β7 ΠΌΠΌ, Π° Π² Π½Π΅ΠΊΠΎΡΠΎΡΡΡ ΡΠ»ΡΡΠ°ΡΡ ΠΈ Π±ΠΎΠ»ΡΡΠ΅. β[c.101]

ΠΡΠΎΠ±ΠΎΠ΅ Π²Π½ΠΈΠΌΠ°Π½ΠΈΠ΅ ΠΎΠ±ΡΠ°ΡΠ°Π΅ΡΡΡ Π½Π° ΡΠΎΡΠ½ΠΎΡΡΡ ΠΏΠΎΠΊΠΎΠ²ΠΎΠΊ. ΠΠΎΠΊΠΎΠ²ΠΊΠ° ΠΏΠΎ ΡΠΎΡΠΌΠ΅ ΠΈ ΡΠ°Π·ΠΌΠ΅ΡΠ°ΠΌ Π΄ΠΎΠ»ΠΆΠ½Π° Π±ΡΡΡ Π±Π»ΠΈΠ·ΠΊΠΎΠΉ ΠΊ ΡΠΎΡΠΌΠ΅ ΠΈ ΡΠ°Π·ΠΌΠ΅ΡΠ°ΠΌ Π³ΠΎΡΠΎΠ²ΠΎΠΉ ΠΎΠ±ΡΠ°Π±ΠΎΡΠ°Π½Π½ΠΎΠΉ Π΄Π΅ΡΠ°Π»ΠΈ, ΡΡΠΎΠ±Ρ ΠΌΠ΅Π½ΡΡΠ΅ ΡΠ½ΠΈΠΌΠ°ΡΡ ΡΡΡΡΠΆΠΊΠΈ Π² ΠΌΠ΅Ρ
Π°Π½ΠΈΡΠ΅ΡΠΊΠΈΡ
ΡΠ΅Ρ
Π°Ρ
, Π° ΡΡΠΎ Π·Π½Π°ΡΠΈΡ, ΡΡΠΎ ΠΏΠΎΡΡΠ΅Π±ΡΠ΅ΡΡΡ ΠΌΠ΅Π½ΡΡΠ΅ ΡΡΠ°Π½ΠΊΠΎΠ², ΠΈΠ½ΡΡΡΡΠΌΠ΅Π½ΡΠΎΠ² ΠΈ ΡΠ°Π±ΠΎΡΠΈΡ
ΠΈ ΠΌΠ΅Π½ΡΡΠ΅ Π±ΡΠ΄Π΅Ρ ΠΎΡΡ
ΠΎΠ΄ΠΎΠ² ΠΌΠ΅ΡΠ°Π»Π»Π°. Π‘ΠΎΠ²ΡΠ΅ΠΌΠ΅Π½Π½Π°Ρ ΡΠ΅Ρ
Π½ΠΎΠ»ΠΎΠ³ΠΈΡ ΡΠ²ΠΎΠ±ΠΎΠ΄Π½ΠΎΠΉ ΠΊΠΎΠ²ΠΊΠΈ ΠΏΠΎΠ·Π²ΠΎΠ»ΡΠ΅Ρ ΠΏΠΎΠ»ΡΡΠ°ΡΡ ΠΎΡΠ΅Π½Ρ ΠΊΡΡΠΏΠ½ΡΠ΅ ΠΏΠΎΠΊΠΎΠ²ΠΊΠΈ Ρ ΠΌΠ°Π»ΡΠΌΠΈ ΠΏΡΠΈΠΏΡΡΠΊΠ°ΠΌΠΈ Π½Π° ΠΏΠΎΡΠ»Π΅Π΄ΡΡΡΡΡ ΠΌΠ΅Ρ
Π°Π½ΠΈΡΠ΅ΡΠΊΡΡ ΠΎΠ±ΡΠ°Π±ΠΎΡΠΊΡ ΠΈ Π΄ΠΎΠΏΡΡΠΊΠ°ΠΌΠΈ Π½Π° Π½Π΅ΡΠΎΡΠ½ΠΎΡΡΡ ΡΠ°Π·ΠΌΠ΅ΡΠΎΠ², ΡΡΠΎ Π΄ΠΎΡΡΠΈΠ³Π°Π΅ΡΡΡ ΠΏΡΠΈΠΌΠ΅Π½Π΅Π½ΠΈΠ΅ΠΌ ΠΏΠΎΠ΄ΠΊΠ»Π°Π΄Π½ΡΡ
ΡΡΠ°ΠΌΠΏΠΎΠ².
Π’Π΅Ρ Π½ΠΎΠ»ΠΎΠ³ΠΈΡ Π³ΠΎΡΡΡΠ΅ΠΉ ΡΡΠ°ΠΌΠΏΠΎΠ²ΠΊΠΈ ΡΠ°Π·ΡΠ°Π±Π°ΡΡΠ²Π°ΡΡ Π² ΡΠ΅Ρ Π½ΠΎΠ»ΠΎΠ³ΠΈΡΠ΅ΡΠΊΠΎΠΌ Π±ΡΡΠΎ ΠΊΡΠ·Π½Π΅ΡΠ½ΠΎ-ΡΡΠ°ΠΌΠΏΠΎΠ²ΠΎΡΠ½ΠΎΠ³ΠΎ ΡΠ΅Ρ Π° ΠΏΡΠΈΠΌΠ΅ΡΠ½ΠΎ ΡΠ°ΠΊ ΠΆΠ΅, ΠΊΠ°ΠΊ ΠΈ Π΄Π»Ρ ΡΠ²ΠΎΠ±ΠΎΠ΄Π½ΠΎΠΉ ΠΊΠΎΠ²ΠΊΠΈ (ΡΠΌ. ΡΡΡ. 279β282), Ρ. Π΅. ΡΠΎΡΡΠ°Π²Π»ΡΡΡ β[c.336]
Π Π·Π°Π΄Π°ΡΠ°Ρ
ΡΠ΅Ρ
Π½ΠΎΠ»ΠΎΠ³ΠΈΠΈ ΠΎΠ±ΡΠ°Π±ΠΎΡΠΊΠΈ ΠΌΠ΅ΡΠ°Π»Π»ΠΎΠ² Π΄Π°Π²Π»Π΅Π½ΠΈΠ΅ΠΌ, ΡΠ΅ΡΠ°Π΅ΠΌΡΡ
ΡΠ°Π·Π»ΠΈΡΠ½ΡΠΌΠΈ ΠΈΠ½ΠΆΠ΅Π½Π΅ΡΠ½ΡΠΌΠΈ ΠΌΠ΅ΡΠΎΠ΄Π°ΠΌΠΈ (ΡΠΌ., Π½Π°ΠΏΡΠΈΠΌΠ΅Ρ [74, 75, 76, 771), Π° ΡΠ°ΠΊΠΆΠ΅ ΠΌΠ΅ΡΠΎΠ΄Π°ΠΌ ΡΠΎΠΏΡΠΎΡΠΈΠ²Π»Π΅Π½ΠΈΡ ΠΌΠ°ΡΠ΅ΡΠΈΠ°Π»ΠΎΠ² ΠΏΠ»Π°ΡΡΠΈΡΠ΅ΡΠΊΠΎΠΌΡ Π΄Π΅ΡΠΎΡΠΌΠΈΡΠΎΠ²Π°Π½ΠΈΡ, ΠΏΡΠΈΡ
ΠΎΠ΄ΠΈΡΡΡ Π²ΡΡΡΠ΅ΡΠ°ΡΡΡΡ Ρ Π²ΠΎΠΏΡΠΎΡΠΎΠΌ ΠΎ Π²ΡΠ±ΠΎΡΠ΅ ΡΠΈΡΠ»Π° ΠΏΠ΅ΡΠ΅Ρ
ΠΎΠ΄ΠΎΠ², Ρ. Π΅. ΡΠΈΡΠ»Π° ΠΎΡΠ΄Π΅Π»ΡΠ½ΡΡ
ΠΎΠΏΠ΅ΡΠ°ΡΠΈΠΉ Π»ΡΠ±ΠΎΠ³ΠΎ Π΄Π°Π½Π½ΠΎΠ³ΠΎ ΡΠ΅Ρ
Π½ΠΎΠ»ΠΎΠ³ΠΈΡΠ΅ΡΠΊΠΎΠ³ΠΎ ΠΏΡΠΎΡΠ΅ΡΡΠ°. ΠΡΠΈ ΡΡΠΎΠΌ Π΅ΡΡΠ΅ΡΡΠ²Π΅Π½Π½ΠΎ, ΡΡΠΎ Π² ΡΠ°Π·Π»ΠΈΡΠ½ΡΡ
ΡΠ»ΡΡΠ°ΡΡ
Π½Π΅ΠΎΠ±Ρ
ΠΎΠ΄ΠΈΠΌΠΎ ΠΏΠΎΠ΄Ρ
ΠΎΠ΄ΠΈΡΡ ΠΊ ΡΠ΅ΡΠ΅Π½ΠΈΡ ΡΡΠΎΠ³ΠΎ Π²ΠΎΠΏΡΠΎΡΠ° Ρ ΡΠΎΠ²Π΅ΡΡΠ΅Π½Π½ΠΎ ΡΠ°Π·Π»ΠΈΡΠ½ΡΡ
ΡΠΎΡΠ΅ΠΊ Π·ΡΠ΅Π½ΠΈΡ. ΠΠ΅ΠΉΡΡΠ²ΠΈΡΠ΅Π»ΡΠ½ΠΎ, ΠΏΡΠ΅ΠΆΠ΄Π΅ ΡΠ΅ΠΌ ΡΠ΅ΡΠ°ΡΡ ΠΏΠΎΠ΄ΠΎΠ±Π½ΡΡ Π·Π°Π΄Π°ΡΡ, Π½Π΅ΠΎΠ±Ρ
ΠΎΠ΄ΠΈΠΌΠΎ Π²ΡΡΡΠ½ΠΈΡΡ, Π·Π°ΡΠ΅ΠΌ ΠΌΠΎΠΆΠ΅Ρ ΠΏΠΎΠ½Π°Π΄ΠΎΠ±ΠΈΡΡΡΡ ΠΏΡΠΎΠΈΠ·Π²ΠΎΠ΄ΠΈΡΡ Π΄Π°Π½Π½ΡΡ ΡΠ΅Ρ
Π½ΠΎΠ»ΠΎΠ³ΠΈΡΠ΅ΡΠΊΡΡ ΠΎΠΏΠ΅ΡΠ°ΡΠΈΡ Π½Π΅ Π·Π° ΠΎΠ΄ΠΈΠ½, Π° Π·Π° Π½Π΅ΡΠΊΠΎΠ»ΡΠΊΠΎ ΠΏΠ΅ΡΠ΅Ρ
ΠΎΠ΄ΠΎΠ². ΠΡΠ²Π΅ΡΡ Π½Π° ΡΡΠΎΡ Π²ΠΎΠΏΡΠΎΡ ΠΌΠΎΠ³ΡΡ Π±ΡΡΡ ΡΠ°Π·Π»ΠΈΡΠ½Ρ. Π ΡΡΠ΄Π΅ ΡΠ»ΡΡΠ°Π΅Π² ΠΏΡΠΈ ΠΏΡΠΎΠΈΠ·Π²ΠΎΠ΄ΡΡΠ²Π΅ ΠΈΠ·Π΄Π΅Π»ΠΈΠΉ ΡΠ»ΠΎΠΆΠ½ΠΎΠΉ ΠΊΠΎΠ½ΡΠΈΠ³ΡΡΠ°ΡΠΈΠΈ ΠΎΠΊΠ°Π·ΡΠ²Π°Π΅ΡΡΡ ΠΊΠΈΠ½Π΅ΠΌΠ°ΡΠΈΡΠ΅ΡΠΊΠΈ Π½Π΅Π²ΠΎΠ·ΠΌΠΎΠΆΠ½ΡΠΌ ΠΏΡΠΈΠ΄Π°ΡΡ Π΄Π΅ΡΠΎΡΠΌΠΈΡΡΠ΅ΠΌΠΎΠΌΡ ΠΌΠ΅ΡΠ°Π»Π»Ρ Π·Π°Π΄Π°Π½Π½ΡΡ ΡΠΎΡΠΌΡ Π·Π° ΠΎΠ΄ΠΈΠ½ ΠΏΠ΅ΡΠ΅Ρ
ΠΎΠ΄, Ρ. Π΅. Π·Π° ΠΎΠ΄ΠΈΠ½ Ρ
ΠΎΠ΄ ΠΏΠΎΠ΄Π²ΠΈΠΆΠ½ΠΎΠΉ Π΄Π΅ΡΠ°Π»ΠΈ ΡΠ°Π±ΠΎΡΠ΅Π³ΠΎ ΠΈΠ½ΡΡΡΡΠΌΠ΅Π½ΡΠ°. ΠΠ° ΠΏΡΠ°ΠΊΡΠΈΠΊΠ΅ Π² ΡΡΠΈΡ
ΡΠ»ΡΡΠ°ΡΡ
ΠΏΡΠΈΠΌΠ΅Π½ΡΠ΅ΡΡΡ ΡΠ²ΠΎΠ±ΠΎΠ΄Π½Π°Ρ ΠΊΠΎΠ²ΠΊΠ° ΠΈΠ»ΠΈ ΠΌΠ½ΠΎΠ³ΠΎΡΡΡΡΠ΅Π²Π°Ρ Π³ΠΎΡΡΡΠ°Ρ ΡΡΠ°ΠΌΠΏΠΎΠ²ΠΊΠ°.
β[c.196]
Π ΠΈΡ. 1Π£-21. ΠΠ½ΡΡΡΡΠΌΠ΅Π½Ρ, ΠΏΡΠΈΠ΅ΠΌΡ ΠΈ ΡΠ΅Ρ Π½ΠΎΠ»ΠΎΠ³ΠΈΡ ΡΠ²ΠΎΠ±ΠΎΠ΄Π½ΠΎΠΉ ΠΊΠΎΠ²ΠΊΠΈ |
ΠΠ½ΠΈΠ³Π° ΡΠΎΡΡΠ°Π²Π»Π΅Π½Π° ΠΏΡΠΈΠΌΠ΅Π½ΠΈΡΠ΅Π»ΡΠ½ΠΎ ΠΊ ΠΏΡΠΎΠ³ΡΠ°ΠΌΠΌΠ΅ Π’Π΅ΠΎΡΠΈΡ ΠΏΠ»Π°ΡΡΠΈΡΠ΅ΡΠΊΠΎΠΉ Π΄Π΅ΡΠΎΡΠΌΠ°ΡΠΈΠΈ ΠΈ ΠΎΠ±ΡΠ°Π±ΠΎΡΠΊΠ° ΠΌΠ΅ΡΠ°Π»Π»ΠΎΠ² Π΄Π°Π²Π»Π΅Π½ΠΈΠ΅ΠΌ , ΡΡΠ²Π΅ΡΠΆΠ΄Π΅Π½Π½ΠΎΠΉ Π΄Π»Ρ ΠΌΠ°ΡΠΈΠ½ΠΎΡΡΡΠΎΠΈΡΠ΅Π»ΡΠ½ΡΡ
ΡΠ΅Ρ
Π½ΠΈΠΊΡΠΌΠΎΠ² ΠΏΠΎ ΡΠΏΠ΅ΡΠΈΠ°Π»ΡΠ½ΠΎΡΡΠΈ ΠΠ΅ΡΠ°Π»Π»ΡΡΠ³ΠΈΡΠ΅ΡΠΊΠΎΠ΅ ΠΌΠ°ΡΠΈΠ½ΠΎΡΡΡΠΎΠ΅Π½ΠΈΠ΅ ΠΈ ΠΡΠΎΠΈΠ·Π²ΠΎΠ΄ΡΡΠ²ΠΎ ΠΏΡΠΎΠΊΠ°ΡΠ½ΠΎΠ³ΠΎ ΠΎΠ±ΠΎΡΡΠ΄ΠΎΠ²Π°Π½ΠΈΡ . Π Π½Π΅ΠΉ ΠΈΠ·Π»ΠΎΠΆΠ΅Π½Π° ΡΠ΅ΠΎΡΠΈΡ ΠΏΠ»Π°ΡΡΠΈΡΠ΅ΡΠΊΠΎΠΉ Π΄Π΅- ΡΠΌΠ°ΡΠΈΠΈ ΠΌΠ΅ΡΠ°Π»Π»ΠΎΠ², ΠΎΠΏΠΈΡΠ°Π½Ρ ΡΠ΅ΠΎΡΠ΅ΡΠΈΡΠ΅ΡΠΊΠΈΠ΅ ΠΎΡΠ½ΠΎΠ²Ρ ΠΏΡΠΎΠΊΠ°ΡΠΊΠΈ ΠΈ ΡΠ»Π΅ΠΌΠ΅Π½ΡΡ ΡΠ΅ΠΎΡΠΈΠΈ Π΄ΡΡΠ³ΠΈΡ
Π²ΠΈΠ΄ΠΎΠ² ΠΎΠ±ΡΠ°Π±ΠΎΡΠΊΠΈ ΠΌΠ΅ΡΠ°Π»Π»ΠΎΠ² Π΄Π°Π²Π»Π΅Π½ΠΈΠ΅ΠΌ. ΠΡΠΈΠ²ΠΎΠ΄ΠΈΡΡΡ ΡΠ΅Ρ
Π½ΠΎΠ»ΠΎΠ³ΠΈΡ ΠΏΡΠΎΠΊΠ°ΡΠΊΠΈ ΠΈ ΠΊΠ°Π»ΠΈΠ±ΡΠΎΠ²ΠΊΠΈ Π²Π°Π»ΠΊΠΎΠ², Π΄Π°Π½ΠΎ ΠΊΡΠ°ΡΠΊΠΎΠ΅ ΠΎΠΏΠΈΡΠ°Π½ΠΈΠ΅ ΠΏΡΠΎΡΠ΅ΡΡΠΎΠ² ΠΏΡΠ΅ΡΡΠΎΠ²Π°Π½ΠΈΡ, Π²ΠΎΠ»ΠΎΡΠ΅Π½ΠΈΡ, ΡΠ²ΠΎΠ±ΠΎΠ΄Π½ΠΎΠΉ ΠΊΠΎΠ²ΠΊΠΈ, Π³ΠΎΡΡΡΠ΅ΠΉ ΠΈ Ρ
ΠΎΠ»ΠΎΠ΄Π½ΠΎΠΉ ΡΡΠ°ΠΌΠΏΠΎΠ²ΠΊΠΈ.
β[c.2]
Π’Π°ΠΊΠΈΠΌ ΠΎΠ±ΡΠ°Π·ΠΎΠΌ, ΡΠ°Π·ΡΠ°Π±ΠΎΡΠΊΠ° ΡΠ΅Ρ Π½ΠΎΠ»ΠΎΠ³ΠΈΡΠ΅ΡΠΊΠΎΠ³ΠΎ ΠΏΡΠΎΡΠ΅ΡΡΠ° ΡΠ²ΠΎΠ±ΠΎΠ΄Π½ΠΎΠΉ ΠΊΠΎΠ²ΠΊΠΈ Π²ΠΊΠ»ΡΡΠ°Π΅Ρ ΡΠΎΡΡΠ°Π²Π»Π΅Π½ΠΈΠ΅ ΡΠ΅ΡΡΠ΅ΠΆΠ° ΠΏΠΎΠΊΠΎΠ²ΠΊΠΈ Ρ Π½Π°Π·Π½Π°ΡΠ΅Π½ΠΈΠ΅ΠΌ ΠΏΡΠΈΠΏΡΡΠΊΠΎΠ², Π΄ΠΎΠΏΡΡΠΊΠΎΠ² ΠΈ Π½Π°ΠΏΡΡΠΊΠΎΠ² ΠΎΠΏΡΠ΅Π΄Π΅Π»Π΅Π½ΠΈΠ΅ Π²Π΅ΡΠ° ΠΈ ΡΠ°Π·ΠΌΠ΅ΡΠΎΠ² Π·Π°Π³ΠΎΡΠΎΠ²ΠΊΠΈ Π²ΡΠ±ΠΎΡ ΠΊΡΠ·Π½Π΅ΡΠ½ΡΡ ΠΎΠΏΠ΅ΡΠ°ΡΠΈΠΉ ΠΈ Π½Π΅ΠΎΠ±Ρ ΠΎΠ΄ΠΈΠΌΠΎΠ³ΠΎ ΠΈΠ½ΡΡΡΡΠΌΠ΅Π½ΡΠ° Π²ΡΠ±ΠΎΡ ΠΌΠ°ΡΠΈΠ½Π½ΠΎΠ³ΠΎ ΠΎΠ±ΠΎΡΡΠ΄ΠΎΠ²Π°Π½ΠΈΡ. ΠΡΠΎΠΌΠ΅ ΡΡΠΎΠ³ΠΎ, ΡΠ΅Ρ Π½ΠΎΠ»ΠΎΠ³ΠΈΠ΅ΠΉ ΠΏΡΠ΅Π΄ΡΡΠΌΠ°ΡΡΠΈΠ²Π°Π΅ΡΡΡ ΠΎΠΏΡΠ΅Π΄Π΅Π»Π΅Π½ΠΈΠ΅ ΡΠ΅ΠΆΠΈΠΌΠ° Π½Π°Π³ΡΠ΅Π²Π° Π·Π°Π³ΠΎΡΠΎΠ²ΠΊΠΈ, ΡΠΈΠΏΠ° ΠΈ ΡΠ°Π·ΠΌΠ΅ΡΠΎΠ² Π½Π°Π³ΡΠ΅Π²Π°ΡΠ΅Π»ΡΠ½ΡΡ ΡΡΡΡΠΎΠΉΡΡΠ², Π° ΡΠ°ΠΊΠΆΠ΅ ΡΠΎΡΡΠ°Π²Π° ΡΠ°Π±ΠΎΡΠ΅ΠΉ ΡΠΈΠ»Ρ ΠΈ Π½ΠΎΡΠΌ Π²ΡΡΠ°Π±ΠΎΡΠΊΠΈ. Π Π΅Π·ΡΠ»ΡΡΠ°ΡΡ ΡΠ°Π·ΡΠ°Π±ΠΎΡΠΊΠΈ ΡΠ΅Ρ Π½ΠΎΠ»ΠΎΠ³ΠΈΡΠ΅ΡΠΊΠΎΠ³ΠΎ ΠΏΡΠΎΡΠ΅ΡΡΠ° ΠΊΠΎΠ²ΠΊΠΈ ΡΠΈΠΊΡΠΈΡΡΡΡΡΡ Π² ΡΠ΅Ρ Π½ΠΎΠ»ΠΎΠ³ΠΈΡΠ΅ΡΠΊΠΎΠΉ ΠΊΠ°ΡΡΠ΅. β[c.569]
Π§ΡΠΎ ΠΊΠ°ΡΠ°Π΅ΡΡΡ ΠΈΠ·Π³ΠΎΡΠΎΠ²Π»Π΅Π½ΠΈΡ Π΄ΡΡΠ³ΠΈΡ
Π΄Π΅ΡΠ°Π»Π΅ΠΉ, ΡΠΎ Π·Π΄Π΅ΡΡ ΡΠΊΠ°Π·ΡΠ²Π°ΡΡΡΡ ΠΎΡΠΎΠ±Π΅Π½Π½ΠΎΡΡΠΈ ΠΌΠ΅Π»ΠΊΠΎΡΠ΅ΡΠΈΠΉΠ½ΠΎΠΉ ΡΠ΅Ρ
Π½ΠΎΠ»ΠΎΠ³ΠΈΠΈ. Π ΠΊΠ°ΡΠ΅ΡΡΠ²Π΅ Π·Π°Π³ΠΎΡΠΎΠ²ΠΎΠΊ ΠΌΠ°ΠΊΡΠΈΠΌΠ°Π»ΡΠ½ΠΎ ΠΈΡΠΏΠΎΠ»ΡΠ·ΡΠ΅ΡΡΡ ΡΠΎΡΡΠΎΠ²ΠΎΠΉ ΠΏΡΠΎΠΊΠ°Ρ. Π¨ΡΠ°ΠΌΠΏΠΎΠ²ΠΊΠΈ,- ΠΊΠ°ΠΊ ΠΏΡΠ°Π²ΠΈΠ»ΠΎ, Π·Π°ΠΌΠ΅Π½ΡΡΡΡΡ Π·Π°Π³ΠΎΡΠΎΠ²ΠΊΠ°ΠΌΠΈ, ΠΏΠΎΠ»ΡΡΠ°Π΅ΠΌΡΠΌΠΈ ΡΠ²ΠΎΠ±ΠΎΠ΄Π½ΠΎΠΉ ΠΊΠΎΠ²ΠΊΠΎΠΉ. ΠΡΡΡΠ΄Π° ΠΏΠΎΠ²ΡΡΠ΅Π½Π½ΡΠ΅ ΠΏΡΠΈΠΏΡΡΠΊΠΈ Π½Π° ΠΎΠ±ΡΠ°Π±ΠΎΡΠΊΡ. ΠΠ»Ρ Π΄Π΅ΡΠ°Π»Π΅ΠΉ, ΠΈΠ·Π³ΠΎΡΠΎΠ²Π»ΡΠ΅ΠΌΡΡ
Π² Π΅Π΄ΠΈΠ½ΠΈΡΠ½ΠΎΠΌ ΠΏΠΎΡΡΠ΄ΠΊΠ΅, ΠΈΡΠΏΠΎΠ»ΡΠ·ΡΡΡΡΡ ΡΠ½ΠΈΠ²Π΅ΡΡΠ°Π»ΡΠ½ΡΠ΅ ΠΏΡΠΈΡΠΏΠΎΡΠΎΠ±Π»Π΅Π½ΠΈΡ. Π‘ΠΏΠ΅ΡΠΈΡΠΈΡΠ½ΡΠΌ Π΄Π»Ρ ΠΈΠ·Π³ΠΎΡΠΎΠ²Π»Π΅Π½ΠΈΡ Π΄Π΅ΡΠ°Π»Π΅ΠΉ ΡΠ²Π»ΡΠ΅ΡΡΡ ΠΏΡΠΈΠΌΠ΅Π½Π΅Π½ΠΈΠ΅ ΡΠ°Π·ΠΌΠ΅ΡΠΊΠΈ. Π¦Π΅Π½ΡΡΠΈΡΠΎΠ²Π°Π½ΠΈΠ΅ Π·Π°Π³ΠΎΡΠΎΠ²ΠΎΠΊ Π²ΡΠΏΠΎΠ»Π½ΡΠ΅ΡΡΡ Π½Π° ΡΠΎΠΊΠ°ΡΠ½ΡΡ
ΠΈΠ»ΠΈ ΡΠ°ΡΡΠΎΡΠ½ΡΡ
ΡΡΠ°Π½ΠΊΠ°Ρ
. ΠΡΠΈΠΌΠ΅Π½ΡΡΡΡΡ ΡΠ½ΠΈΠ²Π΅ΡΡΠ°Π»ΡΠ½ΡΠ΅ Π·Π°Π³Π»ΡΡΠΊΠΈ ΠΈ Π·Π°Π³Π»ΡΡΠΊΠΈ ΡΠ°Π·ΠΎΠ²ΠΎΠ³ΠΎ ΠΏΡΠΈΠΌΠ΅Π½Π΅Π½ΠΈΡ.,
β[c.66]
Π’ΠΠ₯ΠΠΠΠΠΠΠ― Π‘ΠΠΠΠΠΠΠΠ ΠΠΠΠΠ β[c.180]
ΠΡΠΎΠΈΠ·Π²ΠΎΠ΄ΠΈΡΠ΅Π»ΡΠ½ΠΎΡΡΡ ΠΏΡΠΈ ΡΠ²ΠΎΠ±ΠΎΠ΄Π½ΠΎΠΉ ΠΊΠΎΠ²ΠΊΠ΅, ΡΠ°ΡΡ
ΠΎΠ΄ ΠΌΠ΅ΡΠ°Π»Π»Π° ΠΈ ΠΊΠ°ΡΠ΅ΡΡΠ²ΠΎ ΠΏΠΎΠΊΠΎΠ²ΠΎΠΊ Π² Π·Π½Π°ΡΠΈΡΠ΅Π»ΡΠ½ΠΎΠΉ ΠΌΠ΅ΡΠ΅ Π·Π°Π²ΠΈΡΡΡ ΠΎΡ ΠΏΡΠΈΠΌΠ΅Π½ΡΠ΅ΠΌΠΎΠΉ ΡΠ½ΠΈΠ²Π΅ΡΡΠ°Π»ΡΠ½ΠΎΠΉ ΡΠ΅Ρ
Π½ΠΎΠ»ΠΎΠ³ΠΈΡΠ΅ΡΠΊΠΎΠΉ ΠΎΡΠ½Π°ΡΡΠΊΠΈ. ΠΠΎΠ½ΡΡΡΡΠΊΡΠΈΠΈ ΠΈ ΡΠΎΡΠΌΡ ΡΡΠΎΠΉ ΠΎΡΠ½Π°ΡΡΠΊΠΈ, ΠΏΡΠΈΠΌΠ΅Π½ΡΠ΅ΠΌΡΠ΅ Π½Π° ΡΠ°Π·Π½ΡΡ
Π·Π°Π²ΠΎΠ΄Π°Ρ
Π΄Π»Ρ ΠΎΠ΄ΠΈΠ½Π°ΠΊΠΎΠ²ΡΡ
ΡΠ°Π±ΠΎΡ, ΡΠ°Π·Π»ΠΈΡΠ½Ρ ΠΈ Π΄Π°Π»Π΅ΠΊΠΎ Π½Π΅ Π²Π΅Π·Π΄Π΅ ΡΠ²Π»ΡΡΡΡΡ ΡΠ°ΡΠΈΠΎΠ½Π°Π»ΡΠ½ΡΠΌΠΈ. ΠΠΎΡΡΠΎΠΌΡ Π΅Π΅ Π½ΠΎΡΠΌΠ°Π»ΠΈΠ·Π°ΡΠΈΡ, Π±Π΅Π·ΡΡΠ»ΠΎΠ²Π½ΠΎ, Π½Π΅ΠΎΠ±Ρ
ΠΎΠ΄ΠΈΠΌΠ°, ΠΈ Π½Π° ΡΡΠΎ Π΄ΠΎΠ»ΠΆΠ½ΠΎ Π±ΡΡΡ ΠΎΠ±ΡΠ°ΡΠ΅Π½ΠΎ Π²Π½ΠΈΠΌΠ°Π½ΠΈΠ΅. ΠΠ΄Π½Π°ΠΊΠΎ ΠΏΡΠΈ ΠΈΡΠΏΠΎΠ»ΡΠ·ΠΎΠ²Π°Π½ΠΈΠΈ ΡΠΎΠ»ΡΠΊΠΎ ΡΠ½ΠΈΠ²Π΅ΡΡΠ°Π»ΡΠ½ΠΎΠΉ ΠΎΡΠ½Π°ΡΡΠΊΠΈ Π½Π΅Π»ΡΠ·Ρ Π΄ΠΎΡΡΠΈΡΡ Π·Π°ΠΌΠ΅ΡΠ½ΠΎΠ³ΠΎ ΠΏΡΠΎΠ³ΡΠ΅ΡΡΠ° Π² ΡΠ΅Ρ
Π½ΠΎΠ»ΠΎΠ³ΠΈΠΈ ΡΠ²ΠΎΠ±ΠΎΠ΄Π½ΠΎΠΉ ΠΊΠΎΠ²ΠΊΠΈ.
β[c.111]
ΠΠ°Π»ΡΠ½Π΅ΠΉΡΠ΅Π΅ ΡΠ°Π·Π²ΠΈΡΠΈΠ΅ ΡΠ²ΠΎΠ±ΠΎΠ΄Π½ΠΎΠΉ ΠΊΠΎΠ²ΠΊΠΈ ΡΡΠ΅Π±ΡΠ΅Ρ Π½Π΅ΠΏΡΠ΅ΡΡΠ²Π½ΠΎΠ³ΠΎ ΠΊΠΎΠΌΠΏΠ»Π΅ΠΊΡΠ° ΠΈΠ·ΡΡΠ΅Π½ΠΈΡ ΠΈ ΠΎΠ±ΠΎΠ±ΡΠ΅Π½ΠΈΡ ΠΏΠ΅ΡΠ΅Π΄ΠΎΠ²ΠΎΠ³ΠΎ ΠΎΠΏΡΡΠ° Π½Π° ΠΊΠ°ΠΆΠ΄ΠΎΠΌ Π·Π°Π²ΠΎΠ΄Π΅ ΠΏΡΠΈΠΌΠ΅Π½ΠΈΡΠ΅Π»ΡΠ½ΠΎ ΠΊ ΠΊΠΎΠ½ΠΊΡΠ΅ΡΠ½ΡΠΌ ΡΡΠ»ΠΎΠ²ΠΈΡΠΌ ΠΏΡΠΎΠΈΠ·Π²ΠΎΠ΄ΡΡΠ²Π° ΠΏΠΎΠΊΠΎΠ²ΠΎΠΊ Π½Π° ΠΊΠ°ΠΆΠ΄ΠΎΠΌ ΡΠ°Π±ΠΎΡΠ΅ΠΌ ΠΌΠ΅ΡΡΠ΅. ΠΠ΅ΠΎΠ±Ρ ΠΎΠ΄ΠΈΠΌΠ° ΡΠΈΠΏΠΈΠ·Π°ΡΠΈΡ ΡΠ΅Ρ Π½ΠΎΠ»ΠΎΠ³ΠΈΡΠ΅ΡΠΊΠΈΡ ΠΏΡΠΎΡΠ΅ΡΡΠΎΠ² ΠΊΠΎΠ²ΠΊΠΈ ΠΎΠ΄ΠΈΠ½Π°ΠΊΠΎΠ²ΡΡ Π΄Π΅ΡΠ°Π»Π΅ΠΉ ΠΈ ΡΠ°Π·ΡΠ°Π±ΠΎΡΠΊΠ° ΠΌΠ΅ΠΆΠ·Π°Π²ΠΎΠ΄ΡΠΊΠΎΠΉ ΠΏΡΠΎΠ³ΡΠ΅ΡΡΠΈΠ²Π½ΠΎΠΉ ΡΠ΅Ρ Π½ΠΎΠ»ΠΎΠ³ΠΈΠΈ ΡΡΠΈ ΡΠ°Π±ΠΎΡΡ ΡΡΠΏΠ΅ΡΠ½ΠΎ Π½Π°ΡΠ°ΡΡ Π½Π° Π»Π΅Π½ΠΈΠ½Π³ΡΠ°Π΄ΡΠΊΠΈΡ Π·Π°Π²ΠΎΠ΄Π°Ρ [161. ΠΡΠ΅ ΡΡΠΎ Π΄Π°Π΅Ρ ΡΠ°ΠΊΠΆΠ΅ Π½Π°Π΄Π΅ΠΆΠ½ΡΡ ΠΎΡΠ½ΠΎΠ²Ρ Π΄Π»Ρ ΠΊΠΎΠ½ΡΡΡΡΠΈΡΠΎΠ²Π°Π½ΠΈΡ ΡΠ΅Ρ Π½ΠΎΠ»ΠΎΠ³ΠΈΡΠ΅ΡΠΊΠΈΡ ΠΏΡΠΎΡΠ΅ΡΡΠΎΠ² Π½Π° ΠΊΡΠ·Π½Π΅ΡΠ½ΡΡ Π·Π°Π²ΠΎΠ΄Π°Ρ ΠΈ ΡΠ΅Ρ Π°Ρ ΡΠ²ΠΎΠ±ΠΎΠ΄Π½ΠΎΠΉ ΠΊΠΎΠ²ΠΊΠΈ Π½ΠΎΠ²ΡΡ ΡΠΏΠ΅ΡΠΈΠ°Π»ΠΈΠ·ΠΈΡΠΎΠ²Π°Π½Π½ΡΡ ΠΏΡΠ΅Π΄ΠΏΡΠΈΡΡΠΈΠΉ. β[c.114]
ΠΠ΅ΡΠ΅Ρ
ΠΎΠ΄Ρ ΠΊ ΡΠ΅Ρ
Π½ΠΎΠ»ΠΎΠ³ΠΈΠΈ ΡΡΠ°ΠΌΠΏΠΎΠ²ΠΊΠΈ Π½Π° Π³ΠΈΠ΄ΡΠ°Π²Π»ΠΈΡΠ΅ΡΠΊΠΈΡ
ΠΏΡΠ΅ΡΡΠ°Ρ
, ΡΠ»Π΅Π΄ΡΠ΅Ρ ΠΎΡΠΌΠ΅ΡΠΈΡΡ Π·Π½Π°ΡΠΈΡΠ΅Π»ΡΠ½ΠΎΠ΅ ΡΠ°ΡΡΠΈΡΠ΅Π½ΠΈΠ΅ ΠΎΠ±Π»Π°ΡΡΠΈ Π΅Π΅ ΠΏΡΠΈΠΌΠ΅Π½Π΅Π½ΠΈΡ. ΠΠ°ΡΡΠ΄Ρ Ρ ΠΌΠ°ΡΡΠΎΠ²ΡΠΌ ΠΏΡΠΎΠΈΠ·Π²ΠΎΠ΄ΡΡΠ²ΠΎΠΌ Π½Π° Π³ΠΈΠ΄ΡΠ°Π²Π»ΠΈΡΠ΅ΡΠΊΠΈΡ
ΠΏΡΠ΅ΡΡΠ°Ρ
Π·Π°ΠΊΡΡΡΠΎΠΉ ΠΏΡΠΎΡΠΈΠ²ΠΊΠΎΠΉ ΠΈ ΠΏΡΠΎΡΡΠΆΠΊΠΎΠΉ ΠΏΡΡΡΠΎΡΠ΅Π»ΡΡ
ΠΏΠΎΠΊΠΎΠ²ΠΎΠΊ ΡΠΈΠΏΠ° ΡΡΠ°ΠΊΠ°Π½ΠΎΠ² Π² Π½Π°ΡΡΠΎΡΡΠ΅Π΅ Π²ΡΠ΅ΠΌΡ Π½Π° Π³ΠΈΠ΄ΡΠ°Π²Π»ΠΈΡΠ΅ΡΠΊΠΈΡ
ΠΏΡΠ΅ΡΡΠ°Ρ
ΡΡΠ°ΠΌΠΏΡΡΡ Π² ΠΎΡΠΊΡΡΡΡΡ
ΠΈ Π·Π°ΠΊΡΡΡΡΡ
ΡΡΠ°ΠΌΠΏΠ°Ρ
ΠΊΡΡΠΏΠ½ΡΠ΅ ΠΏΠΎΠΊΠΎΠ²ΠΊΠΈ, ΠΏΡΠΈΠΌΠ΅Π½ΡΡ ΡΠ°ΠΊΠΆΠ΅ ΠΊΠΎΠΌΠ±ΠΈΠ½ΠΈΡΠΎΠ²Π°Π½Π½ΡΠ΅ ΠΏΡΠΎΡΠ΅ΡΡΡ ΡΠ²ΠΎΠ±ΠΎΠ΄Π½ΠΎΠΉ ΠΊΠΎΠ²ΠΊΠΈ ΠΈ ΡΡΠ°ΠΌΠΏΠΎΠ²ΠΊΠΈ, Π² ΡΠ°ΡΡΠ½ΠΎΡΡΠΈ, ΡΠ΅ΠΊΡΠΈΠΎΠ½Π½ΠΎΠΉ ΡΡΠ°ΠΌΠΏΠΎΠ²ΠΊΠΈ [22].
β[c.123]
Π ΡΠ°Π·Π²ΠΈΡΠΈΠΈ ΠΈ ΡΠΎΠ²Π΅ΡΡΠ΅Π½ΡΡΠ²ΠΎΠ²Π°Π½ΠΈΠΈ ΠΊΡΠ·Π½Π΅ΡΠ½ΠΎ-ΡΡΠ°ΠΌΠΏΠΎΠ²ΠΎΡΠ½ΠΎΠ³ΠΎ ΠΏΡΠΎΠΈΠ·Π²ΠΎΠ΄ΡΡΠ²Π° Π²ΡΠ΅ Π±ΠΎΠ»ΡΡΠ΅Π΅ Π·Π½Π°ΡΠ΅Π½ΠΈΠ΅ ΠΏΡΠΈΠΎΠ±ΡΠ΅ΡΠ°Π΅Ρ ΡΠ΅Ρ Π½ΠΈΡΠ΅ΡΠΊΠ°Ρ Π»ΠΈΡΠ΅ΡΠ°ΡΡΡΠ°. Π Π½Π°ΡΡΠΎΡΡΠ΅ΠΌ ΡΠΏΡΠ°Π²ΠΎΡΠ½ΠΈΠΊΠ΅, ΠΏΠΎΠ΄Π³ΠΎΡΠΎΠ²Π»Π΅Π½Π½ΠΎΠΌ ΠΊΠΎΠ»Π»Π΅ΠΊΡΠΈΠ²ΠΎΠΌ Π°Π²ΡΠΎΡΠΎΠ² β ΡΠ°Π±ΠΎΡΠ½ΠΈΠΊΠΎΠ² Π£ΡΠ°Π»ΠΌΠ°ΡΠ·Π°Π²ΠΎΠ΄Π°, ΠΏΡΠΈΠ²ΠΎΠ΄ΡΡΡΡ ΠΎΡΠ½ΠΎΠ²Π½ΡΠ΅ ΡΠ²Π΅Π΄Π΅Π½ΠΈΡ ΠΏΠΎ ΡΠ΅Ρ Π½ΠΎΠ»ΠΎΠ³ΠΈΠΈ ΡΠ²ΠΎΠ±ΠΎΠ΄Π½ΠΎΠΉ ΠΊΠΎΠ²ΠΊΠΈ ΠΈ Π³ΠΎΡΡΡΠ΅ΠΉ ΠΎΠ±ΡΠ΅ΠΌΠ½ΠΎΠΉ ΡΡΠ°ΠΌΠΏΠΎΠ²ΠΊΠΈ ΡΠ΅ΡΠ½ΡΡ ΠΈ ΡΠ²Π΅ΡΠ½ΡΡ ΠΌΠ΅ΡΠ°Π»Π»ΠΎΠ², Π° ΡΠ°ΠΊΠΆΠ΅ ΠΎΠ±ΡΠΈΠ΅ ΡΠ΅Ρ Π½ΠΈΡΠ΅ΡΠΊΠΈΠ΅ Π΄Π°Π½Π½ΡΠ΅, Π½Π΅ΠΎΠ±Ρ ΠΎΠ΄ΠΈΠΌΡΠ΅ ΡΠ°Π±ΠΎΡΠ΅ΠΌΡ Π΄Π»Ρ ΡΠ°ΠΌΠΎΡΡΠΎΡΡΠ΅Π»ΡΠ½ΡΡ ΡΠ°ΡΡΠ΅ΡΠΎΠ². β[c.10]
ΠΠΠΠΠ 10 Π’ΠΠ₯ΠΠΠΠΠΠΠ― Π‘ΠΠΠΠΠΠΠΠ ΠΠΠΠΠ β[c.304]
Π£Π²Π΅Π»ΠΈΡΠΈΠ»Π°ΡΡ ΡΠΎΠ»ΠΏΡΠ½Π° Π»ΠΈΡΡΠΎΠ²ΠΎΠ³ΠΎ ΠΌΠ°ΡΠ΅ΡΠΈΠ°Π»Π°, ΠΏΡΠΈΠΌΠ΅Π½ΡΠ΅ΠΌΠΎΠ³ΠΎ Π΄Π»Ρ ΠΊΠΎΠ²ΠΊΠΈ ΠΈ Π³ΠΎΡΡΡΠ΅ΠΉ ΡΡΠ°ΠΌΠΏΠΎΠ²ΠΊΠΈ ΠΊΡΡΠΏΠ½ΡΡ
ΠΏΡΡΡΠΎΡΠ΅Π»ΡΡ
Π΄Π΅ΡΠ°Π»Π΅ΠΉ β Π±Π°ΡΠ°Π±Π°Π½ΠΎΠ², ΠΊΠΎΡΠ»ΠΎΠ². Π ΠΎΡΡ ΠΎΠ±ΡΠ΅ΠΌΠ° ΠΈΠ·Π³ΠΎΡΠΎΠ²Π»Π΅Π½ΠΈΡ ΡΠΎΠ½ΠΊΠΎΠ³ΠΎ Π»ΠΈΡΡΠ° Ρ
ΠΎΠ»ΠΎΠ΄Π½ΠΎΠΉ ΠΏΡΠΎΠΊΠ°ΡΠΊΠΈ ΠΏΠΎΠ²Π»ΠΈΡΠ» Π½Π° ΡΠ΅Ρ
Π½ΠΎΠ»ΠΎΠ³ΠΈΡ Ρ
ΠΎΠ»ΠΎΠ΄Π½ΠΎΠΉ Π»ΠΈΡΡΠΎΠ²ΠΎΠΉ ΡΡΠ°ΠΌΠΏΠΎΠ²ΠΊΠΈ ΠΊΡΡΠΏΠ½ΡΡ
Π°Π²ΡΠΎΠΌΠΎΠ±ΠΈΠ»ΡΠ½ΡΡ
ΠΈ Π΄ΡΡΠ³ΠΈΡ
Π΄Π΅ΡΠ°Π»Π΅ΠΉ ΠΌΠ°ΠΈΡΠ½ΠΎΡΡΡ ΡΠ΅Π½ΠΈΡ. ΠΡΠΏΡΡΠΊ ΡΠΎΠ½ΠΊΠΎΠΉ ΡΡΠ°Π»ΡΠ½ΠΎΠΉ Π»Π΅Π½ΡΡ, ΠΎΠ΄Π½Π°ΠΊΠΎ, Π΄Π°Π»Π΅ΠΊΠΎ Π½Π΅ ΡΠΎΠΎΡΠ²Π΅ΡΡΡΠ²ΠΎΠ²Π°Π» Π·Π°ΠΏΡΠΎΡΠ°ΠΌ ΡΡΠ°ΠΌΠΏΠΎΠ²ΠΎΡΠ½ΠΎΠ³ΠΎ ΠΏΡΠΎΠΈΠ·Π²ΠΎΠ΄ΡΡΠ²Π° ΠΈ ΡΠΎΡΠΌΠΎΠ·ΠΈΠ» ΠΊΠ°ΡΠ΅ΡΡΠΠ΅Π½ΠΊΠΎΠ΅ ΡΠΎΠ²Π΅ΡΡΠ΅Π½ΡΡΠ²ΠΎΠ²Π°Π½ΠΈΠ΅ ΡΠ΅Ρ
Π½ΠΎΠ»ΠΎΠ³ΠΈΠΈ Π»ΠΈΡΡΠΎΠ²ΠΎΠΉ ΡΡΠ°ΠΌΠΏΠΎΠ²ΠΊΠΈ. Π ΡΡΠΎΠΌΡ Π½Π°Π΄ΠΎ Π΄ΠΎΠ±Π°Π²ΠΈΡΡ, ΡΡΠΎ Π΄Π΅ΡΠΈΡΠΈΡΠ½ΠΎΡΡΡ Π½Π΅ΠΊΠΎΡΠΎΡΡΡ
ΠΌΠ°ΡΠ΅ΡΠΈΠ°Π»ΠΎΠ², Π² ΡΠ°ΡΡΠ½ΠΎΡΡΠΈ ΠΌΠΎΠ»ΠΈΠ±Π΄Π΅Π½Π°, Π·Π½Π°ΡΠΈΡΠ΅Π»ΡΠ½ΠΎ Π·Π°ΡΡΡΠ΄Π½ΡΠ»Π° ΡΠ΅ΡΠ΅Π½ΠΈΠ΅ Π·Π°Π΄Π°ΡΠΈ ΠΏΠΎΠ²ΡΡΠ΅Π½ΠΈΡ ΡΡΠΎΠΉΠΊΠΎΡΡΠΈ ΡΡΠ°ΠΌΠΏΠΎΠ² Π΄Π»Ρ Π³ΠΎΡΡΡΠ΅ΠΉ ΡΡΠ°ΠΌΠΏΠΎΠ²ΠΊΠΈ Π½Π° ΠΌΠΎΠ»ΠΎΡΠ°Ρ
ΠΈ ΠΏΡΠ΅ΡΡΠ°Ρ
. ΠΠ° Π²ΡΠ΅ΠΌΡ ΠΏΠ΅ΡΠ²ΡΡ
ΠΏΡΡΠΈΠ»Π΅ΡΠΎΠΊ Π²ΠΎΠ·ΡΠΎΡΠ»ΠΎ ΠΏΡΠΈΠΌΠ΅Π½Π΅Π½ΠΈΠ΅ Π΄Π»Ρ ΡΡΠ°ΠΌΠΏΠΎΠ² ΡΠ²Π΅ΡΠ΄ΡΡ
ΡΠΏΠ»Π°Π²ΠΎΠ² Π² Π²ΠΈΠ΄Π΅ Π½Π°ΠΏΠ»Π°Π²ΠΎΠΊ ΠΈ ΠΎΡΠ΄Π΅Π»ΡΠ½ΡΡ
Π²ΡΡΠ°Π²ΠΎΠΊ Ρ ΡΠ΅Π»ΡΡ ΠΏΠΎΠ²ΡΡΠ΅Π½ΠΈΡ ΠΈΡ
ΡΡΠΎΠΉΠΊΠΎΡΡΠΈ. ΠΠ°Π³ΡΠ΅Π² ΠΌΠ΅ΡΠ°Π»Π»Π° Π΄Π»Ρ ΠΊΠΎΠ²ΠΊΠΈ, Π½Π΅ΡΠΌΠΎΡΡΡ Π½Π° Π½Π΅ΠΊΠΎΡΠΎΡΠΎΠ΅ ΡΠ»ΡΡΡΠ΅Π½ΠΈΠ΅, Π½Π΅ Π΄ΠΎΡΡΠΈΠ³ ΡΠΎΠ³ΠΎ ΡΠΎΡΡΠΎΡΠ½ΠΈΡ, ΠΊΠΎΡΠΎΡΠΎΠ΅ ΠΌΠΎΠΆΠ½ΠΎ Π±ΡΠ»ΠΎ Π±Ρ ΠΏΡΠΈΠ·Π½Π°ΡΡ ΡΠΎΠΎΡΠ²Π΅ΡΡΡΠ²ΡΡΡΠΈΠΌ ΡΡΠΎΠ²Π½Ρ ΡΠ΅Ρ
Π½ΠΈΠΊΠΈ. Π ΠΊΡΠ·Π½Π΅ΡΠ½ΡΡ
ΡΠ΅Ρ
Π°Ρ
ΡΠ²ΠΎΠ±ΠΎΠ΄Π½ΠΎΠΉ ΠΊΠΎΠ²ΠΊΠΈ ΠΏΡΠΎΠ΄ΠΎΠ»ΠΆΠ°Π»ΠΈ ΠΏΡΠΈΠΌΠ΅Π½ΡΡΡΡΡ Π΄Π²Π° ΠΎΡΠ½ΠΎΠ²Π½ΡΡ
β[c.108]
Π’Π΅Ρ Π½ΠΎΠ»ΠΎΠ³ΠΈΡ ΠΊΠΎΠ²ΠΊΠΈ ΠΈ ΡΡΠ°ΠΌΠΏΠΎΠ²ΠΊΠΈ Π΄ΠΎ 1945 Π³. Π² ΡΠ²ΡΠ·ΠΈ Ρ ΡΠ°ΡΡΠΈΡΠ΅Π½ΠΈΠ΅ΠΌ Π½ΠΎΠΌΠ΅Π½ΠΊΠ»Π°ΡΡΡΡ ΠΈΠ·Π³ΠΎΡΠ°Π²Π»ΠΈΠ²Π°Π΅ΠΌΡΡ ΠΏΠΎΠΊΠΎΠ²ΠΎΠΊ, ΠΏΠΎΠ²ΡΡΠ΅Π½ΠΈΠ΅ΠΌ ΡΠΎΡΠ½ΠΎΡΡΠΈ ΡΡΠ°ΠΌΠΏΠΎΠ²ΠΊΠΈ, ΠΏΡΠΈΠ±Π»ΠΈΠΆΠ΅Π½ΠΈΠ΅ΠΌ ΡΠΎΡΠΌΡ ΠΏΠΎΠΊΠΎΠ²ΠΎΠΊ ΠΊ Π³ΠΎΡΠΎΠ²ΡΠΌ Π΄Π΅ΡΠ°Π»ΡΠΌ, ΡΠΊΠΎΠ½ΠΎΠΌΠΈΠ΅ΠΉ ΠΌΠ΅ΡΠ°Π»Π»Π° ΠΈ Π΄ΡΡΠ³ΠΈΠΌΠΈ ΡΡΠ΅Π±ΠΎΠ²Π°Π½ΠΈΡΠΌΠΈ ΠΏΡΠΎΠΈΠ·Π²ΠΎΠ΄ΡΡΠ²Π° ΠΏΡΠ΅ΡΠ΅ΡΠΏΠ΅Π»Π° Π·Π½Π°ΡΠΈΡΠ΅Π»ΡΠ½ΡΠ΅ ΡΠ΄Π²ΠΈΠ³ΠΈ. Π Π°Π½Π΅Π΅ ΠΏΡΠΈΠΌΠ΅Π½ΡΠ΅ΠΌΠ°Ρ ΡΠ²ΠΎΠ±ΠΎΠ΄Π½Π°Ρ ΠΊΠΎΠ²ΠΊΠ° Π²Π°Π³ΠΎΠ½Π½ΡΡ ΠΎΡΠ΅ΠΉ ΠΏΠΎΠ΄ ΠΊΠΎΠ²ΠΎΡΠ½ΡΠΌΠΈ ΠΏΠ°ΡΠΎΠ²ΡΠΌΠΈ ΠΌΠΎΠ»ΠΎΡΠ°ΠΌΠΈ Π·Π°ΠΌΠ΅Π½ΡΠ»Π°ΡΡ Π½Π° ΠΎΠ΄Π½ΠΎΠΌ ΠΈΠ· Π·Π°Π²ΠΎΠ΄ΠΎΠ² ΡΡΠ°ΠΌΠΏΠΎΠ²ΠΊΠΎΠΉ Π² ΡΡΠ΅Ρ ΡΡΡΡΠ΅Π²ΡΡ ΡΡΠ°ΠΌΠΏΠ°Ρ Π½Π° Π³ΠΈΠ΄ΡΠ°Π²Π»ΠΈΡΠ΅ΡΠΊΠΈΡ ΠΏΡΠ΅ΡΡΠ°Ρ Ρ ΠΏΠΎΠΌΠΈΠ½Π°Π»ΡΠ½ΡΠΌ ΡΡΠΈΠ»ΠΈΠ΅ΠΌ 600 Ρ.

Π’Π΅Ρ Π½ΠΎΠ»ΠΎΠ³ΠΈΡ ΠΊΠΎΠ²ΠΊΠΈ Π½Π°ΠΈΠ±ΠΎΠ»Π΅Π΅ ΡΡΡΠ΄ΠΎΠ΅ΠΌΠΊΠΈΡ Π² ΠΈΠ·Π³ΠΎΡΠΎΠ²Π»Π΅Π½ΠΈΠΈ ΠΌΠ½ΠΎΠ³ΠΎΠΊΠΎΠ»Π΅Π½ΡΠ°ΡΡΡ Π²Π°Π»ΠΎΠ² ΡΠ°ΠΊΠΆΠ΅ ΠΏΠΎΠ»ΡΡΠΈΠ»Π° Π·Π½Π°ΡΠΈΡΠ΅Π»ΡΠ½ΠΎΠ΅ ΡΠ°Π·Π²ΠΈΡΠΈΠ΅. ΠΡΠΎΠΌΠ΅ ΠΏΡΠΈΠΌΠ΅Π½Π΅Π½ΠΈΡ ΡΡΠ°ΡΡΡ ΡΠΏΠΎΡΠΎΠ±ΠΎΠ² ΡΠ²ΠΎΠ±ΠΎΠ΄Π½ΠΎΠΉ ΠΊΠΎΠ²ΠΊΠΈ, Π² Π½Π΅ΠΊΠΎΡΠΎΡΡΡ ΠΊΡΠ·Π½Π΅ΡΠ½ΠΎ-ΠΏΡΠ΅ΡΡΠΎΠ²ΡΡ ΡΠ΅Ρ Π°Ρ , ΠΎΠ±ΠΎΡΡΠ΄ΠΎΠ²Π°Π½Π½ΡΡ ΠΌΠΎΡΠ½ΡΠΌΠΈ ΠΊΠΎΠ²ΠΎΡΠ½ΡΠΌΠΈ Π³ΠΈΠ΄ΡΠ°Π²Π»ΠΈΡΠ΅ΡΠΊΠΈΠΌΠΈ ΠΏΡΠ΅ΡΡΠ°ΠΌΠΈ, ΡΠ΅ΡΡΠΈΠΊΠΎΠ»Π΅Π½ΡΠ°ΡΡΠ΅ Π²Π°Π»Ρ ΡΡΠ°.Π»ΠΈ ΠΈΠ·Π³ΠΎΡΠΎΠ²Π»ΡΡΡ ΡΡΠ°ΠΌΠΏΠΎΠ²ΠΊΠΎΠΉ. β[c.109]
Π£ΠΊΠ°Π·Π°Π½ΠΈΡ ΠΊ Π½ΠΎΡΠΌΠ°ΡΠΈΠ²Π°ΠΌ Π΄Π»Ρ ΡΠ°ΡΡΠ΅ΡΠ° ΠΏΡΠΈΠΏΡΡΠΊΠΎΠ² Π½Π° ΠΎΠ±ΡΠ°Π±ΠΎΡΠΊΡ Π·Π°Π³ΠΎΡΠΎΠ²ΠΎΠΊ, ΠΏΠΎΠ»ΡΡΠ΅Π½Π½ΡΡ
ΡΠ²ΠΎΠ±ΠΎΠ΄Π½ΠΎΠΉ ΠΊΠΎΠ²ΠΊΠΎΠΉ ΠΈ Π³ΠΎΡΡΡΠ΅ΠΉ ΡΡΠ°ΠΌΠΏΠΎΠ²ΠΊΠΎΠΉ. ΠΠΎΡΠΌΠ°ΡΠΈΠ²Ρ Π΄Π»Ρ ΡΠ°ΡΡΠ΅ΡΠ° ΠΏΡΠΈΠΏΡΡΠΊΠΎΠ² Π½Π° ΠΎΠ±ΡΠ°Π±ΠΎΡΠΊΡ Π·Π°Π³ΠΎΡΠΎΠ²ΠΎΠΊ, ΠΏΠΎΠ»ΡΡΠ΅Π½Π½ΡΡ
ΡΠ²ΠΎΠ±ΠΎΠ΄Π½ΠΎΠΉ ΠΊΠΎΠ²ΠΊΠΎΠΉ ΠΈ Π³ΠΎΡΡΡΠ΅ΠΉ ΡΡΠ°ΠΌΠΏΠΎΠ²ΠΊΠΎΠΉ, Π½Π΅ ΡΠ°ΡΠΏΡΠΎΡΡΡΠ°Π½ΡΡΡΡΡ ΠΈΠ° ΠΏΡΠΈΠΏΡΡΠΊΠΈ, ΡΠ²ΡΠ·Π°Π½Π½ΡΠ΅ ΡΠΎ ΡΠΏΠ΅ΡΠΈΡΠΈΠΊΠΎΠΉ ΡΠ΅Ρ
Π½ΠΎΠ»ΠΎΠ³ΠΈΠΈ ΠΊΠΎΠ²ΠΊΠΈ ΠΈ ΡΡΠ°ΠΌΠΏΠΎΠ²ΠΊΠΈ (Π½Π°ΠΏΡΡΠΊΠ½, ΡΠΏΡΠΎΡ Π°ΡΡΠΈΠ΅ ΠΊΠΎΠ½ΡΠΈΠ³ΡΡΠ°ΡΠΈΡ ΡΠ΅ΡΠ½ΡΡ
Π·Π°Π³ΠΎΡΠΎΠ²ΠΎΠΊ ΠΈ ΡΠ³Π»Π°ΠΆΠΈΠ²Π°ΡΡΠΈΠ΅ ΠΌΠ΅ΡΡΠ½ΡΠ΅ ΡΠ³Π»ΡΠ±Π»Π΅Π½ΠΈΡ, ΠΏΠ΅ΡΠ΅Ρ
ΠΎΠ΄Ρ ΠΈ ΡΡΡΡΠΏΡ ΡΠ²Π΅Π»ΠΈΡΠ΅Π½Π½ΡΠ΅ ΠΏΡΠΈΠΏΡΡΠΊΠΈ Π½Π° ΡΠΎΠΏΡΡΠΆΠ΅Π½ΠΈΡΡ
ΠΎΠ±ΡΠ°Π±Π°ΡΡΠ²Π°Π΅ΠΌΡΡ
ΠΏΠΎΠ²Π΅ΡΡ
Π½ΠΎΡΡΠ΅ΠΉ ΡΡΠ°ΠΌΠΏΠΎΠ²Π°Π½Π½ΡΡ
Π·Π°Π³ΠΎΡΠΎΠ²ΠΎΠΊ, ΠΏΠΎΠ»ΡΡΠ°ΡΡΠΈΠ΅ΡΡ Π² ΡΠ²ΡΠ·ΠΈ Ρ Π½Π΅ΠΎΠ±Ρ
ΠΎΠ΄ΠΈΠΌΡΠΌΠΈ ΡΠ°Π΄ΠΈΡΡΠ°ΠΌΠΈ Π·Π°ΠΊΡΡΠ³Π»Π΅Π½ΠΈΠ) ΡΠ΅ΡΠ½ΠΎΠΉ Π·Π°Π³ΠΎΡΠΎΠ²ΠΊΠΈ, ΠΈ Ρ. ΠΏ.).
β[c.457]
ΠΠ±ΡΠΈΠΌ Π½Π°ΠΏΡΠ°Π²Π»Π΅Π½ΠΈΠ΅ΠΌ ΡΠΎΠ²Π΅ΡΡΠ΅Π½ΡΡΠ²ΠΎΠ²Π°Π½ΠΈΡ ΡΠ΅Ρ Π½ΠΎΠ»ΠΎΠ³ΠΈΠΈ ΠΏΡΠΎΠΈΠ·Π²ΠΎΠ΄ΡΡΠ²Π° Π·Π°Π³ΠΎΡΠΎΠ²ΠΎΠΊ ΡΠ²Π»ΡΠ΅ΡΡΡ ΠΏΡΠΈΠ±Π»ΠΈΠΆΠ΅Π½ΠΈΠ΅ ΠΈΡ ΡΠΎΡΠΌ ΠΊ ΡΠΎΡΠΌΠ°ΠΌ Π³ΠΎΡΠΎΠ²ΡΡ Π΄Π΅ΡΠ°Π»Π΅ΠΉ-ΡΡΠ°ΠΌΠΏΠΎΠ²ΠΎΠΊ Π²Π·Π°ΠΌΠ΅Π½ ΡΠ²ΠΎΠ±ΠΎΠ΄Π½ΠΎΠΉ ΠΊΠΎΠ²ΠΊΠΈ, ΡΠΎΡΠ½ΠΎΠ³ΠΎ Π»ΠΈΡΡΡ ΠΈ Π΄Ρ. ΠΡΠΎΠ²ΠΎΠ΄ΡΡΡΡ ΡΠ°Π±ΠΎΡΡ ΠΏΠΎ ΠΌΠ΅Ρ Π°Π½ΠΈΠ·Π°ΡΠΈΠΈ ΠΈ Π°Π²ΡΠΎΠΌΠ°ΡΠΈΠ·Π°ΡΠΈΠΈ ΠΊΡΠ·Π½Π΅ΡΠ½ΠΎ-Π½ΡΠ΅ΡΡΠΎΠ²ΠΎΠ³ΠΎ ΠΏΡΠΎΠΈΠ·Π²ΠΎΠ΄ΡΡΠ²Π°. ΠΠ° ΠΠΠ Ρ ΠΏΠΎΠΌΠΎΡΡΡ ΠΠΎΡΠΊΠΎΠ²ΡΠΊΠΎΠ³ΠΎ ΡΡΠ°Π½ΠΊΠΎ-ΠΈΠ½ΡΡΡΡΠΌΠ΅Π½ΡΠ°Π»ΡΠ½ΠΎΠ³ΠΎ ΠΈΠ½ΡΡΠΈΡΡΡΠ° Π±ΡΠ»ΠΈ ΡΡΡΠ°Π½ΠΎΠ²Π»Π΅Π½Ρ Π°Π²ΡΠΎΠΌΠ°ΡΠΈΡΠ΅ΡΠΊΠΈΠ΅ ΡΡΡΡΠΎΠΉΡΡΠ²Π°, ΡΠ°Π±ΠΎΡΠ°ΡΡΠΈΠ΅ Π½Π° ΠΎΡΠ½ΠΎΠ²Π΅ ΠΈΡΠΏΠΎΠ»ΡΠ·ΠΎΠ²Π°Π½ΠΈΡ ΡΠ°Π΄ΠΈΠΎΠ°ΠΊΡΠΈΠ²Π½ΡΡ ΠΈΠ·ΠΎΡΠΎΠΏΠΎΠ². ΠΡΠΈ ΡΡΡΡΠΎΠΉΡΡΠ²Π° ΠΏΠΎΠ·Π²ΠΎΠ»ΡΡΡ ΡΠ΅Π³ΡΠ»ΠΈΡΠΎΠ²Π°ΡΡ ΡΠ΅ΠΆΠΈΠΌ ΡΠ°Π±ΠΎΡΡ ΠΏΡΠ΅ΡΡΠΎΠ² ΠΏΠΎ Π·Π°Π΄Π°Π½Π½ΠΎΠΉ ΠΏΡΠΎΠ³ΡΠ°ΠΌΠΌΠ΅. Π’Π°ΠΊΠ°Ρ Π°Π²ΡΠΎΠΌΠ°ΡΠΈΠ·Π°ΡΠΈΡ ΠΏΡΠ΅ΡΡΠΎΠ² ΠΏΠΎΠ·Π²ΠΎΠ»ΡΠ΅Ρ ΠΏΠΎΠ²ΡΡΠΈΡΡ ΠΏΡΠΎΠΈΠ·Π²ΠΎΠ΄ΠΈΡΠ΅Π»ΡΠ½ΠΎΡΡΡ ΡΡΡΠ΄Π°, ΡΠ½ΠΈΠ·ΠΈΡΡ ΠΊΠ°ΠΊ Π΄ΠΎΠΏΡΡΠΊΠΈ, ΡΠ°ΠΊ ΠΈ ΠΏΡΠΈΠΏΡΡΠΊΠΈ Π½Π° ΠΈΠ·Π³ΠΎΡΠΎΠ²Π»Π΅Π½ΠΈΠ΅ ΠΊΡΡΠΏΠ½ΡΡ ΠΏΠΎΠΊΠΎΠ²ΠΎΠΊ. β[c.73]
ΠΠΎ Π²ΡΠΎΡΠΎΠΌ ΡΠ°Π·Π΄Π΅Π»Π΅, ΠΏΠΎΡΠ²ΡΡΠ΅Π½Π½ΠΎΠΌ Π²ΠΎΠΏΡΠΎΡΠ°ΠΌ Π°Π΅Ρ
Π½ΠΎΠ»ΠΎΠ³ΠΈΠΈ ΠΌΠ°ΡΠΈΠ½ΠΎΡΡΡΠΎΠ΅Π½ΠΈΡ, ΠΏΡΠΈΠ²Π΅Π΄Π΅Π½Ρ ΠΊΡΠ°ΡΠΊΠΈΠ΅ ΡΠΏΡΠ°Π²ΠΎΡΠ½ΡΠ΅ ΡΠ²Π΅Π΄Π΅Π½ΠΈΡ ΠΈ Π΄Π°Π½Π½ΡΠ΅, ΠΎΡΠ½ΠΎΡΡΡΠΈΠ΅ΡΡ ΠΊ Π½ΠΎΠ²ΡΠΌ ΡΠ΅Ρ
Π½ΠΎΠ»ΠΎΠ³ΠΈΡΠ΅ΡΠΊΠΈΠΌ ΠΏΡΠΎΡΠ΅ΡΡΠ°ΠΌ β ΡΠ΅ΠΆΠΈΠΌΠ°ΠΌ, ΠΎΠ±ΠΎΡΡΠ΄ΠΎΠ²Π°Π½ΠΈΡ, ΠΏΡΠΈΡΠΏΠΎΡΠΎΠ±Π»Π΅Π½ΠΈΡΠΌ ΠΈ ΠΈΠ½ΡΡΡΡΠΌΠ΅Π½ΡΠ°ΠΌ. Π ΡΠ°ΡΡΠ½ΠΎΡΡΠΈ, Π² Π³Π»Π°Π²Π΅, ΠΏΠΎΡΠ²ΡΡΠ΅Π½Π½ΠΎΠΉ ΡΠ΅Ρ
Π½ΠΎΠ»ΠΎΠ³ΠΈΠΈ Π»ΠΈΡΠ΅ΠΉΠ½ΠΎΠ³ΠΎ ΠΏΡΠΎΠΈΠ·Π²ΠΎΠ΄ΡΡΠ²Π°, ΠΏΡΠΈΠ²ΠΎΠ΄ΡΡΡΡ ΡΠΏΠ΅ΡΠΈΠ°Π»ΡΠ½ΡΠ΅ ΠΌΠ΅ΡΠΎΠ΄Ρ Π»ΠΈΡΡΡ Π² ΠΏΠΎΡΡΠΎΡΠ½Π½ΡΠ΅ ΡΠΎΡΠΌΡ, ΠΏΠΎΠ΄ Π΄Π°Π²Π»Π΅Π½ΠΈΠ΅ΠΌ, ΠΏΠΎ Π²ΡΠΏΠ»Π°Π²Π»ΡΠ΅ΠΌΡΠΌ ΠΌΠΎΠ΄Π΅Π»ΡΠΌ, ΡΠ΅Π½ΡΡΠΎΠ±Π΅ΠΆΠ½ΠΎΠ³ΠΎ Π»ΠΈΡΡΡ. ΠΠΎΠ΄ΡΠΎΠ±Π½ΡΠ΅ ΡΠΏΡΠ°Π²ΠΎΡΠ½ΡΠ΅ ΠΌΠ°ΡΠ΅ΡΠΈΠ°Π»Ρ Π΄Π°Π½Ρ ΠΏΠΎ Π²ΠΎΠΏΡΠΎΡΠ°ΠΌ Π³ΠΎΡΡΡΠ΅ΠΉ ΠΈ Ρ
ΠΎΠ»ΠΎΠ΄Π½ΠΎΠΉ ΠΎΠ±ΡΠ°Π±ΠΎΡΠΊΠΈ ΠΌΠ΅ΡΠ°Π»Π»ΠΎΠ² Π΄Π°Π²Π»Π΅Π½ΠΈΠ΅ΠΌ (ΡΠ²ΠΎΠ±ΠΎΠ΄Π½Π°Ρ ΠΊΠΎΠ²ΠΊΠ° ΠΈ ΡΡΠ°ΠΌΠΏΠΎΠ²ΠΊΠ°, Π²ΡΡΠ°Π΄ΠΊΠ°, Ρ
ΠΎΠ»ΠΎΠ΄Π½ΠΎΠ΅ ΠΊΠ°Π»ΠΈΠ±ΡΠΎΠ²Π°Π½ΠΈΠ΅ ΠΈ Ρ. ΠΏ.). ΠΠ»Π°Π²Π°, ΠΏΠΎΡΠ²ΡΡΠ΅Π½Π½Π°Ρ ΠΎΠ±ΡΠ°Π±ΠΎΡΠΊΠ΅ ΠΌΠ΅ΡΠ°Π»Π»ΠΎΠ² ΡΠ΅Π·Π°Π½ΠΈΠ΅ΠΌ, ΡΠΎΠ΄Π΅ΡΠΆΠΈΡ ΡΠΏΡΠ°Π²ΠΎΡΠ½ΡΠ΅ Π΄Π°Π½Π½ΡΠ΅ ΠΏΠΎ Π²ΡΠ±ΠΎΡΡ ΡΠ΅ΠΆΠΈΠΌΠΎΠ² ΡΠ΅Π·Π°Π½ΠΈΡ ΠΈ ΠΏΠΎ ΡΠ°Π·Π½ΡΠΌ Π²ΠΈΠ΄Π°ΠΌ ΡΠ΅Ρ
Π½ΠΎΠ»ΠΎΠ³ΠΈΠΈ ΠΌΠ΅Ρ
Π°Π½ΠΈΡΠ΅ΡΠΊΠΎΠΉ ΠΎΠ±ΡΠ°Π±ΠΎΡΠΊΠΈ ΠΌΠ΅ΡΠ°Π»Π»ΠΎΠ², ΠΏΠ»Π°ΡΡΠΌΠ°ΡΡ ΠΈ Π΄Π΅ΡΠ΅Π²Π°, Π²ΠΊΠ»ΡΡΠ°Ρ ΠΌΠ΅ΡΠΎΠ΄Ρ ΠΎΡΠ΄Π΅Π»ΠΎΡΠ½ΠΎΠΉ ΠΎΠ±ΡΠ°Π±ΠΎΡΠΊΠΈ (ΡΠ΅Π²ΠΈΠ½Π³ΠΎΠ²Π°Π½ΠΈΠ΅, ΠΏΡΠΈΡΠΈΡΠΎΡΠ½ΠΎΠ΅ ΡΠ»1.ΡΠΎΠ²Π°Π½ΠΈΠ΅ ΠΈ Π΄Ρ.).
β[c.1087]
Π¨ΠΈΡΠΎΠΊΠΎ ΠΈΠ·Π²Π΅ΡΡΠ½ΠΎ, ΡΡΠΎ Π³ΠΎΡΡΡΠ°Ρ ΠΎΠ±ΡΠ°Π±ΠΎΡΠΊΠ° ΠΌΠ΅ΡΠ°Π»Π»ΠΎΠ² Π΄Π°Π²Π»Π΅Π½ΠΈΠ΅ΠΌ ΠΊ ΠΊΠΎΡΠΎΡΠΎΠΉ ΠΎΡΠ½ΠΎΡΡΡΡΡ ΠΌΠ½ΠΎΠ³ΠΎΡΠΈΡΠ»Π΅Π½Π½ΡΠ΅ ΠΎΠΏΠ΅ΡΠ°ΡΠΈΠΈ ΡΠ²ΠΎΠ±ΠΎΠ΄Π½ΠΎΠΉ ΠΊΠΎΠ²ΠΊΠΈ, ΠΊΠΎΠ²ΠΊΠΈ Π² ΠΏΠΎΠ΄ΠΊΠ»Π°Π΄Π½ΡΡ ΡΡΠ°ΠΌΠΏΠ°Ρ , ΠΎΠ±Π»ΠΎΠΉΠΊΠ°Ρ ΠΈ Π±Π΅Π·ΠΎΠ±Π»ΠΎΠΉΠ½Π°Ρ ΡΡΠ°ΠΌΠΏΠΎΠ²ΠΊΠ° ΠΈ ΠΏΡ., ΠΈΠ³ΡΠ°Π΅Ρ ΠΎΠ³ΡΠΎΠΌΠ½ΡΡ ΡΠΎΠ»Ρ Π² ΡΠΎΠ²ΡΠ΅ΠΌΠ΅Π½Π½ΠΎΠΉ ΡΠ΅Ρ Π½ΠΎΠ»ΠΎΠ³ΠΈΠΈ ΠΌΠ°ΡΠΈΠ½ΠΎΡΡΡΠΎΠ΅Π½ΠΈΡ. β[c.206]
Π’Π΅Ρ
Π½ΠΎΠ»ΠΎΠ³ΠΈΡ ΠΈΠ·Π³ΠΎΡΠΎΠ²Π»Π΅Π½ΠΈΡ ΡΡΠ΅Π΄Π½ΠΈΡ
ΠΏΠΎΠΊΠΎΠ²ΠΎΠΊ ΡΠ²ΠΎΠ±ΠΎΠ΄Π½ΠΎΠΉ ΠΊΠΎΠ²ΠΊΠΈ ΠΈΠ· ΠΊΡΡΠ³Π»ΠΎΠ³ΠΎ ΠΏΡΠΎΠΊΠ°ΡΠ° ΡΠ»Π΅Π΄ΡΡΡΠ°Ρ ΡΡΠ±ΠΊΠ° ΠΏΡΠΎΠΊΠ°ΡΠ° Π½Π° Π·Π°Π³ΠΎΡΠΎΠ²ΠΊΠΈ ΠΏΡΠΈ Π΄ΠΈΠ°ΠΌΠ΅ΡΡΠ΅ ΠΏΡΠΈΠΌΠ΅ΡΠ½ΠΎ Π΄ΠΎ 80 ΠΌΠΌ (Π΄Π»Ρ ΠΌΡΠ³ΠΊΠΎΠΉ ΡΡΠ°Π»ΠΈ) Π½Π° ΠΌΠΎΡΠ½ΡΡ
ΠΏΡΠ΅ΡΡΠ½ΠΎΠΆ-Π½ΠΈΡΠ°Ρ
Π² Ρ
ΠΎΠ»ΠΎΠ΄Π½ΠΎΠΌ ΡΠΎΡΡΠΎΡΠ½ΠΈΠΈ, Π° ΠΏΡΠΈ Π±ΠΎΠ»ΡΡΠ΅ΠΌ Π΄ΠΈΠ°ΠΌΠ΅ΡΡΠ΅ β Ρ ΠΏΠΎΠ΄ΠΎΠ³ΡΠ΅Π²ΠΎΠΌ Π½Π° ΠΏΡΠ΅ΡΡΠ½ΠΎΠΆΠ½ΠΈΡΠ°Ρ
ΠΈΠ»ΠΈ Π² Π³ΠΎΡΡΡΠ΅ΠΌ ΡΠΎΡΡΠΎΡΠ½ΠΈΠΈ Π½Π° ΠΌΠΎΠ»ΠΎΡΠ°Ρ
Π½Π°Π³ΡΠ΅Π² Π·Π°Π³ΠΎΡΠΎΠ²ΠΎΠΊ Π΄ΠΎ ΡΠ΅ΠΌΠΏΠ΅ΡΠ°ΡΡΡΡ ΠΊΠΎΠ²ΠΊΠΈ Π² ΠΊΠ°ΠΌΠ΅ΡΠ½ΠΎΠΉ ΠΏΠ΅ΡΠΈ ΠΈΠ»ΠΈ Π² ΠΈΠ½ΠΎΠΌ Π½Π°Π³ΡΠ΅Π²Π°ΡΠ΅Π»ΡΠ½ΠΎΠΌ ΡΡΡΡΠΎΠΉΡΡΠ²Π΅ (ΡΠΌ. Π³Π». 3) ΠΊΠΎΠ²ΠΊΠ° Π² Π½Π΅ΡΠΊΠΎΠ»ΡΠΊΠΈΡ
ΠΏΠ΅ΡΠ΅Ρ
ΠΎΠ΄Π°Ρ
ΠΈ, Π΅ΡΠ»ΠΈ Π½Π΅ΠΎΠ±Ρ
ΠΎΠ΄ΠΈΠΌΠΎ, ΡΠ΅ΡΠΌΠΈΡΠ΅ΡΠΊΠ°Ρ ΠΎΠ±ΡΠ°Π±ΠΎΡΠΊΠ° Π΄Π»Ρ ΠΏΠΎΠ»ΡΡΠ΅Π½ΠΈΡ Π·Π°Π΄Π°Π½Π½ΠΎΠΉ ΡΡΡΡΠΊΡΡΡΡ ΠΈ ΡΠ²ΠΎΠΉΡΡΠ² ΠΌΠ΅ΡΠ°Π»Π»Π°. ΠΠ΅ΡΠ΅Ρ
ΠΎΠ΄Ρ ΠΊΠΎΠ²ΠΊΠΈ, Π½Π°ΠΏΡΠΈΠΌΠ΅Ρ ΠΏΡΠΈ ΠΊΠΎΠ²ΠΊΠ΅ ΠΊΠΎΠ»ΡΡΠ° ΠΈΠ· ΠΊΡΡΠ³Π»ΠΎΠ³ΠΎ ΠΏΡΠΎΠΊΠ°ΡΠ°, ΠΌΠΎΠ³ΡΡ Π±ΡΡΡ ΡΠ»Π΅Π΄ΡΡΡΠΈΠΌΠΈ (ΡΠΈΡ. 1Π£-21) ΠΎΡΠ°Π΄ΠΊΠ° Π·Π°Π³ΠΎΡΠΎΠ²ΠΊΠΈ 1, ΠΎΠ±ΠΊΠ°ΡΠΊΠ° ΠΏΠΎ Π΄ΠΈΠ°ΠΌΠ΅ΡΡΡ 2, ΠΏΡΠΎΡΠΈΠ²ΠΊΠ° ΠΎΡΠ²Π΅ΡΡΡΠΈΡ 3, ΡΠ°ΡΠΊΠ°ΡΠΊΠ° Π½Π° ΠΎΠΏΡΠ°Π²ΠΊΠ΅ 4.
β[c.192]
ΠΠ° ΡΡΠΎΠΉΠΊΠΎΡΡΡ ΡΡΠ°ΠΌΠΏΠΎΠ² Π·Π½Π°ΡΠΈΡΠ΅Π»ΡΠ½ΠΎΠ΅ Π²Π»ΠΈΡΠ½ΠΈΠ΅ ΠΎΠΊΠ°Π·ΡΠ²Π°Π΅Ρ ΡΠ΅Ρ
Π½ΠΎΠ»ΠΎΠ³ΠΈΡ ΠΏΠΎΠ»ΡΡΠ΅Π½ΠΈΡ Π·Π°Π³ΠΎΡΠΎΠ²ΠΊΠΈ ΠΈ Π΅Π΅ ΡΠ΅ΡΠΌΠΈΡΠ΅ΡΠΊΠ°Ρ ΠΎΠ±ΡΠ°Π±ΠΎΡΠΊΠ°. ΠΠ°ΠΈΠ±ΠΎΠ»ΡΡΠ΅Π΅ ΠΏΡΠΈΠΌΠ΅Π½Π΅Π½ΠΈΠ΅ ΠΈΠΌΠ΅Π΅Ρ ΠΈΠ·Π³ΠΎΡΠΎΠ²Π»Π΅Π½ΠΈΠ΅ ΡΡΠ°ΠΌΠΏΠΎΠ² ΠΈΠ· ΠΊΡΠ±ΠΈΠΊΠΎΠ², ΠΏΠΎΠ»ΡΡΠ΅Π½Π½ΡΡ
ΡΠ²ΠΎΠ±ΠΎΠ΄Π½ΠΎΠΉ ΠΊΠΎΠ²ΠΊΠΎΠΉ Π½Π° ΠΌΠΎΠ»ΠΎΡΠ°Ρ
ΠΈΠ»ΠΈ ΠΏΡΠ΅ΡΡΠ°Ρ
. Π¨ΡΠ°ΠΌΠΏΠΎΠ²ΡΠ΅ ΠΊΡΠ±ΠΈΠΊΠΈ Π΄ΠΎΠ»ΠΆΠ½Ρ ΡΡΠ°ΡΠ΅Π»ΡΠ½ΠΎ ΠΏΡΠΎΠΊΠΎΠ²ΡΠ²Π°ΡΡΡΡ Ρ ΠΎΡΠ°Π΄ΠΊΠΎΠΉ Ρ ΡΠΎΡΡΠ° Π½Π΅ ΠΌΠ΅Π½Π΅Π΅ ΡΠ΅ΠΌ Π½Π° 50% ΠΏΠ΅ΡΠ²ΠΎΠ½Π°ΡΠ°Π»ΡΠ½ΠΎΠΉ Π²ΡΡΠΎΡΡ Ρ ΠΏΠΎΡΠ»Π΅Π΄ΡΡΡΠ΅ΠΉ Π²ΡΡΡΠΆΠΊΠΎΠΉ Π² ΠΏΠ΅ΡΠΏΠ΅Π½Π΄ΠΈΠΊΡΠ»ΡΡΠ½ΠΎΠΌ Π½Π°ΠΏΡΠ°Π²Π»Π΅Π½ΠΈΠΈ. Π£ΠΊΠΎΠ²ΠΊΠ° Ρ ΡΡΠ°ΠΌΠΏΠΎΠ²ΡΡ
ΠΊΡΠ±ΠΈΠΊΠΎΠ² Π΄ΠΎΠ»ΠΆΠ½Π° Π±ΡΡΡ Π½Π΅ ΠΌΠ΅Π½Π΅Π΅ 3 (ΠΎΡΠ½ΠΎΡΠ΅Π½ΠΈΠ΅ ΠΏΠ»ΠΎΡΠ°Π΄ΠΈ ΠΏΠΎΠΏΠ΅ΡΠ΅ΡΠ½ΠΎΠ³ΠΎ ΡΠ΅ΡΠ΅Π½ΠΈΡ ΡΠ»ΠΈΡΠΊΠ° ΠΏΠΎΡΠ»Π΅ ΠΎΡΠ°Π΄ΠΊΠΈ ΠΊ ΠΏΠ»ΠΎΡΠ°Π΄ΠΈ ΠΏΠΎΠΏΠ΅ΡΠ΅ΡΠ½ΠΎΠ³ΠΎ ΡΠ΅ΡΠ΅Π½ΠΈΡ Π³ΠΎΡΠΎΠ²ΠΎΠΉ Π·Π°Π³ΠΎΡΠΎΠ²ΠΊΠΈ Π΄Π»Ρ ΡΡΠ°ΠΌΠΏΠΎΠ²) Π΄Π»Ρ ΠΎΡΠΎΠ±ΠΎ Π½Π°ΠΏΡΡΠΆΠ΅Π½Π½ΠΎ ΡΠ°Π±ΠΎΡΠ°ΡΡΠΈΡ
Π²ΡΡΠ°Π²ΠΎΠΊ β Π΄ΠΎ 6. Π¨ΡΠ°ΠΌΠΏΠΎΠ²ΡΠ΅ ΠΊΡΠ±ΠΈΠΊΠΈ Π½Π΅ Π΄ΠΎΠ»ΠΆΠ½Ρ ΠΈΠΌΠ΅ΡΡ ΡΡΠ°Π΄ΠΎΡΠ½ΠΎΠΉ ΡΡΡ
Π»ΠΎΡΡΠΈ, ΡΠ»ΠΎΠΊΠ΅Π½ΠΎΠ², ΡΠ°ΡΡΠ»ΠΎΠ΅Π½ΠΈΠΉ, ΡΡΠ΅ΡΠΈΠ½ ΠΈ ΠΈΠ΅ΠΌΠ΅ΡΠ°Π»Π»ΠΈ-8 231
β[c. 231]
Π‘Π²ΠΎΠ±ΠΎΠ΄Π½Π°Ρ ΠΊΠΎΠ²ΠΊΠ° Π·Π°Π³ΠΎΡΠΎΠ²ΠΎΠΊ ΠΊΠΎΠ»Π΅Ρ ΠΏΠΎΠ΄ΡΠΈΠΏΠ½ΠΈΠΊΠΎΠ². Π‘Π²ΠΎΠ±ΠΎΠ΄Π½ΡΡ ΠΊΠΎΠ²ΠΊΡ ΠΏΡΠΈΠΌΠ΅Π½ΡΡΡ Π΄Π»Ρ ΠΏΠΎΠ»ΡΡΠ΅Π½ΠΈΡ Π·Π°Π³ΠΎΡΠΎΠ²ΠΎΠΊ ΠΊΠΎΠ»Π΅Ρ ΠΊΡΡΠΏΠ½ΠΎΠ³Π°Π±Π°ΡΠΈΡΠ½ΡΡ ΠΏΠΎΠ΄ΡΠΈΠΏΠ½ΠΈΠΊΠΎΠ², ΠΊΠΎΡΠΎΡΡΠ΅ Π½Π΅ ΠΌΠΎΠ³ΡΡ Π±ΡΡΡ ΠΈΠ·Π³ΠΎΡΠΎΠ²Π»Π΅Π½Ρ ΡΡΠ°ΠΌΠΏΠΎΠ²ΠΊΠΎΠΉ Π½Π° ΠΠΠ, Π° ΡΠ°ΠΊΠΆΠ΅ Π·Π°Π³ΠΎΡΠΎΠ²ΠΎΠΊ Π΄Π»Ρ ΠΌΠ΅Π»ΠΊΠΎΡΠ΅ΡΠΈΠΉΠ½ΠΎΠ³ΠΎ ΠΈΠ»ΠΈ ΠΈΠ½Π΄ΠΈΠ²ΠΈΠ΄ΡΠ°Π»ΡΠ½ΠΎΠ³ΠΎ ΠΏΡΠΎΠΈΠ·Π²ΠΎΠ΄ΡΡΠ²Π° ΠΏΠΎΠ΄Ρ ΠΈΠΏΠ½ΠΈΠΊΠΎΠ², ΠΊΠΎΠ³Π΄Π° ΠΈΠ·Π³ΠΎΡΠΎΠ²Π»Π΅Π½ΠΈΠ΅ ΠΈΠ½ΡΠΌΠΈ ΠΌΠ΅ΡΠΎΠ΄Π°ΠΌΠΈ Π½Π΅ΡΠΊΠΎΠ½ΠΎΠΌΠΈΡΠ½ΠΎ. ΠΡΠΈ ΡΠ΅ΡΠΈΠΉΠ½ΠΎΠΌ ΠΏΡΠΎΠΈΠ·Π²ΠΎΠ΄ΡΡΠ²Π΅ ΠΊΡΡΠΏΠ½ΠΎΠ³Π°Π±Π°ΡΠΈΡΠ½ΡΡ ΠΏΠΎΠ΄ΡΠΈΠΏΠ½ΠΈΠΊΠΎΠ² ΡΠ²ΠΎΠ±ΠΎΠ΄Π½Π°Ρ ΠΊΠΎΠ²ΠΊΠ°, ΠΊΠ°ΠΊ ΠΏΡΠ°Π²ΠΈΠ»ΠΎ, ΡΠ²Π»ΡΠ΅ΡΡΡ ΠΏΡΠΎΠΌΠ΅ΠΆΡΡΠΎΡΠ½ΠΎΠΉ ΠΎΠΏΠ΅ΡΠ°ΡΠΈΠ΅ΠΉ Π² ΡΠ΅Ρ Π½ΠΎΠ»ΠΎΠ³ΠΈΠΈ ΠΈΠ·Π³ΠΎΡΠΎΠ²Π»Π΅Π½ΠΈΡ Π·Π°Π³ΠΎΡΠΎΠ²ΠΎΠΊ ΠΊΠΎΠ»Π΅Ρ, Π·Π°Π²Π΅ΡΡΠ°ΡΡΠ΅ΠΉΡΡ Π³ΠΎΡΡΡΠ΅ΠΉ ΡΠ°ΡΠΊΠ°ΡΠΊΠΎΠΉ ΠΊΠΎΠ»ΡΡΠ΅Π²ΡΡ ΠΏΠΎΠΊΠΎΠ²ΠΎΠΊ. ΠΠ΅ΡΠΎΠ΄Ρ ΡΠ²ΠΎΠ±ΠΎΠ΄Π½ΠΎΠΉ ΠΊΠΎΠ²ΠΊΠΈ ΠΊΠΎΠ»ΡΡΠ΅Π²ΡΡ ΠΏΠΎΠΊΠΎΠ²ΠΎΠΊ, ΠΏΡΠΈΠΌΠ΅Π½ΡΠ΅ΠΌΡΠ΅ Π² ΠΎΡΠ΅ΡΠ΅ΡΡΠ²Π΅Π½Π½ΠΎΠΉ ΠΏΡΠΎΠΌΡΡΠ»Π΅Π½Π½ΠΎΡΡΠΈ, ΠΏΡΠ΅Π΄ΡΡΠΌΠ°ΡΡΠΈΠ²Π°ΡΡ Π²ΡΠΏΠΎΠ»Π½Π΅Π½ΠΈΠ΅ ΡΡΠΈΡ ΡΠ΅Ρ Π½ΠΎΠ»ΠΎΠ³ΠΈΡΠ΅ΡΠΊΠΈΡ ΠΎΠΏΠ΅ΡΠ°ΡΠΈΠΉ Π½Π° ΠΏΠ½Π΅Π²ΠΌΠ°ΡΠΈΡΠ΅ΡΠΊΠΈΡ ΠΈ ΠΏΠ°ΡΠΎΠ²ΠΎΠ·Π΄ΡΡΠ½ΡΡ ΠΌΠΎΠ»ΠΎΡΠ°Ρ Ρ ΠΈΡΠΏΠΎΠ»ΡΠ·ΠΎΠ²Π°Π½ΠΈΠ΅ΠΌ ΡΠ½ΠΈΠ²Π΅ΡΡΠ°Π»ΡΠ½ΠΎΠ³ΠΎ ΠΊΡΠ·Π½Π΅ΡΠ½ΠΎΠ³ΠΎ ΠΈΠ½ΡΡΡΡΠΌΠ΅Π½ΡΠ°, ΡΡΠΎ ΠΎΠ±Π΅ΡΠΏΠ΅ΡΠΈΠ²Π°Π΅Ρ ΠΏΠΎΠ»ΡΡΠ΅Π½ΠΈΠ΅ ΠΏΠΎΠΊΠΎΠ²ΠΎΠΊ ΠΏΡΠΎΡΡΠ΅ΠΉΡΠ΅ΠΉ ΡΠΈΠ»ΠΈΠ½Π΄ΡΠΈΡΠ΅ΡΠΊΠΎΠΉ ΡΠΎΡΠΌΡ [122]. β[c.314]
Π’Π΅Ρ Π½ΠΎΠ»ΠΎΠ³ΠΈΡ Ρ ΡΠ΄ΠΎΠΆΠ΅ΡΡΠ²Π΅Π½Π½ΠΎΠΉ ΠΊΠΎΠ²ΠΊΠΈ ΠΈ ΡΠ»Π΅ΡΠ°ΡΠ½ΠΎΠ³ΠΎ ΠΈΡΠΊΡΡΡΡΠ²Π°. Π§Π°ΡΡΡ 1.
ΠΡΠ·Π½Π΅ΡΠ½ΡΠΉ ΠΈΠ½ΡΡΡΡΠΌΠ΅Π½Ρ ΠΈ ΠΎΠ±ΠΎΡΡΠ΄ΠΎΠ²Π°Π½ΠΈΠ΅
ΠΠ±ΠΎΡΡΠ΄ΠΎΠ²Π°Π½ΠΈΠ΅ ΠΌΠ°ΡΡΠ΅ΡΡΠΊΠΈΡ
Ρ
ΡΠ΄ΠΎΠΆΠ΅ΡΡΠ²Π΅Π½Π½ΠΎΠΉ ΠΊΠΎΠ²ΠΊΠΈ ΠΈ ΡΠ»Π΅ΡΠ°ΡΠ½ΠΎΠ³ΠΎ ΠΈΡΠΊΡΡΡΡΠ²Π° Π² ΠΎΡΠ½ΠΎΠ²Π½ΠΎΠΌ Π½Π΅ ΠΎΡΠ»ΠΈΡΠ°Π΅ΡΡΡ ΠΎΡ ΠΎΠ±ΠΎΡΡΠ΄ΠΎΠ²Π°Π½ΠΈΡ ΠΎΠ±ΡΡΠ½ΠΎΠΉ ΠΊΡΠ·Π½ΠΈΡΡ ΠΈΠ»ΠΈ ΡΠ»Π΅ΡΠ°ΡΠ½ΠΎΠΉ ΠΌΠ°ΡΡΠ΅ΡΡΠΊΠΎΠΉ. ΠΡΠ½ΠΎΠ²Π½ΡΠΌΠΈ ΡΡΡΡΠΎΠΉΡΡΠ²Π°ΠΌΠΈ Π·Π΄Π΅ΡΡ ΡΠ²Π»ΡΡΡΡΡ Π³ΠΎΡΠ½ ΠΈ Π½Π°ΠΊΠΎΠ²Π°Π»ΡΠ½Ρ.
Π ΠΈΡ.1. ΠΡΠ·Π½Π΅ΡΠ½ΡΠΉ Π³ΠΎΡΠ½. | Π ΠΈΡ.2. Π‘Ρ Π΅ΠΌΠ° ΡΡΡΠ°Π½ΠΎΠ²ΠΊΠΈ Π½Π°ΠΊΠΎΠ²Π°Π»ΡΠ½ΠΈ. |
Π Π³ΠΎΡΠ½Ρ (ΡΠΈΡ.1) Π΄ΠΎΠ»ΠΆΠ΅Π½ Π±ΡΡΡ Π΄ΠΎΡΡΡΠΏ Ρ ΡΡΠ΅Ρ ΡΡΠΎΡΠΎΠ½, ΡΡΠΎ Π½Π΅ΠΎΠ±Ρ ΠΎΠ΄ΠΈΠΌΠΎ ΠΎΡΠΎΠ±Π΅Π½Π½ΠΎ ΠΏΡΠΈ ΠΈΠ·Π³ΠΎΡΠΎΠ²Π»Π΅Π½ΠΈΠΈ ΠΊΡΡΠΏΠ½ΡΡ ΠΈΠ·Π΄Π΅Π»ΠΈΠΉ, ΠΏΡΠΈ ΠΈΡ ΡΠΊΠ»Π°Π΄ΠΊΠ΅ ΠΈ Π²ΡΠ½ΠΎΡΠ΅ ΠΏΠΎΡΠ»Π΅ Π½Π°Π³ΡΠ΅Π²Π°. ΠΡΠΎ ΠΎΡΠ½ΠΎΠ²Π½ΠΎΠ΅ ΠΊΡΠ·Π½Π΅ΡΠ½ΠΎΠ΅ ΡΡΡΡΠΎΠΉΡΡΠ²ΠΎ Π΄ΠΎΠ»ΠΆΠ½ΠΎ Π±ΡΡΡ ΠΎΠ±ΠΎΡΡΠ΄ΠΎΠ²Π°Π½ΠΎ Ρ ΠΎΡΠΎΡΠ΅ΠΉ Π²ΡΡΡΠΆΠΊΠΎΠΉ. ΠΡΠ΅Π½Ρ ΡΠ΄ΠΎΠ±Π΅Π½ Π΄Π»Ρ ΡΡΠΎΠΉ ΡΠ΅Π»ΠΈ Π²ΡΠΏΠΎΠΌΠΎΠ³Π°ΡΠ΅Π»ΡΠ½ΡΠΉ Π΄ΡΠΌΠΎΡΠΎΡ Π΄Π»Ρ ΠΎΡΡΠΎΡΠ° ΠΏΡΠΎΠ΄ΡΠΊΡΠΎΠ² Π³ΠΎΡΠ΅Π½ΠΈΡ. ΠΡΠΈ ΡΠ°Π·Π²Π΅Π΄Π΅Π½ΠΈΠΈ ΠΎΠ³Π½Ρ, ΠΎΡΠΎΠ±Π΅Π½Π½ΠΎ Π² Π»Π΅ΡΠ½ΠΈΠ΅ ΠΌΠ΅ΡΡΡΡ, ΡΠ»Π΅Π΄ΡΠ΅Ρ Π΄ΠΎΡΡΠ°ΡΠΎΡΠ½ΠΎ Π΄ΠΎΠ»Π³ΠΎ, Π΄ΠΎΠ»ΡΡΠ΅ ΡΠ΅ΠΌ Π² ΠΎΠ±ΡΡΠ½ΠΎΠΉ Π΄ΡΠΌΠΎΠ²ΠΎΠΉ ΡΡΡΠ±Π΅, ΠΏΠΎΠ΄Π΄Π΅ΡΠΆΠΈΠ²Π°ΡΡ ΡΠ°ΠΊ Π½Π°Π·ΡΠ²Π°Π΅ΠΌΡΡ ΡΡΠ³Ρ Π΄Π»Ρ ΡΠΎΠ³ΠΎ, ΡΡΠΎΠ±Ρ ΠΌΠ°ΡΡΠ΅ΡΡΠΊΠ°Ρ Π½Π΅ Π±ΡΠ»Π° Π·Π°Π΄ΡΠΌΠ»Π΅Π½Π°. ΠΠ»Ρ ΡΡΠΈΡ ΡΠ»ΡΡΠ°Π΅Π½ Π½Π΅ΠΎΠ±Ρ ΠΎΠ΄ΠΈΠΌ Π²ΡΠΏΠΎΠΌΠΎΠ³Π°ΡΠ΅Π»ΡΠ½ΡΠΉ Π²Π΅Π½ΡΠΈΠ»ΡΡΠΎΡ.
ΠΠ°ΠΊΠΎΠ²Π°Π»ΡΠ½Ρ β Π²ΡΠΎΡΠΎΠ΅ ΠΎΡΠ½ΠΎΠ²Π½ΠΎΠ΅ ΡΡΡΡΠΎΠΉΡΡΠ²ΠΎ ΠΌΠ°ΡΡΠ΅ΡΡΠΊΠΎΠΉ Ρ
ΡΠ΄ΠΎΠΆΠ΅ΡΡΠ²Π΅Π½Π½ΠΎΠΉ ΠΊΠΎΠ²ΠΊΠΈ β Π΄ΠΎΠ»ΠΆΠ½Π° Π±ΡΡΡ Ρ
ΠΎΡΠΎΡΠΎ Π·Π°ΠΊΡΠ΅ΠΏΠ»Π΅Π½Π° Π»ΠΈΠ±ΠΎ Π½Π° ΠΆΠ΅ΡΡΠΊΠΎΠΌ ΡΡΡΠ±Π°Π½Π΅ Π»ΠΈΠ±ΠΎ Π½Π° Π΄Π΅ΡΠ΅Π²ΡΠ½Π½ΠΎΠΉ ΠΏΠΎΠ΄ΡΡΠΊΠ΅, ΡΡΡΠ°Π½ΠΎΠ²Π»Π΅Π½Π½ΠΎΠΉ Π² ΠΆΠ΅Π»Π΅Π·Π½ΠΎΠΉ Π±ΠΎΡΠΊΠ΅, Π·Π°ΠΏΠΎΠ»Π½Π΅Π½Π½ΠΎΠΉ ΠΏΠ΅ΡΠΊΠΎΠΌ ΠΈΠ»ΠΈ Π³Π»ΠΈΠ½ΠΎΠΉ (ΡΠΈΡ. 2). ΠΡΠ½ΠΎΠ²Π°Π½ΠΈΠ΅ Π² ΠΎΠ±ΠΎΠΈΡ
ΡΠ»ΡΡΠ°ΡΡ
Π΄ΠΎΠ»ΠΆΠ½ΠΎ Π±ΡΡΡ Π·Π°Π³Π»ΡΠ±Π»Π΅Π½ΠΎ Π² Π·Π΅ΠΌΠ»Ρ, ΡΡΠΎΠ±Ρ Π½Π°ΠΊΠΎΠ½Π°Π»ΡΠ½Ρ ΠΏΡΠΈ ΡΠ΄Π°ΡΠ°Ρ
Π½Π΅ ΡΠ°ΡΠ°Π»Π°ΡΡ. ΠΠ»Ρ ΡΠΊΡΠ΅ΠΏΠ»Π΅Π½ΠΈΡ Π½Π°ΠΊΠΎΠ²Π°Π»ΡΠ½ΠΈ Π½Π° ΠΏΠΎΠ΄ΡΡΠΊΠ΅ Π΄ΠΎΡΡΠ°ΡΠΎΡΠ΅Π½ ΡΠ½ΠΈΠ·Ρ ΡΠ΅Π½ΡΡΠ°Π»ΡΠ½ΡΠΉ ΡΠΈΠΏ, ΡΠ°ΠΊ ΠΊΠ°ΠΊ Π½Π°ΠΊΠΎΠ²Π°Π»ΡΠ½Ρ ΠΌΠΎΠΆΠ΅Ρ Π»ΠΈΡΡ Π·Π° ΡΡΠ΅Ρ ΡΠΈΠ»Ρ ΡΡΠΆΠ΅ΡΡΠΈ ΠΏΡΠΎΡΠ½ΠΎ ΡΠΈΠ΄Π΅ΡΡ Π½Π° ΠΏΠΎΠ΄ΡΡΠΊΠ΅. ΠΠ»Ρ Π³Π»ΡΡΠ΅Π½ΠΈΡ ΡΡΠΌΠ° ΠΌΠΎΠΆΠ½ΠΎ ΠΌΠ΅ΠΆΠ΄Ρ Π½Π°ΠΊΠΎΠ²Π°Π»ΡΠ½Π΅ΠΉ ΠΈ ΠΏΠΎΠ΄ΡΡΠΊΠΎΠΉ ΡΠ»ΠΎΠΆΠΈΡΡ ΠΏΡΠΎΠΊΠ»Π°Π΄ΠΊΡ ΠΈΠ· ΡΠ²Π΅ΡΠ΄ΠΎΠΉ ΡΠ΅Π·ΠΈΠ½Ρ ΡΠΎΠ»ΡΠΈΠ½ΠΎΠΉ ΠΏΡΠΈΠ±Π»ΠΈΠ·ΠΈΡΠ΅Π»ΡΠ½ΠΎ 1 ΡΠΌ. ΠΡΠ»ΠΈ ΠΆΠ΅ Π½Π°ΠΊΠΎΠ²Π°Π»ΡΠ½Ρ ΠΏΠΎΠ΄ ΠΌΠΎΠ»ΠΎΡΠΎΠΌ Β«ΠΏΡΡΠ³Π°Π΅ΡΒ», ΡΠΎ ΡΡΠΎ Π·Π½Π°ΡΠΈΡ, ΡΡΠΎ ΠΏΠΎΠ²Π΅ΡΡ
Π½ΠΎΡΡΡ ΠΏΠΎΠ΄ΡΡΠΊΠΈ Π½Π΅ΡΠΎΠ²Π½Π°Ρ ΠΈ Π΅Π΅ ΡΠ»Π΅Π΄ΡΠ΅Ρ Π²ΡΡΠΎΠ²Π½ΡΡΡ.
Π’ΡΠ΅ΡΡΠ΅ΠΉ ΠΎΡΠ½ΠΎΠ²Π½ΠΎΠΉ ΡΠΎΡΡΠ°Π²Π»ΡΡΡΠ΅ΠΉ ΠΊΡΠ·Π½Π΅ΡΠ½ΠΎΠΉ ΠΎΡΠ½Π°ΡΡΠΊΠΈ ΡΠ²Π»ΡΠ΅ΡΡΡ ΡΡΡΠ½ΠΈΠΊ ΠΌΠ°ΡΡΠΎΠΉ 1β2,5 ΠΊΠ³ Π² Π·Π°Π²ΠΈΡΠΈΠΌΠΎΡΡΠΈ ΠΎΡ ΡΠΈΠ·ΠΈΡΠ΅ΡΠΊΠΈΡ
Π΄Π°Π½Π½ΡΡ
ΠΊΡΠ·Π½Π΅ΡΠ°. Π ΡΠΊΠΎΡΡΠΊΠ° ΡΡΡΠ½ΠΈΠΊΠ° Π΄ΠΎΠ»ΠΆΠ½Π° ΠΈΠΌΠ΅ΡΡ Π΄Π»ΠΈΠ½Ρ Π±ΠΎΠ»Π΅Π΅ 35 ΡΠΌ. ΠΠ»Ρ Π±ΠΎΠ»Π΅Π΅ ΠΊΡΡΠΏΠ½ΡΡ
ΡΠ°Π±ΠΎΡ ΠΏΡΠ΅Π΄Π½Π°Π·Π½Π°ΡΠ΅Π½Π° ΠΊΡΠ²Π°Π»Π΄Π° ΠΏΠΎΠ΄ΡΡΡΠ½ΠΎΠ³ΠΎ (ΠΌΠΎΠ»ΠΎΡΠΎΠ±ΠΎΠΉ ΠΌΠ°ΡΡΠΎΠΉ 3β10 ΠΊΠ³ Ρ ΡΡΠΊΠΎΡΡΡΡ Π΄Π»ΠΈΠ½ΠΎΠΉ 60β80 ΡΠΌ Π² Π·Π°Π²ΠΈΡΠΈΠΌΠΎΡΡΠΈ ΠΎΡ ΠΌΠ°ΡΡΡ ΠΊΡΠ²Π°Π»Π΄Ρ. ΠΠΎ Π²ΡΠ΅ΠΌΡ ΡΠ°Π±ΠΎΡΡ ΠΊΡΠ²Π°Π»Π΄Ρ Π΄Π΅ΡΠΆΠ°Ρ Π΄Π²ΡΠΌΡ ΡΡΠΊΠ°ΠΌΠΈ. Π’ΡΠ°Π΅ΠΊΡΠΎΡΠΈΡ, ΠΊΠΎΡΠΎΡΡΡ ΠΎΠΏΠΈΡΡΠ²Π°Π΅Ρ ΠΏΡΠΈ ΠΊΠΎΠ²ΠΊΠ΅ ΡΡΡΠΊΠ° ΠΈΠ»ΠΈ ΠΊΡΠ²Π°Π»Π΄Π°, Π΄ΠΎΠ»ΠΆΠ½Π° Π±ΡΡΡ Π½Π΅ ΠΏΡΡΠΌΠΎΠΉ, Π° ΡΠΊΡΡΠ³Π»Π΅Π½Π½ΠΎΠΉ. ΠΠ»Ρ Π΄Π΅ΡΠΆΠ°Π½ΠΈΡ Π½Π°Π³ΡΠ΅ΡΠΎΠ³ΠΎ ΠΌΠ°ΡΠ΅ΡΠΈΠ°Π»Π° ΡΠ»ΡΠΆΠ°Ρ ΠΊΠ»Π΅ΡΠΈ. ΠΡΠ½ΠΎΠ²Π½ΠΎΠΉ Π½Π°Π±ΠΎΡ ΠΊΠ»Π΅ΡΠ΅ΠΉ Π΄Π»Ρ ΠΏΠΎΠ»ΠΎΡΠΎΠ²ΠΎΠ³ΠΎ ΠΈ ΠΊΡΡΠ³Π»ΠΎΠ³ΠΎ ΠΌΠ°ΡΠ΅ΡΠΈΠ°Π»Π° (ΡΠΈΡ. 3β6) Π²ΡΠΏΡΡΠΊΠ°Π΅ΡΡΡ ΡΠ΅ΡΠΈΠΉΠ½ΠΎ, ΠΊΠ»Π΅ΡΠΈ Π΄Π»Ρ ΡΠΏΠ΅ΡΠΈΠ°Π»ΡΠ½ΡΡ
ΡΠ°Π±ΠΎΡ ΠΊΡΠ·Π½Π΅Ρ Π΄Π΅Π»Π°Π΅Ρ ΡΠ΅Π±Π΅ ΡΠ°ΠΌ. ΠΡΠΎΠΌΠ΅ ΡΡΡΠ½ΠΈΠΊΠΎΠ², ΠΊΡΠ²Π°Π»Π΄ ΠΈ ΠΊΠ»Π΅ΡΠ΅ΠΉ Ρ
ΡΠ΄ΠΎΠΆΠ΅ΡΡΠ²Π΅Π½Π½ΠΎΠΉ ΠΊΠΎΠ²ΠΊΠΈ ΡΡΠ΅Π±ΡΡΡΡΡ ΡΠ°ΠΊΠΆΠ΅ Π·ΡΠ±ΠΈΠ»Π°, ΡΠΊΡΡΠ³Π»Π΅Π½Π½ΡΠ΅ ΠΌΠΎΠ»ΠΎΡΠΊΠΈ Π΄Π»Ρ ΠΏΡΠΎΡΡΠ³ΠΈΠ²Π°Π½ΠΈΡ(ΡΠΈΡ. 7), Π±ΠΎΡΠΎΠ΄ΠΊΠΈ (ΡΠΈΡ. 8), ΠΏΠΎΠ΄Π±ΠΎΠΉΠΊΠΈ Π΄Π»Ρ Π²ΡΡΠ°Π΄ΠΊΠΈ ΠΈ Π³Π»Π°Π΄ΠΈΠ»ΠΊΠΈ (ΡΠΈΡ. 9, 10).
Π ΠΈΡ.3. ΠΡΠ·Π½Π΅ΡΠ½ΡΠ΅ ΠΊΠ»Π΅ΡΠΈ Π΄Π»Ρ Π½Π°Π³ΡΠ΅ΡΠΎΠ³ΠΎ ΠΌΠ΅ΡΠ°Π»Π»Π° ΠΊΡΡΠ³Π»ΡΠΌΠΈ Π³ΡΠ±ΠΊΠ°ΠΌΠΈ Π ΠΈΡ.4. ΠΡΠ·Π½Π΅ΡΠ½ΡΠ΅ ΠΊΠ»Π΅ΡΠΈ Π΄Π»Ρ Π½Π°Π³ΡΠ΅ΡΠΎΠ³ΠΎ ΠΌΠ΅ΡΠ°Π»Π»Π° Ρ ΠΏΡΡΠΌΠΎΡΠ³ΠΎΠ»ΡΠ½ΡΠΌΠΈ Π³ΡΠ±ΠΊΠ°ΠΌΠΈ. Π ΠΈΡ.5. ΠΡΠ·Π½Π΅ΡΠ½ΡΠ΅ ΠΊΠ»Π΅ΡΠΈ Β«Π²ΠΎΠ»ΡΡΡ ΠΏΠ°ΡΡΡΒ» Π ΠΈΡ.6. ΠΡΠ·Π½Π΅ΡΠ½ΡΠ΅ ΠΊΠ»Π΅ΡΠΈ Π΄Π»Ρ Π½Π°Π³ΡΠ΅ΡΠΎΠ³ΠΎ ΠΌΠ΅ΡΠ°Π»Π»Π° ΠΏΠ»ΠΎΡΠΊΠΈΠ΅ |
ΠΡΠ±ΠΈΠ»Π° Π΄Π΅Π»Π°ΡΡ Π΄Π²ΡΡ
ΡΠΈΠΏΠΎΠ²: Ρ ΡΠΎΠ½ΠΊΠΈΠΌ Π»Π΅Π·Π²ΠΈΠ΅ΠΌ Π΄Π»Ρ Π³ΠΎΡΡΡΠ΅ΠΉ ΡΡΠ±ΠΊΠΈ, Ρ Π±ΠΎΠ»Π΅Π΅ ΡΠΎΠ»ΡΡΡΠΌ Π΄Π»Ρ ΡΡΠ±ΠΊΠΈ Ρ
ΠΎΠ»ΠΎΠ΄Π½ΠΎΠ³ΠΎ ΠΌΠ΅ΡΠ°Π»Π»Π°. ΠΠ΅Π·Π²ΠΈΡ Π·ΡΠ±ΠΈΠ» Π΄Π»Ρ Π±ΠΎΠ»ΡΡΠ΅ΠΉ ΡΠΎΡ
ΡΠ°Π½Π½ΠΎΡΡΠΈ ΡΠ»Π΅Π΄ΡΠ΅Ρ ΠΏΠ΅ΡΠ΅Π΄ ΡΡΠ±ΠΊΠΎΠΉ ΠΏΡΠΎΡΠΈΡΠ°ΡΡ ΡΡΡΠΏΠΊΠΎΠΉ, ΡΠΌΠΎΡΠ΅Π½Π½ΠΎΠΉ Π² ΠΌΠ°ΡΠ»Π΅. Π ΡΡΠΎΠΌ ΡΠ»ΡΡΠ°Π΅ Π»Π΅Π·Π²ΠΈΠ΅ ΠΏΡΠΈ ΡΠ΄Π°ΡΠ΅ ΠΊΡΠ²Π°Π»Π΄ΠΎΠΉ Π½Π΅ ΡΡ
Π²Π°ΡΠΈΡΡΡ Ρ ΠΌΠ΅ΡΠ°Π»Π»ΠΎΠΌ, Π² ΡΠΎ Π²ΡΠ΅ΠΌΡ ΠΊΠ°ΠΊ ΡΡΡ
ΠΎΠ΅ Π»Π΅Π·Π²ΠΈΠ΅ ΠΎΠ±ΡΡΠ½ΠΎ ΡΡ
Π²Π°ΡΡΠ²Π°Π΅ΡΡΡ Ρ ΠΌΠ΅ΡΠ°Π»Π»ΠΎΠΌ Π½Π°ΡΡΠΎΠ»ΡΠΊΠΎ ΠΊΡΠ΅ΠΏΠΊΠΎ, ΡΡΠΎ ΠΌΠΎΠΆΠ΅Ρ Π²ΡΠΊΡΠΎΡΠΈΡΡΡΡ. ΠΡΠ΅ ΠΏΠ΅ΡΠ΅ΡΠΈΡΠ»Π΅Π½Π½ΡΠ΅ Π²ΠΈΠ΄Ρ ΠΈΠ½ΡΡΡΡΠΌΠ΅Π½ΡΠ° Π΄Π΅Π»Π°ΡΡ Π΄Π²ΡΡΡΠΎΡΠΎΠ½Π½ΠΈΠΌΠΈ: Π²Π΅ΡΡ
Π½ΡΡ ΡΠ°ΡΡΡ Π±ΠΎΠ»Π΅Π΅ Π΄Π»ΠΈΠ½Π½Π°Ρ ΠΈ Π½Π΅Π·Π°ΠΊΠ°Π»Π΅Π½Π½Π°Ρ, Π½ΠΈΠΆΠ½ΡΡ β ΠΊΠΎΡΠΎΡΠ΅ ΠΈ Π·Π°ΠΊΠ°Π»Π΅Π½Π°. Π ΠΊΡΡΠΏΠ½ΡΡ
ΠΌΠ°ΡΡΠ΅ΡΡΠΊΠΈΡ
ΠΌΠΎΠΆΠ΅Ρ Π±ΡΡΡ ΡΡΡΠ°Π½ΠΎΠ²Π»Π΅Π½ ΠΌΠ΅Ρ
Π°Π½ΠΈΡΠ΅ΡΠΊΠΈΠΉ ΠΌΠΎΠ»ΠΎΡ, ΡΠ°ΠΊ ΠΊΠ°ΠΊ ΠΎΠ½ ΠΎΠ±Π»Π΅Π³ΡΠ°Π΅Ρ ΡΠ°Π±ΠΎΡΡ. Π Π΅ΡΡΠΎΡΠ½ΠΎ-ΠΏΡΡΠΆΠΈΠ½Π½ΡΠΉ ΠΌΠΎΠ»ΠΎΡ, ΠΏΠΎΠΊΠ°Π·Π°Π½Π½ΡΠΉ Π½Π° ΡΠΈΡ. 11, Π²ΠΏΠΎΠ»Π½Π΅ Π΄ΠΎΡΡΠ°ΡΠΎΡΠ΅Π½ Π΄Π»Ρ Π½ΡΠΆΠ΄ Ρ
ΡΠ΄ΠΎΠΆΠ΅ΡΡΠ²Π΅Π½Π½ΠΎΠΉ ΠΊΠΎΠ²ΠΊΠΈ. Π Π±ΠΎΠ»ΡΡΠΈΡ
ΠΊΡΠ·Π½ΠΈΡΠ°Ρ
ΠΈΠ½ΠΎΠ³Π΄Π° ΡΡΡΠ°Π½Π°Π²Π»ΠΈΠ²Π°ΡΡ ΠΏΠ½Π΅Π²ΠΌΠ°ΡΠΈΡΠ΅ΡΠΊΠΈΠ΅ ΠΌΠΎΠ»ΠΎΡΡ, Π° Π² ΡΠ»ΡΡΠ°Π΅ Π½Π΅ΠΎΠ±Ρ
ΠΎΠ΄ΠΈΠΌΠΎΡΡΠΈ Π±ΠΎΠ»ΡΡΠΈΡ
ΡΡΠΈΠ»ΠΈΠΉ β ΠΌΠΎΠ»ΠΎΡΡ ΡΡΠΈΠΊΡΠΈΠΎΠ½Π½ΡΠ΅. ΠΠΏΡΠΎΡΠ΅ΠΌ Π΄Π»Ρ Ρ
ΡΠ΄ΠΎΠΆΠ΅ΡΡΠ²Π΅Π½Π½ΠΎΠΉ ΠΊΠΎΠ²ΠΊΠΈ ΡΡΠΎ ΠΎΠ±ΠΎΡΡΠ΄ΠΎΠ²Π°Π½ΠΈΠ΅ ΠΎΠ±ΡΡΠ½ΠΎ Π½Π΅ ΠΈΡΠΏΠΎΠ»ΡΠ·ΡΡΡ.
