- Как делают керамогранит — репортаж с фабрики
- Что такое керамогранит и чем отличается от керамической плитки? / ProPlitku.by
- Производство керамогранита, технологии, циклы, этапы
- Технология производства керамогранита
- свойства, отличия от кафеля, укладка
- Укладка керамогранита на пол своими руками
- Состав, виды, типы и технология производства керамической плитки.
Как делают керамогранит — репортаж с фабрики
Керамогранит появился в Италии в конце семидесятых годов двадцатого века и тех пор получил широчайшее распространение по всему миру. В России он называется керамогранит, керамический гранит, или иногда грес. В Италии и остальном мире gres или gres porcelanato,что приблизительно переводится с итальянского как фарфоровая керамика.
Еще совсем недавно керамогранит в нашей стране был всем в диковинку, сегодня им никого уже не удивишь, но далеко не все знают что же в реальности он из себя представляет. Часто даже от продавцов плитки можно услышать что керамогранит прессуется из гранитной крошки, или другие не менее занимательные версии. В этой статье мы расскажем из чего состоит керамогранит и проиллюстрируем фотографиями с фабрик весь процесс его производства, от подготовки сырья до попадания готовой продукции на склад фабрики.
Итак, вопреки распространенным заблуждениям, керамогранит не имеет никакого отношения к граниту и прочим натуральным камням, а производится как и обычная керамическая плитка из глины и по очень похожей технологии, но есть и отличия. Тогда как обычная керамическая плитка производится из красной или белой глины, либо определенных их смесей, в состав керамогранита входят два вида светлых глин, каолиновой и иллитовой, обладающих разными свойствами (в частности иллит более пластичен, а каолинит обладает большей огнеупорностью). Помимо глин в состав керамогранита входят кварцевый песок и полевой шпат.
При взаимодействии всех этих компонентов при высокой температуре и большом давлении происходит процесс остекловывания или витрификации, в ходе которого керамогранит и приобретает свои уникальные свойства. Кстати, подобные процессы происходят и при производстве известного нам всем фарфора, так что можно считать эти два продукта близкими родственниками. Теперь вспомним, что итальянцы называют керамогранит gress porcellanato — фарфоровая керамика.
Для придания керамограниту нужного цвета используются минеральные красящие пигменты, как правило окислы металлов. Керамогранит бывает полной прокраски (другие названия: прокрашенный в массе, tutta massa, неглазированный, full body), в данном случае окрашивается вся смесь из которой прессуется керамогранит и окраска равномерна по всей его толщине.
Второй вид керамогранита — глазурованный, когда сам керамогранит не окрашен (на срезе он сероватого оттенка), а на его поверхность нанесена глазурь нужного цвета. Такой керамогранит называется глазурованным, или смальтированным. Стоимость красителей зависит от цвета и иногда может составлять значительную долю от стоимости готового керамогранита. Попробуйте в магазине поинтересоваться ценами на красный керамогранит полной прокраски, поверьте, результат превзойдет ваши ожидания.
Cырьё, для керамогранита (уже известные нам глина, песок и полевой шпат) хранится в специальных отсеках при определенных параметрах температуры и влажности, и уже готово к превращению в керамический гранит.
Сначала сырье загружается в специальные бункеры, а затем с помощью ленточных конвейеров подаётся на производственную линию. Здесь все компоненты дозируются по определенному рецепту, и попадают в мельницу, представляющую собой огромный металлический цилиндр.
Фотография предоставлена Ассоциацией итальянских производителей керамической плитки Confindustria Ceramica
Перемалывание производится в присутствии воды. Внутри цилиндра-мельницы находится множество мелющих тел: натуральной гальки, либо шаров из определенных материалов, например глинозема или алюбита. Внутри цилиндра несколько камер, в каждой из которых мелющие тела разных размеров. Смесь перемещается от камеры с более крупными мелющими телами к камере с более мелкими, проникая через специальные сетки по мере достижения требуемых размеров. На выходе из мельницы мы получаем суспензию (водный раствор) из мельчайших и одинаковых по величине частиц, называемых шликером (или по итальянски barbottina).