Β
ΠΡΠΎΡ ΠΎΡΠ½ΠΎΠ²Π½ΠΎΠΉ Π½Π°Π±ΠΎΡ ΠΈΠ½ΡΡΡΡΠΌΠ΅Π½ΡΠ° Π΄ΠΎΠΏΠΎΠ»Π½ΡΡΡ ΡΠ°Π·Π»ΠΈΡΠ½ΡΠ΅ ΠΎΠΏΡΠ°Π²ΠΊΠΈ (ΡΠΈΡ. 12β14) Π±ΠΎΠΉΠ½ΡΠ΅ ΠΏΠ»ΠΈΡΡ (ΠΊΡΠ·Π½Π΅ΡΠ½ΡΠ΅ ΠΏΡΠΎΠ±ΠΎΠΉΠ½ΠΈΡΡ, ΡΠΈΡ. 15), ΠΏΠΎΠ΄ΡΠ΅ΡΠΊΠΈ (ΡΠΈΡ.16), Π½Π°ΠΊΠΎΠ½Π΅ΡΠ½ΠΈΠΊΠΈ (ΡΠΈΡ.17) ΠΈ ΠΎΠ±ΠΆΠΈΠΌΠΊΠΈ (ΡΠΈΡ. 18β20). ΠΡΠΎΡ ΠΈΠ½ΡΡΡΡΠΌΠ΅Π½Ρ ΠΊΡΠ·Π½Π΅Ρ-Ρ
ΡΠ΄ΠΎΠΆΠ½ΠΈΠΊ Π΄Π΅Π»Π°Π΅Ρ ΡΠ°ΠΌ Π² Π·Π°Π²ΠΈΡΠΈΠΌΠΎΡΡΠΈ ΠΎΡ ΠΏΠΎΡΡΠ΅Π±Π½ΠΎΡΡΠΈ. ΠΠ΅ ΡΠ»Π΅Π΄ΡΠ΅Ρ Π΄ΠΎΠΏΡΡΠΊΠ°ΡΡ ΠΎΡΡΡΡΡΡΠ²ΠΈΡ ΡΠ°ΠΊΠΆΠ΅ ΡΠΏΠ΅ΡΠ°ΠΊΠΎΠ², ΠΊΠΎΡΠΎΡΡΡ
ΠΈΠΌΠ΅Π΅ΡΡΡ Π½Π΅ΡΠΊΠΎΠ»ΡΠΊΠΎ Π²ΠΈΠ΄ΠΎΠ² (ΡΠΈΡ. 22β24), Π²ΡΠ΅ ΡΠΌΠΎΠ³ΡΡ ΠΏΡΠΈΠ³ΠΎΠ΄ΠΈΡΡΡΡ. ΠΡΠ΅Π½Ρ ΠΏΠΎΠ»Π΅Π·Π½ΠΎΠΉ ΠΌΠΎΠΆΠ΅Ρ ΠΎΠΊΠ°Π·Π°ΡΡΡΡ ΠΏΡΠ°Π²ΠΈΠ»ΡΠ½Π°Ρ ΠΏΠ»ΠΈΡΠ°, ΠΏΠΎΠ²Π΅ΡΡ
Π½ΠΎΡΡΡ ΠΊΠΎΡΠΎΡΠΎΠΉ, Π° ΡΠ°ΠΊΠΆΠ΅ ΠΊΠ°ΠΊ ΠΌΠΈΠ½ΠΈΠΌΡΠΌ Π΄Π²Π΅ ΡΠΎΡΠ΅Π΄Π½ΠΈΡ
Π³ΡΠ°Π½ΠΈ Π½Π΅ Π΄ΠΎΠ»ΠΆΠ½Ρ Π±ΡΡΡ ΠΏΡΠΎΡΡΡΠΎΠ³Π°Π½Ρ ΠΈ ΠΎΠ±ΡΠ°Π·ΠΎΠ²ΡΠ²Π°ΡΡ ΠΌΠ΅ΠΆΠ΄Ρ ΡΠΎΠ±ΠΎΠΉ ΠΏΡΡΠΌΠΎΠΉ ΡΠ³ΠΎΠ». Π ΠΌΠ°ΡΡΠ΅ΡΡΠΊΠΎΠΉ Π΄ΠΎΠ»ΠΆΠ½Ρ Π±ΡΡΡ ΡΠ°ΠΊΠΆΠ΅ ΡΠΎΡΠΌΠΎΠ²Π°Π»ΡΠ½Π°Ρ ΠΏΠ»ΠΈΡΠ° (ΡΠΎΡΠΌΠ°) ΠΈ Π³Π²ΠΎΠ·Π΄ΠΈΠ»ΡΠ½Π°Ρ (ΡΠΈΡ. 25, 26). ΠΡΠΈ ΠΏΠ»ΠΈΡΡ ΡΠΊΠ»Π°Π΄ΡΠ²Π°ΡΡ Π² Π±Π°ΡΠΌΠ°ΠΊ, ΠΈΠ·Π³ΠΎΡΠΎΠ²Π»Π΅Π½Π½ΡΠΉ ΠΈΠ· ΡΠ°ΡΠΎΠ½Π½ΠΎΠ³ΠΎ ΡΡΠ°Π»ΡΠ½ΠΎΠ³ΠΎ ΠΏΡΠΎΠΊΠ°ΡΠ°, ΠΈΠ»ΠΈ Π² Π΄Π΅ΡΠ΅Π²ΡΠ½Π½ΡΡ ΠΏΠΎΠ΄ΡΡΠ°Π²ΠΊΡ. ΠΠ»ΠΈΡΡ Π² Π±Π°ΡΠΌΠ°ΠΊΠ΅ ΠΈΠ»ΠΈ ΠΏΠΎΠ΄ΡΡΠ°Π²ΠΊΠ΅ Π΄ΠΎΠ»ΠΆΠ½Ρ ΠΏΠ»ΠΎΡΠ½ΠΎ ΡΠΈΠ΄Π΅ΡΡ, ΡΠ°ΠΊ ΠΊΠ°ΠΊ ΠΎΠ½ΠΈ ΠΎΠ±ΡΡΠ½ΠΎ Π»ΠΈΡΡΠ΅ ΠΈ ΠΏΠΎΠ΄ ΡΠ΄Π°ΡΠ°ΠΌΠΈ ΠΊΡΠ²Π°Π»Π΄Ρ ΠΌΠΎΠ³ΡΡ ΡΡΠ΅ΡΠ½ΡΡΡ. Π ΡΠΊΠΎΡΡΠΊΠΈ ΡΡΡΠ½ΠΈΠΊΠΎΠ², ΠΊΡΠ²Π°Π»Π΄ ΠΈ Π΄ΡΡΠ³ΠΎΠ³ΠΎ ΠΈΠ½ΡΡΡΡΠΌΠ΅Π½ΡΠ° Π΄Π»Ρ Ρ
ΡΠ΄ΠΎΠΆΠ΅ΡΡΠ²Π΅Π½Π½ΠΎΠΉ ΠΊΠΎΠ²ΠΊΠΈ Π΄ΠΎΠ»ΠΆΠ½Ρ Π±ΡΡΡ Π²ΡΡΠΎΠΊΠΎΠ³ΠΎ ΠΊΠ°ΡΠ΅ΡΡΠ²Π° Π²ΠΎ ΠΈΠ·Π±Π΅ΠΆΠ°Π½ΠΈΠ΅ Π²ΠΎΠ·ΠΌΠΎΠΆΠ½ΡΡ
ΡΡΠ°Π²ΠΌ. Π ΡΠΊΠΎΡΡΠΊΠΈ Π΄ΠΎΠ»ΠΆΠ½Ρ Π±ΡΡΡ ΠΈΠ·Π³ΠΎΡΠΎΠ²Π»Π΅Π½Ρ ΠΈΠ· Π΄ΠΎΠ±ΡΠΎΠΊΠ°ΡΠ΅ΡΡΠ²Π΅Π½Π½ΠΎΠ³ΠΎ Π΄Π΅ΡΠ΅Π²Π°, Π»ΡΡΡΠ΅ Π²ΡΠ΅Π³ΠΎ ΠΈΠ· Π³ΡΠ°Π±Π° ΠΈΠ»ΠΈ Π°ΠΌΠ΅ΡΠΈΠΊΠ°Π½ΡΠΊΠΎΠ³ΠΎ ΠΎΡΠ΅Ρ
ΠΎΠ²ΠΎΠ³ΠΎ Π΄Π΅ΡΠ΅Π²Π°. ΠΠ½ΠΎΠ³Π΄Π° ΡΠ΅ΠΊΠΎΠΌΠ΅Π½Π΄ΡΡΡ Π΄Π»Ρ ΡΡΠΊΠΎΡΡΠΎΠΊ Π±Π΅Π»ΡΡ Π°ΠΊΠ°ΡΠΈΡ, Π½ΠΎ ΠΏΠΎΡΠ»Π΅ ΡΡΡΠΊΠΈ ΠΎΠ½Π° ΡΡΠ°Π½ΠΎΠ²ΠΈΡΡΡ ΠΎΡΠ΅Π½Ρ ΡΠ²Π΅ΡΠ΄ΠΎΠΉ ΠΈ ΠΏΠΎΡΡΠΎΠΌΡ Ρ
ΡΡΠΏΠΊΠΎΠΉ.
ΠΠ»Ρ Ρ
ΠΎΠ»ΠΎΠ΄Π½ΠΎΠΉ ΠΎΠ±ΡΠ°Π±ΠΎΡΠΊΠΈ ΠΊΡΠ·Π½Π΅Ρ-Ρ
ΡΠ΄ΠΎΠΆΠ½ΠΈΠΊ Π΄ΠΎΠ»ΠΆΠ΅Π½ ΠΈΠΌΠ΅ΡΡ Π΅ΡΠ΅ ΠΌΠ½ΠΎΠ³ΠΈΠ΅ Π΄ΠΎΠΏΠΎΠ»Π½ΠΈΡΠ΅Π»ΡΠ½ΡΠ΅ ΠΈΠ½ΡΡΡΡΠΌΠ΅Π½ΡΡ. Π Π½ΠΈΠΌ ΠΎΡΠ½ΠΎΡΡΡΡΡ, Π½Π°ΠΏΡΠΈΠΌΠ΅Ρ, ΠΈΠ½ΡΡΡΡΠΌΠ΅Π½ΡΡ Π΄Π»Ρ ΡΠΈΡΠ»Π΅Π½ΠΈΡ (Π½Π°ΠΊΠ°ΡΠ½ΠΈΠΊΠΈ), Π·Π΅ΡΠ½Π΅Π½ΠΈΡ, ΡΠ°Π·Π³ΠΎΠ½ΠΊΠΈ, Π° ΡΠ°ΠΊΠΆΠ΅ ΡΠ°Π·Π»ΠΈΡΠ½ΡΠ΅ ΠΈΠ½ΡΡΡΡΠΌΠ΅Π½ΡΡ Π΄Π»Ρ ΡΠ΅ΠΊΠ°Π½ΠΊΠΈ, Π² ΡΠΎΠΌ ΡΠΈΡΠ»Π΅ ΡΠ΅ΠΊΠ°Π½Ρ (ΡΠΈΡ. 27β49). ΠΡ
Π½Π°Π·Π½Π°ΡΠ΅Π½ΠΈΠ΅ ΠΎΠΏΠΈΡΠ°Π½ΠΎ Π² ΡΠΎΠΎΡΠ²Π΅ΡΡΡΠ²ΡΡΡΠΈΡ
ΡΠ°Π·Π΄Π΅Π»Π°Ρ
. ΠΠ»Ρ ΡΠΎΠ½ΠΊΠΈΡ
ΠΎΡΠ΄Π΅Π»ΠΎΡΠ½ΡΡ
ΡΠ°Π±ΠΎΡ Π½Π΅ΠΎΠ±Ρ
ΠΎΠ΄ΠΈΠΌΠΎ ΠΈΠΌΠ΅ΡΡ ΠΊΠΎΠΌΠΏΠ»Π΅ΠΊΡΡ ΡΠ°Π·Π»ΠΈΡΠ½ΡΡ
Π½Π°ΠΏΠΈΠ»ΡΠ½ΠΈΠΊΠΎΠ², ΡΠ°Π±Π΅ΡΠΎΠ², ΡΠ΅Π·ΡΠΎΠ² ΠΈ ΡΠ΅ΠΊΠ°Π½ΠΎΡΠ½ΡΡ
ΡΡΠ°ΠΌΠΏΠΎΠ². Π ΠΌΠ°ΡΡΠ΅ΡΡΠΊΠΎΠΉ Ρ
ΡΠ΄ΠΎΠΆΠ΅ΡΡΠ²Π΅Π½Π½ΠΎΠΉ ΠΊΠΎΠ²ΠΊΠΈ ΠΆΠ΅Π»Π°ΡΠ΅Π»ΡΠ½ΠΎ ΠΈΠΌΠ΅ΡΡ ΡΠ°ΠΊΠΆΠ΅ Π²ΡΠ΅ ΡΠΎΠ²ΡΠ΅ΠΌΠ΅Π½Π½ΡΠ΅ ΡΡΠ°Π½ΠΊΠΈ, ΠΎΠ±Π»Π΅Π³ΡΠ°ΡΡΠΈΠ΅ ΡΠ°Π±ΠΎΡΡ. Π’Π°ΠΊ ΠΊΠ°ΠΊ ΠΈΠ½ΠΎΠ³Π΄Π° ΠΎΡΠ²Π΅ΡΡΡΠΈΠ΅ Π² ΠΈΠ·Π΄Π΅Π»ΠΈΠΈ Π±ΡΡΡΡΠ΅Π΅ ΠΏΡΠΎΡΠ²Π΅ΡΠ»ΠΈΡΡ, ΡΠ΅ΠΌ ΠΏΡΠΎΡΠΈΡΡ, ΠΌΠ°ΡΡΠ΅ΡΡΠΊΠ°Ρ Π΄ΠΎΠ»ΠΆΠ½Π° Π±ΡΡΡ ΠΎΠ±ΠΎΡΡΠ΄ΠΎΠ²Π°Π½Π° Π²Π΅ΡΡΠΈΠΊΠ°Π»ΡΠ½ΠΎ-ΡΠ²Π΅ΡΠ»ΠΈΠ»ΡΠ½ΡΠΌ ΡΡΠ°Π½ΠΊΠΎΠΌ. Π ΡΡΠ°ΠΆΠ½ΡΠ΅ Π½ΠΎΠΆΠ½ΠΈΡΡ, ΠΊΠΎΡΠΎΡΡΠΌΠΈ ΠΌΠΎΠΆΠ½ΠΎ ΡΠ΅Π·Π°ΡΡ Π΄Π°ΠΆΠ΅ ΠΌΠ°ΡΠ΅ΡΠΈΠ°Π» Π±ΠΎΠ»ΡΡΠΎΠΉ ΡΠΎΠ»ΡΠΈΠ½Ρ, Π½ΡΠΆΠ½Ρ Π² ΡΠ°Π±ΠΎΡΠ΅. ΠΠ»Π°ΡΡΠΈΡΠ΅ΡΠΊΡΡ Π³ΠΎΡΡΡΡΡ ΡΠ²Π°ΡΠΊΡ ΠΈΡΠΏΠΎΠ»ΡΠ·ΡΡΡ Π² Π½Π°ΡΡΠΎΡΡΠ΅Π΅ Π²ΡΠ΅ΠΌΡ ΠΎΡΠ΅Π½Ρ ΡΠ΅Π΄ΠΊΠΎ. ΠΠΎΡΡΠΎΠΌΡ Π² ΠΌΠ°ΡΡΠ΅ΡΡΠΊΠΎΠΉ Π½Π΅ΠΎΠ±Ρ
ΠΎΠ΄ΠΈΠΌΠ° ΡΡΡΠ°Π½ΠΎΠ²ΠΊΠ° Π΄Π»Ρ Π³Π°Π·ΠΎΠ²ΠΎΠΉ ΡΠ²Π°ΡΠΊΠΈ. ΠΠ΅ ΠΏΠΎΠΌΠ΅ΡΠ°Π΅Ρ ΠΈ ΡΠ»Π΅ΠΊΡΡΠΎΡΠ²Π°ΡΠΎΡΠ½ΡΠΉ Π°ΠΏΠΏΠ°ΡΠ°Ρ. ΠΠ·Π΄Π΅Π»ΠΈΠ΅ Ρ
ΡΠ΄ΠΎΠΆΠ΅ΡΡΠ²Π΅Π½Π½ΠΎΠΉ ΠΊΠΎΠ²ΠΊΠΈ Π΄ΠΎΠ»ΠΆΠ½ΠΎ Π±ΡΡΡ ΠΈΡΠΊΡΡΠ½ΠΎ ΠΎΠ±ΡΠ°Π±ΠΎΡΠ°Π½ΠΎ, Π² Π½Π΅ΠΌ Π΄ΠΎΠ»ΠΆΠ΅Π½ Π²ΡΠ΅Π³Π΄Π° ΠΏΡΠΎΡΠ²Π»ΡΡΡΡΡ Π²ΡΡΠΎΠΊΠΈΠΉ ΡΡΠΎΠ²Π΅Π½Ρ ΠΌΠ°ΡΡΠ΅ΡΡΡΠ²Π°. ΠΠ΄Π½Π°ΠΊΠΎ ΡΡΠΎ Π½Π΅ Π·Π½Π°ΡΠΈΡ, ΡΡΠΎ ΠΊΡΠ·Π½Π΅Ρ-Ρ
ΡΠ΄ΠΎΠΆΠ½ΠΈΠΊ Π΄ΠΎΠ»ΠΆΠ΅Π½ ΠΏΡΠΈΠ΄Π΅ΡΠΆΠΈΠ²Π°ΡΡΡΡ Π»ΠΈΡΡ ΠΏΡΠΈΠ΅ΠΌΠΎΠ² ΡΠ°Π±ΠΎΡΡ, ΠΏΠ΅ΡΠ΅Π½ΡΡΡΡ
Ρ ΡΡΠ°ΡΡΡ
ΠΌΠ°ΡΡΠ΅ΡΠΎΠ² Ρ
ΡΠ΄ΠΎΠΆΠ΅ΡΡΠ²Π΅Π½Π½ΠΎΠΉ ΠΊΠΎΠ²ΠΊΠΈ, ΠΈ ΠΎΠΏΠΈΠ»ΠΈΠ²Π°ΡΡ, Π½Π°ΠΏΡΠΈΠΌΠ΅Ρ, ΡΠ²Π°ΡΠ½ΠΎΠΉ ΡΠΎΠ² Π²ΡΡΡΠ½ΡΡ Π½Π°ΠΏΠΈΠ»ΡΠ½ΠΈΠΊΠΎΠΌ, Π° Π½Π΅ ΠΈΡΠΏΠΎΠ»ΡΠ·ΠΎΠ²Π°ΡΡ Π΄Π»Ρ ΡΡΠΎΠΉ ΡΠ΅Π»ΠΈ Π²ΡΡΠΎΠΊΠΎΠΎΠ±ΠΎΡΠΎΡΠ½ΡΡ Π±ΠΎΡΠΌΠ°ΡΠΈΠ½Ρ, ΠΏΡΠΈΠΌΠ΅Π½Π΅Π½ΠΈΠ΅ ΠΊΠΎΡΠΎΡΠΎΠΉ ΡΡΠΊΠΎΡΡΠ΅Ρ ΡΠ°Π±ΠΎΡΡ Π² 20 ΡΠ°Π·. ΠΠ°ΡΡΠ΅ΡΡΠΊΠ°Ρ Ρ
ΡΠ΄ΠΎΠΆΠ΅ΡΡΠ²Π΅Π½Π½ΠΎΠΉ ΠΊΠΎΠ²ΠΊΠΈ Π΄ΠΎΠ»ΠΆΠ½Π° Π±ΡΡΡ ΠΎΠ±ΠΎΡΡΠ΄ΠΎΠ²Π°Π½Π° Π½Π΅ ΡΠΎΠ»ΡΠΊΠΎ ΠΏΠΎΠ»Π½ΡΠΌ Π½Π°Π±ΠΎΡΠΎΠΌ ΡΡΠ°Π΄ΠΈΡΠΈΠΎΠ½Π½ΡΡ
ΠΈΠ½ΡΡΡΡΠΌΠ΅Π½ΡΠΎΠ², Π½ΠΎ ΠΈ ΠΏΠΎΠ»Π½ΡΠΌ Π½Π°Π±ΠΎΡΠΎΠΌ ΡΠΎΠ²ΡΠ΅ΠΌΠ΅Π½Π½ΡΡ
ΠΈΠ½ΡΡΡΡΠΌΠ΅Π½ΡΠΎΠ² ΠΈ ΡΡΠ°Π½ΠΊΠΎΠ², ΠΊΠΎΡΠΎΡΡΠ΅ ΠΎΠ±Π»Π΅Π³ΡΠ°ΡΡ ΡΡΡ ΡΡΡΠ΄ΠΎΠ΅ΠΌΠΊΡΡ ΡΠ°Π±ΠΎΡΡ.
ΠΡΠ½ΠΎΠ²Π½ΡΠ΅ ΡΠΏΠΎΡΠΎΠ±Ρ Π΄Π΅ΡΠΎΡΠΌΠΈΡΠΎΠ²Π°Π½ΠΈΡ ΠΊΠΎΠ²ΠΊΠΎΠ³ΠΎ ΠΆΠ΅Π»Π΅Π·Π°.
ΠΡΠ½ΠΎΠ²Π½ΡΠΌ ΡΠΏΠΎΡΠΎΠ±ΠΎΠΌ Π΄Π΅ΡΠΎΡΠΌΠΈΡΠΎΠ²Π°Π½ΠΈΡ ΠΊΠΎΠ²ΠΊΠΎΠ³ΠΎ ΠΆΠ΅Π»Π΅Π·Π° ΡΠ²Π»ΡΠ΅ΡΡΡ ΠΊΠΎΠ²ΠΊΠ°. Π£Π΄Π°ΡΡ ΠΊΡΠ²Π°Π»Π΄Ρ ΠΈΠ»ΠΈ ΠΌΠΎΠ»ΠΎΡΠ° ΡΠΎΠΎΠ±ΡΠ°ΡΡ ΠΌΠ°ΡΠ΅ΡΠΈΠ°Π»Ρ Π½Π΅ΠΎΠ±Ρ
ΠΎΠ΄ΠΈΠΌΡΡ ΡΠΎΡΠΌΡ, ΠΏΡΠΈ ΡΡΠΎΠΌ ΠΊΠΎΠ²Π°ΡΡ ΠΌΠΎΠΆΠ½ΠΎ Π»ΠΈΡΡ ΠΏΠ»Π°ΡΡΠΈΡΠ½ΡΠ΅ ΠΌΠ΅ΡΠ°Π»Π»Ρ ΠΈ ΡΠΏΠ»Π°Π²Ρ ΠΈ, ΠΊΠ°ΠΊ ΠΏΡΠ°Π²ΠΈΠ»ΠΎ, Π² Π½Π°Π³ΡΠ΅ΡΠΎΠΌ ΡΠΎΡΡΠΎΡΠ½ΠΈΠΈ. Π Π°Π·Π»ΠΈΡΠ°ΡΡ ΡΠ²ΠΎΠ±ΠΎΠ΄Π½ΡΡ ΠΊΠΎΠ²ΠΊΡ, ΠΏΡΠΈ ΠΊΠΎΡΠΎΡΠΎΠΉ ΡΠΎΡΠΌΡ ΠΈΠ·Π΄Π΅Π»ΠΈΡ ΡΠΎΠΎΠ±ΡΠ°ΡΡ ΡΠ°Π·Π»ΠΈΡΠ½ΠΎ ΠΎΡΡΡΠ΅ΡΡΠ²Π»ΡΠ΅ΠΌΡΠΌΠΈ ΡΠ΄Π°ΡΠ°ΠΌΠΈ, ΠΈ ΠΊΠΎΠ²ΠΊΡ Π² ΡΡΠ°ΠΌΠΏΠ°Ρ
, Π³Π΄Π΅ Π½ΡΠΆΠ½ΡΡ ΡΠΎΡΠΌΡ ΠΏΠΎΠ»ΡΡΠ°ΡΡ Π²Π΄Π°Π²Π»ΠΈΠ²Π°Π½ΠΈΠ΅ΠΌ ΠΌΠ°ΡΠ΅ΡΠΈΠ°Π»ΠΎΠ² Π² ΠΌΠ΅ΡΠ°Π»Π»ΠΈΡΠ΅ΡΠΊΡΡ ΡΠΎΡΠΌΡ, Π½Π°Π·ΡΠ²Π°Π΅ΠΌΡΡ ΡΡΠ°ΠΌΠΏΠΎΠΌ. Π Π·Π°Π²ΠΈΡΠΈΠΌΠΎΡΡΠΈ ΠΎΡ ΡΠΏΠΎΡΠΎΠ±Π° ΡΠ°Π±ΠΎΡΡ ΠΊΠΎΠ²ΠΊΠ° ΠΌΠΎΠΆΠ΅Ρ Π±ΡΡΡ ΡΡΡΠ½ΠΎΠΉ ΠΈΠ»ΠΈ ΠΌΠ°ΡΠΈΠ½Π½ΠΎΠΉ. ΠΠ΅Π»ΠΊΠΈΠ΅ ΠΈΠ·Π΄Π΅Π»ΠΈΡ ΠΊΡΠ·Π½Π΅Ρ ΠΈΠ·Π³ΠΎΡΠΎΠ²Π»ΡΠ΅Ρ Π²ΡΡΡΠ½ΡΡ Π½Π° Π½Π°ΠΊΠΎΠ²Π°Π»ΡΠ½Π΅, Π° Π΄Π»Ρ ΠΎΠ±ΡΠ°Π±ΠΎΡΠΊΠΈ Π±ΠΎΠ»Π΅Π΅ ΠΊΡΡΠΏΠ½ΡΡ
Π·Π°Π³ΠΎΡΠΎΠ²ΠΎΠΊ ΠΏΡΠΈΠΌΠ΅Π½ΡΠ΅Ρ ΠΌΠΎΠ»ΠΎΡ. Π Π°Π½ΡΡΠ΅ ΡΡΡ ΡΠ°Π±ΠΎΡΡ Π²ΡΠΏΠΎΠ»Π½ΡΠ»ΠΈ Π΄Π²Π° ΠΈΠ»ΠΈ Π±ΠΎΠ»Π΅Π΅ ΠΊΡΠ·Π½Π΅ΡΠΎΠ² Π²ΠΌΠ΅ΡΡΠ΅. Π‘ΡΠ°ΡΡΠΈΠΉ ΠΊΡΠ·Π½Π΅Ρ Π΄Π΅ΡΠΆΠ°Π» Π·Π°Π³ΠΎΡΠΎΠ²ΠΊΡ ΠΈ ΡΡΡΠ½ΠΈΠΊΠΎΠΌ ΠΏΠΎΠΊΠ°Π·ΡΠ²Π°Π» Π½Π°ΠΏΡΠ°Π²Π»Π΅Π½ΠΈΠ΅ ΠΊΠΎΠ²ΠΊΠΈ. Π Π½Π°ΡΡΠΎΡΡΠ΅Π΅ Π²ΡΠ΅ΠΌΡ ΠΊΡΡΠΏΠ½ΡΠ΅ Π·Π°Π³ΠΎΡΠΎΠ²ΠΊΠΈ, ΠΊΠ°ΠΊ Π±ΡΠ»ΠΎ ΡΠΊΠ°Π·Π°Π½ΠΎ, ΠΎΠ±ΡΠ°Π±Π°ΡΡΠ²Π°ΡΡ Π½Π° ΠΌΠΎΠ»ΠΎΡΠ΅. ΠΠΎΠ»ΠΎΡ ΡΠΎΡΡΠΎΠΈΡ ΠΈΠ· ΡΡΠ°Π½ΠΈΠ½Ρ, Π±Π°Π±Ρ, ΡΠ°Π±ΠΎΡΠ°, ΠΏΠΎΠ΄ΡΡΠΊΠΈ ΠΈ Π±ΠΎΠΉΠΊΠΎΠ². Π¨Π°Π±ΠΎΡ ΡΡΡΠ°Π½ΠΎΠ²Π»Π΅Π½ Π½Π° ΡΠΎΠ±ΡΡΠ²Π΅Π½Π½ΠΎΠΌ ΡΡΠ½Π΄Π°ΠΌΠ΅Π½ΡΠ΅, ΠΎΡΠ΄Π΅Π»ΡΠ½ΠΎΠΌ ΠΎΡ ΡΡΠ½Π΄Π°ΠΌΠ΅Π½ΡΠ° ΡΡΠ°Π½ΠΈΠ½Ρ Π΄Π»Ρ ΡΠΎΠ³ΠΎ, ΡΡΠΎΠ±Ρ ΠΎΡ ΡΠ°Π±ΠΎΡΠ° Π½Π΅ ΠΏΠ΅ΡΠ΅Π΄Π°Π²Π°Π»ΠΈΡΡ ΡΠΎΡΡΡΡΠ΅Π½ΠΈΡ. ΠΠ°ΡΡΠ° ΡΠ°Π±ΠΎΡΠ°, ΠΈΠ·Π³ΠΎΡΠΎΠ²Π»Π΅Π½Π½ΠΎΠ³ΠΎ ΠΈΠ· ΡΠ΅ΡΠΎΠ³ΠΎ ΡΡΠ³ΡΠ½Π°, Π² 25 ΡΠ°Π· ΠΏΡΠ΅Π²ΠΎΡΡ
ΠΎΠ΄ΠΈΡ ΠΌΠ°ΡΡΡ Π±Π°Π±Ρ, ΡΡΠΎ ΡΠΎΠΎΡΠ½ΠΎΡΠ΅Π½ΠΈΠ΅ ΠΏΡΠΈΠ±Π»ΠΈΠ·ΠΈΡΠ΅Π»ΡΠ½ΠΎ ΡΠ°Π²Π½ΠΎ ΠΎΡΠ½ΠΎΡΠ΅Π½ΠΈΡ ΠΌΠ°ΡΡΡ ΠΏΠ°Π΄Π°ΡΡΠΈΡ
ΡΠ°ΡΡΠ΅ΠΉ ΠΌΠΎΠ»ΠΎΡΠ° ΠΊ ΠΌΠ°ΡΡΠ΅ Π·Π°Π³ΠΎΡΠΎΠ²ΠΊΠΈ. ΠΠ°Π·Π½Π°ΡΠ΅Π½ΠΈΠ΅ ΡΠ°Π±ΠΎΡΠ° β Π°ΠΌΠΎΡΡΠΈΠ·ΠΈΡΠΎΠ²Π°ΡΡ ΡΠ΄Π°ΡΡ ΠΌΠΎΠ»ΠΎΡΠ°. Π Π²Π΅ΡΡ
Π½Π΅ΠΉ ΡΠ°ΡΡΠΈ ΡΠ°Π±ΠΎΡΠ° Π½Π°Ρ
ΠΎΠ΄ΠΈΡΡΡ ΠΏΠΎΠ΄ΡΡΠΊΠ°. Π Π±Π°Π±Π΅ ΠΈ ΠΏΠΎΠ΄ΡΡΠΊΠ΅ ΠΈΠΌΠ΅ΡΡΡΡ ΠΏΠ°Π·Ρ, Π² ΠΊΠΎΡΠΎΡΡΡ
ΠΊΡΠ΅ΠΏΡΡΡΡ ΡΡΠ°Π»ΡΠ½ΡΠ΅ Π±ΠΎΠΉΠΊΠΈ. Π Π·Π°Π²ΠΈΡΠΈΠΌΠΎΡΡΠΈ ΠΎΡ ΡΠΈΠΏΠ° ΠΏΡΠΈΠ²ΠΎΠ΄Π° ΠΌΠΎΠ»ΠΎΡΡ Π±ΡΠ²Π°ΡΡ ΠΏΡΡΠΆΠΈΠ½Π½ΡΠ΅, ΠΏΠ°ΡΠΎΠ²ΡΠ΅ ΠΈ ΠΏΠ½Π΅Π²ΠΌΠ°ΡΠΈΡΠ΅ΡΠΊΠΈΠ΅. ΠΠ°ΠΈΠ±ΠΎΠ»ΡΡΠ΅Π΅ ΡΠ°ΡΠΏΡΠΎΡΡΡΠ°Π½Π΅Π½ΠΈΠ΅ Π² ΠΏΡΠ°ΠΊΡΠΈΠΊΠ΅ Ρ
ΡΠ΄ΠΎΠΆΠ΅ΡΡΠ²Π΅Π½Π½ΠΎΠΉ ΠΊΠΎΠ²ΠΊΠΈ ΠΏΠΎΠ»ΡΡΠΈΠ»ΠΈ ΠΏΡΡΠΆΠΈΠ½Π½ΡΠ΅ ΠΌΠΎΠ»ΠΎΡΡ ΡΠΈΡΠΌΡ Β«ΠΡΠΊΡΒ». ΠΠ΅ΠΊΠΎΡΠΎΡΡΠ΅ ΠΊΡΠ·Π½Π΅ΡΡ ΡΠΌΠ΅ΡΡ ΡΠ΄Π΅ΡΠΆΠΈΠ²Π°ΡΡ Π² ΠΏΡΠΎΡΠ΅ΡΡΠ΅ ΡΠ°Π±ΠΎΡΡ ΡΠ°ΡΡΡΠΎΡΠ½ΠΈΠ΅ ΠΌΠ΅ΠΆΠ΄Ρ Π±ΠΎΠΉΠΊΠ°ΠΌΠΈ Ρ Π½Π΅Π²Π΅ΡΠΎΡΡΠ½ΠΎΠΉ ΡΠΎΡΠ½ΠΎΡΡΡΡ *.
* ΠΠ΅ΠΆΠ΄Ρ ΠΊΡΠ·Π½Π΅ΡΠ°ΠΌΠΈ Π±ΡΡΡΠ΅Ρ ΠΈΡΡΠΎΡΠΈΡ ΠΎΠ± ΠΎΠ΄Π½ΠΎΠΌ ΠΌΠ°ΡΡΠ΅ΡΠ΅ ΠΊΠΎΠ²ΠΊΠΈ Π½Π° Π·Π°Π²ΠΎΠ΄Π΅ Π ΠΈΠ½Π³Ρ
ΠΎΡΠ΅ΡΠ°, ΠΊΠΎΡΠΎΡΡΠΉ, Π΅ΡΠ»ΠΈ Π΅ΠΌΡ Π½Π° Π½ΠΈΠΆΠ½ΠΈΠΉ Π±ΠΎΠ΅ΠΊ ΠΊΠ»Π°Π»ΠΈ ΡΠ°ΡΡ, ΠΏΠΎΠΊΠ°Π·ΡΠ²Π°Π», ΡΡΠΎ ΠΌΠΎΠΆΠ΅Ρ ΠΎΡΡΠ°Π½ΠΎΠ²ΠΈΡΡ Π²Π΅ΡΡ
Π½ΠΈΠΉ Π±ΠΎΠ΅ΠΊ ΡΠ°ΠΊ, ΡΡΠΎ ΠΎΠ½ ΡΠΎΠ»ΡΠΊΠΎ ΠΊΠΎΡΠ½Π΅ΡΡΡ ΡΡΠ΅ΠΊΠ»Π° ΠΈ Π½Π΅ ΠΏΠΎΠ²ΡΠ΅Π΄ΠΈΡ ΡΠ°ΡΡ. Π Π°ΡΡΠΊΠ°Π·ΡΠ²Π°ΡΡ ΡΠ°ΠΊΠΆΠ΅, ΡΡΠΎ ΡΠΎΠ³Π΄Π°ΡΠ½ΠΈΠΉ ΠΈΠΌΠΏΠ΅ΡΠ°ΡΠΎΡ Π€ΡΠ°Π½Ρ ΠΠΎΡΠΈΡ ΠΏΡΠΈ ΠΏΠΎΡΠ΅ΡΠ΅Π½ΠΈΠΈ ΠΡΠ°Π³ΠΈ ΠΈ ΡΡΠΎΠ³ΠΎ Π·Π°Π²ΠΎΠ΄Π° Π±ΡΠ» ΡΠ°ΠΊ ΡΠ΄ΠΈΠ²Π»Π΅Π½ ΡΡΠΈΠΌ ΡΠΌΠ΅Π½ΠΈΠ΅ΠΌ, ΡΡΠΎ ΠΏΠΎΠ»ΠΎΠΆΠΈΠ» Π½Π° Π±ΠΎΠ΅ΠΊ ΡΠΎΠ±ΡΡΠ²Π΅Π½Π½ΡΡ Π³ΠΎΠ»ΠΎΠ²Ρ ΠΈ Π²Π΅Π»Π΅Π» ΠΊΡΠ·Π½Π΅ΡΡ ΠΏΡΡΡΠΈΡΡ ΠΌΠΎΠ»ΠΎΡ ΠΈ ΠΊΠΎΡΠ½ΡΡΡΡΡ Π³ΠΎΠ»ΠΎΠ²Ρ Π±ΠΎΠΉΠΊΠΎΠΌ. Π Π½Π°ΡΠ΅ Π²ΡΠ΅ΠΌΡ ΡΡΡΠ΄Π½ΠΎ ΡΠΊΠ°Π·Π°ΡΡ, ΡΠΊΠΎΠ»ΡΠΊΠΎ Π² ΡΡΠΎΠΉ ΠΈΡΡΠΎΡΠΈΠΈ Π±ΡΠ»ΠΎ ΠΏΡΠ°Π²Π΄Ρ, Π° ΡΠΊΠΎΠ»ΡΠΊΠΎ Π²ΡΠ΄ΡΠΌΠΊΠΈ, ΠΎΠ΄Π½ΠΎ ΡΡΠ½ΠΎ, ΡΡΠΎ ΠΌΠ°ΡΡΠ΅ΡΡΡΠ²ΠΎ ΡΠ΅ΡΡΠΊΠΈΡ
ΠΊΡΠ·Π½Π΅ΡΠΎΠ² Π±ΡΠ»ΠΎ ΠΈ ΠΎΡΡΠ°Π΅ΡΡΡ Π²ΡΡΠΎΠΊΠΈΠΌ, Π° ΡΠ»Π°Π²Π° ΠΎ Π½Π΅ΠΌ ΠΈΠ΄Π΅Ρ ΠΏΠΎ Π²ΡΠ΅ΠΌΡ ΠΌΠΈΡΡ.
ΠΠΎΠ»ΡΡΠ°Ρ ΡΠ°ΡΡΡ ΡΠ°Π±ΠΎΡΡ Π² Ρ ΡΠ΄ΠΎΠΆΠ΅ΡΡΠ²Π΅Π½Π½ΠΎΠΉ ΠΊΠΎΠ²ΠΊΠ΅ ΠΈ ΡΠ»Π΅ΡΠ°ΡΠ½ΠΎΠΌ Π΄Π΅Π»Π΅ Π²ΡΠΏΠΎΠ»Π½ΡΠ΅ΡΡΡ Π²ΡΡΡΠ½ΡΡ; ΠΌΠ΅ΡΠ°Π»Π»Ρ ΡΠΎΠΎΠ±ΡΠ°ΡΡ Π½ΡΠΆΠ½ΡΡ ΡΠΎΡΠΌΡ ΠΏΠΎΡΠ»Π΅Π΄ΠΎΠ²Π°ΡΠ΅Π»ΡΠ½ΡΠΌΠΈ ΡΠ΄Π°ΡΠ°ΠΌΠΈ ΡΡΡΠ½ΠΈΠΊΠ° ΠΈΠ»ΠΈ ΠΊΡΠ²Π°Π»Π΄Ρ, Π½Π°Π½ΠΎΡΠΈΠΌΡΠΌΠΈ ΠΏΠΎ Π΄Π΅ΡΠΎΡΠΌΠΈΡΡΠ΅ΠΌΠΎΠΌΡ ΠΌΠ°ΡΠ΅ΡΠΈΠ°Π»Ρ. Π ΡΡΠ½Π°Ρ ΠΊΠΎΠ²ΠΊΠ° β ΡΠ°Π±ΠΎΡΠ° ΠΎΡΠ΅Π½Ρ ΡΡΠΆΠ΅Π»Π°Ρ, ΠΊΡΠΎΠΏΠΎΡΠ»ΠΈΠ²Π°Ρ, ΡΡΠ΅Π±ΡΡΡΠ°Ρ ΡΠ½ΠΎΡΠΎΠ²ΠΊΠΈ. ΠΡΠ΅ΠΆΠ΄Π΅ ΡΠ΅ΠΌ ΠΏΠ΅ΡΠ΅ΠΉΡΠΈ ΠΊ ΡΠ°ΡΡΠΌΠΎΡΡΠ΅Π½ΠΈΡ ΡΠΎΠ±ΡΡΠ²Π΅Π½Π½ΠΎ Ρ ΡΠ΄ΠΎΠΆΠ΅ΡΡΠ²Π΅Π½Π½ΠΎΠΉ ΠΊΠΎΠ²ΠΊΠΈ, ΡΠ»Π΅Π΄ΡΠ΅Ρ ΡΠΎΠΎΠ±ΡΠΈΡΡ Π½Π΅ΠΊΠΎΡΠΎΡΡΠ΅ ΡΠ²Π΅Π΄Π΅Π½ΠΈΡ ΠΎΠ± ΠΎΡΠ½ΠΎΠ²Π°Ρ ΠΊΠΎΠ²ΠΊΠΈ Π²ΠΎΠΎΠ±ΡΠ΅, Ρ. Π΅. ΠΎ ΠΊΡΠ·Π½Π΅ΡΠ½ΠΎΠΉ Π°Π·Π±ΡΠΊΠ΅.
ΠΠ°Π³ΡΠ΅Π²
ΠΠ°ΡΠ΅ΡΠΈΠ°Π» Π΄Π»Ρ ΠΊΠΎΠ²ΠΊΠΈ Π½Π°Π³ΡΠ΅Π²Π°ΡΡ Π² Π³ΠΎΡΠ½Π΅, ΠΊΠΎΡΠΎΡΡΠΉ Π² Π½Π°ΡΡΠΎΡΡΠ΅Π΅ Π²ΡΠ΅ΠΌΡ ΠΎΠ±ΠΎΡΡΠ΄ΡΡΡ ΡΠ»Π΅ΠΊΡΡΠΈΡΠ΅ΡΠΊΠΈΠΌ Π²Π΅Π½ΡΠΈΠ»ΡΡΠΎΡΠΎΠΌ, Π½Π°Π³Π½Π΅ΡΠ°ΡΡΠΈΠΌ Π² Π³ΠΎΡΠ½ Π½Π΅ΠΎΠ±Ρ
ΠΎΠ΄ΠΈΠΌΠΎΠ΅ ΠΊΠΎΠ»ΠΈΡΠ΅ΡΡΠ²ΠΎ Π²ΠΎΠ·Π΄ΡΡ
Π°. ΠΠΎΡΠ½ ΠΎΡΠ°ΠΏΠ»ΠΈΠ²Π°ΡΡ ΠΊΡΠ·Π½Π΅ΡΠ½ΡΠΌ ΡΠ³Π»Π΅ΠΌ ΠΈΠ»ΠΈ ΠΌΠ΅Π»ΠΊΠΈΠΌ ΠΊΠΎΠΊΡΠΎΠΌ. ΠΠ³ΠΎΠ½Ρ ΡΠ»Π΅Π΄ΡΠ΅Ρ ΠΏΠΎΡΡΠΎΡΠ½Π½ΠΎ ΠΏΠΎΠ΄Π΄Π΅ΡΠΆΠΈΠ²Π°ΡΡ ΡΠΈΡΡΡΠΌ, ΠΏΠ»Π°ΠΌΡ Π½Π΅ Π΄ΠΎΠ»ΠΆΠ½ΠΎ Π±ΡΡΡ Π΄Π»ΠΈΠ½Π½ΡΠΌ, ΡΡΠΎΠ±Ρ ΡΠ°ΠΌΡΠΉ Π±ΠΎΠ»ΡΡΠΎΠΉ ΠΆΠ°Ρ Π±ΡΠ» Π²Π½ΡΡΡΠΈ Π΅Π³ΠΎ. Π‘ ΡΡΠΎΠΉ ΡΠ΅Π»ΡΡ Π²ΡΠ΅ΠΌΡ ΠΎΡ Π²ΡΠ΅ΠΌΠ΅Π½ΠΈ ΠΏΠ»Π°ΠΌΡ ΡΠ²Π΅ΡΡ
Ρ ΠΏΠΎΠ»ΠΈΠ²Π°ΡΡ Π²ΠΎΠ΄ΠΎΠΉ ΠΈΠ· ΠΆΠ΅ΡΡΡΠ½ΠΎΠΉ Π»Π΅ΠΉΠΊΠΈ. ΠΠΎΠ»Ρ, ΠΊΠΎΡΠΎΡΠ°Ρ ΠΎΠ±ΡΠ°Π·ΡΠ΅ΡΡΡ Π½Π° Π΄Π½Π΅ Π³ΠΎΡΠ½Π°, Π½Π΅ ΡΠ°ΡΠΊΠ°Π»ΡΠ²Π°Ρ, Π²ΡΠ³ΡΠ΅Π±Π°ΡΡ ΠΈΠ· Π³ΠΎΡΠ½Π° Π»ΠΎΠΌΠΈΠΊΠΎΠΌ ΠΈΠ»ΠΈ ΠΊΠΎΡΠ΅ΡΠ³ΠΎΠΉ. Π§ΡΠΎΠ±Ρ ΠΏΡΠΈ ΡΠΈΡΡΠΊΠ΅ Π³ΠΎΡΠ½Π° ΠΎΠ³ΠΎΠ½Ρ Π½Π΅ ΠΏΠΎΠ³Π°Ρ, Π² Π³ΠΎΡΠ½ ΠΏΠΎΠ΄ΠΊΠ»Π°Π΄ΡΠ²Π°ΡΡ Π΄ΠΎΠΏΠΎΠ»Π½ΠΈΡΠ΅Π»ΡΠ½ΠΎ ΠΏΠΎΠ±ΠΎΠ»ΡΡΠ΅ ΡΠΎΠΏΠ»ΠΈΠ²Π° ΠΈ Π΄Π°ΡΡ Π΅ΠΌΡ Π²ΠΎΠ·ΠΌΠΎΠΆΠ½ΠΎΡΡΡ ΡΠ°Π·Π³ΠΎΡΠ΅ΡΡΡΡ. Π£Π³ΠΎΠ»Ρ Π² Π³ΠΎΡΠ½ ΠΏΠΎΠ΄ΠΊΠ»Π°Π΄ΡΠ²Π°ΡΡ ΠΏΠΎ ΠΊΡΠ°ΡΠΌ, Π° Π½Π΅ ΡΠ²Π΅ΡΡ
Ρ. ΠΠ°Π³ΡΠ΅Π²Π°Π΅ΠΌΡΠΉ ΠΌΠ°ΡΠ΅ΡΠΈΠ°Π» ΡΠΊΠ»Π°Π΄ΡΠ²Π°ΡΡ Π² Π³ΠΎΡΠ½ ΠΏΠΎΠ΄ Π½Π΅Π±ΠΎΠ»ΡΡΠΎΠΉ ΡΠ»ΠΎΠΉ ΡΠ³Π»Π΅ΠΉ, Π³Π΄Π΅ ΠΆΠ°Ρ Π½Π°ΠΈΠ±ΠΎΠ»ΡΡΠΈΠΉ. ΠΠ°ΡΠ΅ΡΠΈΠ°Π», ΡΠ»ΠΎΠΆΠ΅Π½Π½ΡΠΉ ΡΠ»ΠΈΡΠΊΠΎΠΌ Π³Π»ΡΠ±ΠΎΠΊΠΎ, ΠΎΡ
Π»Π°ΠΆΠ΄Π°Π΅ΡΡΡ ΠΏΠΎΡΡΡΠΏΠ°ΡΡΠΈΠΌ Π² Π³ΠΎΡΠ½ Π²ΠΎΠ·Π΄ΡΡ
ΠΎΠΌ, ΠΈ Π½Π°Π³ΡΠ΅Π² Π·Π΄Π΅ΡΡ ΠΌΠΈΠ½ΠΈΠΌΠ°Π»ΡΠ½ΡΠΉ. ΠΠ°Π³ΡΠ΅Π²Π°ΡΡ ΠΌΠ°ΡΠ΅ΡΠΈΠ°Π» ΡΠ»Π΅Π΄ΡΠ΅Ρ ΠΌΠ΅Π΄Π»Π΅Π½Π½ΠΎ, ΠΎΡΠΎΠ±Π΅Π½Π½ΠΎ ΠΊΡΡΠΏΠ½ΡΠ΅ Π·Π°Π³ΠΎΡΠΎΠ²ΠΊΠΈ, Ρ ΡΠ΅ΠΌ ΡΡΠΎΠ±Ρ ΠΎΠ½ Π΄ΠΎΡΡΠ°ΡΠΎΡΠ½ΠΎ ΠΏΡΠΎΠ³ΡΠ΅Π²Π°Π»ΡΡ. ΠΠ΅Π»ΡΠ·Ρ Π΄ΠΎΠΏΡΡΠΊΠ°ΡΡ ΠΏΠ΅ΡΠ΅Π³ΡΠ΅Π²Π° ΡΡΠ°Π»ΠΈ, ΠΎΡΠΎΠ±Π΅Π½Π½ΠΎ ΠΈΠ½ΡΡΡΡΠΌΠ΅Π½ΡΠ°Π»ΡΠ½ΠΎΠΉ Π²ΠΎ ΠΈΠ·Π±Π΅ΠΆΠ°Π½ΠΈΠ΅ ΠΎΠ±ΡΠ°Π·ΠΎΠ²Π°Π½ΠΈΡ ΡΡΠ΅ΡΠΈΠ½ ΠΈ ΡΠ°Π·ΡΡΡΠ΅Π½ΠΈΡ ΠΏΡΠΈ ΠΊΠΎΠ²ΠΊΠ΅. ΠΡΠ»ΠΈ ΠΏΠΎ Π½Π΅Π΄ΠΎΡΠΌΠΎΡΡΡ Π·Π°Π³ΠΎΡΠΎΠ²ΠΊΠ° Π²ΡΠ΅-ΡΠ°ΠΊΠΈ ΠΎΠΊΠ°ΠΆΠ΅ΡΡΡ ΠΏΠ΅ΡΠ΅Π³ΡΠ΅ΡΠΎΠΉ, ΡΠΎ ΠΏΠ΅ΡΠ΅Π³ΡΠ΅ΡΡΡ ΡΠ°ΡΡΡ ΡΠ»Π΅Π΄ΡΠ΅Ρ ΠΎΡΡΡΠ±ΠΈΡΡ. ΠΠ°ΠΈΠ±ΠΎΠ»Π΅Π΅ Π±Π»Π°Π³ΠΎΠΏΡΠΈΡΡΠ½ΡΠΉ ΡΠ΅ΠΌΠΏΠ΅ΡΠ°ΡΡΡΠ½ΡΠΉ ΠΈΠ½ΡΠ΅ΡΠ²Π°Π» ΠΊΠΎΠ²ΠΊΠΈ 800β900Β° (ΡΠΌ. ΡΠ°Π±Π»ΠΈΡΡ ΡΠ²Π΅ΡΠΎΠ² Π½Π°Π³ΡΠ΅ΡΠΎΠ³ΠΎ ΠΌΠ΅ΡΠ°Π»Π»Π°). ΠΡΠΎΡΠ½ΠΎΡΡΡ ΡΡΠ°Π»ΠΈ ΠΏΡΠΈ ΡΡΠΈΡ
ΡΠ΅ΠΌΠΏΠ΅ΡΠ°ΡΡΡΠ°Ρ
ΡΠΌΠ΅Π½ΡΡΠ°Π΅ΡΡΡ ΠΏΡΠΈΠΌΠ΅ΡΠ½ΠΎ Π² 20 ΡΠ°Π·, Π° ΠΏΠ»Π°ΡΡΠΈΡΠ½ΠΎΡΡΡ ΡΡΡΠ΅ΡΡΠ²Π΅Π½Π½ΠΎ ΡΠ²Π΅Π»ΠΈΡΠΈΠ²Π°Π΅ΡΡΡ.
ΠΠΎΠ²Π°ΡΡ ΠΏΡΠΈ ΠΌΠ΅Π½ΡΡΠΈΡ
ΡΠ΅ΠΌΠΏΠ΅ΡΠ°ΡΡΡΠ°Ρ
Π½Π΅ ΡΠ»Π΅Π΄ΡΠ΅Ρ. ΠΠ°ΠΏΡΠΈΠΌΠ΅Ρ, ΠΏΡΠΈ ΡΠ΅ΠΌΠΏΠ΅ΡΠ°ΡΡΡΠ΅ ΡΠ°ΠΊ Π½Π°Π·ΡΠ²Π°Π΅ΠΌΠΎΠ³ΠΎ ΡΠΈΠ½Π΅Π³ΠΎ ΠΊΠ°Π»Π΅Π½ΠΈΡ, Ρ. Π΅. ΠΏΡΠΈΠΌΠ΅ΡΠ½ΠΎ 400Β°Π‘, ΡΡΠ°Π»Ρ ΡΡΠ°Π½ΠΎΠ²ΠΈΡΡΡ ΠΎΡΠ΅Π½Ρ Ρ
ΡΡΠΏΠΊΠΎΠΉ ΠΈ Π»Π΅Π³ΠΊΠΎ ΡΠ°Π·ΡΡΡΠ°Π΅ΡΡΡ.
Π ΠΈΡ. 50. ΠΡΠΎΡΡΠΆΠΊΠ°: Π° β Π½Π° ΡΠ΅Π±ΡΠ΅; Π± β ΡΠΊΡΡΠ³Π»Π΅Π½Π½ΡΠΌ ΠΌΠΎΠ»ΠΎΡΠΊΠΎΠΌ |
Π ΠΈΡ. 51. Π‘ΠΊΡΡΠ³Π»Π΅Π½ΠΈΠ΅ Π·Π°Π³ΠΎΡΠΎΠ²ΠΊΠΈ |
Π ΠΈΡ. 52. ΠΠΎΠ²ΠΊΠ° ΡΡΡΡΠΏΠΎΠ² |
Π ΠΈΡ. 53. ΠΠΎΠ»ΡΡΠ΅Π½ΠΈΠ΅ ΡΡΡΡΠΏΠ° Π² ΠΎΠ±ΠΆΠΈΠΌΠΊΠ°Ρ |
ΠΡΠΎΡΡΠΆΠΊΠ°
ΠΡΠ»ΠΈ ΠΊΡΠ·Π½Π΅Ρ ΡΠ°Π±ΠΎΡΠ°Π΅Ρ Π² ΠΎΠ΄ΠΈΠ½ΠΎΡΠΊΡ, ΡΠΎ Π² Π±ΠΎΠ»ΡΡΠΈΠ½ΡΡΠ²Π΅ ΡΠ»ΡΡΠ°Π΅Π² ΠΎΠ½ ΠΏΡΠΎΡΡΠ³ΠΈΠ²Π°Π΅Ρ Π·Π°Π³ΠΎΡΠΎΠ²ΠΊΡ Π½Π° ΠΊΡΠΎΠΌΠΊΠ΅ Π½Π°ΠΊΠΎΠ²Π°Π»ΡΠ½ΠΈ. ΠΠ°Π³ΡΠ΅ΡΡΡ Π·Π°Π³ΠΎΡΠΎΠ²ΠΊΡ ΠΎΠ½ ΡΠΊΠ»Π°Π΄ΡΠ²Π°Π΅Ρ Π½Π° ΠΎΡΡΡΡΡ ΠΊΡΠΎΠΌΠΊΡ Π½Π°ΠΊΠΎΠ²Π°Π»ΡΠ½ΠΈ ΠΏΠΎΠ΄ ΡΠ³Π»ΠΎΠΌ ΠΏΡΠΈΠ±Π»ΠΈΠ·ΠΈΡΠ΅Π»ΡΠ½ΠΎ 45Β° (ΡΠΈΡ. 50, Π°) ΠΈ ΡΠ΄Π°ΡΠ°ΠΌΠΈ ΡΡΡΠ½ΠΈΠΊΠ° ΠΏΠΎ ΠΏΡΠΎΡΠΈΠ²ΠΎΠΏΠΎΠ»ΠΎΠΆΠ½ΠΎΠΉ Π³ΡΠ°Π½ΠΈ Π·Π°Π³ΠΎΡΠΎΠ²ΠΊΠΈ ΠΏΡΠΎΡΡΠ³ΠΈΠ²Π°Π΅Ρ Π΅Π΅. ΠΡΠ»ΠΈ Ρ ΠΊΡΠ·Π½Π΅ΡΠ° Π΅ΡΡΡ ΠΏΠΎΠ΄ΡΡΡΠ½ΡΠΉ, ΡΠΎ ΠΊΡΠ·Π½Π΅Ρ ΡΠΊΠ»Π°Π΄ΡΠ²Π°Π΅Ρ Π·Π°Π³ΠΎΡΠΎΠ²ΠΊΡ Π½Π° ΠΏΠ»ΠΎΡΠΊΠΎΡΡΡ Π½Π°ΠΊΠΎΠ²Π°Π»ΡΠ½ΠΈ (ΡΠΈΡ. 50, Π±), Π° Π΄ΡΡΠ³ΠΎΠΉ ΡΡΠΊΠΎΠΉ ΡΡΡΠ°Π½Π°Π²Π»ΠΈΠ²Π°Π΅Ρ Π½Π° Π·Π°Π³ΠΎΡΠΎΠ²ΠΊΡ ΠΌΠΎΠ»ΠΎΡΠΎΠΊ Π΄Π»Ρ ΠΏΡΠΎΡΡΠΆΠΊΠΈ. ΠΠΎΡΠ»Π΅ ΠΏΡΠΎΡΡΠΆΠΊΠΈ Π·Π°Π³ΠΎΡΠΎΠ²ΠΊΡ Π²ΡΡΠ°Π²Π½ΠΈΠ²Π°ΡΡ Ρ ΡΡΠ΅ΡΠΎΠΌ ΡΡΠ΅Π±ΡΠ΅ΠΌΡΡ
ΡΠ°Π·ΠΌΠ΅ΡΠΎΠ² ΠΈ ΡΠΎΡΠΌΡ; Π΅ΡΠ»ΠΈ ΠΆΠ΅ ΠΏΠΎΠ²Π΅ΡΡ
Π½ΠΎΡΡΡ Π·Π°Π³ΠΎΡΠΎΠ²ΠΊΠΈ Π΄ΠΎΠ»ΠΆΠ½Π° Π±ΡΡΡ ΠΈΡΠΊΠ»ΡΡΠΈΡΠ΅Π»ΡΠ½ΠΎ ΡΠΎΠ²Π½ΠΎΠΉ, ΡΠΎ ΠΎΡ
Π»Π°ΠΆΠ΄Π°ΡΡΡΡΡΡ Π·Π°Π³ΠΎΡΠΎΠ²ΠΊΡ Π²ΡΡΠ°Π²Π½ΠΈΠ²Π°ΡΡ Π³Π»Π°Π΄ΠΈΠ»ΠΊΠΎΠΉ (ΡΠΌ. ΡΠΈΡ. 40).
Π‘ΠΊΡΡΠ³Π»Π΅Π½ΠΈΠ΅ Π³ΡΠ°Π½Π΅ΠΉ
ΠΡΡΡΡ Π·Π°Π³ΠΎΡΠΎΠ²ΠΊΡ ΠΊΠ²Π°Π΄ΡΠ°ΡΠ½ΠΎΠ³ΠΎ ΠΈΠ»ΠΈ ΠΏΡΡΠΌΠΎΡΠ³ΠΎΠ»ΡΠ½ΠΎΠ³ΠΎ ΡΠ΅ΡΠ΅Π½ΠΈΡ ΡΡΠ΅Π±ΡΠ΅ΡΡΡ Ρ ΠΎΠ΄Π½ΠΎΠ³ΠΎ ΠΊΠΎΠ½ΡΠ° ΡΠΊΡΡΠ³Π»ΠΈΡΡ. ΠΠ»Ρ ΡΡΠΎΠ³ΠΎ ΠΊΠ²Π°Π΄ΡΠ°ΡΠ½ΡΡ Π·Π°Π³ΠΎΡΠΎΠ²ΠΊΡ ΠΏΠΎΠ²ΠΎΡΠ°ΡΠΈΠ²Π°ΡΡ ΡΠ°ΠΊΠΈΠΌ ΠΎΠ±ΡΠ°Π·ΠΎΠΌ, ΡΡΠΎΠ±Ρ Π΅Π΅ ΡΠ΅Π±ΡΠΎ Π»Π΅ΠΆΠ°Π»ΠΎ Π½Π° ΠΏΠ»ΠΎΡΠΊΠΎΡΡΠΈ Π½Π°ΠΊΠΎΠ²Π°Π»ΡΠ½ΠΈ Π² ΠΏΡΠΎΠ΄ΠΎΠ»ΡΠ½ΠΎΠΌ Π½Π°ΠΏΡΠ°Π²Π»Π΅Π½ΠΈΠΈ ΠΈ, ΡΠ΄Π°ΡΠ°ΠΌΠΈ ΠΊΡΠ²Π°Π»Π΄Ρ ΠΊΠ²Π°Π΄ΡΠ°ΡΠ½ΠΎΠ΅ ΡΠ΅ΡΠ΅Π½ΠΈΠ΅ ΠΏΠ΅ΡΠ΅ΠΊΠΎΠ²ΡΠ²Π°ΡΡ Π½Π° Π²ΠΎΡΡΠΌΠΈΠ³ΡΠ΅ΡΠ½ΠΎΠ΅ (ΡΠΈΡ. 51). Π£Π΄Π°ΡΡ Π΄ΠΎΠ»ΠΆΠ½Ρ Π±ΡΡΡ ΡΠ°Π²Π½ΠΎΠΌΠ΅ΡΠ½ΡΠΌΠΈ, ΡΡΠΎΠ±Ρ Π½Π΅ ΠΈΡΠΊΡΠΈΠ²ΠΈΡΡ Π·Π°Π³ΠΎΡΠΎΠ²ΠΊΡ. Π’ΠΎΠ»ΡΠΊΠΎ ΠΏΠΎΡΠ»Π΅ ΡΠΎΠ³ΠΎ, ΠΊΠ°ΠΊ ΠΏΠΎΠ»ΡΡΠΈΡΡΡ ΠΏΠΎΡΡΠΈ ΠΏΡΠ°Π²ΠΈΠ»ΡΠ½ΡΠΉ Π²ΠΎΡΡΠΌΠΈΠ³ΡΠ°Π½Π½ΠΈΠΊ, Π½Π΅ΠΎΠ±Ρ
ΠΎΠ΄ΠΈΠΌΠΎ ΡΠ°ΡΡΡΠΌΠΈ ΡΠ΄Π°ΡΠ°ΠΌΠΈ Ρ ΠΊΠΎΠ½ΡΠΎΠ²ΠΊΠΎΠΉ Π·Π°Π²Π΅ΡΡΠΈΡΡ ΠΎΠΊΡΡΠ³Π»Π΅Π½ΠΈΠ΅. ΠΠ»Ρ ΠΎΠΊΠΎΠ½ΡΠ°ΡΠ΅Π»ΡΠ½ΠΎΠ³ΠΎ ΠΎΡΠΎΡΠΌΠ»Π΅Π½ΠΈΡ ΠΏΠΎΠ²Π΅ΡΡ
Π½ΠΎΡΡΠΈ ΠΌΠΎΠΆΠ½ΠΎ ΠΈΡΠΏΠΎΠ»ΡΠ·ΠΎΠ²Π°ΡΡ Π²ΡΡΠ΅Π·Π½ΡΡ ΠΎΠ±ΠΆΠΈΠΌΠΊΡ ΠΈ Π²ΡΡΠ΅Π·Π½ΠΎΠΉ ΠΌΠΎΠ»ΠΎΡΠΎΠΊ. ΠΡΠ»ΠΈ Π½Π° ΠΊΠΎΠ½ΡΠ΅ ΡΠΊΡΡΠ³Π»Π΅Π½Π½ΠΎΠ³ΠΎ ΡΡΠ°ΡΡΠΊΠ° Π½Π΅ΠΎΠ±Ρ
ΠΎΠ΄ΠΈΠΌΠΎ ΡΠ΄Π΅Π»Π°ΡΡ ΡΡΡΡΠΏ (ΡΠΌ. ΡΠ»Π΅Π΄ΡΡΡΠΈΠΉ ΠΏΠ°ΡΠ°Π³ΡΠ°Ρ), ΡΠΎ ΡΡΠΎΡ ΡΡΡΡΠΏ Π½Π°Π΄ΠΎ ΠΎΡΠΎΡΠΌΠΈΡΡ ΠΏΠ΅ΡΠ΅Π΄ ΡΠΊΡΡΠ³Π»Π΅Π½ΠΈΠ΅ΠΌ. ΠΡΠ»ΠΈ ΠΎΠ±ΡΠ°Π±Π°ΡΡΠ²Π°ΡΡ ΠΏΠΎΠ»ΠΎΡΠΎΠ²ΡΡ Π·Π°Π³ΠΎΡΠΎΠ²ΠΊΡ ΡΠ΅ΡΠ΅Π½ΠΈΠ΅ΠΌ, Π½Π°ΠΏΡΠΈΠΌΠ΅Ρ, 2×1 ΡΠΌ, ΡΠΎ Π΅Π΅ ΡΠ½Π°ΡΠ°Π»Π° ΠΏΡΠΎΠΊΠΎΠ²ΡΠ²Π°ΡΡ Π½Π° ΠΊΠ²Π°Π΄ΡΠ°Ρ, Π° ΠΏΠΎΡΠ»Π΅Π΄ΡΡΡΠΈΠ΅ ΠΏΠ΅ΡΠ΅Ρ
ΠΎΠ΄Ρ Π°Π½Π°Π»ΠΎΠ³ΠΈΡΠ½Ρ ΠΎΠΏΠΈΡΠ°Π½Π½ΡΠΌ.
ΠΡΠΎΡΠΌΠ»Π΅Π½ΠΈΠ΅ ΡΡΡΡΠΏΠΎΠ²
ΠΡΠΎΡ ΡΠ΅ΡΠΌΠΈΠ½ ΠΈΡΠΏΠΎΠ»ΡΠ·ΡΡΡ Π² ΠΊΡΠ·Π½Π΅ΡΠ½ΠΎΠΌ Π΄Π΅Π»Π΅ Π΄Π»Ρ ΠΎΠΏΠ΅ΡΠ°ΡΠΈΠΉ, Π² ΡΠ΅Π·ΡΠ»ΡΡΠ°ΡΠ΅ ΠΊΠΎΡΠΎΡΡΡ Π½Π° ΠΊΠΎΠ½ΡΠ΅ ΠΏΠΎΠΊΠΎΠ²ΠΊΠΈ ΠΎΡΠΎΡΠΌΠ»ΡΡΡ ΡΡΠ°ΡΡΠΎΠΊ ΠΈΠ½ΠΎΠ³ΠΎ ΡΠ΅ΡΠ΅Π½ΠΈΡ, Π΄ΠΎΠΏΡΡΡΠΈΠΌ, ΠΌΠ΅Π½ΡΡΠ΅Π³ΠΎ ΠΏΠΎ ΡΡΠ°Π²Π½Π΅Π½ΠΈΡ Ρ ΠΈΡΡ ΠΎΠ΄Π½ΡΠΌ, Π½Π°ΠΏΡΠΈΠΌΠ΅Ρ ΡΠ°ΠΏΡΡ ΠΈΠ»ΠΈ ΠΏΠΎΠ΄ΠΎΠ±Π½ΡΠΉ Π΅ΠΉ ΡΠ»Π΅ΠΌΠ΅Π½Ρ.
ΠΠ±ΡΡΠ½ΠΎ ΠΊΠΎΠ²ΠΊΡ ΡΡΡΡΠΏΠΎΠ² Π²ΡΠΏΠΎΠ»Π½ΡΡΡ Π½Π° ΠΎΡΡΡΠΎΠΌ ΡΠ΅Π±ΡΠ΅ Π½Π°ΠΊΠΎΠ²Π°Π»ΡΠ½ΠΈ. ΠΠ°Π³ΠΎΡΠΎΠ²ΠΊΡ ΡΠΊΠ»Π°Π΄ΡΠ²Π°ΡΡ ΠΏΠΎΠΏΠ΅ΡΠ΅ΠΊ Π½Π°ΠΊΠΎΠ²Π°Π»ΡΠ½ΠΈ, ΡΠ΅Π±ΡΠΎ ΠΊΠΎΡΠΎΡΠΎΠΉ ΠΎΠ³ΡΠ°Π½ΠΈΡΠΈΠ²Π°Π΅Ρ Π΄Π»ΠΈΠ½Ρ ΠΎΡΡΡΠ³ΠΈΠ²Π°Π΅ΠΌΠΎΠ³ΠΎ ΡΡΠ°ΡΡΠΊΠ°. Π£Π΄Π°ΡΠ°ΠΌΠΈ ΠΊΡΠ²Π°Π»Π΄Ρ ΠΏΠΎ ΠΏΡΠΎΡΠΈΠ²ΠΎΠΏΠΎΠ»ΠΎΠΆΠ½ΠΎΠΉ Π³ΡΠ°Π½ΠΈ Π·Π°Π³ΠΎΡΠΎΠ²ΠΊΠΈ ΠΎΡΠΎΡΠΌΠ»ΡΡΡ ΡΡΡΡΠΏ (ΡΠΈΡ. 52). ΠΡΠ»ΠΈ ΠΊΡΠ·Π½Π΅Ρ ΡΠ°Π±ΠΎΡΠ°Π΅Ρ Ρ ΠΏΠΎΠ΄ΡΡΡΠ½ΡΠΌ, ΡΠΎ ΠΎΠ½ ΠΎΡΠΊΠΎΠ²ΡΠ²Π°Π΅Ρ ΡΡΡΡΠΏΡ ΠΏΡΠΈ ΠΏΠΎΠΌΠΎΡΠΈ ΡΠΎΠΎΡΠ²Π΅ΡΡΡΠ²ΡΡΡΠ΅Π³ΠΎ ΠΏΠΎΠ΄ΠΊΠ»Π°Π΄Π½ΠΎΠ³ΠΎ ΠΌΠΎΠ»ΠΎΡΠΊΠ°, ΠΏΠΎ ΠΊΠΎΡΠΎΡΠΎΠΌΡ ΠΏΠΎΠ΄ΡΡΡΠ½ΡΠΉ Π½Π°Π½ΠΎΡΠΈΡ ΡΠ΄Π°ΡΡ ΠΊΡΠ²Π°Π»Π΄ΠΎΠΉ. Π ΠΎΠ΄ΠΈΠ½ΠΎΡΠΊΡ ΠΊΡΠ·Π½Π΅Ρ ΠΌΠΎΠΆΠ΅Ρ Π΄Π΅Π»Π°ΡΡ ΡΠΎΠ»ΡΠΊΠΎ ΠΎΠ΄Π½ΠΎΡΡΠΎΡΠΎΠ½Π½ΠΈΠ΅ ΡΡΡΡΠΏΡ. ΠΡΠΈ ΠΊΠΎΠ²ΠΊΠ΅ Π΄Π²ΡΡΡΠΎΡΠΎΠ½Π½ΠΈΡ
ΡΡΡΡΠΏΠΎΠ² Π±Π΅Π· ΠΏΠΎΠΌΠΎΡΠΈ ΠΏΠΎΠ΄ΡΡΡΠ½ΠΎΠ³ΠΎ ΠΎΠ±ΠΎΠΉΡΠΈΡΡ Π½Π΅Π²ΠΎΠ·ΠΌΠΎΠΆΠ½ΠΎ. Π ΡΡΠΎΠΌ ΡΠ»ΡΡΠ°Π΅ Π·Π°Π³ΠΎΡΠΎΠ²ΠΊΡ ΡΠ°ΠΊΠΆΠ΅ ΠΊΠ»Π°Π΄ΡΡ ΠΏΠΎΠΏΠ΅ΡΠ΅ΠΊ Π½Π°ΠΊΠΎΠ²Π°Π»ΡΠ½ΠΈ (ΡΠ΅Π±ΡΠΎ ΠΊΠΎΡΠΎΡΠΎΠΉ ΡΠΎΡΠ½ΠΎ ΠΎΡΠ΄Π΅Π»ΡΠ΅Ρ ΠΏΡΠΎΡΡΠ³ΠΈΠ²Π°Π΅ΠΌΡΠΉ ΡΡΠ°ΡΡΠΎΠΊ), Π½Π°ΠΏΡΠΎΡΠΈΠ² ΡΠ΅Π±ΡΠ° Π½Π°ΠΊΠΎΠ²Π°Π»ΡΠ½ΠΈ ΠΊΡΠ·Π½Π΅Ρ ΡΡΡΠ°Π½Π°Π²Π»ΠΈΠ²Π°Π΅Ρ ΠΏΠΎΠ΄ΠΊΠ»Π°Π΄Π½ΠΎΠΉ ΠΌΠΎΠ»ΠΎΡΠΎΠΊ, ΠΈ ΠΏΠΎΠ΄ΡΡΡΠ½ΡΠΉ ΡΠΈΠ»ΡΠ½ΡΠΌΠΈ ΡΠ΄Π°ΡΠ°ΠΌΠΈ ΠΊΡΠ²Π°Π»Π΄Ρ ΠΏΠΎ ΠΌΠΎΠ»ΠΎΡΠΊΡ Π²ΡΠΏΠΎΠ»Π½ΡΠ΅Ρ ΡΠΎΠ±ΡΡΠ²Π΅Π½Π½ΠΎ ΠΎΡΠΎΡΠΌΠ»Π΅Π½ΠΈΠ΅ ΡΡΡΡΠΏΠ° (ΡΠΈΡ. 53).
ΠΡΡΠ°Π΄ΠΊΠ°
Π Π½Π΅ΠΊΠΎΡΠΎΡΡΡ
ΡΠ»ΡΡΠ°ΡΡ
ΠΈΠ· Π±ΠΎΠ»Π΅Π΅ ΡΠΎΠ½ΠΊΠΎΠΉ Π·Π°Π³ΠΎΡΠΎΠ²ΠΊΠΈ ΠΎΡΠΊΠΎΠ²ΡΠ²Π°ΡΡ ΠΈΠ·Π΄Π΅Π»ΠΈΠ΅, Ρ ΠΊΠΎΡΠΎΡΠΎΠ³ΠΎ Π½Π° ΠΊΠΎΠ½ΡΠ΅ ΠΈΠ»ΠΈ Π½Π° Π½Π΅ΠΊΠΎΡΠΎΡΠΎΠΌ ΠΈΠ½ΠΎΠΌ ΡΡΠ°ΡΡΠΊΠ΅ Π΄ΠΎΠ»ΠΆΠ½ΠΎ Π±ΡΡΡ ΡΡΠΎΠ»ΡΠ΅Π½ΠΈΠ΅, Π² ΡΠ°ΡΡΠ½ΠΎΡΡΠΈ, Π½Π° ΠΊΠΎΠ½ΡΠ΅ Π΄ΠΎΠ»ΠΆΠ½ΠΎ Π±ΡΡΡ ΡΡΠΎΠ»ΡΠ΅Π½ΠΈΠ΅ ΡΡΠ΅ΡΠΈΡΠ΅ΡΠΊΠΎΠΉ ΠΈΠ»ΠΈ ΠΈΠ½ΠΎΠΉ ΠΏΠΎΠ΄ΠΎΠ±Π½ΠΎΠΉ ΡΠΎΡΠΌΡ. ΠΠ΄Π΅ΡΡ Π½Π΅ΠΎΠ±Ρ
ΠΎΠ΄ΠΈΠΌΠ°-ΠΎΠΏΠ΅ΡΠ°ΡΠΈΡ,. ΠΊΠΎΡΠΎΡΠ°Ρ Π½Π°Π·ΡΠ²Π°Π΅ΡΡΡ Π²ΡΡΠ°Π΄ΠΊΠΎΠΉ. ΠΡΠ»ΠΈ Π·Π°Π³ΠΎΡΠΎΠ²ΠΊΠ° ΠΊΠΎΡΠΎΡΠΊΠ°Ρ, ΡΠΎ Π½Π°Π³ΡΠ΅Π²Π°ΡΡ ΡΡΠ°ΡΡΠΎΠΊ Π½Π΅ΠΎΠ±Ρ
ΠΎΠ΄ΠΈΠΌΠΎΠΉ Π΄Π»Ρ Π²ΡΡΠ°Π΄ΠΊΠΈ Π΄Π»ΠΈΠ½Ρ, ΠΏΠΎΡΠ»Π΅ ΡΠ΅Π³ΠΎ ΠΎΡΡΡΠ΅ΡΡΠ²Π»ΡΡΡ Π²ΡΡΠ°Π΄ΠΊΡ ΡΠΈΠ»ΡΠ½ΡΠΌΠΈ ΡΠ΄Π°ΡΠ°ΠΌΠΈ ΠΊΡΠ²Π°Π»Π΄Ρ (ΡΠΈΡ. 54). ΠΡΠ»ΠΈ Π²ΡΡΠ°ΠΆΠΈΠ²Π°Π΅ΠΌΠ°Ρ ΡΠ°ΡΡΡ Π΄ΠΎΠ»ΠΆΠ½Π° ΠΏΠΎΠ»ΡΡΠ°ΡΡΡΡ Π±ΠΎΠ»Π΅Π΅ ΡΠΈΡΠΎΠΊΠΎΠΉ, Π° Π΅Π΅ Π΄Π»ΠΈΠ½Π° ΡΡΠ°Π²Π½ΠΈΡΠ΅Π»ΡΠ½ΠΎ Π½Π΅Π±ΠΎΠ»ΡΡΠΎΠΉ, ΡΠΎ Π² ΡΡΠΎΠΌ ΡΠ»ΡΡΠ°Π΅ Π·Π°Π³ΠΎΡΠΎΠ²ΠΊΡ Π½Π°Π΄ΠΎ ΡΡΡΠ°Π½Π°Π²Π»ΠΈΠ²Π°ΡΡ Ρ
ΠΎΠ»ΠΎΠ΄Π½ΡΠΌ ΠΊΠΎΠ½ΡΠΎΠΌ Π½Π° Π½Π°ΠΊΠΎΠ²Π°Π»ΡΠ½Ρ, Π° ΡΠ΄Π°ΡΡ Π½Π°Π½ΠΎΡΠΈΡΡ Π½Π΅ΠΏΠΎΡΡΠ΅Π΄ΡΡΠ²Π΅Π½Π½ΠΎ ΠΏΠΎ Π½Π°Π³ΡΠ΅ΡΠΎΠΌΡ ΡΡΠ°ΡΡΠΊΡ. ΠΡΠ»ΠΈ, Π½Π°ΠΎΠ±ΠΎΡΠΎΡ, Π²ΡΡΠ°ΠΆΠ΅Π½Π½ΡΡ ΡΠ°ΡΡΡ Π½Π΅ΠΎΠ±Ρ
ΠΎΠ΄ΠΈΠΌΠΎ ΠΏΠΎΠ»ΡΡΠΈΡΡ ΠΏΠΎΠ΄Π»ΠΈΠ½Π½Π΅Π΅, Π·Π°Π³ΠΎΡΠΎΠ²ΠΊΡ ΡΡΡΠ°Π½Π°Π²Π»ΠΈΠ²Π°ΡΡ Π½Π° Π½Π°ΠΊΠΎΠ²Π°Π»ΡΠ½Ρ Π³ΠΎΡΡΡΠΈΠΌ ΠΊΠΎΠ½ΡΠΎΠΌ, Π° ΡΠ΄Π°ΡΡ Π½Π°Π½ΠΎΡΡΡ ΠΏΠΎ Ρ
ΠΎΠ»ΠΎΠ΄Π½ΠΎΠΌΡ ΠΊΠΎΠ½ΡΡ. ΠΠΎΠ»Π΅Π΅ Π΄Π»ΠΈΠ½Π½ΡΠ΅ ΡΡΠ°ΡΡΠΊΠΈ Π²ΡΡΠ°ΠΆΠΈΠ²Π°ΡΡ, ΡΠΊΠ»Π°Π΄ΡΠ²Π°Ρ Π·Π°Π³ΠΎΡΠΎΠ²ΠΊΡ ΠΏΠΎΠΏΠ΅ΡΠ΅ΠΊ Π½Π°ΠΊΠΎΠ²Π°Π»ΡΠ½ΠΈ, ΡΡΠΎΠ±Ρ Π·Π° ΠΏΡΠ΅Π΄Π΅Π»Π°ΠΌΠΈ Π½Π°ΠΊΠΎΠ²Π°Π»ΡΠ½ΠΈ Π½Π°Ρ
ΠΎΠ΄ΠΈΠ»ΡΡ ΡΡΠ°ΡΡΠΎΠΊ, ΠΏΡΠ΅Π΄Π½Π°Π·Π½Π°ΡΠ΅Π½Π½ΡΠΉ Π΄Π»Ρ Π²ΡΡΠ°Π΄ΠΊΠΈ (ΡΠΈΡ. 244), ΠΏΠΎΠ΄ΡΡΡΠ½ΡΠΉ ΠΏΡΠΈΠΆΠΈΠΌΠ°Π΅Ρ Π·Π°Π³ΠΎΡΠΎΠ²ΠΊΡ ΠΊΡΠ²Π°Π»Π΄ΠΎΠΉ, ΠΏΠΎΠΌΠ΅ΡΠ°Ρ Π΅Π΅ Π½Π°ΠΏΡΠΎΡΠΈΠ² ΠΊΡΠΎΠΌΠΊΠΈ Π½Π°ΠΊΠΎΠ²Π°Π»ΡΠ½ΠΈ, Π° ΠΊΡΠ·Π½Π΅Ρ ΡΡΡΠ½ΠΈΠΊΠΎΠΌ ΠΎΡΡΡΠ΅ΡΡΠ²Π»ΡΠ΅Ρ Π²ΡΡΠ°Π΄ΠΊΡ.
ΠΠ½ΠΎΠ³Π΄Π° ΠΏΡΠΈΡ
ΠΎΠ΄ΠΈΡΡΡ Π²ΡΡΠ°ΠΆΠΈΠ²Π°ΡΡ Π·Π°Π³ΠΎΡΠΎΠ²ΠΊΠΈ Π½Π°ΡΡΠΎΠ»ΡΠΊΠΎ Π±ΠΎΠ»ΡΡΠΎΠΉ Π΄Π»ΠΈΠ½Ρ, ΡΡΠΎ Π½Π° ΡΠ°Π±ΠΎΡΠ΅ΠΉ ΠΏΠΎΠ²Π΅ΡΡ
Π½ΠΎΡΡΠΈ Π½Π°ΠΊΠΎΠ²Π°Π»ΡΠ½ΠΈ ΠΎΡΡΡΠ΅ΡΡΠ²ΠΈΡΡ Π²ΡΡΠ°Π΄ΠΊΡ ΠΏΡΠ°ΠΊΡΠΈΡΠ΅ΡΠΊΠΈ Π½Π΅Π²ΠΎΠ·ΠΌΠΎΠΆΠ½ΠΎ. Π ΡΡΠΎΠΌ ΡΠ»ΡΡΠ°Π΅ Π²ΡΡΠ°Π΄ΠΊΡ Π·Π°Π³ΠΎΡΠΎΠ²ΠΎΠΊ ΠΏΡΠΎΠΈΠ·Π²ΠΎΠ΄ΡΡ Π½Π° ΠΏΡΡΠ΅ Π½Π°ΠΊΠΎΠ²Π°Π»ΡΠ½ΠΈ (ΡΠΈΡ. 245). ΠΠ»Π΅ΡΠΈ Ρ Π·Π°Π³ΠΎΡΠΎΠ²ΠΊΠΎΠΉ ΠΎΠΏΠΈΡΠ°ΡΡ ΠΏΡΠΈ ΡΡΠΎΠΌ Π½Π° ΡΠ°Π±ΠΎΡΡΡ ΠΏΠΎΠ²Π΅ΡΡ
Π½ΠΎΡΡΡ Π½Π°ΠΊΠΎΠ²Π°Π»ΡΠ½ΠΈ. ΠΠ°ΠΈΠ±ΠΎΠ»Π΅Π΅ ΡΠ»ΠΎΠΆΠ½ΠΎ Π²ΡΠΏΠΎΠ»Π½ΡΡΡ Π²ΡΡΠ°Π΄ΠΊΡ ΡΡΠ΅Π΄Π½Π΅ΠΉ ΡΠ°ΡΡΠΈ Π·Π°Π³ΠΎΡΠΎΠ²ΠΊΠΈ. ΠΠ°Π³ΠΎΡΠΎΠ²ΠΊΠ°, Π΄ΠΎΠ»ΠΆΠ½Π° Π±ΡΡΡ Π½Π°Π³ΡΠ΅ΡΠ° ΡΠΎΠ»ΡΠΊΠΎ Π² ΡΠΎΠΌ ΠΌΠ΅ΡΡΠ΅, ΠΊΠΎΡΠΎΡΠΎΠ΅ Π½Π΅ΠΎΠ±Ρ
ΠΎΠ΄ΠΈΠΌΠΎ Π²ΡΡΠ°Π΄ΠΈΡΡ. ΠΠ°ΠΊ ΠΏΡΠ°Π²ΠΈΠ»ΠΎ, Π² Π³ΠΎΡΠ½Π΅ ΡΠ°ΠΊΠΎΠΉ ΡΠΎΡΠ½ΡΠΉ Π½Π°Π³ΡΠ΅Π² ΠΏΡΠΎΠ²Π΅ΡΡΠΈ Π½Π΅Π²ΠΎΠ·ΠΌΠΎΠΆΠ½ΠΎ, ΠΏΠΎΡΡΠΎΠΌΡ ΠΏΠ΅ΡΠ΅Π΄ Π²ΡΡΠ°Π΄ΠΊΠΎΠΉ ΠΏΠΎΠ»ΠΈΠ²Π°ΡΡ Π²ΠΎΠ΄ΠΎΠΉ ΡΠ΅ ΠΌΠ΅ΡΡΠ°, ΠΊΠΎΡΠΎΡΡΠ΅ Π½Π΅ Π΄ΠΎΠ»ΠΆΠ½Ρ Π±ΡΡΡ Π²ΡΡΠ°ΠΆΠ΅Π½Ρ. Π ΡΠΎΠ»ΡΠΊΠΎ ΠΏΠΎΡΠΎΠΌ Π²ΡΡΠ°ΠΆΠΈΠ²Π°ΡΡ Π·Π°Π³ΠΎΡΠΎΠ²ΠΊΡ ΡΠΈΠ»ΡΠ½ΡΠΌΠΈ ΡΠ΄Π°ΡΠ°ΠΌΠΈ.
Π Π°Π·Π½ΠΎΠ²ΠΈΠ΄Π½ΠΎΡΡΡΡ Π²ΡΡΠ°Π΄ΠΊΠΈ ΡΠ²Π»ΡΠ΅ΡΡΡ ΠΈΠ·Π³ΠΎΡΠΎΠ²Π»Π΅Π½ΠΈΠ΅ ΠΌΠ΅ΡΠ°Π»Π»ΠΈΡΠ΅ΡΠΊΠΈΡ ΠΊΠΎΡΡΡΠ»Π΅ΠΉ. ΠΠ· ΡΠΈΠ»ΠΈΠ½Π΄ΡΠΈΡΠ΅ΡΠΊΠΎΠΉ Π·Π°Π³ΠΎΡΠΎΠ²ΠΊΠΈ ΠΎΡΠΊΠΎΠ²ΡΠ²Π°ΡΡ ΡΠ½Π°ΡΠ°Π»Π° ΡΡΠ΅ΡΠΆΠ΅Π½Ρ ΠΊΠΎΡΡΡΠ»Ρ ΠΊΠ²Π°Π΄ΡΠ°ΡΠ½ΠΎΠ³ΠΎ ΠΏΡΠΎΡΠΈΠ»Ρ. ΠΠ΅ΠΎΡΠΊΠΎΠ²Π°Π½Π½ΠΎΠΉ ΠΎΡΡΠ°Π²Π»ΡΡΡ Π»ΠΈΡΡ ΡΡ ΡΠ°ΡΡΡ Π·Π°Π³ΠΎΡΠΎΠ²ΠΊΠΈ, ΠΊΠΎΡΠΎΡΠ°Ρ Π½Π΅ΠΎΠ±Ρ ΠΎΠ΄ΠΈΠΌΠ° Π΄Π»Ρ ΠΏΠΎΠ»ΡΡΠ΅Π½ΠΈΡ Π³ΠΎΠ»ΠΎΠ²ΠΊΠΈ ΠΊΠΎΡΡΡΠ»Ρ, Π»ΠΈΡΠ½ΡΡ ΡΠ°ΡΡΡ ΠΎΡΡΡΠ±Π°ΡΡ. Π‘ΡΠ΅ΡΠΆΠ΅Π½Ρ Π²ΡΡΠ°Π²Π»ΡΡΡ Π² ΡΠΎΠΎΡΠ²Π΅ΡΡΡΠ²ΡΡΡΠ΅Π΅ ΠΎΡΠ²Π΅ΡΡΡΠΈΠ΅ Π³Π²ΠΎΠ·-Π΄ΠΈΠ»ΡΠ½ΠΈ ΠΈ ΡΠ΄Π°ΡΠ°ΠΌΠΈ ΡΡΡΠ½ΠΈΠΊΠ° ΠΎΡΠΊΠΎΠ²ΡΠ²Π°ΡΡ Π³ΠΎΠ»ΠΎΠ²ΠΊΡ ΠΊΠΎΡΡΡΠ»Ρ.
Π ΠΈΡ. 54. ΠΡΡΠ°Π΄ΠΊΠ° | Π ΠΈΡ. 55. ΠΡΡΠ°Π΄ΠΊΠ° Π΄Π»ΠΈΠ½Π½ΠΎΠΉ Π·Π°Π³ΠΎΡΠΎΠ²ΠΊΠΈ | Π ΠΈΡ. 56. ΠΡΡΠ°Π΄ΠΊΠ° Π·Π°Π³ΠΎΡΠΎΠ²ΠΊΠΈ Π½Π° ΠΏΡΡΠ΅ Π½Π°ΠΊΠΎΠ²Π°Π»ΡΠ½ΠΈ | Π ΠΈΡ. 57. ΠΠΈΠ±ΠΊΠ° Π·Π°Π³ΠΎΡΠΎΠ²ΠΊΠΈ |
ΠΠΈΠ±ΠΊΠ°
ΠΠΌΠ΅ΡΡΡΡ Π΄Π²Π° Π²ΠΈΠ΄Π° Π³ΠΈΠ±ΠΊΠΈ Π·Π°Π³ΠΎΡΠΎΠ²ΠΎΠΊ: Π³ΠΈΠ±ΠΊΠ° Π½Π° ΡΠ³ΠΎΠ» ΠΈ Π³ΠΈΠ±ΠΊΠ° ΠΏΠΎ ΡΠ°Π΄ΠΈΡΡΡ. ΠΠΈΠ±ΠΊΡ Π½Π° ΡΠ³ΠΎΠ» Π²ΡΠΏΠΎΠ»Π½ΡΡΡ Π½Π° ΠΎΡΡΡΠΎΠΉ ΠΊΡΠΎΠΌΠΊΠ΅ Π½Π°ΠΊΠΎΠ²Π°Π»ΡΠ½ΠΈ ΠΏΠΎΡΠ»Π΅Π΄ΠΎΠ²Π°ΡΠ΅Π»ΡΠ½ΡΠΌΠΈ ΡΠ΄Π°ΡΠ°ΠΌΠΈ ΡΡΡΠ½ΠΈΠΊΠ° ΠΏΠΎ Π·Π°Π³ΠΎΡΠΎΠ²ΠΊΠ΅ ΡΠ²Π΅ΡΡ
Ρ ΠΈ ΡΠ±ΠΎΠΊΡ Π΄ΠΎ ΡΠ΅Ρ
ΠΏΠΎΡ, ΠΏΠΎΠΊΠ° Π½Π΅ ΠΏΠΎΠ»ΡΡΠΈΡΡΡ Π½ΡΠΆΠ½ΡΠΉ ΡΠ³ΠΎΠ» (ΡΠΈΡ. 57, ΡΠ»Π΅Π²Π°).
Π ΠΈΡ. 58. ΠΠΈΠ±ΠΊΠ° Π½Π° ΡΠΎΠ³Π΅ Π½Π°ΠΊΠΎΠ²Π°Π»ΡΠ½ΠΈ |
Π ΠΈΡ. 59. ΠΡΠΎΠ±ΠΈΠ²ΠΊΠ° ΠΈ ΡΠ°Π·Π΄Π°ΡΠ° ΠΎΡΠ²Π΅ΡΡΡΠΈΡ Π² Π·Π°Π³ΠΎΡΠΎΠ²ΠΊΠ΅ |
ΠΡΠ»ΠΈ Π·Π°Π³ΠΎΡΠΎΠ²ΠΊΠ° Π±ΠΎΠ»ΡΡΠΎΠΉ ΡΠΎΠ»ΡΠΈΠ½Ρ, ΠΏΠΎΠ΄ΡΡΡΠ½ΡΠΉ Π² Π½Π°ΡΠ°Π»Π΅ Π³ΠΈΠ±ΠΊΠΈ ΠΏΡΠΈΠΆΠΈΠΌΠ°Π΅Ρ Π΅Π΅ ΠΊΡΠ²Π°Π»Π΄ΠΎΠΉ ΡΠ²Π΅ΡΡ Ρ, Π° ΠΊΡΠ·Π½Π΅Ρ ΡΠ΄Π°ΡΠ°ΠΌΠΈ ΡΡΡΠ½ΠΈΠΊΠ° Π² ΡΡΠΎ Π²ΡΠ΅ΠΌΡ ΠΏΡΠΎΠΈΠ·Π²ΠΎΠ΄ΠΈΡ Π³ΠΈΠ±ΠΊΡ. ΠΠ°Π²Π΅ΡΡΠ°ΡΡ Π³ΠΈΠ±ΠΊΡ ΠΎΠ΄Π½ΠΈΠΌ ΡΡΡΠ½ΠΈΠΊΠΎΠΌ. ΠΠΈΠ±ΠΊΡ ΠΏΠΎ ΡΠ°Π΄ΠΈΡΡΡ Π²ΡΠΏΠΎΠ»Π½ΡΡΡ Π½Π° ΠΊΡΡΠ³Π»ΠΎΠΌ ΡΠΎΠ³Π΅ Π½Π°ΠΊΠΎΠ²Π°Π»ΡΠ½ΠΈ. Π Π°Π΄ΠΈΡΡ Π³ΠΈΠ±ΠΊΠΈ ΡΠ΅Π³ΡΠ»ΠΈΡΡΡΡ ΠΈΠ·ΠΌΠ΅Π½Π΅Π½ΠΈΠ΅ΠΌ ΡΠ°ΡΡΡΠΎΡΠ½ΠΈΡ ΠΎΡ Π²Π΅ΡΡΠΈΠ½Ρ ΡΠΎΠ³Π° (ΡΠΈΡ. 57, ΡΠΏΡΠ°Π²Π°; 58).
ΠΡΠΎΠ±ΠΈΠ²ΠΊΠ°
ΠΠ»Ρ ΠΊΠ»Π΅ΠΏΠΊΠΈ, ΠΏΡΠΎΠ΄Π΅Π²Π°Π½ΠΈΡ ΡΡΠ΅ΡΠΆΠ½Π΅ΠΉ ΠΈ Π΄ΡΡΠ³ΠΈΡ
ΠΏΠΎΠ΄ΠΎΠ±Π½ΡΡ
ΡΠ΅Π»Π΅ΠΉ Π² ΠΎΠ±ΡΠ°Π±Π°ΡΡΠ²Π°Π΅ΠΌΠΎΠΉ Π·Π°Π³ΠΎΡΠΎΠ²ΠΊΠ΅ ΠΏΡΠ΅Π΄Π²Π°ΡΠΈΡΠ΅Π»ΡΠ½ΠΎ ΠΏΡΠΎΠ±ΠΈΠ²Π°ΡΡ ΡΠ°Π·Π»ΠΈΡΠ½ΡΠ΅ ΠΎΡΠ²Π΅ΡΡΡΠΈΡ. ΠΠ°ΠΏΡΠΈΠΌΠ΅Ρ, Π΅ΡΠ»ΠΈ ΡΡΠ΅Π±ΡΠ΅ΡΡΡ ΠΊΡΡΠ³Π»ΠΎΠ΅ ΠΎΡΠ²Π΅ΡΡΡΠΈΠ΅, ΡΠΎ Π΄Π»Ρ ΡΡΠΎΠ³ΠΎ ΠΈΡΠΏΠΎΠ»ΡΠ·ΡΡΡ Π±ΠΎΡΠΎΠ΄ΠΎΠΊ. ΠΠ°Π³ΠΎΡΠΎΠ²ΠΊΡ ΡΠΊΠ»Π°Π΄ΡΠ²Π°ΡΡ Π½Π° ΠΏΡΠΎΠ±ΠΎΠΉΠ½ΡΡ ΠΏΠ»ΠΈΡΡ, ΡΠΎΠ²ΠΌΠ΅ΡΡΠΈΠ² Π΅Π΅ ΠΎΡΠ²Π΅ΡΡΡΠΈΠ΅ Ρ ΠΌΠ΅ΡΡΠΎΠΌ Π·Π°Π³ΠΎΡΠΎΠ²ΠΊΠΈ, Π² ΠΊΠΎΡΠΎΡΠΎΠΌ Π½ΡΠΆΠ½ΠΎ ΠΏΡΠΎΠ±ΠΈΡΡ ΠΎΡΠ²Π΅ΡΡΡΠΈΠ΅ (ΡΠΈΡ. 59). ΠΠΎΡΠ»Π΅ ΡΠΎΠ³ΠΎ ΠΊΠ°ΠΊ Π·Π°Π³ΠΎΡΠΎΠ²ΠΊΠ° ΠΏΡΠΎΠ±ΠΈΡΠ° ΠΏΡΠΈΠ±Π»ΠΈΠ·ΠΈΡΠ΅Π»ΡΠ½ΠΎ Π½Π° ΠΏΠΎΠ»ΠΎΠ²ΠΈΠ½Ρ ΡΠΎΠ»ΡΠΈΠ½Ρ, ΠΈΠ· Π½Π΅Π΅ ΠΈΠ·Π²Π»Π΅ΠΊΠ°ΡΡ Π±ΠΎΡΠΎΠ΄ΠΎΠΊ, ΠΏΠΎΠ²ΠΎΡΠ°ΡΠΈΠ²Π°ΡΡ Π΅Π΅ ΠΎΠ±ΡΠ°ΡΠ½ΠΎΠΉ ΡΡΠΎΡΠΎΠ½ΠΎΠΉ ΠΈ Π·Π°Π²Π΅ΡΡΠ°ΡΡ ΠΏΡΠΎΠ±ΠΈΠ²ΠΊΡ. ΠΡΠΈ Ρ
ΡΠ΄ΠΎΠΆΠ΅ΡΡΠ²Π΅Π½Π½ΠΎΠΉ ΠΊΠΎΠ²ΠΊΠ΅ ΠΎΡΠ²Π΅ΡΡΡΠΈΠ΅ ΠΏΡΠΎΠ±ΠΈΠ²Π°ΡΡ ΠΎΠ±ΡΡΠ½ΠΎ Π±Π΅Π· ΠΏΠΎΡΠ΅ΡΠΈ ΠΌΠ°ΡΠ΅ΡΠΈΠ°Π»Π°. ΠΠ½Π°ΡΠ°Π»Π΅ ΠΏΡΠΎΠ±ΠΈΠ²Π°ΡΡ ΠΎΡΠ²Π΅ΡΡΡΠΈΠ΅ Π±ΠΎΡΠΎΠ΄ΠΊΠΎΠΌ Π½Π°ΠΈΠΌΠ΅Π½ΡΡΠ΅Π³ΠΎ Π΄ΠΈΠ°ΠΌΠ΅ΡΡΠ°. ΠΠ°ΡΠ΅ΠΌ ΠΎΡΠ²Π΅ΡΡΡΠΈΠ΅ ΡΠ°Π·Π³ΠΎΠ½ΡΡΡ ΡΠΈΠ»ΠΈΠ½Π΄ΡΠΈΡΠ΅ΡΠΊΠΎΠΉ ΠΎΠΏΡΠ°Π²ΠΊΠΎΠΉ, Π΅ΡΠ»ΠΈ ΠΆΠ΅ ΠΎΡΠ²Π΅ΡΡΡΠΈΠ΅ Π΄ΠΎΠ»ΠΆΠ½ΠΎ Π±ΡΡΡ Π΅ΡΠ΅ Π±ΠΎΠ»ΡΡΠ΅, ΡΠΎ Π΅Π³ΠΎ ΡΠ°ΡΡΠΈΡΡΡΡ Π±ΠΎΡΠΊΠΎΠΎΠ±ΡΠ°Π·Π½ΠΎΠΉ ΠΎΠΏΡΠ°Π²ΠΊΠΎΠΉ. ΠΡΠ»ΠΈ Π½Π΅ΠΎΠ±Ρ
ΠΎΠ΄ΠΈΠΌΠΎ ΠΏΠΎΠ»ΡΡΠΈΡΡ ΠΊΠ²Π°Π΄ΡΠ°ΡΠ½ΠΎΠ΅ ΠΎΡΠ²Π΅ΡΡΡΠΈΠ΅, ΡΠΎ ΠΈΡΠΏΠΎΠ»ΡΠ·ΡΡΡ Π±ΠΎΡΠΎΠ΄ΠΎΠΊ, ΠΈΠΌΠ΅ΡΡΠΈΠΉ ΡΠΎΡΠΌΡ ΡΠ΅ΡΡΡΠ΅Ρ
Π³ΡΠ°Π½Π½ΠΎΠΉ ΡΡΠ΅ΡΠ΅Π½Π½ΠΎΠΉ ΠΏΠΈΡΠ°ΠΌΠΈΠ΄Ρ. ΠΠ»Ρ ΠΏΡΠΎΠ΄Π΅Π²Π°Π½ΠΈΡ ΡΡΠ΅ΡΠΆΠ½Π΅ΠΉ ΠΈΠ½ΠΎΠ³Π΄Π° ΡΡΠ΅Π±ΡΡΡΡΡ ΠΏΡΠΎΠ΄ΠΎΠ»ΡΠ½ΡΠ΅ ΠΎΡΠ²Π΅ΡΡΡΠΈΡ ΡΠ°Π·Π»ΠΈΡΠ½ΠΎΠΉ Π΄Π»ΠΈΠ½Ρ. Π ΡΡΠΎΠΌ ΡΠ»ΡΡΠ°Π΅ ΠΈΡΠΏΠΎΠ»ΡΠ·ΡΡΡ Π²ΠΌΠ΅ΡΡΠΎ Π±ΠΎΡΠΎΠ΄ΠΊΠ° Π·ΡΠ±ΠΈΠ»ΠΎ, ΠΊΠΎΡΠΎΡΡΠΌ ΠΏΡΠΎΡΠ΅ΠΊΠ°ΡΡ ΠΎΡΠ²Π΅ΡΡΡΠΈΠ΅ Π½ΡΠΆΠ½ΠΎΠΉ Π΄Π»ΠΈΠ½Ρ. ΠΠΎΡΠ»Π΅Π΄ΠΎΠ²Π°ΡΠ΅Π»ΡΠ½ΠΎΡΡΡ ΠΎΠΏΠ΅ΡΠ°ΡΠΈΠΉ ΠΏΡΠΈ ΡΡΠΎΠΌ Π°Π½Π°Π»ΠΎΠ³ΠΈΡΠ½Π° ΠΏΡΠΎΠ±ΠΈΠ²ΠΊΠ΅ Π±ΠΎΡΠΎΠ΄ΠΊΠΎΠΌ. ΠΡΠΆΠ½ΡΡ ΡΠΎΡΠΌΡ ΠΎΡΠ²Π΅ΡΡΡΠΈΡ ΠΏΠΎΠ»ΡΡΠ°ΡΡ Ρ ΠΏΠΎΠΌΠΎΡΡΡ ΡΠΏΠ΅ΡΠΈΠ°Π»ΡΠ½ΠΎ ΠΈΠ·Π³ΠΎΡΠΎΠ²Π»Π΅Π½Π½ΡΡ
ΠΎΠΏΡΠ°Π²ΠΎΠΊ.
Π ΡΠ±ΠΊΠ°
ΠΡΠΈ ΠΊΠΎΠ²ΠΊΠ΅ Π·Π°Π³ΠΎΡΠΎΠ²ΠΊΡ ΠΎΠ±ΡΡΠ½ΠΎ Π½Π΅ ΡΠ΅ΠΆΡΡ, Π° ΡΡΠ±ΡΡ. ΠΡΠ° ΠΎΠΏΠ΅ΡΠ°ΡΠΈΡ ΠΏΡΠΎΡΡΠ° ΠΈ Π·Π°Π²ΠΈΡΠΈΡ ΠΎΡ ΡΠΎΠ»ΡΠΈΠ½Ρ Π·Π°Π³ΠΎΡΠΎΠ²ΠΊΠΈ. Π’ΠΎΠ½ΠΊΡΡ Π·Π°Π³ΠΎΡΠΎΠ²ΠΊΡ ΡΡΠ±ΡΡ Π½Π° ΠΏΠΎΠ΄ΡΠ΅ΡΠΊΠ΅, ΠΊΠΎΡΠΎΡΡΡ ΠΏΠΎΠΌΠ΅ΡΠ°ΡΡ Π² ΠΎΡΠ²Π΅ΡΡΡΠΈΠ΅ Π½Π°ΠΊΠΎΠ²Π°Π»ΡΠ½ΠΈ . ΠΡΠ»ΠΈ Π·Π°Π³ΠΎΡΠΎΠ²ΠΊΠ° Π±ΠΎΠ»ΡΡΠΎΠΉ ΡΠΎΠ»ΡΠΈΠ½Ρ, ΡΠΎ Π΄ΠΎΠΏΠΎΠ»Π½ΠΈΡΠ΅Π»ΡΠ½ΠΎ ΠΈΡΠΏΠΎΠ»ΡΠ·ΡΡΡ Π·ΡΠ±ΠΈΠ»ΠΎ. ΠΠ°Π³ΠΎΡΠΎΠ²ΠΊΡ ΡΠΊΠ»Π°Π΄ΡΠ²Π°ΡΡ Π½Π° ΠΏΠΎΠ΄ΡΠ΅ΡΠΊΡ, Π° Ρ Π΄ΡΡΠ³ΠΎΠΉ ΡΡΠΎΡΠΎΠ½Ρ ΡΡΡΠ°Π½Π°Π²Π»ΠΈΠ²Π°ΡΡ Π·ΡΠ±ΠΈΠ»ΠΎ; ΠΏΠΎΠ΄ΡΡΡΠ½ΡΠΉ ΡΠΈΠ»ΡΠ½ΡΠΌΠΈ ΡΠ΄Π°ΡΠ°ΠΌΠΈ ΠΊΡΠ²Π°Π»Π΄Ρ ΠΎΡΡΡΠ±Π°Π΅Ρ ΡΠΎΠΎΡΠ²Π΅ΡΡΡΠ²ΡΡΡΡΡ ΡΠ°ΡΡΡ.
ΠΡΠΎΠ΄Π΅Π²Π°Π½ΠΈΠ΅
ΠΠ°ΠΆΠ΄ΡΠΉ, ΠΊΡΠΎ Π·Π°Π½ΠΈΠΌΠ°Π΅ΡΡΡ Ρ
ΡΠ΄ΠΎΠΆΠ΅ΡΡΠ²Π΅Π½Π½ΠΎΠΉ ΠΊΠΎΠ²ΠΊΠΎΠΉ ΠΈ ΡΠ»Π΅ΡΠ°ΡΠ½ΡΠΌ Π΄Π΅Π»ΠΎΠΌ, Π΄ΠΎΠ»ΠΆΠ΅Π½ Π±Π΅Π·ΡΡΠ»ΠΎΠ²Π½ΠΎ ΠΈ Π² ΡΠΎΠ²Π΅ΡΡΠ΅Π½ΡΡΠ²Π΅ Π²Π»Π°Π΄Π΅ΡΡ ΠΎΡΠ½ΠΎΠ²Π°ΠΌΠΈ ΠΊΡΠ·Π½Π΅ΡΠ½ΠΎΠ³ΠΎ Π΄Π΅Π»Π°, ΠΎΠΏΠΈΡΠ°Π½Π½ΡΠΌΠΈ Π²ΠΎ Π²Π²ΠΎΠ΄Π½ΠΎΠΉ ΡΠ°ΡΡΠΈ ΡΠ°Π·Π΄Π΅Π»Π°. ΠΠ΅Π· ΡΡΠΈΡ
Π·Π½Π°Π½ΠΈΠΉ Π½Π΅Π»ΡΠ·Ρ ΠΏΡΠΈΡΡΡΠΏΠΈΡΡ ΠΊ ΡΠ°Π±ΠΎΡΠ΅, ΡΡΠ΅Π±ΡΡΡΠ΅ΠΉ ΠΊΠ°ΠΊ ΠΎΠΏΡΠ΅Π΄Π΅Π»Π΅Π½Π½ΠΎΠΉ ΠΊΠ²Π°Π»ΠΈΡΠΈΠΊΠ°ΡΠΈΠΈ, ΡΠ°ΠΊ ΠΈ ΡΠ°Π»Π°Π½ΡΠ° Ρ
ΡΠ΄ΠΎΠΆΠ½ΠΈΠΊΠ°. ΠΠ»Ρ ΡΠ΅ΡΠ΅ΡΠΎΠΊ ΠΈ Π²ΠΎΡΠΎΡ Ρ
Π°ΡΠ°ΠΊΡΠ΅ΡΠ½Π° ΠΊΠΎΠ½ΡΡΡΡΠΊΡΠΈΡ, ΠΏΡΠ΅Π΄ΡΡΠ°Π²Π»ΡΡΡΠ°Ρ ΡΠΎΠ±ΠΎΠΉ ΠΏΡΠΎΠ΄Π΅ΡΡΠ΅ Π΄ΡΡΠ³ Π² Π΄ΡΡΠ³Π° ΡΡΠ΅ΡΠΆΠ½ΠΈ. Π ΡΡΠ΅ΡΠΆΠ½Π΅, ΡΠ΅ΡΠ΅Π· ΠΊΠΎΡΠΎΡΡΠΉ ΠΏΡΠΎΠ΄Π΅Π²Π°ΡΡ, Π½Π΅Π»ΡΠ·Ρ ΡΡΠ°Π·Ρ ΠΏΡΠΎΡΠ΅ΠΊΠ°ΡΡ ΠΎΡΠ²Π΅ΡΡΡΠΈΠ΅, Π½Π΅ΠΎΠ±Ρ
ΠΎΠ΄ΠΈΠΌΠΎΠ΅ Π΄Π»Ρ ΠΏΡΠΎΠ΄Π΅Π²Π°Π½ΠΈΡ Π΄ΡΡΠ³ΠΎΠ³ΠΎ ΡΡΠ΅ΡΠΆΠ½Ρ. Π’Π°ΠΊ ΠΊΠ°ΠΊ ΠΏΡΠΈ ΡΡΠΎΠΌ Π·Π°Π³ΠΎΡΠΎΠ²ΠΊΠ° ΡΡΠΎΠ½ΡΠ΅ΡΡΡ, ΡΠΎ Π²Π°ΠΆΠ½ΠΎ, ΡΡΠΎΠ±Ρ Π³ΠΎΡΠΎΠ²ΠΎΠ΅ ΠΈΠ·Π΄Π΅Π»ΠΈΠ΅ ΡΠΎ ΡΡΠΎΡΠΎΠ½Ρ Π²ΡΠ³Π»ΡΠ΄Π΅Π»ΠΎ ΡΠ΄ΠΎΠ²Π»Π΅ΡΠ²ΠΎΡΠΈΡΠ΅Π»ΡΠ½ΡΠΌ Π² ΠΊΠΎΠ½ΡΡΡΡΠΊΡΠΈΠΎΠ½Π½ΠΎΠΌ ΠΈ ΡΡΡΠ΅ΡΠΈΡΠ΅ΡΠΊΠΎΠΌ ΡΠΌΡΡΠ»Π΅. Π ΠΌΠ΅ΡΡΠ΅, Π³Π΄Π΅ Π΄ΠΎΠ»ΠΆΠ½ΠΎ Π±ΡΡΡ ΠΎΡΠ²Π΅ΡΡΡΠΈΠ΅, ΡΡΠ΅ΡΠΆΠ΅Π½Ρ ΡΠ»Π΅Π³ΠΊΠ° ΠΏΠ΅ΡΠ΅ΠΆΠΈΠΌΠ°ΡΡ, Π° Π·Π°ΡΠ΅ΠΌ Ρ Π΄Π²ΡΡ
ΡΡΠΎΡΠΎΠ½ ΠΏΡΠΎΡΠ΅ΠΊΠ°ΡΡ (ΡΠΈΡ. 60). ΠΠ»Ρ ΡΡΠΎΠΉ ΡΠ΅Π»ΠΈ ΠΊΡΠ·Π½Π΅Ρ ΠΈΠ·Π³ΠΎΡΠΎΠ²Π»ΡΠ΅Ρ Π΄Π»ΠΈΠ½Π½ΠΎΠ΅ ΠΎΡΡΡΠΎΠ΅ Π·ΡΠ±ΠΈΠ»ΠΎ ΠΊΡΡΠ³Π»ΠΎΠ³ΠΎ ΡΠ΅ΡΠ΅Π½ΠΈΡ (ΡΠΈΡ. 61) Ρ ΡΠΈΡΠΎΠΊΠΈΠΌ ΡΠΊΡΡΠ³Π»Π΅Π½Π½ΡΠΌ ΠΎΡΡΡΠΈΠ΅ΠΌ. ΠΡΠ²Π΅ΡΡΡΠΈΡ Π²ΡΠ΅Π³Π΄Π° ΠΏΡΠΎΡΠ΅ΠΊΠ°ΡΡ ΡΠΎΠ»ΡΠΊΠΎ Π² Π³ΠΎΡΡΡΠ΅ΠΌ ΠΏΡΡΡΠΊΠ΅. Π ΡΡΠΎΠΌ ΡΠ»ΡΡΠ°Π΅ Π½Π°Π³ΡΠ΅Π²Π°Π΅ΡΡΡ ΠΈ ΠΎΡΡΡΠΈΠ΅ Π·ΡΠ±ΠΈΠ»Π°. ΠΠ°ΠΊ ΡΠΎΠ»ΡΠΊΠΎ ΠΏΠΎΡΠ»Π΅ ΠΏΡΠΎΡΠ΅ΡΠΊΠΈ ΠΎΡΠ²Π΅ΡΡΡΠΈΡ Π·ΡΠ±ΠΈΠ»ΠΎ ΠΈΠ·Π²Π»Π΅ΠΊΠ°ΡΡ ΠΈΠ· ΠΏΡΡΡΠΊΠ°, Π΅Π³ΠΎ Π½Π΅ΠΌΠ΅Π΄Π»Π΅Π½Π½ΠΎ Π½Π°Π΄ΠΎ Π·Π°ΠΌΠ°ΡΠΈΠ²Π°ΡΡ, Π° Π² ΡΠ»ΡΡΠ°Π΅ Π½Π΅ΠΎΠ±Ρ
ΠΎΠ΄ΠΈΠΌΠΎΡΡΠΈβ Π·Π°ΡΠ°ΡΠΈΠ²Π°ΡΡ ΠΎΡΡΡΠΈΠ΅. ΠΡΠΈ ΠΏΡΠΎΡΠ΅ΡΠΊΠ΅ ΠΎΠ±ΡΠ°Π·ΡΠ΅ΡΡΡ ΡΠ΄Π»ΠΈΠ½Π΅Π½Π½Π°Ρ ΡΠ·ΠΊΠ°Ρ ΠΏΡΠΎΡΠ΅Π·Ρ, ΠΊΠΎΡΠΎΡΡΡ Π² Π΄Π°Π»ΡΠ½Π΅ΠΉΡΠ΅ΠΌ ΠΏΡΠΎΡΡΠ³ΠΈΠ²Π°ΡΡ Ρ ΠΏΠΎΠΌΠΎΡΡΡ ΠΊΡΡΠ³Π»ΠΎΠΉ ΠΎΠΏΡΠ°Π²ΠΊΠΈ ΠΏΠΎΠ΄Ρ
ΠΎΠ΄ΡΡΠ΅Π³ΠΎ Π΄ΠΈΠ°ΠΌΠ΅ΡΡΠ°. Π’Π°ΠΊΠΎΠ² ΠΏΠΎΡΡΠ΄ΠΎΠΊ ΠΎΠΏΠ΅ΡΠ°ΡΠΈΠΈ ΠΏΡΠΈ ΠΏΡΠΎΠ΄Π΅Π²Π°Π½ΠΈΠΈ ΠΊΡΡΠ³Π»ΡΡ
ΡΡΠ΅ΡΠΆΠ½Π΅ΠΉ, ΠΊΠΎΡΠΎΡΡΠ΅ ΡΠ°ΡΠ΅ Π²ΡΠ΅Π³ΠΎ Π²ΡΡΡΠ΅ΡΠ°ΡΡΡΡ Π² ΡΠ΅ΡΠ΅ΡΠΊΠ°Ρ
ΠΏΠ΅ΡΠΈΠΎΠ΄Π° ΠΠΎΠ·ΡΠΎΠΆΠ΄Π΅Π½ΠΈΡ, ΠΎΠ΄Π½Π°ΠΊΠΎ Π½Π°Ρ
ΠΎΠ΄ΡΡ ΡΠΈΡΠΎΠΊΠΎΠ΅ ΠΏΡΠΈΠΌΠ΅Π½Π΅Π½ΠΈΠ΅ ΠΈ Π² ΡΠΎΠ²ΡΠ΅ΠΌΠ΅Π½Π½ΡΡ
ΠΊΠΎΠ²Π°Π½ΡΡ
ΠΈΠ·Π΄Π΅Π»ΠΈΡΡ
.
|
||||||
Π ΠΈΡ. 60. ΠΠΎΡΠ»Π΅Π΄ΠΎΠ²Π°ΡΠ΅Π»ΡΠ½ΠΎΡΡΡ ΠΏΡΠΎΡΠ΅ΡΠΊΠΈ Π΄Π»Ρ ΠΏΡΠΎΠ΄Π΅Π²Π°Π½ΠΈΡ | Π ΠΈΡ. 66. Π’ΠΎΡΡΠΈΡΠΎΠ²Π°Π½Π½ΡΠ΅ ΠΏΡΡΡΡΡ |
Π‘ΡΠ΅ΡΠΆΠ½ΠΈ ΠΊΠ²Π°Π΄ΡΠ°ΡΠ½ΠΎΠ³ΠΎ ΡΠ΅ΡΠ΅Π½ΠΈΡ ΠΏΡΠΎΡΠ΅ΠΊΠ°ΡΡ Π² ΠΎΡΠ½ΠΎΠ²Π½ΠΎΠΌ ΡΠ΅ΠΌ ΠΆΠ΅ ΡΠΏΠΎΡΠΎΠ±ΠΎΠΌ, ΠΎΠ΄Π½Π°ΠΊΠΎ ΠΎΡΠ²Π΅ΡΡΡΠΈΡ ΠΏΡΠΎΡΡΠ³ΠΈΠ²Π°ΡΡ Π½Π΅ ΠΊΡΡΠ³Π»ΠΎΠΉ, Π° ΡΠΏΠ΅ΡΠΈΠ°Π»ΡΠ½ΠΎΠΉ ΠΎΠΏΡΠ°Π²ΠΊΠΎΠΉ ΠΊΠ²Π°Π΄ΡΠ°ΡΠ½ΠΎΠ³ΠΎ ΡΠ΅ΡΠ΅Π½ΠΈΡ. ΠΡΡ ΠΎΠΏΡΠ°Π²ΠΊΡ ΠΆΠ΅Π»Π°ΡΠ΅Π»ΡΠ½ΠΎ ΠΈΠ·Π³ΠΎΡΠΎΠ²Π»ΡΡΡ Ρ Π½Π°ΠΏΡΠ°Π²Π»ΡΡΡΠ΅ΠΉ ΡΡΠΊΠΎΡΡΠΊΠΎΠΉ, Π·Π° ΠΊΠΎΡΠΎΡΡΡ Π΅Π΅ ΠΌΠΎΠΆΠ½ΠΎ Π΄Π΅ΡΠΆΠ°ΡΡ. Π‘ ΠΏΠΎΠΌΠΎΡΡΡ ΡΠ°ΠΊΠΈΡ ΠΎΠΏΡΠ°Π²ΠΎΠΊ Π² ΡΠ»ΡΡΠ°Π΅ Π½Π΅ΠΎΠ±Ρ ΠΎΠ΄ΠΈΠΌΠΎΡΡΠΈ ΠΌΠΎΠΆΠ½ΠΎ ΠΎΠ±Π΅ΡΠΏΠ΅ΡΠΈΡΡ Π±ΠΎΠ»Π΅Π΅ ΡΠΎΡΠ½ΠΎΠ΅ Π½Π°ΠΏΡΠ°Π²Π»Π΅Π½ΠΈΠ΅ ΠΏΡΠΎΡΠ΅ΠΊΠ°Π΅ΠΌΡΡ ΠΎΡΠ²Π΅ΡΡΡΠΈΠΉ. ΠΡΠΈ ΡΠ°Π±ΠΎΡΠ΅ Ρ ΠΎΠΏΡΠ°Π²ΠΊΠ°ΠΌΠΈ Π±Π΅Π· Π½Π°ΠΏΡΠ°Π²Π»ΡΡΡΠ΅ΠΉ ΡΡΠΊΠΎΡΡΠΊΠΈ Π΄Π°ΠΆΠ΅ ΠΏΡΠΈ Π½Π΅Π±ΠΎΠ»ΡΡΠΈΡ ΠΎΡΠΊΠ»ΠΎΠ½Π΅Π½ΠΈΡΡ ΠΎΡ Π½ΡΠΆΠ½ΠΎΠ³ΠΎ Π½Π°ΠΏΡΠ°Π²Π»Π΅Π½ΠΈΡ ΠΏΡΠΎΡΠ΅ΡΠΊΠΈ ΡΡΡΠ΅ΡΠΈΡΠ΅ΡΠΊΠΈΠΉ Π²ΠΈΠ΄ Π³ΠΎΡΠΎΠ²ΡΡ ΠΈΠ·Π΄Π΅Π»ΠΈΠΉ ΠΌΠΎΠΆΠ΅Ρ ΠΎΠΊΠ°Π·Π°ΡΡΡΡ Π½Π΅ΡΠ΄ΠΎΠ²Π»Π΅ΡΠ²ΠΎΡΠΈΡΠ΅Π»ΡΠ½ΡΠΌ.
ΠΠ½Π°ΡΠΈΡΠ΅Π»ΡΠ½ΠΎ ΡΠ»ΠΎΠΆΠ½Π΅Π΅ ΠΏΡΠΎΠ΄Π΅Π²Π°Π½ΠΈΠ΅ ΠΏΡΡΡΠΊΠΎΠ² ΠΊΠ²Π°Π΄ΡΠ°ΡΠ½ΠΎΠ³ΠΎ ΡΠ΅ΡΠ΅Π½ΠΈΡ ΡΠ΅ΡΠ΅Π· ΡΠ΅Π±ΡΠΎ. ΠΠ»Ρ ΡΡΠΎΠ³ΠΎ Π½Π΅ΠΎΠ±Ρ
ΠΎΠ΄ΠΈΠΌΠΎ ΠΏΡΠΈΡΠΏΠΎΡΠΎΠ±Π»Π΅Π½ΠΈΠ΅ (ΡΠΈΡ. 62β65), ΠΏΠΎΡΡΠ΅Π΄ΠΈΠ½Π΅ ΠΊΠΎΡΠΎΡΠΎΠ³ΠΎ ΠΈΠΌΠ΅Π΅ΡΡΡ ΠΆΠ΅Π»ΠΎΠ±ΠΎΠΊ Π΄Π»Ρ ΡΠΊΠ»Π°Π΄ΠΊΠΈ ΠΏΡΠΎΡΠ΅ΠΊΠ°Π΅ΠΌΠΎΠ³ΠΎ ΡΡΠ΅ΡΠΆΠ½Ρ. ΠΡΠΎΡΠ΅ΡΠΊΡ ΠΎΡΡΡΠ΅ΡΡΠ²Π»ΡΡΡ ΡΠ°ΠΊΠΆΠ΅ Ρ Π΄Π²ΡΡ
ΡΡΠΎΡΠΎΠ½ Π΄ΠΎ ΡΠ΅Ρ
ΠΏΠΎΡ, ΠΏΠΎΠΊΠ° Π½Π°ΠΌΠ΅ΡΠΊΠΈ Π½Π΅ Π²ΡΡΡΠ΅ΡΡΡΡΡ. ΠΡΠΎΡΠ΅ΡΠΊΠ° Π΄Π»Ρ ΡΡΠ΅ΡΠΆΠ½Ρ ΠΊΠ²Π°Π΄ΡΠ°ΡΠ½ΠΎΠ³ΠΎ ΡΠ΅ΡΠ΅Π½ΠΈΡ Π΄ΠΎΠ»ΠΆΠ½Π° Π±ΡΡΡ Π½Π° ‘/Π· Π΄Π»ΠΈΠ½Π½Π΅Π΅, ΡΠ΅ΠΌ Π΄Π»Ρ ΠΊΡΡΠ³Π»ΠΎΠ³ΠΎ, ΡΡΠΎ ΠΎΠ±ΡΡΠ»ΠΎΠ²Π»ΠΈΠ²Π°Π΅ΡΡΡ ΡΠ°Π·Π½ΠΈΡΠ΅ΠΉ ΠΏΠ΅ΡΠΈΠΌΠ΅ΡΡΠΎΠ² ΡΡΠΈΡ
ΡΠ΅ΡΠ΅Π½ΠΈΠΉ. ΠΠ»ΠΈΠ½Π° ΠΎΠΊΡΡΠΆΠ½ΠΎΡΡΠΈ ΠΊΡΡΠ³Π»ΠΎΠ³ΠΎ ΡΠ΅ΡΠ΅Π½ΠΈΡ ΡΠ°Π²Π½Π° 3,140 (Π³Π΄Π΅ D β Π΄ΠΈΠ°ΠΌΠ΅ΡΡ ΡΡΠ΅ΡΠΆΠ½Ρ), ΠΊΠ²Π°Π΄ΡΠ°ΡΠ½ΠΎΠ³ΠΎ 45 (Π³Π΄Π΅ 5 β Π΄Π»ΠΈΠ½Π° ΠΈΠ»ΠΈ ΡΠΈΡΠΈΠ½Π° Π³ΡΠ°Π½ΠΈ). ΠΠΎΡΠ»Π΅ ΠΏΡΠΎΡΠ΅ΡΠΊΠΈ ΠΈΡΠΏΠΎΠ»ΡΠ·ΡΡΡ Π΄ΡΡΠ³ΠΎΠ΅ ΠΏΡΠΈΡΠΏΠΎΡΠΎΠ±Π»Π΅Π½ΠΈΠ΅, ΠΏΠΎΠ΄ΠΎΠ±Π½ΠΎΠ΅ ΠΏΠ΅ΡΠ²ΠΎΠΌΡ, ΠΎΠ΄Π½Π°ΠΊΠΎ ΠΈΠΌΠ΅ΡΡΠ΅Π΅ Π² ΡΠ΅Π½ΡΡΠ΅ ΠΎΡΠ²Π΅ΡΡΡΠΈΠ΅, ΡΠ°Π·ΠΌΠ΅ΡΡ ΠΈ ΡΠΎΡΠΌΠ° ΠΊΠΎΡΠΎΡΠΎΠ³ΠΎ ΡΠΎΠΎΡΠ²Π΅ΡΡΡΠ²ΡΡΡ ΡΠ°Π·ΠΌΠ΅ΡΠ°ΠΌ ΠΈ ΡΠΎΡΠΌΠ΅ ΡΠ΅ΡΠ΅Π½ΠΈΡ Π²Π΄Π΅Π²Π°Π΅ΠΌΠΎΠ³ΠΎ ΠΏΡΡΡΠΊΠ°. Π ΡΡΠΎ ΠΏΡΠΈΡΠΏΠΎΡΠΎΠ±Π»Π΅Π½ΠΈΠ΅ ΡΠΊΠ»Π°Π΄ΡΠ²Π°ΡΡ ΠΏΡΠΎΡΠ΅ΡΠ΅Π½Π½ΡΠΉ ΡΡΠ΅ΡΠΆΠ΅Π½Ρ ΠΈ Π² Π½Π΅ΠΌ ΠΏΡΠΎΡΡΠ³ΠΈΠ²Π°ΡΡ ΠΎΡΠ²Π΅ΡΡΡΠΈΠ΅ Ρ ΠΏΠΎΠΌΠΎΡΡΡ ΠΎΠΏΡΠ°Π²ΠΊΠΈ ΠΊΠ²Π°Π΄ΡΠ°ΡΠ½ΠΎΠ³ΠΎ ΡΠ΅ΡΠ΅Π½ΠΈΡ. Π ΡΠΎΠ²ΡΠ΅ΠΌΠ΅Π½Π½ΠΎΠΉ ΠΊΡΠ·Π½Π΅ΡΠ½ΠΎΠΉ ΠΏΡΠ°ΠΊΡΠΈΠΊΠ΅ ΠΈΡΠΏΠΎΠ»ΡΠ·ΡΡΡ Π²ΡΠ΅ ΠΎΠΏΠΈΡΠ°Π½Π½ΡΠ΅ ΡΠΏΠΎΡΠΎΠ±Ρ. Π§Π°ΡΠ΅ Π²ΡΠ΅Π³ΠΎ ΠΊΡΡΠ³Π»ΡΠ΅ ΡΡΠ΅ΡΠΆΠ½ΠΈ ΠΏΡΠΎΠ΄Π΅Π²Π°ΡΡ ΡΡΠ΅ΡΠΆΠ½ΡΠΌΠΈ ΠΏΡΡΠΌΠΎΡΠ³ΠΎΠ»ΡΠ½ΠΎΠ³ΠΎ ΡΠ΅ΡΠ΅Π½ΠΈΡ ΠΈ Ρ. ΠΏ. Π’ΠΎΠ»ΡΠΊΠΎ ΠΎΡ ΠΊΡΠ·Π½Π΅ΡΠ° Π·Π°Π²ΠΈΡΠΈΡ Π²ΡΠ±ΠΎΡ ΡΠ»Π΅ΠΌΠ΅Π½ΡΠΎΠ² Π΄Π»Ρ ΠΈΠ·Π³ΠΎΡΠΎΠ²Π»Π΅Π½ΠΈΡ ΡΡΠΈΠΌ ΡΠΏΠΎΡΠΎΠ±ΠΎΠΌ ΠΊΠΎΠ½ΡΡΡΡΠΊΡΠΈΠΉ, ΡΠΎΠ·Π΄Π°Π²Π°Π΅ΠΌΡΡ
Ρ
ΡΠ΄ΠΎΠΆΠ΅ΡΡΠ²Π΅Π½Π½ΠΎΠΉ ΠΊΠΎΠ²ΠΊΠΎΠΉ.
Π ΠΈΡ. |
Π‘ΠΊΡΡΡΠΈΠ²Π°Π½ΠΈΠ΅-ΡΠΎΡΡΠΈΡΠΎΠ²Π°Π½ΠΈΠ΅
Π Π±ΡΠ»ΡΠ΅ Π³ΠΎΠ΄Ρ ΠΎΡΠ΅Π½Ρ ΠΏΠΎΠΏΡΠ»ΡΡΠ½ΡΠΌ ΡΠ»Π΅ΠΌΠ΅Π½ΡΠΎΠΌ ΡΠΊΡΠ°ΡΠ΅Π½ΠΈΡ ΠΏΡΠΈ ΠΊΠΎΠΌΠΏΠΎΠ·ΠΈΡΠΈΠΈ ΡΠ΅ΡΠ΅ΡΠΎΠΊ Π±ΡΠ» ΡΠ΅ΡΡΡΠ΅Ρ
Π³ΡΠ°Π½Π½ΡΠΉ ΡΡΠ°Π»ΡΠ½ΠΎΠΉ ΡΡΠ΅ΡΠΆΠ΅Π½Ρ, ΡΠΊΡΡΡΠ΅Π½Π½ΡΠΉ Π² ΡΠΏΠΈΡΠ°Π»Ρ. Π Π½Π°ΡΡΠΎΡΡΠ΅Π΅ Π²ΡΠ΅ΠΌΡ ΡΠΎΠΆΠ΅ Π½Π΅ ΠΎΠ±Ρ
ΠΎΠ΄ΡΡΡΡ Π±Π΅Π· ΡΡΠΎΠ³ΠΎ ΡΠ»Π΅ΠΌΠ΅Π½ΡΠ°. Π§Π΅ΡΡΡΠ΅Ρ
Π³ΡΠ°Π½Π½ΡΠ΅ ΡΡΠ΅ΡΠΆΠ½ΠΈ ‘ΡΠΎΠ»ΡΠΈΠ½ΠΎΠΉ Π΄ΠΎ 20 ΠΌΠΌ ΡΠΊΡΡΡΠΈΠ²Π°ΡΡ, ΠΊΠ°ΠΊ ΠΏΡΠ°Π²ΠΈΠ»ΠΎ, Π² Ρ
ΠΎΠ»ΠΎΠ΄Π½ΠΎΠΌ ΡΠΎΡΡΠΎΡΠ½ΠΈΠΈ. ΠΡΠ»ΠΈ ΠΆΠ΅ ΡΠΊΡΡΡΠΈΠ²Π°ΡΡ ΡΡΠ΅Π±ΡΠ΅ΡΡΡ ΡΡΠ΅ΡΠΆΠ½ΠΈ Π±ΠΎΠ»ΡΡΠΎΠΉ ΡΠΎΠ»ΡΠΈΠ½Ρ, ΠΊΠΎΡΠΎΡΡΠ΅ Π² Ρ
ΠΎΠ»ΠΎΠ΄Π½ΠΎΠΌ ΡΠΎΡΡΠΎΡΠ½ΠΈΠΈ ΡΠΊΡΡΡΠΈΡΡ Π½Π΅Π²ΠΎΠ·ΠΌΠΎΠΆΠ½ΠΎ, ΡΠΎ ΠΏΡΠΈΡ
ΠΎΠ΄ΠΈΡΡΡ ΠΏΡΠΈΠΌΠ΅Π½ΡΡΡ Π½Π°Π³ΡΠ΅Π², ΡΡΠΎ Π½Π΅ ΡΠ°ΠΊ ΠΏΡΠΎΡΡΠΎ. ΠΠ΅ΡΠ°Π²Π½ΠΎΠΌΠ΅ΡΠ½ΠΎ Π½Π°Π³ΡΠ΅ΡΡΠΉ ΡΡΠ΅ΡΠΆΠ΅Π½Ρ ΠΏΡΠΈΠ²ΠΎΠ΄ΠΈΡ ΠΊ Π½Π΅ΡΠ°Π²Π½ΠΎΠΌΠ΅ΡΠ½ΠΎΠΌΡ ΡΠΊΡΡΡΠΈΠ²Π°Π½ΠΈΡ, Ρ. Π΅. ΠΏΠΎΠ»ΡΡΠ°Π΅ΡΡΡ Π±ΡΠ°ΠΊ. ΠΡΠΎ ΠΎΠ±ΡΡΠΎΡΡΠ΅Π»ΡΡΡΠ²ΠΎ ΡΠ²Π»ΡΠ΅ΡΡΡ Π³Π»Π°Π²Π½ΠΎΠΉ ΠΏΡΠΈΡΠΈΠ½ΠΎΠΉ ΡΠΎΠ³ΠΎ, ΡΡΠΎ ΡΡΠ΅ΡΠΆΠ½ΠΈ Π½Π΅Π±ΠΎΠ»ΡΡΠΎΠΉ ΡΠΎΠ»ΡΠΈΠ½Ρ ΡΠΊΡΡΡΠΈΠ²Π°ΡΡ Π² Ρ
ΠΎΠ»ΠΎΠ΄Π½ΠΎΠΌ -ΡΠΎΡΡΠΎΡΠ½ΠΈΠΈ. Π‘ΡΠ΅ΡΠΆΠ½ΠΈ Π±ΠΎΠ»ΡΡΠΎΠΉ ΡΠΎΠ»ΡΠΈΠ½Ρ Π½Π°Π³ΡΠ΅Π²Π°ΡΡ Π² ΠΏΠ΅ΡΠΈ, Π³Π΄Π΅ ΠΌΠΎΠΆΠ½ΠΎ Π³Π°ΡΠ°Π½ΡΠΈΡΠΎΠ²Π°ΡΡ ΡΠ°Π²Π½ΠΎΠΌΠ΅ΡΠ½ΠΎΡΡΡ Π½Π°Π³ΡΠ΅Π²Π°. Π Π³ΠΎΡΠ½Π΅ ΡΠ°ΠΊΠΎΠΉ Π½Π°Π³ΡΠ΅Π² ΠΏΠΎΡΡΠΈ Π½Π΅Π²ΠΎΠ·ΠΌΠΎΠΆΠ΅Π½; ΡΡΠΎΠ³ΠΎ ΠΌΠΎΠ³ΡΡ Π΄ΠΎΠ±ΠΈΡΡΡΡ ΡΠΎΠ»ΡΠΊΠΎ ΠΌΠ°ΡΡΠ΅ΡΠ° ΡΠ²ΠΎΠ΅Π³ΠΎ Π΄Π΅Π»Π° Ρ ΠΌΠ½ΠΎΠ³ΠΎΠ»Π΅ΡΠ½ΠΈΠΌ ΠΎΠΏΡΡΠΎΠΌ.
Π‘ΠΊΡΡΡΠΈΠ²Π°Π½ΠΈΠ΅ ΡΡΠ΅ΡΠΆΠ½Π΅ΠΉ ΡΠΎΠ»ΡΠΈΠ½ΠΎΠΉ Π΄ΠΎ 20 ΠΌΠΌ ΠΏΡΠΎΠΈΠ·Π²ΠΎΠ΄ΠΈΡΡΡ, ΠΊΠ°ΠΊ ΡΠΆΠ΅ Π³ΠΎΠ²ΠΎΡΠΈΠ»ΠΎΡΡ, Π² Ρ
ΠΎΠ»ΠΎΠ΄Π½ΠΎΠΌ ΡΠΎΡΡΠΎΡΠ½ΠΈΠΈ. ΠΡΠ·Π½Π΅Ρ ΡΠΎΡΠ½ΠΎ ΠΎΡΠΌΠ΅ΡΠ°Π΅Ρ ΡΡΠ°ΡΡΠΎΠΊ, ΠΊΠΎΡΠΎΡΡΠΉ Π΄ΠΎΠ»ΠΆΠ΅Π½ Π±ΡΡΡ ΡΠΊΡΡΡΠ΅Π½, ΠΈ Π·Π°ΠΆΠΈΠΌΠ°Π΅Ρ ΡΡΠ΅ΡΠΆΠ΅Π½Ρ ΠΏΠΎ Π½ΠΈΠΆΠ½Π΅ΠΉ ΡΠΈΡΠΊΠ΅ Π² ΡΠΈΡΠΊΠ°Ρ
. ΠΠΎΡΠΎΠΌ Π±Π΅ΡΠ΅Ρ ΡΡΡΠ±ΠΊΡ, ΠΊΠΎΡΠΎΡΡΡ Π»Π΅Π³ΠΊΠΎ Π½Π°Π΄Π΅ΡΡ Π½Π° ΡΠ΅ΡΡΡΠ΅Ρ
Π³ΡΠ°Π½Π½ΡΠΉ ΡΡΠ΅ΡΠΆΠ΅Π½Ρ, ΠΈ ΠΎΠ±ΡΠ΅Π·Π°Π΅Ρ Π΅Π΅ Π½Π° Π΄Π»ΠΈΠ½Ρ ΡΡΠ°ΡΡΠΊΠ° ΡΠΊΡΡΡΠΈΠ²Π°Π½ΠΈΡ. Π’ΡΡΠ±ΠΊΡ Π½Π°Π΄Π΅Π²Π°ΡΡ Π½Π° ΡΡΠ΅ΡΠΆΠ΅Π½Ρ, Π° ΡΠ²Π΅ΡΡ
Ρ Π½Π°Π΄Π΅Π²Π°ΡΡ Π²ΠΎΡΠΎΡ. ΠΠΎΡΠΎΡ Π½Π΅ Π΄ΠΎΠ»ΠΆΠ΅Π½ Π±ΡΡΡ Ρ ΠΎΠ΄Π½ΠΈΠΌ ΠΏΠ»Π΅ΡΠΎΠΌ, ΡΠ°ΠΊ ΠΊΠ°ΠΊ ΡΡΠ΅ΡΠΆΠ΅Π½Ρ ΠΎΠ΄Π½ΠΎΠ²ΡΠ΅ΠΌΠ΅Π½Π½ΠΎ ΡΠΎ ΡΠΊΡΡΡΠΈΠ²Π°Π½ΠΈΠ΅ΠΌ ΠΌΠΎΠΆΠ΅Ρ ΠΏΠΎΠ³Π½ΡΡΡΡΡ, ΠΈ Π΅ΡΠ»ΠΈ Π·Π°ΠΊΡΡΡΠ΅Π½Π½Π°Ρ ΠΏΠΎΠ²Π΅ΡΡ
Π½ΠΎΡΡΡ Π΄ΠΎΠ»ΠΆΠ½Π° Π±ΡΡΡ ΡΠΈΡΡΠΎΠΉ, ΡΠΎ ΠΏΠΎΡΠ»Π΅ ΡΠΊΡΡΡΠΈΠ²Π°Π½ΠΈΡ Π²ΡΡΠΎΠ²Π½ΡΡΡ ΡΡΠ΅ΡΠΆΠ΅Π½Ρ Π±ΡΠ΄Π΅Ρ Π½Π΅ΠΏΡΠΎΡΡΠΎ. Π‘ΠΊΡΡΡΠΈΠ²Π°Π½ΠΈΠ΅ ΡΠ΄ΠΎΠ±Π½ΠΎ Π²ΡΠΏΠΎΠ»Π½ΡΡΡ Π΄Π²ΡΡ
ΠΏΠ»Π΅ΡΠΈΠΌ Π²ΠΎΡΠΎΡΠΎΠΌ, Π° Π΅ΡΠ»ΠΈ ΡΡΠ΅ΡΠΆΠ΅Π½Ρ Π±ΠΎΠ»ΡΡΠΎΠΉ ΡΠΎΠ»ΡΠΈΠ½Ρβ ΡΠΎ ΠΈ ΡΠ΅ΡΡΡΠ΅Ρ
ΠΏΠ»Π΅ΡΠΈΠΌ. ΠΠΎΡΠΎΡ ΠΊΡΡΡΡΡ Π΄ΠΎ ΡΠ΅Ρ
ΠΏΠΎΡ, ΠΏΠΎΠΊΠ° Π½Π΅ ΠΏΠΎΠ»ΡΡΠ°Ρ ΡΡΠ΅Π±ΡΠ΅ΠΌΡΡ Π·Π°ΠΊΡΡΡΠΊΡ. ΠΠ° ΡΡΠ±Π΅ΠΆΠ΅ XIX ΠΈ XX ΡΡΠΎΠ»Π΅ΡΠΈΠΉ Π±ΡΠ» ΡΠ°Π·ΡΠ°Π±ΠΎΡΠ°Π½ ΡΠ°ΠΊ Π½Π°Π·ΡΠ²Π°Π΅ΠΌΡΠΉ ΡΠΎΡΡΠΈΡΠΎΠ²ΠΎΡΠ½ΡΠΉ ΡΡΠ°Π½ΠΎΠΊ, Π½Π° ΠΊΠΎΡΠΎΡΠΎΠΌ ΠΌΠΎΠΆΠ½ΠΎ Π±ΡΠ»ΠΎ ΡΠΊΡΡΡΠΈΠ²Π°ΡΡ Π±Π΅Π· ΠΎΡΠΎΠ±ΡΡ
ΡΡΠΈΠ»ΠΈΠΉ ΠΈ ΠΏΠΎΠΌΠΎΡΠΈ ΡΡΡΠ±ΠΊΠΈ ΡΡΠ΅ΡΠΆΠ½ΠΈ ΡΠΎΠ»ΡΠΈΠ½ΠΎΠΉ Π΄ΠΎ 50 ΠΌΠΌ. Π Π½Π°ΡΠΈ Π΄Π½ΠΈ ΡΡΠΈΡ
ΡΡΠ°Π½ΠΊΠΎΠ² ΡΠΆΠ΅ ΠΏΠΎΡΡΠΈ Π½ΠΈΠ³Π΄Π΅ Π½Π΅Ρ, ΠΈΠΌΠΈ ΠΈΠ½ΠΎΠ³Π΄Π° ΠΏΠΎΠ»ΡΠ·ΡΡΡΡΡ ΡΠΎΠ»ΡΠΊΠΎ Π² Π½Π΅ΠΊΠΎΡΠΎΡΡΡ
ΡΡΠ°ΡΡΡ
Π΄Π΅ΡΠ΅Π²Π΅Π½ΡΠΊΠΈΡ
ΠΊΡΠ·Π½ΠΈΡΠ°Ρ
. ΠΡΠ΅Π½Ρ ΠΊΡΠ°ΡΠΈΠ²ΠΎ Π²ΡΠ³Π»ΡΠ΄ΡΡ ΡΠΎΡΡΠΈΡΠΎΠ²Π°Π½Π½ΡΠ΅ ΡΡΠ΅ΡΠΆΠ½ΠΈ, Ρ ΠΊΠΎΡΠΎΡΡΡ
ΠΏΠ΅ΡΠ΅Π΄ ΡΠΊΡΡΡΠΈΠ²Π°Π½ΠΈΠ΅ΠΌ Π²Π΄ΠΎΠ»Ρ Π²ΡΠ΅Ρ
ΡΠ΅ΡΡΡΠ΅Ρ
Π³ΡΠ°Π½Π΅ΠΉ Π²ΡΠ΄Π°Π²Π»Π΅Π½Ρ Π³Π»ΡΠ±ΠΎΠΊΠΈΠ΅ Π±ΠΎΡΠΎΠ·Π΄ΠΊΠΈ (ΡΠΈΡ. 66). Π‘ΠΊΡΡΡΠΈΠ²Π°ΡΡ ΠΌΠΎΠΆΠ½ΠΎ ΠΈ ΠΏΠ»ΠΎΡΠΊΠΈΠ΅ ΡΡΠ΅ΡΠΆΠ½ΠΈ, ΠΊΠΎΠ³Π΄Π° ΡΠΊΡΠ°ΡΠ΅Π½ΠΈΠ΅ Π΄ΠΎΠ»ΠΆΠ½ΠΎ Π²ΡΠ³Π»ΡΠ΄Π΅ΡΡ Π±ΠΎΠ»Π΅Π΅ Π±ΠΎΠ³Π°ΡΡΠΌ. ΠΡΠ»ΠΈ ΡΠ°ΠΊΠΎΠΉ ΡΡΠ΅ΡΠΆΠ΅Π½Ρ Π·Π°ΠΊΡΡΡΠ΅Π½ ΠΏΡΠ°Π²ΠΈΠ»ΡΠ½ΠΎ, ΡΠΎ ΠΎΠ½ Π²ΡΠ³Π»ΡΠ΄ΠΈΡ ΠΎΡΠ΅Π½Ρ ΡΡΡΠ΅ΠΊΡΠ½ΠΎ.
Π¨ΠΈΡΠΊΠΈ
Π Ρ ΡΠ΄ΠΎΠΆΠ΅ΡΡΠ²Π΅Π½Π½ΠΎΠΉ ΠΊΠΎΠ²ΠΊΠ΅ Ρ Π½Π΅Π·Π°ΠΏΠ°ΠΌΡΡΠ½ΡΡ Π²ΡΠ΅ΠΌΠ΅Π½ ΡΠ°ΡΠΏΡΠΎΡΡΡΠ°Π½Π΅Π½Π½ΡΠΌ ΡΠ»Π΅ΠΌΠ΅Π½ΡΠΎΠΌ ΡΠΊΡΠ°ΡΠ΅Π½ΠΈΡ ΡΠ²Π»ΡΡΡΡΡ ΡΠ°Π·Π»ΠΈΡΠ½ΠΎΠΉ ΡΠΎΡΠΌΡ ΡΠΈΡΠΊΠΈ. ΠΡ Π΄Π΅Π»Π°ΡΡ ΡΠ²Π΅ΡΡΡΠ²Π°Π½ΠΈΠ΅ΠΌ ΠΏΡΠΎΠ²ΠΎΠ»ΠΎΠΊΠΈ Π² ΡΠΏΠΈΡΠ°Π»Ρ ΠΈΠ· ΠΎΠ΄Π½ΠΎΠΉ Π½ΠΈΡΠΊΠΈ Π»ΠΈΠ±ΠΎ ΠΈΠ· ΡΡΠ΅Ρ βΡΠ΅ΡΡΠΈ Π½ΠΈΡΠΎΠΊ, ΡΠ²ΡΠ·Π°Π½Π½ΡΡ Π² ΠΏΡΡΠΎΠΊ. Π¨ΠΈΡΠΊΠΈ ΠΏΠ΅ΡΠ²ΠΎΠ³ΠΎ ΡΠΈΠΏΠ° ΠΈΡΠΏΠΎΠ»ΡΠ·ΡΡΡ Π² ΠΊΠ°ΡΠ΅ΡΡΠ²Π΅ ΠΊΠΎΠ½ΡΠ΅Π²ΡΡ ΡΠ»Π΅ΠΌΠ΅Π½ΡΠΎΠ² Π²ΡΡΡΡΠΏΠΎΠ² Ρ ΡΠ΅ΡΠ΅ΡΠΎΠΊ, ΡΠΎΠ³Π΄Π° ΠΊΠ°ΠΊ Π²ΡΠΎΡΠΎΠΉ β Π² ΠΊΠ°ΡΠ΅ΡΡΠ²Π΅ ΡΠΊΡΠ°ΡΠ΅Π½ΠΈΡ ΡΡΠ΅Π΄ΠΈΠ½Π½ΡΡ ΡΡΠ°ΡΡΠΊΠΎΠ² ΡΡΠ΅ΡΠΆΠ½Π΅ΠΉ ΡΠ΅ΡΠ΅ΡΠΎΠΊ ΠΈΠ»ΠΈ Π΄Π»Ρ ΡΡΠΊΠΎΡΡΠΊΠΈ..
Π¨ΠΈΡΠΊΠΈ ΠΈΠ· ΠΎΠ΄Π½ΠΎΠΉ Π½ΠΈΡΠΊΠΈ Π΄Π΅Π»Π°ΡΡ ΠΏΡΠΎΡΡΠΎ. ΠΠ΅ΡΡΡ ΠΏΡΠΎΠ²ΠΎΠ»ΠΎΠΊΡ Π΄ΠΈΠ°ΠΌΠ΅ΡΡΠΎΠΌ 5β8 ΠΌΠΌ ΠΈ Π² Π·Π°Π²ΠΈΡΠΈΠΌΠΎΡΡΠΈ ΠΎΡ ΡΠ°Π·ΠΌΠ΅ΡΠΎΠ² ΡΠΈΡΠΊΠΈ ΠΎΡΡΠ΅Π·Π°ΡΡ ΠΊΡΡΠΎΠΊ Π½ΡΠΆΠ½ΠΎΠΉ Π΄Π»ΠΈΠ½Ρ. ΠΠΎΠ½Π΅Ρ ΠΏΡΠΎΠ²ΠΎΠ»ΠΎΠΊΠΈ (ΠΏΡΠΈΠ±Π»ΠΈΠ·ΠΈΡΠ΅Π»ΡΠ½ΠΎ 3 ΡΠΌ) ΠΎΡΠ³ΠΈΠ±Π°ΡΡ ΠΏΠΎΠ΄ ΠΏΡΡΠΌΡΠΌ ΡΠ³Π»ΠΎΠΌ, Π° ΠΎΡΡΠ°Π²ΡΡΡΡΡ Π΅Π΅ ΡΠ°ΡΡΡ Π½Π°Π³ΡΠ΅Π²Π°ΡΡ. ΠΡΠΎΠ³Π½ΡΡΡΠΉ ΠΊΠΎΠ½Π΅Ρ ΠΏΡΠΎΠ²ΠΎΠ»ΠΎΠΊΠΈ Π·Π°ΠΆΠΈΠΌΠ°ΡΡ Π² ΡΠΈΡΠΊΠ°Ρ
ΡΠ°ΠΊ, ΡΡΠΎΠ±Ρ Π½Π°Π΄ Π³ΡΠ±ΠΊΠ°ΠΌΠΈ ΡΠΈΡΠΊΠΎΠ² Π²ΡΡΡΡΠΏΠ°Π» ΡΡΠ°ΡΡΠΎΠΊ Π΄Π»ΠΈΠ½ΠΎΠΉ Π½Π΅ Π±ΠΎΠ»Π΅Π΅ ΡΠΎΠ»ΡΠΈΠ½Ρ ΠΏΡΠΎΠ²ΠΎΠ»ΠΎΠΊΠΈ. ΠΠΎΡΠ»Π΅ ΡΡΠΎΠ³ΠΎ ΠΏΡΠΎΠ²ΠΎΠ»ΠΎΠΊΡ ΡΡΠ³ΠΎ Π·Π°ΠΊΡΡΡΠΈΠ²Π°ΡΡ Π²ΠΎΠΊΡΡΠ³ ΠΎΠ±ΡΠ°Π·ΠΎΠ²Π°Π²ΡΠ΅Π³ΠΎΡΡ ΡΠ°ΠΊΠΈΠΌ ΠΎΠ±ΡΠ°Π·ΠΎΠΌ ΡΠ΅Π½ΡΡΠ° Π½Π° ΠΏΠΎΠ»ΠΎΠ²ΠΈΠ½Ρ Π΅Π΅ Π΄Π»ΠΈΠ½Ρ. Π’ΠΎ ΠΆΠ΅ ΡΠ°ΠΌΠΎΠ΅ Π΄Π΅Π»Π°ΡΡ Ρ Π΄ΡΡΠ³ΠΎΠΉ ΠΏΠΎΠ»ΠΎΠ²ΠΈΠ½ΠΎΠΉ ΠΏΡΠΎΠ²ΠΎΠ»ΠΎΠΊΠΈ (ΡΠΈΡ. 67). Π’Π΅ΠΏΠ΅ΡΡ, ΠΊΠΎΠ³Π΄Π° ΡΠΈΡΠΊΠ° ΡΠΊΡΡΡΠ΅Π½Π° Π² ΠΎΠ΄Π½ΠΎΠΉ ΠΏΠ»ΠΎΡΠΊΠΎΡΡΠΈ, ΠΊΡΠ·Π½Π΅Ρ ΠΌΠ°Π»ΡΠΌ ΡΡΡΠ½ΠΈΠΊΠΎΠΌ ΡΠΎΡΠΌΡΠ΅Ρ ΠΈΠ· Π½Π΅Π΅ Π½Π° Π½Π°ΠΊΠΎΠ½Π΅ΡΠ½ΠΈΠΊΠ΅ Π½ΡΠΆΠ½ΡΡ ΡΠΎΡΠΌΡ ΠΈ, Π½Π°ΠΊΠΎΠ½Π΅Ρ, ΠΏΠΎΡΠ»Π΅ ΠΏΠΎΠ΄ΠΎΠ³ΡΠ΅Π²Π° ΡΠ²Π΅ΡΡΡΠ²Π°Π΅Ρ ΠΎΠ±Π΅ ΠΏΠΎΠ»ΠΎΠ²ΠΈΠ½ΠΊΠΈ Π΄ΠΎ ΠΈΡ
ΡΠΌΡΠΊΠ°Π½ΠΈΡ (ΡΠΈΡ.68).
ΠΠ½ΠΎΠ³ΠΎΠ³ΡΠ°Π½Π½ΡΠ΅ ΡΠΈΡΠΊΠΈ Π΄Π΅Π»Π°ΡΡ ΠΈΠ· Π½Π΅ΡΠΊΠΎΠ»ΡΠΊΠΈΡ ΠΊΡΡΠΊΠΎΠ² ΠΏΡΠΎΠ²ΠΎΠ»ΠΎΠΊΠΈ ΠΊΡΡΠ³Π»ΠΎΠ³ΠΎ ΠΈΠ»ΠΈ ΠΊΠ²Π°Π΄ΡΠ°ΡΠ½ΠΎΠ³ΠΎ ΡΠ΅ΡΠ΅Π½ΠΈΡ. ΠΡ Π΄Π»ΠΈΠ½Ρ ΠΊΡΠ·Π½Π΅Ρ ΡΠ°Π·ΠΌΠ΅ΡΠ°Π΅Ρ Π±ΠΎΠ»ΡΡΠ΅ΠΉ Π½Π° 1/4 -1/3 Π² Π·Π°Π²ΠΈΡΠΈΠΌΠΎΡΡΠΈ ΠΎΡ ΡΠ³Π»Π° ΡΠΊΡΡΡΠΈΠ²Π°Π½ΠΈΡ ΠΏΠΎ ΡΡΠ°Π²Π½Π΅Π½ΠΈΡ Ρ ΡΠ°Π·ΠΌΠ΅ΡΠΎΠΌ ΡΠΈΡΠΊΠΈ. ΠΠ΅ΠΏΡΠΎΡΡΠΎΠΉ ΡΠ²Π»ΡΠ΅ΡΡΡ ΡΠΈΡΠΊΠ° ΠΈΠ· ΡΠ΅ΡΡΡΠ΅Ρ ΠΏΡΡΡΠΊΠΎΠ² ΠΏΡΠΎΠ²ΠΎΠ»ΠΎΠΊΠΈ. ΠΡΠ»ΠΈ ΠΆΠ΅ ΡΠΈΡΠΊΡ Π΄Π΅Π»Π°ΡΡ ΠΈΠ· ΠΏΡΡΠΈ ΠΈΠ»ΠΈ ΡΠ΅ΡΡΠΈ ΠΏΡΡΡΠΊΠΎΠ², ΡΠΎ ΠΎΠ΄Π½Ρ ΠΈΠ· Π½ΠΈΡ ΠΎΡΡΠ΅Π·Π°ΡΡ ΠΏΡΠΈΠΌΠ΅ΡΠ½ΠΎ Π½Π° 4 ΡΠΌ Π΄Π»ΠΈΠ½Π½Π΅ΠΉ ΠΈ ΠΎΠ±Π° ΠΊΠΎΠ½ΡΠ° Π΅Π΅’Π·Π°Π³ΠΈΠ±Π°ΡΡ Π½Π° 180Β° (ΡΠΈΡ. 69). ΠΠ°ΡΠ΅ΠΌ ΠΊΡΡΠΊΠΈ ΠΏΡΠΎΠ²ΠΎΠ»ΠΎΠΊΠΈ ΡΠΊΠ»Π°Π΄ΡΠ²Π°ΡΡ ΠΏΠ»ΠΎΡΠ½ΠΎ Π΄ΡΡΠ³ Ρ Π΄ΡΡΠ³ΠΎΠΌ, Π° ΠΊΠΎΠ½ΡΡ ΠΈΡ ΡΠ²Π°ΡΠΈΠ²Π°ΡΡ. ΠΠΎΠ΄Π³ΠΎΡΠΎΠ²Π»Π΅Π½Π½ΡΡ ΡΠ°ΠΊΠΈΠΌ ΡΠΏΠΎΡΠΎΠ±ΠΎΠΌ ΡΠ²ΡΠ·ΠΊΡ Π½Π°Π³ΡΠ΅Π²Π°ΡΡ, Π·Π°ΡΠ΅ΠΌ ΠΎΠ΄ΠΈΠ½ ΠΊΠΎΠ½Π΅Ρ ΡΠ²ΡΠ·ΠΊΠΈ Π·Π°ΠΆΠΈΠΌΠ°ΡΡ Π² ΡΠΈΡΠΊΠ°Ρ , Π° Π½Π° Π΄ΡΡΠ³ΠΎΠΉ Π½Π°Π΄Π΅Π²Π°ΡΡ Π²ΠΎΡΠΎΡΠΎΠΊ ΠΈ Π² ΡΠ°ΠΊΠΎΠΌ ΠΏΠΎΠ»ΠΎΠΆΠ΅Π½ΠΈΠΈ ΡΠ²ΡΠ·ΠΊΡ ΡΠΊΡΡΡΠΈΠ²Π°ΡΡ. Π Π·Π°Π²ΠΈΡΠΈΠΌΠΎΡΡΠΈ ΠΎΡ ΡΠΎΠ³ΠΎ, Π½Π°ΡΠΊΠΎΠ»ΡΠΊΠΎ ΡΠ»ΠΎΠΆΠ½ΡΡ Ρ ΠΎΡΡΡ ΠΏΠΎΠ»ΡΡΠΈΡΡ ΡΠΈΡΠΊΡ, ΡΠ²ΡΠ·ΠΊΡ ΡΠΊΡΡΡΠΈΠ²Π°ΡΡ Π½Π° 1,5β3 ΠΎΠ±ΠΎΡΠΎΡΠ°. ΠΠΎΡΠ»Π΅ ΠΎΡ Π»Π°ΠΆΠ΄Π΅Π½ΠΈΡ ΡΠ²ΡΠ·ΠΊΡ Π½Π°ΡΠΈΠ½Π°ΡΡ ΡΠ°ΡΠΊΡΡΡΠΈΠ²Π°ΡΡ Π² ΠΎΠ±ΡΠ°ΡΠ½ΠΎΠΌ Π½Π°ΠΏΡΠ°Π²Π»Π΅Π½ΠΈΠΈ, Π² ΡΠ΅Π·ΡΠ»ΡΡΠ°ΡΠ΅ ΡΠΊΡΡΡΠ΅Π½Π½Π°Ρ ΡΠ²ΡΠ·ΠΊΠ° Π½Π°ΡΠΈΠ½Π°Π΅Ρ ΡΠ°ΡΠΏΡΡΠΊΠ°ΡΡΡΡ Π΄ΠΎ ΡΠ΅Ρ ΠΏΠΎΡ, ΠΏΠΎΠΊΠ° Π½Π΅ ΠΏΠΎΠ»ΡΡΠΈΡΡΡ ΡΡΠ΅Π±ΡΠ΅ΠΌΠ°Ρ ΡΠΎΡΠΌΠ° ΡΠΈΡΠΊΠΈ. ΠΡΠ»ΠΈ ΡΠΈΡΠΊΡ Π½Π°Π΄ΠΎ ΡΠ΄Π΅Π»Π°ΡΡ ΡΠΈΡΠ΅, ΡΠΎ Π² ΠΏΡΠΎΡΠ΅ΡΡΠ΅ ΡΠ°ΡΠΊΡΡΡΠΈΠ²Π°Π½ΠΈΡ ΡΠ²ΡΠ·ΠΊΡ ΠΎΡΠ°ΠΆΠΈΠ²Π°ΡΡ ΡΡΡΠ½ΠΈΠΊΠΎΠΌ Π² ΠΏΡΠΎΠ΄ΠΎΠ»ΡΠ½ΠΎΠΌ Π½Π°ΠΏΡΠ°Π²Π»Π΅Π½ΠΈΠΈ.
Π¨ΠΈΡΠΊΠΈ ΡΠ°ΠΊΠΎΠ³ΠΎ ΡΠΈΠΏΠ° ΠΊΡΠ·Π½Π΅ΡΡ Π² Π΄Π°Π»Π΅ΠΊΠΎΠΌ ΠΏΡΠΎΡΠ»ΠΎΠΌ Π΄Π΅Π»Π°Π»ΠΈ Π½Π΅ ΠΈΠ· ΡΠ²ΡΠ·ΠΊΠΈ ΠΏΡΡΡΠΊΠΎΠ², Π° ΠΈΠ· ΡΠ΅Π»ΠΎΠ³ΠΎ ΠΏΡΡΡΠΊΠ° ΠΊΠ²Π°Π΄ΡΠ°ΡΠ½ΠΎΠ³ΠΎ ΡΠ΅ΡΠ΅Π½ΠΈΡ, ΡΠ°ΡΡΠ΅ΠΊΠ°Ρ Π΅Π³ΠΎ Π² ΠΏΡΠΎΠ΄ΠΎΠ»ΡΠ½ΠΎΠΌ Π½Π°ΠΏΡΠ°Π²Π»Π΅Π½ΠΈΠΈ Π½Π° Π½Π΅ΡΠΊΠΎΠ»ΡΠΊΠΎ Π²Π΅ΡΠ²Π΅ΠΉ ΡΠ°ΠΊΠΆΠ΅ ΡΠ΅ΡΡΡΠ΅Ρ Π³ΡΠ°Π½Π½ΠΎΠ³ΠΎ ΡΠ΅ΡΠ΅Π½ΠΈΡ, Π° Π·Π°ΡΠ΅ΠΌ Π΅Π³ΠΎ ΡΠΊΡΡΡΠΈΠ²Π°Π»ΠΈ. Π Π½Π°ΡΡΠΎΡΡΠ΅Π΅ Π²ΡΠ΅ΠΌΡ ΠΊΡΠ·Π½Π΅ΡΡ Π²ΠΎΠ·Π²ΡΠ°ΡΠ°ΡΡΡΡ ΠΊ ΡΡΠΎΠΌΡ ΡΠΏΠΎΡΠΎΠ±Ρ, ΡΠ°ΠΊ ΠΊΠ°ΠΊ ΠΏΠΎΠ»ΡΡΠ΅Π½Π½Π°Ρ ΡΠ°ΠΊΠΈΠΌ ΡΠΏΠΎΡΠΎΠ±ΠΎΠΌ ΡΠΈΡΠΊΠ° Π²ΡΠ³Π»ΡΠ΄ΠΈΡ ΠΏΡΠΈΠ²Π»Π΅ΠΊΠ°ΡΠ΅Π»ΡΠ½Π΅Π΅. Π‘ΠΏΠΎΡΠΎΠ±ΠΎΠΌ ΡΠ°ΡΡΠ΅ΠΊΠ°Π½ΠΈΡ Π΄Π΅Π»Π°ΡΡ ΠΎΠ±ΡΡΠ½ΠΎ ΡΠΈΡΠΊΠΈ ΠΈΠ· Π΄Π²ΡΡ ΠΈΠ»ΠΈ ΡΠ΅ΡΡΡΠ΅Ρ Π²Π΅ΡΠ²Π΅ΠΉ. ΠΡΡΡΠΎΠΊ ΠΊΠ²Π°Π΄ΡΠ°ΡΠ½ΠΎΠ³ΠΎ ΡΠ΅ΡΠ΅Π½ΠΈΡ ΡΠ½Π°ΡΠ°Π»Π° Π½Π°Π³ΡΠ΅Π²Π°ΡΡ, Π° Π·Π°ΡΠ΅ΠΌ Π² ΡΠΎΠΎΡΠ²Π΅ΡΡΡΠ²ΡΡΡΠ΅ΠΌ ΠΌΠ΅ΡΡΠ΅ ΡΠ°ΡΡΠ΅ΠΊΠ°ΡΡ Π²Π΄ΠΎΠ»Ρ Π²ΡΠ΅Ρ ΡΠ΅ΡΡΡΠ΅Ρ Π³ΡΠ°Π½Π΅ΠΉ (ΡΠΈΡ. 70) Π΄ΠΎ ΡΠ΅Ρ ΠΏΠΎΡ, ΠΏΠΎΠΊΠ° Π²Π΅ΡΠ²ΠΈ Π½Π΅ ΡΠ°Π·ΠΎΠΉΠ΄ΡΡΡΡ. ΠΠ°ΡΠ΅ΠΌ ΡΠ°ΡΡΠ΅ΡΠ΅Π½Π½ΡΠ΅ Π²Π΅ΡΠ²ΠΈ ΡΠ°ΡΡΡΠ³ΠΈΠ²Π°ΡΡ Π½Π° ΠΎΠΏΡΠ°Π²ΠΊΠ΅ ΠΈ ΠΏΡΠ°Π²ΡΡ Π½Π° ΡΠΎΠ³Π΅ Π½Π°ΠΊΠΎΠ²Π°Π»ΡΠ½ΠΈ, Π·Π°Π²Π°Π»ΠΈΠ²Π°Ρ ΠΎΡΡΡΡΠ΅ ΡΠ΅Π±ΡΠ°, Π²ΠΎΠ·Π½ΠΈΠΊΡΠΈΠ΅ ΠΏΡΠΈ ΡΠ°ΡΡΠ΅ΡΠ΅Π½ΠΈΠΈ. ΠΠΎΡΠ»Π΅ ΡΡΠΎΠ³ΠΎ ΠΏΡΡΡΠΎΠΊ Π½Π°Π³ΡΠ΅Π²Π°ΡΡ ΠΈ ΡΠΊΡΡΡΠΈΠ²Π°ΡΡ ΡΠ°ΠΊ ΠΆΠ΅, ΠΊΠ°ΠΊ ΠΈ ΡΠ²ΡΠ·ΠΊΠΈ. ΠΠΎΡΠ»Π΅ ΠΎΡ Π»Π°ΠΆΠ΄Π΅Π½ΠΈΡβ ΡΠ°ΡΠΊΡΡΡΠΈΠ²Π°ΡΡ Π² ΠΎΠ±ΡΠ°ΡΠ½ΠΎΠΌ Π½Π°ΠΏΡΠ°Π²Π»Π΅Π½ΠΈΠΈ Π΄ΠΎ ΠΎΠ±ΡΠ°Π·ΠΎΠ²Π°Π½ΠΈΡ ΡΠΈΡΠΊΠΈ Π½ΡΠΆΠ½ΠΎΠΉ ΡΠΎΡΠΌΡ. ΠΡΠ»ΠΈ ΠΏΡΡΡΠΎΠΊ ΡΠ°ΡΡΠ΅ΠΊΠ°ΡΡ Π½Π° Π΄Π²Π΅ Π²Π΅ΡΠ²ΠΈ (ΡΠΈΡ. 71, 72), ΡΠΎ ΡΠΈΡΠΊΠΈ ΡΠΎΡΠΌΡΡΡ Π½Π΅Π±ΠΎΠ»ΡΡΠΈΠΌ ΡΠΊΡΡΡΠΈΠ²Π°Π½ΠΈΠ΅ΠΌ. Π¨ΠΈΡΠΊΠ° ΠΏΠΎΠ»ΡΡΠ°Π΅ΡΡΡ ΠΎΡΠ΅Π½Ρ ΡΡΡΠ΅ΠΊΡΠ½ΠΎΠΉ, Π΅ΡΠ»ΠΈ ΠΏΠΎΡΠ»Π΅ ΡΠ°ΡΡΠ΅ΡΠ΅Π½ΠΈΡ ΠΏΡΡΡΠΊΠ° Π²Π΅ΡΠ²ΠΈ ΡΠ°Π·Π²ΠΎΠ΄ΡΡ ΠΏΠΎ ΠΊΠΎΠ½ΡΡΡΡ ΠΊΡΡΠ³Π°, ΠΏΡΠ°Π²ΡΡ, Π° Π·Π°ΡΠ΅ΠΌ Π·Π°ΠΊΡΡΡΠΈΠ²Π°ΡΡ Π½Π° ΠΎΠ΄ΠΈΠ½ ΠΎΠ±ΠΎΡΠΎΡ. ΠΠΏΡΠΎΡΠ΅ΠΌ Π²ΡΠ΅ ΡΡΠΎ Π·Π°Π²ΠΈΡΠΈΡ ΠΎΡ ΠΏΡΠΎΠ΅ΠΊΡΠ° ΠΈΠ·Π΄Π΅Π»ΠΈΡ ΠΈ Π²ΠΊΡΡΠ° ΠΊΡΠ·Π½Π΅ΡΠ°. ΠΠΎΠ·ΠΌΠΎΠΆΠ½ΠΎΡΡΠ΅ΠΉ ΠΏΠΎΠ»ΡΡΠΈΡΡ ΡΠΈΡΠΊΠΈ ΡΠ°Π·Π»ΠΈΡΠ½ΠΎΠΉ ΡΠΎΡΠΌΡ β Π±ΠΎΠ»ΡΡΠΎΠ΅ ΠΌΠ½ΠΎΠΆΠ΅ΡΡΠ²ΠΎ.
ΠΠΎΠ»ΡΡΡ-ΡΠΏΠΈΡΠ°Π»ΠΈ
ΠΠ°ΠΈΠ±ΠΎΠ»Π΅Π΅ ΡΠ°ΡΠΏΡΠΎΡΡΡΠ°Π½Π΅Π½Π½ΡΠΌΠΈ Π΄Π΅ΠΊΠΎΡΠ°ΡΠΈΠ²Π½ΡΠΌΠΈ ΡΠ»Π΅ΠΌΠ΅Π½ΡΠ°ΠΌΠΈ Π² Ρ ΡΠ΄ΠΎΠΆΠ΅ΡΡΠ²Π΅Π½Π½ΠΎΠΉ ΠΊΠΎΠ²ΠΊΠ΅, ΠΏΠΎ-Π²ΠΈΠ΄ΠΈΠΌΠΎΠΌΡ, ΡΠ²Π»ΡΡΡΡΡ Π²ΠΎΠ»ΡΡΡ. Π ΡΠ²ΠΎΠ΅ΠΉ ΠΎΡΠ½ΠΎΠ²Π΅ ΠΎΠ½ΠΈ Π²ΠΎΡΡ ΠΎΠ΄ΡΡ ΠΊ ΠΈΠΎΠ½ΠΈΡΠ΅ΡΠΊΠΎΠΌΡ ΡΡΠΈΠ»Ρ, ΠΏΡΠ΅Π΄ΡΡΠ°Π²Π»ΡΡ ΡΠΎΠ±ΠΎΠΉ Π½Π°ΠΈΠ±ΠΎΠ»Π΅Π΅ Ρ Π°ΡΠ°ΠΊΡΠ΅ΡΠ½ΡΠΉ ΡΠ»Π΅ΠΌΠ΅Π½Ρ ΠΊΠ°ΠΏΠΈΡΠ΅Π»Π΅ΠΉ ΠΈΠΎΠ½ΠΈΡΠ΅ΡΠΊΠΈΡ ΠΊΠΎΠ»ΠΎΠ½Π½. ΠΠΎΠ²ΠΊΠ° Π²ΠΎΠ»ΡΡΡ ΠΎΡΡΡΠ΅ΡΡΠ²Π»ΡΠ΅ΡΡΡ ΡΠ²ΠΎΠ±ΠΎΠ΄Π½ΡΠΌ ΡΠΏΠΎΡΠΎΠ±ΠΎΠΌ, ΠΏΡΠΈ ΡΡΠΎΠΌ ΠΏΠΎΠ»ΡΡΠ΅Π½ΠΈΠ΅ ΠΏΡΠ°Π²ΠΈΠ»ΡΠ½ΠΎΠΉ ΡΠΏΠΈΡΠ°Π»ΡΠ½ΠΎΠΉ ΡΠΎΡΠΌΡ ΡΠ΅Π»ΠΈΠΊΠΎΠΌ Π·Π°Π²ΠΈΡΠΈΡ ΠΎΡ ΠΌΠ°ΡΡΠ΅ΡΡΡΠ²Π° ΠΊΡΠ·Π½Π΅ΡΠ°-Ρ ΡΠ΄ΠΎΠΆΠ½ΠΈΠΊΠ°.
Π ΠΈΡ. 73. ΠΠΎΠ²ΠΊΠ° ΡΠΏΠΈΡΠ°Π»ΠΈ | Π ΠΈΡ. 74. ΠΠ΅ΠΊΠΎΡΠ°ΡΠΈΠ²Π½Π°Ρ Π²ΠΎΠ»ΡΡΠ° | Π ΠΈΡ. 75. Π‘ΠΏΠΈΡΠ°Π»Ρ |
Π ΡΠ»Π΅ΡΠ°ΡΠ½ΠΎΠΌ Π΄Π΅Π»Π΅ ΠΏΡΠΈ ΠΈΠ·Π³ΠΎΡΠΎΠ²Π»Π΅Π½ΠΈΠΈ ΠΎΠ΄Π½ΠΎΡΠΈΠΏΠ½ΡΡ ΠΌΠ΅Π»ΠΊΠΈΡ ΡΠΏΠΈΡΠ°Π»Π΅ΠΉ, ΡΡΠ΅Π±ΡΡΡΠΈΡ ΡΡ Π² ΡΠ΅ΡΠ΅ΡΠΊΠ°Ρ ΠΈ Π΄ΡΡΠ³ΠΈΡ ΠΈΠ·Π΄Π΅Π»ΠΈΡΡ Π² Π±ΠΎΠ»ΡΡΠΈΡ ΠΊΠΎΠ»ΠΈΡΠ΅ΡΡΠ²Π°Ρ , ΠΏΠΎΠ»ΡΠ·ΡΡΡΡΡ ΡΠ°Π±Π»ΠΎΠ½Π°ΠΌΠΈ, ΠΊΠΎΡΠΎΡΡΠ΅ ΠΎΠ±Π»Π΅Π³ΡΠ°ΡΡ ΡΠ°Π±ΠΎΡΡ, Π΄Π΅Π»Π°ΡΡ Π΅Π΅ Π½Π΅Π·Π°Π²ΠΈΡΠΈΠΌΠΎΠΉ ΠΎΡ ΠΌΠ°ΡΡΠ΅ΡΡΡΠ²Π° ΠΈΡΠΏΠΎΠ»Π½ΠΈΡΠ΅Π»Ρ, ΡΡΠΊΠΎΡΡΡΡ ΠΏΡΠΎΡΠ΅ΡΡ ΠΈΠ·Π³ΠΎΡΠΎΠ²Π»Π΅Π½ΠΈΡ ΠΈ ΠΏΠΎΠ²ΡΡΠ°ΡΡ ΡΠΎΡΠ½ΠΎΡΡΡ ΡΠ°Π·ΠΌΠ΅ΡΠΎΠ² ΡΠΏΠΈΡΠ°Π»Π΅ΠΉ. ΠΡΠ·Π½Π΅Ρ-Ρ ΡΠ΄ΠΎΠΆΠ½ΠΈΠΊ, Π½Π°ΠΎΠ±ΠΎΡΠΎΡ, ΠΊΠ°ΠΊ ΡΠΆΠ΅ Π±ΡΠ»ΠΎ ΡΠΊΠ°Π·Π°Π½ΠΎ, Π²ΠΎΠ»ΡΡΡ ΠΊΡΠ΅Ρ. Π Π·Π°Π²ΠΈΡΠΈΠΌΠΎΡΡΠΈ ΠΎΡ ΡΠ°Π·ΠΌΠ΅ΡΠΎΠ² Π²ΠΎΠ»ΡΡΡ ΡΠ»Π΅Π΄ΡΠ΅Ρ ΠΏΡΠ΅ΠΆΠ΄Π΅ Π²ΡΠ΅Π³ΠΎ ΠΎΠΏΡΠ΅Π΄Π΅Π»ΠΈΡΡ Π½Π΅ΠΎΠ±Ρ ΠΎΠ΄ΠΈΠΌΡΡ Π΄Π»ΠΈΠ½Ρ Π·Π°Π³ΠΎΡΠΎΠ²ΠΊΠΈ. ΠΡΠΎΡΠ΅ Π²ΡΠ΅Π³ΠΎ ΠΎΠΏΡΠ΅Π΄Π΅Π»ΠΈΡΡ Π΄Π»ΠΈΠ½Ρ Ρ ΠΏΠΎΠΌΠΎΡΡΡ ΡΠΎΠ½ΠΊΠΎΠΉ ΠΏΡΠΎΠ²ΠΎΠ»ΠΎΠΊΠΈ, ΠΊΠΎΡΠΎΡΡΡ ΡΠΊΡΡΡΠΈΠ²Π°ΡΡ ΠΏΠΎ ΡΠΎΡΠΌΠ΅ Π²ΠΎΠ»ΡΡΡ. Π Π°ΡΠΏΡΡΠΌΠΈΠ² ΠΏΡΠΎΠ²ΠΎΠ»ΠΎΠΊΡ, ΠΎΠΏΡΠ΅Π΄Π΅Π»ΡΡΡ ΡΡΠ΅Π±ΡΠ΅ΠΌΡΡ Π΄Π»ΠΈΠ½Ρ Π·Π°Π³ΠΎΡΠΎΠ²ΠΊΠΈ. ΠΠ°Π»Π΅Π΅ ΠΎΡΡΡΠ±Π°ΡΡ Π·Π°Π³ΠΎΡΠΎΠ²ΠΊΡ ΡΡΠΎΠΉ Π΄Π»ΠΈΠ½Ρ ΠΈ Π½Π°Π³ΡΠ΅Π²Π°ΡΡ Π΅Π΅ Ρ ΠΎΠ΄Π½ΠΎΠ³ΠΎ ΠΊΠΎΠ½ΡΠ°. ΠΠ° Π½Π°ΠΊΠΎΠ²Π°Π»ΡΠ½Π΅ ΠΏΡΠΎΠΈΠ·Π²ΠΎΠ΄ΡΡ Π·Π°ΠΊΠΎΠ½ΡΠΎΠ²ΠΊΡ Π²ΠΎΠ»ΡΡΡ ΠΈ ΠΏΠΎΡΠΎΠΌ Π½Π° ΡΠ΅Π±ΡΠ΅ ΠΈΠ»ΠΈ ΡΠΎΠ³Π΅ Π½Π°ΠΊΠΎΠ²Π°Π»ΡΠ½ΠΈ ΠΎΡΠΎΡΠΌΠ»ΡΡΡ Π΅Π΅ ΠΎΡΠ½ΠΎΠ²Π½ΠΎΠΉ Π½Π°ΠΈΠ±ΠΎΠ»Π΅Π΅ ΠΊΡΡΡΠΎΠΉ Π·Π°Π²ΠΈΡΠΎΠΊ. ΠΠΎΡΠ»Π΅ ΡΡΠΎΠ³ΠΎ ΡΠ½ΠΎΠ²Π° Π½Π°Π³ΡΠ΅Π²Π°ΡΡ Π·Π°Π³ΠΎΡΠΎΠ²ΠΊΡ Π½Π° Π²ΠΎΠ·ΠΌΠΎΠΆΠ½ΠΎ Π±ΠΎΠ»ΡΡΡΡ Π΄Π»ΠΈΠ½Ρ ΠΈ Ρ ΠΏΠΎΠΌΠΎΡΡΡ ΡΠΏΠΈΡΠ°Π»ΡΠ½ΠΎΠΉ ΠΎΠΏΡΠ°Π²ΠΊΠΈ (ΡΠΈΡ. 73) ΠΊΡΡΡ ΡΠΏΠΈΡΠ°Π»Ρ. ΠΠΎΠ½ΡΡ Π²ΠΎΠ»ΡΡ ΠΌΠΎΠΆΠ½ΠΎ ΡΠΊΡΠ°ΡΠΈΡΡ ΠΆΠ΅Π»ΠΎΠ±ΠΊΠ°ΠΌΠΈ ΠΈΠ»ΠΈ Π΄ΡΡΠ³ΠΈΠΌ ΠΎΡΠ½Π°ΠΌΠ΅Π½ΡΠΎΠΌ.
ΠΡΠΈ Π½Π΅ΠΎΠ±Ρ ΠΎΠ΄ΠΈΠΌΠΎΡΡΠΈ ΠΈΠ·Π³ΠΎΡΠΎΠ²Π»Π΅Π½ΠΈΡ Π±ΠΎΠ»ΡΡΠΎΠ³ΠΎ ΡΠΈΡΠ»Π° ΠΎΠ΄ΠΈΠ½Π°ΠΊΠΎΠ²ΡΡ ΡΠΏΠΈΡΠ°Π»Π΅ΠΉ ΠΊΡΠ·Π½Π΅Ρ ΠΎΠ±ΡΡΠ½ΠΎ Π΄Π΅Π»Π°Π΅Ρ ΡΠ°Π±Π»ΠΎΠ½. Π§ΡΠΎΠ±Ρ ΡΠ°Π±Π»ΠΎΠ½ ΠΈΠΌΠ΅Π» ΠΏΡΠ°Π²ΠΈΠ»ΡΠ½ΡΡ ΡΠΎΡΠΌΡ, Π½Π΅ΠΎΠ±Ρ ΠΎΠ΄ΠΈΠΌΠΎ ΠΏΡΠ΅ΠΆΠ΄Π΅ Π²ΡΠ΅Π³ΠΎ ΠΎΡΠΊΠΎΠ²Π°ΡΡ ΡΡΠ°Π»ΠΎΠ½Π½ΡΡ ΡΠΏΠΈΡΠ°Π»Ρ. ΠΠΎ ΡΡΠΎΠΉ ΡΠΏΠΈΡΠ°Π»ΠΈ Π΄Π΅Π»Π°ΡΡ ΡΠ°Π±Π»ΠΎΠ½ ΡΠ°ΠΊΠΈΠΌ ΠΎΠ±ΡΠ°Π·ΠΎΠΌ, ΡΡΠΎΠ±Ρ Π² Π΅Π³ΠΎ ΠΊΠΎΠ½ΡΡΡΡ Π²ΠΏΠΈΡΡΠ²Π°Π»ΡΡ ΠΊΠ°ΠΆΠ΄ΡΠΉ ΠΎΠ±ΠΎΡΠΎΡ ΡΠΏΠΈΡΠ°Π»ΠΈ ΠΈ ΡΠΎΠ»ΡΠΈΠ½Π° Π·Π°Π³ΠΎΡΠΎΠ²ΠΊΠΈ, ΠΏΡΠ΅Π΄Π½Π°Π·Π½Π°ΡΠ΅Π½Π½ΠΎΠΉ Π΄Π»Ρ ΠΈΠ·Π³ΠΎΡΠΎΠ²Π»Π΅Π½ΠΈΡ ΡΠΏΠΈΡΠ°Π»ΠΈ. Π ΡΠ΅Π½ΡΡΠ΅ ΡΠ°Π±Π»ΠΎΠ½Π° ΠΏΠΎΠΌΠ΅ΡΠ°ΡΡ Π·Π°Ρ Π²Π°Ρ, Π² ΠΊΠΎΡΠΎΡΡΠΉ Π²ΡΡΠ°Π²Π»ΡΡΡ ΠΡΠ΅Π΄Π²Π°ΡΠΈΡΠ΅Π»ΡΠ½ΠΎ ΠΎΡΠΊΠΎΠ²Π°Π½Π½ΡΡ Π·Π°ΠΊΠΎΠ½ΡΠΎΠ²ΠΊΡ ΡΠΏΠΈΡΠ°Π»ΠΈ. Π‘ΠΎΠ±ΡΡΠ²Π΅Π½Π½ΠΎ ΠΏΡΠΎΡΠ΅ΡΡ Π·Π°ΠΊΡΡΡΠΊΠΈ ΠΏΠΎ ΡΠ°Π±Π»ΠΎΠ½Ρ Π²ΡΠΏΠΎΠ»Π½ΡΡΡ Ρ ΠΏΠΎΠΌΠΎΡΡΡ ΡΠΏΠ΅ΡΠΈΠ°Π»ΡΠ½ΠΎ ΠΈΠ·Π³ΠΎΡΠΎΠ²Π»Π΅Π½Π½ΠΎΠ³ΠΎ Π΄Π»Ρ ΡΡΠΎΠΉ ΡΠ΅Π»ΠΈ Ρ ΠΎΠΌΡΡΠ°. ΠΠ³ΠΈΠ±Π°Π½ΠΈΠ΅ ΠΏΠΎ ΡΠ°Π±Π»ΠΎΠ½Ρ Π΄ΠΎΠ»ΠΆΠ½ΠΎ Π±ΡΡΡ ΠΏΠ»Π°Π²Π½ΡΠΌ, Π½ΠΈΠ³Π΄Π΅ Π½Π΅Π»ΡΠ·Ρ Π΄ΠΎΠΏΡΡΠΊΠ°ΡΡ ΠΏΠ΅ΡΠ΅Π»ΠΎΠΌΠΎΠ². Π’ΠΎΠ»ΡΠΊΠΎ ΠΏΠΎΡΠ»Π΅ Π·Π°Π²Π΅ΡΡΠ΅Π½ΠΈΡ Π·Π°ΠΊΡΡΡΠΊΠΈ ΡΠ²Π΅ΡΠ½ΡΡΡΠΉ ΡΠ°Π±Π»ΠΎΠ½ Π²ΡΡΠ°Π²Π½ΠΈΠ²Π°ΡΡ Π½Π° ΠΏΠ»ΠΎΡΠΊΠΎΠΉ ΠΏΠΎΠ²Π΅ΡΡ Π½ΠΎΡΡΠΈ.
ΠΠΎ ΡΠΎΡΠΌΠ΅ Π²ΠΎΠ»ΡΡΡ ΠΌΠΎΠ³ΡΡ Π±ΡΡΡ ΠΎΠ΄Π½ΠΎΡΡΠΎΡΠΎΠ½Π½ΠΈΠΌΠΈ, Π΄Π²ΡΡΡΠΎΡΠΎΠ½Π½ΠΈΠΌΠΈ, Ρ ΠΎΠ±ΡΠ°ΡΠ½ΠΎΠΉ Π·Π°ΠΊΡΡΡΠΊΠΎΠΉ ΠΈ Ρ ΡΠ°Π·Π²Π΅ΡΠ²Π»Π΅Π½ΠΈΠ΅ΠΌ ΠΎΡ ΠΎΠ΄Π½ΠΎΠ³ΠΎ ΠΏΡΡΡΠΊΠ° (ΡΠΈΡ. 74, 75). ΠΠ°Π³ΠΎΡΠΎΠ²ΠΊΠΈ, ΠΏΡΠ΅Π΄Π½Π°Π·Π½Π°ΡΠ΅Π½Π½ΡΠ΅ Π΄Π»Ρ ΠΈΠ·Π³ΠΎΡΠΎΠ²Π»Π΅Π½ΠΈΡ Π²ΠΎΠ»ΡΡ, ΠΌΠΎΠΆΠ½ΠΎ ΡΠΊΡΠ°ΡΠΈΡΡ ΠΏΡΠΎΠ΄ΠΎΠ»ΡΠ½ΡΠΌΠΈ ΠΆΠ΅Π»ΠΎΠ±ΠΊΠ°ΠΌΠΈ ΠΈΠ»ΠΈ ΠΎΡΠ½Π°ΠΌΠ΅Π½ΡΠ°ΠΌΠΈ, Π²ΡΠΏΠΎΠ»Π½Π΅Π½Π½ΡΠΌΠΈ Ρ ΠΏΠΎΠΌΠΎΡΡΡ ΡΠ΅ΠΊΠ°Π½ΠΎΠ² ΠΈΠ»ΠΈ ΡΠ΅Π»ΡΠ΅ΡΠ½ΡΡ ΠΏΡΠ°Π½ΡΠΎΠ½ΠΎΠ². Π ΠΏΠ΅ΡΠΈΠΎΠ΄ Π½Π°ΠΈΠ±ΠΎΠ»ΡΡΠ΅Π³ΠΎ ΡΠΏΠ°Π΄ΠΊΠ° Ρ ΡΠ΄ΠΎΠΆΠ΅ΡΡΠ²Π΅Π½Π½ΠΎΠΉ ΠΊΠΎΠ²ΠΊΠΈ, ΠΊΠΎΠ³Π΄Π° ΠΈΠ·Π΄Π΅Π»ΠΈΡ ΡΡΠ°Π»ΠΈ ΠΏΡΠΎΠΈΠ·Π²ΠΎΠ΄ΠΈΡΡ ΡΠ΅ΡΠΈΠΉΠ½ΠΎ, ΠΏΠΎΠ²Π΅ΡΡ Π½ΠΎΡΡΡ Π·Π°Π³ΠΎΡΠΎΠ²ΠΊΠΈ ΡΡΠ°Π»ΠΈ Π΄Π΅ΠΊΠΎΡΠΈΡΠΎΠ²Π°ΡΡ ΡΠ°Π·Π»ΠΈΡΠ½ΡΠΌΠΈ ΠΌΠΎΠ»ΠΎΡΠΎΡΠΊΠ°ΠΌΠΈ Ρ Π½Π°ΡΠ΅ΡΠΊΠΎΠΉ, ΡΡΠΎΠ±Ρ ΠΈΠ·Π΄Π΅Π»ΠΈΠ΅ Π²ΡΠ³Π»ΡΠ΄Π΅Π»ΠΎ ΠΊΠ°ΠΊ ΡΡΠ°ΡΠΈΠ½Π½ΠΎΠ΅. Π’Π°ΠΊΠΎΠ΅ Π΄Π΅ΠΊΠΎΡΠΈΡΠΎΠ²Π°Π½ΠΈΠ΅ Π½Π΅ ΠΎΡΠ»ΠΈΡΠ°Π΅ΡΡΡ Π½ΠΈ Π²ΠΊΡΡΠΎΠΌ, Π½ΠΈ ΠΈΠ·ΡΡΠ΅ΡΡΠ²ΠΎΠΌ, ΠΏΠΎΡΡΠΎΠΌΡ Π½Π°ΡΡΠΎΡΡΠΈΠΉ ΠΌΠ°ΡΡΠ΅Ρ Ρ ΡΠ΄ΠΎΠΆΠ΅ΡΡΠ²Π΅Π½Π½ΠΎΠΉ ΠΊΠΎΠ²ΠΊΠΈ Π½ΠΈΠΊΠΎΠ³Π΄Π° Π½Π΅ ΠΏΠΎΠ·Π²ΠΎΠ»ΠΈΡ ΡΠ΅Π±Π΅ ΠΈΡΠΏΠΎΠ»ΡΠ·ΠΎΠ²Π°ΡΡ ΠΏΠΎΠ΄ΠΎΠ±Π½ΡΠΉ ΡΠΏΠΎΡΠΎΠ± ΠΎΠ±ΡΠ°Π±ΠΎΡΠΊΠΈ.
Π‘Π²Π΅ΡΡΠΊΠ° ΠΊΠΎΠ»Π΅Ρ
ΠΡΠΈ ΠΈΠ·Π³ΠΎΡΠΎΠ²Π»Π΅Π½ΠΈΠΈ ΡΠ°Π·Π»ΠΈΡΠ½ΡΡ ΠΏΡΠ΅Π΄ΠΌΠ΅ΡΠΎΠ² Π±ΡΡΠ°, Π½Π°ΠΏΡΠΈΠΌΠ΅Ρ Π»ΡΡΡΡ ΠΈ ΠΏΠΎΠ΄ΠΎΠ±Π½ΡΡ ΠΈΠΌ ΠΈΠ·Π΄Π΅Π»ΠΈΠΉ, ΡΠ°ΡΡΠΎ ΡΡΠ΅Π±ΡΠ΅ΡΡΡ ΡΠ²Π΅ΡΠ½ΡΡΡ Π·Π°Π³ΠΎΡΠΎΠ²ΠΊΡ Π² ΠΊΠΎΠ»ΡΡΠΎ ΡΠΎΠ³ΠΎ ΠΈΠ»ΠΈ ΠΈΠ½ΠΎΠ³ΠΎ Π΄ΠΈΠ°ΠΌΠ΅ΡΡΠ°. Π Ρ ΠΎΡΠΎΡΠΎ ΠΎΠ±ΠΎΡΡΠ΄ΠΎΠ²Π°Π½Π½ΡΡ ΠΊΡΠ·Π½ΠΈΡΠ°Ρ Π½Π΅ΠΏΡΠ΅ΠΌΠ΅Π½Π½ΠΎ Π΄ΠΎΠ»ΠΆΠ½ΠΎ Π±ΡΡΡ Π² Π½Π°Π»ΠΈΡΠΈΠΈ ΠΎΠ΄Π½ΠΎ ΠΈΠ· Π½Π°ΠΈΠ±ΠΎΠ»Π΅Π΅ ΡΡΠ°ΡΡΡ ΠΊΡΠ·Π½Π΅ΡΠ½ΡΡ ΠΏΡΠΈΡΠΏΠΎΡΠΎΠ±Π»Π΅Π½ΠΈΠΉ β ΡΡΡΡΠΎΠΉΡΡΠ²ΠΎ Π΄Π»Ρ ΡΠ²Π΅ΡΡΠΊΠΈ ΠΎΠ±ΠΎΠ΄ΠΎΠ², ΠΊΠΎΡΠΎΡΠΎΠ΅ ΡΡΠ°ΡΡΠ΅ ΠΌΠ°ΡΡΠ΅ΡΠ° Π½Π°Π·ΡΠ²Π°Π»ΠΈ Β«ΡΠ°Ρ-ΠΌΠ°ΡΠΉΠ½ΠΎΠΉΒ». ΠΠ° ΡΡΠΎΠΌ ΡΡΡΡΠΎΠΉΡΡΠ²Π΅ ΠΏΡΡΠ΅ΠΌ ΡΠ°Π·Π»ΠΈΡΠ½ΠΎΠΉ ΡΡΡΠ°Π½ΠΎΠ²ΠΊΠΈ Π²Π°Π»ΡΡΠ΅Π² ΠΌΠΎΠΆΠ½ΠΎ ΡΠ²Π΅ΡΡΡΠ²Π°ΡΡ ΠΊΠΎΠ»ΡΡΠ° ΡΠ°Π·Π»ΠΈΡΠ½ΡΡ Π΄ΠΈΠ°ΠΌΠ΅ΡΡΠΎΠ², Π² ΡΠΎΠΌ ΡΠΈΡΠ»Π΅ ΠΈΠ· Π·Π°Π³ΠΎΡΠΎΠ²ΡΠΊ Π΄ΠΎΡΡΠ°ΡΠΎΡΠ½ΠΎ Π±ΠΎΠ»ΡΡΠΎΠΉ ΡΠΎΠ»ΡΠΈΠ½Ρ; Π΄Π»Ρ ΡΡΠΎΠΉ ΡΠ΅Π»ΠΈ ΡΡΡΡΠΎΠΉΡΡΠ²Π° ΠΎΠ±ΠΎΡΡΠ΄ΠΎΠ²Π°Π½Ρ Π½Π΅ΡΠΊΠΎΠ»ΡΠΊΠΈΠΌΠΈ ΠΏΠ΅ΡΠ΅Π΄Π°ΡΠ°ΠΌΠΈ. ΠΠ΄Π½Π°ΠΊΠΎ, Π΅ΡΠ»ΠΈ Π² ΠΌΠ°ΡΡΠ΅ΡΡΠΊΠΎΠΉ Π½Π΅Ρ ΡΠ°ΠΊΠΎΠ³ΠΎ ΡΡΡΡΠΎΠΉΡΡΠ²Π°, ΡΠΎ ΠΊΠΎΠ»ΡΡΠ° ΡΠ²Π΅ΡΡΡΠ²Π°ΡΡ ΠΏΠΎ ΠΏΡΠ΅Π΄Π²Π°ΡΠΈΡΠ΅Π»ΡΠ½ΠΎ ΠΈΠ·Π³ΠΎΡΠΎΠ²Π»Π΅Π½Π½ΠΎΠΌΡ ΡΠ°Π±Π»ΠΎΠ½Ρ ΠΈΠ»ΠΈ ΠΏΡΠΎΡΡΠΎ ΡΡΡΠ½ΠΎΠΉ ΠΊΠΎΠ²ΠΊΠΎΠΉ. ΠΡΠ»ΠΈ Π·Π°Π³ΠΎΡΠΎΠ²ΠΊΠ° Π½Π΅ ΠΎΡΠ΅Π½Ρ Π±ΠΎΠ»ΡΡΠΎΠΉ ΡΠΎΠ»ΡΠΈΠ½Ρ, ΡΠΎ ΡΡΡ ΠΎΠΏΠ΅ΡΠ°ΡΠΈΡ Π²ΡΠΏΠΎΠ»Π½ΡΡΡ Π² Ρ ΠΎΠ»ΠΎΠ΄Π½ΠΎΠΌ ΡΠΎΡΡΠΎΡΠ½ΠΈΠΈ Ρ ΠΏΠΎΠΌΠΎΡΡΡ ΠΊΡΠ·Π½Π΅ΡΠ½ΡΡ ΡΠΈΡΠΊΠΎΠ².
ΠΠ°Π³ΠΎΡΠΎΠ²ΠΊΡ Π·Π°ΠΆΠΈΠΌΠ°ΡΡ ΠΏΠ΅ΡΠΏΠ΅Π½Π΄ΠΈΠΊΡΠ»ΡΡΠ½ΠΎ Π³ΡΠ±ΠΊΠ°ΠΌ ΡΠΈΡΠΊΠΎΠ², Π²Π½ΡΡΡΠ΅Π½Π½Π΅ΠΉ ΡΡΠΎΡΠΎΠ½ΠΎΠΉ Π±ΡΠ΄ΡΡΠ΅Π³ΠΎ ΠΊΠΎΠ»ΡΡΠ° Π½Π°ΡΡΠΆΡ, ΠΈ ΡΡΡΠ½ΠΈΠΊΠΎΠΌ ΠΏΠΎΡΠ»Π΅Π΄ΠΎΠ²Π°ΡΠ΅Π»ΡΠ½ΠΎ ΡΡΠ°ΡΡΠΎΠΊ Π·Π° ΡΡΠ°ΡΡΠΊΠΎΠΌ ΡΠ³ΠΈΠ±Π°ΡΡ Π·Π°Π³ΠΎΡΠΎΠ²ΠΊΡ Π² ΠΊΠΎΠ»ΡΡΠΎ. ΠΠΎ ΠΏΡΠ΅ΠΆΠ΄Π΅ ΡΡΠ΅Π±ΡΠ΅ΠΌΡΠΉ ΠΊΠΎΠ½ΡΡΡ ΠΊΠΎΠ»ΡΡΠ° Π²ΡΡΠ΅ΡΡΠΈΠ²Π°ΡΡ Π½Π° Π±ΡΠΌΠ°Π³Π΅ ΠΈ, ΠΏΠΎΡΡΠΎΡΠ½Π½ΠΎ ΠΏΡΠΈΠΊΠ»Π°Π΄ΡΠ²Π°Ρ ΡΠ΅ΡΡΠ΅ΠΆ ΠΊ ΡΠΎΠ³Π½ΡΡΠΎΠΉ ΡΠ°ΡΡΠΈ Π·Π°Π³ΠΎΡΠΎΠ²ΠΊΠΈ, ΠΏΡΠΎΠ²Π΅ΡΡΡΡ ΡΠΎΠΎΡΠ²Π΅ΡΡΡΠ²ΠΈΠ΅ ΡΠ°Π΄ΠΈΡΡΠ° Π³ΠΈΠ±ΠΊΠΈ ΠΊΠΎΠ»ΡΡΠ° Π·Π°Π΄Π°Π½Π½ΠΎΠΌΡ. ΠΡΠΎΡ ΠΏΡΠΎΡΠ΅ΡΡ ΠΏΡΠΎΠ΄ΠΎΠ»ΠΆΠ°Π΅ΡΡΡ Π΄ΠΎ ΠΏΠΎΠ»ΡΡΠ΅Π½ΠΈΡ Π²ΡΠ΅Π³ΠΎ ΠΊΠΎΠ»ΡΡΠ°, ΠΊΠΎΠ½ΡΡ ΠΊΠΎΡΠΎΡΠΎΠ³ΠΎ ΡΠ²Π°ΡΠΈΠ²Π°ΡΡ, ΠΏΠΎΡΠ»Π΅ ΡΠ΅Π³ΠΎ ΠΎΠΊΠΎΠ½ΡΠ°ΡΠ΅Π»ΡΠ½ΠΎ Π²ΡΠΏΡΠ°Π²Π»ΡΡΡ ΠΊΠΎΠ½ΡΡΡ ΠΊΡΡΠ³Π°. ΠΠ½Π°Π»ΠΎΠ³ΠΈΡΠ½ΡΠΌ ΡΠΏΠΎΡΠΎΠ±ΠΎΠΌ ΠΏΠΎΠ»ΡΡΠ°ΡΡ ΠΈ Π΄ΡΡΠ³ΠΈΠ΅ ΡΠΎΡΠΌΡ ΠΊΠΎΠ½ΡΡΡΠ° ΠΊΠΎΠ»Π΅Ρ β ΠΎΠ²Π°Π»Ρ, Π²ΠΎΡΡΠΌΠ΅ΡΠΊΠΈ ΠΈ ΠΈΠΌ ΠΏΠΎΠ΄ΠΎΠ±Π½ΡΠ΅. Π Π΅Π·ΡΠ»ΡΡΠ°ΡΡ ΡΡΠΎΠΉ ΡΠ°Π±ΠΎΡΡ Π·Π°Π²ΠΈΡΡΡ Π½Π΅ ΡΡΠΎΠ»ΡΠΊΠΎ ΠΎΡ ΠΌΠ°ΡΡΠ΅ΡΡΡΠ²Π° ΠΊΡΠ·Π½Π΅ΡΠ°, ΡΠΊΠΎΠ»ΡΠΊΠΎ ΠΎΡ Π°ΠΊΠΊΡΡΠ°ΡΠ½ΠΎΡΡΠΈ Π΅Π΅ Π²ΡΠΏΠΎΠ»Π½Π΅Π½ΠΈΡ.
ΠΠ΅ΡΠ΅ΡΠ΅ΡΠ΅Π½ΠΈΠ΅ Π²Π½Π°Ρ Π»Π΅ΡΡ
ΠΡΠΈ ΠΎΠΊΠΎΠ²ΡΠ²Π°Π½ΠΈΠΈ ΡΡΠΆΠ΅Π»ΡΡ Π΄ΡΠ±ΠΎΠ²ΡΡ Π΄Π²Π΅ΡΠ΅ΠΉ ΠΏΠ΅ΡΠ΅ΡΠ΅ΠΊΠ°ΡΡΠΈΠ΅ΡΡ Π²Π½Π°Ρ Π»Π΅ΡΡ ΠΊΠΎΠ²Π°Π½ΡΠ΅ ΠΏΠΎΡΡΠ° Π΄ΠΎΠ»ΠΆΠ½Ρ Π±ΡΡΡ ΡΠ»ΠΎΠΆΠ΅Π½Ρ ΡΠ°ΠΊΠΈΠΌ ΠΎΠ±ΡΠ°Π·ΠΎΠΌ, ΡΡΠΎΠ±Ρ ΠΎΠ±Π° ΠΏΠ»ΠΎΡΠ½ΠΎ ΠΏΡΠΈΠ»Π΅Π³Π°Π»ΠΈ ΠΊ ΠΏΠΎΠ²Π΅ΡΡ Π½ΠΎΡΡΠΈ Π΄Π²Π΅ΡΠΈ, Ρ. Π΅. Π»Π΅ΠΆΠ°Π»ΠΈ Π² ΠΏΠ»ΠΎΡΠΊΠΎΡΡΠΈ Π΄Π²Π΅ΡΠΈ. ΠΠ»Ρ ΡΡΠΎΠΉ ΡΠ΅Π»ΠΈ Π½Π΅ΠΎΠ±Ρ ΠΎΠ΄ΠΈΠΌΠΎ ΠΈΠ·Π³ΠΎΡΠΎΠ²ΠΈΡΡ ΠΏΠΎΠ΄ΠΊΠ»Π°Π΄Π½ΠΎΠΉ ΡΡΠ°ΠΌΠΏ, ΡΠΎΡΠ½ΠΎ Π²ΠΎΡΠΏΡΠΎΠΈΠ·Π²ΠΎΠ΄ΡΡΠΈΠΉ ΠΊΠΎΠ½ΡΡΡ ΠΎΠ³ΠΈΠ±Π°Π½ΠΈΡ ΠΏΠΎΡΡΠ°. ΠΠ°Π³ΠΎΡΠΎΠ²ΠΊΡ Π½Π°Π³ΡΠ΅Π²Π°ΡΡ ΠΈ ΡΠΊΠ»Π°Π΄ΡΠ²Π°ΡΡ Π³ΠΎΡΠΈΠ·ΠΎΠ½ΡΠ°Π»ΡΠ½ΠΎ Π½Π° ΠΏΠΎΠ²Π΅ΡΡ Π½ΠΎΡΡΡ ΡΡΠ°ΠΌΠΏΠ°. Π ΡΡΠ½ΠΈΠΊΠΎΠΌ, ΠΏΠΎ ΠΊΠΎΡΠΎΡΠΎΠΌΡ ΡΠ΄Π°ΡΡΡΡ ΠΊΡΠ²Π°Π»Π΄ΠΎΠΉ, ΠΎΡΠΎΡΠΌΠ»ΡΡΡ Π½Π΅ΠΎΠ±Ρ ΠΎΠ΄ΠΈΠΌΡΠΉ ΠΏΡΠΎΠ³ΠΈΠ±. ΠΡΠΈ ΡΡΠΎΠΌ ΠΏΠΎΠ΄Π½ΠΈΠΌΠ°ΡΡΡΡ ΠΊΠΎΠ½ΡΡ Π΄Π΅ΡΠΎΡΠΌΠΈΡΡΠ΅ΠΌΠΎΠΉ ΠΏΠΎΠ»ΠΎΡΡ, ΠΊΠΎΡΠΎΡΡΠ΅ Π½Π΅ΠΎΠ±Ρ ΠΎΠ΄ΠΈΠΌΠΎ ΠΏΠΎΡΠ»Π΅ ΡΡΠΎΠ³ΠΎ Π²ΡΡΠΎΠ²Π½ΡΡΡ. ΠΠ΅ΡΠ΅ΡΠ΅ΡΠ΅Π½ΠΈΡ Π²Π½Π°Ρ Π»Π΅ΡΡ Π²ΡΡΡΠ΅ΡΠ°ΡΡΡΡ ΠΈ Π² ΡΠ΅ΡΠ΅ΡΠΊΠ°Ρ ΠΈΠ· ΠΊΡΡΠ³Π»ΡΡ ΠΏΡΡΡΠΊΠΎΠ². Π ΡΡΠΎΠΌ ΡΠ»ΡΡΠ°Π΅ ΠΈΡΠΏΠΎΠ»ΡΠ·ΡΡΡ ΡΡΠ°ΠΌΠΏ-ΠΎΠΏΡΠ°Π²ΠΊΡ Ρ ΠΏΠΎΠ»ΡΠΊΡΡΠ³Π»ΡΠΌΠΈ Π²ΡΡΠ΅Π·Π°ΠΌΠΈ Π² Π²Π΅ΡΡ Π½Π΅ΠΉ ΠΈ Π½ΠΈΠΆΠ½Π΅ΠΉ ΡΠ°ΡΡΡΡ . ΠΠ°Π³ΡΠ΅Π²Π°ΡΡ ΠΎΠ±Π° ΠΏΠ΅ΡΠ΅ΡΠ΅ΠΊΠ°ΡΡΠΈΡ ΡΡ ΠΏΡΡΡΠΊΠ°, Π½ΠΈΠΆΠ½ΠΈΠΉ ΠΏΡΡΡΠΎΠΊ ΡΠΊΠ»Π°Π΄ΡΠ²Π°ΡΡ ΠΏΠ΅ΡΠΏΠ΅Π½Π΄ΠΈΠΊΡΠ»ΡΡΠ½ΠΎ Π½ΠΈΠΆΠ½Π΅ΠΌΡ Π²ΡΡΠ΅Π·Ρ ΠΎΠΏΡΠ°Π²ΠΊΠΈ, Π° Π²Π΅ΡΡ Π½ΠΈΠΉ β ΠΏΠ΅ΡΠΏΠ΅Π½Π΄ΠΈΠΊΡΠ»ΡΡΠ½ΠΎ Π½ΠΈΠΆΠ½Π΅ΠΌΡ ΠΏΡΡΡΠΊΡ Π½Π°Π΄ Π½ΠΈΠΆΠ½ΠΈΠΌ Π²ΡΡΠ΅Π·ΠΎΠΌ. ΠΠ° Π²Π΅ΡΡ Π½ΠΈΠΉ ΠΏΡΡΡΠΎΠΊ Π½Π°ΠΊΠ»Π°Π΄ΡΠ²Π°ΡΡ Π²Π΅ΡΡ Π½ΡΡ ΠΏΠΎΠ»ΠΎΠ²ΠΈΠ½Ρ ΠΎΠΏΡΠ°Π²ΠΊΠΈ Π²ΡΡΠ΅Π·ΠΎΠΌ ΠΏΠ΅ΡΠΏΠ΅Π½Π΄ΠΈΠΊΡΠ»ΡΡΠ½ΠΎ ΠΏΡΡΡΠΊΡ ΠΈ ΡΠΈΠ»ΡΠ½ΡΠΌΠΈ ΡΠ΄Π°ΡΠ°ΠΌΠΈ ΠΊΡΠ²Π°Π»Π΄Ρ ΠΎΡΠΎΡΠΌΠ»ΡΡΡ ΠΏΠ΅ΡΠ΅ΡΠ΅ΡΠ΅Π½ΠΈΡ Π²Π½Π°Ρ Π»Π΅ΡΡ.
Π Π°ΡΡΠ΅ΠΊΠ°Π½ΠΈΠ΅
ΠΠ΄Π½ΠΎΠΉ ΠΈΠ· Π½Π°ΠΈΠ±ΠΎΠ»Π΅Π΅ ΡΠ°ΡΡΠΎ ΠΈΡΠΏΠΎΠ»ΡΠ·ΡΠ΅ΠΌΡΡ Π² Ρ ΡΠ΄ΠΎΠΆΠ΅ΡΡΠ²Π΅Π½Π½ΠΎΠΉ ΠΊΠΎΠ²ΠΊΠ΅ ΠΎΠΏΠ΅ΡΠ°ΡΠΈΠΉ ΠΊΠ°ΠΊ Π² ΠΏΡΠΎΡΠ»ΠΎΠΌ, ΡΠ°ΠΊ ΠΈ Π² Π½Π°ΡΡΠΎΡΡΠ΅Π΅ Π²ΡΠ΅ΠΌΡ ΡΠ²Π»ΡΠ΅ΡΡΡ ΡΠ°ΡΡΠ΅ΠΊΠ°Π½ΠΈΠ΅ ΠΌΠ°ΡΠ΅ΡΠΈΠ°Π»Π°. Π ΡΡΠΊΠΈΠ·Π°Ρ ΡΠΎΠ²ΡΠ΅ΠΌΠ΅Π½Π½ΡΡ ΠΈΠ·Π΄Π΅Π»ΠΈΠΉ Ρ ΡΠ΄ΠΎΠΆΠ΅ΡΡΠ²Π΅Π½Π½ΠΎΠΉ ΠΊΠΎΠ²ΠΊΠΈ ΡΠ°ΡΡΠΎ Π²ΡΡΡΠ΅ΡΠ°ΡΡΡΡ ΡΠ»Π΅ΠΌΠ΅Π½ΡΡ, ΠΏΡΠ΅Π΄ΡΡΠ°Π²Π»ΡΡΡΠΈΠ΅ ΡΠΎΠ±ΠΎΠΉ ΡΠ·ΠΎΡΡ, Π²ΡΡ ΠΎΠ΄ΡΡΠΈΠ΅ ΠΈΠ· ΠΎΠ΄Π½ΠΎΠ³ΠΎ ΠΊΡΡΠΊΠ° ΠΌΠ°ΡΠ΅ΡΠΈΠ°Π»Π°. Π’ΠΎΠ»ΡΠΈΠ½Ρ Π·Π°Π³ΠΎΡΠΎΠ²ΠΊΠΈ Π²ΡΠ±ΠΈΡΠ°ΡΡ Π² ΡΡΠΎΠΌ ΡΠ»ΡΡΠ°Π΅ Π² Π·Π°Π²ΠΈΡΠΈΠΌΠΎΡΡΠΈ ΠΎΡ ΡΡΠ΅Π±ΡΠ΅ΠΌΠΎΠ³ΠΎ ΠΊΠΎΠ»ΠΈΡΠ΅ΡΡΠ²Π° ΠΌΠ°ΡΠ΅ΡΠΈΠ°Π»Π°, Π·Π°ΡΠ΅ΠΌ ΠΏΡΠΈΠ±Π»ΠΈΠ·ΠΈΡΠ΅Π»ΡΠ½ΠΎ Π½Π°ΠΌΠ΅ΡΠ°ΡΡ ΡΠΎΡΠΌΡ ΠΈ Π΄Π»ΠΈΠ½Ρ ΡΠ°ΡΡΠ΅ΡΠ΅Π½ΠΈΡ. ΠΠΎΡΠΎΠΌ ΠΏΠΎΡΡΡΠΏΠ°ΡΡ ΠΏΡΠΈΠ±Π»ΠΈΠ·ΠΈΡΠ΅Π»ΡΠ½ΠΎ ΡΠ°ΠΊ ΠΆΠ΅, ΠΊΠ°ΠΊ ΠΏΡΠΈ ΡΡΠ±ΠΊΠ΅, Ρ ΡΠΎΠΉ Π»ΠΈΡΡ ΡΠ°Π·Π½ΠΈΡΠ΅ΠΉ, ΡΡΠΎ ΡΠ°ΡΡΠ΅ΠΊΠ°ΡΡ Ρ ΠΎΠ΄Π½ΠΎΠΉ, Π° Π½Π΅ Ρ Π΄Π²ΡΡ ΡΡΠΎΡΠΎΠ½. ΠΠ»Ρ ΡΡΠΎΠ³ΠΎ ΠΏΠΎΠ΄ ΡΠ°ΡΡΠ΅ΠΊΠ°Π΅ΠΌΡΡ Π·Π°Π³ΠΎΡΠΎΠ²ΠΊΡ ΠΏΠΎΠ΄ΠΊΠ»Π°Π΄ΡΠ²Π°ΡΡ Π»ΠΈΡΡ Π±ΠΎΠ»ΡΡΠΎΠΉ ΡΠΎΠ»ΡΠΈΠ½Ρ, Π·Π°ΡΠΈΡΠ°ΡΡΠΈΠΉ ΠΏΠΎΠ²Π΅ΡΡ Π½ΠΎΡΡΡ Π½Π°ΠΊΠΎΠ²Π°Π»ΡΠ½ΠΈ ΠΈ ΠΎΡΡΡΡΠ΅ Π·ΡΠ±ΠΈΠ»Π° ΠΎΡ ΠΏΠΎΠ²ΡΠ΅ΠΆΠ΄Π΅Π½ΠΈΡ. ΠΠ°Π³ΡΠ΅ΡΡΡ Π·Π°Π³ΠΎΡΠΎΠ²ΠΊΡ ΠΊΡΠ·Π½Π΅Ρ ΡΠΊΠ»Π°Π΄ΡΠ²Π°Π΅Ρ Π½Π° Π½Π°ΠΊΠΎΠ²Π°Π»ΡΠ½Ρ, ΡΡΡΠ°Π½Π°Π²Π»ΠΈΠ²Π°Π΅Ρ Π² ΠΎΠ±ΠΎΠ·Π½Π°ΡΠ΅Π½Π½ΠΎΠΌ ΠΌΠ΅ΡΡΠ΅ Π·ΡΠ±ΠΈΠ»ΠΎ, Π° ΠΏΠΎΠ΄ΡΡΡΠ½ΡΠΉ ΡΠ΄Π°ΡΡΠ΅Ρ ΠΊΡΠ²Π°Π»Π΄ΠΎΠΉ Π΄Π»Ρ ΡΠ°ΡΡΠ΅ΠΊΠ°Π½ΠΈΡ (ΡΠΈΡ. 76).
Π ΠΈΡ. 76. Π Π°ΡΡΠ΅ΡΠ΅Π½ΠΈΠ΅ | Π ΠΈΡ. 77. ΠΡΠ³ΠΈΠ±Π°Π½ΠΈΠ΅ ΡΠ°ΡΡΠ΅ΡΠ΅Π½Π½ΠΎΠΉ Π·Π°Π³ΠΎΡΠΎΠ²ΠΊΠΈ | Π ΠΈΡ. 78. ΠΡΠΎΡΠΌΠ»Π΅Π½ΠΈΠ΅ ΡΠ°ΡΡΠ΅ΡΠ΅Π½Π½ΠΎΠ³ΠΎ ΠΊΠΎΠ½ΡΠ° | Π ΠΈΡ. 79. ΠΡΠΎΡΠΌΠ»Π΅Π½ΠΈΠ΅ ΡΠ°ΡΡΠ΅ΡΠ΅Π½Π½ΡΡ ΠΊΠΎΠ½ΡΠΎΠ² Π·Π°Π³ΠΎΡΠΎΠ²ΠΊΠΈ |
Π Π°ΡΡΠ΅ΡΠ΅Π½Π½ΡΠ΅ Π²Π΅ΡΠ²ΠΈ Π·Π°Π³ΠΎΡΠΎΠ²ΠΊΠΈ ΠΎΡΠ³ΠΈΠ±Π°ΡΡ ΠΎΠ΄Π½Ρ ΠΎΡ Π΄ΡΡΠ³ΠΎΠΉ ΡΠ°ΠΊ, ΡΡΠΎΠ±Ρ ΠΊΠ°ΠΆΠ΄ΡΡ ΠΈΠ· Π½ΠΈΡ ΠΌΠΎΠΆΠ½ΠΎ Π±ΡΠ»ΠΎ ΠΊΠΎΠ²Π°ΡΡ Π² ΠΎΡΠ΄Π΅Π»ΡΠ½ΠΎΡΡΠΈ (ΡΠΈΡ. 77). ΠΠ°Π»Π΅Π΅ ΠΎΡΠΎΡΠΌΠ»ΡΡΡ ΠΈΠ·Π΄Π΅Π»ΠΈΠ΅ ΡΠΎΠ³Π»Π°ΡΠ½ΠΎ ΡΡΠΊΠΈΠ·Ρ (ΡΠΈΡ. 78, 79) ΠΈ Π²ΡΡΠ°Π²Π½ΠΈΠ²Π°ΡΡ Π΅Π³ΠΎ Π²Π΅ΡΠ²ΠΈ Π² ΠΎΡΠ½ΠΎΠ²Π½ΠΎΠΉ ΠΈΠ»ΠΈ Π»ΡΠ±ΡΡ Π·Π°Π΄Π°Π½Π½ΡΡ ΠΏΠ»ΠΎΡΠΊΠΎΡΡΡΡ . ΠΠ½ΠΎΠ³Π΄Π° ΠΏΠΎ ΡΡΠΊΠΈΠ·Ρ ΡΡΠ΅Π±ΡΠ΅ΡΡΡ ΡΠΊΡΡΠ³-Π»Π΅Π½ΠΈΠ΅ ΡΠ°ΡΡΠ΅ΡΠ΅Π½Π½ΡΡ Π²Π΅ΡΠ²Π΅ΠΉ. Π ΡΡΠΎΠΌ ΡΠ»ΡΡΠ°Π΅ Π·Π°Π³ΠΎΡΠΎΠ²ΠΊΡ ΡΠ°ΡΡΠ΅ΠΊΠ°ΡΡ Π΄ΠΎ Π½Π°ΡΠ°Π»Π° ΡΠ°Π΄ΠΈΡΡΠ° Π·Π°ΠΊΡΡΠ³Π»Π΅Π½ΠΈΡ, ΡΠ°ΡΡΠ΅ΡΠ΅Π½Π½ΡΠ΅ Π²Π΅ΡΠ²ΠΈ ΡΠ°Π·Π²ΠΎΠ΄ΡΡ, ΡΠΊΠ»Π°Π΄ΡΠ²Π°ΡΡ Π½Π° ΠΊΡΡΠ³Π»ΡΡ ΠΏΠΎΠ²Π΅ΡΡ Π½ΠΎΡΡΡ ΡΠΎΠ³Π° Π½Π°ΠΊΠΎΠ²Π°Π»ΡΠ½ΠΈ ΠΈ ΡΠΈΠ»ΡΠ½ΡΠΌΠΈ ΡΠ΄Π°ΡΠ°ΠΌΠΈ ΠΊΡΠ²Π°Π»Π΄Ρ ΠΏΡΠΎΠ΄ΠΎΠ»ΠΆΠ°ΡΡ ΠΎΡΠ³ΠΈΠ±Π°ΡΡ Π²Π΅ΡΠ²Ρ, Π° ΡΠ΄Π°ΡΠ°ΠΌΠΈ ΠΏΠΎ ΠΊΠΎΠ½ΡΡ Π²Π΅ΡΠ²ΠΈ ΡΡΠ°ΡΠ°ΡΡΡΡ ΠΏΠΎΠ»ΡΡΠΈΡΡ Π·Π°Π΄Π°Π½Π½ΡΠΉ ΡΠ°Π·ΠΌΠ΅Ρ Π·Π°ΠΊΡΡΠ³Π»Π΅Π½ΠΈΡ.
Π ΠΈΡ. 80. ΠΡΠΎΡΠ΅ΡΠ΅Π½Π½ΡΠΉ ΠΏΡΡΡΠΎΠΊ Ρ ΠΎΡΠ²Π΅ΡΠ²Π»Π΅Π½Π½ΡΠΌΠΈ Π²ΠΎΠ»ΡΡΠ°ΠΌΠΈ | Π ΠΈΡ. 81. ΠΡΠΎΡΠ΅ΡΠ΅Π½Π½ΡΠΉ ΠΏΡΡΡΠΎΠΊ Ρ ΠΎΡΠ²Π΅ΡΠ²Π»Π΅Π½Π½ΡΠΌΠΈ Π²ΠΎΠ»ΡΡΠ°ΠΌΠΈ | Π ΠΈΡ. 82. Π Π°Π·Π²Π΅ΡΠ²Π»Π΅Π½Π½ΡΠΉ ΠΎΡΠ½Π°ΠΌΠ΅Π½Ρ |
ΠΠ½ΠΎΠ³Π΄Π° Π½Π΅ΠΎΠ±Ρ ΠΎΠ΄ΠΈΠΌΠΎ ΠΎΡ ΡΡΠ΅ΡΠΆΠ½Ρ ΠΊΠ²Π°Π΄ΡΠ°ΡΠ½ΠΎΠ³ΠΎ ΡΠ΅ΡΠ΅Π½ΠΈΡ ΠΈΠ»ΠΈ ΠΎΡ ΠΏΠΎΠ»ΠΎΡΡ ΠΎΡΡΠ΅ΡΡ Π²Π΅ΡΠ²Ρ Π·Π½Π°ΡΠΈΡΠ΅Π»ΡΠ½ΠΎ ΠΌΠ΅Π½ΡΡΠ΅ΠΉ ΡΠΎΠ»ΡΠΈΠ½Ρ, ΡΠ΅ΠΌ ΠΎΡΡΠ°ΡΡΠ°ΡΡΡ ΡΠ°ΡΡΡ ΡΡΠ΅ΡΠΆΠ½Ρ. ΠΡΠΎ ΠΎΡΡΠ΅ΠΊΠ°Π½ΠΈΠ΅ ΠΏΡΠΎΠΈΠ·Π²ΠΎΠ΄ΡΡ, ΠΊΠ°ΠΊ ΠΏΡΠ°Π²ΠΈΠ»ΠΎ, Π²Π΅ΡΡΠΈΠΊΠ°Π»ΡΠ½ΠΎ Π² ΡΠΈΡΠΊΠ°Ρ . ΠΠ°Π³ΡΠ΅ΡΡΡ Π·Π°Π³ΠΎΡΠΎΠ²ΠΊΡ Π·Π°ΠΆΠΈΠΌΠ°ΡΡ Π² ΡΠΈΡΠΊΠ°Ρ ΠΈ Π·ΡΠ±ΠΈΠ»ΠΎΠΌ ΠΏΠΎΠ΄ ΡΠΎΠΎΡΠ²Π΅ΡΡΡΠ²ΡΡΡΠΈΠΌ ΡΠ³Π»ΠΎΠΌ ΠΎΡΡΠ΅ΠΊΠ°ΡΡ Π½ΡΠΆΠ½ΡΡ Π²Π΅ΡΠ²Ρ (ΡΠΈΡ. 80β82). Π ΡΡΠΎΠΌ ΡΠ»ΡΡΠ°Π΅ Π·Π°Π³ΠΎΡΠΎΠ²ΠΊΡ ΠΊΠ°ΠΊ Π±Ρ ΠΎΠ±ΡΠ΅ΡΡΠ²Π°ΡΡ. ΠΡΠ° ΠΎΠΏΠ΅ΡΠ°ΡΠΈΡ ΡΡΠ΅Π±ΡΠ΅Ρ Π·Π½Π°ΡΠΈΡΠ΅Π»ΡΠ½ΠΎΠ³ΠΎ ΠΎΠΏΡΡΠ° Π΄Π»Ρ ΡΠΎΠ³ΠΎ, ΡΡΠΎΠ±Ρ ΡΠ°ΡΡΠ΅ΠΊΠ°Π½ΠΈΠ΅ Π±ΡΠ»ΠΎ ΡΠΎΠ²Π½ΡΠΌ ΠΈ ΠΎΡΡΠ΅ΠΊΠ°Π΅ΠΌΠ°Ρ Π²Π΅ΡΠ²Ρ Π±ΡΠ»Π° Π±Ρ ΠΎΠ΄Π½ΠΎΠΉ ΠΈ ΡΠΎΠΉ ΠΆΠ΅ ΡΠΎΠ»ΡΠΈΠ½Ρ.
Π‘ΠΊΠΎΠ±Ρ
Π ΠΈΡ. 83. Π‘ΠΊΠΎΠ±Π° |
ΠΠ΄Π½ΠΈΠΌ ΠΈΠ· ΠΎΡΠΎΠ±Π΅Π½Π½ΠΎ ΠΊΡΠ°ΡΠΈΠ²ΡΡ ΡΠ»Π΅ΠΌΠ΅Π½ΡΠΎΠ² ΠΊΠΎΠ²Π°Π½ΡΡ ΠΊΠΎΠ½ΡΡΡΡΠΊΡΠΈΠΉ ΡΠ²Π»ΡΡΡΡΡ ΡΠΊΠΎΠ±Ρ (ΡΠΈΡ. 83), ΠΊΠΎΡΠΎΡΡΠΌΠΈ ΡΠΎΠ΅Π΄ΠΈΠ½ΡΡΡ Π΄Π²Π΅ ΡΠ°ΠΌΠΎΡΡΠΎΡΡΠ΅Π»ΡΠ½ΡΠ΅ Π΄Π΅ΡΠ°Π»ΠΈ Π±Π΅Π· ΠΈΡΠΏΠΎΠ»ΡΠ·ΠΎΠ²Π°Π½ΠΈΡ, Π½Π°ΠΏΡΠΈΠΌΠ΅Ρ, ΠΊΠ»Π΅ΠΏΠΊΠΈ, ΡΠ²Π°ΡΠΊΠΈ ΠΈ ΠΏΡ. Π₯ΠΎΡΡ ΡΡΠΎΡ ΡΠΏΠΎΡΠΎΠ± ΡΠΎΠ΅Π΄ΠΈΠ½Π΅Π½ΠΈΡ ΠΈΡΠΏΠΎΠ»ΡΠ·ΡΡΡ ΡΠ΅Π΄ΠΊΠΎ, ΠΎΠ΄Π½Π°ΠΊΠΎ Π² ΡΠΎΠ²ΡΠ΅ΠΌΠ΅Π½Π½ΠΎΠΌ ΠΊΡΠ·Π½Π΅ΡΠ½ΠΎΠΌ Π΄Π΅Π»Π΅ ΠΎΠ½ ΠΏΠ΅ΡΡΠΏΠ΅ΠΊΡΠΈΠ²Π΅Π½. ΠΡΠ΅Π½Ρ ΡΠ΄ΠΎΠ±Π½ΠΎ ΠΈΡΠΏΠΎΠ»ΡΠ·ΠΎΠ²Π°ΡΡ ΡΠΊΠΎΠ±Ρ Π΄Π»Ρ ΠΊΡΠ΅ΠΏΠ»Π΅Π½ΠΈΡ ΡΠ°Π·Π½ΡΡ ΠΏΠΎΡΡΡΠ½Π΅ΠΉ, Π½Π΅ΡΠΊΠΎΠ»ΡΠΊΠΈΡ ΠΏΡΡΡΠΊΠΎΠ² ΠΊ Π±ΠΎΠ»Π΅Π΅ ΠΊΡΡΠΏΠ½ΠΎΠΉ ΠΏΠ»ΠΎΡΠΊΠΎΠΉ Π΄Π΅ΡΠ°Π»ΠΈ ΠΈ Ρ. Π΄.
ΠΠ΅ΡΠ°Π»Ρ, ΠΊΠΎΡΠΎΡΡΡ Π½ΡΠΆΠ½ΠΎ Π²ΡΡΠ°Π²ΠΈΡΡ Π² ΡΠΊΠΎΠ±Ρ, ΠΈΠ·ΠΌΠ΅ΡΡΡΡ, ΠΎΠΏΡΠ΅Π΄Π΅Π»ΡΡ ΡΡΠΌΠΌΠ°ΡΠ½ΡΡ Π΄Π»ΠΈΠ½Ρ ΡΡΠ΅Ρ Π³ΡΠ°Π½Π΅ΠΉ Π΅Π΅ ΡΠ΅ΡΠ΅Π½ΠΈΡ (Π΄Π»Ρ ΠΏΡΡΠΌΠΎΡΠ³ΠΎΠ»ΡΠ½ΠΎΠ³ΠΎ ΡΠ΅ΡΠ΅Π½ΠΈΡ β Π΄Π»ΠΈΠ½Ρ Π΄Π²ΡΡ ΠΊΠΎΡΠΎΡΠΊΠΈΡ ΠΈ ΠΎΠ΄Π½ΠΎΠΉ Π΄Π»ΠΈΠ½Π½ΠΎΠΉ ΡΡΠΎΡΠΎΠ½). ΠΡΠ° Π΄Π»ΠΈΠ½Π°, ΡΠ²Π΅Π»ΠΈΡΠ΅Π½Π½Π°Ρ Π½Π° 1/4, ΠΈ Π΅ΡΡΡ Π΄Π»ΠΈΠ½Π° ΠΏΡΠΎΡΠ΅ΡΠΊΠΈ. ΠΠ°ΡΠ΅ΠΌ Π·Π°Π³ΠΎΡΠΎΠ²ΠΊΡ Π½Π°Π³ΡΠ΅Π²Π°ΡΡ ΠΈ Π² Π½ΡΠΆΠ½ΠΎΠΌ ΠΌΠ΅ΡΡΠ΅ Π΄Π΅Π»Π°ΡΡ Π΄Π²Π΅ ΠΏΠ°ΡΠ°Π»Π»Π΅Π»ΡΠ½ΡΠ΅ ΠΏΡΠΎΡΠ΅ΡΠΊΠΈ Π½Π° ΡΠ°ΡΡΡΠΎΡΠ½ΠΈΠΈ, ΡΠΎΠΎΡΠ²Π΅ΡΡΡΠ²ΡΡΡΠ΅ΠΌ ΡΠΎΠ»ΡΠΈΠ½Π΅ ΠΎΠ±ΡΠ°Π±Π°ΡΡΠ²Π°Π΅ΠΌΠΎΠΉ Π·Π°Π³ΠΎΡΠΎΠ²ΠΊΠΈ. ΠΡΠΎΡΠ΅ΡΠΊΡ Π΄Π΅Π»Π°ΡΡ Ρ ΠΎΠ΄Π½ΠΎΠΉ ΡΡΠΎΡΠΎΠ½Ρ, ΠΈΡΠΏΠΎΠ»ΡΠ·ΡΡ, ΠΊΠ°ΠΊ ΠΈ ΡΠ°Π½Π΅Π΅, ΠΏΠ»ΠΎΡΠΊΡΡ ΠΏΠΎΠ΄ΠΊΠ»Π°Π΄ΠΊΡ ΠΏΠΎΠ΄ Π·Π°Π³ΠΎΡΠΎΠ²ΠΊΡ. ΠΠΎΡΠ»Π΅ ΡΡΠΎΠ³ΠΎ Π·Π°Π³ΠΎΡΠΎΠ²ΠΊΡ ΠΏΠΎΠ²ΠΎΡΠ°ΡΠΈΠ²Π°ΡΡ ΠΈ Π²ΡΡΠ΅ΡΠ΅Π½Π½ΡΡ Π²Π½ΡΡΡΠΈ Π·Π°Π³ΠΎΡΠΎΠ²ΠΊΠΈ ΠΏΠΎΠ»ΠΎΡΠΊΡ Π²ΡΠ΄Π°Π²Π»ΠΈΠ²Π°ΡΡ ΡΠ°ΡΠΊΠ°ΡΠΊΠΎΠΉ Π½Π° ΡΠΎΡΠΌΠΎΠ²Π°Π»ΡΠ½ΠΎΠΉ ΠΏΠ»ΠΈΡΠ΅ Π΄ΠΎ Π½ΡΠΆΠ½ΠΎΠΉ Π³Π»ΡΠ±ΠΈΠ½Ρ. Π’Π°ΠΊΠΈΠΌ ΠΎΠ±ΡΠ°Π·ΠΎΠΌ, ΠΏΠΎΠ»ΡΡΠ°Π΅ΡΡΡ Π² Π½Π΅ΠΊΠΎΡΠΎΡΠΎΠΌ ΡΠΎΠ΄Π΅ ΠΎΡΠΊΠΎ, ΠΊΠΎΡΠΎΡΠΎΠ΅ ΠΏΡΠ°Π²ΡΡ Π±ΠΎΡΠΎΠ΄ΠΊΠΎΠΌ Π½Π΅ΡΠΊΠΎΠ»ΡΠΊΠΎ ΠΌΠ΅Π½ΡΡΠΈΡ ΡΠ°Π·ΠΌΠ΅ΡΠΎΠ², ΡΠ΅ΠΌ Π²ΡΡΠ°Π²Π»ΡΠ΅ΠΌΠ°Ρ Π΄Π΅ΡΠ°Π»Ρ. ΠΠΎΠ½Π΅Ρ Π²ΡΡΠ°Π²Π»ΡΠ΅ΠΌΠΎΠΉ Π΄Π΅ΡΠ°Π»ΠΈ ΡΠ»Π΅Π³ΠΊΠ° ΠΎΡΡΡΠ³ΠΈΠ²Π°ΡΡ, ΠΏΠΎΡΠ»Π΅ ΡΠ΅Π³ΠΎ ΠΎΡΠΊΠΎ ΡΠΊΠΎΠ±Ρ ΡΠ½ΠΎΠ²Π° Π½Π°Π³ΡΠ΅Π²Π°ΡΡ ΠΈ Π² ΡΠΊΠΎΠ±Ρ Π² Π½Π°Π³ΡΠ΅ΡΠΎΠΌ ΡΠΎΡΡΠΎΡΠ½ΠΈΠΈ Π²ΡΡΠ°Π²Π»ΡΡΡ ΠΏΠΎΠ΄Π³ΠΎΡΠΎΠ²Π»Π΅Π½Π½ΡΠ΅ ΡΡΠ΅ΡΠΆΠ½ΠΈ. Π ΡΠ΅Π·ΡΠ»ΡΡΠ°ΡΠ΅ Π΅ΡΡΠ΅ΡΡΠ²Π΅Π½Π½ΠΎΠ³ΠΎ ΡΠΆΠ°ΡΠΈΡ ΠΌΠ°ΡΠ΅ΡΠΈΠ°Π»Π° ΠΏΡΠΈ ΠΎΡ Π»Π°ΠΆΠ΄Π΅Π½ΠΈΠΈ ΠΏΠΎΠ»ΡΡΠ°Π΅ΡΡΡ ΠΎΡΠ΅Π½Ρ ΠΊΡΠ΅ΠΏΠΊΠΎΠ΅ ΡΠΎΠ΅Π΄ΠΈΠ½Π΅Π½ΠΈΠ΅.
ΠΠ°Π»Π΅Π΅ (ΡΠ°ΡΡΡ 2)
Π ΠΎΠ³Π»Π°Π²Π»Π΅Π½ΠΈΡ
ΠΠΎΠ²Π°Π½Π°Ρ Π·Π°Π³ΠΎΡΠΎΠ²ΠΊΠ°: ΠΡΠ½ΠΎΠ²Ρ ΠΊΠΎΠ²ΠΊΠΈ ΠΌΠ΅ΡΠ°Π»Π»Π°
ΠΠΎΠ²ΠΊΠ° ΠΌΠ΅ΡΠ°Π»Π»Π°, ΠΊΠ°ΠΊ ΠΈΒ Π»ΠΈΡΡΠ΅, ΡΠ²Π»ΡΠ΅ΡΡΡ ΠΎΠ΄Π½ΠΈΠΌ ΠΈΠ·Β Π΄ΡΠ΅Π²Π½Π΅ΠΉΡΠΈΡ ΠΌΠ΅ΡΠΎΠ΄ΠΎΠ² ΠΎΠ±ΡΠ°Π±ΠΎΡΠΊΠΈ ΠΌΠ°ΡΠ΅ΡΠΈΠ°Π»ΠΎΠ². Π‘Β ΠΏΠΎΠΌΠΎΡΡΡ ΡΡΠΎΠ³ΠΎ ΡΠΏΠΎΡΠΎΠ±Π° Π»ΡΠ΄ΠΈ Π½Π°ΡΡΠΈΠ»ΠΈΡΡ ΠΈΠ·Π³ΠΎΡΠ°Π²Π»ΠΈΠ²Π°ΡΡ ΠΌΠ΅ΡΠ°Π»Π» Π΅ΡΠ΅ Π΄ΠΎΒ ΠΎΡΠΊΡΡΡΠΈΡ ΡΡΠ°Π»ΠΈ ΠΈΒ ΠΆΠ΅Π»Π΅Π·Π°. ΠΠ΅ΡΠ²ΡΠ΅ Π²Β ΠΈΡΡΠΎΡΠΈΠΈ ΠΊΡΠ·Π½Π΅ΡΡ Π½Π°ΡΠ°Π»ΠΈ ΡΠ°Π±ΠΎΡΠ°ΡΡ Π΅ΡΠ΅ 6Β ΡΡΡΡΡΠ΅Π»Π΅ΡΠΈΠΉ Π½Π°Π·Π°Π΄. ΠΠΎΡΡΠ΅ΠΏΠ΅Π½Π½ΠΎ ΡΠ΅Ρ Π½ΠΎΠ»ΠΎΠ³ΠΈΡ ΠΌΠΎΠ΄Π΅ΡΠ½ΠΈΠ·ΠΈΡΠΎΠ²Π°Π»Π°ΡΡ ΠΈΒ ΠΎΠ±ΠΎΠ³Π°ΡΠ°Π»Π°ΡΡ Π½ΠΎΠ²Π΅ΠΉΡΠΈΠΌΠΈ ΠΌΠ΅ΡΠΎΠ΄ΠΈΠΊΠ°ΠΌΠΈ. Π‘Π΅ΠΉΡΠ°Ρ Π½ΠΈΒ Π½Π°Β ΠΎΠ΄Π½ΠΎΠΌ ΠΏΡΠΎΠΈΠ·Π²ΠΎΠ΄ΡΡΠ²Π΅ Π½Π΅Β ΠΎΠ±ΠΎΠΉΡΠΈΡΡ Π±Π΅Π· ΠΌΠ΅ΡΠΎΠ΄Π° ΠΎΠ±ΡΠ°Π±ΠΎΡΠΊΠΈ ΠΌΠ΅ΡΠ°Π»Π»Π° ΡΒ ΠΏΠΎΠΌΠΎΡΡΡ ΠΌΠ΅ΡΠΎΠ΄Π° ΠΊΠΎΠ²ΠΊΠΈ.
ΠΠΎΠ²ΠΊΠ° ΠΌΠ΅ΡΠ°Π»Π»Π°: Π§ΡΠΎ ΡΡΠΎ?