Готовый шликер хранится в специальных бассейнах при постоянном перемешивании, потом в шликер в заданных концентрациях добавляются красящие пигменты, а затем он поступает в атомизатор (башенную распылительную сушилку), где подвергается обезвоживанию. Атомизатор — это вот такой огромный металлический цилиндр внутри которого установлены газовые горелки.
Шликер, распыляясь внутри сушилки, опадает на дно уже в виде порошка, который подается на очередную транспортную ленту.
Влажность порошка после атомизатора составляет 6%, что является оптимальным для последующего прессования. Результатом этого этапа являются пресспорошки, которые имеют соответствующие цвета, хранящиеся вот в этих бункерах.
Впоследствии полученные пресспорошки разных цветов смешиваются в заданных концентрациях для получения нужного оттенка.
Теперь материалы готовы к следующему очень важному этапу — прессованию в ходе которого они наконец-то приобретут свою будущую форму. Прессование происходит при помощи гидравлического пресса, который является одним из самых важных компонентов производства. Именно параметрами пресса определяются максимальные размеры керамогранита производимого фабрикой.
Прессование производится в два этапа Первичное прессование при нагрузке около 80 кг/см2 способствует удалению воздуха. На втором этапе прессования при давлении более 500 кг/см2 происходит формирование плитки. После чего “сырая” плитка помещается в сушильную камеру для полного удаления влаги.
После сушильной камеры влажность смеси в плитке составляет лишь сотые доли процента и плитка уже готова к обжигу. Но до этого (не зря же работали дизайнеры фабрики) плитка как правило проходит еще один этап. Сначала (если необходимо) она попадает в глазуровочную камеру где на нее распыляется глазурь.
Фотография предоставлена Ассоциацией итальянских производителей керамической плитки Confindustria Ceramica
После этого (или вместо этого, в зависимости от дизайна) плитка подвергается окрашиванию или нанесению рисунка, например, с использованием традиционного оборудования Ротаколор. Система состоит из четырех барабанов, каждый из которых наносит на плитку рисунок определенного цвета.
Вот это будет глазурованный керамогранит красного цвета.
Фотография предоставлена Ассоциацией итальянских производителей керамической плитки Confindustria Ceramica
А это, вероятно, керамогранит под камень.
Последние несколько лет получила распространение цифровая струйная печать на керамограните, возможности которой значительно превосходят возможности Ротаколора. Она позволяет наносить на керамогранит любой рисунок с фотографическим разрешением. Главной сложностью здесь пока остается подбор цветов, так как использовать можно только натуральные красители. Так что пока все производители плитки дружно печатают на этих принтерах плитку под дерево и плитку под камень.
После окраски будущие плитки размещаются в специальные хранилища и ждут своей очереди перед этапом, который в корне изменит их свойства, прессованные плитки, которые легко можно раскрошить руками уже совсем скоро превратятся в прочнейший керамогранит.
Обжиг происходит в несколько этапов. Сначала плитки обжигаются при 400 градусах по Цельсию (этап предварительного обжига), потом разогреваются до 900 (предварительный прогрев), затем происходит основной обжиг при температуре 1200-1300 градусов, и наконец постепенное понижение температуры. Во время обжига плитка уменьшается в размерах на 5-10%.
Такие печи работают непрерывно, отключаются только для проведения профилактических работ 1-2 раза в год, остывание и нагрев такой печи занимает по времени около недели. Поэтому все производство рассчитано таким образом, чтобы печь была загружена постоянно. И если, например, выходит из строя пресс, должен оставаться запас готовой для обжига прессованной плитки на все время его простоя.
Далее при необходимости плитка подвергается полировке или реттификации. На фото плитка проходит процесс полировки, на выходе будет плитка с полуполированной поверхностью (по-итальянски lappato), обладающая эффектным неоднородным блеском.
Фотография предоставлена Ассоциацией итальянских
производителей керамической плитки Confindustria Ceramica
Теперь плитка готова. Можно отправлять ее на склад? Пока нет. Осталось еще несколько важных операций. Сначала надо отсеять плитку с дефектами. Это могут быть геометрические искажения плитки, сколы, трещины, пустоты, неравномерность окраски и другие отклонения от заданных параметров. Контроль качества плитки также проходит в автоматическом режиме.