ΠΡΠ»ΠΈ Π³ΠΎΠ²ΠΎΡΠΈΡΡ ΠΏΡΠΎΡΡΡΠΌΠΈ ΡΠ»ΠΎΠ²Π°ΠΌΠΈ, ΡΠΎΒ ΠΏΠΎΠ΄ ΠΊΠΎΠ²ΠΊΠΎΠΉ ΠΏΠΎΠ΄ΡΠ°Π·ΡΠΌΠ΅Π²Π°Π΅ΡΡΡ ΠΎΠ±ΡΠ°Π±ΠΎΡΠΊΠ° ΠΌΠ°ΡΠ΅ΡΠΈΠ°Π»Π°, ΠΊΠΎΡΠΎΡΡΠΉ Π½Π°Π³ΡΠ΅Π²Π°Π΅ΡΡΡ Π΄ΠΎΒ Π½Π΅ΠΎΠ±Ρ ΠΎΠ΄ΠΈΠΌΠΎΠΉ ΡΠ΅ΠΌΠΏΠ΅ΡΠ°ΡΡΡΡ. ΠΡΠΈΠ½ΡΠΈΠΏΡ ΠΏΡΠΎΡΠ΅ΡΡΠ° ΠΎΡΠ½ΠΎΠ²Π°Π½Ρ Π½Π°Β ΡΠΈΠ·ΠΈΡΠ΅ΡΠΊΠΈΡ Ρ Π°ΡΠ°ΠΊΡΠ΅ΡΠΈΡΡΠΈΠΊΠ°Ρ ΠΎΠ±ΡΠ°Π±Π°ΡΡΠ²Π°Π΅ΠΌΠΎΠ³ΠΎ ΠΌΠ΅ΡΠ°Π»Π»Π°, ΠΎΠ±Π»Π°Π΄Π°ΡΡΠ΅Π³ΠΎ ΡΠ΅ΠΌΠΏΠ΅ΡΠ°ΡΡΡΠΎΠΉ ΠΏΠ»Π°Π²Π»Π΅Π½ΠΈΡ. ΠΠΎΒ ΡΠΎΠ³ΠΎ, ΠΊΠ°ΠΊ ΠΌΠ°ΡΠ΅ΡΠΈΠ°Π» Π΄ΠΎΡΡΠΈΠ³Π½Π΅Ρ ΡΡΠΎΠ³ΠΎ ΠΏΠΎΡΠΎΠ³Π°, ΠΎΠ½Β ΡΡΠ°Π½Π΅Ρ ΠΌΡΠ³ΠΊΠΈΠΌ, ΡΠΎΒ Π΅ΡΡΡ Π³ΠΎΡΠΎΠ²ΡΠΌ ΠΊΒ ΠΎΠ±ΡΠ°Π±ΠΎΡΠΊΠ΅.
Π£Β Π²ΡΠ΅Ρ ΠΌΠ΅ΡΠ°Π»Π»ΠΎΠ² Π΅ΡΡΡ ΡΠΎΠ±ΡΡΠ²Π΅Π½Π½Π°Ρ ΡΠ΅ΠΌΠΏΠ΅ΡΠ°ΡΡΡΠ°, ΠΏΡΠΈ ΠΊΠΎΡΠΎΡΠΎΠΉ ΠΌΠ°ΡΠ΅ΡΠΈΠ°Π» ΡΡΠ°Π½ΠΎΠ²ΠΈΡΡΡ ΠΌΡΠ³ΠΊΠΈΠΌ. ΠΡΒ ΡΡΠΎΠ³ΠΎ Π·Π°Π²ΠΈΡΠΈΡ ΠΏΠΎΠ΄Π°ΡΠ»ΠΈΠ²ΠΎΡΡΡ ΡΠΎΠ³ΠΎ ΠΈΠ»ΠΈ ΠΈΠ½ΠΎΠ³ΠΎ ΠΌΠ΅ΡΠ°Π»Π»Π° Π΄Π»Ρ ΠΊΠΎΠ²ΠΊΠΈ.
Π‘ΡΡΠ΅ΡΡΠ²ΡΠ΅Ρ ΠΈΒ ΠΌΠ΅ΡΠΎΠ΄ ΠΌΠ΅ΡΠ°Π»Π»ΠΎΠΎΠ±ΡΠ°Π±ΠΎΡΠΊΠΈ, ΠΏΡΠΈ ΠΊΠΎΡΠΎΡΠΎΠΌ ΠΌΠ°ΡΠ΅ΡΠΈΠ°Π» Π½Π΅Β Π½Π°Π³ΡΠ΅Π²Π°Π΅ΡΡΡ. ΠΠ³ΠΎ ΠΊΡΡΡ Ρ ΠΎΠ»ΠΎΠ΄Π½ΡΠΌ. ΠΠ°Π½Π½Π°Ρ ΠΌΠ΅ΡΠΎΠ΄ΠΈΠΊΠ° ΠΏΠΎΠΌΠΎΠ³Π°Π΅Ρ ΠΏΠΎΠ»ΡΡΠΈΡΡ Π΄ΠΎΡΡΠ°ΡΠΎΡΠ½ΠΎ ΠΏΡΠΎΡΠ½ΡΠ΅ ΠΊΠΎΠ²Π°Π½ΡΠ΅ Π·Π°Π³ΠΎΡΠΎΠ²ΠΊΠΈ. ΠΒ ΡΠ°ΠΊΠΎΠΌ ΡΠ»ΡΡΠ°Π΅ Π·Π°Π³ΠΎΡΠΎΠ²ΠΊΠ° ΠΈΠ·Π³ΠΈΠ±Π°Π΅ΡΡΡ ΠΈΒ ΠΏΡΠ΅ΡΡΡΠ΅ΡΡΡ. ΠΠΈΠΆΠ΅ Π²ΡΒ ΠΌΠΎΠΆΠ΅ΡΠ΅ ΠΏΠΎΡΠΌΠΎΡΡΠ΅ΡΡ Π½Π°Β ΠΏΡΠ΅Π΄Π΅Π»Ρ ΡΠ΅ΠΌΠΏΠ΅ΡΠ°ΡΡΡ ΠΊΠΎΠ²ΠΊΠΈ Π΄Π»Ρ ΡΠ°Π·Π»ΠΈΡΠ½ΡΡ ΠΌΠ΅ΡΠ°Π»Π»ΠΎΠ².
Π’ΠΈΠΏΡ ΠΎΠ±ΡΠ°Π±ΠΎΡΠΊΠΈ ΠΌΠ΅ΡΠ°Π»Π»Π°
ΠΠ°Β Π΄Π°Π½Π½ΡΠΉ ΠΌΠΎΠΌΠ΅Π½Ρ Π΅ΡΡΡ ΡΡΠΈ Π½Π°ΠΈΠ±ΠΎΠ»Π΅Π΅ ΡΠ°ΡΠΏΡΠΎΡΡΡΠ°Π½Π΅Π½Π½ΡΡ ΡΠΈΠΏΠ° ΠΊΠΎΠ²ΠΊΠΈ:
- ΠΌΠ°ΡΠΈΠ½Π½Π°Ρ;
- ΡΠ²ΠΎΠ±ΠΎΠ΄Π½Π°Ρ;
- ΡΡΠ°ΠΌΠΏΠΎΠ²ΠΊΠ°.
ΠΠΎΠ΄ ΠΌΠ°ΡΠΈΠ½Π½ΠΎΠΉ ΠΊΠΎΠ²ΠΊΠΎΠΉ ΠΏΠΎΠ΄ΡΠ°Π·ΡΠΌΠ΅Π²Π°Π΅ΡΡΡ ΡΠΎΠ²ΡΠ΅ΠΌΠ΅Π½Π½ΡΠΉ ΠΌΠ΅ΡΠΎΠ΄ ΠΎΠ±ΡΠ°Π±ΠΎΡΠΊΠΈ, ΠΈΡΠΏΠΎΠ»ΡΠ·ΡΡΡΠΈΠΉΡΡ Π²Β ΡΡΠΆΠ΅Π»ΠΎΠΉ ΠΈΒ ΠΌΠ°ΡΡΠΎΠ²ΠΎΠΉ ΠΏΡΠΎΠΌΡΡΠ»Π΅Π½Π½ΠΎΡΡΠΈ. ΠΡΠΈ ΠΈΡΠΏΠΎΠ»ΡΠ·ΠΎΠ²Π°Π½ΠΈΠΈ ΠΌΠ΅ΡΠΎΠ΄Π° ΠΏΡΠΈΠΌΠ΅Π½ΡΡΡΡΡ ΠΌΠ΅Ρ Π°Π½ΠΈΠ·ΠΈΡΠΎΠ²Π°Π½Π½ΡΠ΅ ΠΊΠΎΡΠ»Ρ, ΠΏΡΠ΅ΡΡΡ ΠΈΠ»ΠΈ ΠΊΠΎΠ²ΠΎΡΠ½ΡΠ΅ ΠΌΠ°ΡΠΈΠ½Ρ. ΠΡΠΎΠΌΠ΅ ΡΠΎΠ³ΠΎ, Π²Π΅Ρ ΠΊΠΎΠ½Π΅ΡΠ½ΡΡ ΠΏΠΎΠΊΠΎΠ²ΠΎΠΊ ΠΈΒ ΠΊΠΎΠ²Π°Π½ΡΡ Π·Π°Π³ΠΎΡΠΎΠ²ΠΎΠΊ Π²Β Π½Π΅ΠΊΠΎΡΠΎΡΡΡ ΡΠ»ΡΡΠ°ΡΡ ΠΌΠΎΠΆΠ΅Ρ Π΄ΠΎΡ ΠΎΠ΄ΠΈΡΡ Π΄ΠΎΒ Π΄Π΅ΡΡΡΠΊΠΎΠ² ΡΠΎΠ½Π½.
ΠΡΠ»ΠΈ Π³ΠΎΠ²ΠΎΡΠΈΡΡ ΠΎΒ ΡΠ²ΠΎΠ±ΠΎΠ΄Π½ΠΎΠΉ ΠΊΠΎΠ²ΠΊΠ΅, ΡΠΎΒ Π²Β Π΄Π°Π½Π½ΠΎΠΌ ΡΠ»ΡΡΠ°Π΅ Π·Π°Π³ΠΎΡΠΎΠ²ΠΊΠ΅ Π½Π΅Β ΠΎΠ³ΡΠ°Π½ΠΈΡΠΈΠ²Π°ΡΡΡΡ ΡΠΎΡΠΌΠ°ΠΌΠΈ. ΠΠΎΠ²Π°Π½Π°Ρ Π·Π°Π³ΠΎΡΠΎΠ²ΠΊΠ° Π·Π°ΠΊΡΠ΅ΠΏΠ»ΡΠ΅ΡΡΡ ΠΊΒ Π½Π°ΠΊΠΎΠ²Π°Π»ΡΠ½Π΅ ΡΒ ΠΎΠ΄Π½ΠΎΠΉ ΡΡΠΎΡΠΎΠ½Ρ. Π ΡΡΠ½Π°Ρ ΠΊΠΎΠ²ΠΊΠ° Π²Β ΡΠ°ΠΊΠΎΠΉ ΡΠΈΡΡΠ°ΡΠΈΠΈ ΠΎΡΠ½ΠΎΡΠΈΡΡΡ ΠΊΒ ΡΡΠΎΠΌΡΒ ΠΆΠ΅ ΠΌΠ΅ΡΠΎΠ΄Ρ. ΠΠ·Π΄Π΅Π»ΠΈΡΠΌ ΠΏΡΠΈΠ΄Π°Π΅ΡΡΡ ΡΠΎΡΠΌΠ° ΡΒ ΠΏΠΎΠΌΠΎΡΡΡ ΠΊΡΠ²Π°Π»Π΄Ρ ΠΈΠ»ΠΈ ΠΌΠΎΠ»ΠΎΡΠΊΠ°. ΠΠ΅ΡΠΎΠ΄ΠΈΠΊΠ° ΠΈΡΠΏΠΎΠ»ΡΠ·ΡΠ΅ΡΡΡ Π΄Π»Ρ ΠΈΠ·Π³ΠΎΡΠΎΠ²Π»Π΅Π½ΠΈΡ ΠΎΡΠ΄Π΅Π»ΡΠ½ΠΎΠΉ ΠΏΡΠΎΠ΄ΡΠΊΡΠΈΠΈ ΠΈΠ»ΠΈ Π΄Π»Ρ ΡΠ»ΡΡΡΠ΅Π½ΠΈΡ Π΅Π΅Β ΠΊΠ°ΡΠ΅ΡΡΠ²Π°.
Π¨ΡΠ°ΠΌΠΏΠΎΠ²ΠΎΡΠ½ΡΠΉ ΠΌΠ΅ΡΠΎΠ΄ ΠΈΡΠΏΠΎΠ»ΡΠ·ΡΠ΅ΡΡΡ Π΄Π»Ρ ΠΌΠ°ΡΡΠΎΠ²ΠΎΠ³ΠΎ ΠΏΡΠΎΠΈΠ·Π²ΠΎΠ΄ΡΡΠ²Π°. ΠΡΠΈ ΠΈΠ·Π³ΠΎΡΠΎΠ²Π»Π΅Π½ΠΈΠΈ ΠΏΡΠΎΠ΄ΡΠΊΡΠΈΠΈ ΠΌΠ΅ΡΠ°Π»Π» ΠΎΠ³ΡΠ°Π½ΠΈΡΠΈΠ²Π°Π΅ΡΡΡ ΡΡΠ°ΠΌΠΏΠ°ΠΌΠΈ ΠΈΒ ΠΏΠΎΠ»ΡΡΠ°Π΅Ρ Π½Π΅ΠΎΠ±Ρ ΠΎΠ΄ΠΈΠΌΡΡ ΡΠΎΡΠΌΡ Π·Π°Β ΡΡΠ΅Ρ Π΄Π΅ΡΠΎΡΠΌΠ°ΡΠΈΠΈ.
Π’Π΅Ρ Π½ΠΎΠ»ΠΎΠ³ΠΈΡ ΠΊΠΎΠ²ΠΊΠΈ Π·Π°Π³ΠΎΡΠΎΠ²ΠΎΠΊ ΠΈΒ ΠΌΠ°ΡΠ΅ΡΠΈΠ°Π»Ρ
ΠΠ·Π½Π°ΡΠ°Π»ΡΠ½ΠΎ ΠΊΡΠ·Π½Π΅ΡΡ ΠΊΠΎΠ²Π°Π»ΠΈ ΠΌΠ΅ΡΠ°Π»Π» ΠΈΠ·Β ΠΌΠ΅Π΄ΠΈ. ΠΠ°Β ΡΡΠΎ Π΅ΡΡΡ Π²ΠΏΠΎΠ»Π½Π΅ ΠΎΠ±ΡΡΠ½ΡΠ΅ ΠΏΡΠΈΡΠΈΠ½Ρ. ΠΠ΅Π΄Ρ Π±ΡΠ»Π° Π½Π°ΠΈΠ±ΠΎΠ»Π΅Π΅ ΡΠ°ΡΠΏΡΠΎΡΡΡΠ°Π½Π΅Π½Π½ΡΠΌ ΠΌΠ°ΡΠ΅ΡΠΈΠ°Π»ΠΎΠΌ. ΠΠ³ΠΎ ΠΌΠΎΠΆΠ½ΠΎ Π±ΡΠ»ΠΎ Π½Π°ΠΉΡΠΈ ΠΏΠΎΡΡΠΈ Π²Β ΡΠΈΡΡΠΎΠΌ Π²ΠΈΠ΄Π΅. Π’Π°ΠΊΠΆΠ΅ ΡΒ Π½Π΅Π΅ Π΄ΠΎΡΡΠ°ΡΠΎΡΠ½ΠΎ Π½ΠΈΠ·ΠΊΠ°Ρ ΡΠ΅ΠΌΠΏΠ΅ΡΠ°ΡΡΡΠ°, ΠΏΡΠΈ ΠΊΠΎΡΠΎΡΠΎΠΉ Π½Π°ΡΠΈΠ½Π°Π΅ΡΡΡ ΠΊΠΎΠ²ΠΊΠ°.
Π§Π΅ΡΠ΅Π· Π½Π΅ΠΊΠΎΡΠΎΡΠΎΠ΅ Π²ΡΠ΅ΠΌΡ ΠΊΡΠ·Π½Π΅ΡΡ ΠΎΡΠ²ΠΎΠΈΠ»ΠΈ ΡΠ°ΠΊΠΈΠ΅ ΠΌΠ°ΡΠ΅ΡΠΈΠ°Π»Ρ, ΠΊΠ°ΠΊ ΠΆΠ΅Π»Π΅Π·ΠΎ ΠΈΒ Π±ΡΠΎΠ½Π·Π°. Π‘Β ΠΈΡ Β ΠΏΠΎΡΠ²Π»Π΅Π½ΠΈΠ΅ΠΌ Π½Π°ΡΠ°Π»ΠΈ ΡΠΎΠ·Π΄Π°Π²Π°ΡΡΡΡ Π½ΠΎΠ²ΡΠ΅ ΠΌΠ΅ΡΠΎΠ΄Ρ ΠΊΠΎΠ²ΠΊΠΈ.
ΠΡΠ·Π½Π΅ΡΠ½Π°Ρ ΠΎΠ±ΡΠ°Π±ΠΎΡΠΊΠ° ΡΡΠ°Π»ΠΈ
ΠΒ ΠΏΡΠΎΠΈΠ·Π²ΠΎΠ΄ΡΡΠ²Π΅ ΠΊΠΎΠ²Π°Π½ΡΡ ΠΈΠ·Π΄Π΅Π»ΠΈΠΉ Π±ΠΎΠ»Π΅Π΅ Π²ΡΠ΅Π³ΠΎ ΡΠ°ΡΠΏΡΠΎΡΡΡΠ°Π½Π΅Π½ΠΎ ΠΈΡΠΏΠΎΠ»ΡΠ·ΠΎΠ²Π°Π½ΠΈΠ΅ ΡΡΠ°Π»ΠΈ, ΡΠ°ΠΊ ΠΊΠ°ΠΊ ΠΎΠ½Π° ΡΠ²Π»ΡΠ΅ΡΡΡ ΠΏΡΠΎΡΠ½Π΅ΠΉΡΠΈΠΌ ΠΌΠ°ΡΠ΅ΡΠΈΠ°Π»ΠΎΠΌ, ΠΊΠΎΡΠΎΡΡΠΉ Π²ΡΠ΅Π³Π΄Π° ΠΏΠΎΠ΄Π΄Π°Π΅ΡΡΡ ΠΎΠ±ΡΠ°Π±ΠΎΡΠΊΠ΅ ΡΒ ΠΏΠΎΠΌΠΎΡΡΡ Π΄Π°Π½Π½ΠΎΠ³ΠΎ ΠΌΠ΅ΡΠΎΠ΄Π°. ΠΡΠΈ ΠΎΠ±ΡΠ°Π±ΠΎΡΠΊΠ΅ ΡΡΠ΅Π±ΡΠ΅ΡΡΡ ΡΠΎΠ±Π»ΡΠ΄Π°ΡΡ ΡΠ»Π΅Π΄ΡΡΡΠΈΠ΅ ΡΡΠ»ΠΎΠ²ΠΈΡ:
ΠΠ°Π³ΠΎΡΠΎΠ²ΠΊΡ (ΠΏΠΎΠΊΠΎΠ²ΠΊΡ) Π½Π΅ΠΎΠ±Ρ ΠΎΠ΄ΠΈΠΌΠΎ Π½Π°Π³ΡΠ΅Π²Π°ΡΡ ΡΠ°Π²Π½ΠΎΠΌΠ΅ΡΠ½ΠΎ ΠΈΒ ΡΠΎΒ Π²ΡΠ΅Ρ ΡΡΠΎΡΠΎΠ½.
ΠΠ΅Π»ΡΠ·Ρ Π²ΡΡ ΠΎΠ΄ΠΈΡΡ Π·Π°Β ΡΠ°ΠΌΠΊΠΈ ΠΎΠΏΡΠ΅Π΄Π΅Π»Π΅Π½Π½ΠΎΠΉ ΡΠ΅ΠΌΠΏΠ΅ΡΠ°ΡΡΡΡ, ΠΎΡΒ ΠΊΠΎΡΠΎΡΠΎΠΉ Π·Π°Π²ΠΈΡΠΈΡ ΡΠ²Π΅ΡΠ΄ΠΎΡΡΡ ΠΌΠ°ΡΠ΅ΡΠΈΠ°Π»Π°. ΠΒ ΠΏΡΠΈΠΌΠ΅ΡΡ, Π»Π΅Π³ΠΈΡΠΎΠ²Π°Π½Π½ΡΠ΅ ΠΈΠ½ΡΡΡΡΠΌΠ΅Π½ΡΠ°Π»ΡΠ½ΡΠ΅ ΠΌΠ°ΡΠΊΠΈ Π·Π°ΠΏΡΠ΅ΡΠ΅Π½ΠΎ Π½Π°Π³ΡΠ΅Π²Π°ΡΡ Π΄ΠΎΒ 1000Β Π³ΡΠ°Π΄ΡΡΠΎΠ², Π°Β ΠΌΡΠ³ΠΊΠΈΠ΅ Π΄ΠΎΒ 1300 Π³ΡΠ°Π΄ΡΡΠΎΠ² ΠΈΒ Π²ΡΡΠ΅. ΠΡΠ»ΠΈ Π½Π°Π³ΡΠ΅ΡΡ Π½Π΅Π΄ΠΎΡΡΠ°ΡΠΎΡΠ½ΠΎ, ΡΠΎΒ Π½ΠΎΡΠΌΠ°Π»ΡΠ½ΠΎ ΠΎΠ±ΡΠ°Π±ΠΎΡΠ°ΡΡ ΠΌΠ°ΡΠ΅ΡΠΈΠ°Π» Π½Π΅Β Π²ΡΠΉΠ΄Π΅Ρ. ΠΡΠΎΠΌΠ΅ ΡΠΎΠ³ΠΎ, Π²Β ΡΠ°ΠΊΠΎΠΌ ΡΠ»ΡΡΠ°Π΅ ΠΌΠΎΠ³ΡΡ ΠΏΠΎΡΠ²ΠΈΡΡΡΡ ΡΡΠ΅ΡΠΈΠ½Ρ.
ΠΠ΅ΡΠ΅Π΄ ΡΠ΅ΠΌ, ΠΊΠ°ΠΊ Π½Π°Π³ΡΠ΅ΡΡ ΠΌΠ°ΡΠ΅ΡΠΈΠ°Π» Π΄ΠΎΒ ΡΠ΅ΠΌΠΏΠ΅ΡΠ°ΡΡΡΡ ΠΊΠΎΠ²ΠΊΠΈ, Π΅Π³ΠΎ ΡΠ»Π΅Π΄ΡΠ΅Ρ ΡΠ°Π·ΠΎΠ³ΡΠ΅ΡΡ ΠΏΡΠΈΠΌΠ΅ΡΠ½ΠΎ Π΄ΠΎΒ 300Β Π³ΡΠ°Π΄ΡΡΠΎΠ².
ΠΠΎΒ ΡΠΎΠ³ΠΎ, ΠΊΠ°ΠΊ ΠΈΠ·ΠΎΠ±ΡΠ΅Π»ΠΈ ΡΠΏΠ΅ΡΠΈΠ°Π»ΡΠ½ΠΎΠ΅ ΡΠ²Π°ΡΠΎΡΠ½ΠΎΠ΅ ΠΎΠ±ΠΎΡΡΠ΄ΠΎΠ²Π°Π½ΠΈΠ΅, ΡΒ ΠΏΠΎΠΌΠΎΡΡΡ ΠΊΡΠ·Π½Π΅ΡΠ½ΡΡ ΠΌΠ΅ΡΠΎΠ΄ΠΎΠ² ΡΠΎΠ΅Π΄ΠΈΠ½ΡΠ»ΠΈ ΠΈΒ ΡΠ°Π·Π½ΡΠ΅ ΠΌΠ΅ΡΠ°Π»Π»ΠΈΡΠ΅ΡΠΊΠΈΠ΅ ΡΠ°ΡΡΠΈ. ΠΠ΅ΠΉΡΡΠ²ΠΈΡ ΠΏΡΠΎΠΈΠ·Π²ΠΎΠ΄ΠΈΠ»ΠΈΡΡ Π±Π»Π°Π³ΠΎΠ΄Π°ΡΡ ΡΠ°Π·ΠΎΠ³ΡΠ΅Π²Ρ ΠΈΒ ΡΠ΄Π°Π²Π»ΠΈΠ²Π°Π½ΠΈΡ ΠΊΠΎΠ½ΡΠΎΠ² Π·Π°Π³ΠΎΡΠΎΠ²ΠΊΠΈ. ΠΠΎΠ΄ΠΎΠ±Π½ΡΠ΅ ΡΠΎΠ΅Π΄ΠΈΠ½Π΅Π½ΠΈΡ ΠΈΡΠΏΠΎΠ»ΡΠ·ΠΎΠ²Π°Π»ΠΈΡΡ ΠΏΠΎΡΡΠΈ Π΄Π»Ρ Π²ΡΠ΅Ρ Π΄ΠΎΡΡΡΠΏΠ½ΡΡ ΠΌΠ΅ΡΠ°Π»Π»ΠΎΠ², Π²ΠΊΠ»ΡΡΠ°Ρ ΠΆΠ΅Π»Π΅Π·ΠΎ, ΠΌΠ΅Π΄ΡΒ ΠΈ.Β Π΄.
Π‘Π΅Π³ΠΎΠ΄Π½Ρ ΡΠ΅Ρ Π½ΠΎΠ»ΠΎΠ³ΠΈΠΈ ΡΡΠ»ΠΈ Π΄Π°Π»Π΅ΠΊΠΎ Π²ΠΏΠ΅ΡΠ΅Π΄, ΠΎΠ΄Π½Π°ΠΊΠΎ ΠΊΠΎΠ²ΠΊΠ° ΠΎΡΡΠ°Π΅ΡΡΡ ΠΎΠ΄Π½ΠΎΠΉ ΠΈΠ·Β Π³Π»Π°Π²Π½ΡΡ ΠΌΠ΅ΡΠΎΠ΄ΠΈΠΊ ΠΏΠΎΠ»ΡΡΠ΅Π½ΠΈΡ ΡΠ°Π·Π½ΡΡ ΠΈΠ·Π΄Π΅Π»ΠΈΠΉ. Π£ΡΠΎΠ²Π΅ΡΡΠ΅Π½ΡΡΠ²ΠΎΠ²Π°Π½ΠΈΠ΅ ΠΌΠ΅ΡΠΎΠ΄ΠΎΠ² ΠΈΒ ΠΏΠΎΡΠ²Π»Π΅Π½ΠΈΠ΅ ΡΠΎΠΎΡΠ²Π΅ΡΡΡΠ²ΡΡΡΠ΅Π³ΠΎ ΠΎΠ±ΠΎΡΡΠ΄ΠΎΠ²Π°Π½ΠΈΡ ΠΏΠΎΠ·Π²ΠΎΠ»ΠΈΠ»ΠΎ ΠΏΠ΅ΡΠ΅ΠΉΡΠΈ ΠΊΒ ΠΌΠ°ΡΡΠΎΠ²ΠΎΠΌΡ ΠΏΡΠΎΠΈΠ·Π²ΠΎΠ΄ΡΡΠ²Ρ ΠΈΒ ΠΎΠ±ΡΠ°Π±ΠΎΡΠΊΠ΅ ΠΊΡΡΠΏΠ½ΠΎΠ³Π°Π±Π°ΡΠΈΡΠ½ΡΡ ΠΈΠ·Π΄Π΅Π»ΠΈΠΉ.
ΠΠ°Π²ΠΎΠ΄ ΠΠΠ Β«Π£ΡΠ°Π»ΡΡΠΊΠΈΠ΅ ΡΠ΅ΡΡΠΎΡΠΏΠ»Π°Π²ΡΒ» (Π§Π΅Π»ΡΠ±ΠΈΠ½ΡΠΊΠ°Ρ ΠΎΠ±Π»Π°ΡΡΡ, ΠΠΈΠ°ΡΡ)Β β ΡΠΆΠ΅ ΠΌΠ½ΠΎΠ³ΠΎ Π»Π΅Ρ Π·Π°Π½ΠΈΠΌΠ°Π΅ΡΡΡ ΠΏΡΠΎΠΈΠ·Π²ΠΎΠ΄ΡΡΠ²ΠΎΠΌ ΠΊΡΠ·Π½Π΅ΡΠ½ΡΡ ΡΠ»ΠΈΡΠΊΠΎΠ² ΠΈΒ ΠΏΠΎΠΊΠΎΠ²ΠΎΠΊ ΠΈΠ·Β ΠΆΠ°ΡΠΎΠΏΡΠΎΡΠ½ΡΡ ΡΠΏΠ»Π°Π²ΠΎΠ² ΠΈΒ Π½ΠΈΠ·ΠΊΠΎΠ»Π΅Π³ΠΈΡΠΎΠ²Π°Π½Π½ΡΡ ΡΡΠ°Π»Π΅ΠΉ. ΠΠΎΒ ΡΡΠ΅Π±ΠΎΠ²Π°Π½ΠΈΡ Π·Π°ΠΊΠ°Π·ΡΠΈΠΊΠ°, ΠΈΠ·Π΄Π΅Π»ΠΈΡ ΠΌΠΎΠ³ΡΡ Π±ΡΡΡ ΡΠ°Π·Π»ΠΈΡΠ½ΡΡ ΡΠ°ΡΠΊΡΠΎΠ΅Π², Π²Β ΡΠΎΠΌ ΡΠΈΡΠ»Π΅ ΡΒ ΡΠ΅Π·ΠΊΠΎΠΉ.
8 (916) 934-09-47 WhatsApp: +7(916) 934-09-47 Viber: +7(916) 934-09-47 E-mail: |
Π’Π΅Ρ
Π½ΠΎΠ»ΠΎΠ³ΠΈΡΠ΅ΡΠΊΠ°Ρ ΠΎΠ±ΡΠ°Π±ΠΎΡΠΊΠ° ΠΌΠ΅ΡΠ°Π»Π»Π° ΠΊΠΎΠ²ΠΊΠΎΠΉ Π²ΠΊΠ»ΡΡΠ°Π΅Ρ Π²Β ΡΠ΅Π±Ρ ΡΠ°Π·Π½ΠΎΠΎΠ±ΡΠ°Π·ΠΈΠ΅ ΠΏΡΠΈΠ΅ΠΌΠΎΠ², ΠΌΠ΅ΡΠΎΠ΄ΠΎΠ², ΠΊΠΎ-ΡΠΎΡΡΠ΅ ΠΏΡΠΎΠ΄ΠΈΠΊΡΠΎΠ²Π°Π½Ρ Ρ
Π°ΡΠ°ΠΊΡΠ΅ΡΠΎΠΌ ΠΌΠ°ΡΠ΅ΡΠΈΠ°Π»Π° ΠΈΒ ΡΠ΅ΠΌΠΈ Π·Π°Π΄Π°ΡΠ°ΠΌΠΈ, ΡΡΠΎΡΡΠΈΠΌΠΈ ΠΏΠ΅ΡΠ΅Π΄ Ρ
ΡΠ΄ΠΎΠΆΠ½ΠΈΠΊΠΎΠΌ-ΠΊΡΠ·Π½Π΅ΡΠΎΠΌβ¦ Π’Π΅Ρ Π½ΠΎΠ»ΠΎΠ³ΠΈΡΠ΅ΡΠΊΠ°Ρ ΠΎΠ±ΡΠ°Π±ΠΎΡΠΊΠ° ΠΌΠ΅ΡΠ°Π»Π»Π° ΠΊΠΎΠ²ΠΊΠΎΠΉ Π²ΠΊΠ»ΡΡΠ°Π΅Ρ Π²Β ΡΠ΅Π±Ρ ΡΠ°Π·Π½ΠΎΠΎΠ±ΡΠ°Π·ΠΈΠ΅ ΠΏΡΠΈΠ΅ΠΌΠΎΠ², ΠΌΠ΅ΡΠΎΠ΄ΠΎΠ², ΠΊΠΎ-ΡΠΎΡΡΠ΅ ΠΏΡΠΎΠ΄ΠΈΠΊΡΠΎΠ²Π°Π½Ρ Ρ Π°ΡΠ°ΠΊΡΠ΅ΡΠΎΠΌ ΠΌΠ°ΡΠ΅ΡΠΈΠ°Π»Π° ΠΈΒ ΡΠ΅ΠΌΠΈ Π·Π°Π΄Π°ΡΠ°ΠΌΠΈ, ΡΡΠΎΡΡΠΈΠΌΠΈ ΠΏΠ΅ΡΠ΅Π΄ Ρ ΡΠ΄ΠΎΠΆΠ½ΠΈΠΊΠΎΠΌ-ΠΊΡΠ·Π½Π΅ΡΠΎΠΌ. ΠΒ ΠΏΡΠΎΡΠ΅ΡΡΠ΅ ΠΊΠΎΠ²ΠΊΠΈ ΠΌΠ°ΡΡΠ΅Ρ ΠΏΡΠΈΠΌΠ΅Π½ΡΠ΅Ρ ΡΠ°Π·Π½ΠΎΠΎΠ±ΡΠ°Π·Π½ΡΠ΅ ΠΏΡΠΈΠ΅ΠΌΡ, ΠΈΡΠΏΠΎΠ»ΡΠ·ΡΡ ΡΠ°Π·Π½ΡΠ΅ ΠΈΠ½ΡΡΡΡΠΌΠ΅Π½ΡΡ, ΡΠ΅ΡΠ΅Π΄ΡΡ ΠΈΡ Β Π²Β ΡΠ°Π·Π»ΠΈΡΠ½ΡΡ ΠΊΠΎΠΌΠ±ΠΈΠ½Π°ΡΠΈΡΡ ΠΈΒ ΠΏΠΎΡΠ»Π΅Π΄ΠΎΠ²Π°ΡΠ΅Π»ΡΠ½ΠΎΡΡΠΈ. Π ΠΎΡΠ½ΠΎΠ²Π½ΠΎΠΌ Π²ΡΠ΅Β ΠΏΡΠΈΠ΅ΠΌΡ ΠΌΠΎΠΆΠ½ΠΎ ΡΠ²Π΅ΡΡΠΈ ΠΊΒ ΡΠ»Π΅Π΄ΡΡΡΠΈΠΌ ΠΎΡΠ½ΠΎΠ²Π½ΡΠΌ ΠΎΠΏΠ΅ΡΠ°ΡΠΈΡΠΌ: ΠΎΡΠ°Π΄ΠΊΠ°, Π²ΡΡΡΠΆΠΊΠ°, ΡΡΠ±ΠΊΠ°, ΡΠ°Π·ΡΡΠ±ΠΊΠ°, ΠΏΡΠΎΠ±ΠΈΠ²ΠΊΠ° ΠΎΡΠ²Π΅ΡΡΡΠΈΠΉ, Π³ΠΈΠ±ΠΊΠ°, Π·Π°ΠΊΡΡΡΠΈΠ²Π°Π½ΠΈΠ΅, Π½Π°ΡΠ΅ΠΊΠ°Π½ΠΈΠ΅ ΡΠΈΡΡΠ½ΠΊΠ°, Π½Π°Π±ΠΈΠ²ΠΊΠ° ΡΠ΅Π»ΡΠ΅ΡΠ°. Β ΠΠΎΡΠ»Π΅Π΄ΠΎΠ²Π°ΡΠ΅Π»ΡΠ½ΡΠ΅ ΠΎΠΏΠ΅ΡΠ°ΡΠΈΠΈ ΠΈΠ·Π³ΠΎΡΠΎΠ²Π»Π΅Π½ΠΈΡ ΠΊΠ»Π΅ΡΠ΅ΠΉ ΠΡΠ°Π΄ΠΊΠ° ΠΡΠΎΒ ΠΎΠΏΠ΅ΡΠ°ΡΠΈΡ, ΠΊΠΎΡΠΎΡΠ°Ρ ΠΏΡΠΈΠΌΠ΅Π½ΡΠ΅ΡΡΡ Π΄Π»ΡΒ ΡΠ²Π΅Π»ΠΈΡΠ΅Π½ΠΈΡ ΠΏΠΎΠΏΠ΅ΡΠ΅ΡΠ½ΠΎΠ³ΠΎ ΡΠ΅ΡΠ΅Π½ΠΈΡ ΠΊΠ°ΠΊΠΎΠΉ-ΡΠΎ ΡΠ°ΡΡΠΈ Π·Π°Π³ΠΎΡΠΎΠ²ΠΊΠΈ Π·Π°Β ΡΡΠ΅Ρ Π΅Π΅Β Π΄Π»ΠΈΠ½Ρ (Π²ΡΡΠΎΡΡ). ΠΡΠ°Π΄ΠΊΠ° ΠΌΠΎΠΆΠ΅Ρ Π±ΡΡΡ ΠΏΠΎΠ»Π½ΠΎΠΉ ΠΈΒ ΠΌΠ΅ΡΡΠ½ΠΎΠΉ. ΠΡΠΈΒ ΠΏΠΎΠ»Π½ΠΎΠΉ ΠΎΡΠ°Π΄ΠΊΠ΅ Π΄Π΅ΡΠΎΡΠΌΠΈΡΡΠ΅ΡΡΡ Π²Π΅ΡΡ ΠΌΠ΅ΡΠ°Π»Π». ΠΡΠΈΒ ΠΌΠ΅ΡΡ-Π½ΠΎΠΉ ΠΎΡΠ°Π΄ΠΊΠ΅ Π΄Π΅ΡΠΎΡΠΌΠΈΡΡΠ΅ΡΡΡ ΡΠΎΠ»ΡΠΊΠΎ ΡΠ°ΡΡΡ ΠΌΠ΅ΡΠ°Π»Π»Π°. ΠΎΠΎΡΠ²Π΅ΡΡΡΠ²Π΅Π½Π½ΠΎ ΡΡΠΎΠΌΡ ΠΈΒ Π΄Π΅Π»Π°Π΅ΡΡΡ Π½Π°Π³ΡΠ΅Π²-ΠΏΠΎΠ»Π½ΡΠΉΒ ΠΈΠ»ΠΈ ΠΌΠ΅ΡΡΠ½ΡΠΉ. ΠΡΠ°Π΄ΠΊΠ° ΠΏΡΠΈΠΌΠ΅Π½ΡΠ΅ΡΡΡ Π²Β ΡΠ»Π΅Π΄ΡΡΡΠΈΡ ΡΠ»ΡΡΠ°ΡΡ . ΠΠ»ΡΒ ΠΏΠΎΠ»ΡΡΠ΅Π½ΠΈΡ ΠΎΡΠ΄Π΅Π»ΡΠ½ΡΡ ΡΡΠΎΠ»ΡΠ΅Π½ΠΈΠΉ Π½Π°Β ΠΏΠΎΠΊΠΎΠ²ΠΊΠ΅ (ΠΎΡΠ°Π΄ΠΊΠΎΠΉ ΠΊΠΎΠ½ΡΠΎΠ²Β ΠΈΠ»ΠΈ ΡΠ΅ΡΠ΅Π΄ΠΈΠ½Ρ) ΠΏΡΠΈΒ ΠΊΠΎΠ²ΠΊΠ΅ Π΄Π΅-ΠΊΠΎΡΠ°ΡΠΈΠ²Π½ΡΡ ΡΠ»Π΅ΠΌΠ΅Π½ΡΠΎΠ², ΠΈΠΌΠ΅ΡΡΠΈΡ ΠΏΠ΅ΡΠ΅ΠΌΠ΅Π½Π½ΠΎΠ΅ ΡΠ΅ΡΠ΅Π½ΠΈΠ΅. ΠΠ°ΠΏΡΠΈΠΌΠ΅Ρ, ΡΠ°ΡΡΠΈΡΠ΅Π»ΡΠ½ΡΠ΅ ΠΎΡΠ½Π°ΠΌΠ΅Π½-ΡΠ°Π»ΡΠ½ΡΠ΅ ΠΌΠΎΡΠΈΠ²Ρ (ΡΡΠΎΠ»ΡΠ΅Π½Π½ΡΠ΅ ΡΠ·Π»Ρ Π½Π°Β ΡΡΠ΅Π±Π»Π΅, ΠΏΠ»ΠΎΠ΄Ρ, ΡΠ³ΠΎΠ΄Ρ ΠΈΒ Ρ.ΠΏ.)ΠΠΎΡΠ»Π΅ ΠΎΡΠ°Π΄ΠΊΠΈ ΠΏΠΎΠΊΠΎΠ²ΠΊΠ° Π΄ΠΎΠΏΠΎΠ»Π½ΠΈΡΠ΅Π»ΡΠ½ΠΎ ΠΎΠ±ΡΠ°Π±Π°ΡΡΠ²Π°Π΅ΡΡΡ ΠΎΠ±ΠΆΠΈΠΌΠΊΠ°ΠΌΠΈ, ΠΏΠΎΠ΄Π±ΠΎΠΉΠΊΠ°ΠΌΠΈ. ΠΠ°ΠΊΒ ΠΏΡΠ΅Π΄Π²Π°ΡΠΈΡΠ΅Π»ΡΠ½Π°Ρ ΠΎΠΏΠ΅ΡΠ°ΡΠΈΡ ΠΏΠ΅ΡΠ΅Π΄ Π·Π°Π³ΠΈΠ±Π°Π½ΠΈΠ΅ΠΌ ΠΏΠΎΠ΄Β ΡΠ³Π»ΠΎΠΌ Π΄Π»ΡΒ Π²ΠΎΡΠΏΠΎΠ»Π½Π΅Π½ΠΈΡ Π½Π΅Π΄ΠΎΡΡΠ°ΡΡΠ΅Π³ΠΎ ΠΌΠ΅ΡΠ°Π»Π»Π° Π΄Π»ΡΒ ΠΎΠ±ΡΠ°Π·ΠΎΠ²Π°Π½ΠΈΡ ΡΠ³Π»Π°. ΠΡΠΈΒ ΠΎΡΠ°Π΄ΠΊΠ΅ ΠΏΠΎΠΊΠΎΠ²ΠΊΡ Π½Π°Π³ΡΠ΅Π²Π°ΡΡ, ΡΡΠ°Π²ΡΡ Π²Π΅ΡΡΠΈΠΊΠ°Π»ΡΠ½ΠΎ Π½Π°Β Π½Π°ΠΊΠΎΠ²Π°Π»ΡΠ½Ρ ΠΈΒ Π±ΡΡΡ ΡΡΡΠ½ΠΈΠΊΠΎΠΌΒ ΠΈΠ»ΠΈ ΠΊΡΠ²Π°Π»Π΄ΠΎΠΉ ΠΏΠΎΒ Π²Π΅ΡΡ Π½Π΅ΠΌΡ ΠΊΠΎΠ½ΡΡ. ΠΠ»ΠΈΠ½Π° ΠΏΠΎΠΊΠΎΠ²ΠΊΠΈ Π½Π΅Β Π΄ΠΎΠ»ΠΆΠ½Π° ΠΏΡΠ΅Π²ΠΎΡΡ ΠΎΠ΄ΠΈΡΡ Π΄ΠΈΠ°ΠΌΠ΅ΡΡ Π±ΠΎΠ»ΡΡΠ΅ ΡΠ΅ΠΌΒ Π²Β 2Β β 2,5 ΡΠ°Π·Π°, ΠΈΠ½Π°ΡΠ΅ ΠΏΡΠΎΠΈΠ·ΠΎΠΉΠ΄ΡΡ ΠΈΠ·Π³ΠΈΠ±Π°Π½ΠΈΠ΅. ΠΡΠΈΠ΅ΠΌΡ ΠΎΡΠ°Π΄ΠΊΠΈ: Π°Β β ΠΎΡΠ°Π΄ΠΊΠ° Π²Β ΡΠΈΡΠΊΠ°Ρ ; Π±Β -ΠΎΡΠ°Π΄ΠΊΠ° Π½Π°Β Π½Π°ΠΊΠΎΠ²Π°Π»ΡΠ½Π΅; Π²Β β ΠΎΡΠ°Π΄ΠΊΠ° ΠΊΠΎΠ½ΡΠ° Π΄Π»ΡΒ ΠΎΠ±ΡΠ°Π·ΠΎΠ²Π°Π½ΠΈΡ Π³ΠΎΠ»ΠΎΠ²ΠΎΠΊ; Π³Β β ΠΎΠ±ΡΠ°Π·ΠΎΠ²Π°Π½ΠΈΠ΅ Π·Π°ΠΏΠ°ΡΠ° ΠΌΠ΅ΡΠ°Π»Π»Π° Π΄Π»ΡΒ Π³ΠΈΠ±ΠΊΠΈ ΠΏΠΎΠ΄Β ΡΠ³Π»ΠΎΠΌ ΠΡΠΈ ΠΎΡΠ°Π΄ΠΊΠ΅ Π²Π°ΠΆΠ½ΠΎ ΡΠΎΠ±Π»Ρ-Π΄Π°ΡΡ ΡΠ»Π΅Π΄ΡΡΡΠΈΠ΅ ΡΡΠ»ΠΎΠ²ΠΈΡ: ΠΊΠΎΠ½ΡΡ Π·Π°Π³ΠΎΡΠΎΠ²ΠΊΠΈ Π΄ΠΎΠ»ΠΆΠ½Ρ Π±ΡΡΡ ΡΡΡΠ±Π»Π΅Π½Ρ ΠΏΠΎΠ΄Β ΡΠ³Π»ΠΎΠΌ 90Β°, Π·Π°Π³ΠΎΡΠΎΠ²ΠΊΠ° Π΄ΠΎΠ»ΠΆ-Π½Π° Π±ΡΡΡ ΠΏΡΡΠΌΠΎΠΉ. ΠΡΠ»ΠΈΒ ΡΡΠ΅Π±ΡΠ΅ΡΡΡ ΠΎΡΠ°Π΄ΠΈΡΡ Π·Π°Π³ΠΎΡΠΎΠ²ΠΊΡ Π½Π°Β ΠΌΠ°Π»ΠΎΠΌ ΡΡΠ°ΡΡΠΊΠ΅ ΡΒ Π±ΠΎΠ»ΡΡΠΎΠΉ ΡΠ°Π·Π½ΠΈΡΠ΅ΠΉ Π²Β ΡΠ΅ΡΠ΅Π½ΠΈΠΈ, Π½Π°Π³ΡΠ΅ΡΡΡ Π·Π°-Π³ΠΎΡΠΎΠ²ΠΊΡ ΠΎΠΏΡΡΠΊΠ°ΡΡ Π²Β Ρ ΠΎΠ»ΠΎΠ΄Π½ΡΡ Π²ΠΎΠ΄Ρ, ΠΈΡΠΊΠ»ΡΡΠ°Ρ ΡΡΠ°ΡΡΠΎΠΊ, ΠΏΠΎΠ΄Π»Π΅ΠΆΠ°ΡΠΈΠΉ ΠΎΡΠ°Π΄ΠΊΠ΅. ΠΡΠ°Β ΠΎΠΏΠ΅ΡΠ°ΡΠΈΡ Π΄ΠΎΠ»ΠΆΠ½Π° ΠΏΡΠΎΠΈΠ·Π²ΠΎΠ΄ΠΈΡΡΡΡ Π±ΡΡΡΡΠΎ, Π·Π°Π³ΠΎΡΠΎΠ²ΠΊΡ Π½Π΅Π»ΡΠ·Ρ ΠΏΠ΅ΡΠ΅Π΄Π΅ΡΠΆΠΈΠ²Π°ΡΡ Π²Β Π²ΠΎΠ΄Π΅, Π½Π΅ΠΎΠ±Ρ ΠΎΠ΄ΠΈΠΌΠΎ ΡΠ»Π΅Π΄ΠΈΡΡ Π·Π°Β Π½Π°Π³ΡΠ΅ΡΡΠΌ ΠΊΠΎΠ½ΡΠΎΠΌ. Π’Π°ΠΊΠΎΠΉ ΠΏΡΠΈΠ΅ΠΌ ΠΏΡΠΈΠΌΠ΅Π½ΡΠ΅ΡΡΡ ΠΏΡΠΈΒ ΠΈΠ·Π³ΠΎΡΠΎΠ²Π»Π΅Π½ΠΈΠΈ Π³ΠΎΠ»ΠΎΠ²ΠΎΠΊ Π±ΠΎΠ»ΡΠΎΠ²Β ΠΈΠ»ΠΈ Π±ΠΎΠ»ΡΡΠΈΡ ΡΡΡΠΎΠΈΡΠ΅Π»ΡΠ½ΡΡ Π³Π²ΠΎΠ·Π΄Π΅ΠΉ. ΠΠ΅ΠΊΠΎΡΠΎΡΡΠ΅ ΠΊΡΠ·Π½Π΅ΡΡ ΠΎΡΠ°Π΄ΠΊΡ ΠΊΠΎΠ½ΡΠΎΠ² Π·Π°Π³ΠΎΡΠΎΠ²ΠΊΠΈ ΠΏΡΠΎΠΈΠ·Π²ΠΎΠ΄ΡΡ ΡΠ°ΠΊ: Π½Π°Π³ΡΠ΅ΡΡΠΉ ΠΊΠΎΠ½Π΅Ρ Π·Π°Π³ΠΈΠ±Π°ΡΡ ΠΏΠΎΠ΄Β ΡΠ³Π»ΠΎΠΌ 90Β° ΠΈ, ΠΏΠ΅ΡΠ΅Π²Π΅ΡΠ½ΡΠ², ΡΠ΄Π°ΡΡΡΡ ΠΏΠΎΒ Π·Π°Π³Π½ΡΡΠΎΠΌΡ ΡΠΎΡΡΡ ΠΌΠ΅ΡΠ°Π»Π»Π°. Π’ΡΡΠ΄Π½ΠΎΡΡΡ ΡΡΠΎΠ³ΠΎ ΠΏΡΠΈΡΠΌΠ° Π·Π°ΠΊΠ»ΡΡΠ°Π΅ΡΡΡ Π²Β ΡΠΎΠΌ, ΡΡΠΎΠ±Ρ ΠΏΡΠΈΒ ΠΎΡΠ°Π΄ΠΊΠ΅ Π½Π΅Β ΡΠ΄Π΅Π»Π°ΡΡ ΡΠΊΠ»Π°Π΄ΠΊΡ Π·Π°Π³Π½ΡΡΠΎΠ³ΠΎ ΠΊΠΎΠ½ΡΠ°. Π₯ΠΎΡΠΎΡΠΎ ΡΡΠΎΡ ΠΏΡΠΈΡΠΌ ΠΈΡΠΏΠΎΠ»ΡΠ·ΠΎΠ²Π°ΡΡ ΠΏΡΠΈΒ Π³ΠΎΡΠ½ΠΎΠΉ ΡΠ²Π°ΡΠΊΠ΅. ΠΡΠ°Π΄ΠΊΡ ΠΊΠΎΠ½ΡΠΎΠ² Π·Π°Π³ΠΎΡΠΎΠ²ΠΎΠΊ ΠΌΠΎΠΆΠ½ΠΎ ΠΏΡΠΎΠΈΠ·Π²ΠΎΠ΄ΠΈΡΡ Π²Β ΡΠΈΡΠΊΠ°Ρ : Π½Π°Π³ΡΠ΅ΡΡΡ Π·Π°Π³ΠΎΡΠΎΠ²ΠΊΡ Π·Π°ΠΊΡΠ΅ΠΏ-Π»ΡΡΡ Π²Β ΡΠΈΡΠΊΠΈ, ΡΠ°ΠΊΒ ΡΡΠΎΠ±Ρ Π½Π°Π΄Β Π³ΡΠ±ΠΊΠ°ΠΌΠΈ Π²ΠΎΠ·Π²ΡΡΠ°Π»Π°ΡΡ ΡΠ°Β ΡΠ°ΡΡΡ ΠΌΠ΅ΡΠ°Π»Π»Π°, ΠΊΠΎΡΠΎΡΡΡ ΡΡΠ΅Π±ΡΠ΅ΡΡΡ ΠΎΡΠ°Π΄ΠΈΡΡ. ΠΡΡΠΎΡΠ° ΠΎΡΠ°ΠΆΠΈΠ²Π°Π΅ΠΌΠΎΠΉ ΡΠ°ΡΡΠΈ Π΄ΠΎΠ»ΠΆΠ½Π° Π±ΡΡΡ Π²Β 2,5 ΡΠ°Π·Π° Π±ΠΎΠ»ΡΡΠ΅ ΡΠ΅ΡΠ΅Π½ΠΈΡ Π·Π°Π³ΠΎΡΠΎΠ²ΠΊΠΈ. ΠΡΡΒ ΠΎΠΏΠ΅ΡΠ°ΡΠΈΡ Π½Π΅-ΠΎΠ±Ρ ΠΎΠ΄ΠΈΠΌΠΎ ΠΏΡΠΎΠΈΠ·Π²ΠΎΠ΄ΠΈΡΡ Π±ΡΡΡΡΠΎ, ΠΏΠΎΡΠΎΠΌΡ ΡΡΠΎΒ ΠΏΡΠΈΒ Π·Π°ΠΆΠ°ΡΠΈΠΈ Π²Β ΡΠΈΡΠΊΠΈ Π½Π°Π³ΡΠ΅ΡΡΠΉ ΠΌΠ΅ΡΠ°Π»Π» Π±ΡΡΡΡΠΎ ΠΎΡΡΡΠ²Π°Π΅Ρ ΠΎΡΒ ΡΠΎΠΏΡΠΈΠΊΠΎΡΠ½ΠΎΠ²Π΅Π½ΠΈΡ ΡΒ Π³ΡΠ±ΠΊΠ°ΠΌΠΈ. ΠΡΡΡΡΠΎ Π·Π°ΠΊΡΠ΅ΠΏΠΈΠ² Π·Π°Π³ΠΎΡΠΎΠ²ΠΊΡ, ΡΡΡΠ½ΠΈΠΊΠΎΠΌ ΠΎΡΠ°ΠΆΠΈΠ²Π°ΡΡ. ΠΡΠΈΒ ΠΎΡΠ°ΠΆΠΈΠ²Π°Π½ΠΈΠΈ ΠΊΠΎΠ½ΡΠΎΠ² Π·Π°Π³ΠΎΡΠΎΠ²ΠΎΠΊ Π±ΠΎΠ»ΡΡΠΎΠ³ΠΎ ΡΠ΅ΡΠ΅Π½ΠΈΡ ΠΎΠ±ΡΡΠ½ΠΎ Π±ΡΠ²Π°Π΅Ρ, ΡΡΠΎΒ ΡΠΈΠ»Π° Π³ΡΠ±ΠΎΠΊ ΡΠΈΡΠΊΠΎΠ² Π½Π΅Π΄ΠΎΡ-ΡΠ°ΡΠΎΡΠ½Π° ΠΈΒ ΠΏΡΠΈΒ ΡΠ΄Π°ΡΠ΅ Π·Π°Π³ΠΎΡΠΎΠ²ΠΊΠ° ΡΠΊΠΎΠ»ΡΠ·ΠΈΡ Π²Β ΡΠΈΡΠΊΠ°Ρ . ΠΒ ΡΡΠΎΠΌ ΡΠ»ΡΡΠ°Π΅, Π΅ΡΠ»ΠΈΒ ΠΏΠΎΠ·Π²ΠΎΠ»ΡΠ΅Ρ Π·Π°Π³ΠΎΡΠΎΠ²ΠΊΠ°, Π²Β Π½Π΅ΠΉΒ Π΄Π΅Π»Π°ΡΡΡΡ ΠΏΠ»Π΅ΡΠΈΠΊΠΈ. ΠΡΠΈΒ ΡΠ°Π±ΠΎΡΠ΅ ΡΒ ΠΏΠΎΠΊΠΎΠ²ΠΊΠ°ΠΌΠΈ Π±ΠΎΠ»ΡΡΠΎΠΉ Π΄Π»ΠΈΠ½Ρ Π±ΡΠ²Π°ΡΡ ΡΠ»ΡΡΠ°ΠΈ, ΠΊΠΎΠ³Π΄Π° Π½Π°Π΄ΠΎ ΠΏΡΠΎΠΈΠ·Π²ΠΎΠ΄ΠΈΡΡ ΠΎΡΠ°Π΄ΠΊΡ Π²Β ΡΠ΅ΡΠ΅Π΄ΠΈ-Π½Π΅ Π·Π°Π³ΠΎΡΠΎΠ²ΠΊΠΈ. ΠΡΠ΅Β ΠΏΠ΅ΡΠ΅ΡΠΈΡΠ»Π΅Π½Π½ΡΠ΅ ΠΏΡΠΈΠ΅ΠΌΡ Π²Β ΡΡΠΎΠΌ ΡΠ»ΡΡΠ°Π΅ Π½Π΅ΠΏΡΠΈΠ΅ΠΌΠ»Π΅ΠΌΡ (Π² ΡΠ°ΡΡΠ½ΠΎΡΡΠΈ, Π½Π΅Π»ΡΠ·Ρ ΠΏΡΠΎΠΈΠ·-Π²ΠΎΠ΄ΠΈΡΡ ΠΎΡΠ°Π΄ΠΊΡ ΡΠ΄Π°ΡΠ°ΠΌΠΈ ΡΠ°ΠΌΠΎΠ³ΠΎ ΠΏΡΠ΅Π΄ΠΌΠ΅ΡΠ° ΠΎΒ Π½Π°ΠΊΠΎΠ²Π°Π»ΡΠ½Ρ). ΠΒ ΡΡΠΎΠΌ ΡΠ»ΡΡΠ°Π΅ Π²Β Π·ΠΎΠ½Π΅ ΠΎΡΠ°Π΄ΠΊΠΈ Π·Π°Π³ΠΎΡΠΎΠ²ΠΊΡ Π²ΡΠ³ΠΈΠ±Π°ΡΡ Π²Β ΡΠΎΡΠΌΠ΅ Π±ΡΠΊΠ²Ρ Z ΠΈΒ ΡΠ²Π΅ΡΡ Ρ ΠΏΠΎΒ ΠΈΠ·Π³ΠΈΠ±Ρ ΡΠ΄Π°ΡΡΡΡ ΡΡΡΠ½ΠΈΠΊΠΎΠΌ; ΠΏΠΎΡΠ»Π΅ ΠΎΡΠ°Π΄ΠΊΠΈ Π·Π°Π³ΠΎΡΠΎΠ²ΠΊΡ Π²ΡΠΏΡΠ°Π²Π»ΡΡΡ. ΠΡΠΎΠΌΠ΅ ΠΏΠ΅ΡΠ΅ΡΠΈΡΠ»Π΅Π½Π½ΡΡ ΠΏΡΠΈΠ΅ΠΌΠΎΠ² ΡΡΡΠ΅ΡΡΠ²ΡΡΡ ΠΈΒ Π΄ΡΡΠ³ΠΈΠ΅ ΡΒ ΠΈΡΠΏΠΎΠ»ΡΠ·ΠΎΠ²Π°Π½ΠΈΠ΅ΠΌ ΠΏΡΠΈΡΠΏΠΎΡΠΎΠ±Π»Π΅Π½ΠΈΠΉ. ΠΡΡΡΠΆΠΊΠ° ΠΡΠ°Β ΠΎΠΏΠ΅ΡΠ°ΡΠΈΡ ΠΏΡΠΈΠΌΠ΅Π½ΡΠ΅ΡΡΡ Π΄Π»ΡΒ ΡΠ²Π΅Π»ΠΈΡΠ΅Π½ΠΈΡ Π΄Π»ΠΈΠ½Ρ Π·Π°Π³ΠΎΡΠΎΠ²ΠΊΠΈ Π·Π°Β ΡΡΠ΅Ρ ΡΠΌΠ΅Π½ΡΡΠ΅Π½ΠΈΡ Π΅Π΅Β ΠΏΠΎΠΏΠ΅ΡΠ΅ΡΠ½ΠΎΠ³ΠΎ ΡΠ΅ΡΠ΅Π½ΠΈΡ. ΠΠ°Π³ΡΠ΅ΡΡΡ Π·Π°Π³ΠΎΡΠΎΠ²ΠΊΡ ΠΊΠ»Π°Π΄ΡΡ Π½Π°Β Π½Π°ΠΊΠΎΠ²Π°Π»ΡΠ½Ρ ΠΈΒ ΡΠ΄Π°ΡΠ°ΠΌ ΠΌΠΎΠ»ΠΎΡΠ° Π²ΡΡΡΠ³ΠΈΠ²Π°ΡΡ. ΠΠΎΠ΅ΠΊ ΠΌΠΎΠ»ΠΎΡΠΊΠ° ΠΈΠΌΠ΅Π΅Ρ ΠΏΠΎΠ²Π΅ΡΡ Π½ΠΎΡΡΡ ΠΈΒ Π³Π»Π°Π΄ΠΊΡΡ, Π°Β Π²ΡΠΏΡΠΊΠ»ΡΡ, ΠΈ, ΠΊΠΎΠ³Π΄Π° ΠΏΡΠΎΠΈΡΡ ΠΎΠ΄ΠΈΡ ΡΠ΄Π°Ρ, ΠΌΠ΅ΡΠ°Π», ΠΊΠ°ΠΊΒ Π±ΡΒ Π²ΡΠ΄Π°Π²Π»ΠΈΠ²Π°Π΅ΡΡΡ Π²ΠΎΒ Π²ΡΠ΅Β ΡΡΠΎΡΠΎΠ½Ρ ΠΈΒ ΠΏΠΎΒ Π΄Π»ΠΈΠ½Π΅, ΠΈΒ ΠΏΠΎΒ ΡΠΈΡΠΈΠ½Π΅ Π·Π°Π³ΠΎΡΠΎΠ²ΠΊΠΈ. ΠΠΎΠ²Π΅ΡΠ½ΡΠ² Π·Π°Π³ΠΎΡΠΎΠ²ΠΊΡ Π½Π°Β 90Β°, ΡΠ΄Π°ΡΡΡΡ ΠΏΠΎΒ Π²ΡΠΏΡΠΊΠ»ΠΎΡΡΠΈ, ΠΊΠΎΡΠΎΡΠ°Ρ ΠΏΠΎΠ»ΡΡΠΈΠ»Π°ΡΡ Π²Β ΡΠ΅Π·ΡΠ»ΡΡΠ°ΡΠ΅ ΠΏΠ΅ΡΠ²ΠΎΠ³ΠΎ ΡΠ΄Π°ΡΠ°. Π’Π°ΠΊ, ΠΏΠ΅ΡΠΈΠΎΠ΄ΠΈΡΠ΅ΡΠΊΠΈ ΠΏΠΎΠ²ΠΎΡΠ°ΡΠΈΠ²Π°Ρ ΠΈΒ ΠΏΠ΅ΡΠ΅Π΄Π²ΠΈΠ³Π°Ρ Π·Π°Π³ΠΎΡΠΎΠ²ΠΊΡ, Π΅Π΅Β Π²ΡΡΡΠ³ΠΈΠ²Π°ΡΡ. Π’Π°ΠΊΠΈΠΌ ΠΎΠ±ΡΠ°Π·ΠΎΠΌ, Π³Π»Π°Π²Π½ΠΎΠ΅ ΡΠΎΡΡΠΎΠΈΡ Π²Β ΡΠΎΠΌ, ΡΡΠΎΠ±Ρ Π²Β ΠΏΡΠΎΡΠ΅ΡΡΠ΅ Π²ΡΡΡΠΆΠΊΠΈ Π²Β ΡΠ΅ΡΠ΅Π½ΠΈΠΈ Π²ΡΠ΅Π³Π΄Π° Π΄ΠΎΠ»ΠΆΠ΅Π½ Π±ΡΡΡ ΠΊΠ²Π°Π΄ΡΠ°Ρ. ΠΠ»ΡΒ ΡΡΠΊΠΎΡΠ΅Π½ΠΈΡ Π²ΡΡΡΠΆΠΊΠΈ ΠΊΠΎΠ²ΠΊΡ ΠΌΠΎΠΆΠ½ΠΎ Π²Π΅ΡΡΠΈ Π½Π°Β ΡΠΎΠ³Π΅ Π½Π°ΠΊΠΎΠ²Π°Π»ΡΠ½ΠΈ; Π²Β ΡΡΠΎΠΌ ΡΠ»ΡΡΠ°Π΅ ΠΌΠ΅ΡΠ°Π»Π» Π±ΡΠ΄Π΅Ρ ΡΡ-Π½ΡΡΡΡΡ (ΡΠ΅ΡΡ) ΠΌΠ΅ΠΆΠ΄Ρ Π΄Π²ΡΡ Π²ΡΠΏΡΠΊΠ»ΠΎΡΡΠ΅ΠΉ, ΡΡΠΎΒ ΡΠΏΠΎΡΠΎΠ±ΡΡΠ²ΡΠ΅Ρ Π±ΠΎΠ»Π΅Π΅ Π±ΡΡΡΡΠΎΠΌΡ ΡΠ²Π΅Π»ΠΈΡΠ΅Π½ΠΈΡ Π΄Π»ΠΈΠ½Ρ Π·Π°Π³ΠΎΡΠΎΠ²ΠΊΠΈ. ΠΡΡΠ³ΠΎΠΉ Π²Π°ΡΠΈΠ°Π½Ρ Π²ΡΡΡΠΆΠΊΠΈΒ β ΡΒ ΡΠ°ΡΠΊΠ°ΡΠΊΠΎΠΉ,Β ΠΈΠ»ΠΈ ΡΠ°Π·Π³ΠΎΠ½ΠΊΠΎΠΉ. Π€ΠΎΡΠΌΠ° ΡΠ°ΡΠΊΠ°ΡΠΊΠΈ ΡΠ°ΡΠ΅ Π²ΡΠ΅Π³ΠΎ ΠΏΠΎΠ»ΡΠΊΡΡΠ³Π»Π°Ρ. ΠΡΒ ΡΠ°ΡΠΏΠΎΠ»ΠΎΠΆΠ΅Π½ΠΈΡ ΡΠ°ΡΠΊΠ°ΡΠΊΠΈ Π½Π°Β ΠΏΠΎΠΊΠΎΠ²ΠΊΠ΅ (Π²Π΄ΠΎΠ»ΡΒ ΠΈΠ»ΠΈ ΠΏΠΎΠΏΠ΅ΡΠ΅ΠΊ) Π·Π°Π²ΠΈΡΠΈΡ Π½Π°ΠΏΡΠ°Π²Π»Π΅Π½ΠΈΠ΅ Π²ΡΡΡΠΆΠΊΠΈ. ΠΡΡΡΠΆΠΊΠ° Π½Π°Β ΠΊΠΎΠ½ΡΠ΅ ΠΏΡΠΈΠΌΠ΅Π½ΡΠ΅ΡΡΡ ΠΏΡΠΈΒ ΠΈΠ·Π³ΠΎΡΠΎΠ²Π»Π΅Π½ΠΈΠΈ Π³Π²ΠΎΠ·Π΄Π΅ΠΉ, ΡΠ²Π΅ΡΡΠΎΠ², ΠΏΡΠΎΠ±ΠΎΠ΅Π², ΠΆΠΈΠΊΠΎΠ²ΠΈΠ½ ΠΈΒ Π΄ΡΡΠ³ΠΈΡ ΠΈΠ·Π΄Π΅Π»ΠΈΠΉ. ΠΠ°Π³ΡΠ΅ΡΡΡ Π·Π°Π³ΠΎΡΠΎΠ²ΠΊΡ Π½Π°ΡΠΈΠ½Π°ΡΡ Π²ΡΡΡΠ³ΠΈΠ²Π°ΡΡ, Π½Π΅ΠΌΠ½ΠΎΠ³ΠΎ ΠΎΡΡΡΡΠΏΠ°Ρ ΠΎΡΒ ΠΊΠΎΠ½ΡΠ°, ΠΈΒ Π²Β ΠΏΡΠΎΡΠ΅ΡΡΠ΅ Π²ΡΡΡΠΆΠΊΠΈ ΠΏΠΎΠ΄Π°-ΡΡ Π½Π°Β ΡΠ΅Π±Ρ. ΠΠΎΒ Π²ΡΠ΅ΠΌΡ ΡΠ°Π±ΠΎΡΡ Π½ΡΠΆΠ½ΠΎ ΡΠ»Π΅Π΄ΠΈΡΡ, ΡΡΠΎΠ±Ρ ΠΊΠ²Π°Π΄ΡΠ°Ρ, ΠΊΠΎΡΠΎΡΡΠΉ ΠΏΠΎΠ»ΡΡΠΈΠ»ΡΡ Π²Β ΠΏΡΠΎΡΠ΅ΡΡΠ΅ ΠΊΠΎΠ²ΠΊΠΈ, ΡΡ ΠΎΠ΄ΠΈΠ» Π½Π°Β ΠΊΠΎΠ½Π΅Ρ ΠΏΠΎΠΊΠΎΠ²ΠΊΠΈ. ΠΡΠΎΒ Π΄ΠΎΡΡΠΈΠ³Π°Π΅ΡΡΡ ΡΠΈΠ»ΠΎΠΉ ΠΈΒ Ρ Π°ΡΠ°ΠΊΡΠ΅ΡΠΎΠΌ ΡΠ΄Π°ΡΠΎΠ². ΠΠ°ΠΊΠ°Π½ΡΠΈΠ²Π°ΡΡ Π²ΡΡΡΠΆΠΊΡ Π½ΡΠΆΠ½ΠΎ Π»Π΅Π³ΠΊΠΈΠΌΠΈ ΡΠ΄Π°ΡΠ°ΠΌΠΈ. ΠΠ°Β ΡΠΈΡ. 2, Π°Β β Π³Β ΠΏΠΎΠΊΠ°Π·Π°Π½Ρ ΠΏΡΠΈΠ΅ΠΌΡ Π²ΡΡΡΠΆΠΊΠΈ. Π ΠΈΡ. 2 Π ΡΠ±ΠΊΠ°Β β ΠΎΠΏΠ΅ΡΠ°ΡΠΈΡ, ΠΏΠΎΡΡΠ΅Π΄ΡΡΠ²ΠΎΠΌ ΠΊΠΎΡΠΎΡΠΎΠΉ ΠΏΠΎΠΊΠΎΠ²ΠΊΡ ΡΠ°Π·Π΄Π΅Π»ΡΡΡ Π½Π°Β ΡΠ°ΡΡΠΈ. ΠΠ»ΡΒ ΡΡΠΎΠ³ΠΎ Π·Π°Π³ΠΎΡΠΎΠ²ΠΊΡ Π½Π°Π³ΡΠ΅-Π²Π°ΡΡ Π΄ΠΎΒ ΡΠ΅ΠΌΠ½ΠΎ-ΠΊΡΠ°ΡΠ½ΠΎΠ³ΠΎ ΠΊΠ°Π»Π΅Π½ΠΈΡ, ΠΊΠ»Π°Π΄ΡΡ Π½Π°Β Π½Π°ΠΊΠΎΠ²Π°Π»ΡΠ½Ρ ΠΈ, Π½Π°ΡΡΠ°Π²ΠΈΠ² ΠΊΡΠ·Π½Π΅ΡΠ½ΠΎΠ΅ Π·ΡΠ±ΠΈΠ»ΠΎ, ΠΏΡΠΎΡΡΠ±Π°ΡΡ Π½Π°Β ΡΡΠΈΒ ΡΠ΅ΡΠ²Π΅ΡΡΠΈ Π΅Π΅Β ΡΠΎΠ»ΡΠΈΠ½Ρ; ΠΏΠ΅ΡΠ΅Π²Π΅ΡΠ½ΡΠ² Π·Π°Π³ΠΎΡΠΎΠ²ΠΊΡ, Π²Π½ΠΎΠ²Ρ Π½Π°ΡΡΠ°Π²Π»ΡΡΡ Π·ΡΠ±ΠΈΠ»ΠΎ ΠΈΒ ΠΎΡΡΡΠ±Π°ΡΡ ΡΠΈΠ»ΡΠ½Ρ-ΠΌΠΈ ΡΠ΄Π°ΡΠ°ΠΌΠΈ. ΠΡΠΈΒ ΡΠ°Π±ΠΎΡΠ΅ ΠΊΡΠ·Π½Π΅ΡΠ½ΡΠΌΠΈ Π·ΡΠ±ΠΈΠ»Π°ΠΌΠΈ ΠΏΠΎΒ Π³ΠΎΡΡΡΠ΅ΠΌΡ Π½Π΅ΠΎΠ±Ρ ΠΎΠ΄ΠΈΠΌΠΎ ΠΏΡΠΈΒ ΡΡΠ±ΠΊΠ΅ ΡΠΎΠ»ΡΡΡΡ Π·Π°Π³ΠΎΡΠΎ-Π²ΠΎΠΊ ΠΏΠ΅ΡΠΈΠΎΠ΄ΠΈΡΠ΅ΡΠΊΠΈ ΠΎΡ Π»Π°ΠΆΠ΄Π°ΡΡ Π·ΡΠ±ΠΈΠ»ΠΎ, ΡΠ°ΠΊΒ ΠΊΠ°ΠΊΒ ΠΏΡΠΈΒ Π΄ΠΎΠ»Π³ΠΎΠΌ ΡΠΎΠΏΡΠΈΠΊΠΎΡΠ½ΠΎΠ²Π΅Π½ΠΈΠΈ ΡΒ Π½Π°Π³ΡΠ΅ΡΡΠΌ ΠΌΠ΅ΡΠ°Π»Π»ΠΎΠΌ Π»Π΅Π·Π²ΠΈΠ΅ Π·ΡΠ±ΠΈΠ»Π° ΠΎΡΠΏΡΡΠΊΠ°Π΅ΡΡΡ. ΠΠ΅ΡΠ΅Π΄ ΡΠ΅ΠΌΒ ΠΊΠ°ΠΊΒ Π²Π½ΠΎΠ²Ρ Π½Π°ΡΡΠ°Π²ΠΈΡΡ Π·ΡΠ±ΠΈΠ»ΠΎ Π½Π°Β Π·Π°Π³ΠΎΡΠΎΠ²ΠΊΡ, Π½Π΅ΠΎΠ±Ρ ΠΎΠ΄ΠΈΠΌΠΎ Π»Π΅Π³-ΠΊΠΈΠΌ ΠΏΠΎΡΡΡΠΊΠΈΠ²Π°Π½ΠΈΠ΅ΠΌ ΠΎΒ ΡΡΡΠ» Π½Π°ΠΊΠΎΠ²Π°Π»ΡΠ½ΠΈ ΡΠ±ΠΈΡΡ ΠΊΠ°ΠΏΠ»ΠΈ Π²ΠΎΠ΄Ρ ΡΒ Π·ΡΠ±ΠΈΠ»Π°. ΠΡΠΈΒ ΡΠ°Π±ΠΎΡΠ΅ Π½Π°Β Π»ΠΈΡΠ΅ Π½Π°ΠΊΠΎΠ²Π°Π»ΡΠ½ΠΈ Π·ΡΠ±ΠΈΠ»Π°ΠΌΠΈ ΠΈΒ Π΄ΡΡΠ³ΠΈΠΌΠΈ ΡΠ΅ΠΆΡΡΠΈΠΌΠΈ ΠΈΠ½ΡΡΡΡΠΌΠ΅Π½ΡΠ°ΠΌΠΈ Π±Π΅Π·Β ΠΏΠΎΠ΄ΠΊΠ»Π°Π΄ΠΊΠΈ Π½ΡΠΆΠ½ΠΎ Π±ΡΡΡ ΠΎΡΠΎΠ±Π΅Π½Π½ΠΎ Π²Π½ΠΈΠΌΠ°ΡΠ΅Π»ΡΠ½ΡΠΌ ΠΈΒ ΠΎΡΡΠΎΡΠΎΠΆΠ½ΡΠΌ ΠΈΒ ΡΠ»Π΅Π΄ΠΈΡΡ, ΡΡΠΎΠ±Ρ Π·Π°Π³ΠΎΡΠΎΠ²ΠΊΠ° Π½Π΅Β ΠΏΡΠΎΡΡΠ±Π°Π»Π°ΡΡ. ΠΡΠΎΒ ΠΌΠΎΠΆΠ΅Ρ ΠΈΡΠΏΠΎΡΡΠΈΡΡ Π»ΠΈΡΠΎ Π½Π°ΠΊΠΎΠ²Π°Π»ΡΠ½ΠΈ. Π Π°Π·ΡΡΠ±ΠΊΠ° (ΠΏΡΠΎΡΡΠ±ΠΊΠ°)Β β ΠΎΠΏΠ΅ΡΠ°ΡΠΈΡ, Π²Β ΡΠ΅Π·ΡΠ»ΡΡΠ°ΡΠ΅ ΠΊΠΎΡΠΎΡΠΎΠΉ Π·Π°Π³ΠΎΡΠΎΠ²ΠΊΠ° ΡΠΎΠ»ΡΠΊΠΎ Π½Π°Π΄ΡΡΠ±Π°Π΅ΡΡΡ. ΠΡΠΎΡ ΠΏΡΠΈΠ΅ΠΌ ΡΠΈΡΠΎΠΊΠΎ ΠΏΡΠΈΠΌΠ΅Π½ΡΠ΅ΡΡΡ Π²Β Ρ ΡΠ΄ΠΎΠΆΠ΅ΡΡΠ²Π΅Π½Π½ΠΎΠΉ ΠΊΠΎΠ²ΠΊΠ΅. ΠΠ°Π΄ΡΡΠ±Π»Π΅Π½Π½ΡΠ΅ ΡΡΠ°ΡΡΠΊΠΈ ΠΎΡΠ³ΠΈΠ±Π°ΡΡΡΡ, Π²ΡΡΡΠ³ΠΈΠ²Π°ΡΡΡΡ, ΠΎΠ½ΠΈΒ ΠΏΡΠ΅ΡΠ΅ΡΠΏΠ΅Π²Π°ΡΡ ΡΠ°Π·Π»ΠΈΡΠ½ΡΠ΅ Π²ΠΈΠ΄Ρ ΠΊΠΎΠ²ΠΊΠΈ, ΠΏΠΎΡΠ»Π΅ ΡΠ΅Π³ΠΎ ΠΏΡΠ΅Π²ΡΠ°ΡΠ°ΡΡΡΡ Π²Β ΡΠ²Π΅ΡΡ, Π·Π°Π²ΠΈΡΠΊΠΈΒ ΠΈΠ»ΠΈ Π»ΠΈΡΡΡΡ. ΠΡΠΎΠ±Π΅Π½Π½ΠΎ ΡΠΈΡΠΎΠΊΠΎ ΡΡΠΎΡ ΠΏΡΠΈΠ΅ΠΌ ΠΏΡΠΈΠΌΠ΅Π½ΡΠ΅ΡΡΡ ΠΏΡΠΈΒ ΠΈΠ·Π³ΠΎΡΠΎΠ²Π»Π΅Π½ΠΈΠΈ ΠΆΠΈΠΊΠΎΠ²ΠΈΠ½, ΡΠ²Π΅ΡΡΠΎΠ² ΠΈΒ Ρ. ΠΏ. ΠΡΠΈΒ ΡΠ°Π·ΡΡΠ±ΠΊΠ΅ Π·Π°Π³ΠΎΡΠΎΠ²ΠΊΡ ΡΠ°Π·ΡΡΠ±Π°ΡΡ ΡΒ ΠΎΠ΄Π½ΠΎΠΉ ΡΡΠΎΡΠΎΠ½Ρ (Π»ΠΈΡΠ΅Π²ΠΎΠΉ). ΠΠ΅ΡΠ²ΡΠ΅ ΡΠ΄Π°ΡΡ Π΄Π΅Π»Π°ΡΡ Π»Π΅Π³ΠΊΠΈΠΌΠΈ; ΠΈΠΌΠΈΒ ΡΠΎΠ»ΡΠΊΠΎ Π½Π°Π΄ΡΡΠ±Π°ΡΡ ΠΊΠ°Π½Π°Π²ΠΊΡ. ΠΠ°Π³ΡΠ΅Π² Π΄ΠΎΠ»ΠΆΠ΅Π½ Π±ΡΡΡ ΡΠ»Π°Π±ΡΠΌΒ β ΡΡΠΎΒ ΠΏΠΎΠ·Π²ΠΎΠ»ΡΠ΅Ρ Π½Π΅Β ΡΠΎΡΠΎΠΏΠΈΡΡΡΡ ΠΈΒ ΡΠΏΠΎ-ΠΊΠΎΠΉΠ½ΠΎ ΡΠ°ΡΠΊΡΠΎΠΈΡΡ ΠΌΠ΅ΡΠ°Π»Π». ΠΠΎΡΠ»Π΅ ΡΠ°ΡΠΊΡΠΎΡ ΠΌΠ°ΡΠ΅ΡΠΈΠ°Π» Π½Π°Π³ΡΠ΅Π²Π°ΡΡ ΠΈΒ ΡΠΈΠ»ΡΠ½ΡΠΌΠΈ ΡΠ΄Π°ΡΠ°ΠΌΠΈ ΡΠ°Π·ΡΡΠ±Π°ΡΡ. ΠΡ-Π±ΠΈΠ»ΠΎ Π²Β ΠΏΡΠΎΡΠ΅ΡΡΠ΅ ΡΡΠ±ΠΊΠΈ ΡΠΎΠ»ΡΠΊΠΎ Π²Β ΠΌΠΎΠΌΠ΅Π½Ρ ΡΠ΄Π°ΡΠ° ΡΡΠ°Π²ΡΡ Π²Β Π½Π°ΠΏΡΠ°Π²Π»ΡΡΡΠΈΠΉ ΠΆΠ΅Π»ΠΎΠ±. Π£Π΄Π°ΡΡ ΠΌΠΎΠ»ΠΎΡΠΎΠΌ Π΄ΠΎΠ»ΠΆΠ½Ρ Π±ΡΡΡ ΡΠ΅Π΄ΠΊΠΈΠ΅, Π½ΠΎΒ ΡΠΈΠ»ΡΠ½ΡΠ΅. ΠΠΎΠ»ΠΎΡΠΎΠ±ΠΎΠ΅Ρ Π΄ΠΎΠ»ΠΆΠ΅Π½ ΠΏΡΠΎΠΈΠ·Π²ΠΎΠ΄ΠΈΡΡ ΡΠ΄Π°Ρ Π²Β ΡΠΎΡΒ ΠΌΠΎΠΌΠ΅Π½Ρ, ΠΊΠΎΠ³Π΄Π° ΡΠ±Π΅Π΄ΠΈΡΡΡ Π²Β ΠΏΡΠ°Π²ΠΈΠ»ΡΠ½ΠΎΡΡΠΈ ΡΡΡΠ°Π½ΠΎΠ²ΠΊΠΈ Π·ΡΠ±ΠΈΠ»Π°. ΠΠ±ΡΡΠ±ΠΊΠ° (ΠΎΠ±ΡΠ΅ΡΠΊΠ°)Β β ΠΎΡΠ΄Π΅Π»Π΅Π½ΠΈΠ΅ ΡΠ°ΡΡΠΈ ΠΌΠ΅ΡΠ°Π»Π»Π° ΠΏΠΎΒ Π½Π°ΡΡΠΆΠ½ΠΎΠΌΡ ΠΊΠΎΠ½ΡΡΡΡ. ΠΡΠΈΠΌΠ΅Π½ΡΠ΅ΡΡΡ ΠΏΡΠΈΒ ΠΊΠΎΠ²ΠΊΠ΅ Π΄Π΅ΠΊΠΎΡΠ°ΡΠΈΠ²Π½ΡΡ ΠΈΠ·Π΄Π΅Π»ΠΈΠΉ ΡΠ»ΠΎΠΆΠ½ΠΎΠΉ ΡΠΎΡΠΌΡ: Π½Π°ΠΊΠ»Π°Π΄ΠΎΠΊ, ΠΆΠΈΠΊΠΎΠ²ΠΈΠ½ ΠΈΒ Ρ.Π΄., Ρ.Π΅. ΡΠ°ΠΌ, Π³Π΄Π΅Β Π½Π΅ΠΎΠ±Ρ ΠΎΠ΄ΠΈΠΌΠΎ ΠΎΠ±ΡΡΠ±ΠΈΡΡ Π΄Π΅ΡΠ°Π»Ρ ΠΏΠΎΒ ΠΊΠΎΠ½ΡΡΡΡ. ΠΡΡΡΠ±ΠΊΠ°Β β ΠΎΠΏΠ΅ΡΠ°ΡΠΈΡ, Π°Π½Π°Π»ΠΎΠ³ΠΈΡΠ½Π°Ρ ΠΎΠ±ΡΡΠ±ΠΊΠ΅. ΠΡΠΈΠΌΠ΅Π½ΡΠ΅ΡΡΡ Π΄Π»ΡΒ Π²ΡΡΡΠ±ΠΊΠΈ ΠΌΠ΅ΡΠ°Π»Π»Π° ΠΏΠΎΒ Π²Π½ΡΡ-ΡΠ΅Π½Π½Π΅ΠΌΡ ΠΊΠΎΠ½ΡΡΡΡ. ΠΠΏΠ΅ΡΠ°ΡΠΈΠΈ ΠΎΠ±ΡΡΠ±ΠΊΠΈ ΠΈΒ Π²ΡΡΡΠ±ΠΊΠΈ Π°Π½Π°Π»ΠΎΠ³ΠΈΡΠ½Ρ ΠΏΡΠΎΡΠ΅ΡΠΊΠ΅, ΡΒ ΡΠΎΠΉΒ ΡΠΎΠ»ΡΠΊΠΎ ΡΠ°Π·Π½ΠΈΡΠ΅ΠΉ, ΡΡΠΎΒ ΠΏΡΠΎΡΠ΅ΡΠΊΠ° Π²ΡΠΏΠΎΠ»Π½ΡΠ΅ΡΡΡ ΠΏΠΎΒ Π±ΠΎΠ»Π΅Π΅ ΡΠΎΠ½ΠΊΠΎΠΌΡ Π»ΠΈΡΡΡ ΡΡΡΠ½ΡΠΌΠΈ Π·ΡΠ±ΠΈΠ»Π°ΠΌΠΈ ΠΈΒ Π²Β Ρ ΠΎΠ»ΠΎΠ΄Π½ΠΎΠΌ ΡΠΎΡΡΠΎΡΠ½ΠΈΠΈ. ΠΡΠ±ΠΈΠ»Π° ΠΏΡΠΈΠΌΠ΅Π½ΡΡΡΡΡ ΡΠ°Π·Π½ΠΎΠ³ΠΎ ΠΏΡΠΎΡΠΈΠ»Ρ: ΠΏΠΎΠ»ΡΠΊΡΡΠ³Π»ΡΠ΅, ΠΏΡΡΠΌΡΠ΅, ΡΠ³ΠΎΠ»ΡΠ½ΡΠ΅ ΠΈΒ Π΄Ρ. ΠΡΠ²Π΅ΡΡΡΠΈΡ Π²Β ΠΏΠΎΠΊΠΎΠ²ΠΊΠ°Ρ
ΠΏΠΎΠ»ΡΡΠ°ΡΡ ΡΒ ΠΏΠΎΠΌΠΎΡΡΡ ΠΏΡΠΎΠ±ΠΈΠ²ΠΊΠΈ. ΠΡΠΈΒ ΠΎΠΏΠ΅ΡΠ°ΡΠΈΠΈ ΠΏΡΠΎΠΈΠ·Π²ΠΎΠ΄ΡΡΡΡ ΠΏΡΠΈΒ Π²ΡΡΠΎΠΊΠΈΡ
ΡΠ΅ΠΌΠΏΠ΅ΡΠ°ΡΡΡΠ°Ρ
. ΠΠ°Β ΠΌΠ΅ΡΡΠΎ, ΠΏΠΎΠ΄Π»Π΅ΠΆΠ°ΡΠ΅Π΅ ΠΏΡΠΎΠ±ΠΈΠ²ΠΊΠ΅, ΡΡΡΠ°Π½Π°Π²Π»ΠΈΠ²Π°ΡΡ ΠΏΡΠΎ-Π±ΠΎΠΉΠ½ΠΈΠΊ (Π±ΠΎΡΠΎΠ΄ΠΎΠΊ) ΠΈΒ Π½Π°Π½ΠΎΡΡΡ ΡΠ΄Π°ΡΡ Π΄ΠΎΡΡΠ°ΡΠΎΡΠ½ΠΎ ΡΠΈΠ»ΡΠ½ΡΠ΅, ΡΡΠΎΠ±Ρ Π±ΠΎΡΠΎΠ΄ΠΎΠΊ Π±ΠΎΡΠΎΠ΄ΠΎΠΊ ΠΏΠΎΠ³ΡΡΠ·ΠΈΠ»ΡΡ Π½Π°Β ΡΡΠΈΒ ΡΠ΅ΡΠ²Π΅ΡΡΠΈ ΡΠΎΠ»ΡΠΈΠ½Ρ ΠΌΠ΅ΡΠ°Π»Π»Π°. Π ΡΠ΅Π·ΡΠ»ΡΡΠ°ΡΠ΅ ΡΠ°ΠΊΠΎΠΉ ΠΏΡΠΎΠ±ΠΈΠ²ΠΊΠΈ Π²ΡΡΡΠ±Π»Π΅Π½Π½ΡΠΉ ΡΡΠ°ΡΡΠΎΠΊ ΠΌΠ΅ΡΠ°Π»Π»Π° Π½Π°Π·ΡΠ²Π°Π΅ΡΡΡ Π²ΡΠ΄ΡΠΎΠΉ. ΠΡΠ»ΠΈΒ Π½Π΅ΠΎΠ±Ρ ΠΎΠ΄ΠΈΠΌΠΎ ΡΠΎΠ΅Π΄ΠΈΠ½ΠΈΡΡ Π²Π·Π°ΠΈΠΌΠ½ΠΎ ΠΏΠ΅ΡΠ΅ΡΠ΅ΠΊΠ°ΡΡΠΈΠ΅ΡΡ Π·Π°Π³ΠΎΡΠΎΠ²ΠΊΠΈ ΠΎΠ΄ΠΈΠ½Π°ΠΊΠΎΠ²ΠΎΠ³ΠΎ ΡΠ΅ΡΠ΅Π½ΠΈΡ, ΡΠΎΒ ΠΎΡΠ²Π΅ΡΡΡΠΈΠ΅ ΡΠ°Π·ΡΡΠ±Π°ΡΡ ΠΈΒ ΡΒ ΠΏΠΎΠΌΠΎΡΡΡ Π±ΠΎΡΠΎΠ΄ΠΊΠ° ΡΠ°Π·Π³ΠΎΠ½ΡΡΡ. ΠΡΠΈΠΌ ΠΏΡΠΈΠ΅ΠΌΠΎΠΌ ΠΏΠΎΠ»ΡΠ·ΠΎΠ²Π°Π»ΠΈΡΡ ΡΡΠ°ΡΡΠ΅ ΠΌΠ°ΡΡΠ΅ΡΠ° ΠΏΡΠΈΒ ΠΈΠ·Π³ΠΎΡΠΎΠ²Π»Π΅Π½ΠΈΠΈ ΠΎΠΊΠΎΠ½Π½ΡΡ ΡΠ΅ΡΠ΅ΡΠΎΠΊ. ΠΡΠΈ ΠΏΠΎΠ»ΡΡΠ΅Π½ΠΈΠΈ ΠΎΡΠ²Π΅ΡΡΡΠΈΠΉ ΠΊΠ²Π°Π΄ΡΠ°ΡΠ½ΠΎΠ³ΠΎ ΡΠ΅ΡΠ΅Π½ΠΈΡΒ ΠΈΠ»ΠΈ Π΄ΡΡΠ³ΠΎΠ³ΠΎ Π²Β ΠΊΡΡΠ³Π»ΠΎΠ΅ ΠΎΡΠ²Π΅ΡΡΡΠΈΠ΅, ΠΏΡΠ΅Π΄Π²Π°ΡΠΈΡΠ΅Π»ΡΠ½ΠΎ Π½Π°Π³ΡΠ΅ΡΠΎΠ΅, Π²ΡΡΠ°Π²Π»ΡΡΡ ΠΎΠΏΡΠ°Π²ΠΊΡ Π½ΡΠΆΠ½ΠΎΠ³ΠΎ ΠΏΡΠΎΡΠΈΠ»Ρ. ΠΡΠ»ΠΈ Π½Π΅ΠΎΠ±Ρ ΠΎΠ΄ΠΈΠΌΠΎ ΡΠ΄Π΅Π»Π°ΡΡ ΠΎΡΠ²Π΅ΡΡΡΠΈΠ΅ Π²Β Π·Π°Π³ΠΎΡΠΎΠ²ΠΊΠ΅ ΠΊΡΡΠ³Π»ΠΎΠ³ΠΎ ΡΠ΅ΡΠ΅Π½ΠΈΡ, ΡΡΠ΅Π½ΠΊΠΈ ΠΊΠΎΡΠΎΡΠΎΠΉ’ Π΄ΠΎΠ»ΠΆΠ½Ρ Π±ΡΡΡ ΡΠ°Π²Π½Ρ ΠΏΠΎΠ»ΠΎΠ²ΠΈΠ½Π΅ ΡΠΎΠ»ΡΠΈΠ½Ρ, Π½Π΅ΠΎΠ±Ρ ΠΎΠ΄ΠΈΠΌΠΎ Π»Π΅Π³ΠΊΠΈΠΌ ΡΠ΄Π°ΡΠΎΠΌ ΡΡΡΠ½ΠΈΠΊΠ° Π²Β Π½Π°Π³ΡΠ΅ΡΠΎΠΌ ΡΠΎΡΡΠΎΡΠ½ΠΈΠΈ ΡΠ΄Π΅Π»Π°ΡΡ ΠΏΠ»ΠΎΡΠΊΠΎΡΡΡ, Π½Π°Β ΠΊΠΎΡΠΎΡΡΡ ΡΡΠ°Π²ΠΈΡΡΡ Π·ΡΠ±ΠΈΠ»ΠΎ. ΠΡΠΎΒ ΠΏΠΎΠ·Π²ΠΎΠ»ΡΠ΅Ρ Π·Π°Π³ΠΎΡΠΎΠ²ΠΊΡ ΡΠ°Π·ΡΡΠ±ΠΈΡΡ ΡΠΎΡΠ½ΠΎ ΠΏΠΎΡΡΠ΅Π΄ΠΈΠ½Π΅. ΠΡΠΎΡΒ ΠΆΠ΅ ΡΠΏΠΎΡΠΎΠ± ΠΏΡΠΈΠΌΠ΅Π½ΡΠ΅ΡΡΡ ΠΈΒ Π΄Π»ΡΒ ΠΏΡΠΎΠ±ΠΈΠ²Π°Π½ΠΈΡ ΠΎΡΠ²Π΅ΡΡΡΠΈΠΉ ΡΠ΅ΡΠ΅Π· Π³ΡΠ°Π½Ρ. ΠΡΠΈ ΠΏΡΠΎΠ±ΠΈΠ²Π°Π½ΠΈΠΈ ΠΎΡΠ²Π΅ΡΡΡΠΈΠΉ, Π±ΠΎΠ»ΡΡΠΈΡ
ΠΏΠΎΒ Π΄ΠΈΠ°ΠΌΠ΅ΡΡΡ, ΡΠ΅ΠΌΒ Π²ΡΠ΅Β ΠΈΠΌΠ΅ΡΡΠΈΠ΅ΡΡ ΠΎΠΏΡΠ°Π²ΠΊΠΈ, ΠΏΠΎΠ»ΡΠ·ΡΡΡΡΡ ΡΠΎΠ³ΠΎΠΌ Π½Π°ΠΊΠΎΠ²Π°Π»ΡΠ½ΠΈ. ΠΠ»ΡΒ ΡΡΠΎΠ³ΠΎ Π·Π°Π³ΠΎΡΠΎΠ²ΠΊΡ ΡΠ°Π·ΡΡΠ±Π°ΡΡ, ΡΠ°Π·Π²ΠΎΠ΄ΡΡ Π½Π°ΠΈΠ±ΠΎΠ»ΡΡΠ΅ΠΉ ΠΎΠΏΡΠ°Π²ΠΊΠΎΠΉ, Π½Π°Π΄Π΅Π²Π°ΡΡ Π²Β Π½Π°Π³ΡΠ΅ΡΠΎΠΌ ΡΠΎΡΡΠΎΡΠ½ΠΈΠΈ Π½Π°Β ΡΠΎΠ³Β ΠΈΒ ΡΡΡΠ½ΠΈΠΊΠΎΠΌ ΠΏΡΠΎΠΊΠΎΠ²ΡΠ²Π°ΡΡ. ΠΠΈΠ±ΠΊΠ° ΠΏΠΎΠ΄Β ΡΠ³Π»ΠΎΠΌΒ β ΠΏΡΠΎΠΈΠ·Π²ΠΎΠ΄ΠΈΡΡΡ Π½Π°Β ΡΠ΅Π±ΡΠ΅ Π½Π°ΠΊΠΎΠ²Π°Π»ΡΠ½ΠΈ ΡΒ ΠΏΡΠ΅Π΄Π²Π°ΡΠΈΡΠ΅Π»ΡΠ½ΡΠΌ Π½Π°Π³ΡΠ΅Π²ΠΎΠΌ ΡΠΎΠ»ΡΠΊΠΎ ΡΡΠ°ΡΡ-ΠΊΠ° Π³ΠΈΠ±ΠΊΠΈ. ΠΠ°Π³ΡΠ΅ΡΡΡ Π·Π°Π³ΠΎΡΠΎΠ²ΠΊΡ ΡΡΡΠ°Π½Π°Π²Π»ΠΈΠ²Π°ΡΡ ΡΠ°ΠΊ, ΡΡΠΎΠ±Ρ Π±ΡΠ΄ΡΡΠ΅Π΅ ΡΠ΅Π±ΡΠΎ ΡΠ³ΠΈΠ±Π° Π½Π°Β Π·Π°Π³ΠΎΡΠΎΠ²ΠΊΠ΅ ΡΠΎΠ²ΠΏΠ°-Π΄Π°Π»ΠΎ ΡΒ ΠΏΠ΅ΡΠ΅Π΄Π½ΠΈΠΌ ΡΠ΅Π±ΡΠΎΠΌ Π½Π°ΠΊΠΎΠ²Π°Π»ΡΠ½ΠΈ, ΠΈΒ ΠΏΡΠΈΠΆΠΈΠΌΠ°ΡΡ ΡΠ²Π΅ΡΡ
Ρ ΠΊΡΠ²Π°Π»Π΄ΠΎΠΉ. Π ΡΡΠ½ΠΈΠΊΠΎΠΌ ΡΠ΄Π°ΡΡΡΡ Π½Π΅Β ΠΏΠΎΒ ΠΊΠΎΠ½-ΡΡ Π·Π°Π³ΠΎΡΠΎΠ²ΠΊΠΈ, Π°Β Π±Π»ΠΈΠΆΠ΅ ΠΊΒ ΡΠ΅Π±ΡΡ Π½Π°ΠΊΠΎΠ²Π°Π»ΡΠ½ΠΈ. ΠΡΠ»ΠΈ Π΄Π»ΠΈΠ½Π½ΡΡ ΠΏΠΎΠ»ΠΎΡΡΒ ΠΈΠ»ΠΈ ΠΏΡΡΡΠΎΠΊ Π½Π΅ΠΎΠ±Ρ ΠΎΠ΄ΠΈΠΌΠΎ ΡΠΎΠ³Π½ΡΡΡ Π½Π΅ΡΠΊΠΎΠ»ΡΠΊΠΎ ΡΠ°Π· (ΠΏΡΠΈΡΠ΅ΠΌ ΠΌΠ΅ΡΡΠ° ΡΠ³ΠΈΠ±ΠΎΠ² ΡΠ°ΡΠΏΠΎ-Π»ΠΎΠΆΠ΅Π½Ρ Π±Π»ΠΈΠ·ΠΊΠΎ Π΄ΡΡΠ³ ΠΊΒ Π΄ΡΡΠ³Ρ), Π³ΠΈΠ±ΠΊΡ ΠΏΡΠΎΠΈΠ·Π²ΠΎΠ΄ΡΡ Π½Π°Β ΡΠΏΠ΅ΡΠ°ΠΊΠ°Ρ ΡΒ ΡΠΎΠ³ΠΎΠΌ ΠΏΠΎΠ΄Ρ ΠΎΠ΄ΡΡΠ΅ΠΉ ΡΠΎΡΠΌΡ. ΠΡΠ»ΠΈ Π½Π΅ΠΎΠ±Ρ
ΠΎΠ΄ΠΈΠΌΠΎ Π³Π½ΡΡΡ Π·Π°Π³ΠΎΡΠΎΠ²ΠΊΠΈ ΠΏΠΎΠ΄Β Π»ΡΠ±ΡΠΌ ΡΠ³Π»ΠΎΠΌ, ΡΠΎΒ ΠΏΡΠΈΠΌΠ΅Π½ΡΡΡ Π½ΠΈΠΆΠ½ΠΈΠΊ, ΠΊΠΎΡΠΎΡΡΠΉ ΠΈΠ·Π³ΠΎΡΠΎΠ²Π»ΡΡΡ Π²Β ΠΏΡΠΎΡΠ΅ΡΡΠ΅ ΡΠ°Π±ΠΎΡΡ. ΠΠ°Π³ΡΠ΅ΡΡΡ Π·Π°Π³ΠΎΡΠΎΠ²ΠΊΡ ΠΊΠ»Π°Π΄ΡΡ Π½Π°Β Π½ΠΈΠΆΠ½ΠΈΠΊ, ΡΠ²Π΅ΡΡ
Ρ ΠΏΠ΅ΡΠΏΠ΅Π½Π΄ΠΈΠΊΡΠ»ΡΡΠ½ΠΎ Π΅ΠΉΒ β ΠΏΠ»Π°ΡΡΠΈΠ½Ρ, ΡΠ°Π²Π½ΡΡ ΠΏΠΎΒ ΡΠΈΡΠΈΠ½Π΅ Π΄Π΅ΡΠ°Π»ΠΈ ΠΠ° Π½Π΅ΠΈΠΌΠ΅Π½ΠΈΠ΅ΠΌ Π½ΠΈΠΆΠ½ΠΈΠΊΠ° ΠΌΠΎΠΆΠ½ΠΎ Π²ΠΎΡΠΏΠΎΠ»ΡΠ·ΠΎΠ²Π°ΡΡΡΡ Π²ΠΈΠ»ΠΊΠΎΠΉ, ΠΊΠΎΡΠΎΡΡΡ ΡΠ°ΠΊΠΆΠ΅ ΠΌΠΎΠΆΠ½ΠΎ ΡΠΎΠ³Π½ΡΡΡ Π²ΠΎΒ Π²ΡΠ΅ΠΌΡ ΡΠ°Π±ΠΎΡΡ Π½Π°Π΄Β ΠΈΠ·Π΄Π΅Π»ΠΈΠ΅ΠΌ. ΠΠ½ΠΎΠ³Π΄Π° ΠΏΠΎΡΠ»Π΅ ΠΈΠ·Π³ΠΈΠ±Π°Π½ΠΈΡ Π²Β Π²ΠΈΠ»ΠΊΠ΅ ΡΡΠΊΠΎΠ²ΠΊΡ Π²ΡΠΏΡΠ°Π²Π»ΡΡΡ ΡΒ ΠΏΠΎΠΌΠΎΡΡΡ Π³Π»Π°Π΄ΠΈΠ»ΠΊΠΈΒ ΠΈΠ»ΠΈ Π½Π°Β ΠΊΠ²Π°Π΄ΡΠ°ΡΠ½ΠΎΠΌ ΡΠΎ-Π³Π΅ Π½Π°ΠΊΠΎΠ²Π°Π»ΡΠ½ΠΈ. ΠΠΈΠ±ΠΊΠ° ΠΏΠΎΒ Π΄ΡΠ³Π΅Β β ΠΎΠΏΠ΅ΡΠ°ΡΠΈΡ, ΠΊΠΎΡΠΎΡΠ°Ρ ΠΏΡΠΎΠΈΠ·Π²ΠΎΠ΄ΠΈΡΡΡ Π½Π°Β ΡΠΎΠ³Π΅ Π½Π°ΠΊΠΎΠ²Π°Π»ΡΠ½ΠΈΒ ΠΈΠ»ΠΈ ΡΠΎΠΎΡΠ²Π΅ΡΡΡΠ²ΡΡΡΠΈΡ ΠΏΠΎΒ Π΄Ρ-Π³Π΅ ΡΠΏΠ΅ΡΠ°ΠΊΠ°Ρ . Π‘Π»ΠΎΠΆΠ½ΡΠ΅ ΠΏΡΠΎΡΠΈΠ»ΠΈ Π³Π½ΡΡ Π½Π°Β ΠΎΠΏΡΠ°Π²ΠΊΠ°Ρ , ΡΠ°Π±Π»ΠΎΠ½Π°Ρ ΠΈΒ Π³ΠΈΠ±ΠΎΡΠ½ΠΎΠΉ ΠΏΠ»ΠΈΡΠ΅. ΠΠΈΠ±ΠΊΡ ΠΏΠΎΒ ΡΠ°Π±Π»ΠΎΠ½Ρ Π΄Π΅Π»Π°ΡΡ ΡΠΎΠ³Π΄Π°, ΠΊΠΎΠ³Π΄Π° Π²Β ΠΈΠ·Π΄Π΅Π»ΠΈΠΈ ΠΎΠ΄ΠΈΠ½ ΠΈΒ ΡΠΎΡΒ ΠΆΠ΅ ΡΠ»Π΅ΠΌΠ΅Π½Ρ ΠΏΠΎΠ²ΡΠΎΡΡΠ΅ΡΡΡ ΠΌΠ½ΠΎΠ³ΠΎ ΡΠ°Π·. ΠΠ·Β Π΄ΠΎΡΡΠ°ΡΠΎΡΠ½ΠΎ ΡΠΎΠ»ΡΡΠΎΠ³ΠΎ ΠΏΠΎΠ»ΠΎΡΠΎΠ²ΠΎΠ³ΠΎ ΠΌΠ΅ΡΠ°Π»Π»Π° Π²ΡΠ³ΠΈΠ±Π°ΡΡ ΡΠ°Π±Π»ΠΎΠ½ Π±ΡΠ΄ΡΡΠ΅Π³ΠΎ ΡΠ»Π΅ΠΌΠ΅Π½ΡΠ°. ΠΠ³ΠΎΒ Π·Π°ΠΊΡΠ΅ΠΏΠ»ΡΡΡ ΠΎΠ΄Π½ΠΈΠΌ ΠΊΠΎΠ½ΡΠΎΠΌ Π²Β ΡΠΈΡΠΊΠΈΒ ΠΈΠ»ΠΈ ΠΎΠ½Β ΠΌΠΎΠΆΠ΅Ρ Π±ΡΡΡ ΡΠΌΠΎΠ½ΡΠΈΡΠΎΠ²Π°Π½ Π½Π°Β ΠΏΠΎΠ΄ΠΊΠ»Π°Π΄ΠΊΡ ΠΈΒ Π½Π°Π³ΡΠ΅ΡΠΎΠΉ Π·Π°Π³ΠΎΡΠΎΠ²ΠΊΠΎΠΉ ΠΎΠ³ΠΈΠ±Π°-ΡΡ. ΠΡΠΎΠ±Π΅Π½Π½ΠΎΡΡΡ Π·Π°ΠΊΠ»ΡΡΠ°Π΅ΡΡΡ Π²Β ΡΠΎΠΌ, ΡΡΠΎΒ ΠΏΡΠΈΒ ΠΈΠ·Π³ΠΎΡΠΎΠ²Π»Π΅Π½ΠΈΠΈ ΡΠ°Π±Π»ΠΎΠ½Π° Π½ΡΠΆΠ½ΠΎ Π±ΡΡΡ Π²Π½ΠΈΠΌΠ°ΡΠ΅Π»ΡΠ½ΡΠΌ ΠΈΒ ΠΈΠ·Π³ΠΎΡΠΎΠ²Π»ΡΡΡ Π΅Π³ΠΎΒ ΡΒ Π±ΠΎΠ»ΡΡΠΎΠΉ ΡΡΠ°ΡΠ΅Π»ΡΠ½ΠΎΡΡΡΡ, ΠΏΠΎΡΠΎΠΌΡ ΡΡΠΎΒ Π±ΡΠ΄ΡΡΠΈΠ΅ ΡΠ»Π΅ΠΌΠ΅Π½ΡΡ ΠΈΠ·Π΄Π΅Π»ΠΈΡ Π±ΡΠ΄ΡΡ ΠΊΠΎΠΏΠΈΡΠΎ-Π²Π°ΡΡ ΡΠ°Π±Π»ΠΎΠ½. ΠΠΎΠ½Π΅Ρ ΠΏΡΡΡΠΊΠ° Π·Π°Π³ΠΈΠ±Π°ΡΡ Π½Π°Β ΡΠ³ΠΎΠ» 90Β°. ΠΒ Π½Π°Π³ΡΠ΅ΡΠΎΠΌ ΡΠΎΡΡΠΎΡΠ½ΠΈΠΈ Π·Π°ΠΊΡΠ΅ΠΏΠ»ΡΡΡ Π²Β ΡΠΈΡΠΊΠ°Ρ ΠΈΒ ΠΎΠ³ΠΈΠ±Π°ΡΡ Π½Π°Β ΡΠ΅Π±Ρ. ΠΡΠΈ Π΄ΠΎΡΡΠ°ΡΠΎΡΠ½ΠΎΠΌ ΠΊΠΎΠ»ΠΈΡΠ΅ΡΡΠ²Π΅ Π²ΠΈΡΠΊΠΎΠ² ΡΠΏΠΈΡΠ°Π»Ρ Π½Π°Π³ΡΠ΅Π²Π°ΡΡ ΠΈΒ Π·Π°Β ΠΊΠΎΠ½Π΅Ρ, ΠΊΠΎΡΠΎΡΡΠΉ ΡΠ²Π»ΡΠ΅ΡΡΡ Π²Π΅ΡΡΠΈΠ½ΠΎΠΉ Π±ΡΠ΄ΡΡΠ΅ΠΉ ΠΊΠΎΠ½ΡΡΠ½ΠΎΠΉ ΡΠΏΠΈΡΠ°Π»ΠΈ, Π²ΡΡΡΠ³ΠΈΠ²Π°ΡΡ. Π‘ΡΡΠ½ΠΎΡΡΡ ΡΡΠΎΠΉ ΠΎΠΏΠ΅ΡΠ°ΡΠΈΠΈ Π·Π°ΠΊΠ»ΡΡΠ°Π΅ΡΡΡ Π²Β ΡΠΎΠΌ, ΡΡΠΎΒ ΠΎΠ΄Π½Ρ ΡΠ°ΡΡΡ ΠΏΠΎΠΊΠΎΠ²ΠΊΠΈ ΠΏΠΎΠ²ΠΎ-ΡΠ°ΡΠΈΠ²Π°ΡΡ ΠΏΠΎΒ ΠΎΡΠ½ΠΎΡΠ΅Π½ΠΈΡ ΠΊΒ Π΄ΡΡΠ³ΠΎΠΉ Π²ΠΎΠΊΡΡΠ³ ΠΎΠ±ΡΠ΅ΠΉ ΠΎΡΠΈ. Π Π°Π·Π»ΠΈΡΠ°ΡΡΡΡ Π΄Π²Π°Β Π²Π°ΡΠΈΠ°Π½ΡΠ°.
Π‘ΠΊΡΡΡΠΈΠ²Π°Π½ΠΈΠ΅ ΡΠΎΠ½ΠΊΠΈΡ Π·Π°Π³ΠΎΡΠΎΠ²ΠΎΠΊ ΠΏΡΠΎΠΈΠ·Π²ΠΎΠ΄ΡΡ Π΄Π²Π°Β ΠΊΡΠ·Π½Π΅ΡΠ°. ΠΠ°Ρ Π²Π°ΡΠΈΠ² Π·Π°Π³ΠΎΡΠΎΠ²ΠΊΡ ΠΊΠ»Π΅ΡΠ°ΠΌΠΈ, ΠΎΠ½ΠΈΒ Π²ΡΠ°ΡΠ°ΡΡ Π΅Π΅Β Π²Β Π΄Π²ΡΡ ΠΏΡΠΎΡΠΈΠ²ΠΎΠΏΠΎΠ»ΠΎΠΆΠ½ΡΡ Π½Π°ΠΏΡΠ°Π²Π»Π΅Π½ΠΈΡΡ ΠΎΠ΄Π½ΠΎΠ²ΡΠ΅ΠΌΠ΅Π½Π½ΠΎ. Π‘ΠΊΡΡΡΠΈΠ²Π°Π½ΠΈΠ΅ Π±ΠΎΠ»Π΅Π΅ ΡΠΎΠ»-ΡΡΡΡ ΠΏΠΎΠΊΠΎΠ²ΠΎΠΊ ΠΏΡΠΎΠΈΠ·Π²ΠΎΠ΄ΡΡ ΠΏΠΎΡΡΠ΅Π΄ΡΡΠ²ΠΎΠΌ Π²ΠΎΡΠΎΡΠΊΠ°, ΠΏΡΠΈΒ ΡΡΠΎΠΌ Π΄ΡΡΠ³ΠΎΠΉ ΠΊΠΎΠ½Π΅Ρ Π·Π°Π³ΠΎΡΠΎΠ²ΠΊΠΈ Π·Π°ΠΆΠΈΠΌΠ°ΡΡ Π²Β ΡΠΈΡΠΊΠΈ. Π¨ΠΈΡΠΎΠΊΠΈΠ΅ ΠΏΠΎΠ»ΠΎΡΡ ΡΠ΄ΠΎΠ±Π½ΠΎ Π·Π°Ρ Π²Π°ΡΡΠ²Π°ΡΡ ΡΒ ΠΏΠΎΠΌΠΎΡΡΡ Π²ΠΈΠ»ΠΊΠΈ. ΠΠ°ΠΈΠ±ΠΎΠ»Π΅Π΅ ΠΊΡΠ°ΡΠΈΠ²ΡΠ΅ Π΄Π΅ΠΊΠΎΡΠ°ΡΠΈΠ²Π½ΡΠ΅ ΡΠ»Π΅-ΠΌΠ΅Π½ΡΡ, Π±ΠΎΠ³Π°ΡΡΠ΅ ΡΠ²Π΅ΡΠΎΡΠ΅Π½ΡΡ, ΠΏΠΎΠ»ΡΡΠ°ΡΡ ΠΈΠ·Β Π΄Π²ΡΡ ΠΊΡΡΠ³Π»ΡΡ ΠΏΡΡΡΠΊΠΎΠ², ΡΡΠ³ΠΎ ΡΠ²ΠΈΡΡΡ ΠΌΠ΅ΠΆΠ΄Ρ ΡΠΎΠ±ΠΎΠΉ. ΠΡΠΈΒ ΡΠΊΡΡΡΠΈΠ²Π°Π½ΠΈΠΈ ΠΈΒ ΡΠ²ΠΈΠ²Π°Π½ΠΈΠΈ Π·Π°Π³ΠΎΡΠΎΠ²ΠΊΠ° Π΄ΠΎΠ»ΠΆΠ½Π° Π±ΡΡΡ Π½Π°Π³ΡΠ΅ΡΠ° Π΄ΠΎΒ ΡΡΠΊΠΎ-ΠΊΡΠ°ΡΠ½ΠΎΠ³ΠΎ ΠΊΠ°Π»Π΅Π½ΠΈΡ; ΠΏΡΠΈΒ Π±ΠΎΠ»Π΅Π΅ Π½ΠΈΠ·-ΠΊΠΎΠΉ ΡΠ΅ΠΌΠΏΠ΅ΡΠ°ΡΡΡΠ΅ ΡΠΊΡΡΡΠΈΠ²Π°Π½ΠΈΠ΅ ΡΡΠ΅Π±ΡΠ΅Ρ Π±ΠΎΠ»ΡΡΠΈΡ ΡΡΠΈΠ»ΠΈΠΉ, Π°Β Π²Β ΠΌΠ΅ΡΠ°Π»Π»Π΅ ΠΌΠΎΠ³ΡΡ Π²ΠΎΠ·Π½ΠΈΠΊΠ½ΡΡΡ ΡΡΠ΅ΡΠΈΠ½Ρ. Π ΡΡΠΎΠΉ ΠΎΠΏΠ΅ΡΠ°ΡΠΈΠΈ ΠΏΡΠΈΡΡΡΠΏΠ°ΡΡ ΠΏΠΎΡΠ»Π΅ ΡΠΎΠ³ΠΎ, ΠΊΠ°ΠΊΒ ΠΎΡΠ½ΠΎΠ²Π½Π°Ρ ΡΠΎΡΠΌΠ° ΠΈΠ·Π΄Π΅Π»ΠΈΡ ΡΠΆΠ΅Β ΠΎΡΠΊΠΎΠ²Π°Π½Π°. Π¦Π΅Π»Ρ ΠΎΠΏΠ΅ΡΠ°ΡΠΈΠΈ: ΠΏΡΠΈΠ΄Π°ΡΡ Π·Π°ΠΊΠΎΠ½ΡΠ΅Π½Π½ΡΠΉ Π²ΠΈΠ΄Β ΠΏΠΎΠΊΠΎΠ²ΠΊΠ΅. ΠΠΎΡΠ»Π΅ ΠΌΠΎΠ»ΠΎΡΠΊΠ° Π²ΡΠ΅Π³Π΄Π° ΠΎΡΡΠ°ΡΡΡΡ ΡΠ»Π΅Π΄Ρ? Π²ΠΎΠ»Π½ΠΈΡΡΠΎΡΡΡ. ΠΡΠΎΠΌΠ΅ ΡΠΎΠ³ΠΎ, ΠΈΠ·Π΄Π΅Π»ΠΈΠ΅ ΠΈΠ·-ΠΏΠΎΠ΄ ΠΌΠΎΠ»ΠΎΡΠΊΠ° (ΠΎΡΠΎΠ±Π΅Π½Π½ΠΎ ΡΠΎΒ ΡΠ»Π΅Π΄Π°ΠΌΠΈ ΠΊΡΠ²Π°Π»Π΄Ρ) ΠΈΠΌΠ΅Π΅Ρ Π½Π΅ΡΡΡΠ»ΠΈΠ²ΡΠΉ ΠΈΒ Π½Π΅Π·Π°ΠΊΠΎΠ½ΡΠ΅Π½Π½ΡΠΉ Π²ΠΈΠ΄. ΠΡΠ³Π»Π°ΠΆΠΈΠ²Π°Π½ΠΈΠ΅ ΠΈΒ ΠΎΠΊΠΎΠ½ΡΠ°ΡΠ΅Π»ΡΠ½Π°Ρ ΠΎΡΠ΄Π΅Π»ΠΊΠ° Π·Π°ΠΊΠ»ΡΡΠ°ΡΡΡΡ Π²Β Π²ΡΡΠ°Π²Π½ΠΈΠ²Π°Π½ΠΈΠΈ ΠΏΠΎΠ²Π΅ΡΡ Π½ΠΎΡΡΠΈ ΡΒ ΠΏΠΎΠΌΠΎΡΡΡ Π³Π»Π°Π΄ΠΈΠ»ΠΎΠΊ ΡΠ°Π·Π»ΠΈΡ-Π½ΡΡ ΡΠΎΡΠΌ. ΠΡΠ³Π»Π°ΠΆΠΈΠ²Π°Π½ΠΈΠ΅ Π²Π΅Π΄ΡΡ ΠΏΡΠΈΒ ΡΠ΅ΠΌΠ½ΠΎ-ΠΊΡΠ°ΡΠ½ΠΎΠΌ Π½Π°Π³ΡΠ΅Π²Π΅ Π·Π°Π³ΠΎΡΠΎΠ²ΠΊΠΈ, ΠΏΠ΅ΡΠ΅ΠΌΠ΅ΡΠ°Ρ Π³Π»Π°Π΄ΠΈΠ»ΠΊΡ ΠΏΠΎΒ ΠΏΠΎ-Π²Π΅ΡΡ Π½ΠΎΡΡΠΈ ΠΈΠ·Π΄Π΅Π»ΠΈΡ ΠΈΒ ΡΠ΄Π°ΡΡΡ ΠΏΠΎΒ Π½Π΅ΠΉΒ ΠΊΡΠ²Π°Π»Π΄ΠΎΠΉ. ΠΠ½ΠΎΠ³Π΄Π° Π²ΡΠ³Π»Π°ΠΆΠΈΠ²Π°ΡΡ ΡΠΎΠ»ΡΠΊΠΎ ΠΎΡΠ΄Π΅Π»ΡΠ½ΡΠ΅ ΡΡΠ°ΡΡΠΊΠΈ ΡΠ΅Π»ΡΠ΅ΡΠ°. ΠΠ°ΠΏΡΠΈΠΌΠ΅Ρ, ΡΠΎΠ»ΡΠΊΠΎ Π΅Π³ΠΎΒ Π½Π°ΠΈΠ±ΠΎΠ»Π΅Π΅ Π²ΡΡΡΡ-ΠΏΠ°ΡΡΠΈΠ΅ ΡΠ°ΡΡΠΈ, Π°Β ΡΠ³Π»ΡΠ±Π»Π΅Π½ΠΈΠ΅ ΡΠΎΡΡΠ°Π²Π»ΡΡΡ Β«ΠΈΠ·-ΠΏΠΎΠ΄ ΠΌΠΎΠ»ΠΎΡΠΊΠ°Β». ΠΡΠΎΒ ΠΏΡΠΈΠ΄Π°Π΅Ρ ΡΠ²ΠΎΠ΅ΠΎΠ±ΡΠ°Π·Π½ΡΡ ΠΆΠΈΠ²ΠΎΠΏΠΈΡ-Π½ΠΎΡΡΡ ΠΈΠ·Π΄Π΅Π»ΠΈΡ. ΠΠΏΠ΅ΡΠ°ΡΠΈΡ Π²ΡΠ³Π»Π°ΠΆΠΈΠ²Π°Π½ΠΈΡ ΠΈΠ³ΡΠ°Π΅Ρ Π±ΠΎΠ»ΡΡΡΡ ΡΠΎΠ»Ρ Π²Β Ρ ΡΠ΄ΠΎΠΆΠ΅ΡΡΠ²Π΅Π½Π½ΠΎΠΉ ΠΊΠΎΠ²ΠΊΠ΅, ΠΎΠ½Π°Β ΠΏΡΠΈΠ΄Π°Π΅Ρ ΠΈΠ·Π΄Π΅Π»ΠΈΡ Π·Π°ΠΊΠΎΠ½ΡΠ΅Π½Π½ΡΠΉ Π²ΠΈΠ΄. ΠΠ°ΡΠ΅ΠΊΠ°Π½ΠΈΠ΅ ΡΠΈΡΡΠ½ΠΊΠ°. ΠΡΠ°Β ΠΎΠΏΠ΅ΡΠ°ΡΠΈΡ, ΠΊΠ°ΠΊΒ ΠΈΒ ΠΏΡΠ΅Π΄ΡΠ΄ΡΡΠΈΠ΅, ΠΎΡΠ½ΠΎΡΠΈΡΡΡ ΠΊΒ ΠΎΡΠ΄Π΅Π»ΠΎΡΠ½ΡΠΌ, Π·Π°ΠΊΠ»Ρ-ΡΠΈΡΠ΅Π»ΡΠ½ΡΠΌ Π²ΠΈΠ΄Π°ΠΌ ΠΊΠΎΠ²ΠΊΠΈ. Π‘ ΠΏΠΎΠΌΠΎΡΡΡ Π·ΡΠ±ΠΈΠ»Π° Π²Β Ρ ΠΎΠ»ΠΎΠ΄Π½ΠΎΠΌΒ ΠΈΠ»ΠΈ Π³ΠΎΡΡΡΠ΅ΠΌ ΡΠΎΡΡΠΎΡΠ½ΠΈΠΈ ΠΌΠΎΠΆΠ½ΠΎ Π²ΠΎΡΠΏΡΠΎΠΈΠ·Π²Π΅ΡΡΠΈ Π½Π°Β ΠΏΠΎΠ²Π΅ΡΡ Π½ΠΎΡΡΠΈ ΠΈΠ·Π΄Π΅-Π»ΠΈΡ ΡΠ°Π·Π»ΠΈΡΠ½ΡΠ΅ ΡΡΡΠΈΡ ΠΈ, Π½Π°ΡΠ΅ΡΠΊΠΈΒ ΠΈΠ»ΠΈ Π±ΠΎΠ»Π΅Π΅ ΡΠ»ΠΎΠΆΠ½ΡΠ΅ ΡΠ·ΠΎΡΡ, Π²ΠΊΠ»ΡΡΠ°Ρ ΠΈΠ·ΠΎΠ±ΡΠ°Π·ΠΈΡΠ΅Π»ΡΠ½ΡΠ΅ ΡΠ»Π΅ΠΌΠ΅Π½ΡΡ ΠΈΒ ΡΡΠΈΡΡΠΎΠ²ΡΠ΅ Π½Π°Π΄ΠΏΠΈΡΠΈ. ΠΠ°ΡΠ΅ΠΊΠ°Π½ΠΈΠ΅ ΠΏΡΠΎΠΈΠ·Π²ΠΎΠ΄ΡΡ Π½Π°Β ΠΏΠΎΠ²Π΅ΡΡ Π½ΠΎΡΡΡΡ , Π±ΠΎΠ»Π΅Π΅Β ΠΈΠ»ΠΈ ΠΌΠ΅Π½Π΅Π΅ ΠΏΠ»ΠΎΡΠΊΠΈΡ ΠΈΒ Ρ ΠΎΡΠΎΡΠΎ Π²ΠΈΠ΄Π½ΡΡ Π½Π°Β Π³ΠΎΡΠΎΠ²ΠΎΠΌ ΠΈΠ·Π΄Π΅Π»ΠΈΠΈ. ΠΡΠ° ΠΎΠΏΠ΅ΡΠ°ΡΠΈΡ ΡΠ°ΠΊΠΆΠ΅ ΠΎΡΠ½ΠΎΡΠΈΡΡΡ ΠΊΒ ΠΎΡΠ΄Π΅Π»ΠΊΠ΅ Π³ΠΎΡΠΎΠ²ΠΎΠ³ΠΎ ΠΈΠ·Π΄Π΅Π»ΠΈΡ ΠΈΒ Π²ΡΠΏΠΎΠ»Π½ΡΠ΅ΡΡΡ ΡΒ ΡΠ΅Π»ΡΡ ΠΎΠ±ΠΎΠ³Π°ΡΠ΅Π½ΠΈΡ Π΅Π³ΠΎΒ ΡΠ°ΠΊΡΡΡΡ ΠΏΡΡΠ΅ΠΌ ΡΠΎΠ·Π΄Π°Π½ΠΈΡ Π΄ΠΎΠΏΠΎΠ»Π½ΠΈΡΠ΅Π»ΡΠ½ΡΡ ΡΠ΅Π»ΡΠ΅ΡΠ½ΡΡ Π²Ρ-ΡΡΡΠΏΠΎΠ²Β ΠΈΠ»ΠΈ ΠΊΠ°Π½Π°Π²ΠΎΠΊ ΠΈΒ ΡΠ³Π»ΡΠ±Π»Π΅Π½ΠΈΠΉ, Π½Π°ΠΏΡΠΈΠΌΠ΅Ρ ΠΆΠΈΠ»ΠΎΠΊ Π½Π°Β Π»ΠΈΡΡΡΡΡ ΠΈΒ Π»Π΅ΠΏΠ΅ΡΡΠΊΠ°Ρ , ΠΊΠ°Π½Π΅Π»ΡΡ Π½Π°Β ΠΊΠΎΠ»ΠΎΠ½Π½Π°Ρ ΠΈΒ Ρ. ΠΏ. Π Π°Π±ΠΎΡΡ Π²ΡΠΏΠΎΠ»Π½ΡΡΡ ΡΠΏΠ΅ΡΠΈΠ°Π»ΡΠ½ΡΠΌΠΈ ΠΏΠΎΠ΄Π±ΠΎΠΉΠΊΠ°ΠΌΠΈΒ ΠΈΠ»ΠΈ ΠΏΡΠ°Π½ΡΠΎΠ½Π°ΠΌΠΈ. Β ΠΡΠ·Π½Π΅ΡΠ½ΡΠ΅ ΡΠ°Π±ΠΎΡΡ ΠΎΡΠ½ΠΎΡΡΡΡΡ ΠΊΒ ΡΠ°Π±ΠΎΡΠ°ΠΌ ΠΏΠΎΠ²ΡΡΠ΅Π½Π½ΠΎΠΉ ΠΎΠΏΠ°ΡΠ½ΠΎΡΡΠΈ, ΠΏΠΎΡΡΠΎΠΌΡ Π±ΠΎΠ»ΡΡΠΎΠ΅ Π²Π½ΠΈΠΌΠ°Π½ΠΈΠ΅ Π΄ΠΎΠ»ΠΆΠ½ΠΎ ΡΠ΄Π΅Π»ΡΡΡΡΡ ΠΊΠ°ΡΠ΅ΡΡΠ²Ρ ΡΡΡΠ½ΠΎΠ³ΠΎ ΠΈΒ ΠΏΠΎΠ΄ΠΊΠ»Π°Π΄Π½ΠΎΠ³ΠΎ ΠΈΠ½ΡΡΡΡΠΌΠ΅Π½ΡΠ°, ΠΎΠ΄Π΅ΠΆΠ΄Π΅ ΠΈΒ ΠΈΠ½Π΄ΠΈΠ²ΠΈΠ΄ΡΠ°Π»ΡΠ½ΡΠΌ ΡΡΠ΅Π΄ΡΡΠ²Π°ΠΌ Π·Π°ΡΠΈΡΡβ¦ ΠΠΎΠ΄ΡΠΎΠ±Π½Π΅Π΅ Π² ΡΡΠ°ΡΡΠ΅ «Π’Π΅Ρ
Π½ΠΈΠΊΠ° Π±Π΅Π·ΠΎΠΏΠ°ΡΠ½ΠΎΡΡΠΈ ΠΏΡΠΈ ΠΊΡΠ·Π½Π΅ΡΠ½ΡΡ
ΡΠ°Π±ΠΎΡΠ°Ρ
» |
Π’Π΅Ρ Π½ΠΎΠ»ΠΎΠ³ΠΈΡ ΠΊΠΎΠ²ΠΊΠΈ
Π‘Π°Π½ΠΊΡ-ΠΠ΅ΡΠ΅ΡΠ±ΡΡΠ³ΡΠΊΠΈΠΉΒ
Π³ΠΎΡΡΠ΄Π°ΡΡΡΠ²Π΅Π½Π½ΡΠΉ ΠΏΠΎΠ»ΠΈΡΠ΅Ρ
Π½ΠΈΡΠ΅ΡΠΊΠΈΠΉ ΡΠ½ΠΈΠ²Π΅ΡΡΠΈΡΠ΅Ρ
Β
Β
Β
ΠΠ°ΡΠ΅Π΄ΡΠ°
Π’Π΅Ρ
Π½ΠΎΠ»ΠΎΠ³ΠΈΡΒ ΠΊΠΎΠ½ΡΡΡΡΠΊΡΠΈΠΎΠ½Π½ΡΡ
Β Β
ΠΌΠ°ΡΠ΅ΡΠΈΠ°Π»ΠΎΠ²
Β
Β
Β
Β
Β
Β
Β
Β
Β
Β
ΠΡΡΠ΅Ρ
ΠΏΠΎΒ Π»Π°Π±ΠΎΡΠ°ΡΠΎΡΠ½ΠΎΠΉ ΡΠ°Π±ΠΎΡΠ΅ βΒ 4
Π’Π΅Ρ Π½ΠΎΠ»ΠΎΠ³ΠΈΡΒ ΠΊΠΎΠ²ΠΊΠΈ
Β
Β
Β
Β
Β
Β
Β
Β
Β
Β
Β
Β
Β
Β
ΠΡΠΏΠΎΠ»Π½ΠΈΠ»Β ΡΡΡΠ΄Π΅Π½ΡΒ Π³Ρ. β 1037/1
ΠΡΠΈΠ½ΡΠ»Π°:
ΠΡΡΠΏΠΊΠΈΠ½Π° Π.Π.
Β
2011 Π³.
Β
Π¦Π΅Π»ΡΒ ΡΠ°Π±ΠΎΡΡ: Π·Π½Π°Π½ΠΈΠ΅ ΠΎΡΠ½ΠΎΠ²Π½ΡΡ ΠΎΠΏΠ΅ΡΠ°ΡΠΈΠΉ ΠΊΠΎΠ²ΠΊΠΈ ΠΈ ΠΎΠ±Π»Π°ΡΡΠΈ ΠΈΡ ΠΏΡΠΈΠΌΠ΅Π½Π΅Π½ΠΈΡ; ΡΠΌΠ΅Π½ΠΈΠ΅ Π²ΡΠΏΠΎΠ»Π½ΡΡΡ ΡΠ΅Ρ Π½ΠΎΠ»ΠΎΠ³ΠΈΡΠ΅ΡΠΊΠΈΠ΅ ΡΠ°ΡΡΠ΅ΡΡ ΠΈ ΠΏΡΠ°Π²ΠΈΠ»ΡΠ½ΠΎ Π²ΡΠ±ΠΈΡΠ°ΡΡ ΠΏΠΎΡΠ»Π΅Π΄ΠΎΠ²Π°ΡΠ΅Π»ΡΠ½ΠΎΡΡΡ ΠΎΡΠ½ΠΎΠ²Π½ΡΡ ΠΎΠΏΠ΅ΡΠ°ΡΠΈΠΉ; Π½Π°Π²ΡΠΊΠΈ Π²ΡΠΏΠΎΠ»Π½Π΅Π½ΠΈΡ ΠΎΠΏΠ΅ΡΠ°ΡΠΈΠΉ ΠΈ ΠΏΡΠΈΠ΅ΠΌΠΎΠ² ΠΊΠΎΠ²ΠΊΠΈ.
ΠΠΎΠ²ΠΊΠ° β ΡΡΠΎ ΠΏΡΠΎΡΠ΅ΡΡ Π³ΠΎΡΡΡΠ΅Π³ΠΎ ΠΏΠ»Π°ΡΡΠΈΡΠ΅ΡΠΊΠΎΠ³ΠΎ Π΄Π΅ΡΠΎΡΠΌΠΈΡΠΎΠ²Π°Π½ΠΈΡ ΠΏΡΡΠ΅ΠΌ ΠΌΠ½ΠΎΠ³ΠΎΠΊΡΠ°ΡΠ½ΠΎΠ³ΠΎ Π²ΠΎΠ·Π΄Π΅ΠΉΡΡΠ²ΠΈΡ Π½Π° ΠΎΡΠ΄Π΅Π»ΡΠ½ΡΠ΅ ΡΠ°ΡΡΠΈ ΠΈΡΡ ΠΎΠ΄Π½ΠΎΠΉ Π·Π°Π³ΠΎΡΠΎΠ²ΠΊΠΈ ΡΠ½ΠΈΠ²Π΅ΡΡΠ°Π»ΡΠ½ΡΠΌ ΠΈΠ½ΡΡΡΡΠΌΠ΅Π½ΡΠΎΠΌ ΠΏΡΠΎΡΡΠΎΠΉ ΡΠΎΡΠΌΡ ΠΏΡΠΈ ΡΠ²ΠΎΠ±ΠΎΠ΄Π½ΠΎΠΌ ΡΠ΅ΡΠ΅Π½ΠΈΠΈ ΠΌΠ΅ΡΠ°Π»Π»Π° Π² ΡΡΠΎΡΠΎΠ½Ρ.
ΠΡΠΈΠΌΠ΅Π½ΡΡΡ ΠΊΠΎΠ²ΠΊΡΒ Π²Β ΠΈΠ½Π΄ΠΈΠ²ΠΈΠ΄ΡΠ°Π»ΡΠ½ΠΎΠΌ ΠΈΒ ΠΌΠ΅Π»ΠΊΠΎΡΠ΅ΡΠΈΠΉΠ½ΠΎΠΌΒ ΠΏΡΠΎΠΈΠ·Π²ΠΎΠ΄ΡΡΠ²Π΅. ΠΠΎΠ²Π°Π½ΡΠ΅Β ΠΈΠ·Π΄Π΅Π»ΠΈΡ (ΠΏΠΎΠΊΠΎΠ²ΠΊΠΈ) ΠΌΠΎΠ³ΡΡΒ ΠΈΠΌΠ΅ΡΡΒ ΠΌΠ°ΡΡΡ ΠΎΡ Π½Π΅ΡΠΊΠΎΠ»ΡΠΊΠΈΡ ΠΊΠΈΠ»ΠΎΠ³ΡΠ°ΠΌΠΌΠΎΠ² Π΄ΠΎ 500 Ρ.
ΠΡΠ·Π½Π΅ΡΠ½ΡΠ΅ ΡΠ΅Ρ ΠΈ Π΄Π»ΡΒ ΠΎΡΡΡΠ΅ΡΡΠ²Π»Π΅Π½ΠΈΡΒ ΠΊΠΎΠ²ΠΊΠΈΒ ΠΈΠΌΠ΅ΡΡΒ Π½Π°Π³ΡΠ΅Π²Π°ΡΠ΅Π»ΡΠ½ΠΎΠ΅ ΠΎΠ±ΠΎΡΡΠ΄ΠΎΠ²Π°Π½ΠΈΠ΅ (Π³Π°Π·ΠΎΠ²ΡΠ΅ ΠΈΠ»ΠΈ ΡΠ»Π΅ΠΊΡΡΠΈΡΠ΅ΡΠΊΠΈΠ΅ ΠΏΠ΅ΡΠΈ), Π΄Π΅ΡΠΎΡΠΌΠΈΡΡΡΡΠ΅Π΅ ΠΎΠ±ΠΎΡΡΠ΄ΠΎΠ²Π°Π½ΠΈΠ΅ (ΠΏΠ°ΡΠΎΠ²ΠΎΠ·Π΄ΡΡΠ½ΡΠ΅ ΠΌΠΎΠ»ΠΎΡΡ, Π³ΠΈΠ΄ΡΠ°Π²Π»ΠΈΡΠ΅ΡΠΊΠΈΠ΅ ΠΏΡΠ΅ΡΡΡ) ΠΈ Π²ΡΠΏΠΎΠΌΠΎΠ³Π°ΡΠ΅Π»ΡΠ½ΠΎΠ΅ ΠΎΠ±ΠΎΡΡΠ΄ΠΎΠ²Π°Π½ΠΈΠ΅ (ΠΌΠ°Π½ΠΈΠΏΡΠ»ΡΡΠΎΡΡ, ΠΌΠΎΡΡΠΎΠ²ΡΠ΅ ΠΊΡΠ°Π½Ρ, ΡΡΠ°Π½ΡΠΏΠΎΡΡΠ½ΡΠ΅ ΡΠ΅Π»Π΅ΠΆΠΊΠΈ, ΠΊΠ°Π½ΡΠΎΠ²Π°ΡΠ΅Π»ΠΈ).
Π’ΠΈΠΏΠΎΠ²ΡΠ΅ ΠΏΠΎΠΊΠΎΠ²ΠΊΠΈ: Π²Π°Π»Ρ Π³Π»Π°Π΄ΠΊΠΈΠ΅ ΠΈ ΡΡΡΠΏΠ΅Π½ΡΠ°ΡΡΠ΅, ΠΊΠΎΠ»Π΅Π½ΡΠ°ΡΡΠ΅ Π²Π°Π»Ρ, ΠΊΠΎΠ»ΡΡΠ°, ΠΏΠ»Π°ΡΡΠΈΠ½Ρ, ΠΏΠ°ΡΠ°Π»Π»Π΅Π»Π΅ΠΏΠΈΠΏΠ΅Π΄Ρ, Π΄ΠΈΡΠΊΠΈ, ΠΏΡΡΡΠΎΡΠ΅Π»ΡΠ΅ ΡΡΡΠ±ΡΠ°ΡΡΠ΅ ΠΈΠ·Π΄Π΅Π»ΠΈΡ ΠΈ Ρ. ΠΏ.
ΠΡΠ½ΠΎΠ²Π½ΡΠΌΠΈ ΠΎΠΏΠ΅ΡΠ°ΡΠΈΡΠΌΠΈ ΠΊΠΎΠ²ΠΊΠΈΒ Π½Π° ΠΏΡΠ΅ΡΡΠ°Ρ Β ΠΈΒ ΠΌΠΎΠ»ΠΎΡΠ°Ρ Β ΡΠ²Π»ΡΡΡΡΡ ΠΎΡΠ°Π΄ΠΊΠ°, ΠΏΡΠΎΡΡΠΆΠΊΠ°, ΠΏΡΠΎΡΡΠΆΠΊΠ° Π½Π° ΠΎΠΏΡΠ°Π²ΠΊΠ΅, ΡΠ°ΡΠΊΠ°ΡΠΊΠ° Π½Π° ΠΎΠΏΡΠ°Π²ΠΊΠ΅ ΠΈ ΠΏΡΠΎΡΠΈΠ²ΠΊΠ° ΠΎΡΠ²Π΅ΡΡΡΠΈΠΉ.
ΠΡΠ°Π΄ΠΊΠ°Β ΡΠ»ΡΠΆΠΈΡ Π΄Π»Ρ ΠΏΠΎΠ»ΡΡΠ΅Π½ΠΈΡ ΠΊΡΡΠ³Π»ΡΡ ΠΈΠ»ΠΈ Π±Π»ΠΈΠ·ΠΊΠΈΡ ΠΊ Π½ΠΈΠΌ ΠΏΠΎ ΡΠΎΡΠΌΠ΅ ΠΏΠΎΠΊΠΎΠ²ΠΎΠΊ ΡΠΈΠΏΠ° Π΄ΠΈΡΠΊΠΎΠ², ΡΠ΅ΡΡΠ΅ΡΠ΅Π½, ΡΠ»Π°Π½ΡΠ΅Π² ΠΏΡΡΠ΅ΠΌ ΡΠΌΠ΅Π½ΡΡΠ΅Π½ΠΈΡ Π²ΡΡΠΎΡΡ Π·Π°Π³ΠΎΡΠΎΠ²ΠΊΠΈ ΠΈ ΡΠ²Π΅Π»ΠΈΡΠ΅Π½ΠΈΡ Π΅Π΅ ΠΏΠΎΠΏΠ΅ΡΠ΅ΡΠ½ΡΡ ΡΠ°Π·ΠΌΠ΅ΡΠΎΠ² (ΡΠΈΡ. 1, Π°). ΠΠ»Ρ ΠΏΠΎΠ»ΡΡΠ΅Π½ΠΈΡ ΡΡΡΠΏΠ΅Π½ΡΠ°ΡΡΡ ΠΏΠΎΠΊΠΎΠ²ΠΎΠΊ ΠΈΠ»ΠΈ ΠΏΡΠ΅Π΄Π²Π°ΡΠΈΡΠ΅Π»ΡΠ½ΠΎΠΉ ΠΎΡΠ°Π΄ΠΊΠΈ ΡΠ»ΠΈΡΠΊΠ° ΠΏΡΠΈΠΌΠ΅Π½ΡΡΡ ΠΏΠΎΠ΄ΠΊΠ»Π°Π΄Π½ΠΎΠ΅ ΠΊΠΎΠ»ΡΡΠΎ (ΡΠΈΡ. 1, Π±).
ΠΡΠΎΡΡΠΆΠΊΠ°Β (ΡΠΈΡ. 2, Π°) Π·Π°ΠΊΠ»ΡΡΠ°Π΅ΡΡΡ Π² ΡΠ²Π΅Π»ΠΈΡΠ΅Π½ΠΈΠΈ Π΄Π»ΠΈΠ½Ρ Π·Π°Π³ΠΎΡΠΎΠ²ΠΊΠΈ ΠΏΡΡΠ΅ΠΌ ΡΡΠ΄Π° ΠΏΠΎΡΠ»Π΅Π΄ΠΎΠ²Π°ΡΠ΅Π»ΡΠ½ΡΡ ΠΎΠ±ΠΆΠ°ΡΠΈΠΉ Π±ΠΎΠΉΠΊΠ°ΠΌΠΈ Ρ ΠΏΠ΅ΡΠ΅ΠΌΠ΅ΡΠ΅Π½ΠΈΠ΅ΠΌ Π·Π°Π³ΠΎΡΠΎΠ²ΠΊΠΈ Π²Π΄ΠΎΠ»Ρ ΠΎΡΠΈ. ΠΡΠΈ ΡΡΠΎΠΌ ΡΠΌΠ΅Π½ΡΡΠ°Π΅ΡΡΡ ΡΠΎΠ»ΡΠΈΠ½Π° Π·Π°Π³ΠΎΡΠΎΠ²ΠΊΠΈ, ΡΠ²Π΅Π»ΠΈΡΠΈΠ²Π°Π΅ΡΡΡ Π΄Π»ΠΈΠ½Π° ΠΏΡΠΈ Π½Π΅ΠΊΠΎΡΠΎΡΠΎΠΌ ΡΡΠΈΡΠ΅Π½ΠΈΠΈ.
ΠΡΠΎΡΡΠΆΠΊΡΒ Π½Π° ΠΎΠΏΡΠ°Π²ΠΊΠ΅Β (ΡΠΈΡ. 2, Π±) ΠΏΡΠΈΠΌΠ΅Π½ΡΡΡ Π΄Π»Ρ Π΄Π»ΠΈΠ½Π½ΡΡ ΠΏΡΡΡΠΎΡΠ΅Π»ΡΡ ΠΏΠΎΠΊΠΎΠ²ΠΎΠΊ ΡΠΈΠΏΠ° ΠΏΡΡΡΠΎΡΠ΅Π»ΡΡ ΠΊΠΎΠ»ΠΎΠ½Π½, ΠΊΡΡΠΏΠ½ΡΡ ΠΎΡΡΠ΄ΠΈΠΉΠ½ΡΡ ΡΡΠ²ΠΎΠ»ΠΎΠ². ΠΠ΅ΡΠΎΡΠΌΠΈΡΠΎΠ²Π°Π½ΠΈΠ΅ ΠΈΡΡ ΠΎΠ΄Π½ΠΎΠΉ Π·Π°Π³ΠΎΡΠΎΠ²ΠΊΠΈ Ρ ΠΎΡΠ²Π΅ΡΡΡΠΈΠ΅ΠΌ, ΠΎΠ΄Π΅ΡΠΎΠΉ Π½Π° ΠΎΠΏΡΠ°Π²ΠΊΡ Ρ Π½Π΅Π±ΠΎΠ»ΡΡΠΎΠΉ ΠΊΠΎΠ½ΡΡΠ½ΠΎΡΡΡΡ, ΡΠΎΠΏΡΠΎΠ²ΠΎΠΆΠ΄Π°Π΅ΡΡΡ ΡΠΌΠ΅Π½ΡΡΠ΅Π½ΠΈΠ΅ΠΌ ΡΠΎΠ»ΡΠΈΠ½Ρ ΡΡΠ΅Π½ΠΊΠΈ ΠΈ ΡΠ²Π΅Π»ΠΈΡΠ΅Π½ΠΈΠ΅ΠΌ Π΄Π»ΠΈΠ½Ρ ΠΏΠΎΠΊΠΎΠ²ΠΊΠΈ.
Π Π°ΡΠΊΠ°ΡΠΊΡΒ Π½Π° ΠΎΠΏΡΠ°Π²ΠΊΠ΅Β ΠΏΡΠΈΠΌΠ΅Π½ΡΡΡ Π΄Π»Ρ ΠΊΠΎΠ»ΡΡΠ΅Π²ΡΡ ΠΏΠΎΠΊΠΎΠ²ΠΎΠΊ; ΠΎΠ½Π° Π·Π°ΠΊΠ»ΡΡΠ°Π΅ΡΡΡ Π² ΠΏΠΎΡΠ»Π΅Π΄ΠΎΠ²Π°ΡΠ΅Π»ΡΠ½ΠΎΠΌ Π΄Π΅ΡΠΎΡΠΌΠΈΡΠΎΠ²Π°Π½ΠΈΠΈ Π·Π°Π³ΠΎΡΠΎΠ²ΠΊΠΈ Ρ ΠΎΡΠ²Π΅ΡΡΡΠΈΠ΅ΠΌ, Π½Π°Π΄Π΅ΡΠΎΠΉ Π½Π° ΠΊΡΡΠ³Π»ΡΡ ΠΎΠΏΡΠ°Π²ΠΊΡ (ΡΠΈΡ. 3)
ΠΡΠΎΡΠΈΠ²ΠΊΡΒ ΠΎΡΠ²Π΅ΡΡΡΠΈΠΉΒ Π² ΠΏΠΎΠΊΠΎΠ²ΠΊΠ°Ρ (ΡΠΈΡ. 4) ΠΈΡΠΏΠΎΠ»ΡΠ·ΡΡΡ Π΄Π»Ρ ΠΏΠΎΠ»ΡΡΠ΅Π½ΠΈΡ ΠΎΡΠ²Π΅ΡΡΡΠΈΠΉ Π² ΡΠΎΠ½ΠΊΠΈΡ Π΄ΠΈΡΠΊΠΎΠ²ΡΡ ΠΏΠΎΠΊΠΎΠ²ΠΊΠ°Ρ ΠΈΠ»ΠΈ ΠΏΡΠΎΠΌΠ΅ΠΆΡΡΠΎΡΠ½ΡΡ Π·Π°Π³ΠΎΡΠΎΠ²ΠΊΠ°Ρ ΠΏΠ΅ΡΠ΅Π΄ ΠΏΡΠΎΡΡΠΆΠΊΠΎΠΉ ΠΈΠ»ΠΈ ΡΠ°ΡΠΊΠ°ΡΠΊΠΎΠΉ Π½Π° ΠΎΠΏΡΠ°Π²-ΠΊΠ΅. ΠΠ½ΡΡΡΡΠΌΠ΅Π½Ρ-ΠΏΡΠΎΡΠΈΠ²Π΅Π½Ρ ΠΈΠΌΠ΅Π΅Ρ ΠΊΠΎΠ½ΡΡΠ½ΠΎΡΡΡ 2-5Β°; ΠΏΡΠΈ Π΅Π³ΠΎ Π²Π΄Π°Π²Π»ΠΈ-Π²Π°Π½ΠΈΠΈ Π² Π·Π°Π³ΠΎΡΠΎΠ²ΠΊΡ ΠΎΠ±ΡΠ°Π·ΡΠ΅ΡΡΡ ΠΏΠΎΠ»ΠΎΡΡΡ Π³Π»ΡΠ±ΠΈΠ½ΠΎΠΉ. ΠΡΡΠ°Π²ΡΡΡΡΡ ΡΠ½ΠΈΠ·Ρ ΡΠ°ΡΡΡ ΠΌΠ΅ΡΠ°Π»Π»Π° (Π²ΡΠ΄ΡΡ) ΡΠ΄Π°Π»ΡΡΡ ΠΏΡΠΎΡΠΈΠ²Π½Π΅ΠΌ ΠΏΠΎΡΠ»Π΅ ΠΏΠ΅ΡΠ΅Π²ΠΎΡΠΎΡΠ° Π·Π°Π³ΠΎΡΠΎΠ²ΠΊΠΈ.
ΠΡΡΡΠ±ΠΊΠ° ΡΠ»ΡΠΆΠΈΡ Π΄Π»Ρ ΠΎΡΠ΄Π΅Π»Π΅Π½ΠΈΡ ΡΠ°ΡΡΠΈ Π·Π°Π³ΠΎΡΠΎΠ²ΠΊΠΈ ΠΈΠ»ΠΈ ΠΎΡΡ ΠΎΠ΄ΠΎΠ² ΠΎΡ ΠΏΠΎΠΊΠΎΠ²ΠΊΠΈ ΠΏΡΡΠ΅ΠΌ Π²Π΄Π°Π²Π»ΠΈΠ²Π°Π½ΠΈΡ ΠΊΠ»ΠΈΠ½ΠΎΠ²ΠΎΠ³ΠΎ ΠΊΡΠ·Π½Π΅ΡΠ½ΠΎΠ³ΠΎ ΡΠΎΠΏΠΎΡΠ° Π±ΠΎΠΉΠΊΠΎΠΌ Ρ ΠΎΠ΄Π½ΠΎΠΉ, Π° Π·Π°ΡΠ΅ΠΌ Ρ Π΄ΡΡΠ³ΠΎΠΉ ΡΡΠΎΡΠΎΠ½Ρ.
ΠΡΠΏΠΎΠΌΠΎΠ³Π°ΡΠ΅Π»ΡΠ½ΡΠΌΠΈΒ ΠΎΠΏΠ΅ΡΠ°ΡΠΈΡΠΌΠΈ ΡΠ²Π»ΡΡΡΡΡ Π±ΠΈΠ»Π»Π΅ΡΠΈΡΠΎΠ²ΠΊΠ°, Π½Π°ΠΌΠ΅ΡΠΊΠ°, ΠΏΠ΅ΡΠ΅ΠΆΠΈΠΌ ΠΈ ΠΏΠ΅ΡΠ΅Π΄Π°ΡΠ°.
ΠΠΈΠ»Π»Π΅ΡΠΈΡΠΎΠ²ΠΊΠ° Π²ΡΠΎΡΠ°Ρ ΠΎΠΏΠ΅ΡΠ°ΡΠΈΡ ΠΏΡΠΈ ΠΊΠΎΠ²ΠΊΠ΅ ΡΠ»ΠΈΡΠΊΠ° ΠΏΠΎΠ΄ ΠΏΡΠ΅ΡΡΠΎΠΌ. ΠΠΈΠ»Π»Π΅ΡΠΈΡΠΎΠ²ΠΊΠΎΠΉ Π½Π°Π·ΡΠ²Π°Π΅ΡΡΡ ΠΎΠ±ΠΊΠ°ΡΠΊΠ° Π³ΡΠ°Π½Π΅ΠΉ ΡΠ»ΠΈΡΠΊΠ°. ΠΠΈΠ»Π»Π΅ΡΠΈΡΠΎΠ²ΠΊΡ ΠΏΡΠΎΠΈΠ·Π²ΠΎΠ΄ΡΡ, Π²ΠΎ-ΠΏΠ΅ΡΠ²ΡΡ , Π΄Π»Ρ ΡΠ½ΠΈΡΡΠΎΠΆΠ΅Π½ΠΈΡ ΠΊΠΎΠ½ΡΡΠ½ΠΎΡΡΠΈ ΡΠ»ΠΈΡΠΊΠ°, Ρ. Π΅. ΠΏΡΠΈΠ΄Π°Π½ΠΈΡ Π΅ΠΌΡ ΡΠΈΠ»ΠΈΠ½Π΄ΡΠΈΡΠ΅ΡΠΊΠΎΠΉ ΡΠΎΡΠΌΡ, Π° Π²ΠΎ-Π²ΡΠΎΡΡΡ , Π΄Π»Ρ Π΄ΠΎΡΡΠΈΠΆΠ΅Π½ΠΈΡ Π±ΠΎΠ»ΡΡΠ΅ΠΉ ΠΏΠ»ΠΎΡΠ½ΠΎΡΡΠΈ ΠΌΠ΅ΡΠ°Π»Π»Π° Π² ΡΠ³Π»Π°Ρ ΡΠ»ΠΈΡΠΊΠ°.
ΠΠ°ΠΌΠ΅ΡΠΊΠ° ΠΈΒ ΠΏΠ΅ΡΠ΅ΠΆΠΈΠΌ ΠΏΡΠΈΠΌΠ΅Π½ΡΡΡΡΡ ΠΏΡΠΈ Π²ΡΡΡΠΆΠΊΠ΅ Ρ ΠΎΠ±ΡΠ°Π·ΠΎΠ²Π°Π½ΠΈΠ΅ΠΌ ΡΡΡΡΠΏΠΎΠ² ΠΈ Π²ΡΠ΅ΠΌΠΎΠΊ. ΠΠ°ΠΌΠ΅ΡΠΊΠΎΠΉ Π½Π° ΠΏΠΎΠ²Π΅ΡΡ Π½ΠΎΡΡΡ Π·Π°Π³ΠΎΡΠΎΠ²ΠΊΠΈ Π½Π°Π½ΠΎΡΡΡ Π½Π°ΠΌΠ΅ΡΠΎΡΠ½ΡΠ΅ ΡΠ³Π»ΡΠ±Π»Π΅Π½ΠΈΡ Π΄Π»Ρ ΡΠ°Π·Π΄Π΅Π»Π΅Π½ΠΈΡ Π΅Π΅ Π½Π° ΠΎΡΠ΄Π΅Π»ΡΠ½ΡΠ΅ ΠΎΡΡΠ΅Π·ΠΊΠΈ ΠΏΠΎ Π²ΡΠ΅ΠΉ Π΄Π»ΠΈΠ½Π΅. ΠΠ°ΠΌΠ΅ΡΠΊΡ ΠΏΡΠΎΠΈΠ·Π²ΠΎΠ΄ΡΡΒ ΡΠ°ΡΠΊΠ°ΡΠΊΠ°ΠΌΠΈ Π½Π΅Π±ΠΎΠ»ΡΡΠΈΡ Π΄ΠΈΠ°ΠΌΠ΅ΡΡΠΎΠ².
ΠΠ΅ΡΠ΅ΠΆΠΈΠΌ ΡΠ»ΡΠΆΠΈΡ Π΄Π»ΡΒ ΡΠ²Π΅Π»ΠΈΡΠ΅Π½ΠΈΡ ΡΠ°Π·ΠΌΠ΅ΡΠΎΡΠ½ΡΡ Β ΡΠ³Π»ΡΠ±Π»Π΅Π½ΠΈΠΉ Π½Π° ΠΎΠΏΡΠ΅Π΄Π΅Π»Π΅Π½Π½ΡΡ Π³Π»ΡΠ±ΠΈΠ½Ρ. ΠΠ΅ΡΠ΅ΠΆΠΈΠΌΒ ΠΎΡΡΡΠ΅ΡΡΠ²Π»ΡΡΡ Π²Β Π·Π°Π²ΠΈΡΠΈΠΌΠΎΡΡΠΈΒ ΠΎΡ ΡΡΠ΅Π±ΡΠ΅ΠΌΠΎΠ³ΠΎ ΠΏΡΠΎΡΠΈΠ»ΡΒ ΡΠΎΠΎΡΠ²Π΅ΡΡΡΠ²ΡΡΡΠΈΠΌΠΈ ΡΠ°ΡΠΊΠ°ΡΠΊΠ°ΠΌΠΈ. ΠΠ°ΠΌΠ΅ΡΠΊΡ ΠΈ ΠΏΠ΅ΡΠ΅ΠΆΠΈΠΌ Π²ΡΠΏΠΎΠ»Π½ΡΡΡ Ρ ΠΎΠ΄Π½ΠΎΠΉ ΠΈΠ»ΠΈ Π½Π΅ΡΠΊΠΎΠ»ΡΠΊΠΈΡ ΡΡΠΎΡΠΎΠ½ Π·Π°Π³ΠΎΡΠΎΠ²ΠΊΠΈ.
ΠΠ΅ΡΠ΅Π΄Π°ΡΠ° ΡΠ»ΡΠΆΠΈΡ Π΄Π»Ρ ΡΠΌΠ΅ΡΠ΅Π½ΠΈΡ ΠΎΠ΄Π½ΠΎ ΡΠ°ΡΡΠΈ ΡΠ»ΠΈΡΠΊΠ° ΠΎΡΠ½ΠΎΡΠΈΡΠ΅Π»ΡΠ½ΠΎ Π΄ΡΡΠ³ΠΎΠΉ.
Π‘Π΅Π±Π΅ΡΡΠΎΠΈΠΌΠΎΡΡΡ ΠΊΠΎΠ²Π°Π½ΡΡ Β ΠΏΠΎΠΊΠΎΠ²ΠΎΠΊΒ ΡΡΠ°Π²Π½ΠΈΡΠ΅Π»ΡΠ½ΠΎ Π²ΡΡΠΎΠΊΠ°, Π½ΠΎ ΠΏΡΠΈΒ ΡΡΠΎΠΌ Π³Π°ΡΠ°Π½ΡΠΈΡΡΡΡΡΡΒ Π²ΡΡΠΎΠΊΠΈΠ΅ ΠΌΠ΅Ρ Π°Π½ΠΈΡΠ΅ΡΠΊΠΈΠ΅ ΡΠ²ΠΎΠΉΡΡΠ²Π° ΠΈ Π½Π°Π΄Π΅ΠΆΠ½ΠΎΡΡΡ ΠΈΠ·Π΄Π΅Π»ΠΈΠΉ.
Π’Π΅Ρ Π½ΠΎΠ»ΠΎΠ³ΠΈΡΠ΅ΡΠΊΠΈΠΉ ΠΏΡΠΎΡΠ΅ΡΡΒ ΠΊΠΎΠ²ΠΊΠΈΒ ΠΊΠΎΠ»ΡΡΠ΅Π²ΠΎΠΉΒ ΠΏΠΎΠΊΠΎΠ²ΠΊΠΈ
ΠΠΎΠΊΠΎΠ²ΠΊΠ° | ΠΠ°Π³ΠΎΡΠΎΠ²ΠΊΠ° | |||||
βΒ | ΠΠ°ΠΈΠΌΠ΅Π½ΠΎΠ²Π°Π½ΠΈΠ΅ ΠΎΠΏΠ΅ΡΠ°ΡΠΈΠΈ | ΠΠΏΠ΅ΡΠ°ΡΠΈΠΎΠ½Π½ΡΠΉΒ ΡΡΠΊΠΈΠ· | ΠΠ±ΠΎΡΡΠ΄ΠΎΠ²Π°Π½ΠΈΠ΅ | ΠΠ½ΡΡΡΡΠΌΠ΅Π½Ρ | Π‘Ρ
Π΅ΠΌΠ° Β | |
1 | ΠΡΠ°Π΄ΠΊΠ° | ΠΡΠ΅ΡΡ Π³ΠΈΠ΄ΡΠ°Π²Π»ΠΈΡΠ΅ΡΠΊΠΈΠΉ | ΠΠΎΠΉΠΊΠΈ Β | |||
2 | ΠΡΠΎΡΠΈΠ²ΠΊΠ°Β | ΠΡΠΎΡΠΈΠ²Π΅Π½Ρ. ΠΠΎΠΉΠΊΠΈΒ Β | ||||
3 | Π Π°ΡΠΊΠ°ΡΠΊΠ°Β Π½Π° ΠΎΠΏΡΠ°Π²ΠΊΠ΅Β | ΠΠΏΡΠ°Π²ΠΊΠΈ. ΠΠΏΠΎΡΠ°Β | ||||
4 | Π Π°ΡΠΊΠ°ΡΠΊΠ°Β Π½Π° ΠΎΠΏΡΠ°Π²ΠΊΠ΅Β |
Β
Π Π°ΡΡΠ΅ΡΒ ΡΠ°Π·ΠΌΠ΅ΡΠΎΠ² Π·Π°Π³ΠΎΡΠΎΠ²ΠΊΠΈ:
Β
Β
Β
Β
Β
Β
D1 β Π΄ΠΈΠ°ΠΌΠ΅ΡΡ ΠΎΡΠ²Π΅ΡΡΡΠΈΡ Π² Π΄Π΅ΡΠ°Π»ΠΈ, ΠΌΠΌ
D2 β Π΄ΠΈΠ°ΠΌΠ΅ΡΡ Π΄Π΅ΡΠ°Π»ΠΈ, ΠΌΠΌ
h β Π²ΡΡΠΎΡΠ° Π΄Π΅ΡΠ°Π»ΠΈ, ΠΌΠΌ
dβ β Π΄ΠΈΠ°ΠΌΠ΅ΡΡ Π²ΡΠ΄ΡΡ, ΠΌΠΌ
hβ β Π²ΡΡΠΎΡΠ° Π²ΡΠ΄ΡΡ, ΠΌΠΌ
D β Π΄ΠΈΠ°ΠΌΠ΅ΡΡ Π·Π°Π³ΠΎΡΠΎΠ²ΠΊΠΈ, ΠΌΠΌ
H β Π²ΡΡΠΎΡΠ° Π·Π°Π³ΠΎΡΠΎΠ²ΠΊΠΈ, ΠΌΠΌ
Π Π°ΡΡΠ΅ΡΒ ΡΠ°Π·ΠΌΠ΅ΡΠΎΠ² Π·Π°Π³ΠΎΡΠΎΠ²ΠΊΠΈΒ ΠΏΠΎΡΠ»Π΅Β ΠΎΡΠ°Π΄ΠΊΠΈ:
Β
Β
V β ΠΎΠ±ΡΠ΅ΠΌ Π·Π°Π³ΠΎΡΠΎΠ²ΠΊΠΈ Π½Π° Π΄Π°Π½Π½ΠΎΠΌ ΡΡΠ°ΠΏΠ΅ ΠΊΠΎΠ²ΠΊΠΈ, ΠΌΠΌ3
D β Π΄ΠΈΠ°ΠΌΠ΅ΡΡ Π·Π°Π³ΠΎΡΠΎΠ²ΠΊΠΈ, ΠΌΠΌ
h β Π²ΡΡΠΎΡΠ° Π·Π°Π³ΠΎΡΠΎΠ²ΠΊΠΈ, ΠΌΠΌ
Π Π°ΡΡΠ΅ΡΒ ΡΠ°Π·ΠΌΠ΅ΡΠΎΠ² Π·Π°Π³ΠΎΡΠΎΠ²ΠΊΠΈΒ ΠΏΠΎΡΠ»Π΅Β ΠΏΡΠΎΡΠΈΠ²ΠΊΠΈ ΠΎΡΠ²Π΅ΡΡΡΠΈΡ:
Β
Β
V β ΠΎΠ±ΡΠ΅ΠΌ Π·Π°Π³ΠΎΡΠΎΠ²ΠΊΠΈ Π½Π° Π΄Π°Π½Π½ΠΎΠΌ ΡΡΠ°ΠΏΠ΅ ΠΊΠΎΠ²ΠΊΠΈ, ΠΌΠΌ3
VΠ· β ΠΎΠ±ΡΠ΅ΠΌ Π·Π°Π³ΠΎΡΠΎΠ²ΠΊΠΈ Π±Π΅Π· ΡΡΠ΅ΡΠ° ΡΠ³Π»ΡΠ±Π»Π΅Π½ΠΈΡ ΠΎΡ ΠΏΡΠΎΡΠΈΠ²ΠΊΠΈ Ρ ΠΎΠ΄Π½ΠΎΠΉ ΡΡΠΎΡΠΎΠ½Ρ, ΠΌΠΌ3
D β Π΄ΠΈΠ°ΠΌΠ΅ΡΡ Π·Π°Π³ΠΎΡΠΎΠ²ΠΊΠΈ Π½Π° Π΄Π°Π½Π½ΠΎΠΌ ΡΡΠ°ΠΏΠ΅ ΠΊΠΎΠ²ΠΊΠΈ, ΠΌΠΌ
h β Π²ΡΡΠΎΡΠ° Π·Π°Π³ΠΎΡΠΎΠ²ΠΊΠΈ Π½Π° Π΄Π°Π½Π½ΠΎΠΌ ΡΡΠ°ΠΏΠ΅ ΠΊΠΎΠ²ΠΊΠΈ, ΠΌΠΌ
VΡΠ³Π» β ΠΎΠ±ΡΠ΅ΠΌ ΡΠ³Π»ΡΠ±Π»Π΅Π½ΠΈΡ ΠΎΡ ΠΏΡΠΎΡΠΈΠ²ΠΊΠΈ Ρ ΠΎΠ΄Π½ΠΎΠΉ ΡΡΠΎΡΠΎΠ½Ρ, ΠΌΠΌ3
D1 β Π΄ΠΈΠ°ΠΌΠ΅ΡΡ ΡΠ³Π»ΡΠ±Π»Π΅Π½ΠΈΡ, ΠΌΠΌ
h1 β Π²ΡΡΠΎΡΠ° ΡΠ³Π»ΡΠ±Π»Π΅Π½ΠΈΡ, ΠΌΠΌ
Π Π°ΡΡΠ΅ΡΒ ΡΠ°Π·ΠΌΠ΅ΡΠΎΠ² Π·Π°Π³ΠΎΡΠΎΠ²ΠΊΠΈΒ ΠΏΠΎΡΠ»Π΅Β ΡΠ°ΡΠΊΠ°ΡΠΊΠΈ Π½Π° ΠΎΠΏΡΠ°Π²ΠΊΠ΅:
Β
Β
V β ΠΎΠ±ΡΠ΅ΠΌ Π·Π°Π³ΠΎΡΠΎΠ²ΠΊΠΈ Π½Π° Π΄Π°Π½Π½ΠΎΠΌ ΡΡΠ°ΠΏΠ΅ ΠΊΠΎΠ²ΠΊΠΈ, ΠΌΠΌ3
D2 β Π΄ΠΈΠ°ΠΌΠ΅ΡΡ Π·Π°Π³ΠΎΡΠΎΠ²ΠΊΠΈ Π½Π° Π΄Π°Π½Π½ΠΎΠΌ ΡΡΠ°ΠΏΠ΅ ΠΊΠΎΠ²ΠΊΠΈ, ΠΌΠΌ
h β Π²ΡΡΠΎΡΠ° Π·Π°Π³ΠΎΡΠΎΠ²ΠΊΠΈ Π½Π° Π΄Π°Π½Π½ΠΎΠΌ ΡΡΠ°ΠΏΠ΅ ΠΊΠΎΠ²ΠΊΠΈ, ΠΌΠΌ
D1 β Π΄ΠΈΠ°ΠΌΠ΅ΡΡ ΠΎΡΠ²Π΅ΡΡΡΠΈΡ, ΠΌΠΌ
ΠΡΠ²ΠΎΠ΄:
ΠΠΎΡΠ»Π΅ Π·Π°Π²Π΅ΡΡΠ΅Π½ΠΈΡ Π²ΡΠ΅Π³ΠΎ ΡΠ΅Ρ Π½ΠΎΠ»ΠΎΠ³ΠΈΡΠ΅ΡΠΊΠΎΠ³ΠΎ ΠΏΡΠΎΡΠ΅ΡΡΠ° ΠΌΡ ΠΈΠ· ΡΠ²ΠΈΠ½ΡΠ° ΡΠΈΠ»ΠΈΠ½Π΄ΡΠΈΡΠ΅ΡΠΊΠΎΠΉ ΡΠΎΡΠΌΡ ΠΏΠΎΠ»ΡΡΠΈΠ»ΠΈ Π½Π΅ΠΎΠ±Ρ ΠΎΠ΄ΠΈΠΌΡΡ Π½Π°ΠΌ Π·Π°Π³ΠΎΡΠΎΠ²ΠΊΡ ΠΏΠΎΡ ΠΎΠΆΡΡ Π½Π° Π½Π΅ΠΎΠ±Ρ ΠΎΠ΄ΠΈΠΌΡΡ Π½Π°ΠΌ Π΄Π΅ΡΠ°Π»Ρ. Π’Π°ΠΊ ΠΊΠ°ΠΊ Π² Π½Π°ΡΠ΅ΠΌ ΡΠ»ΡΡΠ°Π΅ ΠΊΠΎΠ²ΠΊΠ° ΡΠ²Π»ΡΠ΅ΡΡΡ Π΄ΠΎΠ²ΠΎΠ»ΡΠ½ΠΎ Π³ΡΡΠ±ΡΠΌ ΠΏΡΠΎΡΠ΅ΡΡΠΎΠΌ, ΡΠΎ ΠΏΠΎΠ»ΡΡΠΈΠ²ΡΠ°ΡΡΡ Π·Π°Π³ΠΎΡΠΎΠ²ΠΊΠ° ΠΎΠ±Π»Π°Π΄Π°Π΅ΠΌ ΡΡΠ΄ΠΎΠΌ Π½Π΅ΡΠ΅ΡΡΠ΅Π·Π½ΡΡ Π½Π΅Π΄ΠΎΡΡΠ°ΡΠΊΠΎΠ² ΡΠ°ΠΊΠΈΡ ΠΊΠ°ΠΊ: ΠΊΠΎΠ½ΡΡΠ½ΠΎΡΡΡ, ΠΎΠ³ΡΠ°Π½ΠΊΠ° (Π²ΠΌΠ΅ΡΡΠΎ Π³Π»Π°Π΄ΠΊΠΈΡ ΡΠΈΠ»ΠΈΠ½Π΄ΡΠΈΡΠ΅ΡΠΊΠΈΡ ΡΡΠΎΡΠΎΠ½ ΠΌΡ ΠΏΠΎΠ»ΡΡΠΈΠ»ΠΈ Π½Π΅ΠΊΡΡ ΠΌΠ½ΠΎΠ³ΠΎΠ³ΡΠ°Π½Π½ΡΡ Π³Π°ΠΉΠΊΡ), Π½Π΅ΡΠ°Π²Π΅Π½ΡΡΠ²ΠΎ Π΄ΠΈΠ°ΠΌΠ΅ΡΡΠΎΠ² ΠΎΠΊΡΡΠΆΠ½ΠΎΡΡΠ΅ΠΉ, ΠΎΡΡΡΡΡΡΠ²ΠΈΠ΅ ΠΈΡ ΠΊΠΎΠ½ΡΠ΅Π½ΡΡΠΈΡΠ½ΠΎΡΡΠΈ, ΡΠ°Π·Π½ΠΎΡΠΎΠ΄Π½ΠΎΡΡΡ ΠΏΠΎ Π²ΡΡΠΎΡΠ΅. ΠΠΎ Π²ΡΠ΅ ΡΡΠΈ Π½Π΅Π΄ΠΎΡΡΠ°ΡΠΊΠΈ ΠΌΠΎΠ³ΡΡ Π±ΡΡΡ Π»Π΅Π³ΠΊΠΎ ΡΠ±ΡΠ°Π½Ρ ΠΏΡΠΈ ΠΏΠΎΠΌΠΎΡΠΈ Π΄Π°Π»ΡΠ½Π΅ΠΉΡΠ΅ΠΉ ΠΎΠ±ΡΠ°Π±ΠΎΡΠΊΠΈ Π·Π°Π³ΠΎΡΠΎΠ²ΠΊΠΈ ΠΊΠ°ΠΊ Π½Π° ΠΏΡΠ΅ΡΡΠ΅, ΡΠ°ΠΊ ΠΈ Π½Π° ΡΠ°Π·Π»ΠΈΡΠ½ΡΡ ΡΡΠ°Π½ΠΊΠ°Ρ .
Β
Β
Β
Β
Β
Β
Β
Π’Π΅Ρ Π½ΠΎΠ»ΠΎΠ³ΠΈΡ ΡΡΡΠ½ΠΎΠΉ ΠΊΠΎΠ²ΠΊΠΈ
Π‘ΠΎΠ΄Π΅ΡΠΆΠ°Π½ΠΈΠ΅.
ΠΠ»Π°Π²Π° I. ΠΡΠ°ΡΠΊΠΈΠ΅ ΡΠ²Π΅Π΄Π΅Π½ΠΈΡ ΠΎ ΠΊΡΠ·Π½Π΅ΡΠ½ΠΎΠΌ ΠΏΡΠΎΠΈΠ·Π²ΠΎΠ΄ΡΡΠ²Π΅
Β§ 1. ΠΠΎΠ·Π½ΠΈΠΊΠ½ΠΎΠ²Π΅Π½ΠΈΠ΅ ΠΈ ΡΠ°Π·Π²ΠΈΡΠΈΠ΅ ΠΊΡΠ·Π½Π΅ΡΠ½ΠΎΠ³ΠΎ ΠΏΡΠΎΠΈΠ·Π²ΠΎΠ΄ΡΡΠ²Π°
Β§ 2. ΠΡΠ½ΠΎΠ²Π½ΡΠ΅ ΠΏΠΎΠ½ΡΡΠΈΡ ΠΎΠ± ΠΎΠ±ΡΠ°Π±ΠΎΡΠΊΠ΅ ΠΌΠ΅ΡΠ°Π»Π»ΠΎΠ² Π΄Π°Π²Π»Π΅Π½ΠΈΠ΅ΠΌ
Β§ 3. Π‘ΡΡΠ½ΠΎΡΡΡ ΠΈ ΠΎΠ±Π»Π°ΡΡΡ ΠΏΡΠΈΠΌΠ΅Π½Π΅Π½ΠΈΡ ΠΊΠΎΠ²ΠΊΠΈ
Β§ 4. ΠΡΠΎΠΈΠ·Π²ΠΎΠ΄ΡΡΠ²Π΅Π½Π½ΡΠ΅ ΠΏΡΠΎΡΠ΅ΡΡΡ ΠΊΡΠ·Π½Π΅ΡΠ½ΠΎΠ³ΠΎ ΡΠ΅Ρ
Π°
ΠΠ»Π°Π²Π° II. ΠΠ±ΡΠΈΠ΅ ΡΠ²Π΅Π΄Π΅Π½ΠΈΡ ΠΎ Π½Π°Π³ΡΠ΅Π²Π΅ ΠΌΠ΅ΡΠ°Π»Π»ΠΎΠ²
Β§ 5. ΠΠ±ΡΠΈΠ΅ ΡΠ²Π΅Π΄Π΅Π½ΠΈΡ ΠΎ Π³ΠΎΡΠ΅Π½ΠΈΠΈ ΠΈ ΠΏΠ΅ΡΠ΅Π΄Π°ΡΠ΅ ΡΠ΅ΠΏΠ»Π° ΠΌΠ΅ΡΠ°Π»Π»Ρ
Β§ 6. ΠΠΈΠ΄Ρ ΡΠΎΠΏΠ»ΠΈΠ²Π°, ΠΏΡΠΈΠΌΠ΅Π½ΡΠ΅ΠΌΡΠ΅ Π² ΠΊΡΠ·Π½Π΅ΡΠ½ΠΎΠΌ ΠΏΡΠΎΠΈΠ·Π²ΠΎΠ΄ΡΡΠ²Π΅
Β§ 7. ΠΠ»ΠΈΡΠ½ΠΈΠ΅ Π½Π°Π³ΡΠ΅Π²Π° Π½Π° ΡΠ²ΠΎΠΉΡΡΠ²Π° ΠΌΠ΅ΡΠ°Π»Π»Π°
Β§ 8. ΠΠΎΠ½ΡΡΠΈΠ΅ ΠΎ ΡΠ΅ΠΆΠΈΠΌΠ΅ Π½Π°Π³ΡΠ΅Π²Π°
Β§ 9. ΠΠ»ΠΈΡΠ½ΠΈΠ΅ Ρ
Π°ΡΠ°ΠΊΡΠ΅ΡΠ° ΠΏΠ»Π°ΠΌΠ΅Π½ΠΈ Π½Π° ΠΊΠ°ΡΠ΅ΡΡΠ²ΠΎ Π½Π°Π³ΡΠ΅Π²Π° ΠΌΠ΅ΡΠ°Π»Π»Π° ΠΈ Π²ΠΈΠ΄Ρ Π΄Π΅ΡΠ΅ΠΊΡΠΎΠ²
Β§ 10. Π’Π΅ΠΌΠΏΠ΅ΡΠ°ΡΡΡΠ½ΡΠ΅ ΠΈΠ½ΡΠ΅ΡΠ²Π°Π»Ρ ΠΊΠΎΠ²ΠΊΠΈ
Β§ 11. ΠΡΠΈΠ±ΠΎΡΡ, ΠΏΡΠΈΠΌΠ΅Π½ΡΠ΅ΠΌΡΠ΅ Π΄Π»Ρ Π·Π°ΠΌΠ΅ΡΠ° ΡΠ΅ΠΌΠΏΠ΅ΡΠ°ΡΡΡ
ΠΠ»Π°Π²Π° III. ΠΠ°Π³ΡΠ΅Π²Π°ΡΠ΅Π»ΡΠ½ΡΠ΅ ΡΡΡΡΠΎΠΉΡΡΠ²Π°
Β§ 12. ΠΡΠ·Π½Π΅ΡΠ½ΡΠ΅ Π³ΠΎΡΠ½Ρ
Β§ 13. ΠΠ»Π°ΠΌΠ΅Π½Π½ΡΠ΅ Π½Π°Π³ΡΠ΅Π²Π°ΡΠ΅Π»ΡΠ½ΡΠ΅ ΠΊΡΠ·Π½Π΅ΡΠ½ΡΠ΅ ΠΏΠ΅ΡΠΈ
Β§ 14. Π£ΡΡΡΠΎΠΉΡΡΠ²Π° Π΄Π»Ρ ΡΠΆΠΈΠ³Π°Π½ΠΈΡ ΠΆΠΈΠ΄ΠΊΠΎΠ³ΠΎ ΡΠΎΠΏΠ»ΠΈΠ²Π°
Β§ 15. Π£ΡΡΡΠΎΠΉΡΡΠ²Π° Π΄Π»Ρ ΡΠΆΠΈΠ³Π°Π½ΠΈΡ Π³Π°Π·ΠΎΠΎΠ±ΡΠ°Π·Π½ΠΎΠ³ΠΎ ΡΠΎΠΏΠ»ΠΈΠ²Π°
Β§ 16. ΠΡΠΏΠΎΠΌΠΎΠ³Π°ΡΠ΅Π»ΡΠ½ΡΠ΅ ΡΡΡΡΠΎΠΉΡΡΠ²Π° ΠΊ ΠΏΠ»Π°ΠΌΠ΅Π½Π½ΡΠΌ ΠΏΠ΅ΡΠ°ΠΌ
Β§ 17. ΠΠ»Π΅ΠΊΡΡΠΈΡΠ΅ΡΠΊΠΈΠ΅ Π½Π°Π³ΡΠ΅Π²Π°ΡΠ΅Π»ΡΠ½ΡΠ΅ ΠΊΡΠ·Π½Π΅ΡΠ½ΡΠ΅ ΠΏΠ΅ΡΠΈ ΠΈ ΡΡΡΡΠΎΠΉΡΡΠ²Π°
Β§ 48. ΠΠ½ΠΎΠ³ΠΎΠΊΡΠ°ΡΠ½ΡΠΉ Π½Π°Π³ΡΠ΅Π² ΠΈ Π΅Π³ΠΎ Π²Π»ΠΈΡΠ½ΠΈΠ΅ Π½Π° ΡΠ°ΡΡ
ΠΎΠ΄ ΡΠΎΠΏΠ»ΠΈΠ²Π°
Β§ 19. Π‘ΠΏΠΎΡΠΎΠ±Ρ Π±Π΅Π·ΠΎΠΊΠΈΡΠ»ΠΈΡΠ΅Π»ΡΠ½ΠΎΠ³ΠΎ Π½Π°Π³ΡΠ΅Π²Π°
Β§ 20. ΠΡ
Π»Π°ΠΆΠ΄Π΅Π½ΠΈΠ΅ ΠΏΠΎΠΊΠΎΠ²ΠΎΠΊ
Β§ 21. ΠΡΠΎΠΈΠ·Π²ΠΎΠ΄ΠΈΡΠ΅Π»ΡΠ½ΠΎΡΡΡ Π½Π°Π³ΡΠ΅Π²Π°ΡΠ΅Π»ΡΠ½ΡΡ
ΠΏΠ΅ΡΠ΅ΠΉ
Β§ 22. ΠΡΠ°ΡΠΊΠΈΠ΅ ΡΠ²Π΅Π΄Π΅Π½ΠΈΡ ΠΎΠ± ΠΎΠ³Π½Π΅ΡΠΏΠΎΡΠ½ΡΡ
ΠΈ ΡΠ΅ΠΏΠ»ΠΎΠΈΠ·ΠΎΠ»ΡΡΠΈΠΎΠ½Π½ΡΡ
ΠΌΠ°ΡΠ΅ΡΠΈΠ°Π»Π°Ρ
Β§ 23. ΠΠ±ΡΠ»ΡΠΆΠΈΠ²Π°Π½ΠΈΠ΅ ΠΊΠ°ΠΌΠ΅ΡΠ½ΡΡ
ΠΏΠ΅ΡΠ΅ΠΉ
Β§ 24. Π’Π΅Ρ
Π½ΠΈΠΊΠ° Π±Π΅Π·ΠΎΠΏΠ°ΡΠ½ΠΎΡΡΠΈ ΠΈ ΠΏΡΠΎΡΠΈΠ²ΠΎΠΏΠΎΠΆΠ°ΡΠ½ΡΠ΅ ΠΌΠ΅ΡΠΎΠΏΡΠΈΡΡΠΈΡ ΠΏΡΠΈ ΡΠ°Π±ΠΎΡΠ΅ Ρ Π½Π°Π³ΡΠ΅Π²Π°ΡΠ΅Π»ΡΠ½ΡΡ
ΠΏΠ΅ΡΠ΅ΠΉ
ΠΠ»Π°Π²Π° IV. ΠΠ½ΡΡΡΡΠΌΠ΅Π½ΡΡ ΠΈ ΠΏΡΠΈΡΠΏΠΎΡΠΎΠ±Π»Π΅Π½ΠΈΡ Π΄Π»Ρ ΡΡΡΠ½ΠΎΠΉ ΠΊΠΎΠ²ΠΊΠΈ
Β§ 25. ΠΠ»Π°ΡΡΠΈΡΠΈΠΊΠ°ΡΠΈΡ ΠΊΡΠ·Π½Π΅ΡΠ½ΠΎΠ³ΠΎ ΠΈΠ½ΡΡΡΡΠΌΠ΅Π½ΡΠ°
Β§ 26. ΠΡΠ½ΠΎΠ²Π½ΠΎΠΉ ΠΈΠ½ΡΡΡΡΠΌΠ΅Π½Ρ Π΄Π»Ρ ΡΡΡΠ½ΠΎΠΉ ΠΊΠΎΠ²ΠΊΠΈ
Β§ 27. ΠΡΠΏΠΎΠΌΠΎΠ³Π°ΡΠ΅Π»ΡΠ½ΡΠΉ ΠΈΠ½ΡΡΡΡΠΌΠ΅Π½Ρ Π΄Π»Ρ ΡΡΡΠ½ΠΎΠΉ ΠΊΠΎΠ²ΠΊΠΈ
Β§ 28. ΠΠΎΠ½ΡΡΠΎΠ»ΡΠ½ΠΎ-ΠΈΠ·ΠΌΠ΅ΡΠΈΡΠ΅Π»ΡΠ½ΡΠΉ ΠΈΠ½ΡΡΡΡΠΌΠ΅Π½Ρ
Β§ 29. ΠΡΠΈΠ±ΠΎΡΡ Π΄Π»Ρ ΠΎΠΏΡΠ΅Π΄Π΅Π»Π΅Π½ΠΈΡ ΡΠ²Π΅ΡΠ΄ΠΎΡΡΠΈ ΠΌΠ΅ΡΠ°Π»Π»ΠΎΠ²
ΠΠ»Π°Π²Π° V. ΠΡΠ·Π½Π΅ΡΠ½ΡΠ΅ ΠΎΠΏΠ΅ΡΠ°ΡΠΈΠΈ
Β§ 30. ΠΡΡΡΠ±ΠΊΠ°
Β§ 31. ΠΡΠ°Π΄ΠΊΠ°
Β§ 32. ΠΡΠΎΡΡΠΆΠΊΠ° ΠΈ ΠΏΠ΅ΡΠ΅ΠΆΠΈΠΌ ΠΌΠ΅ΡΠ°Π»Π»Π°
Β§ 33. ΠΠΈΠ±ΠΊΠ°, ΡΠ°ΡΠΊΠ°ΡΠΊΠ° ΠΈ ΡΠΊΡΡΡΠΈΠ²Π°Π½ΠΈΠ΅
Β§ 34. ΠΡΠΎΠ±ΠΈΠ²ΠΊΠ° ΠΈ ΠΏΡΠΎΡΠΈΠ²ΠΊΠ° ΠΎΡΠ²Π΅ΡΡΡΠΈΠΉ
Β§ 35. ΠΡΠ·Π½Π΅ΡΠ½Π°Ρ ΡΠ²Π°ΡΠΊΠ°
Β§ 36. Π€Π°ΡΠΎΠ½Π½Π°Ρ ΠΊΠΎΠ²ΠΊΠ°
Β§ 37. ΠΡΠ°Π²ΠΊΠ°
ΠΠ»Π°Π²Π° VI. Π‘Π²Π΅Π΄Π΅Π½ΠΈΡ ΠΈΠ· ΡΠ΅ΠΎΡΠΈΠΈ ΠΎΠ±ΡΠ°Π±ΠΎΡΠΊΠΈ ΠΌΠ΅ΡΠ°Π»Π»ΠΎΠ² Π΄Π°Π²Π»Π΅Π½ΠΈΠ΅ΠΌ
Β§ 38. Π‘ΡΡΠΎΠ΅Π½ΠΈΠ΅ ΠΌΠ΅ΡΠ°Π»Π»ΠΎΠ² ΠΈ Π²ΠΈΠ΄Ρ Π΄Π΅ΡΠΎΡΠΌΠ°ΡΠΈΠΈ
Β§ 39. Π€ΠΈΠ·ΠΈΡΠ΅ΡΠΊΠ°Ρ ΡΡΡΠ½ΠΎΡΡΡ ΠΏΠ»Π°ΡΡΠΈΡΠ΅ΡΠΊΠΎΠΉ Π΄Π΅ΡΠΎΡΠΌΠ°ΡΠΈΠΈ
Β§ 40. ΠΡΠ½ΠΎΠ²Π½ΡΠ΅ Π·Π°ΠΊΠΎΠ½Ρ ΠΏΠ»Π°ΡΡΠΈΡΠ΅ΡΠΊΠΎΠΉ Π΄Π΅ΡΠΎΡΠΌΠ°ΡΠΈΠΈ
Β§ 41. ΠΠ»ΠΈΡΠ½ΠΈΠ΅ ΡΠΎΡΡΠΎΡΠ½ΠΈΡ ΠΏΠΎΠ²Π΅ΡΡ
Π½ΠΎΡΡΠΈ Π±ΠΎΠΉΠΊΠΎΠ² Π½Π° ΡΠ΅ΡΠ΅Π½ΠΈΠ΅.ΠΌΠ΅ΡΠ°Π»Π»Π° ΠΏΡΠΈ ΠΊΠΎΠ²ΠΊΠ΅
ΠΠ»Π°Π²Π° VII. Π‘ΠΎΡΡΠ°Π²Π»Π΅Π½ΠΈΠ΅ ΡΠ΅ΡΡΠ΅ΠΆΠ° ΠΏΠΎΠΊΠΎΠ²ΠΊΠΈ ΠΈ ΡΠ²Π΅Π΄Π΅Π½ΠΈΡ ΠΎ Π΄ΠΎΠΏΡΡΠΊΠ°Ρ , ΠΏΡΠΈΠΏΡΡΠΊΠ°Ρ ΠΈ Π½Π°ΠΏΡΡΠΊΠ°Ρ Π² ΠΊΡΠ·Π½Π΅ΡΠ½ΠΎΠΌ ΠΏΡΠΎΠΈΠ·Π²ΠΎΠ΄ΡΡΠ²Π΅
Β§ 42. Π‘ΠΎΡΡΠ°Π²Π»Π΅Π½ΠΈΠ΅ ΡΠ΅ΡΡΠ΅ΠΆΠ° ΠΏΠΎΠΊΠΎΠ²ΠΊΠΈ
Β§ 43. ΠΡΠΈΠΌΠ΅ΡΡ ΠΏΠΎ ΠΠΏΡΠ΅Π΄Π΅Π»Π΅Π½ΠΈΡ ΡΠ°Π·ΠΌΠ΅ΡΠΎΠ², ΠΏΡΠΈΠΏΡΡΠΊΠΎΠ² ΠΈ Π΄ΠΎΠΏΡΡΠΊΠΎΠ² Π½Π° ΠΏΠΎΠΊΠΎΠ²ΠΊΡ ΠΏΠΎ ΡΠ°Π±ΠΎΡΠ΅ΠΌΡ ΡΠ΅ΡΡΠ΅ΠΆΡ Π΄Π΅ΡΠ°Π»ΠΈ
Β§ 44. ΠΠΏΡΠ΅Π΄Π΅Π»Π΅Π½ΠΈΠ΅ ΡΠ°Π·ΠΌΠ΅ΡΠΎΠ² ΠΈ ΠΌΠ°ΡΡΡ Π·Π°Π³ΠΎΡΠΎΠ²ΠΊΠΈ
Β§ 45. ΠΠΎΠ½ΡΡΠΈΠ΅ ΠΎ ΠΊΠΎΡΡΡΠΈΡΠΈΠ΅Π½ΡΠ΅ ΠΈΡΠΏΠΎΠ»ΡΠ·ΠΎΠ²Π°Π½ΠΈΡ ΠΌΠ΅ΡΠ°Π»Π»ΠΎΠ²
ΠΠ»Π°Π²Π° VIII. Π’Π΅Ρ Π½ΠΈΠΊΠ° Π±Π΅Π·ΠΎΠΏΠ°ΡΠ½ΠΎΡΡΠΈ, ΡΠ»Π΅ΠΊΡΡΠΎΠ±Π΅Π·ΠΎΠΏΠ°ΡΠ½ΠΎΡΡΡ ΠΈ ΠΏΡΠΎΡΠΈΠ²ΠΎΠΏΠΎΠΆΠ°ΡΠ½ΡΠ΅ ΠΌΠ΅ΡΠΎΠΏΡΠΈΡΡΠΈΡ
Β§ 46. ΠΠ»Π΅ΠΊΡΡΠΎΠ±Π΅Π·ΠΎΠΏΠ°ΡΠ½ΠΎΡΡΡ
Β§ 47. ΠΡΠΎΠΈΠ·Π²ΠΎΠ΄ΡΡΠ²Π΅Π½Π½ΡΠΉ ΠΈΠ½ΡΡΡΡΠΊΡΠ°ΠΆ ΠΏΠΎ ΡΠ΅Ρ
Π½ΠΈΠΊΠ΅ Π±Π΅Π·ΠΎΠΏΠ°ΡΠ½ΠΎΡΡΠΈ ΠΈ ΠΏΡΠ°Π²ΠΈΠ»Π° ΠΏΠΎΠ²Π΅Π΄Π΅Π½ΠΈΡ Π² ΡΠ΅Ρ
Π°Ρ
Β§ 48. ΠΠ΅ΡΠ²Π°Ρ ΠΏΠΎΠΌΠΎΡΡ ΠΏΡΠΈ Π½Π΅ΡΡΠ°ΡΡΠ½ΡΡ
ΡΠ»ΡΡΠ°ΡΡ
Β§ 49. ΠΡΠΎΡΠΈΠ²ΠΎΠΏΠΎΠΆΠ°ΡΠ½ΡΠ΅ ΠΌΠ΅ΡΠΎΠΏΡΠΈΡΡΠΈΡ Π² ΡΠ΅Ρ
Π΅
ΠΠ»Π°Π²Π° IX. ΠΠΎΠ΄Π³ΠΎΡΠΎΠ²ΠΊΠ° ΠΈΡΡ ΠΎΠ΄Π½ΡΡ ΠΌΠ°ΡΠ΅ΡΠΈΠ°Π»ΠΎΠ²
Β§ 50. ΠΠ°ΡΠ΅ΡΠΈΠ°Π»Ρ, ΠΎΠ±ΡΠ°Π±Π°ΡΡΠ²Π°Π΅ΠΌΡΠ΅ Π² ΠΊΡΠ·Π½Π΅ΡΠ½ΠΎΠΌ ΠΏΡΠΎΠΈΠ·Π²ΠΎΠ΄ΡΡΠ²Π΅
Β§ 51. ΠΠ°ΡΠΊΠΈ ΡΡΠ°Π»Π΅ΠΉ
Β§ 52. Π‘ΠΏΠ»Π°Π²Ρ ΡΠ²Π΅ΡΠ½ΡΡ
ΠΌΠ΅ΡΠ°Π»Π»ΠΎΠ²
Β§ 53. ΠΡΠΈΠ΅ΠΌΠΊΠ° ΠΈ Ρ
ΡΠ°Π½Π΅Π½ΠΈΠ΅ ΠΌΠ΅ΡΠ°Π»Π»Π°
Β§ 54. ΠΠΎΠ΄Π³ΠΎΡΠΎΠ²ΠΊΠ° ΠΈΡΡ
ΠΎΠ΄Π½ΠΎΠ³ΠΎ ΠΌΠ΅ΡΠ°Π»Π»Π° Π΄Π»Ρ ΠΊΠΎΠ²ΠΊΠΈ
ΠΠ»Π°Π²Π° X. Π‘Π²Π΅Π΄Π΅Π½ΠΈΡ ΠΎ ΡΡΡΡΠΊΡΡΡΠ½ΡΡ ΠΏΡΠ΅Π²ΡΠ°ΡΠ΅Π½ΠΈΡΡ Π² ΡΠΏΠ»Π°Π²Π°Ρ ΠΏΡΠΈ Π½Π°Π³ΡΠ΅Π²Π΅ ΠΈ ΠΊΠΎΠ²ΠΊΠ΅
Β§ 55. Π‘ΡΡΠΎΠ΅Π½ΠΈΠ΅ ΡΠΏΠ»Π°Π²ΠΎΠ²
Β§ 56. Π‘ΡΡΡΠΊΡΡΡΠ½ΡΠ΅ ΡΠΎΡΡΠ°Π²Π»ΡΡΡΠΈΠ΅ Π² ΡΡΠ°Π»ΡΡ
Β§ 57. Π‘ΡΡΡΠΊΡΡΡΠ½ΡΠ΅ ΠΏΡΠ΅Π²ΡΠ°ΡΠ΅Π½ΠΈΡ Π² ΡΡΠ°Π»ΡΡ
ΠΏΡΠΈ Π½Π°Π³ΡΠ΅Π²Π°Π½ΠΈΠΈ
Β§ 58. ΠΠ·ΠΌΠ΅Π½Π΅Π½ΠΈΡ ΡΡΡΡΠΊΡΡΡΡ ΡΠΏΠ»Π°Π²ΠΎΠ² ΠΏΡΠΈ ΠΊΠΎΠ²ΠΊΠ΅ ΠΈ ΠΌΠ΅ΡΠΎΠ΄Ρ ΠΈΡ
ΠΈΡΠΏΠΎΠ»ΡΠ·ΠΎΠ²Π°Π½ΠΈΡ
Β§ 59. ΠΡΠ½ΠΎΠ²Π½ΡΠ΅ ΡΠ²Π΅Π΄Π΅Π½ΠΈΡ ΠΎ ΡΠ΅ΡΠΌΠΈΡΠ΅ΡΠΊΠΎΠΉ ΠΎΠ±ΡΠ°Π±ΠΎΡΠΊΠ΅
ΠΠ»Π°Π²Π° XI. Π’Π΅Ρ Π½ΠΎΠ»ΠΎΠ³ΠΈΡΠ΅ΡΠΊΠΈΠΉ ΠΏΡΠΎΡΠ΅ΡΡ ΡΡΡΠ½ΠΎΠΉ ΠΊΠΎΠ²ΠΊΠΈ
Β§ 60. ΠΠ±ΡΠΈΠ΅ ΡΠ²Π΅Π΄Π΅Π½ΠΈΡ
Β§ 61. Π Π°Π·Π΄Π΅Π»Π΅Π½ΠΈΠ΅ ΠΏΡΠΎΡΠ΅ΡΡΠ° ΠΊΠΎΠ²ΠΊΠΈ Π½Π° ΠΎΠΏΠ΅ΡΠ°ΡΠΈΠΈ ΠΈ ΠΏΠ΅ΡΠ΅Ρ
ΠΎΠ΄Ρ, ΠΎΠΏΡΠ΅Π΄Π΅Π»Π΅Π½ΠΈΠ΅ ΠΏΠΎΡΠ»Π΅Π΄ΠΎΠ²Π°ΡΠ΅Π»ΡΠ½ΠΎΡΡΠΈ ΠΈΡ
Π²ΡΠΏΠΎΠ»Π½Π΅Π½ΠΈΡ
Β§ 62. Π’Π΅Ρ
Π½ΠΎΠ»ΠΎΠ³ΠΈΡΠ΅ΡΠΊΠ°Ρ Π΄ΠΈΡΡΠΈΠΏΠ»ΠΈΠ½Π° ΠΈ Π΄ΠΎΠΊΡΠΌΠ΅Π½ΡΠ°ΡΠΈΡ
Β§ 63. ΠΡΠ½ΠΎΠ²Π½ΡΠ΅ ΡΠΈΠΏΡ ΠΏΠΎΠΊΠΎΠ²ΠΎΠΊ ΠΈΠ· ΡΠ³Π»Π΅ΡΠΎΠ΄ΠΈΡΡΡΡ
ΠΈ Π»Π΅Π³ΠΈΡΠΎΠ²Π°Π½Π½ΡΡ
ΡΡΠ°Π»Π΅ΠΉ
Β§ 64. ΠΡΠ½ΠΎΠ²Π½ΡΠ΅ ΡΠΈΠΏΡ ΡΠ»Π΅ΡΠ°ΡΠ½ΡΡ
ΠΈ ΠΊΡΠ·Π½Π΅ΡΠ½ΡΡ
ΠΈΠ½ΡΡΡΡΠΌΠ΅Π½ΡΠΎΠ², ΠΈΠ·Π³ΠΎΡΠΎΠ²Π»ΡΠ΅ΠΌΡΡ
ΠΊΠΎΠ²ΠΊΠΎΠΉ
Β§ 65. Π’Π΅Ρ
Π½ΠΎΠ»ΠΎΠ³ΠΈΡΠ΅ΡΠΊΠΈΠ΅ ΠΏΡΠΎΡΠ΅ΡΡΡ ΠΊΠΎΠ²ΠΊΠΈ ΡΠ»Π΅ΡΠ°ΡΠ½ΡΡ
ΠΈ ΠΊΡΠ·Π½Π΅ΡΠ½ΡΡ
ΠΈΠ½ΡΡΡΡΠΌΠ΅Π½ΡΠΎΠ²
Β§ 66. ΠΠ·Π³ΠΎΡΠΎΠ²Π»Π΅Π½ΠΈΠ΅ ΠΊΠΎΠ²ΠΊΠΎΠΉ ΠΊΡΠ·Π½Π΅ΡΠ½ΠΎΠ³ΠΎ ΠΈΠ½ΡΡΡΡΠΌΠ΅Π½ΡΠ° ΠΈΠ· Π²ΡΡΠΎΠΊΠΎΡΠ³Π»Π΅ΡΠΎΠ΄ΠΈΡΡΠΎΠΉ ΡΡΠ°Π»ΠΈ
Β§ 67. ΠΡΠΈΠΌΠ΅Ρ ΠΎΠΏΡΠ΅Π΄Π΅Π»Π΅Π½ΠΈΡ ΠΌΠ°ΡΡΡ ΠΈ ΡΠ°Π·ΠΌΠ΅ΡΠ° Π·Π°Π³ΠΎΡΠΎΠ²ΠΊΠΈ ΠΏΡΠΈ ΠΊΠΎΠ²ΠΊΠ΅ ΠΏΠ»ΠΎΡΠΊΠΎΠΉ ΠΊΡΠ·Π½Π΅ΡΠ½ΠΎΠΉ Π³Π»Π°Π΄ΠΈΠ»ΠΊΠΈ
ΠΠ»Π°Π²Π° XII. ΠΠ°Π²Π΅ΡΡΠ°ΡΡΠΈΠ΅ ΠΎΠΏΠ΅ΡΠ°ΡΠΈΠΈ ΠΏΡΠΎΠΈΠ·Π²ΠΎΠ΄ΡΡΠ²Π° ΠΏΠΎΠΊΠΎΠ²ΠΎΠΊ
Β§ 68. Π’Π΅ΡΠΌΠΈΡΠ΅ΡΠΊΠ°Ρ ΠΎΠ±ΡΠ°Π±ΠΎΡΠΊΠ° ΠΏΠΎΠΊΠΎΠ²ΠΎΠΊ
Β§ 69. Π‘ΠΏΠΎΡΠΎΠ±Ρ ΠΎΡΠΈΡΡΠΊΠΈ ΠΏΠΎΠΊΠΎΠ²ΠΎΠΊ
Β§ 70. ΠΠΈΠ΄Ρ Π΄Π΅ΡΠ΅ΠΊΡΠΎΠ² ΠΈ ΠΏΡΠΈΡΠΈΠ½Ρ ΠΈΡ
ΠΏΠΎΡΠ²Π»Π΅Π½ΠΈΡ
Β§ 71. ΠΡΠ½ΠΎΠ²Π½ΡΠ΅ ΡΠΏΠΎΡΠΎΠ±Ρ ΠΊΠΎΠ½ΡΡΠΎΠ»Ρ ΠΏΠΎΠΊΠΎΠ²ΠΎΠΊ
Β§ 72. Π‘ΠΎΠ²ΡΠ΅ΠΌΠ΅Π½Π½ΡΠ΅ Π²ΠΈΠ΄Ρ ΠΊΠΎΠ½ΡΡΠΎΠ»Ρ ΠΏΠΎΠΊΠΎΠ²ΠΎΠΊ
ΠΠ»Π°Π²Π° XIII. ΠΠΏΠ΅ΡΠ°ΡΠΈΠΈ ΠΌΠ°ΡΠΈΠ½Π½ΠΎΠΉ ΠΊΠΎΠ²ΠΊΠΈ
Β§ 73. ΠΡΡΡΠ±ΠΊΠ° ΠΏΠΎΠ΄ ΠΌΠΎΠ»ΠΎΡΠ°ΠΌΠΈ ΠΈ ΠΏΡΠ΅ΡΡΠ°ΠΌΠΈ
Β§ 74. ΠΡΠ°Π΄ΠΊΠ° ΠΏΡΠΈ ΠΊΠΎΠ²ΠΊΠ΅ Π½Π° ΠΌΠΎΠ»ΠΎΡΠ°Ρ
ΠΈ ΠΏΡΠ΅ΡΡΠ°Ρ
Β§ 75. ΠΡΡΠ°Π΄ΠΊΠ° ΠΏΠΎΠ΄ ΠΌΠΎΠ»ΠΎΡΠΎΠΌ ΠΈΠ»ΠΈ ΠΏΡΠ΅ΡΡΠΎΠΌ
Β§ 16. ΠΠΏΠ΅ΡΠ°ΡΠΈΡ ΠΏΡΠΎΡΡΠΆΠΊΠΈ ΠΏΡΠΈ ΠΊΠΎΠ²ΠΊΠ΅ Π½Π° ΠΌΠΎΠ»ΠΎΡΠ°Ρ
ΠΈ ΠΏΡΠ΅ΡΡΠ°Ρ
Β§ 77. ΠΠΈΠ±ΠΊΠ° ΠΈ ΡΠΊΡΡΡΠΈΠ²Π°Π½ΠΈΠ΅
Β§ 78. ΠΡΠΎΠ±ΠΈΠ²ΠΊΠ° ΠΈ ΠΏΡΠΎΡΠΈΠ²ΠΊΠ°
Β§ 79. ΠΠ·Π³ΠΎΡΠΎΠ²Π»Π΅Π½ΠΈΠ΅ ΠΏΠΎΠΊΠΎΠ²ΠΎΠΊ ΡΠ°ΡΠΎΠ½Π½ΠΎΠΉ ΠΊΠΎΠ²ΠΊΠΎΠΉ ΠΈ ΠΊΡΠ·Π½Π΅ΡΠ½Π°Ρ ΡΠ²Π°ΡΠΊΠ° ΠΏΠΎΠ΄ ΠΌΠΎΠ»ΠΎΡΠΎΠΌ
ΠΠ»Π°Π²Π° XIV. ΠΡΡ ΠΎΠ΄Π½ΡΠ΅ ΠΌΠ°ΡΠ΅ΡΠΈΠ°Π»Ρ
Β§ 80. ΠΠΈΠ΄Ρ Π·Π°Π³ΠΎΡΠΎΠ²ΠΎΠΊ
Β§ 81. ΠΠ±ΠΆΠ°ΡΡΠ΅, ΠΊΠ°ΡΠ°Π½ΡΠ΅ ΠΈ ΠΏΡΠ΅ΡΡΠΎΠ²Π°Π½Π½ΡΠ΅ Π·Π°Π³ΠΎΡΠΎΠ²ΠΊΠΈ
Β§ 82. ΠΠΎΠ΄Π³ΠΎΡΠΎΠ²ΠΊΠ° ΠΌΠ΅ΡΠ°Π»Π»Π° Π΄Π»Ρ ΠΊΠΎΠ²ΠΊΠΈ ΠΈ ΡΡΠ°ΠΌΠΏΠΎΠ²ΠΊΠΈ
ΠΠ»Π°Π²Π° XV. ΠΠ½ΡΡΡΡΠΌΠ΅Π½Ρ Π΄Π»Ρ ΠΌΠ°ΡΠΈΠ½Π½ΠΎΠΉ ΠΊΠΎΠ²ΠΊΠΈ
Β§ 83. ΠΡΠ½ΠΎΠ²Π½ΠΎΠΉ ΠΈΠ½ΡΡΡΡΠΌΠ΅Π½Ρ
Β§ 84. ΠΡΠΏΠΎΠΌΠΎΠ³Π°ΡΠ΅Π»ΡΠ½ΡΠΉ ΠΈΠ½ΡΡΡΡΠΌΠ΅Π½Ρ Π΄Π»Ρ ΠΌΠ°ΡΠΈΠ½Π½ΠΎΠΉ ΠΊΠΎΠ²ΠΊΠΈ
Β§ 85. ΠΠΎΠ½ΡΡΠΎΠ»ΡΠ½ΠΎ-ΠΈΠ·ΠΌΠ΅ΡΠΈΡΠ΅Π»ΡΠ½ΡΠΉ ΠΈΠ½ΡΡΡΡΠΌΠ΅Π½Ρ, ΠΏΡΠΈΠΌΠ΅Π½ΡΠ΅ΠΌΡΠΉ ΠΏΡΠΈ ΠΌΠ°ΡΠΈΠ½Π½ΠΎΠΉ ΠΊΠΎΠ²ΠΊΠ΅
ΠΠ»Π°Π²Π° XVI. ΠΠΎΠ²ΠΎΡΠ½ΠΎΠ΅ ΠΎΠ±ΠΎΡΡΠ΄ΠΎΠ²Π°Π½ΠΈΠ΅, Π΅Π³ΠΎ Π²ΡΠ±ΠΎΡ ΠΈ ΠΏΡΠ°Π²ΠΈΠ»Π° ΡΠΊΡΠΏΠ»ΡΠ°ΡΠ°ΡΠΈΠΈ
Β§ 86. ΠΠΎΠ²ΠΎΡΠ½ΡΠ΅ ΠΌΠΎΠ»ΠΎΡΡ ΠΈ ΠΏΡΠ΅ΡΡΡ
Β§ 87. ΠΠ½Π΅Π²ΠΌΠ°ΡΠΈΡΠ΅ΡΠΊΠΈΠ΅ ΠΌΠΎΠ»ΠΎΡΡ
Β§ 88. ΠΠ°ΡΠΎΠ²ΠΎΠ·Π΄ΡΡΠ½ΡΠ΅ ΠΌΠΎΠ»ΠΎΡΡ
Β§ 89. Π£ΠΏΡΠ°Π²Π»Π΅Π½ΠΈΠ΅ ΠΌΠΎΠ»ΠΎΡΠΎΠΌ
Β§ 90. ΠΠΎΠ»ΠΎΡΡ Ρ Π°Π²ΡΠΌΠ°ΡΠΈΡΠ΅ΡΠΊΠΈΠΌ ΠΈ ΡΠΌΠ΅ΡΠ°Π½Π½ΡΠΌ ΡΠΏΡΠ°Π²Π»Π΅Π½ΠΈΠ΅ΠΌ
Β§ 91. ΠΡΡΠ΅ΠΊΡΠΈΠ²Π½Π°Ρ ΡΠ½Π΅ΡΠ³ΠΈΡ ΡΠ΄Π°ΡΠ° Π½ ΠΏΠ°ΡΠΏΠΎΡΡ ΠΌΠΎΠ»ΠΎΡΠ°
Β§ 92. Π’Π΅Ρ
Π½ΠΈΠΊΠ° Π±Π΅Π·ΠΎΠΏΠ°ΡΠ½ΠΎΡΡΠΈ ΠΏΡΠΈ ΠΊΠΎΠ²ΠΊΠ΅ Π½Π° ΠΌΠΎΠ»ΠΎΡΠ°Ρ
Β§ 93. Π’ΠΈΠΏΡ ΠΏΡΠ΅ΡΡΠΎΠ²
Β§ 94. Π’Π΅Ρ
Π½ΠΈΠΊΠ° Π±Π΅Π·ΠΎΠΏΠ°ΡΠ½ΠΎΡΡΠΈ ΠΏΡΠΈ ΠΊΠΎΠ²ΠΊΠ΅ Π½Π° ΠΏΡΠ΅ΡΡΠ°Ρ
Β§ 95. ΠΡΠ΅ΠΈΠΌΡΡΠ΅ΡΡΠ²Π° ΠΈ Π½Π΅Π΄ΠΎΡΡΠ°ΡΠΊΠΈ ΡΠ°Π±ΠΎΡΡ ΠΏΡΠ΅ΡΡΠΎΠ² ΠΏΠΎ ΡΡΠ°Π²Π½Π΅Π½ΠΈΡ Ρ ΠΌΠΎΠ»ΠΎΡΠ°ΠΌΠΈ
Β§ 96. ΠΠΎΠ²ΠΊΠ° ΠΊΠΎΠ»Π΅Π½ΡΠ°ΡΠΎΠ³ΠΎ Π²Π°Π»Π° Π½Π° ΠΏΡΠ΅ΡΡΠ΅
Β§ 97. ΠΠΎΠΊΠΎΠ²ΠΊΠΈ ΠΈΠ· ΡΠ³Π»Π΅ΡΠΎΠ΄ΠΈΡΡΡΡ
ΠΈ Π»Π΅Π³ΠΈΡΠΎΠ²Π°Π½Π½ΡΡ
ΡΡΠ°Π»Π΅ΠΉ, ΠΈΠ·Π³ΠΎΡΠΎΠ²Π»ΡΠ΅ΠΌΡΠ΅ ΠΌΠ°ΡΠΈΠ½Π½ΠΎΠΉ ΠΊΠΎΠ²ΠΊΠΎΠΉ
Β§ 98. ΠΡΠΈΠΌΠ΅Ρ Π²Π΅Π»ΠΈΡΠΈΠ½Ρ ΠΏΡΠΈΠΏΡΡΠΊΠ° Π½Π° ΠΊΠΎΠ²ΠΊΡ Π΄Π΅ΡΠ°Π»Π΅ΠΉ ΠΈΠ· ΡΠ³Π»Π΅ΡΠΎΠ΄ΠΈΡΡΠΎΠΉ ΠΈ Π»Π΅Π³ΠΈΡΠΎΠ²Π°Π½Π½ΠΎΠΉ ΡΡΠ°Π»ΠΈ ΠΈ ΠΎΠΏΡΠ΅Π΄Π΅Π»Π΅Π½ΠΈΡ ΡΠ°Π·ΠΌΠ΅ΡΠΎΠ² ΠΈ ΠΌΠ°ΡΡΡ Π·Π°Π³ΠΎΡΠΎΠ²ΠΊΠΈ
Β§ 99. Π Π΅ΠΆΠΈΠΌ ΠΊΠΎΠ²ΠΊΠΈ Π½Π° ΠΌΠΎΠ»ΠΎΡΠ°Ρ
ΠΈ ΠΏΡΠ΅ΡΡΠ°Ρ
Β§ 100. Π Π°ΡΠΈΠΎΠ½Π°Π»ΡΠ½ΠΎΠ΅ ΠΏΡΠΈΠΌΠ΅Π½Π΅Π½ΠΈΠ΅ ΠΈΠ½ΡΡΡΡΠΌΠ΅Π½ΡΠ°, ΠΏΡΠΈΡΠΏΠΎΡΠΎΠ±Π»Π΅Π½ΠΈΠΉ ΠΏΡΠΈ ΠΌΠ°ΡΠΈΠ½Π½ΠΎΠΉ ΠΊΠΎΠ²ΠΊΠ΅ ΠΈ ΠΏΡΠΈΠΌΠ΅ΡΡ ΠΈΠ·Π³ΠΎΡΠΎΠ²Π»Π΅Π½ΠΈΡ ΠΊΠΎΠ²Π°Π½ΠΎ-ΡΠ²Π°ΡΠ½ΡΡ
ΠΏΠΎΠΊΠΎΠ²ΠΎΠΊ
ΠΠ»Π°Π²Π° XVII. Π‘Π²Π΅Π΄Π΅Π½ΠΈΡ ΠΎ ΠΏΡΠΎΠΈΠ·Π²ΠΎΠ΄ΡΡΠ²Π΅ ΠΏΠΎΠΊΠΎΠ²ΠΎΠΊ ΠΌΠ΅ΡΠΎΠ΄ΠΎΠΌ Π³ΠΎΡΡΡΠ΅ΠΉ ΡΡΠ°ΠΌΠΏΠΎΠ²ΠΊΠΈ.
Β§ 101. ΠΠ°ΡΠΈΠ½Ρ Π΄Π»Ρ Π³ΠΎΡΡΡΠ΅ΠΉ ΠΎΠ±ΡΠ΅ΠΌΠ½ΠΎΠΉ ΡΡΠ°ΠΌΠΏΠΎΠ²ΠΊΠΈ
Β§ 102. ΠΠΎΡΡΡΠ°Ρ ΡΡΠ°ΠΌΠΏΠΎΠ²ΠΊΠ° ΠΈ Π΅Π΅ ΠΏΡΠ΅ΠΈΠΌΡΡΠ΅ΡΡΠ²Π° ΠΏΠ΅ΡΠ΅Π΄ ΠΊΠΎΠ²ΠΊΠΎΠΉ
Β§ 103. ΠΠΎΠ²ΡΡΠ΅Π½ΠΈΠ΅ ΡΠΎΡΠ½ΠΎΡΡΠΈ ΠΏΠΎΠΊΠΎΠ²ΠΎΠΊ ΠΏΠΎΡΠ»Π΅ ΡΡΠ°ΠΌΠΏΠΎΠ²ΠΊΠΈ
Β§ 104. ΠΠ»Π°ΡΡΠΈΡΠΈΠΊΠ°ΡΠΈΡ ΡΡΠ°ΠΌΠΏΠΎΠ²
Β§ 105. ΠΠ°ΡΡΠ΅Π½ΡΡ, ΠΈΡ
ΡΠΎΡΠΌΠ° ΠΈ ΡΠ°ΡΠΏΠΎΠ»ΠΎΠΆΠ΅Π½ΠΈΠ΅ Π½Π° ΠΏΠΎΠΊΠΎΠ²ΠΊΠ΅
Β§ 106 Π‘ΡΠ°Π»ΠΈ ΠΏΡΠΈΠΌΠ΅Π½ΡΠ΅ΠΌΡΠ΅ Π΄Π»Ρ ΠΈΠ·Π³ΠΎΡΠΎΠ²Π»Π΅Π½ΠΈΡ ΡΡΠ°ΠΌΠΏΠΎΠ²
Β§ 107.ΠΡΠ°Π²ΠΈΠ»Π° ΡΠΊΡΠΏΠ»ΡΠ°ΡΠ°ΡΠΈΠΈ ΠΈ ΡΡ
ΠΎΠ΄Π° Π·Π° ΡΡΠ°ΠΌΠΏΠ°ΠΌΠΈ
Β§ 108.ΠΡΠ½ΠΎΠ²Π½ΡΠ΅ ΡΠ²Π΅Π΄Π΅Π½ΠΈΡ ΠΎ Π²ΡΠ±ΠΎΡΠ΅ ΡΡΠ°ΠΌΠΏΠΎΠ²ΠΎΡΠ½ΠΎΠ³ΠΎ ΠΌΠΎΠ»ΠΎΡΠ° ΠΈ ΠΎΠΏΡΠ΅Π΄Π΅Π»Π΅Π½ΠΈΠΈ ΡΠ°ΡΡΠ΅ΡΠ½ΠΎΠΉ Π·Π°Π³ΠΎΡΠΎΠ²ΠΊΠΈ
Β§ 109.Π’Π΅Ρ
Π½ΠΎΠ»ΠΎΠ³ΠΈΡΠ΅ΡΠΊΠΈΠ΅ ΠΎΠΏΠ΅ΡΠ°ΡΠΈΠΈ Π³ΠΎΡΡΡΠ΅ΠΉ ΡΡΠ°ΠΌΠΏΠΎΠ²ΠΊΠΈ
Β§ 110.ΠΠΎΠ»ΡΡΠ΅Π½ΠΈΠ΅ ΠΏΡΠΎΡΡΡΡ
ΠΈ ΡΠ»ΠΎΠΆΠ½ΡΡ
ΠΏΠΎΠΊΠΎΠ²ΠΎΠΊ Π² Π½Π΅ΡΠΊΠΎΠ»ΡΠΊΠΈΡ
ΠΏΠΎΡΠ»Π΅Π΄ΠΎΠ²Π°ΡΠ΅Π»ΡΠ½ΠΎ ΠΏΡΠΈΠΌΠ΅Π½ΡΠ΅ΠΌΡΡ
ΡΡΠ°ΠΌΠΏΠ°Ρ
Β§ 111.ΠΠΎΡΡΡΠ°Ρ ΡΡΠ°ΠΌΠΏΠΎΠ²ΠΊΠ° Ρ ΠΏΡΠ΅Π΄Π²Π°ΡΠΈΡΠ΅Π»ΡΠ½ΠΎΠΉ ΠΊΠΎΠ²ΠΊΠΎΠΉ Π·Π°Π³ΠΎΡΠΎΠ²ΠΊΠΈ ΠΏΠΎΠ΄ ΠΌΠΎΠ»ΠΎΡΠ°ΠΌΠΈ ΠΈΠ»ΠΈ Π½Π° Π²Π°Π»ΡΡΠ°Ρ
ΠΠ»Π°Π²Π° XVIII. ΠΠΎΠ²ΠΊΠ° ΡΠ²Π΅ΡΠ½ΡΡ ΡΠΏΠ»Π°Π²ΠΎΠ² ΡΠΏΠ»Π°Π²ΠΎΠ²
Β§ 112. Π‘ΠΏΠ»Π°Π²Ρ ΡΠ²Π΅ΡΠ½ΡΡ
ΠΌΠ΅ΡΠ°Π»Π»ΠΎΠ², ΠΎΠ±ΡΠ°Π±Π°ΡΡΠ²Π°Π΅ΠΌΡΠ΅ ΠΊΠΎΠ²ΠΊΠΎΠΉ ΠΈ ΡΡΠ°ΠΌΠΏΠΎΠ²ΠΊΠΎΠΉ
Β§ 113. ΠΠ»Π°ΡΡΠΈΡΠ½ΠΎΡΡΡ ΡΠ²Π΅ΡΠ½ΡΡ
ΡΠΏΠ»Π°Π²ΠΎΠ²
Β§ 114. ΠΡΠΎΠ±Π΅Π½Π½ΠΎΡΡΠΈ Π½Π°Π³ΡΠ΅Π²Π° ΡΠ²Π΅ΡΠ½ΡΡ
ΡΠΏΠ»Π°Π²ΠΎΠ² ΡΠ²Π΅ΡΠ½ΡΡ
ΡΠΏΠ»Π°Π²ΠΎΠ²
Β§ 115. ΠΡΠΎΠ±Π΅Π½Π½ΠΎΡΡΠΈ ΠΊΠΎΠ²ΠΊΠΈ ΠΈ ΠΎΠ±ΡΠ΅ΠΌΠ½ΠΎΠΉ ΡΡΠ°ΠΌΠΏΠΎΠ²ΠΊΠΈ ΡΠ²Π΅ΡΠ½ΡΡ
ΡΠΏΠ»Π°Π²ΠΎΠ²
Π’Π΅Ρ
Π½ΠΈΡΠ΅ΡΠΊΠ°Ρ Π»ΠΈΡΠ΅ΡΠ°ΡΡΡΠ°.
Π§ΡΠΎ ΡΠ°ΠΊΠΎΠ΅ ΠΊΠΎΠ²ΠΊΠ°? Π Π°Π·Π»ΠΈΡΠ½ΡΠ΅ Π²ΠΈΠ΄Ρ ΠΏΠΎΠΊΠΎΠ²ΠΎΠΊ Π² ΠΏΠΎΠ΄Π΅ΡΠΆΠ°Π½Π½ΠΎΠΌ ΠΏΡΠΎΠΈΠ·Π²ΠΎΠ΄ΡΡΠ²Π΅
ΠΠΎΠ²ΠΊΠ°, ΠΌΠ΅ΡΠΎΠ΄ ΡΠΎΡΠΌΠΎΠ²Π°Π½ΠΈΡ ΠΌΠ΅ΡΠ°Π»Π»Π° Ρ ΠΈΡΠΏΠΎΠ»ΡΠ·ΠΎΠ²Π°Π½ΠΈΠ΅ΠΌ ΡΠΆΠΈΠΌΠ°ΡΡΠΈΡ , Π»ΠΎΠΊΠ°Π»ΠΈΠ·ΠΎΠ²Π°Π½Π½ΡΡ ΡΠΈΠ», Π±ΡΠ» ΠΎΡΠ½ΠΎΠ²Π½ΡΠΌ ΠΌΠ΅ΡΠΎΠ΄ΠΎΠΌ ΠΈΠ·Π³ΠΎΡΠΎΠ²Π»Π΅Π½ΠΈΡ ΠΌΠ΅ΡΠ°Π»Π»Π° ΡΠΎ Π²ΡΠ΅ΠΌΠ΅Π½ Π΄ΡΠ΅Π²Π½ΠΈΡ ΠΌΠ΅ΡΠΎΠΏΠΎΡΠ°ΠΌΡΠ΅Π². Π‘ ΠΌΠΎΠΌΠ΅Π½ΡΠ° ΡΠ²ΠΎΠ΅Π³ΠΎ Π²ΠΎΠ·Π½ΠΈΠΊΠ½ΠΎΠ²Π΅Π½ΠΈΡ Π² ΠΏΠ»ΠΎΠ΄ΠΎΡΠΎΠ΄Π½ΠΎΠΌ ΠΏΠΎΠ»ΡΠΌΠ΅ΡΡΡΠ΅ ΠΊΠΎΠ²ΠΊΠ° ΠΏΡΠ΅ΡΠ΅ΡΠΏΠ΅Π»Π° Π·Π½Π°ΡΠΈΡΠ΅Π»ΡΠ½ΡΠ΅ ΠΈΠ·ΠΌΠ΅Π½Π΅Π½ΠΈΡ, Π² ΡΠ΅Π·ΡΠ»ΡΡΠ°ΡΠ΅ ΡΠ΅Π³ΠΎ ΠΏΡΠΎΡΠ΅ΡΡ ΡΡΠ°Π» Π±ΠΎΠ»Π΅Π΅ ΡΡΡΠ΅ΠΊΡΠΈΠ²Π½ΡΠΌ, Π±ΡΡΡΡΡΠΌ ΠΈ Π΄ΠΎΠ»Π³ΠΎΠ²Π΅ΡΠ½ΡΠΌ. ΠΡΠΎ ΡΠ²ΡΠ·Π°Π½ΠΎ Ρ ΡΠ΅ΠΌ, ΡΡΠΎ ΡΠ΅Π³ΠΎΠ΄Π½Ρ ΠΊΠΎΠ²ΠΊΠ° ΡΠ°ΡΠ΅ Π²ΡΠ΅Π³ΠΎ Π²ΡΠΏΠΎΠ»Π½ΡΠ΅ΡΡΡ Ρ ΠΈΡΠΏΠΎΠ»ΡΠ·ΠΎΠ²Π°Π½ΠΈΠ΅ΠΌ ΠΊΡΠ·Π½Π΅ΡΠ½ΡΡ ΠΏΡΠ΅ΡΡΠΎΠ² ΠΈΠ»ΠΈ ΡΠ΄Π°ΡΠ½ΡΡ ΠΈΠ½ΡΡΡΡΠΌΠ΅Π½ΡΠΎΠ², ΠΊΠΎΡΠΎΡΡΠ΅ ΡΠ°Π±ΠΎΡΠ°ΡΡ ΠΎΡ ΡΠ»Π΅ΠΊΡΡΠΈΡΠ΅ΡΡΠ²Π°, Π³ΠΈΠ΄ΡΠ°Π²Π»ΠΈΠΊΠΈ ΠΈΠ»ΠΈ ΡΠΆΠ°ΡΠΎΠ³ΠΎ Π²ΠΎΠ·Π΄ΡΡ Π°.ΠΠ΅ΠΊΠΎΡΠΎΡΡΠ΅ ΠΈΠ· ΡΠ°ΡΠΏΡΠΎΡΡΡΠ°Π½Π΅Π½Π½ΡΡ ΠΌΠ°ΡΠ΅ΡΠΈΠ°Π»ΠΎΠ², ΠΈΡΠΏΠΎΠ»ΡΠ·ΡΠ΅ΠΌΡΡ Π΄Π»Ρ ΠΊΠΎΠ²ΠΊΠΈ, — ΡΡΠΎ ΡΠ³Π»Π΅ΡΠΎΠ΄ΠΈΡΡΠ°Ρ ΡΡΠ°Π»Ρ, Π»Π΅Π³ΠΈΡΠΎΠ²Π°Π½Π½Π°Ρ ΡΡΠ°Π»Ρ, ΠΌΠΈΠΊΡΠΎΠ»Π΅Π³ΠΈΡΠΎΠ²Π°Π½Π½Π°Ρ ΡΡΠ°Π»Ρ, Π½Π΅ΡΠΆΠ°Π²Π΅ΡΡΠ°Ρ ΡΡΠ°Π»Ρ, Π°Π»ΡΠΌΠΈΠ½ΠΈΠΉ ΠΈ ΡΠΈΡΠ°Π½.
ΠΠ»Ρ ΠΊΠΎΠ²ΠΊΠΈ ΠΈΡΠΏΠΎΠ»ΡΠ·ΡΡΡΡΡ ΡΡΠ°Π΄ΠΈΡΠΈΠΎΠ½Π½ΡΠΉ ΠΌΠΎΠ»ΠΎΡΠΎΠΊ ΠΈ Π½Π°ΠΊΠΎΠ²Π°Π»ΡΠ½Ρ.ΠΠ·ΠΎΠ±ΡΠ°ΠΆΠ΅Π½ΠΈΠ΅ ΠΏΡΠ΅Π΄ΠΎΡΡΠ°Π²Π»Π΅Π½ΠΎ: Shutterstock.com/Drpixel
ΠΠ»Ρ ΡΠ΅Π³ΠΎ Π½ΡΠΆΠ½Π° ΠΊΠΎΠ²ΠΊΠ°?
Π¦Π΅Π»ΡΡ ΠΊΠΎΠ²ΠΊΠΈ ΡΠ²Π»ΡΠ΅ΡΡΡ ΠΈΠ·Π³ΠΎΡΠΎΠ²Π»Π΅Π½ΠΈΠ΅ ΠΌΠ΅ΡΠ°Π»Π»ΠΈΡΠ΅ΡΠΊΠΈΡ Π΄Π΅ΡΠ°Π»Π΅ΠΉ. ΠΠΎ ΡΡΠ°Π²Π½Π΅Π½ΠΈΡ Ρ Π΄ΡΡΠ³ΠΈΠΌΠΈ ΠΌΠ΅ΡΠΎΠ΄Π°ΠΌΠΈ ΠΏΡΠΎΠΈΠ·Π²ΠΎΠ΄ΡΡΠ²Π°, ΠΊΠΎΠ²ΠΊΠ° ΠΌΠ΅ΡΠ°Π»Π»Π° ΠΏΠΎΠ·Π²ΠΎΠ»ΡΠ΅Ρ ΠΏΡΠΎΠΈΠ·Π²ΠΎΠ΄ΠΈΡΡ ΠΎΠ΄Π½ΠΈ ΠΈΠ· ΡΠ°ΠΌΡΡ ΠΏΡΠΎΡΠ½ΡΡ Π΄ΠΎΡΡΡΠΏΠ½ΡΡ Π΄Π΅ΡΠ°Π»Π΅ΠΉ. ΠΠΎ ΠΌΠ΅ΡΠ΅ Π½Π°Π³ΡΠ΅Π²Π° ΠΈ ΠΏΡΠ΅ΡΡΠΎΠ²Π°Π½ΠΈΡ ΠΌΠ΅ΡΠ°Π»Π»Π° ΠΌΠ΅Π»ΠΊΠΈΠ΅ ΡΡΠ΅ΡΠΈΠ½Ρ Π·Π°Π΄Π΅Π»ΡΠ²Π°ΡΡΡΡ, Π° Π»ΡΠ±ΡΠ΅ ΠΏΡΡΡΠΎΡΡ Π² ΠΌΠ΅ΡΠ°Π»Π»Π΅ Π·Π°ΠΊΡΡΠ²Π°ΡΡΡΡ.
ΠΡΠΎΡΠ΅ΡΡ Π³ΠΎΡΡΡΠ΅ΠΉ ΡΡΠ°ΠΌΠΏΠΎΠ²ΠΊΠΈ ΡΠ°ΠΊΠΆΠ΅ ΡΠ°Π·ΡΡΡΠ°Π΅Ρ ΠΏΡΠΈΠΌΠ΅ΡΠΈ Π² ΠΌΠ΅ΡΠ°Π»Π»Π΅ ΠΈ ΠΏΠ΅ΡΠ΅ΡΠ°ΡΠΏΡΠ΅Π΄Π΅Π»ΡΠ΅Ρ ΠΈΡ ΠΏΠΎ ΠΌΠ΅ΡΠ°Π»Π»ΠΎΠΊΠΎΠ½ΡΡΡΡΠΊΡΠΈΡΠΌ. ΠΡΠΎ Π·Π½Π°ΡΠΈΡΠ΅Π»ΡΠ½ΠΎ ΡΠΌΠ΅Π½ΡΡΠ°Π΅Ρ ΠΊΠΎΠ»ΠΈΡΠ΅ΡΡΠ²ΠΎ Π²ΠΊΠ»ΡΡΠ΅Π½ΠΈΠΉ Π² ΠΊΠΎΠ²Π°Π½ΠΎΠΉ Π΄Π΅ΡΠ°Π»ΠΈ. ΠΠΊΠ»ΡΡΠ΅Π½ΠΈΡ ΠΏΡΠ΅Π΄ΡΡΠ°Π²Π»ΡΡΡ ΡΠΎΠ±ΠΎΠΉ ΡΠΎΡΡΠ°Π²Π½ΡΠ΅ ΠΌΠ°ΡΠ΅ΡΠΈΠ°Π»Ρ, ΠΈΠΌΠΏΠ»Π°Π½ΡΠΈΡΠΎΠ²Π°Π½Π½ΡΠ΅ Π²Π½ΡΡΡΡ ΡΡΠ°Π»ΠΈ Π½Π° ΠΏΡΠΎΡΡΠΆΠ΅Π½ΠΈΠΈ Π²ΡΠ΅Π³ΠΎ ΠΏΡΠΎΠΈΠ·Π²ΠΎΠ΄ΡΡΠ²Π°, ΠΊΠΎΡΠΎΡΡΠ΅ Π²ΡΠ·ΡΠ²Π°ΡΡ ΡΠΎΡΠΊΠΈ Π½Π°ΠΏΡΡΠΆΠ΅Π½ΠΈΡ Π² Π³ΠΎΡΠΎΠ²ΡΡ ΠΊΠΎΠ²Π°Π½ΡΡ Π΄Π΅ΡΠ°Π»ΡΡ .
Π ΡΠΎ Π²ΡΠ΅ΠΌΡ ΠΊΠ°ΠΊ ΠΏΡΠΈΠΌΠ΅ΡΠΈ Π½Π΅ΠΎΠ±Ρ ΠΎΠ΄ΠΈΠΌΠΎ ΠΊΠΎΠ½ΡΡΠΎΠ»ΠΈΡΠΎΠ²Π°ΡΡ Π²ΠΎ Π²ΡΠ΅ΠΌΡ Π½Π°ΡΠ°Π»ΡΠ½ΠΎΠ³ΠΎ ΠΏΡΠΎΡΠ΅ΡΡΠ° Π»ΠΈΡΡΡ, ΠΊΠΎΠ²ΠΊΠ° Π΄ΠΎΠΏΠΎΠ»Π½ΠΈΡΠ΅Π»ΡΠ½ΠΎ ΠΎΡΠΈΡΠ°Π΅Ρ ΠΌΠ΅ΡΠ°Π»Π».
ΠΡΡΠ³ΠΎΠΉ ΡΠΏΠΎΡΠΎΠ±, ΠΊΠΎΡΠΎΡΡΠΌ ΠΊΠΎΠ²ΠΊΠ° ΡΠΊΡΠ΅ΠΏΠ»ΡΠ΅Ρ ΠΌΠ΅ΡΠ°Π»Π», — ΡΡΠΎ ΡΠ΅ΡΠ΅Π΄ΠΎΠ²Π°Π½ΠΈΠ΅ Π΅Π³ΠΎ Π·Π΅ΡΠ΅Π½Π½ΠΎΠΉ ΡΡΡΡΠΊΡΡΡΡ, ΠΊΠΎΡΠΎΡΠ°Ρ ΠΏΡΠ΅Π΄ΡΡΠ°Π²Π»ΡΠ΅Ρ ΡΠΎΠ±ΠΎΠΉ ΠΏΠΎΡΠΎΠΊ Π·Π΅ΡΠ΅Π½ ΠΌΠ΅ΡΠ°Π»Π»ΠΈΡΠ΅ΡΠΊΠΎΠ³ΠΎ ΠΌΠ°ΡΠ΅ΡΠΈΠ°Π»Π° ΠΏΡΠΈ Π΅Π³ΠΎ Π΄Π΅ΡΠΎΡΠΌΠ°ΡΠΈΠΈ.ΠΠΎΠΊΠΎΠ²ΠΊΠΎΠΉ ΠΌΠΎΠΆΠ½ΠΎ ΡΠΎΠ·Π΄Π°ΡΡ Π±Π»Π°Π³ΠΎΠΏΡΠΈΡΡΠ½ΡΡ Π·Π΅ΡΠ½ΠΈΡΡΡΡ ΡΡΡΡΠΊΡΡΡΡ, ΡΡΠΎ ΡΠ΄Π΅Π»Π°Π΅Ρ ΠΊΠΎΠ²Π°Π½ΡΠΉ ΠΌΠ΅ΡΠ°Π»Π» Π±ΠΎΠ»Π΅Π΅ ΠΏΡΠΎΡΠ½ΡΠΌ.
ΠΡΠΎΡΠ΅ΡΡ ΠΊΠΎΠ²ΠΊΠΈ ΠΎΡΠ΅Π½Ρ ΡΠ½ΠΈΠ²Π΅ΡΡΠ°Π»Π΅Π½ ΠΈ ΠΌΠΎΠΆΠ΅Ρ ΠΈΡΠΏΠΎΠ»ΡΠ·ΠΎΠ²Π°ΡΡΡΡ ΠΊΠ°ΠΊ Π΄Π»Ρ Π½Π΅Π±ΠΎΠ»ΡΡΠΈΡ Π΄Π΅ΡΠ°Π»Π΅ΠΉ ΡΠ°Π·ΠΌΠ΅ΡΠΎΠΌ Π²ΡΠ΅Π³ΠΎ Π½Π΅ΡΠΊΠΎΠ»ΡΠΊΠΎ Π΄ΡΠΉΠΌΠΎΠ², ΡΠ°ΠΊ ΠΈ Π΄Π»Ρ ΠΊΡΡΠΏΠ½ΡΡ ΠΊΠΎΠΌΠΏΠΎΠ½Π΅Π½ΡΠΎΠ², ΠΊΠΎΡΠΎΡΡΠ΅ Π²Π΅ΡΡΡ Π΄ΠΎ 700 000 ΡΡΠ½ΡΠΎΠ². ΠΠ½ ΠΈΡΠΏΠΎΠ»ΡΠ·ΡΠ΅ΡΡΡ Π΄Π»Ρ ΠΏΡΠΎΠΈΠ·Π²ΠΎΠ΄ΡΡΠ²Π° ΠΎΡΠ²Π΅ΡΡΡΠ²Π΅Π½Π½ΡΡ Π΄Π΅ΡΠ°Π»Π΅ΠΉ ΡΠ°ΠΌΠΎΠ»Π΅ΡΠΎΠ² ΠΈ ΡΡΠ°Π½ΡΠΏΠΎΡΡΠ½ΠΎΠ³ΠΎ ΠΎΠ±ΠΎΡΡΠ΄ΠΎΠ²Π°Π½ΠΈΡ. ΠΠΎΠ²ΠΊΠ° ΡΠ°ΠΊΠΆΠ΅ ΠΈΡΠΏΠΎΠ»ΡΠ·ΡΠ΅ΡΡΡ Π΄Π»Ρ ΡΠΊΡΠ΅ΠΏΠ»Π΅Π½ΠΈΡ ΡΡΡΠ½ΡΡ ΠΈΠ½ΡΡΡΡΠΌΠ΅Π½ΡΠΎΠ², ΡΠ°ΠΊΠΈΡ ΠΊΠ°ΠΊ Π΄ΠΎΠ»ΠΎΡΠ°, Π·Π°ΠΊΠ»Π΅ΠΏΠΊΠΈ, Π²ΠΈΠ½ΡΡ ΠΈ Π±ΠΎΠ»ΡΡ.
ΠΠ°ΠΊΠΈΠ΅ Π±ΡΠ²Π°ΡΡ Π²ΠΈΠ΄Ρ ΠΊΠΎΠ²ΠΊΠΈ?
Π£Π΄Π°Ρ ΠΏΠΎΠΊΠΎΠ²ΠΊΠΈ Π΄Π΅ΡΠΎΡΠΌΠΈΡΡΠ΅Ρ ΠΈ ΡΠΎΡΠΌΠΈΡΡΠ΅Ρ ΠΌΠ΅ΡΠ°Π»Π», ΡΡΠΎ ΠΏΡΠΈΠ²ΠΎΠ΄ΠΈΡ ΠΊ Π½Π΅ΠΏΡΠ΅ΡΡΠ²Π½ΠΎΠΌΡ ΠΏΠΎΡΠΎΠΊΡ Π·Π΅ΡΠ½Π°.ΠΡΠΎ Π·Π°ΡΡΠ°Π²Π»ΡΠ΅Ρ ΠΌΠ΅ΡΠ°Π»Π» ΡΠΎΡ ΡΠ°Π½ΡΡΡ ΡΠ²ΠΎΡ ΠΏΡΠΎΡΠ½ΠΎΡΡΡ. ΠΠΎΠΏΠΎΠ»Π½ΠΈΡΠ΅Π»ΡΠ½ΡΠ΅ ΡΡΡΠ΅ΠΊΡΡ ΡΡΠΎΠ³ΠΎ ΡΠ½ΠΈΠΊΠ°Π»ΡΠ½ΠΎΠ³ΠΎ ΠΏΠΎΡΠΎΠΊΠ° Π·Π΅ΡΠ½Π° Π²ΠΊΠ»ΡΡΠ°ΡΡ ΡΡΡΡΠ°Π½Π΅Π½ΠΈΠ΅ Π΄Π΅ΡΠ΅ΠΊΡΠΎΠ², Π²ΠΊΠ»ΡΡΠ΅Π½ΠΈΠΉ ΠΈ ΠΏΠΎΡΠΈΡΡΠΎΡΡΠΈ Π² ΠΏΡΠΎΠ΄ΡΠΊΡΠ΅. ΠΡΠ΅ ΠΎΠ΄Π½ΠΈΠΌ ΠΏΡΠ΅ΠΈΠΌΡΡΠ΅ΡΡΠ²ΠΎΠΌ ΠΊΠΎΠ²ΠΊΠΈ ΡΠ²Π»ΡΠ΅ΡΡΡ ΠΎΡΠ½ΠΎΡΠΈΡΠ΅Π»ΡΠ½ΠΎ Π½ΠΈΠ·ΠΊΠ°Ρ ΡΡΠΎΠΈΠΌΠΎΡΡΡ, ΡΠ²ΡΠ·Π°Π½Π½Π°Ρ Ρ ΡΠΌΠ΅ΡΠ΅Π½Π½ΡΠΌΠΈ ΠΈ Π΄Π»ΠΈΡΠ΅Π»ΡΠ½ΡΠΌΠΈ ΠΏΡΠΎΠΈΠ·Π²ΠΎΠ΄ΡΡΠ²Π΅Π½Π½ΡΠΌΠΈ ΡΠΈΠΊΠ»Π°ΠΌΠΈ. ΠΠΎΡΠ»Π΅ ΡΠΎΠ·Π΄Π°Π½ΠΈΡ ΠΈΠ½ΡΡΡΡΠΌΠ΅Π½ΡΠΎΠ² Π΄Π»Ρ ΠΊΠΎΠ²ΠΊΠΈ ΠΈΠ·Π΄Π΅Π»ΠΈΡ ΠΌΠΎΠΆΠ½ΠΎ ΠΏΡΠΎΠΈΠ·Π²ΠΎΠ΄ΠΈΡΡ Π½Π° ΠΎΡΠ½ΠΎΡΠΈΡΠ΅Π»ΡΠ½ΠΎ Π²ΡΡΠΎΠΊΠΈΡ ΡΠΊΠΎΡΠΎΡΡΡΡ Ρ ΠΌΠΈΠ½ΠΈΠΌΠ°Π»ΡΠ½ΡΠΌ Π²ΡΠ΅ΠΌΠ΅Π½Π΅ΠΌ ΠΏΡΠΎΡΡΠΎΡ. Π‘ΡΡΠ΅ΡΡΠ²ΡΠ΅Ρ Π΄Π²Π° ΠΎΡΠ½ΠΎΠ²Π½ΡΡ ΡΠΈΠΏΠ° ΠΊΠΎΠ²ΠΊΠΈ: Π³ΠΎΡΡΡΠ°Ρ ΠΈ Ρ ΠΎΠ»ΠΎΠ΄Π½Π°Ρ.
ΠΠΎΡΡΡΠ°Ρ ΡΡΠ°ΠΌΠΏΠΎΠ²ΠΊΠ°
ΠΠ»Ρ Π³ΠΎΡΡΡΠ΅ΠΉ ΡΡΠ°ΠΌΠΏΠΎΠ²ΠΊΠΈ ΠΌΠ΅ΡΠ°Π»Π» Π΄ΠΎΠ»ΠΆΠ΅Π½ Π±ΡΡΡ Π½Π°Π³ΡΠ΅Ρ Π²ΡΡΠ΅ ΡΠ΅ΠΌΠΏΠ΅ΡΠ°ΡΡΡΡ ΡΠ΅ΠΊΡΠΈΡΡΠ°Π»Π»ΠΈΠ·Π°ΡΠΈΠΈ.ΠΡΠΎ ΠΌΠΎΠΆΠ΅Ρ ΠΎΠ·Π½Π°ΡΠ°ΡΡ Π½Π°Π³ΡΠ΅Π² ΠΌΠ΅ΡΠ°Π»Π»ΠΎΠ² Π΄ΠΎ 2300 Π³ΡΠ°Π΄ΡΡΠΎΠ² ΠΏΠΎ Π€Π°ΡΠ΅Π½Π³Π΅ΠΉΡΡ. ΠΡΠ½ΠΎΠ²Π½ΠΎΠ΅ ΠΏΡΠ΅ΠΈΠΌΡΡΠ΅ΡΡΠ²ΠΎ Π³ΠΎΡΡΡΠ΅ΠΉ ΠΊΠΎΠ²ΠΊΠΈ — ΡΠ½ΠΈΠΆΠ΅Π½ΠΈΠ΅ ΡΠ½Π΅ΡΠ³ΠΈΠΈ, Π½Π΅ΠΎΠ±Ρ ΠΎΠ΄ΠΈΠΌΠΎΠΉ Π΄Π»Ρ ΠΏΡΠ°Π²ΠΈΠ»ΡΠ½ΠΎΠ³ΠΎ ΡΠΎΡΠΌΠΎΠ²Π°Π½ΠΈΡ ΠΌΠ΅ΡΠ°Π»Π»Π°. ΠΡΠΎ ΡΠ²ΡΠ·Π°Π½ΠΎ Ρ ΡΠ΅ΠΌ, ΡΡΠΎ ΡΡΠ΅Π·ΠΌΠ΅ΡΠ½ΠΎΠ΅ Π½Π°Π³ΡΠ΅Π²Π°Π½ΠΈΠ΅ ΡΠ½ΠΈΠΆΠ°Π΅Ρ ΠΏΡΠ΅Π΄Π΅Π» ΡΠ΅ΠΊΡΡΠ΅ΡΡΠΈ ΠΈ ΡΠ»ΡΡΡΠ°Π΅Ρ ΠΏΠ»Π°ΡΡΠΈΡΠ½ΠΎΡΡΡ. ΠΠΎΡΡΡΠΈΠ΅ ΠΊΠΎΠ²Π°Π½ΡΠ΅ ΠΈΠ·Π΄Π΅Π»ΠΈΡ ΡΠ°ΠΊΠΆΠ΅ Π²ΡΠΈΠ³ΡΡΠ²Π°ΡΡ ΠΎΡ ΡΡΡΡΠ°Π½Π΅Π½ΠΈΡ Ρ ΠΈΠΌΠΈΡΠ΅ΡΠΊΠΈΡ Π½Π΅ΡΠΎΠΎΡΠ²Π΅ΡΡΡΠ²ΠΈΠΉ.
ΠΡΠΆΠ½Π° ΠΊΠΎΠΌΠΏΠ°Π½ΠΈΡ ΠΏΠΎ Π³ΠΎΡΡΡΠ΅ΠΉ ΡΡΠ°ΠΌΠΏΠΎΠ²ΠΊΠ΅? ΠΠΎΠΌΠΏΠ°Π½ΠΈΡ Thomas ‘Supplier Discovery ΠΈΠΌΠ΅Π΅Ρ ΠΏΡΠΎΠ²Π΅ΡΠ΅Π½Π½ΡΠΉ ΡΠΏΠΈΡΠΎΠΊ ΠΊΠΎΠΌΠΏΠ°Π½ΠΈΠΉ ΠΏΠΎ Π³ΠΎΡΡΡΠ΅ΠΉ ΡΡΠ°ΠΌΠΏΠΎΠ²ΠΊΠ΅ Π² Π‘Π¨Π ΠΈ ΠΠ°Π½Π°Π΄Π΅.
Π₯ΠΎΠ»ΠΎΠ΄Π½Π°Ρ ΡΡΠ°ΠΌΠΏΠΎΠ²ΠΊΠ°
Π₯ΠΎΠ»ΠΎΠ΄Π½Π°Ρ ΠΊΠΎΠ²ΠΊΠ° ΠΎΠ±ΡΡΠ½ΠΎ ΠΎΡΠ½ΠΎΡΠΈΡΡΡ ΠΊ ΠΊΠΎΠ²ΠΊΠ΅ ΠΌΠ΅ΡΠ°Π»Π»Π° ΠΏΡΠΈ ΠΊΠΎΠΌΠ½Π°ΡΠ½ΠΎΠΉ ΡΠ΅ΠΌΠΏΠ΅ΡΠ°ΡΡΡΠ΅, Ρ ΠΎΡΡ Π²ΠΎΠ·ΠΌΠΎΠΆΠ½Π° Π»ΡΠ±Π°Ρ ΡΠ΅ΠΌΠΏΠ΅ΡΠ°ΡΡΡΠ° Π½ΠΈΠΆΠ΅ ΡΠ΅ΠΊΡΠΈΡΡΠ°Π»Π»ΠΈΠ·Π°ΡΠΈΠΈ.ΠΠ½ΠΎΠ³ΠΈΠ΅ ΠΌΠ΅ΡΠ°Π»Π»Ρ, ΡΠ°ΠΊΠΈΠ΅ ΠΊΠ°ΠΊ ΡΡΠ°Π»Ρ Ρ Π²ΡΡΠΎΠΊΠΈΠΌ ΡΠΎΠ΄Π΅ΡΠΆΠ°Π½ΠΈΠ΅ΠΌ ΡΠ³Π»Π΅ΡΠΎΠ΄Π°, ΠΏΡΠΎΡΡΠΎ ΡΠ»ΠΈΡΠΊΠΎΠΌ ΠΏΡΠΎΡΠ½Ρ Π΄Π»Ρ Ρ ΠΎΠ»ΠΎΠ΄Π½ΠΎΠΉ ΠΊΠΎΠ²ΠΊΠΈ. ΠΠ΅ΡΠΌΠΎΡΡΡ Π½Π° ΡΡΠΎ ΠΏΡΠ΅ΠΏΡΡΡΡΠ²ΠΈΠ΅, Ρ ΠΎΠ»ΠΎΠ΄Π½Π°Ρ ΠΊΠΎΠ²ΠΊΠ° ΠΏΡΠ΅Π²ΠΎΡΡ ΠΎΠ΄ΠΈΡ ΡΠ²ΠΎΠ΅Π³ΠΎ Π±ΠΎΠ»Π΅Π΅ ΡΠ΅ΠΏΠ»ΠΎΠ³ΠΎ ΡΠΊΠ²ΠΈΠ²Π°Π»Π΅Π½ΡΠ°, ΠΊΠΎΠ³Π΄Π° ΡΠ΅ΡΡ ΠΈΠ΄Π΅Ρ ΠΎ ΡΡΠ°Π½Π΄Π°ΡΡΠ°Ρ ΠΊΠΎΠ½ΡΡΠΎΠ»Ρ ΡΠ°Π·ΠΌΠ΅ΡΠΎΠ², ΠΎΠ΄Π½ΠΎΡΠΎΠ΄Π½ΠΎΡΡΠΈ ΠΏΡΠΎΠ΄ΡΠΊΡΠ°, ΠΎΠ±ΡΠ°Π±ΠΎΡΠΊΠΈ ΠΏΠΎΠ²Π΅ΡΡ Π½ΠΎΡΡΠΈ ΠΈ Π·Π°Π³ΡΡΠ·Π½Π΅Π½ΠΈΡ. Π₯ΠΎΠ»ΠΎΠ΄Π½Π°Ρ ΠΊΠΎΠ²ΠΊΠ° Π²ΠΊΠ»ΡΡΠ°Π΅Ρ Π² ΡΠ΅Π±Ρ ΠΌΠ½ΠΎΠΆΠ΅ΡΡΠ²ΠΎ ΠΌΠ΅ΡΠΎΠ΄ΠΎΠ² ΠΊΠΎΠ²ΠΊΠΈ, Π²ΠΊΠ»ΡΡΠ°Ρ Π³ΠΈΠ±ΠΊΡ, ΡΠΊΡΡΡΡΠ·ΠΈΡ, Ρ ΠΎΠ»ΠΎΠ΄Π½ΠΎΠ΅ Π²ΠΎΠ»ΠΎΡΠ΅Π½ΠΈΠ΅, ΡΠ΅ΠΊΠ°Π½ΠΊΡ ΠΈ Ρ ΠΎΠ»ΠΎΠ΄Π½ΡΡ Π²ΡΡΠ°Π΄ΠΊΡ. ΠΠ΄Π½Π°ΠΊΠΎ ΡΠ°ΠΊΠ°Ρ ΠΏΠΎΠ²ΡΡΠ΅Π½Π½Π°Ρ ΡΠ½ΠΈΠ²Π΅ΡΡΠ°Π»ΡΠ½ΠΎΡΡΡ ΠΎΠ±Ρ ΠΎΠ΄ΠΈΡΡΡ Π΄ΠΎΡΠΎΠ³ΠΎ, ΠΏΠΎΡΠΊΠΎΠ»ΡΠΊΡ Ρ ΠΎΠ»ΠΎΠ΄Π½Π°Ρ ΡΡΠ°ΠΌΠΏΠΎΠ²ΠΊΠ° ΡΡΠ΅Π±ΡΠ΅Ρ Π±ΠΎΠ»Π΅Π΅ ΠΌΠΎΡΠ½ΠΎΠ³ΠΎ ΠΎΠ±ΠΎΡΡΠ΄ΠΎΠ²Π°Π½ΠΈΡ ΠΈ ΠΌΠΎΠΆΠ΅Ρ ΠΏΠΎΡΡΠ΅Π±ΠΎΠ²Π°ΡΡ ΠΈΡΠΏΠΎΠ»ΡΠ·ΠΎΠ²Π°Π½ΠΈΡ ΠΏΡΠΎΠΌΠ΅ΠΆΡΡΠΎΡΠ½ΡΡ ΠΎΡΠΆΠΈΠ³ΠΎΠ².
ΠΡΠΆΠ½Π° ΠΊΠΎΠΌΠΏΠ°Π½ΠΈΡ ΠΏΠΎ Ρ ΠΎΠ»ΠΎΠ΄Π½ΠΎΠΉ ΠΊΠΎΠ²ΠΊΠ΅? ΠΠΎΠΌΠΏΠ°Π½ΠΈΡ Thomas ‘Supplier Discovery ΠΈΠΌΠ΅Π΅Ρ ΠΏΡΠΎΠ²Π΅ΡΠ΅Π½Π½ΡΠΉ ΡΠΏΠΈΡΠΎΠΊ ΠΊΠΎΠΌΠΏΠ°Π½ΠΈΠΉ ΠΏΠΎ Ρ ΠΎΠ»ΠΎΠ΄Π½ΠΎΠΉ ΡΡΠ°ΠΌΠΏΠΎΠ²ΠΊΠ΅ Π² Π‘Π¨Π ΠΈ ΠΠ°Π½Π°Π΄Π΅.
ΠΠ»Ρ ΠΏΠΎΠ»ΡΡΠ΅Π½ΠΈΡ Π±ΠΎΠ»Π΅Π΅ ΠΏΠΎΠ΄ΡΠΎΠ±Π½ΠΎΠΉ ΠΈΠ½ΡΠΎΡΠΌΠ°ΡΠΈΠΈ ΠΏΠΎ Π»ΡΠ±ΠΎΠΌΡ ΠΈΠ· ΡΡΠΈΡ ΠΏΡΠΎΡΠ΅ΡΡΠΎΠ², ΠΏΠΎΠΆΠ°Π»ΡΠΉΡΡΠ°, ΠΏΡΠΎΡΡΠΈΡΠ΅ Π½Π°ΡΠ΅ ΠΏΠΎΠ»Π½ΠΎΠ΅ ΡΡΠΊΠΎΠ²ΠΎΠ΄ΡΡΠ²ΠΎ ΠΏΠΎ Π³ΠΎΡΡΡΠ΅ΠΉ ΠΈ Ρ ΠΎΠ»ΠΎΠ΄Π½ΠΎΠΉ ΡΡΠ°ΠΌΠΏΠΎΠ²ΠΊΠ΅.
ΠΠΎΡΡΡΠ°Ρ ΠΊΠΎΠ²ΠΊΠ° ΠΈΡΠΏΠΎΠ»ΡΠ·ΡΠ΅ΡΡΡ Π΄Π»Ρ ΠΈΠ·Π³ΠΎΡΠΎΠ²Π»Π΅Π½ΠΈΡ Π°Π²ΡΠΎΠΌΠΎΠ±ΠΈΠ»ΡΠ½ΡΡ Π΄Π΅ΡΠ°Π»Π΅ΠΉ.ΠΠ·ΠΎΠ±ΡΠ°ΠΆΠ΅Π½ΠΈΠ΅ ΠΏΡΠ΅Π΄ΠΎΡΡΠ°Π²Π»Π΅Π½ΠΎ: Shutterstock.com/Aumm graphixphoto
ΠΠ°ΠΊΠΈΠ΅ ΡΡΡΠ΅ΡΡΠ²ΡΡΡ ΠΏΡΠΎΡΠ΅ΡΡΡ ΠΊΠΎΠ²ΠΊΠΈ?
ΠΠΎΠΌΠΈΠΌΠΎ ΠΎΡΠ½ΠΎΠ²Π½ΠΎΠΉ Π³ΠΎΡΡΡΠ΅ΠΉ ΠΈ Ρ ΠΎΠ»ΠΎΠ΄Π½ΠΎΠΉ ΡΡΠ°ΠΌΠΏΠΎΠ²ΠΊΠΈ, ΡΡΡΠ΅ΡΡΠ²ΡΠ΅Ρ ΠΌΠ½ΠΎΠΆΠ΅ΡΡΠ²ΠΎ ΡΠΏΠ΅ΡΠΈΡΠΈΡΠ΅ΡΠΊΠΈΡ ΠΏΡΠΎΡΠ΅ΡΡΠΎΠ².ΠΡΠΎΡ ΡΠΈΡΠΎΠΊΠΈΠΉ ΡΠΏΠ΅ΠΊΡΡ ΠΏΡΠΎΡΠ΅ΡΡΠΎΠ² ΠΌΠΎΠΆΠ½ΠΎ ΡΠ³ΡΡΠΏΠΏΠΈΡΠΎΠ²Π°ΡΡ Π² ΡΡΠΈ ΠΎΡΠ½ΠΎΠ²Π½ΡΠ΅ Π·ΠΎΠ½ΡΠΈΡΠ½ΡΠ΅ Π³ΡΡΠΏΠΏΡ:
Π€ΠΎΡΠΌΠΈΡΠΎΠ²Π°Π½ΠΈΠ΅ Π²ΡΡΡΠΆΠΊΠΈ ΡΠΌΠ΅Π½ΡΡΠ°Π΅Ρ ΡΠΈΡΠΈΠ½Ρ
ΠΈΠ·Π΄Π΅Π»ΠΈΡ ΠΈ ΡΠ²Π΅Π»ΠΈΡΠΈΠ²Π°Π΅Ρ Π΄Π»ΠΈΠ½Ρ. ΠΡΡΠ°ΠΆΠ΅Π½Π½Π°Ρ ΠΊΠΎΠ²ΠΊΠ° ΡΠ²Π΅Π»ΠΈΡΠΈΠ²Π°Π΅Ρ ΡΠΈΡΠΈΠ½Ρ ΠΈΠ·Π΄Π΅Π»ΠΈΠΉ ΠΈ ΡΠΌΠ΅Π½ΡΡΠ°Π΅Ρ Π΄Π»ΠΈΠ½Ρ. Π€ΠΎΡΠΌΠΎΠ²ΠΊΠ° ΡΠΆΠ°ΡΠΈΠ΅ΠΌ ΠΎΠ±Π΅ΡΠΏΠ΅ΡΠΈΠ²Π°Π΅Ρ ΠΏΠΎΡΠΎΠΊ ΡΡΠ°ΠΌΠΏΠΎΠ²ΠΊΠΈ Π² Π½Π΅ΡΠΊΠΎΠ»ΡΠΊΠΈΡ ΠΈΠ»ΠΈ Π½Π°ΡΡΡΠ°ΠΈΠ²Π°Π΅ΠΌΡΡ Π½Π°ΠΏΡΠ°Π²Π»Π΅Π½ΠΈΡΡ .
ΠΡΠΈ ΡΡΠΈ ΠΊΠ°ΡΠ΅Π³ΠΎΡΠΈΠΈ Π²ΠΊΠ»ΡΡΠ°ΡΡ Π² ΡΠ΅Π±Ρ ΠΌΠ½ΠΎΠΆΠ΅ΡΡΠ²ΠΎ ΡΠ°Π·Π»ΠΈΡΠ½ΡΡ ΠΌΠ΅ΡΠΎΠ΄ΠΎΠ² ΠΊΠΎΠ²ΠΊΠΈ ΠΌΠ΅ΡΠ°Π»Π»Π°.
ΠΡΠΎΡΠ΅ΡΡ ΠΏΡΡΠΌΠΎΠΉ ΡΡΠ°ΠΌΠΏΠΎΠ²ΠΊΠΈ
ΠΠ°ΠΏΠ΅Π»ΡΠ½Π°Ρ ΠΊΠΎΠ²ΠΊΠ° ΠΏΠΎΠ»ΡΡΠΈΠ»Π° ΡΠ²ΠΎΠ΅ Π½Π°Π·Π²Π°Π½ΠΈΠ΅ ΠΎΡ ΠΏΡΠΎΡΠ΅ΡΡΠ° ΠΏΠ°Π΄Π΅Π½ΠΈΡ ΠΌΠΎΠ»ΠΎΡΠΊΠ° Π½Π° ΠΌΠ΅ΡΠ°Π»Π» Π΄Π»Ρ ΠΏΡΠΈΠ΄Π°Π½ΠΈΡ Π΅ΠΌΡ ΡΠΎΡΠΌΡ ΡΡΠ°ΠΌΠΏΠ°.ΠΠ°ΡΡΠΈΡΠ° — ΡΡΠΎ ΠΏΠΎΠ²Π΅ΡΡ Π½ΠΎΡΡΡ, ΠΊΠΎΡΠΎΡΠ°Ρ ΠΊΠΎΠ½ΡΠ°ΠΊΡΠΈΡΡΠ΅Ρ Ρ ΠΌΠ΅ΡΠ°Π»Π»ΠΎΠΌ. Π‘ΡΡΠ΅ΡΡΠ²ΡΠ΅Ρ Π΄Π²Π° ΡΠΈΠΏΠ° ΠΊΠΎΠ²ΠΊΠΈ ΠΌΠ΅ΡΠΎΠ΄ΠΎΠΌ ΠΏΡΡΠΌΠΎΠΉ ΡΡΠ°ΠΌΠΏΠΎΠ²ΠΊΠΈ: ΡΡΠ°ΠΌΠΏΠΎΠ²ΠΊΠ° Π² ΠΎΡΠΊΡΡΡΡΡ ΡΡΠ°ΠΌΠΏΠ°Ρ ΠΈ ΡΡΠ°ΠΌΠΏΠΎΠ²ΠΊΠ° Π² Π·Π°ΠΊΡΡΡΡΡ ΡΡΠ°ΠΌΠΏΠ°Ρ . Π¨ΡΠ°ΠΌΠΏΡ ΠΎΠ±ΡΡΠ½ΠΎ ΠΈΠΌΠ΅ΡΡ ΠΏΠ»ΠΎΡΠΊΡΡ ΡΠΎΡΠΌΡ, Π° Π½Π΅ΠΊΠΎΡΠΎΡΡΠ΅ ΠΈΠ· Π½ΠΈΡ ΠΈΠΌΠ΅ΡΡ ΠΏΠΎΠ²Π΅ΡΡ Π½ΠΎΡΡΡ ΠΎΡΠΎΠ±ΠΎΠΉ ΡΠΎΡΠΌΡ Π΄Π»Ρ ΡΠΏΠ΅ΡΠΈΠ°Π»ΡΠ½ΡΡ ΠΎΠΏΠ΅ΡΠ°ΡΠΈΠΉ.
ΠΡΠΎΡΠ΅ΡΡ ΠΎΡΠΊΡΡΡΠΎΠΉ ΡΡΠ°ΠΌΠΏΠΎΠ²ΠΊΠΈ
ΠΠΎΠ³Π΄Π° ΠΏΠ»ΠΎΡΠΊΠΈΠ΅ ΡΡΠ°ΠΌΠΏΡ Π±Π΅Π· ΠΏΡΠ΅Π΄Π²Π°ΡΠΈΡΠ΅Π»ΡΠ½ΠΎ Π²ΡΡΠ΅Π·Π°Π½Π½ΡΡ ΠΏΡΠΎΡΠΈΠ»Π΅ΠΉ ΡΡΠ°ΡΡΠ²ΡΡΡ Π² ΠΊΠΎΠ²ΠΊΠ΅, ΠΏΡΠΎΡΠ΅ΡΡ ΡΡΠ°ΠΌΠΏΠΎΠ²ΠΊΠΈ Π½Π°Π·ΡΠ²Π°Π΅ΡΡΡ ΠΎΡΠΊΡΡΡΠΎΠΉ ΡΡΠ°ΠΌΠΏΠΎΠ²ΠΊΠΎΠΉ (ΠΈΠ»ΠΈ ΠΊΡΠ·Π½Π΅ΡΠ½ΠΎΠΉ ΠΊΠΎΠ²ΠΊΠΎΠΉ). ΠΡΠΊΡΡΡΠ°Ρ ΠΊΠΎΠ½ΡΡΡΡΠΊΡΠΈΡ ΠΏΠΎΠ·Π²ΠΎΠ»ΡΠ΅Ρ ΠΌΠ΅ΡΠ°Π»Π»Ρ ΡΠ΅ΡΡ ΠΏΠΎΠ²ΡΡΠ΄Ρ, ΠΊΡΠΎΠΌΠ΅ ΡΠΎΠ³ΠΎ ΠΌΠ΅ΡΡΠ°, Π³Π΄Π΅ ΠΎΠ½ ΠΊΠ°ΡΠ°Π΅ΡΡΡ ΠΌΠ°ΡΡΠΈΡΡ.ΠΠ»Ρ Π΄ΠΎΡΡΠΈΠΆΠ΅Π½ΠΈΡ ΠΌΠ°ΠΊΡΠΈΠΌΠ°Π»ΡΠ½ΡΡ ΡΠ΅Π·ΡΠ»ΡΡΠ°ΡΠΎΠ² ΠΏΡΠ°Π²ΠΈΠ»ΡΠ½ΠΎΠ΅ ΠΏΠ΅ΡΠ΅ΠΌΠ΅ΡΠ΅Π½ΠΈΠ΅ Π·Π°Π³ΠΎΡΠΎΠ²ΠΊΠΈ, ΠΊΠΎΡΠΎΡΠ°Ρ Π΄ΠΎΠ»ΠΆΠ½Π° ΡΠΎΡΡΠ°Π²Π»ΡΡΡ Π±ΠΎΠ»Π΅Π΅ 200 000 ΡΡΠ½ΡΠΎΠ². ΠΏΠΎ Π²Π΅ΡΡ ΠΈ Π΄Π»ΠΈΠ½Π΅ 80 ΡΡΡΠΎΠ², ΠΈΠΌΠ΅Π΅Ρ Π²Π°ΠΆΠ½ΠΎΠ΅ Π·Π½Π°ΡΠ΅Π½ΠΈΠ΅. ΠΡΠΎ ΠΏΠΎΠ»Π΅Π·Π½ΠΎ Π΄Π»Ρ ΠΌΠ΅Π»ΠΊΠΎΡΠ΅ΡΠΈΠΉΠ½ΠΎΠΉ Ρ ΡΠ΄ΠΎΠΆΠ΅ΡΡΠ²Π΅Π½Π½ΠΎΠΉ ΠΊΠΎΠ²ΠΊΠΈ ΠΈΠ»ΠΈ Π΄Π»Ρ ΡΠΎΡΠΌΠΎΠ²Π°Π½ΠΈΡ ΡΠ»ΠΈΡΠΊΠΎΠ² ΠΏΠ΅ΡΠ΅Π΄ ΠΌΠ΅ΡΠ°ΠΌΠΈ Π²ΡΠΎΡΠΈΡΠ½ΠΎΠΉ ΠΎΠ±ΡΠ°Π±ΠΎΡΠΊΠΈ. ΠΠΎΠΊΠΎΠ²ΠΊΠ° Π² ΠΎΡΠΊΡΡΡΡΡ ΡΡΠ°ΠΌΠΏΠ°Ρ ΠΏΠΎΠ·Π²ΠΎΠ»ΡΠ΅Ρ ΡΠΎΠ·Π΄Π°Π²Π°ΡΡ ΠΈΠ·Π΄Π΅Π»ΠΈΡ Ρ Π»ΡΡΡΠΈΠΌ ΡΠΎΠΏΡΠΎΡΠΈΠ²Π»Π΅Π½ΠΈΠ΅ΠΌ ΡΡΡΠ°Π»ΠΎΡΡΠΈ ΠΈ ΠΏΡΠΎΡΠ½ΠΎΡΡΡΡ, Π° ΡΠ°ΠΊΠΆΠ΅ ΡΠ½ΠΈΠΆΠ°Π΅Ρ Π²Π΅ΡΠΎΡΡΠ½ΠΎΡΡΡ ΠΎΡΠΈΠ±ΠΊΠΈ ΠΈΠ»ΠΈ ΠΎΠ±ΡΠ°Π·ΠΎΠ²Π°Π½ΠΈΡ ΠΎΡΠ²Π΅ΡΡΡΠΈΠΉ. ΠΠ³ΠΎ ΡΠ°ΠΊΠΆΠ΅ ΠΌΠΎΠΆΠ½ΠΎ ΠΈΡΠΏΠΎΠ»ΡΠ·ΠΎΠ²Π°ΡΡ Π΄Π»Ρ Π±ΠΎΠ»Π΅Π΅ ΠΌΠ΅Π»ΠΊΠΎΠ³ΠΎ ΡΠ°Π·ΠΌΠ΅ΡΠ° Π·Π΅ΡΠ½Π°, ΡΠ΅ΠΌ Π² Π΄ΡΡΠ³ΠΈΡ ΠΏΡΠΎΡΠ΅ΡΡΠ°Ρ .
ΠΡΠΎΡΠ΅ΡΡ ΡΡΠ°ΠΌΠΏΠΎΠ²ΠΊΠΈ Π² Π·Π°ΠΊΡΡΡΠΎΠΌ ΡΠΎΡΡΠΎΡΠ½ΠΈΠΈ
ΠΠΎΠΊΠΎΠ²ΠΊΠ° Π² Π·Π°ΠΊΡΡΡΡΡ ΡΡΠ°ΠΌΠΏΠ°Ρ , ΠΈΠ½ΠΎΠ³Π΄Π° Π½Π°Π·ΡΠ²Π°Π΅ΠΌΠ°Ρ ΡΡΠ°ΠΌΠΏΠΎΠ²ΠΊΠΎΠΉ Π² ββΡΡΠ°ΠΌΠΏΠ°Ρ , ΠΏΡΠ΅Π΄ΠΏΠΎΠ»Π°Π³Π°Π΅Ρ ΠΈΡΠΏΠΎΠ»ΡΠ·ΠΎΠ²Π°Π½ΠΈΠ΅ ΠΏΡΠ΅ΡΡ-ΡΠΎΡΠΌ.ΠΡΠΈ ΡΠΎΡΠΌΡ ΠΏΡΠΈΠΊΡΠ΅ΠΏΠ»Π΅Π½Ρ ΠΊ ΠΎΠΏΠΎΡΠ΅, Π² ΡΠΎ Π²ΡΠ΅ΠΌΡ ΠΊΠ°ΠΊ ΠΌΠΎΠ»ΠΎΡ Π·Π°ΡΡΠ°Π²Π»ΡΠ΅Ρ ΡΠ°ΡΠΏΠ»Π°Π²Π»Π΅Π½Π½ΡΠΉ ΠΌΠ΅ΡΠ°Π»Π» ΡΠ΅ΡΡ Π² ΠΏΠΎΠ»ΠΎΡΡΠΈ ΠΌΠ°ΡΡΠΈΡΡ. ΠΡΠΈ ΠΊΠΎΠ²ΠΊΠ΅ ΡΠ»ΠΎΠΆΠ½ΠΎΠΉ Π³Π΅ΠΎΠΌΠ΅ΡΡΠΈΠΈ ΡΠ°ΡΡΠΎ ΠΈΡΠΏΠΎΠ»ΡΠ·ΡΡΡΡΡ ΠΌΠ½ΠΎΠΆΠ΅ΡΡΠ²Π΅Π½Π½ΡΠ΅ ΡΠ΄Π°ΡΡ ΠΈ / ΠΈΠ»ΠΈ ΠΏΠΎΠ»ΠΎΡΡΠΈ ΡΡΠ°ΠΌΠΏΠ°. ΠΡΡΠΎΠΊΠΈΠ΅ Π½Π°ΡΠ°Π»ΡΠ½ΡΠ΅ Π·Π°ΡΡΠ°ΡΡ Π½Π° ΠΈΠ½ΡΡΡΡΠΌΠ΅Π½Ρ Π΄Π΅Π»Π°ΡΡ ΠΊΠΎΠ²ΠΊΡ Π² Π·Π°ΠΊΡΡΡΡΡ ΡΡΠ°ΠΌΠΏΠ°Ρ Π΄ΠΎΡΠΎΠ³ΠΎΡΡΠΎΡΡΠ΅ΠΉ Π΄Π»Ρ ΠΊΡΠ°ΡΠΊΠΎΡΡΠΎΡΠ½ΡΡ ΠΎΠΏΠ΅ΡΠ°ΡΠΈΠΉ, Π½ΠΎ ΠΏΡΠΎΡΠ΅ΡΡ ΠΊΠΎΠ²ΠΊΠΈ ΡΡΠ°Π½ΠΎΠ²ΠΈΡΡΡ ΡΠ΅Π½ΡΠ°Π±Π΅Π»ΡΠ½ΡΠΌ ΠΏΠΎ ΠΌΠ΅ΡΠ΅ ΡΠ²Π΅Π»ΠΈΡΠ΅Π½ΠΈΡ ΠΊΠΎΠ»ΠΈΡΠ΅ΡΡΠ²Π° ΠΏΡΠΎΠΈΠ·Π²ΠΎΠ΄ΠΈΠΌΡΡ Π΄Π΅ΡΠ°Π»Π΅ΠΉ. ΠΠΎΠ²ΠΊΠ° Π² Π·Π°ΠΊΡΡΡΡΡ ΡΡΠ°ΠΌΠΏΠ°Ρ ΡΠ°ΠΊΠΆΠ΅ ΠΎΠ±Π΅ΡΠΏΠ΅ΡΠΈΠ²Π°Π΅Ρ ΠΈΡΠΊΠ»ΡΡΠΈΡΠ΅Π»ΡΠ½ΡΡ ΠΏΡΠΎΡΠ½ΠΎΡΡΡ ΠΏΠΎ ΡΡΠ°Π²Π½Π΅Π½ΠΈΡ Ρ Π°Π»ΡΡΠ΅ΡΠ½Π°ΡΠΈΠ²Π½ΡΠΌΠΈ ΠΌΠ΅ΡΠΎΠ΄Π°ΠΌΠΈ. Π Π°ΡΠΏΡΠΎΡΡΡΠ°Π½Π΅Π½Π½ΡΠ΅ ΠΎΠ±Π»Π°ΡΡΠΈ ΠΏΡΠΈΠΌΠ΅Π½Π΅Π½ΠΈΡ ΡΡΠ°ΠΌΠΏΠΎΠ²ΠΊΠΈ Π² Π·Π°ΠΊΡΡΡΡΡ ΡΡΠ°ΠΌΠΏΠ°Ρ Π²ΠΊΠ»ΡΡΠ°ΡΡ ΠΏΡΠΎΠΈΠ·Π²ΠΎΠ΄ΡΡΠ²ΠΎ Π°Π²ΡΠΎΠΌΠΎΠ±ΠΈΠ»ΡΠ½ΡΡ ΠΊΠΎΠΌΠΏΠΎΠ½Π΅Π½ΡΠΎΠ² ΠΈ Π°ΠΏΠΏΠ°ΡΠ°ΡΠ½ΡΡ ΠΈΠ½ΡΡΡΡΠΌΠ΅Π½ΡΠΎΠ².
ΠΡΠΎΡΠ΅ΡΡ ΠΊΠΎΠ²ΠΊΠΈ Π½Π° ΠΏΡΠ΅ΡΡΠ΅
ΠΡΠΈ ΠΊΠΎΠ²ΠΊΠ΅ Π½Π° ΠΏΡΠ΅ΡΡΠ΅ ΠΎΡΠ½ΠΎΠ²Π½ΡΠΌ ΡΠ°ΠΊΡΠΎΡΠΎΠΌ ΡΠΎΡΠΌΠΎΠ²Π°Π½ΠΈΡ ΡΠ²Π»ΡΠ΅ΡΡΡ ΡΠΆΠ°ΡΠΈΠ΅. ΠΠ΅ΡΠ°Π»Π» Π½Π°Ρ ΠΎΠ΄ΠΈΡΡΡ Π½Π° Π½Π΅ΠΏΠΎΠ΄Π²ΠΈΠΆΠ½ΠΎΠΌ ΡΡΠ°ΠΌΠΏΠ΅, Π² ΡΠΎ Π²ΡΠ΅ΠΌΡ ΠΊΠ°ΠΊ ΠΏΡΠ΅ΡΡΡΡΡΠΈΠΉ ΡΡΠ°ΠΌΠΏ ΠΎΠΊΠ°Π·ΡΠ²Π°Π΅Ρ ΠΏΠΎΡΡΠΎΡΠ½Π½ΠΎΠ΅ Π΄Π°Π²Π»Π΅Π½ΠΈΠ΅, Π΄ΠΎΡΡΠΈΠ³Π°Ρ ΠΆΠ΅Π»Π°Π΅ΠΌΠΎΠΉ ΡΠΎΡΠΌΡ. ΠΡΠ΅ΠΌΡ ΠΊΠΎΠ½ΡΠ°ΠΊΡΠ° ΠΌΠ΅ΡΠ°Π»Π»Π° Ρ ΠΌΠ°ΡΡΠΈΡΠ°ΠΌΠΈ Π·Π½Π°ΡΠΈΡΠ΅Π»ΡΠ½ΠΎ Π±ΠΎΠ»ΡΡΠ΅, ΡΠ΅ΠΌ Ρ Π΄ΡΡΠ³ΠΈΡ ΡΠΈΠΏΠΎΠ² ΠΊΠΎΠ²ΠΊΠΈ, Π½ΠΎ ΠΏΡΠΎΡΠ΅ΡΡ ΠΊΠΎΠ²ΠΊΠΈ Π²ΡΠΈΠ³ΡΡΠ²Π°Π΅Ρ ΠΎΡ Π²ΠΎΠ·ΠΌΠΎΠΆΠ½ΠΎΡΡΠΈ ΠΎΠ΄Π½ΠΎΠ²ΡΠ΅ΠΌΠ΅Π½Π½ΠΎΠΉ Π΄Π΅ΡΠΎΡΠΌΠ°ΡΠΈΠΈ Π²ΡΠ΅Π³ΠΎ ΠΈΠ·Π΄Π΅Π»ΠΈΡ, Π² ΠΎΡΠ»ΠΈΡΠΈΠ΅ ΠΎΡ Π»ΠΎΠΊΠ°Π»ΠΈΠ·ΠΎΠ²Π°Π½Π½ΠΎΠ³ΠΎ ΡΡΠ°ΡΡΠΊΠ°. ΠΡΠ΅ ΠΎΠ΄Π½ΠΈΠΌ ΠΏΡΠ΅ΠΈΠΌΡΡΠ΅ΡΡΠ²ΠΎΠΌ ΠΊΠΎΠ²ΠΎΡΠ½ΠΎΠ³ΠΎ ΠΏΡΠ΅ΡΡΠ° ΡΠ²Π»ΡΠ΅ΡΡΡ Π²ΠΎΠ·ΠΌΠΎΠΆΠ½ΠΎΡΡΡ ΠΏΡΠΎΠΈΠ·Π²ΠΎΠ΄ΠΈΡΠ΅Π»Ρ ΠΊΠΎΠ½ΡΡΠΎΠ»ΠΈΡΠΎΠ²Π°ΡΡ ΠΈ ΠΊΠΎΠ½ΡΡΠΎΠ»ΠΈΡΠΎΠ²Π°ΡΡ ΡΠ΄Π΅Π»ΡΠ½ΡΡ ΡΡΠ΅ΠΏΠ΅Π½Ρ ΡΠΆΠ°ΡΠΈΡ.ΠΡΠΈΠΌΠ΅Π½Π΅Π½ΠΈΡ ΠΊΠΎΠ²ΠΎΡΠ½ΠΎΠ³ΠΎ ΠΏΡΠ΅ΡΡΠ° ΠΌΠ½ΠΎΠ³ΠΎΡΠΈΡΠ»Π΅Π½Π½Ρ, ΡΠ°ΠΊ ΠΊΠ°ΠΊ Π½Π΅Ρ ΠΎΠ³ΡΠ°Π½ΠΈΡΠ΅Π½ΠΈΠΉ Π½Π° ΡΠ°Π·ΠΌΠ΅Ρ ΠΏΡΠΎΠ΄ΡΠΊΡΠ°, ΠΊΠΎΡΠΎΡΡΠΉ ΠΌΠΎΠΆΠ΅Ρ Π±ΡΡΡ ΡΠΎΠ·Π΄Π°Π½. ΠΠΎΠ²ΠΊΠ° Π½Π° ΠΏΡΠ΅ΡΡΠ΅ ΠΌΠΎΠΆΠ΅Ρ Π±ΡΡΡ Π³ΠΎΡΡΡΠ΅ΠΉ ΠΈΠ»ΠΈ Ρ ΠΎΠ»ΠΎΠ΄Π½ΠΎΠΉ.
ΠΡΠΎΡΠ΅ΡΡ ΠΊΠΎΠ²ΠΊΠΈ Π²Π°Π»ΠΊΠΎΠ²
ΠΠ°Π»ΠΊΠΎΠ²Π°Ρ ΠΊΠΎΠ²ΠΊΠ° — ΡΡΠΎ ΠΏΡΠΎΡΠ΅ΡΡ ΡΠ²Π΅Π»ΠΈΡΠ΅Π½ΠΈΡ Π΄Π»ΠΈΠ½Ρ ΠΏΡΡΡΠΊΠΎΠ² ΠΈΠ»ΠΈ ΠΏΡΠΎΠ²ΠΎΠ»ΠΎΠΊΠΈ. ΠΡΠΎΠΈΠ·Π²ΠΎΠ΄ΠΈΡΠ΅Π»Ρ ΠΏΠΎΠΌΠ΅ΡΠ°Π΅Ρ Π½Π°Π³ΡΠ΅ΡΡΠ΅ ΠΌΠ΅ΡΠ°Π»Π»ΠΈΡΠ΅ΡΠΊΠΈΠ΅ ΡΡΠ΅ΡΠΆΠ½ΠΈ ΠΌΠ΅ΠΆΠ΄Ρ Π΄Π²ΡΠΌΡ ΡΠΈΠ»ΠΈΠ½Π΄ΡΠΈΡΠ΅ΡΠΊΠΈΠΌΠΈ Π²Π°Π»ΠΊΠ°ΠΌΠΈ Ρ ΠΊΠ°Π½Π°Π²ΠΊΠ°ΠΌΠΈ, ΠΊΠΎΡΠΎΡΡΠ΅ Π²ΡΠ°ΡΠ°ΡΡΡΡ ΠΈ ΠΏΡΠΈΠΊΠ»Π°Π΄ΡΠ²Π°ΡΡ ΠΏΡΠΎΠ³ΡΠ΅ΡΡΠΈΠ²Π½ΠΎΠ΅ Π΄Π°Π²Π»Π΅Π½ΠΈΠ΅ Π΄Π»Ρ ΠΏΡΠΈΠ΄Π°Π½ΠΈΡ ΠΌΠ΅ΡΠ°Π»Π»Ρ ΡΠΎΡΠΌΡ. ΠΠ»Π°Π³ΠΎΠ΄Π°ΡΡ ΡΠΎΡΠ½ΠΎΠΉ Π³Π΅ΠΎΠΌΠ΅ΡΡΠΈΠΈ ΡΡΠΈΡ ΠΊΠ°Π½Π°Π²ΠΎΠΊ ΠΌΠ΅ΡΠ°Π»Π»ΠΈΡΠ΅ΡΠΊΠ°Ρ Π΄Π΅ΡΠ°Π»Ρ ΠΏΡΠΈΠΎΠ±ΡΠ΅ΡΠ°Π΅Ρ ΠΆΠ΅Π»Π°Π΅ΠΌΡΡ ΡΠΎΡΠΌΡ.ΠΡΠ΅ΠΈΠΌΡΡΠ΅ΡΡΠ²Π° ΡΡΠΎΠ³ΠΎ ΠΌΠ΅ΡΠΎΠ΄Π° ΠΊΠΎΠ²ΠΊΠΈ Π²ΠΊΠ»ΡΡΠ°ΡΡ ΡΡΡΡΠ°Π½Π΅Π½ΠΈΠ΅ Π·Π°ΡΡΠ΅Π½ΡΠ΅Π² ΠΈ Π±Π»Π°Π³ΠΎΠΏΡΠΈΡΡΠ½ΡΡ ΡΡΡΡΠΊΡΡΡΡ Π·Π΅ΡΠ½Π°. Π₯ΠΎΡΡ ΠΏΡΠΈ ΠΊΠΎΠ²ΠΊΠ΅ Π²Π°Π»ΠΊΠΎΠ² ΠΈΡΠΏΠΎΠ»ΡΠ·ΡΡΡΡΡ Π²Π°Π»ΠΊΠΈ Π΄Π»Ρ ΠΏΡΠΎΠΈΠ·Π²ΠΎΠ΄ΡΡΠ²Π° Π΄Π΅ΡΠ°Π»Π΅ΠΉ ΠΈ ΠΊΠΎΠΌΠΏΠΎΠ½Π΅Π½ΡΠΎΠ², ΠΎΠ½Π° ΠΏΠΎ-ΠΏΡΠ΅ΠΆΠ½Π΅ΠΌΡ ΡΡΠΈΡΠ°Π΅ΡΡΡ ΠΏΡΠΎΡΠ΅ΡΡΠΎΠΌ ΠΊΠΎΠ²ΠΊΠΈ ΠΌΠ΅ΡΠ°Π»Π»Π°, Π° Π½Π΅ ΠΏΡΠΎΠΊΠ°ΡΠΊΠΎΠΉ. ΠΠ°Π»ΠΊΠΎΠ²Π°Ρ ΠΊΠΎΠ²ΠΊΠ° ΡΠ°ΡΡΠΎ ΠΈΡΠΏΠΎΠ»ΡΠ·ΡΠ΅ΡΡΡ Π΄Π»Ρ ΠΈΠ·Π³ΠΎΡΠΎΠ²Π»Π΅Π½ΠΈΡ Π΄Π΅ΡΠ°Π»Π΅ΠΉ Π΄Π»Ρ Π°Π²ΡΠΎΠΌΠΎΠ±ΠΈΠ»ΡΠ½ΠΎΠΉ ΠΏΡΠΎΠΌΡΡΠ»Π΅Π½Π½ΠΎΡΡΠΈ. ΠΠ½ ΡΠ°ΠΊΠΆΠ΅ ΠΈΡΠΏΠΎΠ»ΡΠ·ΡΠ΅ΡΡΡ Π΄Π»Ρ ΠΈΠ·Π³ΠΎΡΠΎΠ²Π»Π΅Π½ΠΈΡ Π½ΠΎΠΆΠ΅ΠΉ ΠΈ ΡΡΡΠ½ΡΡ ΠΈΠ½ΡΡΡΡΠΌΠ΅Π½ΡΠΎΠ².
ΠΡΠΎΡΠ΅ΡΡ ΡΡΠ°ΠΌΠΏΠΎΠ²ΠΊΠΈ Ρ ΠΎΡΠ°ΠΆΠ΄Π΅Π½ΠΈΠ΅ΠΌ
ΠΠΎΠ²ΠΊΠ° Ρ Π²ΡΡΠ°Π΄ΠΊΠΎΠΉ — ΡΡΠΎ ΠΏΡΠΎΡΠ΅ΡΡ ΠΊΠΎΠ²ΠΊΠΈ, ΠΏΡΠΈ ΠΊΠΎΡΠΎΡΠΎΠΌ Π΄ΠΈΠ°ΠΌΠ΅ΡΡ ΠΌΠ΅ΡΠ°Π»Π»Π° ΡΠ²Π΅Π»ΠΈΡΠΈΠ²Π°Π΅ΡΡΡ Π·Π° ΡΡΠ΅Ρ ΡΠΆΠ°ΡΠΈΡ.ΠΡΠΈΠ²ΠΎΡΠΈΠΏΠ½ΡΠ΅ ΠΏΡΠ΅ΡΡΡ, ΠΎΡΠΎΠ±ΡΠΉ Π²ΡΡΠΎΠΊΠΎΡΠΊΠΎΡΠΎΡΡΠ½ΠΎΠΉ ΡΡΠ°Π½ΠΎΠΊ, ΠΈΡΠΏΠΎΠ»ΡΠ·ΡΡΡΡΡ Π² ΠΏΡΠΎΡΠ΅ΡΡΠ°Ρ ΡΡΠ°ΠΌΠΏΠΎΠ²ΠΊΠΈ Ρ ΠΎΡΠ°ΠΆΠ΄Π΅Π½ΠΈΠ΅ΠΌ. ΠΡΠΈΠ²ΠΎΡΠΈΠΏΠ½ΡΠ΅ ΠΏΡΠ΅ΡΡΡ ΠΎΠ±ΡΡΠ½ΠΎ ΡΡΡΠ°Π½Π°Π²Π»ΠΈΠ²Π°ΡΡΡΡ Π² Π³ΠΎΡΠΈΠ·ΠΎΠ½ΡΠ°Π»ΡΠ½ΠΎΠΉ ΠΏΠ»ΠΎΡΠΊΠΎΡΡΠΈ Π΄Π»Ρ ΠΏΠΎΠ²ΡΡΠ΅Π½ΠΈΡ ΡΡΡΠ΅ΠΊΡΠΈΠ²Π½ΠΎΡΡΠΈ ΠΈ Π±ΡΡΡΡΠΎΠΉ Π·Π°ΠΌΠ΅Π½Ρ ΠΌΠ΅ΡΠ°Π»Π»Π° ΠΎΡ ΠΎΠ΄Π½ΠΎΠΉ ΡΡΠ°Π½ΡΠΈΠΈ ΠΊ Π΄ΡΡΠ³ΠΎΠΉ. Π’Π°ΠΊΠΆΠ΅ ΠΈΡΠΏΠΎΠ»ΡΠ·ΡΡΡΡΡ Π²Π΅ΡΡΠΈΠΊΠ°Π»ΡΠ½ΡΠ΅ ΠΊΡΠΈΠ²ΠΎΡΠΈΠΏΠ½ΡΠ΅ ΠΏΡΠ΅ΡΡΡ ΠΈΠ»ΠΈ Π³ΠΈΠ΄ΡΠ°Π²Π»ΠΈΡΠ΅ΡΠΊΠΈΠ΅ ΠΏΡΠ΅ΡΡΡ. ΠΡΠ΅ΠΈΠΌΡΡΠ΅ΡΡΠ²Π° ΡΡΠΎΠ³ΠΎ ΠΏΡΠΎΡΠ΅ΡΡΠ° Π·Π°ΠΊΠ»ΡΡΠ°ΡΡΡΡ Π² ΡΠΎΠΌ, ΡΡΠΎ ΠΎΠ½ ΠΎΠ±Π΅ΡΠΏΠ΅ΡΠΈΠ²Π°Π΅Ρ Π²ΡΡΠΎΠΊΡΡ ΠΏΡΠΎΠΈΠ·Π²ΠΎΠ΄ΠΈΡΠ΅Π»ΡΠ½ΠΎΡΡΡ Π΄ΠΎ 4500 Π΄Π΅ΡΠ°Π»Π΅ΠΉ Π² ΡΠ°Ρ ΠΈ Π²ΠΎΠ·ΠΌΠΎΠΆΠ½Π° ΠΏΠΎΠ»Π½Π°Ρ Π°Π²ΡΠΎΠΌΠ°ΡΠΈΠ·Π°ΡΠΈΡ. ΠΡΠΎΠΌΠ΅ ΡΠΎΠ³ΠΎ, ΠΎΠ½ ΠΏΡΠ°ΠΊΡΠΈΡΠ΅ΡΠΊΠΈ Π½Π΅ ΠΏΡΠΎΠΈΠ·Π²ΠΎΠ΄ΠΈΡ ΠΎΡΡ ΠΎΠ΄ΠΎΠ².
ΠΡΠΎΡΠ΅ΡΡ ΠΈΠ·ΠΎΡΠ΅ΡΠΌΠΈΡΠ΅ΡΠΊΠΎΠΉ ΠΊΠΎΠ²ΠΊΠΈ
ΠΠ·ΠΎΡΠ΅ΡΠΌΠΈΡΠ΅ΡΠΊΠ°Ρ ΠΊΠΎΠ²ΠΊΠ° — ΡΡΠΎ ΠΏΡΠΎΡΠ΅ΡΡ ΠΊΠΎΠ²ΠΊΠΈ, ΠΏΡΠΈ ΠΊΠΎΡΠΎΡΠΎΠΌ ΠΌΠ°ΡΠ΅ΡΠΈΠ°Π»Ρ ΠΈ ΠΌΠ°ΡΡΠΈΡΠ° Π½Π°Π³ΡΠ΅Π²Π°ΡΡΡΡ Π΄ΠΎ ΠΎΠ΄ΠΈΠ½Π°ΠΊΠΎΠ²ΠΎΠΉ ΡΠ΅ΠΌΠΏΠ΅ΡΠ°ΡΡΡΡ.ΠΠ°Π·Π²Π°Π½ΠΈΠ΅ ΠΏΡΠΎΠΈΡΡ ΠΎΠ΄ΠΈΡ ΠΎΡ Β«isoΒ», ΡΡΠΎ ΠΎΠ·Π½Π°ΡΠ°Π΅Ρ Β«ΡΠ°Π²Π½ΡΠΉΒ». ΠΡΠΎΡ ΠΌΠ΅ΡΠΎΠ΄ ΠΊΠΎΠ²ΠΊΠΈ ΠΎΠ±ΡΡΠ½ΠΎ ΠΈΡΠΏΠΎΠ»ΡΠ·ΡΠ΅ΡΡΡ Π΄Π»Ρ ΠΊΠΎΠ²ΠΊΠΈ Π°Π»ΡΠΌΠΈΠ½ΠΈΡ, ΠΊΠΎΡΠΎΡΡΠΉ ΠΈΠΌΠ΅Π΅Ρ Π±ΠΎΠ»Π΅Π΅ Π½ΠΈΠ·ΠΊΡΡ ΡΠ΅ΠΌΠΏΠ΅ΡΠ°ΡΡΡΡ ΠΊΠΎΠ²ΠΊΠΈ, ΡΠ΅ΠΌ Π΄ΡΡΠ³ΠΈΠ΅ ΠΌΠ΅ΡΠ°Π»Π»Ρ, ΡΠ°ΠΊΠΈΠ΅ ΠΊΠ°ΠΊ ΡΡΠ°Π»Ρ. Π’Π΅ΠΌΠΏΠ΅ΡΠ°ΡΡΡΠ° ΠΊΠΎΠ²ΠΊΠΈ Π°Π»ΡΠΌΠΈΠ½ΠΈΡ ΡΠΎΡΡΠ°Π²Π»ΡΠ΅Ρ ΠΎΠΊΠΎΠ»ΠΎ 430 Β° C, Π° Π΄Π»Ρ ΡΡΠ°Π»Π΅ΠΉ ΠΈ ΡΡΠΏΠ΅ΡΡΠΏΠ»Π°Π²ΠΎΠ² — ΠΎΡ 930 Π΄ΠΎ 1260 Β° C. ΠΡΠ΅ΠΈΠΌΡΡΠ΅ΡΡΠ²ΠΎ Π·Π°ΠΊΠ»ΡΡΠ°Π΅ΡΡΡ Π² ΡΠΎΠΌ, ΡΡΠΎ ΡΠΎΡΠΌΠ°, Π±Π»ΠΈΠ·ΠΊΠ°Ρ ΠΊ ΠΊΠΎΠ½Π΅ΡΠ½ΠΎΠΉ, ΡΠ½ΠΈΠΆΠ°Π΅Ρ ΡΡΠ΅Π±ΠΎΠ²Π°Π½ΠΈΡ ΠΊ ΠΌΠ΅Ρ Π°Π½ΠΈΡΠ΅ΡΠΊΠΎΠΉ ΠΎΠ±ΡΠ°Π±ΠΎΡΠΊΠ΅ ΠΈ, ΡΠ»Π΅Π΄ΠΎΠ²Π°ΡΠ΅Π»ΡΠ½ΠΎ, ΡΠ½ΠΈΠΆΠ°Π΅Ρ ΠΏΡΠΎΡΠ΅Π½Ρ Π±ΡΠ°ΠΊΠ°, Π° ΠΌΠ΅ΡΠ°Π»Π»ΠΈΡΠ΅ΡΠΊΠ°Ρ Π΄Π΅ΡΠ°Π»Ρ Π»Π΅Π³ΠΊΠΎ Π²ΠΎΡΠΏΡΠΎΠΈΠ·Π²ΠΎΠ΄ΠΈΡΡΡ. ΠΡΠ΅ ΠΎΠ΄Π½ΠΎ ΠΏΡΠ΅ΠΈΠΌΡΡΠ΅ΡΡΠ²ΠΎ ΡΠΎΡΡΠΎΠΈΡ Π² ΡΠΎΠΌ, ΡΡΠΎ Π΄Π»Ρ ΠΊΠΎΠ²ΠΊΠΈ ΠΌΠΎΠΆΠ½ΠΎ ΠΈΡΠΏΠΎΠ»ΡΠ·ΠΎΠ²Π°ΡΡ ΠΌΠ°ΡΠΈΠ½Ρ ΠΌΠ΅Π½ΡΡΠ΅Π³ΠΎ ΡΠ°Π·ΠΌΠ΅ΡΠ° ΠΈΠ·-Π·Π° ΠΌΠ΅Π½ΡΡΠΈΡ ΡΠ΅ΠΏΠ»ΠΎΠ²ΡΡ ΠΏΠΎΡΠ΅ΡΡ.ΠΠ΅ΠΊΠΎΡΠΎΡΡΠΌΠΈ Π½Π΅Π΄ΠΎΡΡΠ°ΡΠΊΠ°ΠΌΠΈ ΡΠ²Π»ΡΡΡΡΡ Π±ΠΎΠ»Π΅Π΅ Π²ΡΡΠΎΠΊΠ°Ρ ΡΡΠΎΠΈΠΌΠΎΡΡΡ ΠΌΠ°ΡΠ΅ΡΠΈΠ°Π»Π° ΡΠΈΠ»ΡΠ΅ΡΡ Π΄Π»Ρ Π²ΡΠ΄Π΅ΡΠΆΠΈΠ²Π°Π½ΠΈΡ ΡΠ΅ΠΌΠΏΠ΅ΡΠ°ΡΡΡΡ ΠΈ Π΄Π°Π²Π»Π΅Π½ΠΈΡ, Π° ΡΠ°ΠΊΠΆΠ΅ ΡΡΠ΅Π±ΡΠ΅ΠΌΡΠ΅ ΡΠΈΡΡΠ΅ΠΌΡ ΡΠ°Π²Π½ΠΎΠΌΠ΅ΡΠ½ΠΎΠ³ΠΎ Π½Π°Π³ΡΠ΅Π²Π°. Π’Π°ΠΊΠΆΠ΅ ΠΎΠ½ ΠΈΠΌΠ΅Π΅Ρ Π½ΠΈΠ·ΠΊΡΡ ΠΏΡΠΎΠΈΠ·Π²ΠΎΠ΄ΠΈΡΠ΅Π»ΡΠ½ΠΎΡΡΡ.
ΠΠ°ΠΊΠΎΠ΅ ΠΎΠ±ΠΎΡΡΠ΄ΠΎΠ²Π°Π½ΠΈΠ΅ ΠΈΡΠΏΠΎΠ»ΡΠ·ΡΠ΅ΡΡΡ Π΄Π»Ρ ΠΊΠΎΠ²ΠΊΠΈ?
Π‘Π°ΠΌΡΠΉ ΠΏΠΎΠΏΡΠ»ΡΡΠ½ΡΠΉ Π²ΠΈΠ΄ ΠΊΡΠ·Π½Π΅ΡΠ½ΠΎΠ³ΠΎ ΠΎΠ±ΠΎΡΡΠ΄ΠΎΠ²Π°Π½ΠΈΡ — ΠΌΠΎΠ»ΠΎΡ ΠΈ Π½Π°ΠΊΠΎΠ²Π°Π»ΡΠ½Ρ. ΠΠ΄Π΅Ρ ΠΌΠΎΠ»ΠΎΡΠΊΠ° ΠΈ Π½Π°ΠΊΠΎΠ²Π°Π»ΡΠ½ΠΈ Π΄ΠΎ ΡΠΈΡ ΠΏΠΎΡ ΠΈΡΠΏΠΎΠ»ΡΠ·ΡΠ΅ΡΡΡ Π² ΠΊΠΎΠ²ΠΎΡΠ½ΠΎΠΌ ΠΎΠ±ΠΎΡΡΠ΄ΠΎΠ²Π°Π½ΠΈΠΈ Ρ ΡΠ΄Π°ΡΠ½ΡΠΌ ΠΌΠΎΠ»ΠΎΡΠΊΠΎΠΌ. ΠΠΎΠ»ΠΎΡ ΠΏΠΎΠ΄Π½ΠΈΠΌΠ°Π΅ΡΡΡ, Π° Π·Π°ΡΠ΅ΠΌ ΠΎΠΏΡΡΠΊΠ°Π΅ΡΡΡ ΠΈΠ»ΠΈ Π·Π°Π±ΠΈΠ²Π°Π΅ΡΡΡ Π² Π·Π°Π³ΠΎΡΠΎΠ²ΠΊΡ, ΠΊΠΎΡΠΎΡΠ°Ρ Π»Π΅ΠΆΠΈΡ Π½Π° ΠΎΠΏΠΎΡΠ΅. ΠΡΠ½ΠΎΠ²Π½ΡΠ΅ ΡΠ°Π·Π»ΠΈΡΠΈΡ ΠΌΠ΅ΠΆΠ΄Ρ ΡΠ΄Π°ΡΠ½ΡΠΌΠΈ ΠΌΠΎΠ»ΠΎΡΠΊΠ°ΠΌΠΈ Π·Π°ΠΊΠ»ΡΡΠ°ΡΡΡΡ Π² ΠΏΡΠΈΠ²ΠΎΠ΄Π΅ ΠΌΠΎΠ»ΠΎΡΠ° Π² Π΄Π΅ΠΉΡΡΠ²ΠΈΠ΅, Π½Π°ΠΈΠ±ΠΎΠ»Π΅Π΅ ΡΠ°ΡΠΏΡΠΎΡΡΡΠ°Π½Π΅Π½Π½ΡΠΌΠΈ ΠΈΠ· ΠΊΠΎΡΠΎΡΡΡ ΡΠ²Π»ΡΡΡΡΡ ΠΏΠ½Π΅Π²ΠΌΠ°ΡΠΈΡΠ΅ΡΠΊΠΈΠ΅ ΠΈ ΠΏΠ°ΡΠΎΠ²ΡΠ΅ ΠΌΠΎΠ»ΠΎΡΡ.ΠΡΠ±ΠΎΠΉΠ½ΡΠ΅ ΠΌΠΎΠ»ΠΎΡΠΊΠΈ ΠΎΠ±ΡΡΠ½ΠΎ ΡΠ°Π±ΠΎΡΠ°ΡΡ Π² Π²Π΅ΡΡΠΈΠΊΠ°Π»ΡΠ½ΠΎΠΌ ΠΏΠΎΠ»ΠΎΠΆΠ΅Π½ΠΈΠΈ. ΠΡΠΎ ΡΠ²ΡΠ·Π°Π½ΠΎ Ρ ΡΠ΅ΠΌ, ΡΡΠΎ ΠΈΠ·Π±ΡΡΠΎΡΠ½Π°Ρ ΡΠ½Π΅ΡΠ³ΠΈΡ, ΠΊΠΎΡΠΎΡΠ°Ρ Π½Π΅ Π²ΡΠ΄Π΅Π»ΡΠ΅ΡΡΡ Π² Π²ΠΈΠ΄Π΅ ΡΠ΅ΠΏΠ»Π° ΠΈΠ»ΠΈ Π·Π²ΡΠΊΠ°, ΡΠΎ Π΅ΡΡΡ ΡΠ½Π΅ΡΠ³ΠΈΡ, ΠΊΠΎΡΠΎΡΠ°Ρ Π½Π΅ ΠΈΡΠΏΠΎΠ»ΡΠ·ΡΠ΅ΡΡΡ Π΄Π»Ρ ΠΏΡΠΈΠ΄Π°Π½ΠΈΡ ΡΠΎΡΠΌΡ Π·Π°Π³ΠΎΡΠΎΠ²ΠΊΠ΅, Π΄ΠΎΠ»ΠΆΠ½Π° ΠΏΠ΅ΡΠ΅Π΄Π°Π²Π°ΡΡΡΡ Π² ΡΡΠ½Π΄Π°ΠΌΠ΅Π½Ρ. Π’Π°ΠΊΠΆΠ΅ ΡΡΠ΅Π±ΡΠ΅ΡΡΡ Π±ΠΎΠ»ΡΡΠ°Ρ ΠΎΡΠ½ΠΎΠ²Π° ΠΌΠ°ΡΠΈΠ½Ρ Π΄Π»Ρ ΠΏΠΎΠ³Π»ΠΎΡΠ΅Π½ΠΈΡ ΡΠ΄Π°ΡΠΎΠ².
ΠΠ»Ρ ΡΡΡΡΠ°Π½Π΅Π½ΠΈΡ Π½Π΅ΠΊΠΎΡΠΎΡΡΡ Π½Π΅Π΄ΠΎΡΡΠ°ΡΠΊΠΎΠ² ΠΎΡΠ±ΠΎΠΉΠ½ΠΎΠ³ΠΎ ΠΌΠΎΠ»ΠΎΡΠΊΠ° ΠΈΡΠΏΠΎΠ»ΡΠ·ΡΠ΅ΡΡΡ ΡΡΡΠ°Π½ΠΎΠ²ΠΊΠ° Π²ΡΡΡΠ΅ΡΠ½ΠΎΠ³ΠΎ ΡΠ΄Π°ΡΠ° ΠΈΠ»ΠΈ ΡΠ΄Π°ΡΠ½ΡΠΉ ΠΌΠ΅Ρ Π°Π½ΠΈΠ·ΠΌ. Π ΠΌΠΎΠ»ΠΎΡ, ΠΈ Π½Π°ΠΊΠΎΠ²Π°Π»ΡΠ½Ρ ΠΏΠ΅ΡΠ΅ΠΌΠ΅ΡΠ°ΡΡΡΡ Π² ΠΌΠ°ΡΠΈΠ½Π΅ Π΄Π»Ρ Π²ΡΡΡΠ΅ΡΠ½ΠΎΠ³ΠΎ ΡΠ΄Π°ΡΠ°, ΠΏΡΠΈ ΡΡΠΎΠΌ ΠΎΠ±ΡΠ°Π±Π°ΡΡΠ²Π°Π΅ΠΌΠ°Ρ Π΄Π΅ΡΠ°Π»Ρ ΡΠ΄Π΅ΡΠΆΠΈΠ²Π°Π΅ΡΡΡ ΠΌΠ΅ΠΆΠ΄Ρ Π½ΠΈΠΌΠΈ. ΠΠ΄Π΅ΡΡ ΠΈΠ·Π±ΡΡΠΎΡΠ½Π°Ρ ΡΠ½Π΅ΡΠ³ΠΈΡ ΡΡΠ°Π½ΠΎΠ²ΠΈΡΡΡ ΠΎΡΠ΄Π°ΡΠ΅ΠΉ, ΠΏΠΎΠ·Π²ΠΎΠ»ΡΡ ΠΌΠ°ΡΠΈΠ½Π΅ ΡΠ°Π±ΠΎΡΠ°ΡΡ Π³ΠΎΡΠΈΠ·ΠΎΠ½ΡΠ°Π»ΡΠ½ΠΎ ΠΈ ΠΈΠΌΠ΅ΡΡ ΠΌΠ΅Π½ΡΡΡΡ Π±Π°Π·Ρ.ΠΡΠΎ ΡΠΎΠ·Π΄Π°Π΅Ρ ΠΌΠ΅Π½ΡΡΠ΅ ΡΡΠΌΠ°, ΡΠ΅ΠΏΠ»Π° ΠΈ Π²ΠΈΠ±ΡΠ°ΡΠΈΠΈ. ΠΡΠΎ ΡΠ°ΠΊΠΆΠ΅ ΡΠΎΠ·Π΄Π°Π΅Ρ ΡΠΎΠ²Π΅ΡΡΠ΅Π½Π½ΠΎ Π΄ΡΡΠ³ΡΡ ΠΊΠ°ΡΡΠΈΠ½Ρ ΠΏΠΎΡΠΎΠΊΠ°. ΠΡΠΈ ΠΌΠ°ΡΠΈΠ½Ρ ΠΈΡΠΏΠΎΠ»ΡΠ·ΡΡΡΡΡ Π΄Π»Ρ ΡΡΠ°ΠΌΠΏΠΎΠ²ΠΊΠΈ Π² ΠΎΡΠΊΡΡΡΡΡ ΠΈΠ»ΠΈ Π·Π°ΠΊΡΡΡΡΡ ΡΡΠ°ΠΌΠΏΠ°Ρ .
ΠΠ»Ρ ΠΊΠΎΠ²ΠΊΠΈ ΠΏΡΠ΅ΡΡΠ° ΠΈΡΠΏΠΎΠ»ΡΠ·ΡΠ΅ΡΡΡ ΠΏΡΠ΅ΡΡ. ΠΠ²Π° ΠΎΡΠ½ΠΎΠ²Π½ΡΡ ΡΠΈΠΏΠ° — ΡΡΠΎ ΠΌΠ΅Ρ Π°Π½ΠΈΡΠ΅ΡΠΊΠΈΠ΅ ΠΈ Π³ΠΈΠ΄ΡΠ°Π²Π»ΠΈΡΠ΅ΡΠΊΠΈΠ΅ ΠΏΡΠ΅ΡΡΡ. ΠΠ΅Ρ Π°Π½ΠΈΡΠ΅ΡΠΊΠΈΠ΅ ΠΏΡΠ΅ΡΡΡ ΡΠ°Π±ΠΎΡΠ°ΡΡ Ρ ΠΈΡΠΏΠΎΠ»ΡΠ·ΠΎΠ²Π°Π½ΠΈΠ΅ΠΌ ΠΊΡΠ»Π°ΡΠΊΠΎΠ², ΠΊΡΠΈΠ²ΠΎΡΠΈΠΏΠΎΠ² ΠΈ ΠΏΠ΅ΡΠ΅ΠΊΠ»ΡΡΠ°ΡΠ΅Π»Π΅ΠΉ Π΄Π»Ρ Π²ΡΠΏΠΎΠ»Π½Π΅Π½ΠΈΡ Π·Π°Π΄Π°Π½Π½ΡΡ ΠΈ Π²ΠΎΡΠΏΡΠΎΠΈΠ·Π²ΠΎΠ΄ΠΈΠΌΡΡ ΡΠ΄Π°ΡΠΎΠ² ΠΌΠΎΠ»ΠΎΡΠΊΠΎΠΌ. ΠΠ·-Π·Π° Ρ Π°ΡΠ°ΠΊΡΠ΅ΡΠΈΡΡΠΈΠΊ ΡΡΠΎΠ³ΠΎ ΡΠΈΠΏΠ° ΡΠΈΡΡΠ΅ΠΌΡ Π² ΡΠ°Π·Π½ΡΡ ΠΏΠΎΠ»ΠΎΠΆΠ΅Π½ΠΈΡΡ Ρ ΠΎΠ΄Π° Π΄ΠΎΡΡΡΠΏΠ½Ρ ΡΠ°Π·Π½ΡΠ΅ ΡΠΈΠ»Ρ. Π ΡΠ΅Π·ΡΠ»ΡΡΠ°ΡΠ΅ ΡΡΠΈ ΠΏΡΠ΅ΡΡΡ Π±ΡΡΡΡΠ΅Π΅ ΡΠ²ΠΎΠΈΡ Π³ΠΈΠ΄ΡΠ°Π²Π»ΠΈΡΠ΅ΡΠΊΠΈΡ Π°Π½Π°Π»ΠΎΠ³ΠΎΠ² Π½Π° 50 Ρ ΠΎΠ΄ΠΎΠ² Π² ΠΌΠΈΠ½ΡΡΡ.ΠΡ ΠΌΠΎΡΠ½ΠΎΡΡΠΈ ΠΊΠΎΠ»Π΅Π±Π»ΡΡΡΡ ΠΎΡ ΡΡΠ΅Ρ Π΄ΠΎ 160 ΠΠ. ΠΠΈΠ΄ΡΠ°Π²Π»ΠΈΡΠ΅ΡΠΊΠΈΠ΅ ΠΏΡΠ΅ΡΡΡ ΠΈΡΠΏΠΎΠ»ΡΠ·ΡΡΡ Π΄Π°Π²Π»Π΅Π½ΠΈΠ΅ ΠΆΠΈΠ΄ΠΊΠΎΡΡΠΈ ΠΈ ΠΏΠΎΡΡΠ΅Π½Ρ Π΄Π»Ρ ΡΠΎΠ·Π΄Π°Π½ΠΈΡ ΡΠΈΠ»Ρ. ΠΡΠ΅ΠΈΠΌΡΡΠ΅ΡΡΠ²Π° Π³ΠΈΠ΄ΡΠ°Π²Π»ΠΈΠΊΠΈ ΠΏΠ΅ΡΠ΅Π΄ ΠΌΠ΅Ρ Π°Π½ΠΈΡΠ΅ΡΠΊΠΎΠΉ — ΡΡΠΎ Π΅Π΅ Π³ΠΈΠ±ΠΊΠΎΡΡΡ ΠΈ ΠΏΡΠ΅Π²ΠΎΡΡ ΠΎΠ΄Π½Π°Ρ ΠΏΡΠΎΠΈΠ·Π²ΠΎΠ΄ΠΈΡΠ΅Π»ΡΠ½ΠΎΡΡΡ. ΠΠ΅Π΄ΠΎΡΡΠ°ΡΠΊΠΈ Π·Π°ΠΊΠ»ΡΡΠ°ΡΡΡΡ Π² ΡΠΎΠΌ, ΡΡΠΎ ΡΡΠΎ Π±ΠΎΠ»Π΅Π΅ ΠΌΠ΅Π΄Π»Π΅Π½Π½Π°Ρ, Π±ΠΎΠ»ΡΡΠ°Ρ ΠΈ Π±ΠΎΠ»Π΅Π΅ Π΄ΠΎΡΠΎΠ³Π°Ρ ΠΌΠ°ΡΠΈΠ½Π° Π² ΡΠΊΡΠΏΠ»ΡΠ°ΡΠ°ΡΠΈΠΈ.
ΠΠ»Ρ ΠΊΠΎΠ²ΠΊΠΈ Π²Π°Π»ΠΊΠΎΠ², Π°Π²ΡΠΎΠΌΠ°ΡΠΈΡΠ΅ΡΠΊΠΎΠΉ Π³ΠΎΡΡΡΠ΅ΠΉ ΡΡΠ°ΠΌΠΏΠΎΠ²ΠΊΠΈ ΠΈ Π²ΡΡΠ°Π΄ΠΊΠΈ ΠΈΡΠΏΠΎΠ»ΡΠ·ΡΠ΅ΡΡΡ ΡΠΏΠ΅ΡΠΈΠ°Π»ΠΈΠ·ΠΈΡΠΎΠ²Π°Π½Π½ΠΎΠ΅ ΠΎΠ±ΠΎΡΡΠ΄ΠΎΠ²Π°Π½ΠΈΠ΅.
Π‘Π²ΠΎΠ΄ΠΊΠ°
ΠΡΠΎ ΡΡΠΊΠΎΠ²ΠΎΠ΄ΡΡΠ²ΠΎ Π΄Π°Π΅Ρ ΠΎΠ±ΡΠ΅Π΅ ΠΏΡΠ΅Π΄ΡΡΠ°Π²Π»Π΅Π½ΠΈΠ΅ ΠΎ ΡΠΎΠΌ, ΡΡΠΎ ΡΠ°ΠΊΠΎΠ΅ ΠΊΠΎΠ²ΠΊΠ°, ΠΈ ΠΎ ΡΠ°Π·Π»ΠΈΡΠ½ΡΡ ΠΏΡΠΎΡΠ΅ΡΡΠ°Ρ ΠΊΠΎΠ²ΠΊΠΈ.Π§ΡΠΎΠ±Ρ ΡΠ·Π½Π°ΡΡ Π±ΠΎΠ»ΡΡΠ΅ ΠΎ Π΄ΡΡΠ³ΠΈΡ ΠΌΠ΅ΡΠΎΠ΄Π°Ρ ΠΈΠ·Π³ΠΎΡΠΎΠ²Π»Π΅Π½ΠΈΡ ΠΌΠ΅ΡΠ°Π»Π»Π°, ΠΏΡΠΎΡΡΠΈΡΠ΅ Π½Π°ΡΠ΅ ΡΡΠΊΠΎΠ²ΠΎΠ΄ΡΡΠ²ΠΎ Π·Π΄Π΅ΡΡ. ΠΠ»Ρ ΠΏΠΎΠ»ΡΡΠ΅Π½ΠΈΡ Π΄ΠΎΠΏΠΎΠ»Π½ΠΈΡΠ΅Π»ΡΠ½ΠΎΠΉ ΠΈΠ½ΡΠΎΡΠΌΠ°ΡΠΈΠΈ ΠΎ ΡΠΎΠΏΡΡΡΡΠ²ΡΡΡΠΈΡ ΡΡΠ»ΡΠ³Π°Ρ ΠΎΠ±ΡΠ°ΡΠΈΡΠ΅ΡΡ ΠΊ Π½Π°ΡΠΈΠΌ ΡΡΠΊΠΎΠ²ΠΎΠ΄ΡΡΠ²Π°ΠΌ ΠΏΠΎ Π΄ΡΡΠ³ΠΈΠΌ ΠΏΡΠΎΠ΄ΡΠΊΡΠ°ΠΌ ΠΈΠ»ΠΈ ΠΏΠΎΡΠ΅ΡΠΈΡΠ΅ ΠΏΠ»Π°ΡΡΠΎΡΠΌΡ Thomas Supplier Discovery Platform, ΡΡΠΎΠ±Ρ Π½Π°ΠΉΡΠΈ ΠΏΠΎΡΠ΅Π½ΡΠΈΠ°Π»ΡΠ½ΡΠ΅ ΠΈΡΡΠΎΡΠ½ΠΈΠΊΠΈ ΠΈΠ»ΠΈ ΠΏΡΠΎΡΠΌΠΎΡΡΠ΅ΡΡ ΠΏΠΎΠ΄ΡΠΎΠ±Π½ΡΡ ΠΈΠ½ΡΠΎΡΠΌΠ°ΡΠΈΡ ΠΎ ΠΊΠΎΠ½ΠΊΡΠ΅ΡΠ½ΡΡ ΠΏΡΠΎΠ΄ΡΠΊΡΠ°Ρ .
ΠΡΡΠΎΡΠ½ΠΈΠΊΠΈ
ΠΡΠΎΡΠΈΠ΅ ΠΈΠ·Π΄Π΅Π»ΠΈΡ ΠΈΠ· ΠΌΠ΅ΡΠ°Π»Π»Π°
ΠΠΎΠ»ΡΡΠ΅ ΠΎΡ Custom Manufacturing & Fabricating
Π΄ΠΎΡΡΠΈΠΆΠ΅Π½ΠΈΠΉ Π² ΡΠ΅Ρ Π½ΠΎΠ»ΠΎΠ³ΠΈΠΈ ΠΊΠΎΠ²ΠΊΠΈ Π΄Π»Ρ ΡΡΠΆΠ΅Π»ΠΎΠΉ ΠΏΠΎΠ΄Π²ΠΈΠΆΠ½ΠΎΠΉ ΠΊΠΎΠ½ΡΡΡΡΠΊΡΠΈΠΈ Stru
ΠΠ΅ΡΠ°Π»Π»ΠΎΠΎΠ±ΡΠ°Π±ΠΎΡΠΊΠ° ΠΈ ΠΈΠ½ΡΡΠ°ΡΡΡΡΠΊΡΡΡΠ° Π² U.Π‘.
Π 2015 Π³ΠΎΠ΄Ρ ΡΠ΅Π²Π΅ΡΠΎΠ°ΠΌΠ΅ΡΠΈΠΊΠ°Π½ΡΠΊΠΈΠ΅ ΠΏΡΠΎΠΈΠ·Π²ΠΎΠ΄ΠΈΡΠ΅Π»ΠΈ ΠΏΠΎΠΊΠΎΠ²ΠΎΠΊ ΠΏΠΎΡΡΠ°Π²ΠΈΠ»ΠΈ ΠΏΠΎΠΊΠΎΠ²ΠΊΠΈ Ρ ΠΎΡΠΊΡΡΡΡΠΌ ΡΡΠ°ΠΌΠΏΠΎΠΌ ΠΈ ΠΊΠ°ΡΠ°Π½ΡΠΌ ΠΊΠΎΠ»ΡΡΠΎΠΌ Π½Π° ΡΡΠΌΠΌΡ 6,2 ΠΌΠΈΠ»Π»ΠΈΠΎΠ½Π° Π΄ΠΎΠ»Π»Π°ΡΠΎΠ² Π΄Π»Ρ ΠΌΠΎΡΡΠΎΠ² ΠΈ Π΄ΡΡΠ³ΠΈΡ ΡΠ°Π±ΠΎΡ ΠΠΈΠ½ΠΈΡΡΠ΅ΡΡΡΠ²Π° ΡΡΠ°Π½ΡΠΏΠΎΡΡΠ°. 1 ΠΠΎ Π΄Π°Π½Π½ΡΠΌ ΠΠΌΠ΅ΡΠΈΠΊΠ°Π½ΡΠΊΠΎΠ³ΠΎ ΠΎΠ±ΡΠ΅ΡΡΠ²Π° ΠΈΠ½ΠΆΠ΅Π½Π΅ΡΠΎΠ²-ΡΡΡΠΎΠΈΡΠ΅Π»Π΅ΠΉ, ΠΌΠΎΡΡΡ Π² Π‘Π¨Π Π½Π°Ρ ΠΎΠ΄ΡΡΡΡ Π² ΠΏΠ»ΠΎΡ ΠΎΠΌ ΡΠΎΡΡΠΎΡΠ½ΠΈΠΈ, ΠΈΠΌ ΠΏΡΠΈΡΠ²ΠΎΠ΅Π½Π° ΠΎΡΠ΅Π½ΠΊΠ° Β«C +Β». 2 Π ΡΠ΅Π·ΡΠ»ΡΡΠ°ΡΠ΅, ΠΏΠΎ ΠΎΡΠ΅Π½ΠΊΠ°ΠΌ Π€Π΅Π΄Π΅ΡΠ°Π»ΡΠ½ΠΎΠ³ΠΎ ΡΠΏΡΠ°Π²Π»Π΅Π½ΠΈΡ ΡΠΎΡΡΠ΅ΠΉΠ½ΡΡ Π΄ΠΎΡΠΎΠ³, ΠΏΠΎΡΡΠΈ 25% ΠΌΠΎΡΡΠΎΠ² Π² ΡΡΡΠ°Π½Π΅ ΡΡΠ΅Π±ΡΡΡ ΡΠ΅ΠΌΠΎΠ½ΡΠ° ΠΈ Π·Π°ΠΌΠ΅Π½Ρ, ΠΏΠΎΡΠΊΠΎΠ»ΡΠΊΡ ΡΡΡΠ΅ΡΡΠ²ΡΡΡΠΈΠ΅ ΡΠΎΠΎΡΡΠΆΠ΅Π½ΠΈΡ ΠΏΠΎΠ΄Ρ ΠΎΠ΄ΡΡ ΠΊ ΠΊΠΎΠ½ΡΡ ΡΠ²ΠΎΠ΅Π³ΠΎ ΡΡΠΎΠΊΠ° ΡΠ»ΡΠΆΠ±Ρ ΠΈ ΠΈΠ·ΠΎ Π²ΡΠ΅Ρ ΡΠΈΠ» ΠΏΡΡΠ°ΡΡΡΡ ΡΠΏΡΠ°Π²ΠΈΡΡΡΡ Ρ ΡΠ²Π΅Π»ΠΈΡΠΈΠ²Π°ΡΡΠΈΠΌΡΡ ΡΡΠ°ΡΠΈΠΊΠΎΠΌ. 3
ΠΠΎΡΡΡ ΡΡΠΈΡΠ°ΡΡΡΡ ΠΊΠΎΠ½ΡΡΡΡΠΊΡΠΈΠ²Π½ΠΎ Π½Π΅ΡΠΎΠ²Π΅ΡΡΠ΅Π½Π½ΡΠΌΠΈ, Π΅ΡΠ»ΠΈ ΠΎΠ±Π½Π°ΡΡΠΆΠΈΠ²Π°Π΅ΡΡΡ, ΡΡΠΎ Π·Π½Π°ΡΠΈΡΠ΅Π»ΡΠ½ΡΠ΅ Π½Π΅ΡΡΡΠΈΠ΅ ΡΠ»Π΅ΠΌΠ΅Π½ΡΡ Π½Π°Ρ ΠΎΠ΄ΡΡΡΡ Π² ΠΏΠ»ΠΎΡ ΠΎΠΌ ΠΈΠ»ΠΈ Ρ ΡΠ΄ΡΠ΅ΠΌ ΡΠΎΡΡΠΎΡΠ½ΠΈΠΈ ΠΈΠ·-Π·Π° ΠΈΠ·Π½ΠΎΡΠ° ΠΈ / ΠΈΠ»ΠΈ ΠΏΠΎΠ²ΡΠ΅ΠΆΠ΄Π΅Π½ΠΈΡ. Β«ΠΠ΅ΠΈΡΠΏΡΠ°Π²Π½ΡΠΉΒ» ΠΌΠΎΡΡ, ΠΊΠΎΠ³Π΄Π° ΠΎΠ½ ΠΎΡΡΠ°Π΅ΡΡΡ ΠΎΡΠΊΡΡΡΡΠΌ Π΄Π»Ρ Π΄Π²ΠΈΠΆΠ΅Π½ΠΈΡ, ΠΎΠ±ΡΡΠ½ΠΎ ΡΡΠ΅Π±ΡΠ΅Ρ Π·Π½Π°ΡΠΈΡΠ΅Π»ΡΠ½ΠΎΠ³ΠΎ ΡΠ΅Ρ Π½ΠΈΡΠ΅ΡΠΊΠΎΠ³ΠΎ ΠΎΠ±ΡΠ»ΡΠΆΠΈΠ²Π°Π½ΠΈΡ ΠΈ ΡΠ΅ΠΌΠΎΠ½ΡΠ°, ΡΡΠΎΠ±Ρ ΠΎΡΡΠ°Π²Π°ΡΡΡΡ Π² ΡΠΊΡΠΏΠ»ΡΠ°ΡΠ°ΡΠΈΠΈ, ΠΈ Π²ΠΎΠ·ΠΌΠΎΠΆΠ½ΠΎΠ³ΠΎ Π²ΠΎΡΡΡΠ°Π½ΠΎΠ²Π»Π΅Π½ΠΈΡ ΠΈΠ»ΠΈ Π·Π°ΠΌΠ΅Π½Ρ Π΄Π»Ρ ΡΡΡΡΠ°Π½Π΅Π½ΠΈΡ Π½Π΅Π΄ΠΎΡΡΠ°ΡΠΊΠΎΠ². ΠΡΡΠΎΠΊΠΈΠΉ ΠΏΡΠΎΡΠ΅Π½Ρ Π½Π΅ΠΈΡΠΏΡΠ°Π²Π½ΡΡ ΠΌΠΎΡΡΠΎΠ² ΠΈ Π±ΠΎΠ»ΡΡΠΎΠ΅ ΡΡΡΠ΅ΡΡΠ²ΡΡΡΠ΅Π΅ ΠΎΡΡΡΠ°Π²Π°Π½ΠΈΠ΅ ΠΎΡΡΠ°ΡΡΠΈ ΠΎΠ±ΡΡΡΠ½ΡΠ΅ΡΡΡ Π²ΠΎΠ·ΡΠ°ΡΡΠΎΠΌ ΡΠ΅ΡΠΈ.ΠΠΎΠ»ΠΎΠ²ΠΈΠ½Π° Π²ΡΠ΅Ρ ΠΌΠΎΡΡΠΎΠ² Π² Π‘ΠΎΠ΅Π΄ΠΈΠ½Π΅Π½Π½ΡΡ Π¨ΡΠ°ΡΠ°Ρ Π±ΡΠ»Π° ΠΏΠΎΡΡΡΠΎΠ΅Π½Π° Π΄ΠΎ 1964 Π³ΠΎΠ΄Π°, Π° ΡΡΠ΅Π΄Π½ΠΈΠΉ Π²ΠΎΠ·ΡΠ°ΡΡ 607 380 ΠΌΠΎΡΡΠΎΠ² Π² ΡΡΡΠ°Π½Π΅ Π² Π½Π°ΡΡΠΎΡΡΠ΅Π΅ Π²ΡΠ΅ΠΌΡ ΡΠΎΡΡΠ°Π²Π»ΡΠ΅Ρ 42 Π³ΠΎΠ΄Π°. 4
ΠΠΎΠ³Π΄Π° Π²Π»Π°Π΄Π΅Π»ΡΡΡ ΠΌΠΎΡΡΠΎΠ² Π΄ΠΎΠ»ΠΆΠ½Ρ Π²ΡΠ±ΡΠ°ΡΡ ΠΏΡΠΎΡΠ΅ΡΡ ΠΈ ΠΏΠΎΡΡΠ°Π²ΡΠΈΠΊΠ° Π΄Π»Ρ ΠΏΡΠΎΠΈΠ·Π²ΠΎΠ΄ΡΡΠ²Π° ΠΊΡΠΈΡΠΈΡΠ΅ΡΠΊΠΈ Π²Π°ΠΆΠ½ΠΎΠ³ΠΎ ΠΌΠ΅ΡΠ°Π»Π»ΠΈΡΠ΅ΡΠΊΠΎΠ³ΠΎ ΠΊΠΎΠΌΠΏΠΎΠ½Π΅Π½ΡΠ°, ΠΎΠ½ΠΈ ΡΡΠ°Π»ΠΊΠΈΠ²Π°ΡΡΡΡ Ρ ΠΎΠ³ΡΠΎΠΌΠ½ΡΠΌ ΠΊΠΎΠ»ΠΈΡΠ΅ΡΡΠ²ΠΎΠΌ Π²ΠΎΠ·ΠΌΠΎΠΆΠ½ΡΡ Π°Π»ΡΡΠ΅ΡΠ½Π°ΡΠΈΠ². ΠΠΎΡΡΡΠΏΠ½ΠΎ ΠΌΠ½ΠΎΠΆΠ΅ΡΡΠ²ΠΎ ΠΏΡΠΎΡΠ΅ΡΡΠΎΠ² ΠΌΠ΅ΡΠ°Π»Π»ΠΎΠΎΠ±ΡΠ°Π±ΠΎΡΠΊΠΈ, ΠΊΠ°ΠΆΠ΄ΡΠΉ ΠΈΠ· ΠΊΠΎΡΠΎΡΡΡ ΠΏΡΠ΅Π΄Π»Π°Π³Π°Π΅Ρ ΡΠ½ΠΈΠΊΠ°Π»ΡΠ½ΡΠΉ Π½Π°Π±ΠΎΡ Π²ΠΎΠ·ΠΌΠΎΠΆΠ½ΠΎΡΡΠ΅ΠΉ, Π·Π°ΡΡΠ°Ρ ΠΈ ΠΏΡΠ΅ΠΈΠΌΡΡΠ΅ΡΡΠ². ΠΡΠΎΡΠ΅ΡΡ ΠΊΠΎΠ²ΠΊΠΈ ΠΈΠ΄Π΅Π°Π»ΡΠ½ΠΎ ΠΏΠΎΠ΄Ρ ΠΎΠ΄ΠΈΡ Π΄Π»Ρ ΠΌΠ½ΠΎΠ³ΠΈΡ ΠΎΠ±Π»Π°ΡΡΠ΅ΠΉ ΠΏΡΠΈΠΌΠ΅Π½Π΅Π½ΠΈΡ.Π€Π°ΠΊΡΠΈΡΠ΅ΡΠΊΠΈ, ΠΊΠΎΠ²ΠΊΠ° ΡΠ°ΡΡΠΎ ΡΠ²Π»ΡΠ΅ΡΡΡ ΠΎΠΏΡΠΈΠΌΠ°Π»ΡΠ½ΡΠΌ ΠΏΡΠΎΡΠ΅ΡΡΠΎΠΌ ΠΊΠ°ΠΊ Ρ ΡΠΎΡΠΊΠΈ Π·ΡΠ΅Π½ΠΈΡ ΠΊΠ°ΡΠ΅ΡΡΠ²Π° Π΄Π΅ΡΠ°Π»Π΅ΠΉ, ΡΠ°ΠΊ ΠΈ Ρ ΡΠΎΡΠΊΠΈ Π·ΡΠ΅Π½ΠΈΡ ΡΡΠΎΠΈΠΌΠΎΡΡΠΈ, ΠΎΡΠΎΠ±Π΅Π½Π½ΠΎ Π΄Π»Ρ ΠΏΡΠΈΠ»ΠΎΠΆΠ΅Π½ΠΈΠΉ, ΡΡΠ΅Π±ΡΡΡΠΈΡ ΠΌΠ°ΠΊΡΠΈΠΌΠ°Π»ΡΠ½ΠΎΠΉ ΠΏΡΠΎΡΠ½ΠΎΡΡΠΈ Π΄Π΅ΡΠ°Π»ΠΈ, Π½Π΅ΡΡΠ°Π½Π΄Π°ΡΡΠ½ΡΡ ΡΠ°Π·ΠΌΠ΅ΡΠΎΠ² ΠΈΠ»ΠΈ ΠΊΡΠΈΡΠΈΡΠ΅ΡΠΊΠΈΡ Ρ Π°ΡΠ°ΠΊΡΠ΅ΡΠΈΡΡΠΈΠΊ ΠΏΡΠΎΠΈΠ·Π²ΠΎΠ΄ΠΈΡΠ΅Π»ΡΠ½ΠΎΡΡΠΈ. Π’Π°ΠΊ ΠΏΠΎΡΠ΅ΠΌΡ ΠΆΠ΅ Π½Π° ΠΏΠΈΠΊΠ΅ ΡΡΡΠΎΠΈΡΠ΅Π»ΡΡΡΠ²Π° ΠΌΠΎΡΡΠΎΠ² (ΠΎΠΊ. 1960 Π³.) ΡΠ°ΠΊ ΠΌΠ½ΠΎΠ³ΠΎ ΠΈΠ½ΠΆΠ΅Π½Π΅ΡΠΎΠ² ΠΏΡΠ΅Π΄ΠΏΠΎΡΠ»ΠΈ ΠΎΡΠ»ΠΈΠ²ΠΊΡ ΠΏΠΎΠΊΠΎΠ²ΠΊΠ΅?
Π ΡΠΎΠΆΠ°Π»Π΅Π½ΠΈΡ, Π±ΠΎΠ»ΡΡΠΈΠ½ΡΡΠ²ΠΎ ΡΠ΅Π΄Π΅ΡΠ°Π»ΡΠ½ΡΡ ΡΡΠ°Π½Π΄Π°ΡΡΠΎΠ² Π±Π΅Π·ΠΎΠΏΠ°ΡΠ½ΠΎΡΡΠΈ ΠΌΠΎΡΡΠΎΠ² Π½Π΅ Π±ΡΠ»ΠΎ ΡΠ°Π·ΡΠ°Π±ΠΎΡΠ°Π½ΠΎ Π΄ΠΎ ΠΊΠΎΠ½ΡΠ° 1960-Ρ Π³ΠΎΠ΄ΠΎΠ² Π² ΠΎΡΠ²Π΅Ρ Π½Π° ΠΎΠ±ΡΡΡΠ΅Π½ΠΈΠ΅ ΠΌΠΎΡΡΠ° ΡΠ΅ΡΠ΅Π· ΡΠ΅ΠΊΡ ΠΠ³Π°ΠΉΠΎ. ΠΠ²Π°ΡΠΈΡ Π±ΡΠ»Π° Π²ΡΠ·Π²Π°Π½Π° ΠΊΠΎΡΡΠΎΠ·ΠΈΠ΅ΠΉ ΠΈ ΡΠ°Π·ΡΡΡΠ΅Π½ΠΈΠ΅ΠΌ ΠΌΠΎΡΡΠ°, ΠΊΠΎΡΠΎΡΡΠΉ ΠΎΡΠ»Π°Π±ΠΈΠ» Π΅Π³ΠΎ Π΄ΠΎ ΡΠΎΡΠΊΠΈ ΠΎΠ±ΡΡΡΠ΅Π½ΠΈΡ, Π² ΡΠ΅Π·ΡΠ»ΡΡΠ°ΡΠ΅ ΡΠ΅Π³ΠΎ ΠΏΠΎΠ³ΠΈΠ±Π»ΠΎ 46 ΡΠ΅Π»ΠΎΠ²Π΅ΠΊ.ΠΠΎΡΠ»Π΅ Π°Π½Π°Π»ΠΈΠ·Π° Π±ΡΠ»ΠΎ ΠΎΠ±Π½Π°ΡΡΠΆΠ΅Π½ΠΎ, ΡΡΠΎ Π²ΠΎ Π²ΡΠ΅ΠΌΡ ΠΏΡΠΎΡΠ΅ΡΡΠ° Π»ΠΈΡΡΡ Π² ΡΡΠ°Π»ΡΠ½ΠΎΠΉ ΠΏΡΠΎΡΡΠΈΠ½Π΅, ΠΈΡΠΏΠΎΠ»ΡΠ·ΠΎΠ²Π°Π½Π½ΠΎΠΉ Π² ΠΊΠΎΠ½ΡΡΡΡΠΊΡΠΈΠΈ ΠΌΠΎΡΡΠ°, ΠΎΠ±ΡΠ°Π·ΠΎΠ²Π°Π»Π°ΡΡ ΠΌΠΈΠΊΡΠΎΡΠΊΠΎΠΏΠΈΡΠ΅ΡΠΊΠ°Ρ ΡΡΠ΅ΡΠΈΠ½Π°, ΡΠΎ Π²ΡΠ΅ΠΌΠ΅Π½Π΅ΠΌ Π½Π°ΠΏΡΡΠΆΠ΅Π½ΠΈΠ΅ ΠΈ ΠΊΠΎΡΡΠΎΠ·ΠΈΠΎΠ½Π½Π°Ρ ΡΡΡΠ°Π»ΠΎΡΡΡ ΠΏΡΠΈΠ²Π΅Π»ΠΈ ΠΊ ΡΠΎΡΡΡ ΡΡΠ΅ΡΠΈΠ½Ρ, ΠΏΠΎΠΊΠ° ΠΊΠΎΠΌΠΏΠΎΠ½Π΅Π½Ρ Π½Π΅ Π²ΡΡΠ΅Π» ΠΈΠ· ΡΡΡΠΎΡ. Π‘Π΅Π³ΠΎΠ΄Π½Ρ Ρ ΠΎΡΠΎΡΠΎ ΠΈΠ·Π²Π΅ΡΡΠ½ΠΎ, ΡΡΠΎ ΠΎΡΠ»ΠΈΠ²ΠΊΠ°ΠΌ Π½Π΅ Ρ Π²Π°ΡΠ°Π΅Ρ Π½Π΅ΠΏΡΠ΅ΡΡΠ²Π½ΠΎΠ³ΠΎ ΠΏΠΎΡΠΎΠΊΠ° Π·Π΅ΡΠ½Π°, ΠΌΠ΅Π»ΠΊΠΎΠΉ ΡΡΡΡΠΊΡΡΡΡ Π·Π΅ΡΠ½Π° ΠΈ Π½Π°ΠΏΡΠ°Π²Π»Π΅Π½Π½ΠΎΠΉ ΠΏΡΠΎΡΠ½ΠΎΡΡΠΈ, Π½Π΅ΠΎΠ±Ρ ΠΎΠ΄ΠΈΠΌΡΡ Π΄Π»Ρ ΠΊΡΠΈΡΠΈΡΠ΅ΡΠΊΠΈΡ ΠΎΠΏΠ΅ΡΠ°ΡΠΈΠΉ, Π½Π΅ΡΡΡΠΈΡ Π½Π°Π³ΡΡΠ·ΠΊΡ. ΠΡΡΡΡΡΡΠ²ΠΈΠ΅ ΠΏΡΠ°Π²ΠΈΠ»ΡΠ½ΠΎ ΠΎΡΠΈΠ΅Π½ΡΠΈΡΠΎΠ²Π°Π½Π½ΠΎΠ³ΠΎ ΠΏΠΎΡΠΎΠΊΠ° Π·Π΅ΡΠ½Π°, Π° ΡΠ°ΠΊΠΆΠ΅ ΠΈΠ·ΠΌΠ΅Π»ΡΡΠ΅Π½ΠΈΡ Π·Π΅ΡΠ½Π° ΠΌΠΎΠΆΠ΅Ρ ΠΏΡΠΈΠ²Π΅ΡΡΠΈ ΠΊ ΠΏΠΎΡΠ΅Π½ΡΠΈΠ°Π»ΡΠ½ΡΠΌ ΠΏΡΠΎΠ±Π»Π΅ΠΌΠ°ΠΌ Ρ ΡΠ΅Π»ΠΎΡΡΠ½ΠΎΡΡΡΡ Π΄Π΅ΡΠ°Π»Π΅ΠΉ, Π²ΡΠ·ΡΠ²Π°ΡΡΠΈΠΌ ΠΏΠΎΠ»ΠΎΠΌΠΊΠΈ Π² ΠΏΠΎΠ»Π΅Π²ΡΡ ΡΡΠ»ΠΎΠ²ΠΈΡΡ .
Π 60-Ρ Π³ΠΎΠ΄Π°Ρ Π² Π‘Π¨Π Π±ΡΠ»ΠΈ ΡΠΎΡΠ½ΠΈ Π»ΠΈΡΠ΅ΠΉΠ½ΡΡ Π·Π°Π²ΠΎΠ΄ΠΎΠ², ΠΊΠΎΡΠΎΡΡΠ΅ ΠΌΠΎΠ³Π»ΠΈ ΠΏΠΎΡΡΠ°Π²Π»ΡΡΡ ΡΠ»ΠΎΠΆΠ½ΡΠ΅ ΠΈΠ»ΠΈ ΠΊΡΡΠΏΠ½ΡΠ΅ ΠΌΠ΅ΡΠ°Π»Π»ΠΈΡΠ΅ΡΠΊΠΈΠ΅ ΠΊΠΎΠΌΠΏΠΎΠ½Π΅Π½ΡΡ, Π½Π΅ΠΎΠ±Ρ ΠΎΠ΄ΠΈΠΌΡΠ΅ Π΄Π»Ρ ΠΌΠΎΡΡΠΎΠ²ΡΡ ΡΠ°Π±ΠΎΡ. ΠΡΠ»ΠΈΠ²ΠΊΠΈ Π±ΡΠ»ΠΈ Π΄Π΅ΡΠ΅Π²ΡΠΌΠΈ ΠΈ ΠΌΠ½ΠΎΠ³ΠΎΡΠΈΡΠ»Π΅Π½Π½ΡΠΌΠΈ ΠΏΠΎ ΡΡΠ°Π²Π½Π΅Π½ΠΈΡ ΡΠΎ ΡΡΠ°Π»ΡΠ½ΡΠΌΠΈ ΠΏΠΎΠΊΠΎΠ²ΠΊΠ°ΠΌΠΈ ΡΠΎΠ³ΠΎ Π²ΡΠ΅ΠΌΠ΅Π½ΠΈ. ΠΠ΄Π½Π°ΠΊΠΎ, ΠΏΠΎΡΠΊΠΎΠ»ΡΠΊΡ ΡΠΏΡΠΎΡ Π½Π° ΡΡΠ°Π»ΡΠ½ΡΠ΅ ΠΎΡΠ»ΠΈΠ²ΠΊΠΈ ΠΏΡΠ΅Π²ΡΡΠΈΠ» ΠΏΡΠ΅Π΄Π»ΠΎΠΆΠ΅Π½ΠΈΠ΅, ΠΊΠΎΠΌΠΏΠ°Π½ΠΈΠΈ Π½Π°ΡΠ°Π»ΠΈ ΠΈΡΠΊΠ°ΡΡ ΡΠ΅ΡΠ΅Π½ΠΈΡ Π·Π° ΠΏΡΠ΅Π΄Π΅Π»Π°ΠΌΠΈ Π‘Π¨Π ΠΈ ΠΠ°Π½Π°Π΄Ρ, ΡΡΠΎ Π² ΠΊΠΎΠ½Π΅ΡΠ½ΠΎΠΌ ΠΈΡΠΎΠ³Π΅ ΠΏΠΎΠ²Π»ΠΈΡΠ»ΠΎ Π½Π° ΡΠ΅ΠΏΠΎΡΠΊΡ ΠΏΠΎΡΡΠ°Π²ΠΎΠΊ Π΄Π²ΡΠΌΡ ΡΠΏΠΎΡΠΎΠ±Π°ΠΌΠΈ:
- ΠΡΠΎ Π΄Π°Π»ΠΎ Π½Π°ΡΠ°Π»ΠΎ ΠΎΡΡΠΎΡΠ½ΠΎΠΌΡ Π²Π°ΡΠΈΠ°Π½ΡΡ ΡΡΠ°Π»ΡΠ½ΠΎΠ³ΠΎ Π»ΠΈΡΡΡ, ΠΊΠΎΡΠΎΡΠΎΠ΅ Π΄ΠΎΡΡΠΈΠ³Π»ΠΎ ΡΠ²ΠΎΠ΅Π³ΠΎ Π°ΠΏΠΎΠ³Π΅Ρ ΠΈ Π½Π°Π½Π΅ΡΠ»ΠΎ Π·Π½Π°ΡΠΈΡΠ΅Π»ΡΠ½ΡΠΉ ΡΡΠ΅ΡΠ± ΠΎΡΠ΅ΡΠ΅ΡΡΠ²Π΅Π½Π½ΠΎΠΉ ΠΏΡΠΎΠΌΡΡΠ»Π΅Π½Π½ΠΎΡΡΠΈ Π² ΠΏΠΎΡΠ»Π΅Π΄ΡΡΡΠΈΠ΅ Π΄Π΅ΡΡΡΠΈΠ»Π΅ΡΠΈΡ. Π ΡΠΎ Π²ΡΠ΅ΠΌΡ OEM-ΠΏΡΠΎΠΈΠ·Π²ΠΎΠ΄ΠΈΡΠ΅Π»ΠΈ
- Π½Π΅ Π±ΡΠ»ΠΈ Π΄ΠΎΠ²ΠΎΠ»ΡΠ½Ρ ΡΠ΅ΠΌ, ΡΡΠΎΠ±Ρ Π΄ΠΎΠΆΠ΄Π°ΡΡΡΡ ΠΏΠΎΠ»Π½ΠΎΠ³ΠΎ ΡΠ°Π·Π²ΠΈΡΠΈΡ ΠΎΡΡΠΎΡΠ½ΠΎΠ³ΠΎ Π²Π°ΡΠΈΠ°Π½ΡΠ°, ΠΏΠΎΠ»ΡΠ·ΠΎΠ²Π°ΡΠ΅Π»ΠΈ Π»ΠΈΡΡΡ Π°Π³ΡΠ΅ΡΡΠΈΠ²Π½ΠΎ Π½Π°ΡΠ°Π»ΠΈ ΠΈΠ½Π²Π΅ΡΡΠΈΡΠΎΠ²Π°ΡΡ Π² Π°Π»ΡΡΠ΅ΡΠ½Π°ΡΠΈΠ²Π½ΡΠΉ ΠΏΡΠΎΡΠ΅ΡΡ — ΠΏΡΠΎΠΈΠ·Π²ΠΎΠ΄ΡΡΠ²ΠΎ ΡΡΠ°Π»ΠΈ. Π€Π°ΠΊΡΠΈΡΠ΅ΡΠΊΠΈ, Π½Π°Π»ΠΈΡΠΈΠ΅ ΡΠ°Π±ΡΠΈΠΊ ΠΏΡΠ°ΠΊΡΠΈΡΠ΅ΡΠΊΠΈ Π½Π° ΠΊΠ°ΠΆΠ΄ΠΎΠΌ ΠΏΡΠΎΠΈΠ·Π²ΠΎΠ΄ΡΡΠ²Π΅Π½Π½ΠΎΠΌ ΠΏΡΠ΅Π΄ΠΏΡΠΈΡΡΠΈΠΈ — ΡΡΠΎ ΠΌΡ ΡΡΠΈΡΠ°Π΅ΠΌ ΡΠ°ΠΌΠΎ ΡΠΎΠ±ΠΎΠΉ ΡΠ°Π·ΡΠΌΠ΅ΡΡΠΈΠΌΡΡ ΡΠ΅Π³ΠΎΠ΄Π½Ρ — Π½Π΅ ΡΡΡΠ΅ΡΡΠ²ΠΎΠ²Π°Π»ΠΎ Π΄ΠΎ ΠΊΠΎΠ½ΡΠ° 1970-Ρ Π³ΠΎΠ΄ΠΎΠ² ΠΈ ΡΠ²Π»ΡΠ΅ΡΡΡ ΠΏΡΡΠΌΡΠΌ ΡΠ΅Π·ΡΠ»ΡΡΠ°ΡΠΎΠΌ Π²ΡΡΠ΅ΡΠΏΠΎΠΌΡΠ½ΡΡΠΎΠ³ΠΎ.
Π Π½Π°ΡΡΠΎΡΡΠ΅Π΅ Π²ΡΠ΅ΠΌΡ ΡΡΠ°Π»Π΅Π»ΠΈΡΠ΅ΠΉΠ½ΠΎΠ΅ ΠΏΡΠΎΠΈΠ·Π²ΠΎΠ΄ΡΡΠ²ΠΎ Π² Π‘Π΅Π²Π΅ΡΠ½ΠΎΠΉ ΠΠΌΠ΅ΡΠΈΠΊΠ΅ ΡΠ²Π»ΡΠ΅ΡΡΡ ΡΠ΅Π½ΡΡ ΡΠ°ΠΌΠΎΠ³ΠΎ ΡΠ΅Π±Ρ.Π 2015 Π³ΠΎΠ΄Ρ ΠΎΡΡΠ°Π»ΠΎΡΡ ΠΌΠ΅Π½Π΅Π΅ 200 ΡΡΠ°Π»Π΅ΠΏΠ»Π°Π²ΠΈΠ»ΡΠ½ΡΡ Π·Π°Π²ΠΎΠ΄ΠΎΠ², ΡΡΠΎ Π² ΠΏΡΡΡ ΡΠ°Π· Π±ΠΎΠ»ΡΡΠ΅, ΡΠ΅ΠΌ Π² 1970-Ρ Π³ΠΎΠ΄Π°Ρ .
Π‘Π΅Π³ΠΎΠ΄Π½ΡΡΠ½ΠΈΠ΅ Π±ΠΎΠ»Π΅Π΅ ΡΡΠ΅Π±ΠΎΠ²Π°ΡΠ΅Π»ΡΠ½ΡΠ΅ ΠΏΠΎΠ»ΡΠ·ΠΎΠ²Π°ΡΠ΅Π»ΠΈ ΠΌΠ°ΡΠ΅ΡΠΈΠ°Π»ΠΎΠ² Π² ΡΠΈΠ»Ρ ΠΏΠΎΠ²ΡΠ΅Π΄Π½Π΅Π²Π½ΡΡ ΡΠΊΠΎΠ½ΠΎΠΌΠΈΡΠ΅ΡΠΊΠΈΡ ΠΈ ΠΊΠΎΠ½ΠΊΡΡΠ΅Π½ΡΠ½ΡΡ ΡΠ΅Π°Π»ΠΈΠΉ Π²ΡΠ΅ ΡΠ°ΡΠ΅ Π²ΡΠ½ΡΠΆΠ΄Π΅Π½Ρ ΠΈΡΠΊΠ°ΡΡ Π»ΡΡΡΠ΅Π΅ ΡΠ΅ΡΠ΅Π½ΠΈΠ΅ Π΄Π»Ρ ΡΠ΅ΠΏΠΎΡΠΊΠΈ ΠΏΠΎΡΡΠ°Π²ΠΎΠΊ ΠΈ Π±ΠΎΠ»Π΅Π΅ ΠΏΡΠΎΡΠ½ΡΠΉ, Π½Π°Π΄Π΅ΠΆΠ½ΡΠΉ ΠΈ ΡΠ΅Ρ Π½ΠΈΡΠ΅ΡΠΊΠΈ ΡΠΎΠ²Π΅ΡΡΠ΅Π½Π½ΡΠΉ ΠΏΡΠΎΠ΄ΡΠΊΡ. ΠΠ΄Π½Π°ΠΊΠΎ ΠΊΠΎΠ³Π΄Π° Π΄Π΅Π»ΠΎ Π΄ΠΎΡ ΠΎΠ΄ΠΈΡ Π΄ΠΎ ΠΏΡΠΈΠ½ΡΡΠΈΡ ΡΠ΅ΡΠ΅Π½ΠΈΡ ΠΎ ΡΡΡΠΎΠΈΡΠ΅Π»ΡΡΡΠ²Π΅ ΠΈ ΡΠ΅ΠΌΠΎΠ½ΡΠ΅ ΠΌΠΎΡΡΠ°, Π²ΡΠ΅ ΡΠ°Π²Π½ΠΎ Π²ΠΎΠ·Π½ΠΈΠΊΠ°Π΅Ρ Π²ΠΎΠΏΡΠΎΡβ¦ Β«Π»ΠΈΡΡΠ΅, ΠΈΠ·Π³ΠΎΡΠΎΠ²Π»Π΅Π½ΠΈΠ΅ ΠΈΠ»ΠΈ ΠΊΠΎΠ²ΠΊΠ°?Β» Π Π΅Π°Π»ΡΠ½ΠΎΡΡΡ ΡΠΎΠ³ΠΎ, ΡΡΠΎ ΠΏΡΠΎΡΠ΅ΡΡ ΠΊΠΎΠ²ΠΊΠΈ ΠΏΡΠΎΡΠ΅Π» Π΄ΠΎΠ»Π³ΠΈΠΉ ΠΏΡΡΡ Ρ 1960-Ρ Π³ΠΎΠ΄ΠΎΠ², ΠΏΠΎΡΡΠ΅ΠΏΠ΅Π½Π½ΠΎ ΠΎΡΠΎΠ·Π½Π°Π΅ΡΡΡ.ΠΠ½ΠΆΠ΅Π½Π΅ΡΡ ΠΈ ΠΌΠ΅ΡΠ°Π»Π»ΡΡΠ³ΠΈ ΠΏΠΎΠ²ΡΡΠΈΠ»ΠΈ ΡΡΠΎΠ²Π΅Π½Ρ ΡΠ²ΠΎΠ΅Π³ΠΎ ΠΎΠ±ΡΠ°Π·ΠΎΠ²Π°Π½ΠΈΡ Π² ΠΎΠ±Π»Π°ΡΡΠΈ ΠΏΡΠΎΡΠ΅ΡΡΠΎΠ² ΠΎΠ±ΡΠ°Π±ΠΎΡΠΊΠΈ ΠΌΠ΅ΡΠ°Π»Π»ΠΎΠ² ΠΈ Π½Π°ΡΠ°Π»ΠΈ ΠΎΡΠ΅Π½ΠΈΠ²Π°ΡΡ Π΄ΠΎΠ»Π³ΠΎΡΡΠΎΡΠ½ΡΠ΅ ΠΏΡΠ΅ΠΈΠΌΡΡΠ΅ΡΡΠ²Π° ΠΏΠΎΠΊΠΎΠ²ΠΎΠΊ ΠΏΠΎ ΡΡΠ°Π²Π½Π΅Π½ΠΈΡ Ρ ΠΎΡΠ»ΠΈΠ²ΠΊΠ°ΠΌΠΈ ΠΈΠ»ΠΈ ΡΠ°Π±ΡΠΈΠΊΠ°ΡΠΈΡΠΌΠΈ. ΠΡΠΎΠΌΠ΅ ΡΠΎΠ³ΠΎ, ΡΠ΅Ρ Π½ΠΈΡΠ΅ΡΠΊΠΈΠΉ ΠΏΡΠΎΠ³ΡΠ΅ΡΡ ΡΠ΄Π΅Π»Π°Π» ΠΏΠΎΠΊΠΎΠ²ΠΊΠΈ ΡΡΠΎΠ»Ρ ΠΆΠ΅ ΠΊΠΎΠ½ΠΊΡΡΠ΅Π½ΡΠΎΡΠΏΠΎΡΠΎΠ±Π½ΡΠΌΠΈ ΠΏΠΎ ΡΠ΅Π½Π΅, ΠΊΠ°ΠΊ ΠΈ Π°Π»ΡΡΠ΅ΡΠ½Π°ΡΠΈΠ²Π½ΡΠ΅ ΠΌΠ΅ΡΠΎΠ΄Ρ, Π½ΠΎ ΠΏΡΠΈ ΡΡΠΎΠΌ ΠΏΡΠ΅Π΄ΠΎΡΡΠ°Π²ΠΈΠ» ΡΡΠ΅Π΄ΡΡΠ²Π° Π΄Π»Ρ ΡΠ΅ΡΠ΅Π½ΠΈΡ ΡΡΡΡΠΊΡΡΡΠ½ΠΎ Π½Π΅ΡΠΎΠ²Π΅ΡΡΠ΅Π½Π½ΡΡ ΠΈΠ»ΠΈ ΡΡΠ½ΠΊΡΠΈΠΎΠ½Π°Π»ΡΠ½ΠΎ ΡΡΡΠ°ΡΠ΅Π²ΡΠΈΡ ΠΏΡΠΎΠ±Π»Π΅ΠΌ, Ρ ΠΊΠΎΡΠΎΡΡΠΌΠΈ ΡΡΠ°Π»ΠΊΠΈΠ²Π°Π΅ΡΡΡ ΠΈΠ½ΡΡΠ°ΡΡΡΡΠΊΡΡΡΠ½Π°Ρ ΠΎΡΡΠ°ΡΠ»Ρ Π‘Π¨Π.
Π§ΡΠΎ ΡΠ°ΠΊΠΎΠ΅ ΠΊΠΎΠ²ΠΊΠ°?
ΠΠΎΡΡΡΠΏΠ½ΠΎ Π½Π΅ΡΠΊΠΎΠ»ΡΠΊΠΎ ΠΏΡΠΎΡΠ΅ΡΡΠΎΠ² ΠΊΠΎΠ²ΠΊΠΈ, Π² ΡΠΎΠΌ ΡΠΈΡΠ»Π΅ ΡΡΠ°ΠΌΠΏΠΎΠ²ΠΊΠ° Π΄Π»Ρ ΡΠ»Π΅ΠΏΠΊΠΎΠ² (ΡΠ°ΠΊΠΆΠ΅ ΠΈΠ·Π²Π΅ΡΡΠ½Π°Ρ ΠΊΠ°ΠΊ Π·Π°ΠΊΡΡΡΠ°Ρ ΡΡΠ°ΠΌΠΏΠ°), Ρ ΠΎΠ»ΠΎΠ΄Π½Π°Ρ ΡΡΠ°ΠΌΠΏΠΎΠ²ΠΊΠ° ΠΈ ΡΠΊΡΡΡΡΠ·ΠΈΡ.ΠΠ΄Π½Π°ΠΊΠΎ Π·Π΄Π΅ΡΡ ΠΌΡ ΠΏΠΎΠ΄ΡΠΎΠ±Π½ΠΎ ΠΎΠ±ΡΡΠ΄ΠΈΠΌ ΠΌΠ΅ΡΠΎΠ΄Ρ, ΠΏΡΠΈΠΌΠ΅Π½Π΅Π½ΠΈΠ΅ ΠΈ ΡΡΠ°Π²Π½ΠΈΡΠ΅Π»ΡΠ½ΡΠ΅ ΠΏΡΠ΅ΠΈΠΌΡΡΠ΅ΡΡΠ²Π° ΠΏΡΠΎΡΠ΅ΡΡΠΎΠ² ΠΎΡΠΊΡΡΡΠΎΠΉ ΡΡΠ°ΠΌΠΏΠΎΠ²ΠΊΠΈ. ΠΡ ΠΏΡΠΈΠ³Π»Π°ΡΠ°Π΅ΠΌ Π²Π°Ρ ΠΏΡΠΈΠ½ΡΡΡ Π²ΠΎ Π²Π½ΠΈΠΌΠ°Π½ΠΈΠ΅ ΡΡΡ ΠΈΠ½ΡΠΎΡΠΌΠ°ΡΠΈΡ ΠΏΡΠΈ Π²ΡΠ±ΠΎΡΠ΅ ΠΎΠΏΡΠΈΠΌΠ°Π»ΡΠ½ΠΎΠ³ΠΎ ΠΏΡΠΎΡΠ΅ΡΡΠ° Π΄Π»Ρ Π²Π°ΡΠΈΡ ΠΊΡΠΈΡΠΈΡΠ΅ΡΠΊΠΈ Π²Π°ΠΆΠ½ΡΡ ΠΏΡΠΈΠ»ΠΎΠΆΠ΅Π½ΠΈΠΉ.
ΠΠ° ΡΠ°ΠΌΠΎΠΌ Π±Π°Π·ΠΎΠ²ΠΎΠΌ ΡΡΠΎΠ²Π½Π΅ ΠΊΠΎΠ²ΠΊΠ° — ΡΡΠΎ ΠΏΡΠΎΡΠ΅ΡΡ ΡΠΎΡΠΌΠΎΠ²Π°Π½ΠΈΡ ΠΈ ΠΏΡΠΈΠ΄Π°Π½ΠΈΡ ΡΠΎΡΠΌΡ ΠΌΠ΅ΡΠ°Π»Π»Π°ΠΌ Ρ ΠΈΡΠΏΠΎΠ»ΡΠ·ΠΎΠ²Π°Π½ΠΈΠ΅ΠΌ ΠΌΠΎΠ»ΠΎΡΠΊΠ°, ΠΏΡΠ΅ΡΡΠΎΠ²Π°Π½ΠΈΡ ΠΈΠ»ΠΈ ΠΏΡΠΎΠΊΠ°ΡΠΊΠΈ. ΠΡΠΎΡΠ΅ΡΡ Π½Π°ΡΠΈΠ½Π°Π΅ΡΡΡ Ρ ΠΈΡΡ ΠΎΠ΄Π½ΠΎΠΉ Π·Π°Π³ΠΎΡΠΎΠ²ΠΊΠΈ, ΠΎΠ±ΡΡΠ½ΠΎ Π»ΠΈΡΠΎΠ³ΠΎ ΡΠ»ΠΈΡΠΊΠ° (ΠΈΠ»ΠΈ Β«Π·ΡΠ±ΡΠ°ΡΠΎΠΉΒ» Π·Π°Π³ΠΎΡΠΎΠ²ΠΊΠΈ, ΠΊΠΎΡΠΎΡΠ°Ρ ΡΠΆΠ΅ Π±ΡΠ»Π° Π²ΡΠΊΠΎΠ²Π°Π½Π° ΠΈΠ· Π»ΠΈΡΠΎΠ³ΠΎ ΡΠ»ΠΈΡΠΊΠ°), ΠΊΠΎΡΠΎΡΡΡ Π½Π°Π³ΡΠ΅Π²Π°ΡΡ Π΄ΠΎ ΡΠ΅ΠΌΠΏΠ΅ΡΠ°ΡΡΡΡ ΠΏΠ»Π°ΡΡΠΈΡΠ΅ΡΠΊΠΎΠΉ Π΄Π΅ΡΠΎΡΠΌΠ°ΡΠΈΠΈ, Π·Π°ΡΠ΅ΠΌ Π²ΡΡΠ°ΠΆΠΈΠ²Π°ΡΡ ΠΈΠ»ΠΈ Β«Π·Π°ΠΌΠ΅ΡΠΈΠ²Π°ΡΡΒ» ΠΌΠ΅ΠΆΠ΄Ρ ΡΡΠ°ΠΌΠΏΠ°ΠΌΠΈ Π΄ΠΎ ΠΆΠ΅Π»Π°Π΅ΠΌΠΎΠΉ ΡΠΎΡΠΌΡ. ΠΈ ΡΠ°Π·ΠΌΠ΅Ρ.
Π ΠΏΡΠΎΡΠ΅ΡΡΠ΅ Π³ΠΎΡΡΡΠ΅ΠΉ ΡΡΠ°ΠΌΠΏΠΎΠ²ΠΊΠΈ Π»ΠΈΡΠ°Ρ ΠΊΡΡΠΏΠ½ΠΎΠ·Π΅ΡΠ½ΠΈΡΡΠ°Ρ ΡΡΡΡΠΊΡΡΡΠ° ΡΠ°Π·ΡΡΡΠ°Π΅ΡΡΡ ΠΈ Π·Π°ΠΌΠ΅Π½ΡΠ΅ΡΡΡ Π±ΠΎΠ»Π΅Π΅ ΠΌΠ΅Π»ΠΊΠΈΠΌΠΈ Π·Π΅ΡΠ½Π°ΠΌΠΈ. Π£ΡΠ°Π΄ΠΊΠ° ΠΈ Π³Π°Π·ΠΎΠ²Π°Ρ ΠΏΠΎΡΠΈΡΡΠΎΡΡΡ, ΠΏΡΠΈΡΡΡΠΈΠ΅ Π»ΠΈΡΠΎΠΌΡ ΠΌΠ΅ΡΠ°Π»Π»Ρ, ΠΊΠΎΠ½ΡΠΎΠ»ΠΈΠ΄ΠΈΡΡΡΡΡΡ Π·Π° ΡΡΠ΅Ρ ΡΠΌΠ΅Π½ΡΡΠ΅Π½ΠΈΡ ΡΠ°Π·ΠΌΠ΅ΡΠ° ΡΠ»ΠΈΡΠΊΠ°, Π΄ΠΎΡΡΠΈΠΆΠ΅Π½ΠΈΡ ΠΏΡΠΎΡΠ½ΡΡ ΡΠ΅Π½ΡΡΠΎΠ² ΠΈ ΡΡΡΡΠΊΡΡΡΠ½ΠΎΠΉ ΡΠ΅Π»ΠΎΡΡΠ½ΠΎΡΡΠΈ. Π’Π°ΠΊΠΈΠΌ ΠΎΠ±ΡΠ°Π·ΠΎΠΌ, ΠΌΠ΅Ρ Π°Π½ΠΈΡΠ΅ΡΠΊΠΈΠ΅ ΡΠ²ΠΎΠΉΡΡΠ²Π° ΡΠ»ΡΡΡΠ°ΡΡΡΡ Π·Π° ΡΡΠ΅Ρ ΡΠΌΠ΅Π½ΡΡΠ΅Π½ΠΈΡ Π»ΠΈΡΠΎΠΉ ΡΡΡΡΠΊΡΡΡΡ, ΠΏΡΡΡΠΎΡ ΠΈ ΡΠ°ΡΡΠ»ΠΎΠ΅Π½ΠΈΡ.
Π ΡΠΎ Π²ΡΠ΅ΠΌΡ ΠΊΠ°ΠΊ ΡΡΠ°ΠΌΠΏΠΎΠ²ΠΊΠ° ΠΈΠ»ΠΈ Π·Π°ΠΊΡΡΡΠ°Ρ ΡΡΠ°ΠΌΠΏΠΎΠ²ΠΊΠ° ΠΎΠ³ΡΠ°Π½ΠΈΡΠΈΠ²Π°ΡΡ ΠΌΠ΅ΡΠ°Π»Π» Π² ΡΡΠ°ΠΌΠΏΠ°Ρ , ΠΎΡΠΊΡΡΡΠ°Ρ ΡΡΠ°ΠΌΠΏΠΎΠ²ΠΊΠ° ΠΎΡΠ»ΠΈΡΠ°Π΅ΡΡΡ ΡΠ΅ΠΌ, ΡΡΠΎ ΠΌΠ΅ΡΠ°Π»Π» Π½ΠΈΠΊΠΎΠ³Π΄Π° ΠΏΠΎΠ»Π½ΠΎΡΡΡΡ Π½Π΅ ΠΎΠ³ΡΠ°Π½ΠΈΡΠΈΠ²Π°Π΅ΡΡΡ ΠΈΠ»ΠΈ ΡΠ΄Π΅ΡΠΆΠΈΠ²Π°Π΅ΡΡΡ Π² ΡΡΠ°ΠΌΠΏΠ°Ρ .ΠΠΎΠ»ΡΡΠΈΠ½ΡΡΠ²ΠΎ ΠΏΠΎΠΊΠΎΠ²ΠΎΠΊ Π² ΠΎΡΠΊΡΡΡΡΡ ΡΡΠ°ΠΌΠΏΠ°Ρ ΠΏΡΠΎΠΈΠ·Π²ΠΎΠ΄ΡΡΡΡ Π½Π° ΠΏΠ»ΠΎΡΠΊΠΈΡ ΡΡΠ°ΠΌΠΏΠ°Ρ . ΠΠ΄Π½Π°ΠΊΠΎ ΡΠ°ΠΊΠΆΠ΅ ΠΈΡΠΏΠΎΠ»ΡΠ·ΡΡΡΡΡ ΠΊΡΡΠ³Π»ΡΠ΅ ΠΎΠ±ΠΆΠΈΠΌΠ½ΡΠ΅ ΠΌΠ°ΡΡΠΈΡΡ, V-ΠΎΠ±ΡΠ°Π·Π½ΡΠ΅ ΠΌΠ°ΡΡΠΈΡΡ, ΠΎΠΏΡΠ°Π²ΠΊΠΈ, ΡΡΠΈΡΡΡ ΠΈ Π½Π΅Π·Π°ΠΊΡΠ΅ΠΏΠ»Π΅Π½Π½ΡΠ΅ ΠΈΠ½ΡΡΡΡΠΌΠ΅Π½ΡΡ Π² Π·Π°Π²ΠΈΡΠΈΠΌΠΎΡΡΠΈ ΠΎΡ ΠΆΠ΅Π»Π°Π΅ΠΌΠΎΠΉ ΠΊΠΎΠ½ΡΠΈΠ³ΡΡΠ°ΡΠΈΠΈ Π΄Π΅ΡΠ°Π»ΠΈ ΠΈ Π΅Π΅ ΡΠ°Π·ΠΌΠ΅ΡΠ°.
Π‘ΡΠ°Π²Π½Π΅Π½ΠΈΠ΅ ΠΎΡΠΊΡΡΡΡΡ ΡΡΠ°ΠΌΠΏΠΎΠ² ΠΈ ΠΎΡΠ»ΠΈΠ²ΠΎΠΊ
Forging ΠΎΠ±Π΅ΡΠΏΠ΅ΡΠΈΠ²Π°Π΅Ρ Π·Π½Π°ΡΠΈΡΠ΅Π»ΡΠ½ΡΠ΅ ΡΠΊΠΎΠ½ΠΎΠΌΠΈΡΠ΅ΡΠΊΠΈΠ΅, ΠΏΡΠΎΠΈΠ·Π²ΠΎΠ΄ΡΡΠ²Π΅Π½Π½ΡΠ΅ ΠΈ ΠΊΠ°ΡΠ΅ΡΡΠ²Π΅Π½Π½ΡΠ΅ ΠΏΡΠ΅ΠΈΠΌΡΡΠ΅ΡΡΠ²Π° ΠΏΠΎ ΡΡΠ°Π²Π½Π΅Π½ΠΈΡ Ρ Π°Π»ΡΡΠ΅ΡΠ½Π°ΡΠΈΠ²Π½ΡΠΌΠΈ ΠΏΡΠΎΡΠ΅ΡΡΠ°ΠΌΠΈ ΠΌΠ΅ΡΠ°Π»Π»ΠΎΠΎΠ±ΡΠ°Π±ΠΎΡΠΊΠΈ, ΡΠ°ΠΊΠΈΠΌΠΈ ΠΊΠ°ΠΊ Π½Π°ΠΏΡΠ°Π²Π»Π΅Π½Π½Π°Ρ ΠΏΡΠΎΡΠ½ΠΎΡΡΡ, ΡΡΡΡΠΊΡΡΡΠ½Π°Ρ ΠΏΡΠΎΡΠ½ΠΎΡΡΡ ΠΈ ΡΠ΄Π°ΡΠ½Π°Ρ Π²ΡΠ·ΠΊΠΎΡΡΡ. Π£Π·Π½Π°ΠΉΡΠ΅ Π±ΠΎΠ»ΡΡΠ΅ ΠΎ ΡΡΠ°Π²Π½Π΅Π½ΠΈΠΈ ΡΠ΅Π»ΠΎΡΡΠ½ΠΎΡΡΠΈ Π΄Π΅ΡΠ°Π»Π΅ΠΉ ΠΈ ΠΏΠΎΡΠΎΠΊΠ° Π·Π΅ΡΠ½Π°, ΠΏΠΎΡΠ΅ΡΠΈΠ² Π½Π°ΡΡ ΡΡΡΠ°Π½ΠΈΡΡ Β«ΠΠΎΠ²ΠΊΠ° 101: ΠΏΡΠ΅ΠΈΠΌΡΡΠ΅ΡΡΠ²Π° ΠΊΠΎΠ²ΠΊΠΈΒ».
ΠΠΎΠ²ΠΊΠ° ΡΠ°ΠΊΠΆΠ΅ ΠΎΠ±Π΅ΡΠΏΠ΅ΡΠΈΠ²Π°Π΅Ρ ΡΡΠ΅Π΄ΡΡΠ²Π° Π΄Π»Ρ Π²ΡΡΠ°Π²Π½ΠΈΠ²Π°Π½ΠΈΡ ΠΏΠΎΡΠΎΠΊΠ° Π·Π΅ΡΠ½Π° Π΄Π»Ρ Π½Π°ΠΈΠ»ΡΡΡΠ΅Π³ΠΎ Π΄ΠΎΡΡΠΈΠΆΠ΅Π½ΠΈΡ ΠΆΠ΅Π»Π°Π΅ΠΌΠΎΠΉ Π½Π°ΠΏΡΠ°Π²Π»Π΅Π½Π½ΠΎΡΡΠΈ. Π₯ΠΎΡΠΎΡΠΎ ΠΈΠ·Π²Π΅ΡΡΠ½ΠΎ, ΡΡΠΎ ΠΌΠΎΡΡΡ ΡΠΊΠ»ΠΎΠ½Π½Ρ ΠΊ ΡΠ°ΡΡΡΠ΅ΡΠΊΠΈΠ²Π°Π½ΠΈΡ ΠΈ ΡΡΡΠ°Π»ΠΎΡΡΠ½ΡΠΌ ΠΏΡΠΎΠ±Π»Π΅ΠΌΠ°ΠΌ. ΠΠΎΡΡΠΎΠΌΡ ΠΏΠΎΠ»Π΅Π·Π½ΠΎ ΠΏΠΎΠ½ΠΈΠΌΠ°ΡΡ, ΠΊΠ°ΠΊ ΠΏΡΠ°Π²ΠΈΠ»ΡΠ½Π°Ρ ΠΎΡΠΈΠ΅Π½ΡΠ°ΡΠΈΡ ΠΏΠΎΡΠΎΠΊΠ° Π·Π΅ΡΠ½Π° ΠΌΠΎΠΆΠ΅Ρ ΠΎΠ±Π΅ΡΠΏΠ΅ΡΠΈΡΡ ΠΌΠ°ΠΊΡΠΈΠΌΠ°Π»ΡΠ½ΠΎΠ΅ ΡΠΎΠΏΡΠΎΡΠΈΠ²Π»Π΅Π½ΠΈΠ΅ ΡΡΡΠ°Π»ΠΎΡΡΠΈ. ΠΡΠΈ ΠΎΡΠΊΡΡΡΠΎΠΉ ΡΡΠ°ΠΌΠΏΠΎΠ²ΠΊΠ΅ ΠΌΠ΅ΡΠ°Π»Π» (ΠΏΠΎΠ΄Π²Π΅ΡΠ³ΡΠΈΠΉΡΡ Π²ΠΎΠ·Π΄Π΅ΠΉΡΡΠ²ΠΈΡ ΡΠΆΠΈΠΌΠ°ΡΡΠ΅Π³ΠΎ Π½Π°ΠΏΡΡΠΆΠ΅Π½ΠΈΡ) Π±ΡΠ΄Π΅Ρ ΡΠ΅ΡΡ Π² Π»ΡΠ±ΠΎΠΌ Π½Π΅ΠΎΠ³ΡΠ°Π½ΠΈΡΠ΅Π½Π½ΠΎΠΌ Π½Π°ΠΏΡΠ°Π²Π»Π΅Π½ΠΈΠΈ. Π Π°ΡΡΠΈΡΡΡΡΠΈΠΉΡΡ ΠΌΠ΅ΡΠ°Π»Π» Π±ΡΠ΄Π΅Ρ ΡΠ°ΡΡΡΠ³ΠΈΠ²Π°ΡΡ ΡΡΡΠ΅ΡΡΠ²ΡΡΡΠΈΠ΅ Π·Π΅ΡΠ½Π° ΠΈ, Π΅ΡΠ»ΠΈ ΡΠ΅ΠΌΠΏΠ΅ΡΠ°ΡΡΡΠ° Π½Π°Ρ ΠΎΠ΄ΠΈΡΡΡ Π² ΠΏΡΠ΅Π΄Π΅Π»Π°Ρ Π΄ΠΈΠ°ΠΏΠ°Π·ΠΎΠ½Π° ΡΠ΅ΠΌΠΏΠ΅ΡΠ°ΡΡΡ ΠΊΠΎΠ²ΠΊΠΈ, ΡΠ΅ΠΊΡΠΈΡΡΠ°Π»Π»ΠΈΠ·ΠΎΠ²ΡΠ²Π°Π΅ΡΡΡ ΠΈ ΠΎΠ±ΡΠ°Π·ΡΠ΅Ρ Π½ΠΎΠ²ΡΠ΅ Π·Π΅ΡΠ½Π° Π±Π΅Π· Π΄Π΅ΡΠΎΡΠΌΠ°ΡΠΈΠΈ.ΠΡΠΎ ΠΎΠ±Π΅ΡΠΏΠ΅ΡΠΈΠ²Π°Π΅Ρ Π΄Π°ΠΆΠ΅ Π»ΡΡΡΡΡ ΡΡΡΠΎΠΉΡΠΈΠ²ΠΎΡΡΡ ΠΊ ΡΡΡΠ°Π»ΠΎΡΡΠΈ ΠΈ ΠΊΠΎΡΡΠΎΠ·ΠΈΠΈ ΠΏΠΎΠ΄ Π½Π°ΠΏΡΡΠΆΠ΅Π½ΠΈΠ΅ΠΌ, ΡΠ΅ΠΌ ΠΏΠΎΠΊΠΎΠ²ΠΊΠ°, ΠΊΠΎΡΠΎΡΠ°Ρ Π½Π΅ ΡΠΎΡΠΌΠΈΡΡΠ΅Ρ ΠΊΠΎΠ½ΡΡΡ Π΄Π΅ΡΠ°Π»ΠΈ.
ΠΡΠ° ΠΏΡΠ΅Π΄ΡΠΊΠ°Π·ΡΠ΅ΠΌΠ°Ρ ΡΡΡΡΠΊΡΡΡΠ½Π°Ρ ΡΠ΅Π»ΠΎΡΡΠ½ΠΎΡΡΡ, ΠΏΡΠΈΡΡΡΠ°Ρ ΠΏΡΠΎΡΠ΅ΡΡΡ ΠΊΠΎΠ²ΠΊΠΈ, ΡΠ½ΠΈΠΆΠ°Π΅Ρ ΡΡΠ΅Π±ΠΎΠ²Π°Π½ΠΈΡ ΠΊ ΠΊΠΎΠ½ΡΡΠΎΠ»Ρ Π΄Π΅ΡΠ°Π»Π΅ΠΉ, ΡΠΏΡΠΎΡΠ°Π΅Ρ ΡΠ΅ΡΠΌΠΎΠΎΠ±ΡΠ°Π±ΠΎΡΠΊΡ ΠΈ ΠΌΠ΅Ρ Π°Π½ΠΈΡΠ΅ΡΠΊΡΡ ΠΎΠ±ΡΠ°Π±ΠΎΡΠΊΡ ΠΈ ΠΎΠ±Π΅ΡΠΏΠ΅ΡΠΈΠ²Π°Π΅Ρ ΠΎΠΏΡΠΈΠΌΠ°Π»ΡΠ½ΡΡ ΡΠ°Π±ΠΎΡΡ Π΄Π΅ΡΠ°Π»ΠΈ Π² ΡΡΠ»ΠΎΠ²ΠΈΡΡ ΠΏΠΎΠ»Π΅Π²ΡΡ Π½Π°Π³ΡΡΠ·ΠΎΠΊ. ΠΡΡΠΎΠΊΠΎΠΏΡΠΎΡΠ½ΡΠ΅ ΡΠ²ΠΎΠΉΡΡΠ²Π° ΠΏΡΠΎΡΠ΅ΡΡΠ° ΠΊΠΎΠ²ΠΊΠΈ ΠΌΠΎΠ³ΡΡ Π±ΡΡΡ ΠΈΡΠΏΠΎΠ»ΡΠ·ΠΎΠ²Π°Π½Ρ Π΄Π»Ρ ΡΠΌΠ΅Π½ΡΡΠ΅Π½ΠΈΡ ΡΠΎΠ»ΡΠΈΠ½Ρ ΡΠ΅ΡΠ΅Π½ΠΈΡ ΠΈ ΠΎΠ±ΡΠ΅Π³ΠΎ Π²Π΅ΡΠ° Π±Π΅Π· Π½Π°ΡΡΡΠ΅Π½ΠΈΡ ΡΠ΅Π»ΠΎΡΡΠ½ΠΎΡΡΠΈ ΠΊΠΎΠ½Π΅ΡΠ½ΠΎΠΉ Π΄Π΅ΡΠ°Π»ΠΈ.
ΠΡΠΎΠΌΠ΅ ΡΠΎΠ³ΠΎ, ΠΊΠΎΠ²ΠΊΠ° ΠΌΠΎΠΆΠ΅Ρ Π·Π°ΠΌΠ΅ΡΠ½ΠΎ ΡΠ½ΠΈΠ·ΠΈΡΡ ΠΌΠ°ΡΠ΅ΡΠΈΠ°Π»ΡΠ½ΡΠ΅ Π·Π°ΡΡΠ°ΡΡ, ΠΏΠΎΡΠΊΠΎΠ»ΡΠΊΡ Π΄Π»Ρ ΠΏΡΠΎΠΈΠ·Π²ΠΎΠ΄ΡΡΠ²Π° Π΄Π΅ΡΠ°Π»Π΅ΠΉ ΠΌΠ½ΠΎΠ³ΠΈΡ ΡΠΎΡΠΌ ΡΡΠ΅Π±ΡΠ΅ΡΡΡ ΠΌΠ΅Π½ΡΡΠ΅ ΠΈΡΡ ΠΎΠ΄Π½ΠΎΠ³ΠΎ ΠΌΠ°ΡΠ΅ΡΠΈΠ°Π»Π°. Π‘Π»Π΅Π΄ΠΎΠ²Π°ΡΠ΅Π»ΡΠ½ΠΎ, Π΄Π»Ρ ΡΠΈΡΡΠΎΠ²ΠΎΠΉ ΠΎΠ±ΡΠ°Π±ΠΎΡΠΊΠΈ Π΄Π΅ΡΠ°Π»ΠΈ ΡΡΠ΅Π±ΡΠ΅ΡΡΡ ΠΌΠ΅Π½ΡΡΠ΅ ΠΎΠ±ΡΠ°Π±ΠΎΡΠΊΠΈ, Π° Π΄ΠΎΠΏΠΎΠ»Π½ΠΈΡΠ΅Π»ΡΠ½ΡΠ΅ ΠΏΡΠ΅ΠΈΠΌΡΡΠ΅ΡΡΠ²Π° Π·Π°ΠΊΠ»ΡΡΠ°ΡΡΡΡ Π² ΡΠΎΠΊΡΠ°ΡΠ΅Π½ΠΈΠΈ Π²ΡΠ΅ΠΌΠ΅Π½ΠΈ Π²ΡΠΏΠΎΠ»Π½Π΅Π½ΠΈΡ Π·Π°ΠΊΠ°Π·Π° ΠΈ ΡΠΌΠ΅Π½ΡΡΠ΅Π½ΠΈΠΈ ΠΈΠ·Π½ΠΎΡΠ° ΠΎΠ±ΠΎΡΡΠ΄ΠΎΠ²Π°Π½ΠΈΡ. ΠΡΠ°ΠΊΡΠΈΡΠ΅ΡΠΊΠΈ Π²ΡΠ΅ ΠΏΠΎΠΊΠΎΠ²ΠΊΠΈ Π² ΠΎΡΠΊΡΡΡΡΡ ΡΡΠ°ΠΌΠΏΠ°Ρ ΠΈΠ·Π³ΠΎΡΠ°Π²Π»ΠΈΠ²Π°ΡΡΡΡ ΠΏΠΎ ΠΈΠ½Π΄ΠΈΠ²ΠΈΠ΄ΡΠ°Π»ΡΠ½ΠΎΠΌΡ Π·Π°ΠΊΠ°Π·Ρ, ΡΡΠΎ Π΄Π°Π΅Ρ Π²ΠΎΠ·ΠΌΠΎΠΆΠ½ΠΎΡΡΡ ΠΏΡΠΈΠΎΠ±ΡΠ΅ΡΡΠΈ ΠΎΠ΄Π½Ρ, Π΄ΡΠΆΠΈΠ½Ρ ΠΈΠ»ΠΈ ΡΠΎΡΠ½ΠΈ Π΄Π΅ΡΠ°Π»Π΅ΠΉ ΠΏΠΎ ΠΌΠ΅ΡΠ΅ Π½Π΅ΠΎΠ±Ρ ΠΎΠ΄ΠΈΠΌΠΎΡΡΠΈ. ΠΡΠΎΠΌΠ΅ ΡΠΎΠ³ΠΎ, ΠΈΡΠΊΠ»ΡΡΠ°ΡΡΡΡ Π²ΡΡΠΎΠΊΠΈΠ΅ Π·Π°ΡΡΠ°ΡΡ ΠΈ Π΄Π»ΠΈΡΠ΅Π»ΡΠ½ΠΎΠ΅ Π²ΡΠ΅ΠΌΡ Π²ΡΠΏΠΎΠ»Π½Π΅Π½ΠΈΡ Π·Π°ΠΊΠ°Π·Π°, ΡΠ²ΡΠ·Π°Π½Π½ΡΠ΅ Ρ Π»ΠΈΡΠ΅ΠΉΠ½ΡΠΌΠΈ ΡΠΎΡΠΌΠ°ΠΌΠΈ ΠΈΠ»ΠΈ ΠΎΡΠ½Π°ΡΡΠΊΠΎΠΉ Ρ Π·Π°ΠΊΡΡΡΠΎΠΉ ΠΌΠ°ΡΡΠΈΡΠ΅ΠΉ ΠΈ Π½Π°ΡΡΡΠΎΠΉΠΊΠ°ΠΌΠΈ.
ΠΡΠΎΠΌΠ΅ ΡΠΎΠ³ΠΎ, ΠΎΠ±Π΅ΡΠΏΠ΅ΡΠΈΠ²Π°Ρ ΠΈΠ·Π³ΠΎΡΠΎΠ²Π»Π΅Π½ΠΈΠ΅ Π΄Π΅ΡΠ°Π»Π΅ΠΉ Π±Π΅Π· ΡΠ²Π°ΡΠ½ΡΡ ΡΠ²ΠΎΠ² ΠΈΠ· Π±ΠΎΠ»Π΅Π΅ ΡΠΈΡΡΠΎΠ³ΠΎ ΠΌΠ°ΡΠ΅ΡΠΈΠ°Π»Π° Π²ΡΡΠΎΠΊΠΎΠ³ΠΎ ΠΊΠ°ΡΠ΅ΡΡΠ²Π° Π΄Π»Ρ ΠΏΠΎΠΊΠΎΠ²ΠΊΠΈ ΠΈ ΡΠ»ΡΡΡΠ΅Π½Π½ΠΎΠΉ ΡΡΡΡΠΊΡΡΡΠ½ΠΎΠΉ ΡΠ΅Π»ΠΎΡΡΠ½ΠΎΡΡΠΈ, ΠΊΠΎΠ²ΠΊΠ° ΠΌΠΎΠΆΠ΅Ρ ΠΏΡΠ°ΠΊΡΠΈΡΠ΅ΡΠΊΠΈ ΠΈΡΠΊΠ»ΡΡΠΈΡΡ Π±ΡΠ°ΠΊ (Π² ΠΎΡΠ»ΠΈΡΠΈΠ΅ ΠΎΡ ΠΈΠ·Π³ΠΎΡΠΎΠ²Π»Π΅Π½ΠΈΡ). ΠΡΠΏΠΎΠ»ΡΠ·ΡΡ ΠΏΡΠΎΡΠ΅ΡΡ ΠΊΠΎΠ²ΠΊΠΈ, ΠΎΠ΄Π½Ρ ΠΈ ΡΡ ΠΆΠ΅ Π΄Π΅ΡΠ°Π»Ρ ΠΌΠΎΠΆΠ½ΠΎ ΠΈΠ·Π³ΠΎΡΠ°Π²Π»ΠΈΠ²Π°ΡΡ ΠΈΠ· ΠΈΡΡ ΠΎΠ΄Π½ΡΡ ΡΠ»ΠΈΡΠΊΠΎΠ² ΠΈΠ»ΠΈ Π·Π°Π³ΠΎΡΠΎΠ²ΠΎΠΊ ΡΠ°Π·Π½ΡΡ ΡΠ°Π·ΠΌΠ΅ΡΠΎΠ², ΡΡΠΎ ΠΏΠΎΠ·Π²ΠΎΠ»ΡΠ΅Ρ ΠΏΠΎΠ»ΡΡΠΈΡΡ Π±ΠΎΠ»Π΅Π΅ ΡΠΈΡΠΎΠΊΠΈΠΉ ΡΠΏΠ΅ΠΊΡΡ ΠΈΠ½Π²Π΅Π½ΡΠ°ΡΠ½ΡΡ ΡΠΎΡΡΠΎΠ². Π’Π°ΠΊΠ°Ρ Π³ΠΈΠ±ΠΊΠΎΡΡΡ ΠΎΠ·Π½Π°ΡΠ°Π΅Ρ, ΡΡΠΎ ΠΊΠΎΠ²Π°Π½ΡΠ΅ Π΄Π΅ΡΠ°Π»ΠΈ ΠΏΡΠ°ΠΊΡΠΈΡΠ΅ΡΠΊΠΈ Π»ΡΠ±ΠΎΠΉ ΠΌΠ°ΡΠΊΠΈ ΠΈ Π³Π΅ΠΎΠΌΠ΅ΡΡΠΈΠΈ ΠΌΠΎΠΆΠ½ΠΎ ΠΈΠ·Π³ΠΎΡΠ°Π²Π»ΠΈΠ²Π°ΡΡ ΠΎΡΠ½ΠΎΡΠΈΡΠ΅Π»ΡΠ½ΠΎ Π±ΡΡΡΡΠΎ ΠΈ ΡΠΊΠΎΠ½ΠΎΠΌΠΈΡΠ½ΠΎ.
ΠΠΎΡΡΠΈΠΆΠ΅Π½ΠΈΡ Π² ΠΎΠ±Π»Π°ΡΡΠΈ ΠΎΡΠΊΡΡΡΠΎΠΉ ΡΡΠ°ΠΌΠΏΠΎΠ²ΠΊΠΈ
ΠΠΎΡΡΠ°Π²ΡΠΈΠΊΠΈ ΠΏΠΎΠΊΠΎΠ²ΠΎΠΊ ΡΠΆΠ΅ Π΄Π°Π²Π½ΠΎ ΠΈΡΠΏΠΎΠ»ΡΠ·ΡΡΡ ΠΈΠ½ΡΡΡΡΠΌΠ΅Π½ΡΡ Π΄Π»Ρ ΠΏΠΎΠ»ΡΡΠ΅Π½ΠΈΡ ΠΏΠΎΡΡΠΈ ΡΠΈΡΡΡΡ ΠΈΠ»ΠΈ ΡΠΈΡΡΠΎΠ²ΡΡ ΡΠ°Π·ΠΌΠ΅ΡΠΎΠ² ΠΈ ΡΠΎΡΠΌΡ. Π ΠΊΠ°ΠΆΠ΄ΠΎΠΌ ΠΏΡΠΎΡΠ΅ΡΡΠ΅ ΠΊΠΎΠ²ΠΊΠΈ ΠΈΡΠΏΠΎΠ»ΡΠ·ΡΠ΅ΡΡΡ ΠΊΡΠ·Π½Π΅ΡΠ½ΡΠΉ ΠΈΠ½ΡΡΡΡΠΌΠ΅Π½Ρ ΠΏΠΎ-ΡΠ°Π·Π½ΠΎΠΌΡ, ΡΡΠΎΠ±Ρ ΠΌΠ°ΠΊΡΠΈΠΌΠ°Π»ΡΠ½ΠΎ ΡΠΎΠΊΡΠ°ΡΠΈΡΡ ΠΈΡΡ ΠΎΠ΄Π½ΡΠΉ ΠΌΠ°ΡΠ΅ΡΠΈΠ°Π» ΠΈ Π²ΡΠ΅ΠΌΡ ΠΏΡΠΎΡΠ΅ΡΡΠ° ΠΎΠ±ΡΠ°Π±ΠΎΡΠΊΠΈ. ΠΠ°ΠΏΡΠΈΠΌΠ΅Ρ, ΠΈΠ½ΡΡΡΡΠΌΠ΅Π½ΡΠ°Π»ΡΠ½Π°Ρ ΠΎΡΠ½Π°ΡΡΠΊΠ° ΡΠ²Π»ΡΠ΅ΡΡΡ ΠΊΡΠ°Π΅ΡΠ³ΠΎΠ»ΡΠ½ΡΠΌ ΠΊΠ°ΠΌΠ½Π΅ΠΌ Π΄Π»Ρ ΡΡΠ°ΠΌΠΏΠΎΠ²ΠΊΠΈ ΠΏΠΎΠΊΠΎΠ²ΠΎΠΊ. ΠΡΠΎ ΠΏΡΠΈΠ»ΠΎΠΆΠ΅Π½ΠΈΠ΅ ΠΈΠ΄Π΅Π°Π»ΡΠ½ΠΎ ΠΏΠΎΠ΄Ρ ΠΎΠ΄ΠΈΡ Π΄Π»Ρ ΠΏΠΎΠ²ΡΠΎΡΡΡΡΠΈΡ ΡΡ ΠΏΡΠΎΠ΄ΡΠΊΡΠΎΠ² Π±ΠΎΠ»ΡΡΠΎΠ³ΠΎ ΠΎΠ±ΡΠ΅ΠΌΠ°. ΠΠΎΡΡΠΈΠ³Π½ΡΡΡΠ΅ Π΄ΠΎΠΏΡΡΠΊΠΈ ΠΏΡΠ΅Π΄ΠΏΠΎΠ»Π°Π³Π°ΡΡ ΠΌΠ΅Π½ΡΡΡΡ ΠΎΠ±ΡΠ°Π±ΠΎΡΠΊΡ, Π½Π΅ΠΎΠ±Ρ ΠΎΠ΄ΠΈΠΌΡΡ Π΄Π»Ρ ΠΏΠΎΠ»ΡΡΠ΅Π½ΠΈΡ Π³ΠΎΡΠΎΠ²ΡΡ ΡΠΎΡΠΌ ΠΈΠ»ΠΈ ΡΠ°Π·ΠΌΠ΅ΡΠΎΠ².
ΠΠ΄Π½Π°ΠΊΠΎ Π·Π° ΠΏΠΎΡΠ»Π΅Π΄Π½ΠΈΠ΅ Π³ΠΎΠ΄Ρ ΠΈΠ½ΡΡΡΡΠΌΠ΅Π½ΡΠ°Π»ΡΠ½Π°Ρ ΠΎΡΠ½Π°ΡΡΠΊΠ° ΠΏΠΎΠ·Π²ΠΎΠ»ΠΈΠ»Π° ΠΏΡΠΎΡΠ΅ΡΡΡ ΠΎΡΠΊΡΡΡΠΎΠΉ ΡΡΠ°ΠΌΠΏΠΎΠ²ΠΊΠΈ ΡΡΠ°ΡΡ ΠΊΠΎΠ½ΠΊΡΡΠ΅Π½ΡΠΎΡΠΏΠΎΡΠΎΠ±Π½ΡΠΌ ΠΏΠΎ ΡΡΠΎΠΈΠΌΠΎΡΡΠΈ ΠΏΠΎ ΡΡΠ°Π²Π½Π΅Π½ΠΈΡ Ρ Π΄ΡΡΠ³ΠΈΠΌΠΈ Π°Π»ΡΡΠ΅ΡΠ½Π°ΡΠΈΠ²Π°ΠΌΠΈ ΠΌΠ΅ΡΠ°Π»Π»ΠΎΠΎΠ±ΡΠ°Π±ΠΎΡΠΊΠΈ. Π₯ΠΎΡΡ ΠΏΡΠΎΡΠ΅ΡΡ ΠΎΡΠΊΡΡΡΠΎΠΉ ΡΡΠ°ΠΌΠΏΠΎΠ²ΠΊΠΈ ΡΠ°ΡΡΠΎ Π°ΡΡΠΎΡΠΈΠΈΡΡΠ΅ΡΡΡ Ρ Π±ΠΎΠ»Π΅Π΅ ΠΊΡΡΠΏΠ½ΡΠΌΠΈ Π΄Π΅ΡΠ°Π»ΡΠΌΠΈ ΠΏΡΠΎΡΡΠΎΠΉ ΡΠΎΡΠΌΡ, ΡΠ°ΠΊΠΈΠΌΠΈ ΠΊΠ°ΠΊ ΡΡΠ΅ΡΠΆΠ½ΠΈ, Π·Π°Π³ΠΎΡΠΎΠ²ΠΊΠΈ, ΠΊΠΎΠ»ΡΡΠ°, Π²ΡΠ΅ΠΌΠΊΠΈ ΠΈΠ»ΠΈ ΡΠΏΠΈΠ½Π΄Π΅Π»ΠΈ, Π΅Π³ΠΎ ΠΌΠΎΠΆΠ½ΠΎ ΡΡΠΈΡΠ°ΡΡ ΠΎΠΏΡΠΈΠΌΠ°Π»ΡΠ½ΡΠΌ Π²Π°ΡΠΈΠ°Π½ΡΠΎΠΌ Π΄Π»Ρ ΠΌΠ΅ΡΠ°Π»Π»ΠΈΡΠ΅ΡΠΊΠΈΡ ΠΊΠΎΠΌΠΏΠΎΠ½Π΅Π½ΡΠΎΠ², ΠΈΠ·Π³ΠΎΡΠΎΠ²Π»Π΅Π½Π½ΡΡ ΠΏΠΎ ΠΈΠ½Π΄ΠΈΠ²ΠΈΠ΄ΡΠ°Π»ΡΠ½ΠΎΠΌΡ Π·Π°ΠΊΠ°Π·Ρ. Π‘Π΅Π³ΠΎΠ΄Π½Ρ Π²ΡΡΠΎΠΊΠΎΠΏΡΠΎΡΠ½ΡΠ΅ ΠΈ Π΄ΠΎΠ»Π³ΠΎΠ²Π΅ΡΠ½ΡΠ΅ Π΄Π΅ΡΠ°Π»ΠΈ, ΠΎΠΏΡΠΈΠΌΠΈΠ·ΠΈΡΠΎΠ²Π°Π½Π½ΡΠ΅ Ρ ΡΠΎΡΠΊΠΈ Π·ΡΠ΅Π½ΠΈΡ ΠΊΠ°ΠΊ ΠΌΠ΅Ρ Π°Π½ΠΈΡΠ΅ΡΠΊΠΈΡ ΡΠ²ΠΎΠΉΡΡΠ², ΡΠ°ΠΊ ΠΈ ΡΡΡΡΠΊΡΡΡΠ½ΠΎΠΉ ΡΠ΅Π»ΠΎΡΡΠ½ΠΎΡΡΠΈ, ΠΏΡΠΎΠΈΠ·Π²ΠΎΠ΄ΡΡΡΡ Π² ΡΠ°Π·ΠΌΠ΅ΡΠ°Ρ ΠΎΡ Π½Π΅ΡΠΊΠΎΠ»ΡΠΊΠΈΡ ΡΡΠ½ΡΠΎΠ² Π΄ΠΎ ΡΠΎΡΠ΅Π½ ΡΠΎΠ½Π½.
ΠΠ½ΠΎΠ³ΠΈΠ΅ ΠΏΡΠΎΠΈΠ·Π²ΠΎΠ΄ΠΈΡΠ΅Π»ΠΈ ΠΎΡΠΊΡΡΡΡΡ ΡΡΠ°ΠΌΠΏΠΎΠ² ΠΈΠΌΠ΅ΡΡ Π² Π½Π°Π»ΠΈΡΠΈΠΈ ΡΠΈΡΠΎΠΊΠΈΠΉ ΡΠΏΠ΅ΠΊΡΡ Π½Π΅Π·Π°ΠΊΡΠ΅ΠΏΠ»Π΅Π½Π½ΡΡ ΠΈΠ½ΡΡΡΡΠΌΠ΅Π½ΡΠΎΠ², ΠΊΠΎΡΠΎΡΡΠ΅ ΠΌΠΎΠΆΠ½ΠΎ ΠΈΡΠΏΠΎΠ»ΡΠ·ΠΎΠ²Π°ΡΡ Π΄Π»Ρ ΠΏΠΎΠ»ΡΡΠ΅Π½ΠΈΡ ΡΠ°Π·Π»ΠΈΡΠ½ΡΡ ΡΠΎΡΠΌ Π±Π»ΠΈΠΆΠ΅ ΠΊ ΡΠΈΡΡΠΎΠ²ΠΎΠΉ ΠΎΠ±ΡΠ°Π±ΠΎΡΠΊΠ΅, ΡΠ΅ΠΌ ΡΡΠΎ Π±ΡΠ»ΠΎ Π±Ρ Π²ΠΎΠ·ΠΌΠΎΠΆΠ½ΠΎ Ρ ΠΏΠΎΠΌΠΎΡΡΡ ΡΠΈΡΡΠΎ ΠΎΡΠΊΡΡΡΠΎΠ³ΠΎ ΠΏΡΠΎΡΠ΅ΡΡΠ° ΡΡΠ°ΠΌΠΏΠΎΠ²ΠΊΠΈ. Π‘ΠΎΠ²ΡΠ΅ΠΌΠ΅Π½Π½ΡΠ΅ ΠΊΡΠ·Π½Π΅ΡΠ½ΡΠ΅ ΡΠ΅Ρ Π° ΡΠ΅ΠΏΠ΅ΡΡ ΠΏΡΠ΅Π΄Π»Π°Π³Π°ΡΡ ΡΠΎΡΠΌΡ, ΠΊΠΎΡΠΎΡΡΠ΅ ΡΠ°Π½ΡΡΠ΅ Π½ΠΈΠΊΠΎΠ³Π΄Π° Π½Π΅ ΡΡΠΈΡΠ°Π»ΠΈΡΡ ΠΏΡΠΈΠ³ΠΎΠ΄Π½ΡΠΌΠΈ Π΄Π»Ρ ΠΈΠ·Π³ΠΎΡΠΎΠ²Π»Π΅Π½ΠΈΡ ΠΌΠ΅ΡΠΎΠ΄ΠΎΠΌ ΠΎΡΠΊΡΡΡΠΎΠΉ ΡΡΠ°ΠΌΠΏΠΎΠ²ΠΊΠΈ. ΠΡΠΎ ΠΏΡΠ΅Π΄Π»ΠΎΠΆΠ΅Π½ΠΈΠ΅ ΠΈΠ΄Π΅Π°Π»ΡΠ½ΠΎ ΠΏΠΎΠ΄Ρ ΠΎΠ΄ΠΈΡ Π΄Π»Ρ ΠΏΡΠΎΡΠΎΡΠΈΠΏΠΎΠ² ΠΈΠ»ΠΈ ΠΌΠ΅Π»ΠΊΠΎΡΠ΅ΡΠΈΠΉΠ½ΠΎΠ³ΠΎ ΠΏΡΠΎΠΈΠ·Π²ΠΎΠ΄ΡΡΠ²Π°, ΠΊΠΎΠ³Π΄Π° ΡΡΠΎΠΈΠΌΠΎΡΡΡ Π±Π»ΠΎΠΊΠ° ΡΡΠ°ΠΌΠΏΠ° Π΄Π»Ρ ΡΡΠ°ΠΌΠΏΠ° Π΄Π»Ρ ΡΠ»Π΅ΠΏΠΊΠ° Π½Π΅ ΠΎΠ±Π΅ΡΠΏΠ΅ΡΠΈΠ²Π°Π΅Ρ ΡΠΊΠΎΠ½ΠΎΠΌΠΈΡΠ΅ΡΠΊΠΎΠ³ΠΎ ΠΎΠ±ΠΎΡΠ½ΠΎΠ²Π°Π½ΠΈΡ. ΠΠ΅ΠΏΠΎΡΡΠ΅Π΄ΡΡΠ²Π΅Π½Π½Π°Ρ Π΄ΠΎΡΡΡΠΏΠ½ΠΎΡΡΡ ΡΡΠΎΠ³ΠΎ ΠΈΠ½ΡΡΡΡΠΌΠ΅Π½ΡΠ° ΡΠ°ΠΊΠΆΠ΅ ΠΏΠΎΠ·Π²ΠΎΠ»ΡΠ΅Ρ ΡΠΎΠΊΡΠ°ΡΠΈΡΡ Π²ΡΠ΅ΠΌΡ ΠΏΡΠΎΠΈΠ·Π²ΠΎΠ΄ΡΡΠ²Π΅Π½Π½ΠΎΠ³ΠΎ ΡΠΈΠΊΠ»Π°, ΠΏΡΠ΅Π΄Π»Π°Π³Π°Ρ Π³ΠΈΠ±ΠΊΠΈΠ΅ ΠΎΠ±ΡΠ΅ΠΌΡ Π·Π°ΠΊΠ°Π·Π° ΠΈ ΡΠΎΠΊΡΠ°ΡΠ΅Π½Π½ΠΎΠ΅ Π²ΡΠ΅ΠΌΡ Π²ΡΠΏΠΎΠ»Π½Π΅Π½ΠΈΡ Π·Π°ΠΊΠ°Π·Π° Π² ΡΠ΅Ρ ΡΠ»ΡΡΠ°ΡΡ , ΠΊΠΎΠ³Π΄Π° ΡΡΠΎ Π½Π΅ΠΎΠ±Ρ ΠΎΠ΄ΠΈΠΌΠΎ.
ΠΠΎΠ²Π°Π½ΡΠ΅ ΠΠΠ | GKN Sinter Metals
Π ΠΏΡΠΎΡΠ΅ΡΡΠ΅ FPM ΠΈΡΠΏΠΎΠ»ΡΠ·ΡΡΡΡΡ ΡΠΆΠΈΠΌΠ°ΡΡΠΈΠ΅ ΡΠΈΠ»Ρ, ΡΠΏΠΎΡΠΎΠ±ΡΡΠ²ΡΡΡΠΈΠ΅ Π²ΡΡΠΎΠΊΠΎΠΉ Π΄Π΅ΡΠΎΡΠΌΠ°ΡΠΈΠΈ ΠΈ Π±ΠΎΠΊΠΎΠ²ΠΎΠΌΡ ΠΏΠΎΡΠΎΠΊΡ ΠΌΠ°ΡΠ΅ΡΠΈΠ°Π»Π° Π΄Π»Ρ ΠΏΠΎΠ»ΡΡΠ΅Π½ΠΈΡ ΠΆΠ΅Π»Π°Π΅ΠΌΠΎΠΉ Π³Π΅ΠΎΠΌΠ΅ΡΡΠΈΠΈ ΠΈ ΡΠ²ΠΎΠΉΡΡΠ² ΠΌΠ°ΡΠ΅ΡΠΈΠ°Π»Π°.
Π ΠΏΡΠΎΡΠ΅ΡΡΠ΅ ΠΊΠΎΠ²ΠΊΠΈ ΠΌΠ°ΡΠ΅ΡΠΈΠ°Π»Ρ ΡΠΏΡΠΎΡΠ½ΡΡΡΡΡ Π·Π° ΡΡΠ΅Ρ ΡΠ»ΡΡΡΠ΅Π½ΠΈΡ Π·Π΅ΡΠ½ΠΈΡΡΠΎΠΉ ΡΡΡΡΠΊΡΡΡΡ, Π° Π²ΡΡΠΎΠΊΠΈΠΉ ΡΡΠΎΠ²Π΅Π½Ρ Π΄Π΅ΡΠΎΡΠΌΠ°ΡΠΈΠΈ ΠΎΠ±Π΅ΡΠΏΠ΅ΡΠΈΠ²Π°Π΅Ρ Π·Π½Π°ΡΠΈΡΠ΅Π»ΡΠ½ΡΠΉ ΡΠ΄Π²ΠΈΠ³ Π΄Π»Ρ ΠΏΠΎΠ»ΡΡΠ΅Π½ΠΈΡ ΠΏΡΠΎΡΠ½ΠΎΠΉ ΠΌΠΈΠΊΡΠΎΡΡΡΡΠΊΡΡΡΡ.Π ΡΠ΅Π·ΡΠ»ΡΡΠ°ΡΠ΅ ΠΏΠΎΠ»ΡΡΠ°Π΅ΡΡΡ ΠΌΠ΅Π»ΠΊΠΈΠΉ ΡΠ°Π·ΠΌΠ΅Ρ Π·Π΅ΡΠ½Π°, ΠΎΠ΄Π½ΠΎΡΠΎΠ΄Π½ΠΎΠ΅ Ρ ΠΈΠΌΠΈΡΠ΅ΡΠΊΠΎΠ΅ ΡΠ°ΡΠΏΡΠ΅Π΄Π΅Π»Π΅Π½ΠΈΠ΅ Π±Π΅Π· ΡΠ΅Π³ΡΠ΅Π³Π°ΡΠΈΠΈ Π΄Π΅ΡΠΎΡΠΌΠΈΡΡΠ΅ΠΌΠΎΠ³ΠΎ ΡΠΏΠ»Π°Π²Π° ΠΈ ΠΎΠ΄Π½ΠΎΡΠΎΠ΄Π½Π°Ρ ΡΠ΅Π°ΠΊΡΠΈΡ Π½Π° ΡΠ΅ΡΠΌΠΎΠΎΠ±ΡΠ°Π±ΠΎΡΠΊΡ.
ΠΠΎΠΌΠΏΠΎΠ½Π΅Π½ΡΡFPM ΠΏΡΠΎΠΈΠ·Π²ΠΎΠ΄ΡΡΡΡ ΠΈΠ· ΡΡΠ΄Π° ΡΠΏΠ»Π°Π²ΠΎΠ², Π²ΠΊΠ»ΡΡΠ°Ρ ΡΠΊΠ²ΠΈΠ²Π°Π»Π΅Π½ΡΡ ΠΏΡΠΎΡΡΠΎΠΉ ΡΠ³Π»Π΅ΡΠΎΠ΄ΠΈΡΡΠΎΠΉ ΡΡΠ°Π»ΠΈ, Π½ΠΈΠ·ΠΊΠΎΠ»Π΅Π³ΠΈΡΠΎΠ²Π°Π½Π½ΠΎΠΉ ΡΡΠ°Π»ΠΈ ΠΈ ΡΠΏΠ»Π°Π²ΠΎΠ², ΠΊΠΎΡΠΎΡΡΠ΅ ΠΌΠΎΠΆΠ½ΠΎ ΠΏΠΎΠ΄Π²Π΅ΡΠ³Π°ΡΡ ΡΠ΅ΡΠΌΠΎΠΎΠ±ΡΠ°Π±ΠΎΡΠΊΠ΅ Π΄ΠΎ ΡΠ²Π΅ΡΠ΄ΠΎΡΡΠΈ C 60 ΠΏΠΎ Π ΠΎΠΊΠ²Π΅Π»Π»Ρ.
FPM ΠΎΡΠ»ΠΈΡΠ°Π΅ΡΡΡ ΠΎΡ ΡΡΠ°Π΄ΠΈΡΠΈΠΎΠ½Π½ΡΡ ΠΏΡΠΎΡΠ΅ΡΡΠΎΠ² ΡΠ΅ΠΌ, ΡΡΠΎ ΠΌΠΎΠΆΠ½ΠΎ ΠΈΠ·Π³ΠΎΡΠ°Π²Π»ΠΈΠ²Π°ΡΡ ΠΈΠ·Π΄Π΅Π»ΠΈΡ ΡΠ»ΠΎΠΆΠ½ΠΎΠΉ ΠΈ Π½Π΅ΡΡΠ°Π½Π΄Π°ΡΡΠ½ΠΎΠΉ Π³Π΅ΠΎΠΌΠ΅ΡΡΠΈΡΠ΅ΡΠΊΠΎΠΉ ΡΠΎΡΠΌΡ.
Π’ΡΠ°ΡΠ΅Π»ΡΠ½ΠΎ ΡΠΏΡΠΎΠ΅ΠΊΡΠΈΡΠΎΠ²Π°Π½Π½ΡΠ΅ ΠΏΡΠ΅ΡΠΎΡΠΌΡ, ΡΠΎΡΠ΅ΡΠ°Π½ΠΈΠ΅ ΡΠΎΡΠ½ΠΎΠ³ΠΎ ΡΠ°ΡΠΏΡΠ΅Π΄Π΅Π»Π΅Π½ΠΈΡ ΠΌΠ°ΡΠ΅ΡΠΈΠ°Π»Π° ΠΈ Π²ΡΡΠΎΠΊΠΎΠΉ ΡΠΎΡΠΌΡΠ΅ΠΌΠΎΡΡΠΈ ΠΌΠ°ΡΠ΅ΡΠΈΠ°Π»Π°, ΠΏΠΎΠ·Π²ΠΎΠ»ΡΡΡ ΠΊΠΎΠ²ΠΊΡ ΠΈΠ·Π΄Π΅Π»ΠΈΠΉ ΡΠ»ΠΎΠΆΠ½ΠΎΠΉ ΠΈ Π½Π΅ΡΡΠ°Π½Π΄Π°ΡΡΠ½ΠΎΠΉ ΡΠΎΡΠΌΡ.
ΠΡΠΈ ΠΈΠ½ΡΠ΅Π»Π»Π΅ΠΊΡΡΠ°Π»ΡΠ½ΡΠ΅ ΠΏΡΠ΅ΡΠΎΡΠΌΡ ΠΏΠΎΠ·Π²ΠΎΠ»ΡΡΡ ΠΈΠ·Π³ΠΎΡΠ°Π²Π»ΠΈΠ²Π°ΡΡ ΠΊΠΎΠΌΠΏΠΎΠ½Π΅Π½ΡΡ Π·Π° ΠΎΠ΄ΠΈΠ½ Ρ ΠΎΠ΄ ΠΊΠΎΠ²ΠΎΡΠ½ΠΎΠ³ΠΎ ΠΏΡΠ΅ΡΡΠ°, Π° Π½Π΅ Π·Π° ΡΡΠΈ Ρ ΠΎΠ΄Π° ΡΡΠ°ΠΌΠΏΠΎΠ²ΠΊΠΈ — Ρ ΠΌΠΈΠ½ΠΈΠΌΠ°Π»ΡΠ½ΡΠΌ ΠΊΠΎΠ»ΠΈΡΠ΅ΡΡΠ²ΠΎΠΌ Π·Π°ΡΡΠ΅Π½ΡΠ΅Π² ΠΈ ΠΎΡΡ ΠΎΠ΄ΠΎΠ².
ΠΠΎΡΡΡΠΈΡΠΈΠ΅Π½Ρ ΠΈΡΠΏΠΎΠ»ΡΠ·ΠΎΠ²Π°Π½ΠΈΡ ΠΌΠ°ΡΠ΅ΡΠΈΠ°Π»Π° Π½Π° 20-50% Π²ΡΡΠ΅, ΡΠ΅ΠΌ ΠΏΡΠΈ ΡΡΠ°Π΄ΠΈΡΠΈΠΎΠ½Π½ΠΎΠΉ ΠΏΠΎΠΊΠΎΠ²ΠΊΠ΅ ΠΏΡΡΡΠΊΠΎΠ², Π½Π°ΡΡΠ΄Ρ Ρ Π»ΡΡΡΠΈΠΌ Π·Π°ΠΏΠΎΠ»Π½Π΅Π½ΠΈΠ΅ΠΌ ΡΡΠ°ΠΌΠΏΠ° ΠΈ Π±ΠΎΠ»ΡΡΠ΅ΠΉ ΡΠ»ΠΎΠΆΠ½ΠΎΡΡΡΡ Π΄Π΅ΡΠ°Π»Π΅ΠΉ ΠΏΠΎΡΠ»Π΅ ΠΏΠΎΠΊΠΎΠ²ΠΊΠΈ.
ΠΡΠΎΠ΄ΡΠΊΡΡFPM ΠΏΠΎΠ·Π²ΠΎΠ»ΡΡΡ ΠΈΡΠΏΠΎΠ»ΡΠ·ΠΎΠ²Π°ΡΡ ΡΠ½ΠΈΠΊΠ°Π»ΡΠ½ΡΠ΅ ΠΊΠΎΠ½ΡΡΡΡΠΊΡΠΈΠΈ ΠΈ ΡΠΏΠ»Π°Π²Ρ, ΠΏΡΠ΅Π²ΠΎΡΡ ΠΎΠ΄ΡΡΠΈΠ΅ ΠΏΠΎ Ρ Π°ΡΠ°ΠΊΡΠ΅ΡΠΈΡΡΠΈΠΊΠ°ΠΌ ΡΠ°ΠΌΡΠ΅ Π»Π΅Π³ΠΈΡΠΎΠ²Π°Π½Π½ΡΠ΅ ΡΡΠ°Π»ΠΈ.
ΠΠ°ΡΠ΅ΡΠΈΠ°Π»ΡFPM ΠΏΡΠ΅Π²ΠΎΡΡ ΠΎΠ΄ΡΡ ΠΎΠ±ΡΡΠ½ΡΠ΅ Π΄Π΅ΡΠΎΡΠΌΠΈΡΡΠ΅ΠΌΡΠ΅ ΡΡΠ°Π»ΠΈ 16/20MnCr5 ΠΏΠΎ Π΄ΠΎΠ»Π³ΠΎΠ²Π΅ΡΠ½ΠΎΡΡΠΈ Π½Π° 30%.ΠΠΎΠ·ΠΌΠΎΠΆΠ½ΠΎΡΡΠΈ Π΄Π°ΠΆΠ΅ Π²ΡΡΠΎΠΊΠΎΠ»Π΅Π³ΠΈΡΠΎΠ²Π°Π½Π½ΠΎΠ³ΠΎ Π΄Π΅ΡΠΎΡΠΌΠΈΡΡΠ΅ΠΌΠΎΠ³ΠΎ 18CrNiMo7-6 Π·Π½Π°ΡΠΈΡΠ΅Π»ΡΠ½ΠΎ Π½ΠΈΠΆΠ΅ Π²ΠΎΠ·ΠΌΠΎΠΆΠ½ΠΎΡΡΠ΅ΠΉ ΠΌΠ°ΡΠ΅ΡΠΈΠ°Π»Π° FPM.
ΠΡΠ° Π΄ΠΎΠ»Π³ΠΎΠ²Π΅ΡΠ½ΠΎΡΡΡ ΡΠΏΠΎΡΠΎΠ±ΡΡΠ²ΡΠ΅Ρ ΡΠΌΠ΅Π½ΡΡΠ΅Π½ΠΈΡ ΠΌΠ°ΡΡΡ ΠΈ ΡΠ²Π΅Π»ΠΈΡΠ΅Π½ΠΈΡ ΡΡΠ΅Π±ΠΎΠ²Π°Π½ΠΈΠΉ ΠΊ ΠΊΡΡΡΡΡΠ΅ΠΌΡ ΠΌΠΎΠΌΠ΅Π½ΡΡ Π±Π»Π°Π³ΠΎΠ΄Π°ΡΡ ΠΏΡΠΎΠ²Π΅ΡΠ΅Π½Π½ΠΎΠΉ ΠΈΡΡΠΎΡΠΈΠΈ ΠΈΡΠΏΠΎΠ»ΡΠ·ΠΎΠ²Π°Π½ΠΈΡ ΠΏΡΠΎΠ²Π΅ΡΠ΅Π½Π½ΡΡ ΠΏΡΠΎΠ΄ΡΠΊΡΠΎΠ² ΠΈ ΡΠ°ΡΡΡΡΠ΅ΠΌΡ ΡΠΈΡΠ»Ρ ΡΠ΅ΡΠΈΠΉΠ½ΡΡ ΠΏΡΠΈΠΌΠ΅Π½Π΅Π½ΠΈΠΉ.
ΠΠΏΠ΅ΡΠ²ΡΠ΅ Π² Π°Π²ΡΠΎΠΌΠΎΠ±ΠΈΠ»Π΅ΡΡΡΠΎΠ΅Π½ΠΈΠΈ ΠΈ ΠΏΡΠΎΠΈΠ·Π²ΠΎΠ΄ΡΡΠ²Π΅ PM: ΠΊΠΎΠΌΠΏΠ»Π΅ΠΊΡ Π΄ΠΈΡΡΠ΅ΡΠ΅Π½ΡΠΈΠ°Π»ΡΠ½ΠΎΠΉ ΡΠ΅ΡΡΠ΅ΡΠ½ΠΈ FPM, ΠΈΡΠΏΠΎΠ»ΡΠ·ΡΠ΅ΠΌΡΠΉ Π² Π·Π°Π΄Π½Π΅ΠΌ Π΄ΠΈΡΡΠ΅ΡΠ΅Π½ΡΠΈΠ°Π»Π΅ Ρ ΡΠ»Π΅ΠΊΡΡΠΎΠ½Π½ΠΎΠΉ Π±Π»ΠΎΠΊΠΈΡΠΎΠ²ΠΊΠΎΠΉ.
FPM ΠΏΠΎΠΊΠ°Π·Π°Π» Π±ΠΎΠ»Π΅Π΅ Π²ΡΡΠΎΠΊΠΈΠ΅ Ρ Π°ΡΠ°ΠΊΡΠ΅ΡΠΈΡΡΠΈΠΊΠΈ ΠΏΠΎ ΡΡΠ°Π²Π½Π΅Π½ΠΈΡ Ρ ΠΊΠΎΠ½ΠΊΡΡΠΈΡΡΡΡΠΈΠΌΠΈ ΡΠ΅Ρ Π½ΠΎΠ»ΠΎΠ³ΠΈΡΠΌΠΈ ΠΏΠΎ ΡΡΡΠ°Π»ΠΎΡΡΠ½ΡΠΌ Ρ Π°ΡΠ°ΠΊΡΠ΅ΡΠΈΡΡΠΈΠΊΠ°ΠΌ Π·ΡΠ±ΡΠ°ΡΠΎΠΉ ββΠΏΠ΅ΡΠ΅Π΄Π°ΡΠΈ, ΡΠ΄Π°ΡΠΎΠΏΡΠΎΡΠ½ΠΎΡΡΠΈ, Π΄ΠΎΠ»Π³ΠΎΠ²Π΅ΡΠ½ΠΎΡΡΠΈ ΡΠΈΡΡΠ΅ΠΌΡ Π±Π»ΠΎΠΊΠΈΡΠΎΠ²ΠΊΠΈ ΠΈ ΠΊΠΎΡΡΡΠΈΡΠΈΠ΅Π½ΡΡ Π±Π΅Π·ΠΎΠΏΠ°ΡΠ½ΠΎΡΡΠΈ.
Π’ΡΠ΅Π±ΠΎΠ²Π°Π½ΠΈΡ ΠΊ ΠΏΡΠΎΠΈΠ·Π²ΠΎΠ΄ΠΈΡΠ΅Π»ΡΠ½ΠΎΡΡΠΈ Π±ΡΠ»ΠΈ ΠΏΡΠ΅Π²ΡΡΠ΅Π½Ρ ΠΈΠ·-Π·Π° ΠΎΠΏΡΠΈΠΌΠΈΠ·Π°ΡΠΈΠΈ Π³Π΅ΠΎΠΌΠ΅ΡΡΠΈΠΈ, ΠΌΠ΅ΡΠ°Π»Π»ΡΡΠ³ΠΈΠΈ ΠΈ ΠΏΡΠΎΡΠ΅ΡΡΠ° Π΄Π»Ρ ΠΏΡΡΠΈ ΠΊΠΎΠΌΠΏΠΎΠ½Π΅Π½ΡΠΎΠ² Π½Π° Π΄ΠΈΡΡΠ΅ΡΠ΅Π½ΡΠΈΠ°Π»:
- ΠΠΎΠΊΠΎΠ²Π°Ρ ΠΏΠ΅ΡΠ΅Π΄Π°ΡΠ°
- Π¨Π΅ΡΡΠ΅ΡΠ½ΠΈ (2)
- ΠΠ»ΠΎΠΊΠΈΡΠΎΠ²ΠΊΠ° Π±ΠΎΠΊΠΎΠ²ΠΎΠΉ ΡΠ΅ΡΡΠ΅ΡΠ½ΠΈ
- ΠΠ°ΠΏΠΎΡΠ½Π°Ρ ΠΏΠ»Π°Π½ΠΊΠ°
ΠΠΈΡΡΠ΅ΡΠ΅Π½ΡΠΈΠ°Π»ΡΠ½Π°Ρ Π·ΡΠ±ΡΠ°ΡΠ°Ρ ΠΏΠ΅ΡΠ΅Π΄Π°ΡΠ° FPM ΠΊΠΎΠΌΠΏΠ°Π½ΠΈΠΈ GKN ΡΡΡΠ°Π½Π°Π²Π»ΠΈΠ²Π°Π΅Ρ ΡΡΠ°Π»ΠΎΠ½Π½ΡΠ΅ Ρ Π°ΡΠ°ΠΊΡΠ΅ΡΠΈΡΡΠΈΠΊΠΈ Π΄ΠΈΡΡΠ΅ΡΠ΅Π½ΡΠΈΠ°Π»ΡΠ½ΠΎΠΉ Π·ΡΠ±ΡΠ°ΡΠΎΠΉ ββΠΏΠ΅ΡΠ΅Π΄Π°ΡΠΈ: ΡΠ²Π΅Π»ΠΈΡΠ΅Π½Π½ΡΠΉ Π΄ΠΎΠΏΡΡΡΠΈΠΌΡΠΉ ΠΊΡΡΡΡΡΠΈΠΉ ΠΌΠΎΠΌΠ΅Π½Ρ, ΡΠΏΠΎΡΠΎΠ±ΡΡΠ²ΡΡΡΠΈΠΉ Π΄ΠΎΡΡΠΈΠΆΠ΅Π½ΠΈΡ ΡΠΎΠΏΠ»ΠΈΠ²Π½ΠΎΠΉ ΡΠΊΠΎΠ½ΠΎΠΌΠΈΡΠ½ΠΎΡΡΠΈ Π² Π±ΡΠ΄ΡΡΠ΅ΠΌ ΠΈ Π²ΠΎΠ·ΠΌΠΎΠΆΠ½ΠΎΡΡΡ ΡΠΌΠ΅Π½ΡΡΠ΅Π½ΠΈΡ Π³Π°Π±Π°ΡΠΈΡΠΎΠ² Π±ΡΠ΄ΡΡΠΈΡ ΡΠΈΡΡΠ΅ΠΌ.
GKN ΠΏΡΠΎΠΈΠ·Π²ΠΎΠ΄ΠΈΡ ΠΊΠΎΠ²Π°Π½ΡΠ΅ ΡΠ°ΡΡΠ½Ρ ΠΈΠ· ΠΏΠΎΡΠΎΡΠΊΠΎΠ²ΠΎΠ³ΠΎ ΠΌΠ΅ΡΠ°Π»Π»Π° Π½Π°ΠΈΠ²ΡΡΡΠ΅ΠΉ ΠΌΠΎΡΠ½ΠΎΡΡΠΈ Π΄Π»Ρ ΠΌΠ°ΡΠΈΠ½ΠΎΡΡΡΠΎΠΈΡΠ΅Π»ΡΠ½ΠΎΠΉ ΠΈ Π°Π²ΡΠΎΠΌΠΎΠ±ΠΈΠ»ΡΠ½ΠΎΠΉ ΠΏΡΠΎΠΌΡΡΠ»Π΅Π½Π½ΠΎΡΡΠΈ.
ΠΡΠΈΠ»ΠΎΠΆΠ΅Π½ΠΈΠ΅ Π²ΡΡΠΎΠΊΠΎΠΏΡΠΎΠΈΠ·Π²ΠΎΠ΄ΠΈΡΠ΅Π»ΡΠ½ΠΎΠ΅, Π½Π°Π΄Π΄ΡΠ²Π½ΠΎΠ΅ 6.ΠΠ²ΠΈΠ³Π°ΡΠ΅Π»Ρ 2L V-8, ΡΠ΅ΡΡΠΈΡΠΈΡΠΈΡΠΎΠ²Π°Π½Π½ΡΠΉ SAE, ΠΌΠΎΡΠ½ΠΎΡΡΡΡ 650 Π»ΠΎΡΠ°Π΄ΠΈΠ½ΡΡ ΡΠΈΠ» ΠΏΡΠΈ 6400 ΠΎΠ±ΠΎΡΠΎΡΠ°Ρ Π² ΠΌΠΈΠ½ΡΡΡ ΠΈ ββ650 ΡΡΠ½Ρ-ΡΡΡ. ΠΊΡΡΡΡΡΠ΅Π³ΠΎ ΠΌΠΎΠΌΠ΅Π½ΡΠ° ΠΏΡΠΈ 3600 ΠΎΠ± / ΠΌΠΈΠ½.
FPM ΠΏΡΠ΅Π΄Π»Π°Π³Π°Π΅Ρ Π²ΡΡΠΎΡΠ°ΠΉΡΡΡ ΠΏΡΠΎΡΠ½ΠΎΡΡΡ ΠΈ Π»Π΅Π³ΠΊΡΡ ΠΊΠΎΠ½ΡΡΡΡΠΊΡΠΈΡ Π΄Π»Ρ ΡΠΌΠ΅Π½ΡΡΠ΅Π½ΠΈΡ Π²ΠΎΠ·Π²ΡΠ°ΡΠ½ΠΎ-ΠΏΠΎΡΡΡΠΏΠ°ΡΠ΅Π»ΡΠ½ΠΎΠΉ ΠΌΠ°ΡΡΡ, Π° ΡΠ°ΠΊΠΆΠ΅ Π±ΠΎΠ»Π΅Π΅ Π±ΡΡΡΡΡΡ Π²ΠΎΠ·ΠΌΠΎΠΆΠ½ΠΎΡΡΡ REV. Π ΠΊΠΎΠ½ΡΡΡΡΠΊΡΠΈΠΈ ΠΈΡΠΏΠΎΠ»ΡΠ·ΠΎΠ²Π°Π½Ρ ΠΏΡΠ΅ΠΈΠΌΡΡΠ΅ΡΡΠ²Π° Π»Π΅Π³ΠΊΠΎΡΡΠΈ Π·Π° ΡΡΠ΅Ρ ΠΌΠ΅Ρ Π°Π½ΠΈΡΠ΅ΡΠΊΠΈ ΠΎΠ±ΡΠ°Π±ΠΎΡΠ°Π½Π½ΡΡ ΠΏΡΠΎΡΠ΅Π·Π΅ΠΉ Π΄Π»Ρ ΠΎΡΠ²Π΅ΡΠ΅Π½ΠΈΡ ΠΈ Π΄ΠΎΠΏΠΎΠ»Π½ΠΈΡΠ΅Π»ΡΠ½ΡΡ ΡΡΠ½ΠΊΡΠΈΠΉ ΠΎΡΠ²Π΅ΡΠ΅Π½ΠΈΡ ΠΏΡΠΈ ΡΠΎΡ ΡΠ°Π½Π΅Π½ΠΈΠΈ Π²ΡΡΠΎΠΊΠΎΠΉ Π³ΡΡΠ·ΠΎΠΏΠΎΠ΄ΡΠ΅ΠΌΠ½ΠΎΡΡΠΈ.
FPM Π·Π°ΠΌΠ΅Π½ΠΈΠ» ΡΠΈΡΠ°Π½ΠΎΠ²ΡΠΉ ΠΌΠ°ΡΠ΅ΡΠΈΠ°Π», ΠΊΠΎΡΠΎΡΡΠΉ Π±ΡΠ» Π΄ΠΎΡΠΎΠ³ΠΈΠΌ, ΠΈΠΌΠ΅Π» ΠΌΠ°Π»ΠΎ ΠΏΠΎΡΡΠ°Π²ΠΎΠΊ ΠΈ ΠΏΡΠ΅Π΄Π»Π°Π³Π°Π» Π΄Π»ΠΈΡΠ΅Π»ΡΠ½ΡΠ΅ ΡΡΠΎΠΊΠΈ Π²ΡΠΏΠΎΠ»Π½Π΅Π½ΠΈΡ Π·Π°ΠΊΠ°Π·Π°.
ΠΡΠ° ΡΠ΅Ρ Π½ΠΎΠ»ΠΎΠ³ΠΈΡ ΡΡΡΠ°Π½Π°Π²Π»ΠΈΠ²Π°Π΅Ρ ΡΡΠ°Π½Π΄Π°ΡΡ ΠΏΡΠΎΠΈΠ·Π²ΠΎΠ΄ΠΈΡΠ΅Π»ΡΠ½ΠΎΡΡΠΈ ΠΏΡΠΈ ΠΏΡΠΎΠΈΠ·Π²ΠΎΠ΄ΡΡΠ²Π΅ ΡΠ°ΡΡΠ½ΠΎΠ² FPM.
ΠΠΎΠ²ΡΠ΅ ΡΠ΅Π½Π΄Π΅Π½ΡΠΈΠΈ Π² ΠΊΡΠ·Π½Π΅ΡΠ½ΡΡ ΡΠ΅Ρ Π½ΠΎΠ»ΠΎΠ³ΠΈΡΡ : ΠΠ°ΡΠ΅ΡΠΈΠ°Π»Ρ ΠΊΠΎΠ½ΡΠ΅ΡΠ΅Π½ΡΠΈΠΈ AIP: Π’ΠΎΠΌ 1353, β 1
ΠΠ³ΡΠ°Π½ΠΈΡΠ΅Π½Π½ΡΠ΅ ΠΏΡΠΈΡΠΎΠ΄Π½ΡΠ΅ ΡΠ΅ΡΡΡΡΡ ΡΠ²Π΅Π»ΠΈΡΠΈΠ²Π°ΡΡ ΡΠΏΡΠΎΡ Π½Π° Π²ΡΡΠΎΠΊΠΎΡΡΡΠ΅ΠΊΡΠΈΠ²Π½ΠΎΠ΅ ΠΎΠ±ΠΎΡΡΠ΄ΠΎΠ²Π°Π½ΠΈΠ΅ ΠΈ ΡΡΠ°Π½ΡΠΏΠΎΡΡΠ½ΡΠ΅ ΡΡΠ΅Π΄ΡΡΠ²Π°. ΠΠΎΠ²ΡΠ΅ ΡΠ½Π΅ΡΠ³ΠΎΡΠ±Π΅ΡΠ΅Π³Π°ΡΡΠΈΠ΅ ΠΊΠΎΠ½ΡΠ΅ΠΏΡΠΈΠΈ ΠΌΠΎΠ±ΠΈΠ»ΡΠ½ΠΎΡΡΠΈ ΡΡΠ΅Π±ΡΡΡ ΠΎΠΏΡΠΈΠΌΠΈΠ·Π°ΡΠΈΠΈ ΠΊΠΎΠ½ΡΡΡΡΠΊΡΠΈΠΈ Π·Π° ΡΡΠ΅Ρ ΡΠΌΠ΅Π½ΡΡΠ΅Π½ΠΈΡ ΡΠ°Π·ΠΌΠ΅ΡΠΎΠ² ΠΊΠΎΠΌΠΏΠΎΠ½Π΅Π½ΡΠΎΠ² ΠΈ Π²ΡΠ±ΠΎΡΠ° ΠΊΠΎΡΡΠΎΠ·ΠΈΠΎΠ½Π½ΠΎ-ΡΡΠΎΠΉΠΊΠΈΡ ΠΌΠ°ΡΠ΅ΡΠΈΠ°Π»ΠΎΠ², ΠΎΠ±Π»Π°Π΄Π°ΡΡΠΈΡ Π²ΡΡΠΎΠΊΠΈΠΌ ΠΎΡΠ½ΠΎΡΠ΅Π½ΠΈΠ΅ΠΌ ΠΏΡΠΎΡΠ½ΠΎΡΡΠΈ ΠΊ ΠΏΠ»ΠΎΡΠ½ΠΎΡΡΠΈ.Π£ΠΌΠ΅Π½ΡΡΠ΅Π½ΠΈΠ΅ ΡΠ°Π·ΠΌΠ΅ΡΠ° ΠΊΠΎΠΌΠΏΠΎΠ½Π΅Π½ΡΠΎΠ² ΠΌΠΎΠΆΠ΅Ρ Π±ΡΡΡ Π²ΡΠΏΠΎΠ»Π½Π΅Π½ΠΎ Π»ΠΈΠ±ΠΎ ΠΏΡΡΠ΅ΠΌ ΠΊΠΎΠ½ΡΡΡΡΠΊΡΠΈΠ²Π½ΠΎΠΉ ΠΎΠΏΡΠΈΠΌΠΈΠ·Π°ΡΠΈΠΈ ΠΊΠΎΠ½ΡΡΡΡΠΊΡΠΈΠΈ, Π»ΠΈΠ±ΠΎ ΠΏΡΡΠ΅ΠΌ Π·Π°ΠΌΠ΅Π½Ρ ΡΡΠΆΠ΅Π»ΡΡ ΠΌΠ°ΡΠ΅ΡΠΈΠ°Π»ΠΎΠ² Π½Π° Π±ΠΎΠ»Π΅Π΅ Π»Π΅Π³ΠΊΠΈΠ΅ ΠΈ Π²ΡΡΠΎΠΊΠΎΠΏΡΠΎΡΠ½ΡΠ΅. Π ΡΡΠΎΠΌ ΠΊΠΎΠ½ΡΠ΅ΠΊΡΡΠ΅ ΠΊΠΎΠ²ΠΊΠ° ΠΈΠ³ΡΠ°Π΅Ρ Π²Π°ΠΆΠ½ΡΡ ΡΠΎΠ»Ρ Π² ΠΏΡΠΎΠΈΠ·Π²ΠΎΠ΄ΡΡΠ²Π΅ ΠΊΠΎΠ½ΡΡΡΡΠΊΡΠΈΠ²Π½ΡΡ ΡΠ»Π΅ΠΌΠ΅Π½ΡΠΎΠ² Ρ ΠΎΠΏΡΠΈΠΌΠ°Π»ΡΠ½ΠΎΠΉ Π½Π°Π³ΡΡΠ·ΠΊΠΎΠΉ. Π ΠΠ½ΡΡΠΈΡΡΡΠ΅ ΠΎΠ±ΡΠ°Π±ΠΎΡΠΊΠΈ ΠΌΠ΅ΡΠ°Π»Π»ΠΎΠ² Π΄Π°Π²Π»Π΅Π½ΠΈΠ΅ΠΌ ΠΈ ΠΌΠ΅ΡΠ°Π»Π»ΠΎΠΎΠ±ΡΠ°Π±Π°ΡΡΠ²Π°ΡΡΠΈΡ ΡΡΠ°Π½ΠΊΠΎΠ² (IFUM) Π±ΡΠ»ΠΈ ΡΠ°Π·ΡΠ°Π±ΠΎΡΠ°Π½Ρ ΡΠ°Π·Π»ΠΈΡΠ½ΡΠ΅ ΠΈΠ½Π½ΠΎΠ²Π°ΡΠΈΠΎΠ½Π½ΡΠ΅ ΡΠ΅Ρ Π½ΠΎΠ»ΠΎΠ³ΠΈΠΈ ΠΊΠΎΠ²ΠΊΠΈ. Π§ΡΠΎ ΠΊΠ°ΡΠ°Π΅ΡΡΡ ΡΡΡΡΠΊΡΡΡΠ½ΠΎΠΉ ΠΎΠΏΡΠΈΠΌΠΈΠ·Π°ΡΠΈΠΈ, Π±ΡΠ»ΠΈ ΠΈΡΡΠ»Π΅Π΄ΠΎΠ²Π°Π½Ρ ΡΠ°Π·Π»ΠΈΡΠ½ΡΠ΅ ΡΡΡΠ°ΡΠ΅Π³ΠΈΠΈ Π»ΠΎΠΊΠ°Π»ΡΠ½ΠΎΠ³ΠΎ ΡΡΠΈΠ»Π΅Π½ΠΈΡ ΠΊΠΎΠΌΠΏΠΎΠ½Π΅Π½ΡΠΎΠ².ΠΠΎΠΆΠ΅Ρ Π±ΡΡΡ ΡΠ΅Π°Π»ΠΈΠ·ΠΎΠ²Π°Π½ΠΎ Π»ΠΎΠΊΠ°Π»ΡΠ½ΠΎ ΠΈΠ½Π΄ΡΡΠΈΡΠΎΠ²Π°Π½Π½ΠΎΠ΅ Π΄Π΅ΡΠΎΡΠΌΠ°ΡΠΈΠΎΠ½Π½ΠΎΠ΅ ΡΠΏΡΠΎΡΠ½Π΅Π½ΠΈΠ΅ ΠΏΠΎΡΡΠ΅Π΄ΡΡΠ²ΠΎΠΌ Ρ ΠΎΠ»ΠΎΠ΄Π½ΠΎΠΉ ΠΊΠΎΠ²ΠΊΠΈ ΠΏΠΎΠ΄ Π½Π°Π»ΠΎΠΆΠ΅Π½Π½ΡΠΌ Π³ΠΈΠ΄ΡΠΎΡΡΠ°ΡΠΈΡΠ΅ΡΠΊΠΈΠΌ Π΄Π°Π²Π»Π΅Π½ΠΈΠ΅ΠΌ. ΠΡΠΎΠΌΠ΅ ΡΠΎΠ³ΠΎ, ΠΊΠΎΠ½ΡΡΠΎΠ»ΠΈΡΡΠ΅ΠΌΡΠ΅ ΠΌΠ°ΡΡΠ΅Π½ΡΠΈΡΠ½ΡΠ΅ Π·ΠΎΠ½Ρ ΠΌΠΎΠ³ΡΡ Π±ΡΡΡ ΡΠΎΠ·Π΄Π°Π½Ρ ΠΏΡΡΠ΅ΠΌ ΡΠΎΡΠΌΠΈΡΠΎΠ²Π°Π½ΠΈΡ ΠΈΠ½Π΄ΡΡΠΈΡΠΎΠ²Π°Π½Π½ΠΎΠ³ΠΎ ΡΠ°Π·ΠΎΠ²ΠΎΠ³ΠΎ ΠΏΡΠ΅Π²ΡΠ°ΡΠ΅Π½ΠΈΡ Π² ΠΌΠ΅ΡΠ°ΡΡΠ°Π±ΠΈΠ»ΡΠ½ΡΡ Π°ΡΡΡΠ΅Π½ΠΈΡΠ½ΡΡ ΡΡΠ°Π»ΡΡ . ΠΡΡΠ³ΠΈΠ΅ ΠΈΡΡΠ»Π΅Π΄ΠΎΠ²Π°Π½ΠΈΡ Π±ΡΠ»ΠΈ ΡΠΎΡΡΠ΅Π΄ΠΎΡΠΎΡΠ΅Π½Ρ Π½Π° Π·Π°ΠΌΠ΅Π½Π΅ ΡΡΠΆΠ΅Π»ΡΡ ΡΡΠ°Π»ΡΠ½ΡΡ Π΄Π΅ΡΠ°Π»Π΅ΠΉ Π²ΡΡΠΎΠΊΠΎΠΏΡΠΎΡΠ½ΡΠΌΠΈ ΡΠΏΠ»Π°Π²Π°ΠΌΠΈ ΡΠ²Π΅ΡΠ½ΡΡ ΠΌΠ΅ΡΠ°Π»Π»ΠΎΠ² ΠΈΠ»ΠΈ Π³ΠΈΠ±ΡΠΈΠ΄Π½ΡΠΌΠΈ ΡΠΎΠ΅Π΄ΠΈΠ½Π΅Π½ΠΈΡΠΌΠΈ ΠΌΠ°ΡΠ΅ΡΠΈΠ°Π»ΠΎΠ². ΠΡΠ»ΠΎ ΡΠ°Π·ΡΠ°Π±ΠΎΡΠ°Π½ΠΎ Π½Π΅ΡΠΊΠΎΠ»ΡΠΊΠΎ ΠΏΡΠΎΡΠ΅ΡΡΠΎΠ² ΠΊΠΎΠ²ΠΊΠΈ ΠΌΠ°Π³Π½ΠΈΠ΅Π²ΡΡ , Π°Π»ΡΠΌΠΈΠ½ΠΈΠ΅Π²ΡΡ ΠΈ ΡΠΈΡΠ°Π½ΠΎΠ²ΡΡ ΡΠΏΠ»Π°Π²ΠΎΠ² Π΄Π»Ρ ΡΠ°Π·Π»ΠΈΡΠ½ΡΡ Π°Π²ΠΈΠ°ΡΠΈΠΎΠ½Π½ΡΡ ΠΈ Π°Π²ΡΠΎΠΌΠΎΠ±ΠΈΠ»ΡΠ½ΡΡ ΠΏΡΠΈΠΌΠ΅Π½Π΅Π½ΠΈΠΉ.ΠΡΠ»Π° ΡΠ°ΡΡΠΌΠΎΡΡΠ΅Π½Π° Π²ΡΡ ΡΠ΅Ρ Π½ΠΎΠ»ΠΎΠ³ΠΈΡΠ΅ΡΠΊΠ°Ρ ΡΠ΅ΠΏΠΎΡΠΊΠ° ΠΎΡ ΠΎΠΏΡΠ΅Π΄Π΅Π»Π΅Π½ΠΈΡ Ρ Π°ΡΠ°ΠΊΡΠ΅ΡΠΈΡΡΠΈΠΊ ΠΌΠ°ΡΠ΅ΡΠΈΠ°Π»Π° ΡΠ΅ΡΠ΅Π· ΠΌΠΎΠ΄Π΅Π»ΠΈΡΠΎΠ²Π°Π½ΠΈΠ΅ ΠΏΡΠΎΡΠ΅ΡΡΠ° Π΄ΠΎ ΠΏΡΠΎΠΈΠ·Π²ΠΎΠ΄ΡΡΠ²Π° Π΄Π΅ΡΠ°Π»Π΅ΠΉ. ΠΠΎΠ΄ΡΠ²Π΅ΡΠΆΠ΄Π΅Π½Π° Π²ΠΎΠ·ΠΌΠΎΠΆΠ½ΠΎΡΡΡ ΠΊΠΎΠ²ΠΊΠΈ ΠΈΠ·Π΄Π΅Π»ΠΈΠΉ ΡΠ»ΠΎΠΆΠ½ΠΎΠΉ ΡΠΎΡΠΌΡ ΠΈΠ· ΡΡΠΈΡ ΡΠΏΠ»Π°Π²ΠΎΠ². ΠΠ΅ΡΠΌΠΎΡΡΡ Π½Π° ΡΡΡΠ΄Π½ΠΎΡΡΠΈ, ΡΠ²ΡΠ·Π°Π½Π½ΡΠ΅ Ρ ΠΌΠ°ΡΠΈΠ½Π½ΡΠΌ ΡΡΠΌΠΎΠΌ ΠΈ Π²ΡΡΠΎΠΊΠΎΠΉ ΡΠ΅ΠΌΠΏΠ΅ΡΠ°ΡΡΡΠΎΠΉ, ΠΌΠ΅ΡΠΎΠ΄ Π°ΠΊΡΡΡΠΈΡΠ΅ΡΠΊΠΎΠΉ ΡΠΌΠΈΡΡΠΈΠΈ (ΠΠ) ΡΡΠΏΠ΅ΡΠ½ΠΎ ΠΏΡΠΈΠΌΠ΅Π½ΡΠ΅ΡΡΡ Π΄Π»Ρ ΠΎΠ½Π»Π°ΠΉΠ½-ΠΌΠΎΠ½ΠΈΡΠΎΡΠΈΠ½Π³Π° Π΄Π΅ΡΠ΅ΠΊΡΠΎΠ² ΠΏΠΎΠΊΠΎΠ²ΠΊΠΈ. ΠΡΠ» ΡΠ°Π·ΡΠ°Π±ΠΎΡΠ°Π½ Π½ΠΎΠ²ΡΠΉ Π°Π»Π³ΠΎΡΠΈΡΠΌ Π°Π½Π°Π»ΠΈΠ·Π° ΠΠ, ΡΡΠΎΠ±Ρ ΠΌΠΎΠΆΠ½ΠΎ Π±ΡΠ»ΠΎ ΠΎΠ±Π½Π°ΡΡΠΆΠΈΠ²Π°ΡΡ ΠΈ ΠΊΠ»Π°ΡΡΠΈΡΠΈΡΠΈΡΠΎΠ²Π°ΡΡ ΡΠ°Π·Π»ΠΈΡΠ½ΡΠ΅ ΠΎΠ±ΡΠ°Π·ΡΡ ΡΠΈΠ³Π½Π°Π»ΠΎΠ² ΠΈΠ·-Π·Π° ΡΠ°Π·Π»ΠΈΡΠ½ΡΡ ΡΠΎΠ±ΡΡΠΈΠΉ, ΡΠ°ΠΊΠΈΡ ΠΊΠ°ΠΊ ΡΠ°ΡΡΡΠ΅ΡΠΊΠΈΠ²Π°Π½ΠΈΠ΅ ΠΏΡΠΎΠ΄ΡΠΊΡΠ° / ΡΡΠ°ΠΌΠΏΠ° ΠΈΠ»ΠΈ ΠΈΠ·Π½ΠΎΡ ΡΡΠ°ΠΌΠΏΠ°.ΠΡΠΎΠΌΠ΅ ΡΠΎΠ³ΠΎ, ΠΎΡΡΡΠ΅ΡΡΠ²ΠΈΠΌΠΎΡΡΡ ΡΠΏΠΎΠΌΡΠ½ΡΡΡΡ ΡΠ΅Ρ Π½ΠΎΠ»ΠΎΠ³ΠΈΠΉ ΠΊΠΎΠ²ΠΊΠΈ Π±ΡΠ»Π° Π΄ΠΎΠΊΠ°Π·Π°Π½Π° Ρ ΠΏΠΎΠΌΠΎΡΡΡ Π°Π½Π°Π»ΠΈΠ·Π° ΠΌΠ΅ΡΠΎΠ΄ΠΎΠΌ ΠΊΠΎΠ½Π΅ΡΠ½ΡΡ ΡΠ»Π΅ΠΌΠ΅Π½ΡΠΎΠ² (FEA). ΠΠ°ΠΏΡΠΈΠΌΠ΅Ρ, ΡΠ΅Π»ΠΎΡΡΠ½ΠΎΡΡΡ ΡΡΠ°ΠΌΠΏΠΎΠ²ΠΎΠΊ ΠΏΠΎ ΠΎΡΠ½ΠΎΡΠ΅Π½ΠΈΡ ΠΊ Π²ΠΎΠ·Π½ΠΈΠΊΠ½ΠΎΠ²Π΅Π½ΠΈΡ ΡΡΠ΅ΡΠΈΠ½ ΠΈΠ·-Π·Π° ΡΠ΅ΡΠΌΠΎΠΌΠ΅Ρ Π°Π½ΠΈΡΠ΅ΡΠΊΠΎΠΉ ΡΡΡΠ°Π»ΠΎΡΡΠΈ, Π° ΡΠ°ΠΊΠΆΠ΅ ΠΏΠ»Π°ΡΡΠΈΡΠ΅ΡΠΊΠΎΠ΅ ΠΏΠΎΠ²ΡΠ΅ΠΆΠ΄Π΅Π½ΠΈΠ΅ ΠΏΠΎΠΊΠΎΠ²ΠΎΠΊ Π±ΡΠ»ΠΎ ΠΈΡΡΠ»Π΅Π΄ΠΎΠ²Π°Π½ΠΎ Ρ ΠΏΠΎΠΌΠΎΡΡΡ ΠΌΠΎΠ΄Π΅Π»Π΅ΠΉ ΡΠΎΠ²ΠΎΠΊΡΠΏΠ½ΠΎΠ³ΠΎ ΠΏΠΎΠ²ΡΠ΅ΠΆΠ΄Π΅Π½ΠΈΡ. Π ΡΡΠΎΠΉ ΡΡΠ°ΡΡΠ΅ ΠΎΠΏΠΈΡΠ°Π½Ρ Π½Π΅ΠΊΠΎΡΠΎΡΡΠ΅ ΠΈΠ· ΡΠΏΠΎΠΌΡΠ½ΡΡΡΡ ΠΏΠΎΠ΄Ρ ΠΎΠ΄ΠΎΠ².
ΠΠΎΡΡΡΠ°Ρ ΡΡΠ°ΠΌΠΏΠΎΠ²ΠΊΠ° — ΠΎΠ±Π·ΠΎΡ
13.1 ΠΠ²Π΅Π΄Π΅Π½ΠΈΠ΅
Π Π»Π΅Π³ΠΊΠΎΠ²ΡΡ Π°Π²ΡΠΎΠΌΠΎΠ±ΠΈΠ»ΡΡ , Π³ΡΡΠ·ΠΎΠ²ΠΈΠΊΠ°Ρ ΠΈ ΡΡΠ°ΠΊΡΠΎΡΠ°Ρ (Π΄Π»Ρ ΡΠ΅Π»ΡΡΠΊΠΎΠ³ΠΎ Ρ ΠΎΠ·ΡΠΉΡΡΠ²Π°) ΠΊΠΎΠ²Π°Π½ΡΠ΅ ΠΊΠΎΠΌΠΏΠΎΠ½Π΅Π½ΡΡ ΠΎΠ±ΡΡΠ½ΠΎ ΠΈΡΠΏΠΎΠ»ΡΠ·ΡΡΡΡΡ Π²Π΅Π·Π΄Π΅, Π³Π΄Π΅ Π²ΡΡΡΠ΅ΡΠ°ΡΡΡΡ ΡΠΎΡΠΊΠΈ, ΠΏΠΎΠ΄Π²Π΅ΡΠΆΠ΅Π½Π½ΡΠ΅ Π½Π°Π³ΡΡΠ·ΠΊΠ°ΠΌ ΠΈ ΡΠ΄Π°ΡΠΎΠΏΡΠΎΡΠ½ΠΎΡΡΠΈ.ΠΠ΅Π³ΠΊΠΎΠ²ΡΠ΅ ΠΈ Π³ΡΡΠ·ΠΎΠ²ΡΠ΅ Π°Π²ΡΠΎΠΌΠΎΠ±ΠΈΠ»ΠΈ ΠΌΠΎΠ³ΡΡ ΡΠΎΠ΄Π΅ΡΠΆΠ°ΡΡ Π±ΠΎΠ»Π΅Π΅ 250 ΠΏΠΎΠΊΠΎΠ²ΠΎΠΊ, Π±ΠΎΠ»ΡΡΠΈΠ½ΡΡΠ²ΠΎ ΠΈΠ· ΠΊΠΎΡΠΎΡΡΡ ΠΈΠ·Π³ΠΎΡΠΎΠ²Π»Π΅Π½ΠΎ ΠΈΠ· ΡΠ³Π»Π΅ΡΠΎΠ΄ΠΈΡΡΠΎΠΉ ΠΈΠ»ΠΈ Π»Π΅Π³ΠΈΡΠΎΠ²Π°Π½Π½ΠΎΠΉ ΡΡΠ°Π»ΠΈ. ΠΠΎΠ²Π°Π½ΡΠ΅ ΠΊΠΎΠΌΠΏΠΎΠ½Π΅Π½ΡΡ Π΄Π²ΠΈΠ³Π°ΡΠ΅Π»Ρ ΠΈ ΡΡΠ°Π½ΡΠΌΠΈΡΡΠΈΠΈ Π²ΠΊΠ»ΡΡΠ°ΡΡ Π² ΡΠ΅Π±Ρ ΡΠ°ΡΡΠ½Ρ, ΠΊΠΎΠ»Π΅Π½ΡΠ°ΡΡΠ΅ Π²Π°Π»Ρ, ΡΡΠ°Π½ΡΠΌΠΈΡΡΠΈΠΎΠ½Π½ΡΠ΅ Π²Π°Π»Ρ ΠΈ ΡΠ΅ΡΡΠ΅ΡΠ½ΠΈ, Π΄ΠΈΡΡΠ΅ΡΠ΅Π½ΡΠΈΠ°Π»Ρ, ΠΏΡΠΈΠ²ΠΎΠ΄Π½ΡΠ΅ Π²Π°Π»Ρ, ΡΡΡΠΏΠΈΡΡ ΡΡΠ΅ΠΏΠ»Π΅Π½ΠΈΡ, Π° ΡΠ°ΠΊΠΆΠ΅ Π²ΠΈΠ»ΠΊΠΈ ΠΈ ΠΊΡΠ΅ΡΡΠΎΠ²ΠΈΠ½Ρ ΠΊΠ°ΡΠ΄Π°Π½Π½ΡΡ ΡΠ°ΡΠ½ΠΈΡΠΎΠ². ΠΠΎΠ²Π°Π½ΡΠ΅ ΠΊΠΎΠΌΠΏΠΎΠ½Π΅Π½ΡΡ, ΡΠ°ΠΊΠΈΠ΅ ΠΊΠ°ΠΊ ΡΠ°ΡΠΏΡΠ΅Π΄Π΅Π»ΠΈΡΠ΅Π»ΡΠ½ΡΠ΅ Π²Π°Π»Ρ, ΡΠ΅ΡΡΠ΅ΡΠ½ΠΈ, ΡΠ΅ΡΡΠ΅ΡΠ½ΠΈ ΠΈ ΠΊΠΎΡΠΎΠΌΡΡΠ»Π°, ΠΌΠΎΠ³ΡΡ ΠΏΡΠΈΠΎΠ±ΡΠ΅ΡΠ°ΡΡ ΡΡΠ΄ ΡΠ²ΠΎΠΉΡΡΠ², ΠΎΡΠ½ΠΎΠ²Π°Π½Π½ΡΡ Π½Π° ΡΠ°Π·Π»ΠΈΡΠ½ΡΡ ΠΌΠΈΠΊΡΠΎΡΡΡΡΠΊΡΡΡΠ°Ρ , ΠΏΠΎΠ»ΡΡΠ΅Π½Π½ΡΡ Π² ΡΠ΅Π·ΡΠ»ΡΡΠ°ΡΠ΅ ΡΠ΅ΡΠΌΠΈΡΠ΅ΡΠΊΠΎΠΉ ΠΎΠ±ΡΠ°Π±ΠΎΡΠΊΠΈ. ΠΠΎΠ»Π΅ΡΠ½ΡΠ΅ ΡΠΏΠΈΠ½Π΄Π΅Π»ΠΈ, ΡΠΊΠ²ΠΎΡΠ½ΠΈ, Π±Π°Π»ΠΊΠΈ ΠΈ Π²Π°Π»Ρ ΠΎΡΠ΅ΠΉ, ΡΠΎΡΡΠΈΠΎΠ½Ρ, ΡΠ°ΡΠΈΠΊΠΎΠ²ΡΠ΅ ΡΠΏΠΈΠ»ΡΠΊΠΈ, ΠΏΡΠΎΠΌΠ΅ΠΆΡΡΠΎΡΠ½ΡΠ΅ ΡΡΡΠ°Π³ΠΈ, ΡΡΡΠ°Π³ΠΈ ΡΠ°ΡΡΠ½Π°, ΡΡΠ»Π΅Π²ΡΠ΅ ΡΡΡΠ°Π³ΠΈ ΠΈ ΡΡΡΠ°Π³ΠΈ Π΄Π»Ρ Π»Π΅Π³ΠΊΠΎΠ²ΡΡ Π°Π²ΡΠΎΠΌΠΎΠ±ΠΈΠ»Π΅ΠΉ, Π°Π²ΡΠΎΠ±ΡΡΠΎΠ² ΠΈ Π³ΡΡΠ·ΠΎΠ²ΠΈΠΊΠΎΠ² ΡΠ»ΡΠΆΠ°Ρ ΠΏΡΠΈΠΌΠ΅ΡΠ°ΠΌΠΈ ΠΏΡΠΈΠ»ΠΎΠΆΠ΅Π½ΠΈΠΉ, ΡΡΠ΅Π±ΡΡΡΠΈΡ ΡΠΊΡΡΡΠ΅ΠΌΠ°Π»ΡΠ½ΡΡ ΡΡΠ»ΠΎΠ²ΠΈΠΉ ΠΏΡΠΎΡΠ½ΠΎΡΡΠΈ ΠΈ ΠΏΡΠΎΡΠ½ΠΎΡΡΠΈ.
Π ΡΠ΅Π»ΡΡΠΊΠΎΡ ΠΎΠ·ΡΠΉΡΡΠ²Π΅Π½Π½ΠΎΠΌ Π½Π°Π²Π΅ΡΠ½ΠΎΠΌ ΠΎΠ±ΠΎΡΡΠ΄ΠΎΠ²Π°Π½ΠΈΠΈ, ΠΏΠΎΠΌΠΈΠΌΠΎ ΠΊΠΎΠΌΠΏΠΎΠ½Π΅Π½ΡΠΎΠ² Π΄Π²ΠΈΠ³Π°ΡΠ΅Π»Ρ ΠΈ ΡΡΠ°Π½ΡΠΌΠΈΡΡΠΈΠΈ, ΠΈΡΠΏΠΎΠ»ΡΠ·ΡΡΡΡΡ ΠΊΠ»ΡΡΠ΅Π²ΡΠ΅ ΠΏΠΎΠΊΠΎΠ²ΠΊΠΈ, Π½Π°ΡΠΈΠ½Π°Ρ ΠΎΡ ΡΠ΅ΡΡΠ΅ΡΠ΅Π½, Π²Π°Π»ΠΎΠ², ΡΡΡΠ°Π³ΠΎΠ² ΠΈ ΡΠΏΠΈΠ½Π΄Π΅Π»Π΅ΠΉ, ΠΈ Π·Π°ΠΊΠ°Π½ΡΠΈΠ²Π°Ρ ΠΊΠΎΠ½ΡΠ°ΠΌΠΈ ΡΡΠ»Π΅Π²ΡΡ ΡΡΠ³, Π·ΡΠ±ΡΡΠΌΠΈ Π±ΠΎΡΠΎΠ½Ρ ΠΈ ΡΡΠΎΠΉΠΊΠ°ΠΌΠΈ ΠΊΡΠ»ΡΡΠΈΠ²Π°ΡΠΎΡΠ°. Π’ΡΠΆΠ΅Π»ΡΠ΅ ΡΠ°Π½ΠΊΠΈ ΡΠΎΠ΄Π΅ΡΠΆΠ°Ρ Π±ΠΎΠ»Π΅Π΅ 550 ΠΎΡΠ΄Π΅Π»ΡΠ½ΡΡ ΠΏΠΎΠΊΠΎΠ²ΠΎΠΊ; Π Π±ΡΠΎΠ½Π΅ΡΡΠ°Π½ΡΠΏΠΎΡΡΠ΅ΡΠ°Ρ Π·Π°Π½ΡΡΠΎ Π±ΠΎΠ»Π΅Π΅ 250 ΡΠ΅Π»ΠΎΠ²Π΅ΠΊ.
Π‘ΡΠ°Π»ΡΠ½ΡΠ΅ ΠΏΠΎΠΊΠΎΠ²ΠΊΠΈ ΡΠ΅Π³ΡΠ»ΡΡΠ½ΠΎ ΡΡΠΎΡΠ½ΡΡΡΡΡ, ΠΊΠΎΠ³Π΄Π° ΠΏΡΠΎΡΠ½ΠΎΡΡΡ, ΡΡΡΠΎΠΉΡΠΈΠ²ΠΎΡΡΡ ΠΊ ΡΠ΄Π°ΡΠ°ΠΌ ΠΈ ΡΡΡΠ°Π»ΠΎΡΡΠΈ, Π½Π°Π΄Π΅ΠΆΠ½ΠΎΡΡΡ ΠΈ ΡΠΊΠΎΠ½ΠΎΠΌΠΈΡΠ½ΠΎΡΡΡ ΡΠ²Π»ΡΡΡΡΡ ΠΆΠΈΠ·Π½Π΅Π½Π½ΠΎ Π²Π°ΠΆΠ½ΡΠΌΠΈ ΡΠ°ΠΊΡΠΎΡΠ°ΠΌΠΈ. ΠΠΎΠ²Π°Π½ΡΠ΅ ΠΌΠ°ΡΠ΅ΡΠΈΠ°Π»Ρ ΡΠ°ΠΊΠΆΠ΅ ΠΎΠ±Π»Π°Π΄Π°ΡΡ ΠΆΠ΅Π»Π°Π΅ΠΌΡΠΌΠΈ Ρ Π°ΡΠ°ΠΊΡΠ΅ΡΠΈΡΡΠΈΠΊΠ°ΠΌΠΈ ΠΏΡΠΈ Π²ΡΡΠΎΠΊΠΈΡ ΠΈΠ»ΠΈ Π½ΠΈΠ·ΠΊΠΈΡ ΡΠ΅ΠΌΠΏΠ΅ΡΠ°ΡΡΡΠ°Ρ , ΠΏΠ»Π°ΡΡΠΈΡΠ½ΠΎΡΡΡΡ, ΡΠ²Π΅ΡΠ΄ΠΎΡΡΡΡ ΠΈ ΠΎΠ±ΡΠ°Π±Π°ΡΡΠ²Π°Π΅ΠΌΠΎΡΡΡΡ.ΠΠΎΡΡΠΈΠΆΠ΅Π½ΠΈΡ Π² ΡΠ΅Ρ Π½ΠΎΠ»ΠΎΠ³ΠΈΠΈ ΠΊΠΎΠ²ΠΊΠΈ ΡΠ°ΡΡΠΈΡΠΈΠ»ΠΈ Π΄ΠΈΠ°ΠΏΠ°Π·ΠΎΠ½ ΡΠΎΡΠΌ, ΡΠ°Π·ΠΌΠ΅ΡΠΎΠ² ΠΈ ΡΠ²ΠΎΠΉΡΡΠ², Π΄ΠΎΡΡΡΠΏΠ½ΡΡ Π² ΠΊΠΎΠ²Π°Π½ΡΡ ΠΈΠ·Π΄Π΅Π»ΠΈΡΡ , ΡΡΠΎΠ±Ρ ΡΠ΄ΠΎΠ²Π»Π΅ΡΠ²ΠΎΡΠΈΡΡ ΡΠ°ΡΡΡΡΠ΅Π΅ ΡΠ°Π·Π½ΠΎΠΎΠ±ΡΠ°Π·ΠΈΠ΅ ΡΡΠ΅Π±ΠΎΠ²Π°Π½ΠΈΠΉ ΠΊ ΠΊΠΎΠ½ΡΡΡΡΠΊΡΠΈΠΈ ΠΈ Ρ Π°ΡΠ°ΠΊΡΠ΅ΡΠΈΡΡΠΈΠΊΠ°ΠΌ.
Π ΠΎΠ±ΡΠ΅ΠΌ, ΡΡΠ°Π»ΡΠ½ΡΠ΅ ΠΏΠΎΠΊΠΎΠ²ΠΊΠΈ ΠΏΡΠΎΡ ΠΎΠ΄ΡΡ: (Π°) Π³ΠΎΡΡΡΡΡ ΠΊΠΎΠ²ΠΊΡ, (Π±) Π³ΠΎΡΡΡΡΡ ΠΊΠΎΠ²ΠΊΡ ΠΈΠ»ΠΈ (Π²) Ρ ΠΎΠ»ΠΎΠ΄Π½ΡΡ ΠΊΠΎΠ²ΠΊΡ. ΠΡ ΠΊΡΠ°ΡΠΊΠΎΠ΅ ΠΎΠΏΠΈΡΠ°Π½ΠΈΠ΅ Π²ΡΠ³Π»ΡΠ΄ΠΈΡ ΡΠ»Π΅Π΄ΡΡΡΠΈΠΌ ΠΎΠ±ΡΠ°Π·ΠΎΠΌ:
- a.
ΠΠΎΡΡΡΠ°Ρ ΠΊΠΎΠ²ΠΊΠ° ΡΡΠ°Π»ΠΈ : Π’Π΅ΠΌΠΏΠ΅ΡΠ°ΡΡΡΠ° ΠΊΠΎΠ²ΠΊΠΈ Π²ΡΡΠ΅ ΡΠ΅ΠΌΠΏΠ΅ΡΠ°ΡΡΡΡ ΡΠ΅ΠΊΡΠΈΡΡΠ°Π»Π»ΠΈΠ·Π°ΡΠΈΠΈ ΠΈ ΠΎΠ±ΡΡΠ½ΠΎ ΡΠΎΡΡΠ°Π²Π»ΡΠ΅Ρ 950β1250 Β° C.ΠΠ±ΡΡΠ½ΠΎ Π½Π°Π±Π»ΡΠ΄Π°Π΅ΡΡΡ Ρ ΠΎΡΠΎΡΠ°Ρ ΡΠΎΡΠΌΡΠ΅ΠΌΠΎΡΡΡ (ΡΠΎ Π΅ΡΡΡ Π·Π°ΠΏΠΎΠ»Π½Π΅Π½ΠΈΠ΅ ΠΏΠΎΠ»ΠΎΡΡΠΈ ΠΌΠ°ΡΡΠΈΡΡ Π² ΠΊΠΎΠ½ΡΠ΅ΠΊΡΡΠ΅ ΠΊΠΎΠ²ΠΊΠΈ), Π½ΠΈΠ·ΠΊΠΈΠ΅ ΡΡΠΈΠ»ΠΈΡ ΡΠΎΡΠΌΠΎΠ²Π°Π½ΠΈΡ ΠΈ ΠΏΠΎΡΡΠΈ ΠΎΠ΄Π½ΠΎΡΠΎΠ΄Π½Π°Ρ ΠΏΡΠΎΡΠ½ΠΎΡΡΡ Π½Π° ΡΠ°ΡΡΡΠΆΠ΅Π½ΠΈΠ΅ ΠΎΠ±ΡΠ°Π±Π°ΡΡΠ²Π°Π΅ΠΌΠΎΠΉ Π΄Π΅ΡΠ°Π»ΠΈ.
- Π±.
ΠΠΎΡΡΡΠ°Ρ ΠΊΠΎΠ²ΠΊΠ° ΡΡΠ°Π»ΠΈ : Π’Π΅ΠΌΠΏΠ΅ΡΠ°ΡΡΡΠ° ΠΊΠΎΠ²ΠΊΠΈ Π²ΡΠ΅ Π΅ΡΠ΅ Π²ΡΡΠ΅ ΡΠ΅ΠΌΠΏΠ΅ΡΠ°ΡΡΡΡ ΡΠ΅ΠΊΡΠΈΡΡΠ°Π»Π»ΠΈΠ·Π°ΡΠΈΠΈ: ΠΎΡ 750 Β° C Π΄ΠΎ 950 Β° C. ΠΠΎΡΠ΅ΡΡ ΠΎΠΊΠ°Π»ΠΈΠ½Ρ Π½Π° ΠΏΠΎΠ²Π΅ΡΡ Π½ΠΎΡΡΠΈ Π΄Π΅ΡΠ°Π»ΠΈ ΠΌΠ΅Π½ΡΡΠ΅, Π° Π΄ΠΎΠΏΡΡΠΊ ΠΌΠ΅Π½ΡΡΠ΅ ΠΏΠΎ ΡΡΠ°Π²Π½Π΅Π½ΠΈΡ Ρ Π³ΠΎΡΡΡΠ΅ΠΉ ΡΡΠ°ΠΌΠΏΠΎΠ²ΠΊΠΎΠΉ. ΠΡΠΏΡΡΡΠ²Π°ΡΡ ΠΎΠ³ΡΠ°Π½ΠΈΡΠ΅Π½Π½ΡΡ ΡΠΎΡΠΌΡΠ΅ΠΌΠΎΡΡΡ ΠΈ Π±ΠΎΠ»Π΅Π΅ Π²ΡΡΠΎΠΊΠΈΠ΅ ΡΡΠΈΠ»ΠΈΡ ΡΠΎΡΠΌΠΎΠ²Π°Π½ΠΈΡ, ΡΠ΅ΠΌ ΠΏΡΠΈ Π³ΠΎΡΡΡΠ΅ΠΉ ΡΡΠ°ΠΌΠΏΠΎΠ²ΠΊΠ΅, Π½ΠΎ Π±ΠΎΠ»Π΅Π΅ Π½ΠΈΠ·ΠΊΠΈΠ΅ ΡΡΠΈΠ»ΠΈΡ ΡΠΎΡΠΌΠΎΠ²Π°Π½ΠΈΡ, ΡΠ΅ΠΌ ΠΏΡΠΈ Ρ ΠΎΠ»ΠΎΠ΄Π½ΠΎΠΉ ΡΡΠ°ΠΌΠΏΠΎΠ²ΠΊΠ΅.
- Π³.
Π₯ΠΎΠ»ΠΎΠ΄Π½Π°Ρ ΠΊΠΎΠ²ΠΊΠ° ΡΡΠ°Π»ΠΈ : Π’Π΅ΠΌΠΏΠ΅ΡΠ°ΡΡΡΠ° ΠΊΠΎΠ²ΠΊΠΈ Π±Π»ΠΈΠ·ΠΊΠ° ΠΊ ΠΊΠΎΠΌΠ½Π°ΡΠ½ΡΠΌ ΡΡΠ»ΠΎΠ²ΠΈΡΠΌ, Π°Π΄ΠΈΠ°Π±Π°ΡΠΈΡΠ΅ΡΠΊΠΈΠΉ ΡΠ°ΠΌΠΎΠ½Π°Π³ΡΠ΅Π² ΠΌΠΎΠΆΠ΅Ρ ΠΏΡΠΈΠ²Π΅ΡΡΠΈ ΠΊ ΡΠ΅ΠΌΠΏΠ΅ΡΠ°ΡΡΡΠ΅ Π΄ΠΎ 150 Β° C. ΠΡΠΏΡΡΡΠ²Π°ΡΡ ΠΌΠ°ΠΊΡΠΈΠΌΠ°Π»ΡΠ½ΠΎ ΡΠ·ΠΊΠΈΠ΅ Π΄ΠΎΠΏΡΡΡΠΈΠΌΡΠ΅ ΠΎΡΠΊΠ»ΠΎΠ½Π΅Π½ΠΈΡ ΠΈ ΠΎΡΡΡΡΡΡΠ²ΠΈΠ΅ Π½Π°ΠΊΠΈΠΏΠΈ Π½Π° ΠΏΠΎΠ²Π΅ΡΡ Π½ΠΎΡΡΠΈ Π΄Π΅ΡΠ°Π»ΠΈ. ΠΡΠΎΠΌΠ΅ ΡΠΎΠ³ΠΎ, ΠΌΠΎΠΆΠ΅Ρ ΠΈΠΌΠ΅ΡΡ ΠΌΠ΅ΡΡΠΎ ΡΠ²Π΅Π»ΠΈΡΠ΅Π½ΠΈΠ΅ ΠΏΡΠΎΡΠ½ΠΎΡΡΠΈ ΠΈ ΠΏΠ°Π΄Π΅Π½ΠΈΠ΅ ΠΏΠ»Π°ΡΡΠΈΡΠ½ΠΎΡΡΠΈ ΠΈΠ·-Π·Π° Π΄Π΅ΡΠΎΡΠΌΠ°ΡΠΈΠΎΠ½Π½ΠΎΠ³ΠΎ ΡΠΏΡΠΎΡΠ½Π΅Π½ΠΈΡ. Π€ΠΎΡΠΌΠΈΡΡΠ΅ΠΌΠΎΡΡΡ Π΄ΠΎΠ²ΠΎΠ»ΡΠ½ΠΎ Π½ΠΈΠ·ΠΊΠ°Ρ, ΠΈ Π½Π΅ΠΎΠ±Ρ ΠΎΠ΄ΠΈΠΌΡ Π²ΡΡΠΎΠΊΠΈΠ΅ ΡΡΠΈΠ»ΠΈΡ ΡΠΎΡΠΌΠΎΠ²Π°Π½ΠΈΡ.
Π§ΡΠΎ ΠΊΠ°ΡΠ°Π΅ΡΡΡ ΠΎΠ±ΡΠ΅ΠΌΠ° ΠΏΡΠΎΠΌΡΡΠ»Π΅Π½Π½ΡΡ ΠΏΠΎΠΊΠΎΠ²ΠΎΠΊ, Π³ΠΎΡΡΡΠ°Ρ ΡΡΠ°ΠΌΠΏΠΎΠ²ΠΊΠ° ΡΠ²Π»ΡΠ΅ΡΡΡ ΠΏΡΠ΅Π΄ΠΏΠΎΡΡΠΈΡΠ΅Π»ΡΠ½ΡΠΌ ΠΏΡΠΎΡΠ΅ΡΡΠΎΠΌ, ΠΏΠΎΡΠΊΠΎΠ»ΡΠΊΡ Π΄Π»Ρ ΡΡΠΎΠ³ΠΎ ΡΠΏΠΎΡΠΎΠ±Π° ΠΏΠΎΠ΄Ρ ΠΎΠ΄ΠΈΡ ΡΠΈΡΠΎΠΊΠΈΠΉ ΡΠΏΠ΅ΠΊΡΡ ΡΡΠ°Π»Π΅ΠΉ ΠΈ ΠΊΠΎΠΌΠΏΠΎΠ½Π΅Π½ΡΠΎΠ².ΠΠΎΡΡΠΎΠΌΡ Π² ΡΡΠΎΠΉ Π³Π»Π°Π²Π΅ ΠΎΡΠ½ΠΎΠ²Π½ΠΎΠ΅ Π²Π½ΠΈΠΌΠ°Π½ΠΈΠ΅ Π±ΡΠ΄Π΅Ρ ΡΠ΄Π΅Π»Π΅Π½ΠΎ Π³ΠΎΡΡΡΠ΅ΠΉ ΡΡΠ°ΠΌΠΏΠΎΠ²ΠΊΠ΅ ΡΡΠ°Π»Π΅ΠΉ. ΠΠΏΡΡΡ ΠΆΠ΅, ΡΡΠΎ ΠΊΠ°ΡΠ°Π΅ΡΡΡ ΡΠΈΡΠΎΠΊΠΎΠΉ ΠΎΠ±Π»Π°ΡΡΠΈ Π³ΠΎΡΡΡΠ΅ΠΉ ΡΡΠ°ΠΌΠΏΠΎΠ²ΠΊΠΈ, Π² Π½Π°ΡΡΠΎΡΡΠ΅ΠΉ Π³Π»Π°Π²Π΅ ΠΎΡΠ½ΠΎΠ²Π½ΠΎΠ΅ Π²Π½ΠΈΠΌΠ°Π½ΠΈΠ΅ Π±ΡΠ΄Π΅Ρ ΡΠ΄Π΅Π»Π΅Π½ΠΎ ΡΡΠ°ΠΌΠΏΠΎΠ²ΠΊΠ΅ Π² Π·Π°ΠΊΡΡΡΡΡ ΡΡΠ°ΠΌΠΏΠ°Ρ (Π° Π½Π΅ ΡΡΠ°ΠΌΠΏΠΎΠ²ΠΊΠ΅), ΠΊΠΎΡΠΎΡΠ°Ρ ΠΈΡΠΏΠΎΠ»ΡΠ·ΡΠ΅ΡΡΡ Π΄Π»Ρ ΠΏΡΠΎΠΈΠ·Π²ΠΎΠ΄ΡΡΠ²Π° Π³ΠΎΡΠΎΠ²ΡΡ ΠΈΠ·Π΄Π΅Π»ΠΈΠΉ Ρ ΠΆΠ΅ΡΡΠΊΠΈΠΌΠΈ Π΄ΠΎΠΏΡΡΠΊΠ°ΠΌΠΈ ΠΏΠΎ ΡΠ°Π·ΠΌΠ΅ΡΠ°ΠΌ.
ΠΡΠΈ ΡΠ°ΡΡΠΌΠΎΡΡΠ΅Π½ΠΈΠΈ Π³ΠΎΡΡΡΠ΅ΠΉ ΡΡΠ°ΠΌΠΏΠΎΠ²ΠΊΠΈ Π²Π°ΠΆΠ½ΠΎ ΠΎΠ±ΡΠ°ΡΠΈΡΡ Π²Π½ΠΈΠΌΠ°Π½ΠΈΠ΅ Π½Π° ΡΠΎ, ΡΡΠΎ ΠΏΡΡΡΠΎΠΊ ΠΏΠΎΠ²ΡΠΎΡΠ½ΠΎ Π½Π°Π³ΡΠ΅Π²Π°Π΅ΡΡΡ, ΠΎΠ±ΡΡΠ½ΠΎ Π² ΠΈΠ½Π΄ΡΠΊΡΠΈΠΎΠ½Π½ΠΎΠΉ ΠΏΠ΅ΡΠΈ, Π΄ΠΎ ΡΠ΅ΠΌΠΏΠ΅ΡΠ°ΡΡΡΡ ~ 1200 Β° C, Π° Π·Π°ΡΠ΅ΠΌ ΠΏΡΠΎΠΏΡΡΠΊΠ°Π΅ΡΡΡ ΡΠ΅ΡΠ΅Π· ΠΊΠΎΠ²ΠΎΡΠ½ΡΠΉ ΠΏΡΠ΅ΡΡ.ΠΠ° ΠΏΡΠ΅ΡΡΠ΅ ΠΎΠ½ ΠΌΠΎΠΆΠ΅Ρ ΠΏΡΠΎΠΉΡΠΈ ΠΌΠ½ΠΎΠ³ΠΎΡΡΡΠΏΠ΅Π½ΡΠ°ΡΡΡ ΠΊΠΎΠ²ΠΊΡ ΠΏΠ΅ΡΠ΅Π΄ ΠΎΠ±ΡΠ΅Π·ΠΊΠΎΠΉ. ΠΠΎΡΠ»Π΅ ΡΡΠΎΠ³ΠΎ ΡΡΠΎΡΠΌΠΈΡΠΎΠ²Π°Π½Π½ΡΠΉ ΠΊΠΎΠΌΠΏΠΎΠ½Π΅Π½Ρ ΠΌΠΎΠΆΠ΅Ρ ΠΎΡ Π»Π°ΠΆΠ΄Π°ΡΡΡΡ Π½Π° Π²ΠΎΠ·Π΄ΡΡ Π΅ ΠΈΠ»ΠΈ ΠΏΠΎΠ΄Π²Π΅ΡΠ³Π°ΡΡΡΡ ΡΠ΅ΡΠΌΠΎΠΎΠ±ΡΠ°Π±ΠΎΡΠΊΠ΅ Π² Π·Π°Π²ΠΈΡΠΈΠΌΠΎΡΡΠΈ ΠΎΡ ΡΠ΅Π»Π΅Π²ΡΡ ΡΠ²ΠΎΠΉΡΡΠ².
ΠΠΎΠ»ΡΡΠΈΠ½ΡΡΠ²ΠΎ ΠΏΠΎΠΊΠΎΠ²ΠΎΠΊ ΠΈΠ· Π³ΠΎΡΡΡΠ΅ΠΊΠ°ΡΠ°Π½ΠΎΠΉ ΡΡΠ°Π»ΠΈ ΠΈΠ·Π³ΠΎΡΠ°Π²Π»ΠΈΠ²Π°ΡΡ Ρ ΠΈΡΠΏΠΎΠ»ΡΠ·ΠΎΠ²Π°Π½ΠΈΠ΅ΠΌ ΠΏΡΠΎΡΡΡΡ ΡΠ³Π»Π΅ΡΠΎΠ΄ΠΈΡΡΡΡ ΠΈΠ»ΠΈ Π½ΠΈΠ·ΠΊΠΎΠ»Π΅Π³ΠΈΡΠΎΠ²Π°Π½Π½ΡΡ ΡΡΠ°Π»Π΅ΠΉ Ρ ΡΠΎΠ΄Π΅ΡΠΆΠ°Π½ΠΈΠ΅ΠΌ ΡΠ³Π»Π΅ΡΠΎΠ΄Π°, Π²ΡΠ±ΡΠ°Π½Π½ΡΠΌ Π΄Π»Ρ ΠΏΠΎΠ»ΡΡΠ΅Π½ΠΈΡ ΠΏΡΠΈΠ΅ΠΌΠ»Π΅ΠΌΠΎΠ³ΠΎ ΡΠΎΡΠ΅ΡΠ°Π½ΠΈΡ ΠΏΡΠΎΡΠ½ΠΎΡΡΠΈ, ΡΠ΄Π°ΡΠ½ΠΎΠΉ Π²ΡΠ·ΠΊΠΎΡΡΠΈ ΠΈ ΠΊΠΎΠ²ΠΊΠΎΡΡΠΈ. ΠΡΡΠΎΠΊΠΎΠΏΡΠΎΡΠ½ΡΠ΅ ΠΏΠΎΠΊΠΎΠ²ΠΊΠΈ ΠΎΠ±ΡΡΠ½ΠΎ ΡΠΎΠ΄Π΅ΡΠΆΠ°Ρ ΠΏΡΠΈΠΌΠ΅ΡΠ½ΠΎ 0,2β0,5 ΠΌΠ°Ρ.% Π£Π³Π»Π΅ΡΠΎΠ΄Π°, ΡΡΠΎ ΠΏΠΎΠ·Π²ΠΎΠ»ΡΠ΅Ρ ΠΏΠΎΠ΄Π²Π΅ΡΠ³Π°ΡΡ ΠΏΠΎΠΊΠΎΠ²ΠΊΠΈ ΡΠ΅ΡΠΌΠΎΠΎΠ±ΡΠ°Π±ΠΎΡΠΊΠ΅ Π΄ΠΎ ΡΡΠ΅Π±ΡΠ΅ΠΌΠΎΠΉ ΠΏΡΠΎΡΠ½ΠΎΡΡΠΈ ΠΏΠΎΡΠ»Π΅ ΠΎΠΏΠ΅ΡΠ°ΡΠΈΠΈ ΠΊΠΎΠ²ΠΊΠΈ.Π’Π΅ΡΠΌΠΈΡΠ΅ΡΠΊΠ°Ρ ΠΎΠ±ΡΠ°Π±ΠΎΡΠΊΠ°, Π² ΠΏΠ΅ΡΠ²ΡΡ ΠΎΡΠ΅ΡΠ΅Π΄Ρ Π·Π°ΠΊΠ°Π»ΠΊΠ° ΠΈ ΠΎΡΠΏΡΡΠΊ ( Q + T ), ΡΡΠ΅Π±ΡΠ΅Ρ Π·Π½Π°ΡΠΈΡΠ΅Π»ΡΠ½ΡΡ Π·Π°ΡΡΠ°Ρ ΡΠ½Π΅ΡΠ³ΠΈΠΈ (ΠΈ, ΡΠ»Π΅Π΄ΠΎΠ²Π°ΡΠ΅Π»ΡΠ½ΠΎ, ΡΠ²Π»ΡΠ΅ΡΡΡ Π΄ΠΎΡΠΎΠ³ΠΎΡΡΠΎΡΡΠ΅ΠΉ) ΠΈ ΠΎΡΡΠΈΡΠ°ΡΠ΅Π»ΡΠ½ΠΎ ΡΠΊΠ°Π·ΡΠ²Π°Π΅ΡΡΡ Π½Π° ΠΏΡΠΎΠΈΠ·Π²ΠΎΠ΄ΠΈΡΠ΅Π»ΡΠ½ΠΎΡΡΠΈ. ΠΡΠΎΠΌΠ΅ ΡΠΎΠ³ΠΎ, Π·Π°ΠΊΠ°Π»ΠΊΠ° ΡΠ°ΠΊΠΆΠ΅ Π²ΡΠ·ΡΠ²Π°Π΅Ρ ΡΠΈΡΠΊ Π²ΡΡΠΎΠΊΠΈΡ ΠΎΡΡΠ°ΡΠΎΡΠ½ΡΡ Π½Π°ΠΏΡΡΠΆΠ΅Π½ΠΈΠΉ ΠΏΡΠΈ ΡΠ°ΡΡΡΠΆΠ΅Π½ΠΈΠΈ, Π΄Π΅ΡΠΎΡΠΌΠ°ΡΠΈΠΈ, Π° ΠΈΠ½ΠΎΠ³Π΄Π° ΠΈ ΡΡΠ΅ΡΠΈΠ½ Π² ΠΊΠΎΠΌΠΏΠΎΠ½Π΅Π½ΡΠ°Ρ . ΠΠΎΡΡΠΎΠΌΡ Π΄Π»Ρ ΠΌΠΈΠ½ΠΈΠΌΠΈΠ·Π°ΡΠΈΠΈ ΠΎΡΡΠ°ΡΠΎΡΠ½ΡΡ Π½Π°ΠΏΡΡΠΆΠ΅Π½ΠΈΠΉ ΠΏΡΠΈ ΡΠ°ΡΡΡΠΆΠ΅Π½ΠΈΠΈ ΡΡΠ΅Π±ΡΠ΅ΡΡΡ ΠΎΠΏΠ΅ΡΠ°ΡΠΈΡ ΠΏΡΠ°Π²ΠΊΠΈ Ρ ΠΏΠΎΡΠ»Π΅Π΄ΡΡΡΠΈΠΌ ΠΎΡΠΆΠΈΠ³ΠΎΠΌ Π΄Π»Ρ ΡΠ½ΡΡΠΈΡ Π½Π°ΠΏΡΡΠΆΠ΅Π½ΠΈΡ. ΠΡΠ΅Π²ΠΈΠ΄Π½ΠΎ, ΡΡΠΎ ΡΡΠΈ ΠΎΠΏΠ΅ΡΠ°ΡΠΈΠΈ ΡΠ²Π΅Π»ΠΈΡΠΈΠ²Π°ΡΡ ΠΎΠ±ΡΡΡ ΡΡΠΎΠΈΠΌΠΎΡΡΡ ΠΎΠ±ΡΠ°Π±ΠΎΡΠΊΠΈ.ΠΠ° ΠΌΠ½ΠΎΠ³ΠΈΡ ΠΏΡΠ΅Π΄ΠΏΡΠΈΡΡΠΈΡΡ Π·Π° ΠΎΠΏΠ΅ΡΠ°ΡΠΈΠ΅ΠΉ ΠΏΡΠ°Π²ΠΊΠΈ Π½Π΅ ΡΠ»Π΅Π΄ΡΠ΅Ρ ΠΎΡΠΆΠΈΠ³ Π΄Π»Ρ ΡΠ½ΡΡΠΈΡ Π½Π°ΠΏΡΡΠΆΠ΅Π½ΠΈΠΉ, ΡΡΠΎ ΠΌΠΎΠΆΠ΅Ρ ΠΏΡΠΈΠ²Π΅ΡΡΠΈ ΠΊ ΡΠ½ΠΈΠΆΠ΅Π½ΠΈΡ ΡΡΡΠ°Π»ΠΎΡΡΠ½ΠΎΠΉ Π΄ΠΎΠ»Π³ΠΎΠ²Π΅ΡΠ½ΠΎΡΡΠΈ ΠΈΠ·-Π·Π° Π½Π°Π»ΠΈΡΠΈΡ ΠΎΡΡΠ°ΡΠΎΡΠ½ΡΡ Π½Π°ΠΏΡΡΠΆΠ΅Π½ΠΈΠΉ ΠΏΡΠΈ ΡΠ°ΡΡΡΠΆΠ΅Π½ΠΈΠΈ. Π‘Π»Π΅Π΄ΠΎΠ²Π°ΡΠ΅Π»ΡΠ½ΠΎ, Π±ΡΠ»ΠΈ ΠΏΠΎΠΏΡΡΠΊΠΈ ΡΠ°Π·ΡΠ°Π±ΠΎΡΠ°ΡΡ ΠΌΠ°ΡΠΊΠΈ ΡΡΠ°Π»ΠΈ (Π² ΠΏΠ΅ΡΠ²ΡΡ ΠΎΡΠ΅ΡΠ΅Π΄Ρ ΠΌΠΈΠΊΡΠΎΠ»Π΅Π³ΠΈΡΠΎΠ²Π°Π½Π½ΡΠ΅, ΠΠ), ΠΊΠΎΡΠΎΡΡΠ΅ Π½Π΅ ΡΡΡΠ°Π΄Π°Π»ΠΈ Π±Ρ Π½Π΅ΠΊΠΎΡΠΎΡΡΠΌΠΈ ΠΈΠ· ΡΡΠΈΡ Π·Π°Π±ΠΎΠ»Π΅Π²Π°Π½ΠΈΠΉ. Π‘Ρ Π΅ΠΌΠ° ΠΏΠΎΠΊΠΎΠ²ΠΎΠΊ ΡΠ΅ΡΠΈΠΈ MA Q + T , ΠΎΠ±ΡΠ°Π±ΠΎΡΠ°Π½Π½ΡΡ ΠΈ ΠΎΡ Π»Π°ΠΆΠ΄Π°Π΅ΠΌΡΡ Π²ΠΎΠ·Π΄ΡΡ ΠΎΠΌ, ΠΏΠΎΠΊΠ°Π·Π°Π½Π° Π½Π° ΡΠΈΡ. 13.1.
Π ΠΈΡΡΠ½ΠΎΠΊ 13.1. Π‘ΡΠ°Π²Π½Π΅Π½ΠΈΠ΅ ΠΏΡΠΎΡΠ΅ΡΡΠΎΠ², ΠΏΡΠΎΠΈΡΡ ΠΎΠ΄ΡΡΠΈΡ Π² ΠΎΠ±ΡΡΠ½ΡΡ Π·Π°ΠΊΠ°Π»Π΅Π½Π½ΡΡ ΡΡΠ°Π»ΡΡ Ρ ΠΎΡΠΏΡΡΠΊΠΎΠΌ ΠΈ Π² MA-ΡΡΠ°Π»ΡΡ Ρ ΠΏΡΡΠΌΡΠΌ Π²ΠΎΠ·Π΄ΡΡΠ½ΡΠΌ ΠΎΡ Π»Π°ΠΆΠ΄Π΅Π½ΠΈΠ΅ΠΌ [1].
Π Π½Π°ΡΠ°Π»Π΅ 1970-Ρ Π³ΠΎΠ΄ΠΎΠ² ΠΈΡΠΏΠΎΠ»ΡΠ·ΠΎΠ²Π°Π½ΠΈΠ΅ ΡΡΠ΅Π΄Π½Π΅ΡΠ³Π»Π΅ΡΠΎΠ΄ΠΈΡΡΡΡ ΠΌΠΈΠΊΡΠΎΠ»Π΅Π³ΠΈΡΠΎΠ²Π°Π½Π½ΡΡ ΡΡΠ°Π»Π΅ΠΉ Π΄Π»Ρ Π³ΠΎΡΡΡΠ΅ΠΉ ΡΡΠ°ΠΌΠΏΠΎΠ²ΠΊΠΈ Ρ Π²ΠΎΠ·Π΄ΡΡΠ½ΡΠΌ ΠΎΡ Π»Π°ΠΆΠ΄Π΅Π½ΠΈΠ΅ΠΌ Π½Π°ΡΠ°Π»ΠΎΡΡ Π² ΠΠ²ΡΠΎΠΏΠ΅, Π° ΡΠ°ΠΊΠΆΠ΅ Π² Π‘Π¨Π, ΡΡΠΎΠ±Ρ ΠΈΠ·Π±Π΅ΠΆΠ°ΡΡ Π·Π°ΠΊΠ°Π»ΠΊΠΈ ΠΈ ΡΠ΅ΡΠΌΠΈΡΠ΅ΡΠΊΠΎΠΉ ΠΎΠ±ΡΠ°Π±ΠΎΡΠΊΠΈ Ρ ΠΎΡΠΏΡΡΠΊΠΎΠΌ, Π° ΡΠ°ΠΊΠΆΠ΅ ΡΠΎΠΏΡΡΡΡΠ²ΡΡΡΠΈΡ ΠΏΡΠΎΠ±Π»Π΅ΠΌ. Π’ΡΠ΅Π±ΠΎΠ²Π°Π½ΠΈΠ΅ ΠΏΡΠΎΡΠ½ΠΎΡΡΠΈ ΡΠ΄ΠΎΠ²Π»Π΅ΡΠ²ΠΎΡΡΠ»ΠΎΡΡ Π² ΠΏΠ΅ΡΠ²ΡΡ ΠΎΡΠ΅ΡΠ΅Π΄Ρ Π·Π° ΡΡΠ΅Ρ Π²ΡΠ΄Π΅Π»Π΅Π½ΠΈΡ Π² ΡΠ΅ΡΡΠΈΡΠ½ΠΎ-ΠΏΠ΅ΡΠ»ΠΈΡΠ½ΠΎΠΉ ΠΌΠ°ΡΡΠΈΡΠ΅. ΠΠ΄Π½Π°ΠΊΠΎ ΡΠ°ΠΊΠ°Ρ ΠΌΠΈΠΊΡΠΎΡΡΡΡΠΊΡΡΡΠ° ΠΏΡΠΈΠ²ΠΎΠ΄ΠΈΡ ΠΊ ΡΠ½ΠΈΠΆΠ΅Π½ΠΈΡ ΡΠ΄Π°ΡΠ½ΠΎΠΉ Π²ΡΠ·ΠΊΠΎΡΡΠΈ, ΠΈ ΡΡΠΈ ΡΡΠ°Π»ΠΈ ΡΡΡΠ°Π΄Π°ΡΡ ΠΏΠ»ΠΎΡ ΠΎΠΉ ΡΠ²Π°ΡΠΈΠ²Π°Π΅ΠΌΠΎΡΡΡΡ; ΠΏΠΎΡΡΠΎΠΌΡ ΠΈΡΠΏΠΎΠ»ΡΠ·ΠΎΠ²Π°Π½ΠΈΠ΅ ΡΠ°ΠΊΠΈΡ ΠΏΠΎΠΊΠΎΠ²ΠΎΠΊ Π±ΡΠ»ΠΎ ΠΎΠ³ΡΠ°Π½ΠΈΡΠ΅Π½ΠΎ ΠΌΠ΅Π½Π΅Π΅ Π²Π°ΠΆΠ½ΡΠΌΠΈ ΠΊΠΎΠΌΠΏΠΎΠ½Π΅Π½ΡΠ°ΠΌΠΈ.Π₯ΠΎΡΠΎΡΠΈΠΉ ΠΎΡΡΠ΅Ρ ΠΎΠ± ΡΡΠΈΡ ΡΠ°Π·ΡΠ°Π±ΠΎΡΠΊΠ°Ρ Π±ΡΠ» Π΄Π°Π½ Hulka et al. [2].
ΠΡΠ»ΠΎ ΠΎΠ±Π½Π°ΡΡΠΆΠ΅Π½ΠΎ, ΡΡΠΎ ΠΌΠΈΠΊΡΠΎΠ»Π΅Π³ΠΈΡΠΎΠ²Π°Π½Π½ΡΠ΅ Π±Π΅ΠΉΠ½ΠΈΡΠ½ΡΠ΅ ΡΡΡΡΠΊΡΡΡΡ Ρ Π½ΠΈΠ·ΠΊΠΈΠΌ ΡΠΎΠ΄Π΅ΡΠΆΠ°Π½ΠΈΠ΅ΠΌ ΡΠ³Π»Π΅ΡΠΎΠ΄Π° Π² ΡΡΠ»ΠΎΠ²ΠΈΡΡ Π²ΠΎΠ·Π΄ΡΡΠ½ΠΎΠ³ΠΎ ΠΎΡ Π»Π°ΠΆΠ΄Π΅Π½ΠΈΡ ΠΎΠ±Π΅ΡΠΏΠ΅ΡΠΈΠ²Π°ΡΡ ΠΎΠΏΡΠΈΠΌΠ°Π»ΡΠ½ΠΎΠ΅ ΡΠΎΡΠ΅ΡΠ°Π½ΠΈΠ΅ ΠΏΡΠΎΡΠ½ΠΎΡΡΠΈ ΠΈ Π²ΡΠ·ΠΊΠΎΡΡΠΈ; Π½ΠΎΠ²ΡΠ΅ ΡΠ°Π·ΡΠ°Π±ΠΎΡΠΊΠΈ Π² ΡΡΠΎΠΉ ΠΎΠ±Π»Π°ΡΡΠΈ ΠΏΡΠΎΠΈΠ·ΠΎΡΠ»ΠΈ Π·Π° ΠΏΠΎΡΠ»Π΅Π΄Π½ΠΈΠ΅ 15β20 Π»Π΅Ρ [Π½Π°ΠΏΡΠΈΠΌΠ΅Ρ, 3]. Π Π―ΠΏΠΎΠ½ΠΈΠΈ, Π½Π°ΠΏΡΠΈΠΌΠ΅Ρ, Π΄ΠΈΡΠΏΠ΅ΡΡΠΈΠΎΠ½Π½ΠΎΠ΅ ΡΠ²Π΅ΡΠ΄Π΅Π½ΠΈΠ΅ ΡΠ΅ΡΠ΅Π· ΠΌΠ΅Π΄Ρ Π² Π±Π΅ΠΉΠ½ΠΈΡΠ½ΠΎΠΉ ΠΌΠ°ΡΡΠΈΡΠ΅ ΠΏΡΠΈΠ²Π΅Π»ΠΎ ΠΊ Π½ΠΎΠ²ΡΠΌ Π³ΠΎΡΡΡΠΈΠΌ ΠΏΠΎΠΊΠΎΠ²ΠΊΠ°ΠΌ Ρ Π²ΠΎΠ·Π΄ΡΡΠ½ΡΠΌ ΠΎΡ Π»Π°ΠΆΠ΄Π΅Π½ΠΈΠ΅ΠΌ, Π²ΡΡΠΎΠΊΠΎΠΉ ΠΏΡΠΎΡΠ½ΠΎΡΡΠΈ ΠΈ ΠΏΡΠΈΠ΅ΠΌΠ»Π΅ΠΌΠΎΠΉ ΡΠ΄Π°ΡΠ½ΠΎΠΉ Π²ΡΠ·ΠΊΠΎΡΡΠΈ [4]. Π Π‘Π¨Π Π΅ΡΡΡ ΠΏΠ°ΡΠ΅Π½ΡΡ, Π΄Π΅ΠΌΠΎΠ½ΡΡΡΠΈΡΡΡΡΠΈΠ΅ ΡΠ°Π·ΡΠ°Π±ΠΎΡΠΊΡ ΠΌΠΈΠΊΡΠΎΠ»Π΅Π³ΠΈΡΠΎΠ²Π°Π½Π½ΡΡ ΡΡΠ΅Π΄Π½Π΅ΡΠ³Π»Π΅ΡΠΎΠ΄ΠΈΡΡΡΡ ΡΡΠ°Π»Π΅ΠΉ, ΠΊΠΎΡΠΎΡΡΠ΅ ΠΌΠΎΠ³ΡΡ ΠΈΡΠΏΠΎΠ»ΡΠ·ΠΎΠ²Π°ΡΡΡΡ Π² ΠΏΠΎΠΊΠΎΠ²ΠΊΠ°Ρ Π±Π΅Π· ΡΠ΅ΡΠΌΠΈΡΠ΅ΡΠΊΠΎΠΉ ΠΎΠ±ΡΠ°Π±ΠΎΡΠΊΠΈ [5].
ΠΡΠ΅ ΠΎΠ΄Π½Π° ΠΏΡΠΎΠ±Π»Π΅ΠΌΠ° Π·Π°ΠΊΠ»ΡΡΠ°Π»Π°ΡΡ Π² ΠΎΠ±Π΅ΡΠΏΠ΅ΡΠ΅Π½ΠΈΠΈ ΡΠ°Π·ΡΠΌΠ½ΠΎΠΉ ΠΎΠ΄Π½ΠΎΡΠΎΠ΄Π½ΠΎΡΡΠΈ ΠΏΡΠΎΡΠ½ΠΎΡΡΠ½ΡΡ ΡΠ²ΠΎΠΉΡΡΠ² Π½Π° ΡΠ°Π·Π½ΠΎΠΉ Π³Π»ΡΠ±ΠΈΠ½Π΅ Π±ΠΎΠ»ΡΡΠΎΠΉ ΠΏΠΎΠΊΠΎΠ²ΠΊΠΈ, ΠΊΠΎΡΠΎΡΠ°Ρ ΠΌΠΎΠ³Π»Π° Π±Ρ ΠΎΡ Π»Π°ΠΆΠ΄Π°ΡΡΡΡ Ρ ΡΠ°Π·Π½ΠΎΠΉ ΡΠΊΠΎΡΠΎΡΡΡΡ. ΠΡΠ»ΠΎ ΠΈΡΠΏΠΎΠ»ΡΠ·ΠΎΠ²Π°Π½ΠΎ Π½Π΅ΡΠΊΠΎΠ»ΡΠΊΠΎ ΠΏΠΎΠ΄Ρ ΠΎΠ΄ΠΎΠ²; ΠΠ΄Π½Π° ΠΈΠ· ΠΏΡΠΈΠ²Π»Π΅ΠΊΠ°ΡΠ΅Π»ΡΠ½ΡΡ ΡΡΡΠ°ΡΠ΅Π³ΠΈΠΉ ΡΠΎΡΡΠΎΠΈΡ Π² ΠΈΡΠΏΠΎΠ»ΡΠ·ΠΎΠ²Π°Π½ΠΈΠΈ Ρ ΠΈΠΌΠΈΡΠ΅ΡΠΊΠΎΠ³ΠΎ ΡΠΎΡΡΠ°Π²Π°, ΠΊΠΎΡΠΎΡΡΠΉ Π΄Π΅Π»Π°Π΅Ρ ΠΏΠΎΠ»ΡΡΠ΅Π½Π½ΡΠ΅ ΠΏΡΠΎΡΠ½ΠΎΡΡΠ½ΡΠ΅ Ρ Π°ΡΠ°ΠΊΡΠ΅ΡΠΈΡΡΠΈΠΊΠΈ Π½Π΅Π·Π°Π²ΠΈΡΠΈΠΌΡΠΌΠΈ ΠΎΡ ΡΠΊΠΎΡΠΎΡΡΠΈ ΠΎΡ Π»Π°ΠΆΠ΄Π΅Π½ΠΈΡ. Π ΠΏΡΠΈΠ½ΡΠΈΠΏΠ΅ ΡΡΠΎ Π²ΠΎΠ·ΠΌΠΎΠΆΠ½ΠΎ ΡΠΎΠ»ΡΠΊΠΎ Ρ ΠΎΡΠ΅Π½Ρ Π½ΠΈΠ·ΠΊΠΎΡΠ³Π»Π΅ΡΠΎΠ΄ΠΈΡΡΡΠΌΠΈ ΡΡΠ°Π»ΡΠΌΠΈ [4].
ΠΡΠΎΠΌΠ΅ ΡΠΎΠ³ΠΎ, Π²Π°ΠΆΠ½ΡΠΌ ΡΡΠ΅Π±ΠΎΠ²Π°Π½ΠΈΠ΅ΠΌ ΡΠ²Π»ΡΠ΅ΡΡΡ ΡΠΎΠΏΡΠΎΡΠΈΠ²Π»Π΅Π½ΠΈΠ΅ ΡΡΡΠ°Π»ΠΎΡΡΠΈ Π°Π²ΡΠΎΠΌΠΎΠ±ΠΈΠ»ΡΠ½ΡΡ ΠΊΠΎΠΌΠΏΠΎΠ½Π΅Π½ΡΠΎΠ². ΠΠ°ΠΊ ΠΏΡΠ°Π²ΠΈΠ»ΠΎ, ΠΏΡΠ΅Π΄Π΅Π» Π²ΡΠ½ΠΎΡΠ»ΠΈΠ²ΠΎΡΡΠΈ (ΠΎΠ±ΡΠ΅ΠΏΡΠΈΠ½ΡΡΠ°Ρ ΠΌΠ΅ΡΠ° ΡΠΎΠΏΡΠΎΡΠΈΠ²Π»Π΅Π½ΠΈΡ ΡΡΡΠ°Π»ΠΎΡΡΠΈ) ΡΠΎΡΡΠ°Π²Π»ΡΠ΅Ρ ~ 0.4β0,5 ΠΠ’Π‘ Π² Π±ΠΎΠ»ΡΡΠΈΠ½ΡΡΠ²Π΅ ΡΡΠ°Π»Π΅ΠΉ [Π½Π°ΠΏΡΠΈΠΌΠ΅Ρ, 1,6].
ΠΠ°ΠΊ Π²ΠΈΠ΄Π½ΠΎ ΠΈΠ· Π΄Π°Π½Π½ΡΡ ΡΠΈΡ. 13.2, ΠΊΠΎΠ½ΡΡΠΎΠ»ΡΠ½ΡΠ΅ ΠΏΡΠΎΠΊΠ°ΡΠ°Π½Π½ΡΠ΅ ΠΌΠΈΠΊΡΠΎΠ»Π΅Π³ΠΈΡΠΎΠ²Π°Π½Π½ΡΠ΅ (ΠΠ) ΡΡΠ°Π»ΠΈ ΠΏΡΠΈ ΠΎΠ΄ΠΈΠ½Π°ΠΊΠΎΠ²ΠΎΠΌ ΡΡΠΎΠ²Π½Π΅ ΠΏΡΠΎΡΠ½ΠΎΡΡΠΈ Π½Π° ΡΠ°Π·ΡΡΠ² Π΄Π΅ΠΌΠΎΠ½ΡΡΡΠΈΡΡΡΡ Π±ΠΎΠ»Π΅Π΅ Π²ΡΡΠΎΠΊΡΡ ΡΡΡΠ°Π»ΠΎΡΡΠ½ΡΡ ΠΏΡΠΎΡΠ½ΠΎΡΡΡ.
Π ΠΈΡΡΠ½ΠΎΠΊ 13.2. ΠΠ·Π°ΠΈΠΌΠΎΡΠ²ΡΠ·Ρ ΠΌΠ΅ΠΆΠ΄Ρ ΠΏΡΠ΅Π΄Π΅Π»ΠΎΠΌ Π²ΡΠ½ΠΎΡΠ»ΠΈΠ²ΠΎΡΡΠΈ ( Οw ) ΠΈ ΠΏΡΠ΅Π΄Π΅Π»ΠΎΠΌ ΠΏΡΠΎΡΠ½ΠΎΡΡΠΈ (TS) Π΄Π»Ρ ΠΌΠΈΠΊΡΠΎΠ»Π΅Π³ΠΈΡΠΎΠ²Π°Π½Π½ΡΡ ΡΡΠ°Π»Π΅ΠΉ ΠΈ ΡΠ³Π»Π΅ΡΠΎΠ΄ΠΈΡΡΡΡ ΡΡΠ°Π»Π΅ΠΉ [1].
Π’Π°ΠΊΠΆΠ΅ Π΄ΠΎΡΡΡΠΏΠ½Ρ Π±ΠΎΠ»Π΅Π΅ ΡΠ»ΠΎΠΆΠ½ΡΠ΅ ΠΏΠΎΠ΄Ρ ΠΎΠ΄Ρ ΠΊ ΡΠ°Π·ΡΠ°Π±ΠΎΡΠΊΠ΅ Π½ΠΎΠ²ΠΎΠ³ΠΎ ΠΏΠΎΠΊΠΎΠ»Π΅Π½ΠΈΡ ΡΡΡΠ°Π»ΠΎΡΡΠ½ΡΡ ΡΡΠ°Π»Π΅ΠΉ Π΄Π»Ρ Π°Π²ΡΠΎΠΌΠΎΠ±ΠΈΠ»Π΅ΠΉ [7].
ΠΡΠ΅ ΠΎΠ΄Π½ΠΎ ΡΠ²ΠΎΠΉΡΡΠ²ΠΎ, ΠΊΠΎΡΠΎΡΠΎΠ΅ ΡΠ°Π½Π΅Π΅ Π½Π΅ ΡΡΠΈΡΠ°Π»ΠΎΡΡ ΠΊΡΠΈΡΠΈΡΠ΅ΡΠΊΠΈΠΌ Π² ΠΊΡΠ·Π½Π΅ΡΠ½ΠΎΠΉ ΠΏΡΠΎΠΌΡΡΠ»Π΅Π½Π½ΠΎΡΡΠΈ, Π½ΠΎ ΠΊΠΎΡΠΎΡΠΎΠ΅ Π²ΡΠ΅ ΡΠ°ΡΠ΅ ΠΏΡΠΈΠ½ΠΈΠΌΠ°Π΅ΡΡΡ Π²ΠΎ Π²Π½ΠΈΠΌΠ°Π½ΠΈΠ΅ Π² ΡΠΎΠ²ΡΠ΅ΠΌΠ΅Π½Π½ΡΡ ΠΊΠΎΠ½ΡΡΡΡΠΊΡΠΈΡΡ , — ΡΡΠΎ ΡΠ²Π°ΡΠΈΠ²Π°Π΅ΠΌΠΎΡΡΡ. Π ΠΎΠ±ΡΠ΅ΠΌ, ΠΏΡΠΎΡΡΠΎΠΉ ΠΌΠ΅ΡΠΎΠΉ ΡΠ²Π°ΡΠΈΠ²Π°Π΅ΠΌΠΎΡΡΠΈ ΡΠ²Π»ΡΠ΅ΡΡΡ ΡΠΎΠ΄Π΅ΡΠΆΠ°Π½ΠΈΠ΅ ΡΠ³Π»Π΅ΡΠΎΠ΄Π° Π² ΡΠΎΡΠ΅ΡΠ°Π½ΠΈΠΈ Ρ ΡΠ³Π»Π΅ΡΠΎΠ΄Π½ΡΠΌ ΡΠΊΠ²ΠΈΠ²Π°Π»Π΅Π½ΡΠΎΠΌ [C.E. = C + Mn / 6 + (Ni + Cu) / 15 + (Cr + Mo + V) / 5]. ΠΠΌΠ΅ΡΡΠ΅ ΠΎΠ½ΠΈ ΠΏΠΎΠΊΠ°Π·ΡΠ²Π°ΡΡ ΡΠ΅Π½Π΄Π΅Π½ΡΠΈΡ ΠΊ ΡΠ°ΡΡΡΠ΅ΡΠΊΠΈΠ²Π°Π½ΠΈΡ ΠΏΠΎΠ΄ Π±ΠΎΡΡΠΎΠΌ (Ρ ΠΎΠ»ΠΎΠ΄Π½ΠΎΠΌΡ) ΠΏΠΎΡΠ»Π΅ ΡΠ²Π°ΡΠΊΠΈ, ΠΊΠ°ΠΊ ΡΡΠΎ ΠΎΠ±ΡΡΠ½ΠΎ ΠΏΡΠ΅Π΄ΡΡΠ°Π²Π»Π΅Π½ΠΎ Π½Π° Π΄ΠΈΠ°Π³ΡΠ°ΠΌΠΌΠ΅ ΠΡΠ°Π²ΠΈΠ»Π»Ρ [8]. Π£ΡΡΠ°Π½ΠΎΠ²Π»Π΅Π½ΠΎ, ΡΡΠΎ ΡΠΎΠ΄Π΅ΡΠΆΠ°Π½ΠΈΠ΅ ΡΠ³Π»Π΅ΡΠΎΠ΄Π° Π½ΠΈΠΆΠ΅ 0,1 ΠΌΠ°Ρ.% ΠΠ΅Π·ΠΎΠΏΠ°ΡΠ½ΠΎ ΠΈ Π»Π΅Π³ΠΊΠΎ ΡΠ²Π°ΡΠΈΠ²Π°Π΅ΡΡΡ.Π‘ Π΄ΡΡΠ³ΠΎΠΉ ΡΡΠΎΡΠΎΠ½Ρ, ΠΊΠΎΠΌΠ±ΠΈΠ½Π°ΡΠΈΡ C> 0,15% Ρ C.E.> 0,6 ΡΡΠΈΡΠ°Π΅ΡΡΡ ΡΡΡΠ΄Π½ΠΎΠΉ Π΄Π»Ρ ΡΠ²Π°ΡΠΊΠΈ, ΡΡΠ·Π²ΠΈΠΌΠΎΠΉ Π΄Π»Ρ ΡΠ°ΡΡΡΠ΅ΡΠΊΠΈΠ²Π°Π½ΠΈΡ ΠΈ ΡΡΠ΅Π±ΡΠ΅Ρ ΠΏΡΠ΅Π΄Π²Π°ΡΠΈΡΠ΅Π»ΡΠ½ΠΎΠΉ ΠΈ / ΠΈΠ»ΠΈ ΠΏΠΎΡΠ»Π΅ΡΠ²Π°ΡΠΎΡΠ½ΠΎΠΉ ΠΎΠ±ΡΠ°Π±ΠΎΡΠΊΠΈ.
ΠΠ·Π²Π΅ΡΡΠ½ΠΎ, ΡΡΠΎ ΠΏΡΡΡΠΊΠΈ ΠΈΠ· ΠΎΠ±ΡΡΠ½ΡΡ ΠΌΠ°ΡΠΎΠΊ ΡΡΠ°Π»ΠΈ Π΄Π»Ρ ΠΊΠΎΠ²ΠΊΠΈ (Π½Π°ΠΏΡΠΈΠΌΠ΅Ρ, 37 C 15; 40 Cr 3 B ΠΈ Ρ. Π.) ΠΡΠΈ Π½Π°Π³ΡΠ΅Π²Π°Π½ΠΈΠΈ Π΄ΠΎ ~ 1200 Β° C Π±ΡΠ΄ΡΡ ΠΈΠΌΠ΅ΡΡ Π±ΠΎΠ»ΡΡΠΎΠΉ ΡΠ°Π·ΠΌΠ΅Ρ Π·Π΅ΡΠ½Π° Π°ΡΡΡΠ΅Π½ΠΈΡΠ° ΠΈ ΡΡΠΎ ΠΏΡΠΎΠ΄ΡΠΊΡΡ ΠΏΡΠ΅Π²ΡΠ°ΡΠ΅Π½ΠΈΡ ΠΈΠ· ΡΠ°ΠΊΠΈΡ Π°ΡΡΡΠ΅Π½ΠΈΡ ΠΏΠΎΠΊΠ°Π·Π°Π» Π±Ρ Π½ΠΈΠ·ΠΊΡΡ ΠΏΠ»Π°ΡΡΠΈΡΠ½ΠΎΡΡΡ. ΠΠΎΡΡΠΎΠΌΡ ΠΎΠ΄Π½Π° ΠΈΠ· ΠΏΡΠΎΠ±Π»Π΅ΠΌ ΠΊΠΎΠ²ΠΊΠΈ ΡΠΎΡΡΠΎΠΈΡ Π² ΡΠΎΠΌ, ΡΡΠΎΠ±Ρ ΠΎΠ³ΡΠ°Π½ΠΈΡΠΈΡΡ ΡΠ°Π·ΠΌΠ΅Ρ Π·Π΅ΡΠ½Π° Π°ΡΡΡΠ΅Π½ΠΈΡΠ° Π²ΠΎ Π²ΡΠ΅ΠΌΡ ΠΊΠΎΠ²ΠΊΠΈ.ΠΡΠΎ Π±ΡΠ»ΠΎ ΡΠ΄Π΅Π»Π°Π½ΠΎ Ρ ΠΏΠΎΠΌΠΎΡΡΡ ΠΌΠΈΠΊΡΠΎΠ»Π΅Π³ΠΈΡΠΎΠ²Π°Π½ΠΈΡ, Π° ΡΠ°ΠΊΠΆΠ΅ Ρ ΠΏΠΎΠΌΠΎΡΡΡ ΡΠ΅ΡΠΌΠΎΠΌΠ΅Ρ Π°Π½ΠΈΡΠ΅ΡΠΊΠΎΠΉ ΠΎΠ±ΡΠ°Π±ΠΎΡΠΊΠΈ.
ΠΠ· Π²ΡΡΠ΅ΡΠΊΠ°Π·Π°Π½Π½ΠΎΠ³ΠΎ ΠΎΡΠ΅Π²ΠΈΠ΄Π½ΠΎ, ΡΡΠΎ ΡΡΠ°Π»ΠΈ Π΄Π»Ρ Π°Π²ΡΠΎΠΌΠΎΠ±ΠΈΠ»ΡΠ½ΠΎΠΉ ΠΊΠΎΠ²ΠΊΠΈ Π΄ΠΎΠ»ΠΆΠ½Ρ ΠΎΠ±Π»Π°Π΄Π°ΡΡ ΡΠΏΠΎΡΠΎΠ±Π½ΠΎΡΡΡΡ ΡΠΎΡΠ΅ΡΠ°ΡΡ Π² ΡΠ΅Π±Π΅ ΠΏΡΠΎΡΠ½ΠΎΡΡΡ, ΡΠ΄Π°ΡΠ½ΡΡ Π²ΡΠ·ΠΊΠΎΡΡΡ, ΡΠΎΠΏΡΠΎΡΠΈΠ²Π»Π΅Π½ΠΈΠ΅ ΡΡΡΠ°Π»ΠΎΡΡΠΈ ΠΈ, Π²ΠΎ ΠΌΠ½ΠΎΠ³ΠΈΡ ΡΠ»ΡΡΠ°ΡΡ , Π²ΡΡΠΎΠΊΡΡ ΡΠ²Π°ΡΠΈΠ²Π°Π΅ΠΌΠΎΡΡΡ. Π‘ ΡΠ»ΡΡΡΠ΅Π½ΠΈΠ΅ΠΌ Π΄ΠΎΡΠΎΠΆΠ½ΡΡ ΡΡΠ»ΠΎΠ²ΠΈΠΉ ΠΏΠΎΡΡΠ΅Π±Π½ΠΎΡΡΡ Π² Π±ΠΎΠ»Π΅Π΅ Π²ΡΡΠΎΠΊΠΎΠΉ ΡΠΊΠΎΡΠΎΡΡΠΈ Π°Π²ΡΠΎΠΌΠΎΠ±ΠΈΠ»Π΅ΠΉ ΠΏΠΎΡΡΠΎΡΠ½Π½ΠΎ ΡΠ°ΡΡΠ΅Ρ, Π° Ρ ΠΏΠΎΠ²ΡΡΠ΅Π½ΠΈΠ΅ΠΌ ΡΠΊΠΎΡΠΎΡΡΠΈ ΠΊΡΡΡΡΡΠΈΠΉ ΠΌΠΎΠΌΠ΅Π½Ρ Π΄Π»Ρ ΡΡΠ°Π½ΡΠΌΠΈΡΡΠΈΠΈ ΡΠ°ΠΊΠΆΠ΅ ΡΠ²Π΅Π»ΠΈΡΠΈΠ²Π°Π΅ΡΡΡ, ΡΡΠΎ ΠΏΡΠ΅Π΄ΡΡΠ²Π»ΡΠ΅Ρ ΠΏΠΎΠ²ΡΡΠ΅Π½Π½ΡΠ΅ ΡΡΠ΅Π±ΠΎΠ²Π°Π½ΠΈΡ ΠΊΠΎ ΠΌΠ½ΠΎΠ³ΠΈΠΌ ΠΈΠ· Π²ΡΡΠ΅ΠΏΠ΅ΡΠ΅ΡΠΈΡΠ»Π΅Π½Π½ΡΡ ΡΠ²ΠΎΠΉΡΡΠ².ΠΡΠΎΠΌΠ΅ ΡΠΎΠ³ΠΎ, ΡΡΠΎΠ±Ρ ΡΠΌΠ΅Π½ΡΡΠΈΡΡ ΡΠ³Π»Π΅ΡΠΎΠ΄Π½ΡΠΉ ΡΠ»Π΅Π΄, Π½Π΅ΠΎΠ±Ρ ΠΎΠ΄ΠΈΠΌΠΎ ΡΠΌΠ΅Π½ΡΡΠΈΡΡ Π²Π΅Ρ Π±Π΅Π· ΡΡΠ΅ΡΠ±Π° Π΄Π»Ρ ΠΊΠ°ΠΊΠΈΡ -Π»ΠΈΠ±ΠΎ ΠΈΠ· ΡΠΏΠΎΠΌΡΠ½ΡΡΡΡ ΡΠ²ΠΎΠΉΡΡΠ². Π ΡΠ΅Π»ΠΎΠΌ, Π²ΡΠ±ΠΎΡ ΡΡΠ°Π»Π΅ΠΉ, ΠΏΡΠΎΡΠ΅ΡΡ ΠΈΡ ΠΊΠΎΠ²ΠΊΠΈ ΠΈ ΠΏΠΎΡΠ»Π΅Π΄ΡΡΡΠ°Ρ ΠΎΠ±ΡΠ°Π±ΠΎΡΠΊΠ° Π°Π²ΡΠΎΠΌΠΎΠ±ΠΈΠ»ΡΠ½ΡΡ ΠΊΠΎΠΌΠΏΠΎΠ½Π΅Π½ΡΠΎΠ² — Π²ΡΠ΅ ΡΡΠΎ ΠΈΠ³ΡΠ°Π΅Ρ Π²Π°ΠΆΠ½ΡΡ ΡΠΎΠ»Ρ Π² ΡΠ΅ΡΠ΅Π½ΠΈΠΈ ΠΏΠΎΡΡΠΎΡΠ½Π½ΠΎ ΡΠ°ΡΡΡΡΠΈΡ ΠΏΡΠΎΠ±Π»Π΅ΠΌ. Π ΡΡΠΎΠΉ Π³Π»Π°Π²Π΅ Π² ΠΎΡΠ½ΠΎΠ²Π½ΠΎΠΌ ΡΠ°ΡΡΠΌΠ°ΡΡΠΈΠ²Π°ΡΡΡΡ ΠΌΠΈΠΊΡΠΎΠ»Π΅Π³ΠΈΡΠΎΠ²Π°Π½Π½ΡΠ΅ ΡΡΠ°Π»ΠΈ Π΄Π»Ρ Π°Π²ΡΠΎΠΌΠΎΠ±ΠΈΠ»ΡΠ½ΠΎΠΉ ΠΊΠΎΠ²ΠΊΠΈ.
ΠΡΠ΄ΡΡΠ΅Π΅ ΠΊΡΠ·Π½Π΅ΡΠ½ΠΎΠΉ ΠΎΠ±ΡΠ°Π±ΠΎΡΠΊΠΈ — ΠΠ°ΠΌΠ΅Π½ΠΈΡ Π»ΠΈ ΠΊΠΎΠ²ΠΊΠ° Π½ΠΎΠ²ΡΠΌΠΈ ΠΏΡΠΎΡΠ΅ΡΡΠ°ΠΌΠΈ?
Π₯ΠΎΡΡ Π½Π΅Ρ Π½ΠΈΠΊΠ°ΠΊΠΈΡ ΡΠ²Π΅Π΄Π΅Π½ΠΈΠΉ ΠΎ ΡΠΎΠΌ, ΠΊΠΎΠ³Π΄Π° ΠΈ ΠΊΠ°ΠΊ ΠΏΡΠΎΡΠ΅ΡΡ ΠΊΠΎΠ²ΠΊΠΈ Π±ΡΠ» Β«ΠΎΡΠΊΡΡΡΒ» Π»ΡΠ΄ΡΠΌΠΈ, ΠΌΡ ΠΌΠΎΠΆΠ΅ΠΌ ΠΏΡΠ΅Π΄ΡΡΠ°Π²ΠΈΡΡ ΡΠ΅Π±Π΅ ΠΈΡΡΠΎΠΊΠΈ ΡΡΠΎΠ³ΠΎ ΠΏΡΠΎΡΠ΅ΡΡΠ°.ΠΠΈΠ΄ΠΊΠΈΠ΅ ΠΌΠ΅ΡΠ°Π»Π»Ρ, Π²ΡΠΏΠ»Π°Π²Π»Π΅Π½Π½ΡΠ΅ ΠΈΠ· ΡΡΡΠΎΠΉ ΡΡΠ΄Ρ, Π½ΡΠΆΠ½ΠΎ Π±ΡΠ»ΠΎ ΠΏΡΠ΅Π²ΡΠ°ΡΠΈΡΡ Π² Π±ΠΎΠ»Π΅Π΅ ΠΏΠΎΠ»Π΅Π·Π½ΡΠ΅ ΠΏΡΠ΅Π΄ΠΌΠ΅ΡΡ. ΠΠ°Π±ΠΈΠ²Π°Π½ΠΈΠ΅ ΠΊΡΡΠΊΠΎΠ² ΠΌΠ΅ΡΠ°Π»Π»Π° Π±ΡΠ»ΠΎ ΡΡΠ΅Π΄ΡΡΠ²ΠΎΠΌ ΠΏΡΠΈΠ΄Π°ΡΡ ΠΈΠΌ Π±ΠΎΠ»Π΅Π΅ ΠΏΠΎΠ»Π΅Π·Π½ΡΠ΅ ΡΠΎΡΠΌΡ.
ΠΡΡΡ Π½Π΅ΠΊΠΎΡΠΎΡΡΠ΅, ΠΊΡΠΎ Π²ΡΠ΅ Π΅ΡΠ΅ Π΄ΡΠΌΠ°Π΅Ρ, ΡΡΠΎ ΠΊΠΎΠ²ΠΊΠ° — ΡΡΠΎ Π½Π΅ ΡΡΠΎ ΠΈΠ½ΠΎΠ΅, ΠΊΠ°ΠΊ Β«Π½Π°Π³ΡΠ΅ΡΡ ΠΈ ΡΠ°Π·Π±ΠΈΡΡΒ» Π΄Π»Ρ ΠΏΠΎΠ»ΡΡΠ΅Π½ΠΈΡ ΡΡΡΡΡ ΠΊΠΎΠ½Π΅ΡΠ½ΡΡ ΠΏΡΠΎΠ΄ΡΠΊΡΠΎΠ². ΠΠΎΠ·ΠΌΠΎΠΆΠ½ΠΎ, ΡΡΠΎ Π±ΡΠ»Π° ΠΏΠ΅ΡΠ²ΠΎΠ½Π°ΡΠ°Π»ΡΠ½Π°Ρ ΠΊΠΎΠ½ΡΠ΅ΠΏΡΠΈΡ, Π½ΠΎ ΠΏΡΠ΅Π²ΡΠ°ΡΠ΅Π½ΠΈΠ΅ ΠΌΠ΅ΡΠ°Π»Π»Π° Π² Π²ΡΡΠΎΠΊΠΎΠΊΠ°ΡΠ΅ΡΡΠ²Π΅Π½Π½ΡΡ ΠΏΡΠΎΠ΄ΡΠΊΡΠΈΡ Π±ΡΠ»ΠΎ ΠΎΡΠ»ΠΈΡΠΈΡΠ΅Π»ΡΠ½ΠΎΠΉ ΡΠ΅ΡΡΠΎΠΉ ΡΠΈΠ²ΠΈΠ»ΠΈΠ·Π°ΡΠΈΠΈ Π½Π° ΠΏΡΠΎΡΡΠΆΠ΅Π½ΠΈΠΈ ΡΡΡΡΡΠ΅Π»Π΅ΡΠΈΠΉ.
ΠΠ΅ΡΠ°Π»Π»ΡΡΠ³ΠΈΡ
ΠΠ΅ΡΠ°Π»Π»ΡΡΠ³ΠΈΡ, ΡΠ°ΠΊΠΆΠ΅ Π½Π°Π·ΡΠ²Π°Π΅ΠΌΠ°Ρ ΠΊΡΠ·Π½Π΅ΡΠ½ΡΠΌ Π΄Π΅Π»ΠΎΠΌ, Π±ΡΠ»Π° Π²Π°ΠΆΠ½ΡΠΌ Π·Π°Π½ΡΡΠΈΠ΅ΠΌ.Π’Π΅, ΠΊΡΠΎ ΡΠΌΠ΅Π» ΠΊΡΠ·Π½Π΅ΡΠ½ΡΠΌ Π΄Π΅Π»ΠΎΠΌ, ΡΠΌΠ΅Π»ΠΎ Π·Π°Π½ΠΈΠΌΠ°Π»ΠΈΡΡ ΡΠ΅ΠΌΠ΅ΡΠ»ΠΎΠΌ, ΠΈΠΌΠ΅Ρ ΡΡΠ°ΡΡΡ Π² ΡΠ²ΠΎΠΈΡ ΠΎΠ±ΡΠΈΠ½Π°Ρ . ΠΠΎΠ»ΠΈΡΠ΅ΡΡΠ²ΠΎ Π»ΡΠ΄Π΅ΠΉ Ρ ΡΠ°ΠΌΠΈΠ»ΠΈΠ΅ΠΉ Β«Π‘ΠΌΠΈΡΒ» ΠΈ Π΅Π΅ ΡΠΊΠ²ΠΈΠ²Π°Π»Π΅Π½ΡΠΎΠΌ Π½Π° Π΄ΡΡΠ³ΠΈΡ ΡΠ·ΡΠΊΠ°Ρ ΠΎΡΡΠ°ΠΆΠ°Π΅Ρ ΠΊΠΎΠ»ΠΈΡΠ΅ΡΡΠ²ΠΎ Π»ΡΠ΄Π΅ΠΉ, ΠΊΠΎΠ³Π΄Π°-ΡΠΎ Π·Π°Π½ΠΈΠΌΠ°Π²ΡΠΈΡ ΡΡ ΠΎΠ±ΡΠ°Π±ΠΎΡΠΊΠΎΠΉ ΠΌΠ΅ΡΠ°Π»Π»ΠΎΠ², ΠΈ Π²Π°ΠΆΠ½ΠΎΡΡΡ ΡΠ΅Ρ , ΠΊΡΠΎ ΠΎΠ±Π»Π°Π΄Π°Π» ΡΠΏΠ΅ΡΠΈΠ°Π»ΡΠ½ΡΠΌΠΈ Π·Π½Π°Π½ΠΈΡΠΌΠΈ ΠΈ Π½Π°Π²ΡΠΊΠ°ΠΌΠΈ.
ΠΠΎΠ³Π΄Π° Π±ΠΎΠ»ΡΡΠΈΠ½ΡΡΠ²ΠΎ Π»ΡΠ΄Π΅ΠΉ ΠΏΡΠΎΡΡΡ ΠΏΡΠ΅Π΄ΡΡΠ°Π²ΠΈΡΡ ΡΠ΅Π±Π΅ ΠΊΠΎΠ²ΠΊΡ, ΠΏΠΎΡΠ²Π»ΡΠ΅ΡΡΡ ΠΈΠ·ΠΎΠ±ΡΠ°ΠΆΠ΅Π½ΠΈΠ΅ ΠΊΡΠ΅ΠΏΠΊΠΎΠ³ΠΎ ΠΊΡΠ·Π½Π΅ΡΠ° Π² ΡΠ΅ΠΌΠ½ΠΎΠΉ ΠΈ ΠΎΠ³Π½Π΅Π½Π½ΠΎΠΉ ΠΊΡΠ·Π½ΠΈΡΠ΅, Π΄Π΅ΡΠΆΠ°ΡΠ΅Π³ΠΎ ΠΌΠΎΠ»ΠΎΡΠΎΠΊ, ΡΡΠΎΠ±Ρ ΡΡΡΡΠ°ΡΡ ΠΏΠΎ ΡΠ°ΡΠΊΠ°Π»Π΅Π½Π½ΠΎΠΌΡ ΠΌΠ΅ΡΠ°Π»Π»Ρ ΠΏΠΎ ΡΡΠ°ΡΠΎΠΌΠΎΠ΄Π½ΠΎΠΉ Π½Π°ΠΊΠΎΠ²Π°Π»ΡΠ½Π΅ — Π»Π΅ΡΡΡ ΠΈΡΠΊΡΡ.Π ΡΠΎ Π²ΡΠ΅ΠΌΡ ΠΊΠ°ΠΊ ΠΊΡΠ·Π½Π΅ΡΡ ΠΈ ΠΌΠ°ΡΡΠ΅ΡΠ° ΠΏΠΎ ΠΌΠ΅ΡΠ°Π»Π»Ρ Π²ΡΠ΅ Π΅ΡΠ΅ Π·Π°Π½ΠΈΠΌΠ°ΡΡΡΡ ΡΠ΅ΠΌΠ΅ΡΠ»ΠΎΠΌ, ΠΊΠΎΠ²ΠΊΠ° Ρ ΠΌΠΎΠ»ΠΎΡΠΊΠ°ΠΌΠΈ Π²ΡΡΠ»Π° Π΄Π°Π»Π΅ΠΊΠΎ Π·Π° ΡΠ°ΠΌΠΊΠΈ ΡΡΠΈΡ ΠΎΡΠΈΠ³ΠΈΠ½Π°Π»ΡΠ½ΡΡ ΠΏΡΠΎΡΠ΅ΡΡΠΎΠ². ΠΠ°ΡΠΈ ΠΏΠ΅ΡΠ΅Π΄ΠΎΠ²ΡΠ΅ ΡΠ΅Ρ Π½ΠΎΠ»ΠΎΠ³ΠΈΠΈ ΠΈ ΠΌΠ΅ΡΠΎΠ΄Ρ — ΡΡΠΎ ΡΠ°ΠΊΠΈΠ΅, ΠΊΠΎΡΠΎΡΡΠ΅ Π½ΠΈ ΠΎΠ΄ΠΈΠ½ ΠΊΡΠ·Π½Π΅Ρ Π΄Π°ΠΆΠ΅ 100 Π»Π΅Ρ Π½Π°Π·Π°Π΄ Π½Π΅ ΠΌΠΎΠ³ ΡΠ΅Π±Π΅ ΠΏΡΠ΅Π΄ΡΡΠ°Π²ΠΈΡΡ.
ΠΡ ΠΏΠ°ΡΠΎΠ²ΡΡ ΠΊΡΠ·Π½ΠΈΡ ΡΠΏΠΎΡ ΠΈ ΠΏΡΠΎΠΌΡΡΠ»Π΅Π½Π½ΠΎΠΉ ΡΠ΅Π²ΠΎΠ»ΡΡΠΈΠΈ ΠΏΡΠΎΠΌΡΡΠ»Π΅Π½Π½ΠΎΡΡΡ ΠΏΠ΅ΡΠ΅ΡΠ»Π° ΠΊ Π²ΡΡΠΎΠΊΠΎΠ°Π²ΡΠΎΠΌΠ°ΡΠΈΠ·ΠΈΡΠΎΠ²Π°Π½Π½ΠΎΠΌΡ ΠΎΠ±ΠΎΡΡΠ΄ΠΎΠ²Π°Π½ΠΈΡ. Π ΠΎΡΡΠ°ΡΠ»ΠΈ ΠΏΠΎΡΡΠΎΡΠ½Π½ΠΎ ΡΠ°Π·Π²ΠΈΠ²Π°ΡΡΡΡ ΡΠΏΠ»Π°Π²Ρ ΠΈ ΠΊΠΎΠ²Π°Π½ΡΠ΅ ΠΊΠΎΠΌΠΏΠΎΠ·ΠΈΡΡ, Π° ΡΠ°ΠΊΠΆΠ΅ Π²Π΅Π΄Π΅ΡΡΡ ΠΊΠΎΠΌΠΏΡΡΡΠ΅ΡΠ½ΠΎΠ΅ ΠΌΠΎΠ΄Π΅Π»ΠΈΡΠΎΠ²Π°Π½ΠΈΠ΅ ΠΈ ΡΠΈΠΌΡΠ»ΡΡΠΈΡ, ΡΡΠΎΠ±Ρ ΡΡΠΊΠΎΡΠΈΡΡ ΠΈ ΠΎΠ±Π»Π΅Π³ΡΠΈΡΡ ΠΏΡΠΎΠ΅ΠΊΡΠΈΡΠΎΠ²Π°Π½ΠΈΠ΅ ΠΈ ΠΏΡΠΎΠ΅ΠΊΡΠΈΡΠΎΠ²Π°Π½ΠΈΠ΅.ΠΠΎΠ»ΡΡΠΈΠ½ΡΡΠ²ΠΎ ΠΊΡΠ·Π½ΠΈΡ ΡΠ΅Π³ΠΎΠ΄Π½Ρ Π±ΠΎΠ»ΡΡΠ΅ Π½Π΅ ΠΏΠΎΡ ΠΎΠΆΠΈ Π½Π° ΡΠ΅ΠΌΠ½ΡΠ΅ ΠΏΠ΅ΡΠ΅ΡΡ Ρ ΠΈΠ·ΡΡΠ³Π°ΡΡΠΈΠΌΠΈ ΠΏΠ»Π°ΠΌΠ΅Π½Π΅ΠΌ ΠΏΠ΅ΡΠ°ΠΌΠΈ.
Β«Π€Π°Π±ΡΠΈΠΊΠΈ Π±ΡΠ΄ΡΡΠ΅Π³ΠΎΒ»
Π‘Π΅Π³ΠΎΠ΄Π½Ρ ΠΊΠΎΠ²ΠΊΠ° Π²ΡΠΏΠΎΠ»Π½ΡΠ΅ΡΡΡ Π½Π° ΡΠ°Π±ΡΠΈΠΊΠ°Ρ , ΠΊΠΎΡΠΎΡΡΠ΅ ΠΌΠΎΠ³ΡΡ Π½Π°ΠΏΠΎΠΌΠΈΠ½Π°ΡΡ Π»ΡΠ±ΡΠ΅ ΠΏΠ΅ΡΠ΅Π΄ΠΎΠ²ΡΠ΅ ΠΏΡΠΎΠΈΠ·Π²ΠΎΠ΄ΡΡΠ²Π΅Π½Π½ΡΠ΅ ΠΌΠΎΡΠ½ΠΎΡΡΠΈ, ΡΠ°ΡΡΠΎ Π½Π°Π·ΡΠ²Π°Π΅ΠΌΡΠ΅ Β«ΡΠ°Π±ΡΠΈΠΊΠ°ΠΌΠΈ Π±ΡΠ΄ΡΡΠ΅Π³ΠΎΒ». ΠΠΎΠ²ΠΊΠ° ΠΏΡΠΎΠ΄Π²ΠΈΠ½ΡΠ»Π°ΡΡ Π²ΠΏΠ΅ΡΠ΅Π΄ Ρ ΡΠ΅Ρ Π½ΠΎΠ»ΠΎΠ³ΠΈΡΠΌΠΈ, ΠΏΠΎΡΠΊΠΎΠ»ΡΠΊΡ ΠΏΠΎΡΡΠ΅Π±Π½ΠΎΡΡΡ Π² ΠΈΡΡΠΈΠ½Π½ΠΎ ΠΊΠΎΠ²Π°Π½ΡΡ ΠΈΠ·Π΄Π΅Π»ΠΈΡΡ ΠΏΠΎ-ΠΏΡΠ΅ΠΆΠ½Π΅ΠΌΡ Π²ΠΎΡΡΡΠ΅Π±ΠΎΠ²Π°Π½Π° ΠΊΠ°ΠΊ Π»ΡΡΡΠΈΠ΅ ΠΊΠΎΠ²Π°Π½ΡΠ΅ Π΄Π΅ΡΠ°Π»ΠΈ Π½Π° Π·Π΅ΠΌΠ»Π΅.
ΠΠΎΡΠ΅ΠΌΡ Π΄ΡΡΠ³ΠΈΠ΅ ΠΏΡΠΎΡΠ΅ΡΡΡ ΠΏΡΠΎΠ΄ΠΎΠ»ΠΆΠ°ΡΡ Π·Π°ΡΠ²Π»ΡΡΡ ΠΎ Β«ΡΠ²ΠΎΠΉΡΡΠ²Π°Ρ ΠΊΠΎΠ²ΠΊΠΈΒ», ΡΠ΅ΠΊΠ»Π°ΠΌΠΈΡΡΡ ΠΊΠ°ΡΠ΅ΡΡΠ²ΠΎ ΡΠ²ΠΎΠ΅ΠΉ ΠΊΠΎΠ½Π΅ΡΠ½ΠΎΠΉ ΠΏΡΠΎΠ΄ΡΠΊΡΠΈΠΈ? ΠΡΠΎΡΠ΅ΡΡ Π΄Π΅ΡΠΎΡΠΌΠ°ΡΠΈΠΈ ΡΠΎΡΠΌΠΎΠ²Π°Π½ΠΈΡ ΠΈ ΡΠΎΡΠΌΠΎΠ²Π°Π½ΠΈΡ ΠΌΠ°ΡΠ΅ΡΠΈΠ°Π»ΠΎΠ², ΠΎΡΠΎΠ±Π΅Π½Π½ΠΎ ΠΌΠ΅ΡΠ°Π»Π»ΠΈΡΠ΅ΡΠΊΠΈΡ ΡΠΏΠ»Π°Π²ΠΎΠ² Π² ΡΠ²Π΅ΡΠ΄ΠΎΠΌ ΡΠΎΡΡΠΎΡΠ½ΠΈΠΈ, Π²ΡΠ·ΡΠ²Π°Π΅Ρ ΡΡΠ°Π½ΡΡΠΎΡΠΌΠ°ΡΠΈΡ ΠΌΠΈΠΊΡΠΎΡΡΡΡΠΊΡΡΡΡ ΡΠΏΠΎΡΠΎΠ±Π°ΠΌΠΈ, Ρ ΠΊΠΎΡΠΎΡΡΠΌΠΈ Π½Π΅ ΠΌΠΎΠΆΠ΅Ρ ΡΡΠ°Π²Π½ΠΈΡΡΡΡ Π½ΠΈ ΠΎΠ΄ΠΈΠ½ Π΄ΡΡΠ³ΠΎΠΉ ΠΏΡΠΎΡΠ΅ΡΡ.ΠΠ±ΡΡΠ½Π°Ρ Π°Π½Π°Π»ΠΎΠ³ΠΈΡ — Π·Π°ΠΌΠ΅ΡΠΈΠ²Π°Π½ΠΈΠ΅ ΡΠ΅ΡΡΠ° Π΄Π»Ρ ΠΏΠ΅ΡΠ΅ΠΌΠ΅ΡΠΈΠ²Π°Π½ΠΈΡ ΠΈ ΠΏΡΠ΅ΠΎΠ±ΡΠ°Π·ΠΎΠ²Π°Π½ΠΈΡ ΡΠΎΡΡΠ°Π²Π»ΡΡΡΠΈΡ ΠΌΠ°ΡΠ΅ΡΠΈΠ°Π»ΠΎΠ².
Π Π°Π±ΠΎΡΠ΅Π΅ ΡΠ΅ΡΡΠΎ, ΠΊΠ°ΠΊ ΠΈ ΠΎΠ±ΡΠ°Π±ΠΎΡΠΊΠ° ΠΌΠ΅ΡΠ°Π»Π»Π°, ΠΏΡΠ΅Π΄Π½Π°Π·Π½Π°ΡΠ΅Π½ΠΎ Π½Π΅ ΡΠΎΠ»ΡΠΊΠΎ Π΄Π»Ρ ΠΏΡΠΈΠ΄Π°Π½ΠΈΡ Π΅ΠΌΡ ΠΎΠΏΡΠ΅Π΄Π΅Π»Π΅Π½Π½ΠΎΠΉ ΡΠΎΡΠΌΡ, Π½ΠΎ ΠΈ Π΄Π»Ρ ΡΠ»ΡΡΡΠ΅Π½ΠΈΡ ΠΌΠ°ΡΠ΅ΡΠΈΠ°Π»Π° Π΄Π»Ρ ΠΈΡΠΏΠΎΠ»ΡΠ·ΠΎΠ²Π°Π½ΠΈΡ ΠΏΠΎ Π½Π°Π·Π½Π°ΡΠ΅Π½ΠΈΡ. Π’Π²Π΅ΡΠ΄ΠΎΡΠ΅Π»ΡΠ½Π°Ρ Π΄Π΅ΡΠΎΡΠΌΠ°ΡΠΈΡ ΠΏΠΎΠΊΠΎΠ²ΠΊΠΈ ΡΠ»ΡΡΡΠ°Π΅Ρ ΡΠ²ΠΎΠΉΡΡΠ²Π° ΠΌΠ΅ΡΠ°Π»Π»ΠΈΡΠ΅ΡΠΊΠΈΡ ΡΠΏΠ»Π°Π²ΠΎΠ². ΠΡΠΎΡΠ½ΠΎΡΡΡ ΠΈ Π΄ΠΎΠ»Π³ΠΎΠ²Π΅ΡΠ½ΠΎΡΡΡ, Π²ΡΡΠ°ΠΆΠ΅Π½Π½ΡΠ΅ ΠΊΠ°ΠΊ ΡΠ΄Π°ΡΠ½Π°Ρ Π²ΡΠ·ΠΊΠΎΡΡΡ ΠΈ ΡΡΡΠ°Π»ΠΎΡΡΠ½ΡΠ΅ ΡΠ²ΠΎΠΉΡΡΠ²Π°, ΡΠ²Π»ΡΡΡΡΡ ΠΊΠ»ΡΡΠ΅Π²ΡΠΌΠΈ ΠΏΡΠ΅ΠΈΠΌΡΡΠ΅ΡΡΠ²Π°ΠΌΠΈ, Π½Π΅ΠΎΠ±Ρ ΠΎΠ΄ΠΈΠΌΡΠΌΠΈ Π΄Π»Ρ Π»ΡΠ±ΠΎΠ³ΠΎ ΡΠ»Π΅ΠΌΠ΅Π½ΡΠ°, ΠΊΠΎΡΠΎΡΡΠΉ Π±ΡΠ΄Π΅Ρ ΠΈΡΠΏΠΎΠ»ΡΠ·ΠΎΠ²Π°ΡΡΡΡ Π² ΠΊΡΠΈΡΠΈΡΠ΅ΡΠΊΠΈ Π²Π°ΠΆΠ½ΡΡ Π΄Π»Ρ Π±Π΅Π·ΠΎΠΏΠ°ΡΠ½ΠΎΡΡΠΈ ΠΎΠ±Π»Π°ΡΡΡΡ . ΠΠ±Π΅ΡΠΏΠ΅ΡΠ΅Π½ΠΈΠ΅ ΠΌΠ°ΠΊΡΠΈΠΌΠ°Π»ΡΠ½ΡΡ ΠΌΠ΅ΡΠ°Π»Π»ΡΡΠ³ΠΈΡΠ΅ΡΠΊΠΈΡ ΡΠ²ΠΎΠΉΡΡΠ² — Π·Π°Π΄Π°ΡΠ°, ΠΊΠΎΡΠΎΡΡΡ ΠΊΠΎΠ²ΠΊΠ° Π±ΡΠ΄Π΅Ρ Π²ΡΠΏΠΎΠ»Π½ΡΡΡ ΠΈ Π² Π±ΡΠ΄ΡΡΠ΅ΠΌ.
Π ΡΠ½ΠΎΠΊ ΠΌΠ°ΡΠ΅ΡΠΈΠ°Π»ΠΎΠ² ΠΈ ΡΠ°ΡΠΏΡΠΎΡΡΡΠ°Π½Π΅Π½ΠΈΠ΅ Π½ΠΎΠ²ΡΡ ΡΠΏΠΎΡΠΎΠ±ΠΎΠ² ΠΎΠ±ΡΠ°Π±ΠΎΡΠΊΠΈ ΠΌΠ°ΡΠ΅ΡΠΈΠ°Π»ΠΎΠ² ΠΈ ΠΏΡΠΎΠΈΠ·Π²ΠΎΠ΄ΡΡΠ²Π° ΠΏΡΠΎΠ΄ΡΠΊΡΠΈΠΈ Π·Π½Π°ΡΠΈΡΠ΅Π»ΡΠ½ΠΎ ΡΠ°ΡΡΠΈΡΠΈΠ»ΠΈΡΡ Π·Π° ΠΏΠΎΡΠ»Π΅Π΄Π½ΠΈΠ΅ Π½Π΅ΡΠΊΠΎΠ»ΡΠΊΠΎ ΡΠΎΡΠ΅Π½ Π»Π΅Ρ. ΠΠ°ΠΆΠ΄ΡΠΉ ΠΏΡΠΎΡΠ΅ΡΡ ΠΈ ΡΠΈΠΏ ΠΌΠ°ΡΠ΅ΡΠΈΠ°Π»Π° Π·Π°Π½ΡΠ»ΠΈ ΡΠ²ΠΎΡ Π½ΠΈΡΡ ΠΏΡΠΎΠ΄ΡΠΊΡΠ° ΠΈΠ»ΠΈ ΠΏΡΠΎΡΠ΅ΡΡΠ°. Π‘ΡΠΎΠΈΠΌΠΎΡΡΡ ΠΎΠ±Π΅ΡΠΏΠ΅ΡΠ΅Π½ΠΈΡ ΠΊΠΎΠ½ΠΊΡΠ΅ΡΠ½ΠΎΠ³ΠΎ ΠΏΡΠ΅ΠΈΠΌΡΡΠ΅ΡΡΠ²Π° ΠΈΡΠΏΠΎΠ»ΡΠ·ΠΎΠ²Π°Π½ΠΈΡ ΠΎΠΊΠ°Π·Π°Π»Π°ΡΡ ΡΡΠΏΠ΅ΡΠ½ΠΎΠΉ Π½Π° ΡΡΠ½ΠΊΠ΅. ΠΠ½ΠΎΠ³ΠΈΠ΅ ΠΈΠ· ΡΡΠΈΡ ΠΏΡΠΎΡΠ΅ΡΡΠΎΠ² Π²ΡΡΠ΅ΡΠ½ΠΈΠ»ΠΈ ΠΊΠΎΠ²Π°Π½ΡΠ΅ ΠΈΠ·Π΄Π΅Π»ΠΈΡ, Π·Π°ΡΡΠ°Π²Π»ΡΡ ΠΌΠ½ΠΎΠ³ΠΈΡ ΠΏΠΎΠ»Π°Π³Π°ΡΡ, ΡΡΠΎ ΠΊΠΎΠ²ΠΊΠ° ΡΡΡΠ°ΡΠ΅Π²Π°Π΅Ρ.
Π Π°Π·Π²ΠΈΡΠΈΠ΅ ΡΠ΅Ρ Π½ΠΎΠ»ΠΎΠ³ΠΈΠΉ
ΠΠΎΠ»Π΅Π΅ ΠΏΠΎΠ»Π΅Π·Π½ΠΎ ΠΏΡΠΈΠ·Π½Π°ΡΡ ΡΡΠΎ ΠΊΠ°ΠΊ ΠΏΡΠΎΠ΄ΠΎΠ»ΠΆΠ°ΡΡΡΡΡΡ ΡΠ²ΠΎΠ»ΡΡΠΈΡ ΡΠ΅Ρ Π½ΠΎΠ»ΠΎΠ³ΠΈΠΉ.ΠΡΠΎ ΠΊΠ°ΡΠ°Π΅ΡΡΡ Π½Π΅ ΡΠΎΠ»ΡΠΊΠΎ ΠΈΠ·Π΄Π΅Π»ΠΈΠΉ, ΠΊΠΎΡΠΎΡΡΠ΅ ΡΡΠ°Π΄ΠΈΡΠΈΠΎΠ½Π½ΠΎ Π²ΡΠΊΠΎΠ²ΡΠ²Π°Π»ΠΈ, Π½ΠΎ ΠΈ ΠΈΠ·Π΄Π΅Π»ΠΈΠΉ, ΠΊΠΎΠ³Π΄Π°-ΡΠΎ Π²ΡΡΠ΅Π·Π°Π½Π½ΡΡ ΠΈΠ· ΠΊΠΎΡΡΠΈ, Π΄Π΅ΡΠ΅Π²Π° ΠΈΠ»ΠΈ ΠΊΠ°ΠΌΠ½Ρ, ΠΈΠ·Π΄Π΅Π»ΠΈΠΉ, ΠΎΡΠ»ΠΈΡΡΡ ΠΈΠ· ΠΌΠ΅ΡΠ°Π»Π»Π° ΠΈΠ»ΠΈ ΡΡΠ΅ΠΊΠ»Π°, ΠΈΠ»ΠΈ ΡΠΏΡΠΎΡΠ° Π½Π° Π±ΡΠΌΠ°Π³Ρ Π΄Π»Ρ ΠΊΠ½ΠΈΠ³ ΠΈΠ»ΠΈ Π³Π°Π·Π΅ΡΠ½ΡΡ Π±ΡΠΌΠ°Π³Ρ. ΠΠΎΠ²ΡΠ΅ ΠΏΡΠΎΠΈΠ·Π²ΠΎΠ΄ΡΡΠ²Π΅Π½Π½ΡΠ΅ ΡΠ΅Ρ Π½ΠΎΠ»ΠΎΠ³ΠΈΠΈ Π±Π΅ΡΡΡ Π²Π΅ΡΡ ΡΠ°ΠΌ, Π³Π΄Π΅ ΡΡΠ½ΠΊΡΠΈΡ ΠΌΠΎΠΆΠ΅Ρ Π²ΡΠΏΠΎΠ»Π½ΡΡΡΡΡ Π±ΠΎΠ»Π΅Π΅ ΡΡΡΠ΅ΠΊΡΠΈΠ²Π½ΠΎ ΠΈ ΡΠ΅Π·ΡΠ»ΡΡΠ°ΡΠΈΠ²Π½ΠΎ. ΠΠΎΠ»Π΅Π΅ ΡΠΈΡΠΎΠΊΠΎ ΠΈΠ·Π²Π΅ΡΡΠ½ΡΠ΅ ΠΊΠΎΠ²Π°Π½ΡΠ΅ ΠΈΠ·Π΄Π΅Π»ΠΈΡ, Π²ΠΎΠ·ΠΌΠΎΠΆΠ½ΠΎ, Π±ΡΠ»ΠΈ Π²ΡΡΠ΅ΡΠ½Π΅Π½Ρ Ρ Π³ΠΎΠ΄Π°ΠΌΠΈ, Π½ΠΎ ΠΊΠΎΠ²ΠΊΠ° Π²ΡΠ΅ Π΅ΡΠ΅ ΠΈΡΠΏΠΎΠ»ΡΠ·ΡΠ΅ΡΡΡ Π΄Π»Ρ ΠΈΠ·Π³ΠΎΡΠΎΠ²Π»Π΅Π½ΠΈΡ ΠΊΡΠΈΡΠΈΡΠ΅ΡΠΊΠΈ Π²Π°ΠΆΠ½ΡΡ ΠΊΠΎΠΌΠΏΠΎΠ½Π΅Π½ΡΠΎΠ², Π»Π΅ΠΆΠ°ΡΠΈΡ Π² ΠΎΡΠ½ΠΎΠ²Π΅ ΠΌΠ°ΡΠΈΠ½, Π½Π° ΠΊΠΎΡΠΎΡΡΡ ΠΎΠΏΠΈΡΠ°Π΅ΡΡΡ ΡΠΈΠ²ΠΈΠ»ΠΈΠ·Π°ΡΠΈΡ.
ΠΠΎΠ²ΠΊΠ° ΠΏΠΎ-ΠΏΡΠ΅ΠΆΠ½Π΅ΠΌΡ ΡΡΠΈΡΠ°Π΅ΡΡΡ ΠΏΠ΅ΡΠ²ΠΎΠΊΠ»Π°ΡΡΠ½ΡΠΌ ΡΠ΅ΡΠΌΠΎΠΌΠ΅Ρ Π°Π½ΠΈΡΠ΅ΡΠΊΠΈΠΌ ΠΏΡΠΎΡΠ΅ΡΡΠΎΠΌ.ΠΠ΅ ΡΠΎΠ»ΡΠΊΠΎ Π΄Π»Ρ ΠΏΡΠΈΠ΄Π°Π½ΠΈΡ ΡΠΎΡΠΌΡ ΠΌΠ΅ΡΠ°Π»Π»Π°ΠΌ, ΠΌΠ΅ΡΠ°Π»Π»ΠΈΡΠ΅ΡΠΊΠΎΠΉ ΠΌΠ°ΡΡΠΈΡΠ΅ ΠΈ ΠΌΠ΅ΡΠ°Π»Π»ΠΈΡΠ΅ΡΠΊΠΈΠΌ ΠΊΠΎΠΌΠΏΠΎΠ·ΠΈΡΠΈΠΎΠ½Π½ΡΠΌ ΠΌΠ°ΡΠ΅ΡΠΈΠ°Π»Π°ΠΌ, Π½ΠΎ ΡΠ°ΠΊΠΆΠ΅ Π΄Π»Ρ ΡΠ»ΡΡΡΠ΅Π½ΠΈΡ ΠΈ ΠΏΡΠ΅ΠΎΠ±ΡΠ°Π·ΠΎΠ²Π°Π½ΠΈΡ ΠΌΠ΅ΡΠ°Π»Π»ΡΡΠ³ΠΈΡΠ΅ΡΠΊΠΎΠΉ ΡΡΡΡΠΊΡΡΡΡ. ΠΠΎΠ²ΠΊΠ° ΠΎΠ±Π΅ΡΠΏΠ΅ΡΠΈΠ²Π°Π΅Ρ ΠΊΠ°ΠΊ Π΄ΠΎΠ»Π³ΠΎΠ²Π΅ΡΠ½ΡΠ΅, Π½Π°Π΄Π΅ΠΆΠ½ΡΠ΅ ΡΠΎΡΠΌΡ ΠΊΠΎΠΌΠΏΠΎΠ½Π΅Π½ΡΠΎΠ², ΡΠ°ΠΊ ΠΈ Π½Π΅ΠΎΠ±Ρ ΠΎΠ΄ΠΈΠΌΠΎΡΡΡ Π² ΠΈΠ½ΠΆΠ΅Π½Π΅ΡΠ½ΠΎΠΉ ΠΌΠ΅ΡΠ°Π»Π»ΡΡΠ³ΠΈΠΈ Π΄Π»Ρ ΡΠ΄ΠΎΠ²Π»Π΅ΡΠ²ΠΎΡΠ΅Π½ΠΈΡ ΠΊΠΎΠ½ΠΊΡΠ΅ΡΠ½ΡΡ ΡΡΠ΅Π±ΠΎΠ²Π°Π½ΠΈΠΉ ΠΊ ΠΏΡΠΎΠ΄ΡΠΊΡΠΈΠΈ.
Π Π°Π·Π½ΠΎΠΎΠ±ΡΠ°Π·ΠΈΠ΅ ΠΌΠ°ΡΠ΅ΡΠΈΠ°Π»ΠΎΠ² ΠΈ ΠΏΡΠΎΡΠ΅ΡΡΠΎΠ², Π΄ΠΎΡΡΡΠΏΠ½ΡΡ ΠΈΠ½ΠΆΠ΅Π½Π΅ΡΠ°ΠΌ-ΠΊΠΎΠ½ΡΡΡΡΠΊΡΠΎΡΠ°ΠΌ Π΄Π»Ρ ΡΠΎΠ·Π΄Π°Π½ΠΈΡ ΠΊΠΎΠΌΠΏΠΎΠ½Π΅Π½ΡΠΎΠ² ΠΈ ΠΊΠΎΠ½ΡΡΡΡΠΊΡΠΈΠΉ, ΠΈΡΠΏΠΎΠ»ΡΠ·ΡΠ΅ΠΌΡΡ Π² ΠΏΡΠΎΠ΄ΡΠΊΡΠΈΠΈ, Π½ΠΈΠΊΠΎΠ³Π΄Π° Π½Π΅ Π±ΡΠ»ΠΎ ΡΠ°ΠΊΠΈΠΌ Π±ΠΎΠ»ΡΡΠΈΠΌ. ΠΡΠΎ Π²ΠΊΠ»ΡΡΠ°Π΅Ρ Π² ΡΠ΅Π±Ρ ΠΊΠΎΠ²ΠΊΡ, Π° ΡΠ°ΠΊΠΆΠ΅ Π²ΡΠ΅ Π΄ΡΡΠ³ΠΈΠ΅ Π΄ΠΎΡΡΡΠΏΠ½ΡΠ΅ ΡΠ΅ΠΉΡΠ°Ρ ΠΏΡΠΎΡΠ΅ΡΡΡ.
ΠΠΎΠ²ΠΊΠ° ΠΏΡΠΎΡΠ»Π° ΠΏΡΡΡ ΠΎΡ ΡΠΏΠΎΡΠΎΠ±Π° ΠΈΠ·Π³ΠΎΡΠΎΠ²Π»Π΅Π½ΠΈΡ ΠΈΠ»ΠΈ ΡΠ΅ΠΌΠΎΠ½ΡΠ° Β«ΡΠ΅Π³ΠΎ-Π½ΠΈΠ±ΡΠ΄Ρ Ρ ΠΎΡΠΎΡΠ΅Π³ΠΎΒ» Π΄ΠΎ ΠΎΠ΄Π½ΠΎΠ³ΠΎ ΠΈΠ· Π΄Π΅ΡΡΡΠΊΠΎΠ² ΡΠΏΠΎΡΠΎΠ±ΠΎΠ² ΠΈΠ·Π³ΠΎΡΠΎΠ²Π»Π΅Π½ΠΈΡ ΠΆΠ΅Π»Π°Π΅ΠΌΠΎΠ³ΠΎ ΠΎΠ±ΡΠ΅ΠΊΡΠ°. ΠΠΎ ΠΌΠ΅ΡΠ΅ ΡΠ°ΡΡΠΈΡΠ΅Π½ΠΈΡ ΡΡΠ½ΠΊΠ° ΠΌΠ°ΡΠ΅ΡΠΈΠ°Π»ΠΎΠ² ΠΊΠΎΠ²ΠΊΠ° ΠΎΡΡΠ°Π΅ΡΡΡ ΠΎΠ΄Π½ΠΈΠΌ ΠΈΠ· Π²Π°ΠΆΠ½Π΅ΠΉΡΠΈΡ ΠΌΠ΅ΡΠΎΠ΄ΠΎΠ² ΠΏΡΠ΅Π²ΡΠ°ΡΠ΅Π½ΠΈΡ ΡΡΡΡΡ Π² ΡΠ°ΠΌΡΠ΅ Π½Π°Π΄Π΅ΠΆΠ½ΡΠ΅, Π΄ΠΎΠ»Π³ΠΎΠ²Π΅ΡΠ½ΡΠ΅, ΠΌΠ΅ΡΠ°Π»Π»ΡΡΠ³ΠΈΡΠ΅ΡΠΊΠΈ Π±Π΅Π·ΡΠΏΡΠ΅ΡΠ½ΡΠ΅ Π΄Π΅ΡΠ°Π»ΠΈ, Π΄Π΅ΡΠ°Π»ΠΈ ΠΈ ΠΊΠΎΠΌΠΏΠΎΠ½Π΅Π½ΡΡ. Π‘ΠΎΠ²ΡΠ΅ΠΌΠ΅Π½Π½Π°Ρ ΠΊΠΎΠ²ΠΊΠ° ΠΏΠΎΠ·Π²ΠΎΠ»ΡΠ΅Ρ Π½Π°ΠΌ ΡΠ²Π΅ΡΠ΅Π½Π½ΠΎ ΡΠΎΠ·Π΄Π°Π²Π°ΡΡ ΠΈ ΠΈΠ·Π³ΠΎΡΠ°Π²Π»ΠΈΠ²Π°ΡΡ ΠΈΠ·Π΄Π΅Π»ΠΈΡ.
Π§ΡΠΎ ΡΠ°ΠΊΠΎΠ΅ ΠΏΡΠΎΡΠ΅ΡΡ ΠΊΠΎΠ²ΠΊΠΈ, ΠΎΠΏΠ΅ΡΠ°ΡΠΈΡ, ΡΠΈΠΏΡ, ΠΏΡΠΈΠΌΠ΅Π½Π΅Π½ΠΈΠ΅, ΠΏΡΠ΅ΠΈΠΌΡΡΠ΅ΡΡΠ²Π° ΠΈ Π½Π΅Π΄ΠΎΡΡΠ°ΡΠΊΠΈ?
Π‘Π΅Π³ΠΎΠ΄Π½Ρ ΠΌΡ ΡΠ·Π½Π°Π΅ΠΌ, ΡΡΠΎ ΡΠ°ΠΊΠΎΠ΅ ΠΊΠΎΠ²ΠΊΠ° ΠΈ Π²ΠΈΠ΄Ρ ΠΊΠΎΠ²ΠΊΠΈ.ΠΠ°Π»Π΅Π΅ ΠΌΡ ΠΏΠΎΠ³ΠΎΠ²ΠΎΡΠΈΠΌ ΠΎ ΡΠ°Π±ΠΎΡΠ΅, ΠΏΡΠΈΠΌΠ΅Π½Π΅Π½ΠΈΠΈ, ΠΏΡΠ΅ΠΈΠΌΡΡΠ΅ΡΡΠ²Π°Ρ ΠΈ Π½Π΅Π΄ΠΎΡΡΠ°ΡΠΊΠ°Ρ ΡΡΠΎΠ³ΠΎ ΠΏΡΠΎΡΠ΅ΡΡΠ°. ΠΠΎΠ²ΠΊΠ° — ΡΡΠΎ ΠΏΡΠΎΡΠ΅ΡΡ ΡΠΎΡΠΌΠΎΠ²ΠΊΠΈ ΠΌΠ΅ΡΠ°Π»Π»Π° , Π² ΠΊΠΎΡΠΎΡΠΎΠΌ ΠΌΠ΅ΡΠ°Π»Π» Π½Π°Π³ΡΠ΅Π²Π°ΡΡ ΠΈ ΠΏΡΠΈΠΊΠ»Π°Π΄ΡΠ²Π°ΡΡ ΡΠΈΠ»Ρ ΡΠ°ΠΊΠΈΠΌ ΠΎΠ±ΡΠ°Π·ΠΎΠΌ, ΡΡΠΎΠ±Ρ ΠΌΠΎΠΆΠ½ΠΎ Π±ΡΠ»ΠΎ ΠΏΠΎΠ»ΡΡΠΈΡΡ ΡΡΠ΅Π±ΡΠ΅ΠΌΡΡ ΡΠΎΡΠΌΡ. ΠΠΎ ΡΡΡΠΈ, ΡΡΠΎ ΠΏΡΠΎΡΠ΅ΡΡ Π³ΠΎΡΡΡΠ΅ΠΉ ΠΎΠ±ΡΠ°Π±ΠΎΡΠΊΠΈ , Π² ΠΊΠΎΡΠΎΡΠΎΠΌ Π·Π°Π³ΠΎΡΠΎΠ²ΠΊΠ° Π½Π°Π³ΡΠ΅Π²Π°Π΅ΡΡΡ Π΄ΠΎ ΠΏΠ»Π°ΡΡΠΈΡΠ΅ΡΠΊΠΎΠΉ ΡΡΠ°Π΄ΠΈΠΈ ΠΈ ΡΡΠΈΠ»ΠΈΠ΅ ΠΏΡΠΈΠΊΠ»Π°Π΄ΡΠ²Π°Π΅ΡΡΡ Π²ΡΡΡΠ½ΡΡ ΠΈΠ»ΠΈ Ρ ΠΏΠΎΠΌΠΎΡΡΡ ΠΏΡΠ΅ΡΡΠ° Π² Π·Π°Π²ΠΈΡΠΈΠΌΠΎΡΡΠΈ ΠΎΡ ΡΡΠ΅Π±ΠΎΠ²Π°Π½ΠΈΠΉ. ΠΡΠ° ΡΠΈΠ»Π° ΡΠ²Π»ΡΠ΅ΡΡΡ ΡΠΆΠΈΠΌΠ°ΡΡΠ΅ΠΉ ΠΏΠΎ ΡΠ²ΠΎΠ΅ΠΉ ΠΏΡΠΈΡΠΎΠ΄Π΅, ΡΡΠΎ ΡΠ²Π»ΡΠ΅ΡΡΡ ΠΎΡΠ½ΠΎΠ²Π½ΡΠΌ ΡΡΠ΅Π±ΠΎΠ²Π°Π½ΠΈΠ΅ΠΌ ΠΊΠΎΠ²ΠΊΠΈ.ΠΠ½ΠΎΠ³Π΄Π° ΠΊΠΎΠ²ΠΊΠ° Π²ΡΠΏΠΎΠ»Π½ΡΠ΅ΡΡΡ Π±Π΅Π· ΠΏΡΠΈΠΌΠ΅Π½Π΅Π½ΠΈΡ ΡΠ΅ΠΏΠ»Π°, ΡΡΠΎ Π½Π°Π·ΡΠ²Π°Π΅ΡΡΡ Ρ ΠΎΠ»ΠΎΠ΄Π½ΠΎΠΉ ΠΊΠΎΠ²ΠΊΠΎΠΉ. Π Π½Π°ΡΠΈ Π΄Π½ΠΈ ΠΊΠΎΠ²ΠΊΠ° ΠΈΡΠΏΠΎΠ»ΡΠ·ΡΠ΅ΡΡΡ Π²ΠΎ Π²ΡΠ΅Ρ ΠΎΡΡΠ°ΡΠ»ΡΡ ΠΎΠ±ΡΠ°Π±Π°ΡΡΠ²Π°ΡΡΠ΅ΠΉ ΠΏΡΠΎΠΌΡΡΠ»Π΅Π½Π½ΠΎΡΡΠΈ.Π§ΡΠΎ ΡΠ°ΠΊΠΎΠ΅ ΠΏΡΠΎΡΠ΅ΡΡ ΠΊΠΎΠ²ΠΊΠΈ?
ΠΠΏΠ΅ΡΠ°ΡΠΈΡ:
Π ΠΎΡΠ½ΠΎΠ²Π½ΠΎΠΌ ΠΊΠΎΠ²ΠΊΠ° ΡΠΎΡΡΠΎΠΈΡ ΠΈΠ· Π΄Π²ΡΡ ΠΎΠΏΠ΅ΡΠ°ΡΠΈΠΉ Π² Π·Π°Π²ΠΈΡΠΈΠΌΠΎΡΡΠΈ ΠΎΡ ΠΏΡΠΈΠ»ΠΎΠΆΠ΅Π½Π½ΠΎΠΉ ΡΠΈΠ»Ρ.
1.) ΠΡΡΡΠΆΠΊΠ°:
ΠΡΡΡΠΆΠΊΠ° — ΡΡΠΎ ΠΏΡΠΎΡΠ΅ΡΡ ΡΠ²Π΅Π»ΠΈΡΠ΅Π½ΠΈΡ Π΄Π»ΠΈΠ½Ρ ΠΈ ΡΠΌΠ΅Π½ΡΡΠ΅Π½ΠΈΡ ΠΏΠ»ΠΎΡΠ°Π΄ΠΈ ΠΏΠΎΠΏΠ΅ΡΠ΅ΡΠ½ΠΎΠ³ΠΎ ΡΠ΅ΡΠ΅Π½ΠΈΡ Π·Π°Π³ΠΎΡΠΎΠ²ΠΊΠΈ. ΠΡΠΎΡΡΠΎ Π² ΡΡΠΎΠΉ ΠΎΠΏΠ΅ΡΠ°ΡΠΈΠΈ Π΄Π»ΠΈΠ½Π° Π·Π°Π³ΠΎΡΠΎΠ²ΠΊΠΈ ΡΠ²Π΅Π»ΠΈΡΠΈΠ²Π°Π΅ΡΡΡ, Π° ΠΏΠ»ΠΎΡΠ°Π΄Ρ ΠΏΠΎΠΏΠ΅ΡΠ΅ΡΠ½ΠΎΠ³ΠΎ ΡΠ΅ΡΠ΅Π½ΠΈΡ ΡΠΌΠ΅Π½ΡΡΠ°Π΅ΡΡΡ.Π ΡΡΠΎΠΌ ΠΏΡΠΎΡΠ΅ΡΡΠ΅ ΡΠΆΠΈΠΌΠ°ΡΡΠ°Ρ ΡΠΈΠ»Π° ΠΏΡΠΈΠΊΠ»Π°Π΄ΡΠ²Π°Π΅ΡΡΡ ΠΏΠ΅ΡΠΏΠ΅Π½Π΄ΠΈΠΊΡΠ»ΡΡΠ½ΠΎ Π΅Π³ΠΎ ΠΏΡΠΎΠ΄ΠΎΠ»ΡΠ½ΠΎΠΉ ΠΎΡΠΈ. ΠΡΠ»ΠΈ ΡΠ°ΡΡΡΠ³ΠΈΠ²Π°ΡΡΠ΅Π΅ ΡΡΠΈΠ»ΠΈΠ΅ ΠΏΡΠΈΠΌΠ΅Π½ΡΠ΅ΡΡΡ Π΄Π»Ρ ΠΈΠ·ΠΌΠ΅Π½Π΅Π½ΠΈΡ Π΅Π³ΠΎ Π΄Π»ΠΈΠ½Ρ ΠΏΠ°ΡΠ°Π»Π»Π΅Π»ΡΠ½ΠΎ Π΅Π³ΠΎ ΠΎΡΠΈ Π΄Π»ΠΈΠ½Ρ, ΡΡΠΎΡ ΠΏΡΠΎΡΠ΅ΡΡ ΠΈΠ·Π²Π΅ΡΡΠ΅Π½ ΠΊΠ°ΠΊ Π²ΠΎΠ»ΠΎΡΠ΅Π½ΠΈΠ΅ ΠΏΡΠΎΠ²ΠΎΠ»ΠΎΠΊΠΈ.
2.) ΠΡΠ°Π΄ΠΊΠ°:
ΠΡΠ°Π΄ΠΊΠ° — ΡΡΠΎ ΠΎΠΏΠ΅ΡΠ°ΡΠΈΡ, ΠΏΡΡΠΌΠΎ ΠΏΡΠΎΡΠΈΠ²ΠΎΠΏΠΎΠ»ΠΎΠΆΠ½Π°Ρ ΠΎΠΏΡΡΠΊΠ°Π½ΠΈΡ. ΠΡΠΈ ΡΡΠΎΠΉ ΠΎΠΏΠ΅ΡΠ°ΡΠΈΠΈ Π΄Π»ΠΈΠ½Π° Π·Π°Π³ΠΎΡΠΎΠ²ΠΊΠΈ ΡΠΌΠ΅Π½ΡΡΠ°Π΅ΡΡΡ, Π° ΠΏΠ»ΠΎΡΠ°Π΄Ρ Π΅Π΅ ΠΏΠΎΠΏΠ΅ΡΠ΅ΡΠ½ΠΎΠ³ΠΎ ΡΠ΅ΡΠ΅Π½ΠΈΡ ΡΠ²Π΅Π»ΠΈΡΠΈΠ²Π°Π΅ΡΡΡ. Π ΡΡΠΎΠΌ ΠΏΡΠΎΡΠ΅ΡΡΠ΅ ΡΠΆΠΈΠΌΠ°ΡΡΠ°Ρ ΡΠΈΠ»Π° ΠΏΡΠΈΠ»Π°Π³Π°Π΅ΡΡΡ Π² Π½Π°ΠΏΡΠ°Π²Π»Π΅Π½ΠΈΠΈ, ΠΏΠ°ΡΠ°Π»Π»Π΅Π»ΡΠ½ΠΎΠΌ Π΅Π³ΠΎ ΠΏΡΠΎΠ΄ΠΎΠ»ΡΠ½ΠΎΠΉ ΠΎΡΠΈ.
Π’ΠΈΠΏΡ ΠΊΠΎΠ²ΠΊΠΈ:
ΠΠΎΠ²ΠΊΠΈ ΠΌΠΎΠΆΠ½ΠΎ ΡΠ°Π·Π΄Π΅Π»ΠΈΡΡ Π½Π° ΡΠ»Π΅Π΄ΡΡΡΠΈΠ΅ Π²ΠΈΠ΄Ρ.
1.) Π ΡΠΎΠΎΡΠ²Π΅ΡΡΡΠ²ΠΈΠΈ Ρ ΡΠ΅ΠΌΠΏΠ΅ΡΠ°ΡΡΡΠΎΠΉ:
a.) ΠΠΎΡΡΡΠ°Ρ ΡΡΠ°ΠΌΠΏΠΎΠ²ΠΊΠ°:
ΠΡΠ»ΠΈ Π·Π°Π³ΠΎΡΠΎΠ²ΠΊΠ° Π½Π°Π³ΡΠ΅Π²Π°Π΅ΡΡΡ Π²ΡΡΠ΅ ΡΠ΅ΠΌΠΏΠ΅ΡΠ°ΡΡΡΡ ΡΠ΅ΠΊΡΠΈΡΡΠ°Π»Π»ΠΈΠ·Π°ΡΠΈΠΈ, Π° Π·Π°ΡΠ΅ΠΌ ΠΏΡΠΈΠΊΠ»Π°Π΄ΡΠ²Π°Π΅ΡΡΡ ΡΠΈΠ»Π°, ΠΏΡΠΎΡΠ΅ΡΡ Π½Π°Π·ΡΠ²Π°Π΅ΡΡΡ Π³ΠΎΡΡΡΠ΅ΠΉ ΡΡΠ°ΠΌΠΏΠΎΠ²ΠΊΠΎΠΉ. Π’Π΅ΠΌΠΏΠ΅ΡΠ°ΡΡΡΠ° ΡΠ΅ΠΊΡΠΈΡΡΠ°Π»Π»ΠΈΠ·Π°ΡΠΈΠΈ Π±ΠΎΠ»ΡΡΠΈΠ½ΡΡΠ²Π° ΠΌΠ΅ΡΠ°Π»Π»ΠΎΠ² ΡΠΎΡΡΠ°Π²Π»ΡΠ΅Ρ ΠΏΠΎΠ»ΠΎΠ²ΠΈΠ½Ρ ΠΈΡ ΡΠ΅ΠΌΠΏΠ΅ΡΠ°ΡΡΡΡ ΠΏΠ»Π°Π²Π»Π΅Π½ΠΈΡ.
Π±.) Π’Π΅ΠΏΠ»Π°Ρ ΠΊΠΎΠ²ΠΊΠ°:
Π’Π΅ΠΏΠ»Π°Ρ ΠΊΠΎΠ²ΠΊΠ° Π²ΡΠΏΠΎΠ»Π½ΡΠ΅ΡΡΡ ΠΏΡΠΈ ΡΠ΅ΠΌΠΏΠ΅ΡΠ°ΡΡΡΠ΅ ΠΏΡΠΈΠΌΠ΅ΡΠ½ΠΎ 40 ΠΏΡΠΎΡΠ΅Π½ΡΠΎΠ² ΠΎΡ ΡΠ΅ΠΌΠΏΠ΅ΡΠ°ΡΡΡΡ ΠΏΠ»Π°Π²Π»Π΅Π½ΠΈΡ.
c.) Π₯ΠΎΠ»ΠΎΠ΄Π½Π°Ρ ΡΡΠ°ΠΌΠΏΠΎΠ²ΠΊΠ°:
Π₯ΠΎΠ»ΠΎΠ΄Π½Π°Ρ ΡΡΠ°ΠΌΠΏΠΎΠ²ΠΊΠ° Π²ΡΠΏΠΎΠ»Π½ΡΠ΅ΡΡΡ ΠΏΡΠΈ ΠΊΠΎΠΌΠ½Π°ΡΠ½ΠΎΠΉ ΡΠ΅ΠΌΠΏΠ΅ΡΠ°ΡΡΡΠ΅. ΠΡΠΎΡ ΠΏΡΠΎΡΠ΅ΡΡ ΠΎΠ±Π΅ΡΠΏΠ΅ΡΠΈΠ²Π°Π΅Ρ ΡΠ°ΠΌΡΠ΅ Π²ΡΡΠΎΠΊΠΈΠ΅ ΠΌΠ΅Ρ Π°Π½ΠΈΡΠ΅ΡΠΊΠΈΠ΅ ΡΠ²ΠΎΠΉΡΡΠ²Π° ΡΡΠ΅Π΄ΠΈ Π²ΡΠ΅Ρ ΠΏΡΠΎΡΠ΅ΡΡΠΎΠ² ΠΊΠΎΠ²ΠΊΠΈ.
2.) Π ΡΠΎΠΎΡΠ²Π΅ΡΡΡΠ²ΠΈΠΈ Ρ ΡΠ°ΡΠΏΠΎΠ»ΠΎΠΆΠ΅Π½ΠΈΠ΅ΠΌ ΡΡΠ°ΠΌΠΏΠ°:
a.) ΠΡΠΊΡΡΡΠ°Ρ ΡΡΠ°ΠΌΠΏΠΎΠ²ΠΊΠ°:
Π ΡΡΠΎΠΌ ΠΏΡΠΎΡΠ΅ΡΡΠ΅ ΠΊΠΎΠ²ΠΊΠΈ ΠΈΡΠΏΠΎΠ»ΡΠ·ΡΡΡΡΡ ΠΏΠ»ΠΎΡΠΊΠΈΠ΅ ΡΡΠ°ΠΌΠΏΡ ΠΈΠ»ΠΈ Π±Π΅Π· ΡΡΠ°ΠΌΠΏΠ°. Π ΠΎΡΠ½ΠΎΠ²Π½ΠΎΠΌ ΡΡΠΎ ΠΏΡΠΎΡΠ΅ΡΡ Π³ΠΎΡΡΡΠ΅ΠΉ ΡΡΠ°ΠΌΠΏΠΎΠ²ΠΊΠΈ, ΠΏΡΠΈ ΠΊΠΎΡΠΎΡΠΎΠΌ Π·Π°Π³ΠΎΡΠΎΠ²ΠΊΠ° Π½Π°Π³ΡΠ΅Π²Π°Π΅ΡΡΡ ΠΈ ΠΎΠ±ΡΠ°ΡΠΈΠ²Π°Π΅ΡΡΡ Π΄Π»Ρ ΠΏΠΎΠ»ΡΡΠ΅Π½ΠΈΡ ΠΆΠ΅Π»Π°Π΅ΠΌΠΎΠΉ ΡΠΎΡΠΌΡ. ΠΡΠΎΡ ΠΏΡΠΎΡΠ΅ΡΡ ΠΏΡΠΎΠΈΠ·Π²ΠΎΠ΄ΠΈΡ Π³ΡΡΠ±ΡΠΉ ΠΏΡΠΎΠ΄ΡΠΊΡ.
Π±.) ΠΠΎΠ²ΠΊΠ° Π² Π·Π°ΠΊΡΡΡΡΡ ΡΡΠ°ΠΌΠΏΠ°Ρ :
ΠΠΎΠ²ΠΊΠ° Π² Π·Π°ΠΊΡΡΡΡΡ ΡΡΠ°ΠΌΠΏΠ°Ρ — ΡΡΠΎ ΠΏΡΠΎΡΠ΅ΡΡ, Π² ΠΊΠΎΡΠΎΡΠΎΠΌ Π½Π°Π±ΠΎΡ ΡΡΠ°ΠΌΠΏΠΎΠ²ΠΎΡΠ½ΡΡ ΡΡΠ°ΠΌΠΏΠΎΠ² ΠΈΡΠΏΠΎΠ»ΡΠ·ΡΠ΅ΡΡΡ Π΄Π»Ρ ΠΏΠΎΠ»ΡΡΠ΅Π½ΠΈΡ Π·Π°Π³ΠΎΡΠΎΠ²ΠΊΠΈ ΠΆΠ΅Π»Π°Π΅ΠΌΠΎΠΉ ΡΠΎΡΠΌΡ. Π Π±ΠΎΠ»ΡΡΠΈΠ½ΡΡΠ²Π΅ ΡΠ»ΡΡΠ°Π΅Π² ΡΡΠΈ ΠΈΠ·Π΄Π΅Π»ΠΈΡ Π½Π΅ Π½ΡΠΆΠ΄Π°ΡΡΡΡ Π² ΠΎΡΠ΄Π΅Π»ΠΊΠ΅. ΠΡΠΎΡ ΠΏΡΠΎΡΠ΅ΡΡ ΡΡΠ΅Π±ΠΎΠ²Π°Π» Π±ΠΎΠ»ΡΡΠ΅ΠΉ ΡΠΈΠ»Ρ.
3.) Π ΡΠΎΠΎΡΠ²Π΅ΡΡΡΠ²ΠΈΠΈ Ρ ΠΎΠ±ΠΎΡΡΠ΄ΠΎΠ²Π°Π½ΠΈΠ΅ΠΌ Π΄Π»Ρ ΠΊΠΎΠ²ΠΊΠΈ:
a.) ΠΠΎΠ²ΠΊΠ° Π‘ΠΌΠΈΡΠ°:
ΠΠΎΠ²ΠΊΠ° Π‘ΠΌΠΈΡΠ° — ΡΡΠ°Π΄ΠΈΡΠΈΠΎΠ½Π½ΡΠΉ ΠΌΠ΅ΡΠΎΠ΄ ΡΡΠ°ΠΌΠΏΠΎΠ²ΠΊΠΈ ΠΌΠ΅ΡΠ°Π»Π»Π°. ΠΡΠΎ ΠΌΠ΅ΡΠΎΠ΄ ΠΎΡΠΊΡΡΡΠΎΠΉ ΡΡΠ°ΠΌΠΏΠΎΠ²ΠΊΠΈ, ΠΏΡΠΈ ΠΊΠΎΡΠΎΡΠΎΠΌ Π·Π°Π³ΠΎΡΠΎΠ²ΠΊΡ ΠΏΠΎΠΌΠ΅ΡΠ°ΡΡ Π½Π° Π½Π΅ΠΏΠΎΠ΄Π²ΠΈΠΆΠ½ΡΡ ΠΎΠΏΠΎΡΡ, ΠΈ ΠΌΠΎΠ»ΠΎΡ ΡΠ΄Π°ΡΡΠ΅Ρ ΠΈ Π΄Π΅ΡΠΎΡΠΌΠΈΡΡΠ΅Ρ Π·Π°Π³ΠΎΡΠΎΠ²ΠΊΡ.Π£ΡΠΈΠ»ΠΈΠ΅ ΠΏΡΠΈΠΊΠ»Π°Π΄ΡΠ²Π°Π΅ΡΡΡ Π»ΠΈΠ±ΠΎ Π²ΡΡΡΠ½ΡΡ, Π»ΠΈΠ±ΠΎ ΠΎΡΠ±ΠΎΠΉΠ½ΡΠΌ ΠΌΠΎΠ»ΠΎΡΠΊΠΎΠΌ .b.) ΠΡΡΠΌΠ°Ρ ΡΡΠ°ΠΌΠΏΠΎΠ²ΠΊΠ°:
ΠΡΡΠΌΠ°Ρ ΡΡΠ°ΠΌΠΏΠΎΠ²ΠΊΠ° Π²ΡΠΏΠΎΠ»Π½ΡΠ΅ΡΡΡ Π² Π·Π°ΠΊΡΡΡΡΡ
ΡΡΠ°ΠΌΠΏΠ°Ρ
. ΠΠ²ΡΠΎΠΌΠ°ΡΠΈΡΠ΅ΡΠΊΠΈΠΉ ΠΌΠΎΠ»ΠΎΡ
ΠΏΡΠΈΠΌΠ΅Π½ΡΠ» ΡΠΈΠ»Ρ ΠΏΠΎΡΠ»Π΅Π΄ΠΎΠ²Π°ΡΠ΅Π»ΡΠ½ΠΎ ΡΠ΄Π°ΡΠ°ΠΌΠΈ ΠΏΡΡΠ΅ΠΌ ΠΏΠ°Π΄Π΅Π½ΠΈΡ. Π ΡΡΠΎΠΌ ΡΠΈΠΏΠ΅ ΠΈΡΠΏΠΎΠ»ΡΠ·ΡΠ΅ΡΡΡ Π²Π½Π΅Π·Π°ΠΏΠ½ΠΎ ΠΏΡΠΈΠ»ΠΎΠΆΠ΅Π½Π½Π°Ρ ΡΠΈΠ»Π°.
c.) ΠΠΎΠ²ΠΊΠ° Π½Π° ΠΏΡΠ΅ΡΡΠ΅:
ΠΠΎΠ²ΠΊΠ° Π½Π° ΠΏΡΠ΅ΡΡΠ΅ ΠΏΠΎΡ ΠΎΠΆΠ° Π½Π° ΠΏΡΡΠΌΡΡ ΠΊΠΎΠ²ΠΊΡ, Π·Π° ΠΈΡΠΊΠ»ΡΡΠ΅Π½ΠΈΠ΅ΠΌ ΡΠΎΠ³ΠΎ, ΡΡΠΎ Π² Π½Π΅ΠΉ ΠΈΡΠΏΠΎΠ»ΡΠ·ΡΠ΅ΡΡΡ ΡΠΈΠ»Π° Π½Π΅ΠΏΡΠ΅ΡΡΠ²Π½ΠΎΠ³ΠΎ ΡΠΆΠ°ΡΠΈΡ, ΠΏΡΠΈΠΊΠ»Π°Π΄ΡΠ²Π°Π΅ΠΌΠ°Ρ Π³ΠΈΠ΄ΡΠ°Π²Π»ΠΈΡΠ΅ΡΠΊΠΈΠΌ ΠΏΡΠ΅ΡΡΠΎΠΌ. ΠΡΠΎΡ ΠΏΡΠΎΡΠ΅ΡΡ ΡΠ²Π΅Π»ΠΈΡΠΈΠ²Π°Π΅Ρ Π΄Π»ΠΈΠ½Ρ ΠΈ ΡΠΌΠ΅Π½ΡΡΠ°Π΅Ρ ΠΏΠΎΠΏΠ΅ΡΠ΅ΡΠ½ΠΎΠ΅ ΡΠ΅ΡΠ΅Π½ΠΈΠ΅ Π·Π°Π³ΠΎΡΠΎΠ²ΠΊΠΈ.
d.) ΠΠ°ΡΠΈΠ½Π½Π°Ρ ΠΊΠΎΠ²ΠΊΠ°:
ΠΠ΅Ρ Π°Π½ΠΈΡΠ΅ΡΠΊΠ°Ρ ΠΊΠΎΠ²ΠΊΠ° — ΡΡΠΎ ΠΏΡΠΎΡΠ΅ΡΡ Π²ΡΡΠ°Π΄ΠΊΠΈ, ΠΏΡΠΈ ΠΊΠΎΡΠΎΡΠΎΠΌ ΠΏΠΎΠΏΠ΅ΡΠ΅ΡΠ½ΠΎΠ΅ ΡΠ΅ΡΠ΅Π½ΠΈΠ΅ Π·Π°Π³ΠΎΡΠΎΠ²ΠΊΠΈ ΡΠ²Π΅Π»ΠΈΡΠΈΠ²Π°Π΅ΡΡΡ, Π° Π΄Π»ΠΈΠ½Π° ΡΠΌΠ΅Π½ΡΡΠ°Π΅ΡΡΡ.
ΠΡΠ΅ΠΈΠΌΡΡΠ΅ΡΡΠ²Π° ΠΈ Π½Π΅Π΄ΠΎΡΡΠ°ΡΠΊΠΈ:
ΠΡΠ΅ΠΈΠΌΡΡΠ΅ΡΡΠ²Π°:
- ΠΠΎΠΊΠΎΠ²ΠΊΠ° Π΄Π°Π΅Ρ ΡΡΠ°Π²Π½ΠΈΡΠ΅Π»ΡΠ½ΠΎ Π±ΠΎΠ»Π΅Π΅ ΠΏΡΠΎΡΠ½ΡΠΉ ΠΏΡΠΎΠ΄ΡΠΊΡ ΠΏΠΎ ΡΡΠ°Π²Π½Π΅Π½ΠΈΡ Ρ Π»ΠΈΡΡΠ΅ΠΌ .
- Π£ ΠΊΡΠ·Π½Π΅ΡΠ½ΠΎΠ³ΠΎ ΠΈΠ·Π΄Π΅Π»ΠΈΡ ΠΏΠΎΠ²ΡΡΠ΅Π½Π½Π°Ρ ΡΡΡΠ°Π»ΠΎΡΡΠ½Π°Ρ ΠΏΡΠΎΡΠ½ΠΎΡΡΡ ΠΈ ΡΠΎΠΏΡΠΎΡΠΈΠ²Π»Π΅Π½ΠΈΠ΅ ΠΏΠΎΠ»Π·ΡΡΠ΅ΡΡΠΈ.
- ΠΡΠ·Π½Π΅ΡΠ½ΡΠΉ ΠΏΡΠΎΠ΄ΡΠΊΡ ΠΈΠΌΠ΅Π΅Ρ Π±ΠΎΠ»Π΅Π΅ Π²ΡΡΠΎΠΊΠΈΠ΅ ΠΌΠ΅Ρ Π°Π½ΠΈΡΠ΅ΡΠΊΠΈΠ΅ ΡΠ²ΠΎΠΉΡΡΠ²Π°.
- ΠΠΈΠ·ΠΊΠ°Ρ ΡΡΠΎΠΈΠΌΠΎΡΡΡ ΡΠΊΡΠΏΠ»ΡΠ°ΡΠ°ΡΠΈΠΈ.
- ΠΡΠΎΡ ΠΏΡΠΎΡΠ΅ΡΡ Π½Π΅ ΡΡΠ΅Π±ΡΠ΅Ρ ΡΠΏΠ΅ΡΠΈΠ°Π»ΡΠ½ΡΡ Π½Π°Π²ΡΠΊΠΎΠ² ΠΎΠΏΠ΅ΡΠ°ΡΠΎΡΠ°.
- Π‘ ΠΏΠΎΠΌΠΎΡΡΡ ΡΡΠΎΠ³ΠΎ ΠΏΡΠΎΡΠ΅ΡΡΠ° ΠΌΠΎΠΆΠ½ΠΎ ΡΠΎΡΠΌΠΈΡΠΎΠ²Π°ΡΡ ΡΠ°ΠΌΡΠ΅ ΡΠ°Π·Π½ΡΠ΅ ΡΠΎΡΠΌΡ.
ΠΠ΅Π΄ΠΎΡΡΠ°ΡΠΊΠΈ:
- ΠΠΎΠ»Π΅Π΅ Π²ΡΡΠΎΠΊΠ°Ρ Π½Π°ΡΠ°Π»ΡΠ½Π°Ρ ΡΡΠΎΠΈΠΌΠΎΡΡΡ Π΄Π»Ρ Π±ΠΎΠ»ΡΡΠΈΡ ΠΊΠΎΠ²ΠΎΡΠ½ΡΡ ΠΏΡΠ΅ΡΡΠΎΠ².
- ΠΡΠΈ Π³ΠΎΡΡΡΠ΅ΠΉ ΡΡΠ°ΠΌΠΏΠΎΠ²ΠΊΠ΅ ΡΡΠ΅Π±ΡΠ΅ΡΡΡ Π²ΡΠΎΡΠΈΡΠ½ΡΠΉ ΠΏΡΠΎΡΠ΅ΡΡ ΡΠΈΡΡΠΎΠ²ΠΎΠΉ ΠΎΠ±ΡΠ°Π±ΠΎΡΠΊΠΈ.
- ΠΠ½ Π½Π΅ ΠΌΠΎΠΆΠ΅Ρ ΠΏΡΠΎΠΈΠ·Π²ΠΎΠ΄ΠΈΡΡ ΡΠ»ΠΎΠΆΠ½ΡΠ΅ ΡΠΎΡΠΌΡ.
- Π Π°Π·ΠΌΠ΅Ρ ΠΎΠ³ΡΠ°Π½ΠΈΡΠ΅Π½ ΡΠ°Π·ΠΌΠ΅ΡΠΎΠΌ ΠΏΡΠ΅ΡΡΠ°.
- Π₯ΡΡΠΏΠΊΠΈΠΉ ΠΌΠ΅ΡΠ°Π»Π» Π½Π΅Π»ΡΠ·Ρ ΠΏΠΎΠ΄Π΄Π΅Π»Π°ΡΡ.
ΠΡΠΈΠΌΠ΅Π½Π΅Π½ΠΈΠ΅ ΠΊΠΎΠ²ΠΊΠΈ:
- Π ΠΊΠ°ΠΆΠ΄ΠΎΠΉ ΠΌΠ΅Ρ Π°Π½ΠΈΡΠ΅ΡΠΊΠΎΠΉ ΠΎΡΡΠ°ΡΠ»ΠΈ Π² ΠΎΡΠ½ΠΎΠ²Π½ΠΎΠΌ ΠΈΡΠΏΠΎΠ»ΡΠ·ΡΡΡΡΡ ΠΊΠΎΠ²Π°Π½ΡΠ΅ ΠΈΠ·Π΄Π΅Π»ΠΈΡ.
- Π ΠΎΡΠΎΡ ΡΡΡΠ±ΠΈΠ½Ρ , ΡΠΎΡΠΎΡ Π³Π΅Π½Π΅ΡΠ°ΡΠΎΡΠ° ΠΈ Ρ. Π. Π―Π²Π»ΡΡΡΡΡ ΠΊΠΎΠ²Π°Π½ΡΠΌΠΈ ΠΈΠ·Π΄Π΅Π»ΠΈΡΠΌΠΈ.
- ΠΠ½ ΠΎΠ±Π΅ΡΠΏΠ΅ΡΠΈΠ²Π°Π΅Ρ Π±ΠΎΠ»Π΅Π΅ Π²ΡΡΠΎΠΊΡΡ ΡΡΡΠ°Π»ΠΎΡΡΠ½ΡΡ ΠΏΡΠΎΡΠ½ΠΎΡΡΡ, ΠΏΠΎΡΡΠΎΠΌΡ Π±ΠΎΠ»ΡΡΠΈΠ½ΡΡΠ²ΠΎ Π΄Π²ΠΈΠΆΡΡΠΈΡ ΡΡ ΡΠ°ΡΡΠ΅ΠΉ, ΡΠ°ΠΊΠΈΡ ΠΊΠ°ΠΊ ΠΊΠΎΠ»Π΅Π½ΡΠ°ΡΡΠΉ Π²Π°Π», ΡΠ°ΡΠΏΡΠ΅Π΄Π΅Π»ΠΈΡΠ΅Π»ΡΠ½ΡΠΉ Π²Π°Π» , ΡΠ΅ΡΡΠ΅ΡΠ½ΠΈ ΠΈ Ρ. Π., ΠΠ·Π³ΠΎΡΠ°Π²Π»ΠΈΠ²Π°ΡΡΡΡ ΠΌΠ΅ΡΠΎΠ΄ΠΎΠΌ ΠΊΠΎΠ²ΠΊΠΈ.
- Π₯ΠΎΠ»ΠΎΠ΄Π½Π°Ρ ΡΡΠ°ΠΌΠΏΠΎΠ²ΠΊΠ° ΠΈΡΠΏΠΎΠ»ΡΠ·ΡΠ΅ΡΡΡ Π΄Π»Ρ ΠΏΡΠΎΠΈΠ·Π²ΠΎΠ΄ΡΡΠ²Π° ΡΡΠ°ΠΌΠ΅ΡΠΊΠΈ, Π±ΠΎΠ»ΡΠΎΠ² ΠΈ Ρ. Π.
- ΠΠ½ΠΈ Π² ΠΎΡΠ½ΠΎΠ²Π½ΠΎΠΌ ΠΈΡΠΏΠΎΠ»ΡΠ·ΡΡΡΡΡ Π² ΠΏΡΠΎΠΈΠ·Π²ΠΎΠ΄ΡΡΠ²Π΅ ΡΡΡΠ½ΡΡ ΠΈΠ½ΡΡΡΡΠΌΠ΅Π½ΡΠΎΠ² ΠΈ ΠΌΠ΅ΡΠΈΠ·ΠΎΠ².