На стенде представлены различные дефекты плитки, у итальянцев вообще с этим очень строго, по российским ГОСТам эта плитка, скорее всего, вполне могла бы попасть к покупателю.
Мы уже знаем,что во время обжига плитка уменьшается в рамерах на 5-10%. Так как глина “живой” материал, то понятно что не существует двух абсолютно одинаковых плиток, и в итоге при номинальном размере плитки, например 500х500 мм из печи выходят плитки и размером 500х500 мм и 495х495 мм и 505х505 мм, попробуйте уложить все это разнообразие в одну и ту же комнату. Чтобы избежать такой ситуации готовая плитка сортируется по калибрам, вариации размеров внутри одного калибра не превышают 1 мм и укладка такой плитки не представляет никакой сложности.
Сортировка по калибрам, как и все уже известные нам этапы производства полностью автоматизирована.
Но на современной фабрике производящей керамогранит есть один этап, где нельзя обойтись без участия человека. Это сортировка плитки по тонам. Тона — это вариации оттенков плитки, которые, аналогично размерам плиток могут различаться на выходе из печи. Кому то может и понравится, когда все плитки на кухне будут разных оттенков, это выглядит натуральнее. Большинство же покупателей плитки хотят однотонный пол, поэтому фабрики вынуждены сортировать плитку по тонам.
И как оказалось, человеческий глаз очень чувствительный и совершенный прибор и никакие компьютерные системы оснащенные самой дорогой оптикой не могут с ним сравниться в способности безошибочно различать оттенки. Поэтому сортировку плитки по тона производит человек, сравнивая плитку с эталонными образцами. Именно этим занята итальянская синьора на фото под присмотром главного технолога фабрики.
Видите разницу?
Теперь осталось всего-то упаковать керамогранит в коробки.
Разложить на палеты так, чтобы на каждой был керамогранит определенного тона и калибра.
И отвезти на склад фабрики, где он будет дожидаться, своего покупателя.
Редакция благодарит группу компаний Ricchetti Group и Ассоциацию итальянских производителей керамической плитки Confindustria Ceramica за содействие в подготовке данной статьи.
Смотрите также статьи:
Производство керамогранита — видео от керамогранитного завода Италон
Монокоттура и бикоттура — плитка одинарного и двойного обжига
Разные тона плитки или почему опасно докупать плитку спустя два года
etoprosto.ru
Что такое керамогранит и чем отличается от керамической плитки? / ProPlitku.by
Керамогранит – это особо прочный облицовочный материал экстра-класса. Его также называют керамический гранит и керогранит. Делают его из различных смесей молотых горных пород (кварц, шпат) на основе глин высокого качества и естественных минеральных красителей.
О вариантах применения керамогранита можно прочесть здесь.
Содержание
- Как появился керамогранит?
- Как делают керамическую плитку?
- Технические характеристики керамогранита
- Виды керамогранита
- Стандартные размеры керамогранитной плитки
- Особенность укладки керамогранита
Как появился керамогранит?
В 1978 году в газетах заговорили, что итальянские мастера создали композитный материал, коэффициент водопоглощения которого стремился к нолю. Материал по многим показателям не уступал натуральному граниту, что было очень ново на рынке керамической плитки.
Итальянцы, привыкшие в своем жарком климате тысячелетиями использовать керамическую плитку в интерьерах, не остановились в поисках путей ее усовершенствования. Они разработали технологию высокотемпературного однократного обжига благородных белых глин. Процесс обжига происходит при температуре порядка 1300 °C и очень похож на рождение камня в естественных условиях, с одной лишь разницей – скорость изготовления керамогранита в разы выше, а керамогранитная плитка на выходе не нуждается в обработке мастером по резке камня. В итоге получается доступная по цене стильная плитка с характеристиками натуральной горной породы.
Как делают керамогранитную плитку?
Производственный процесс керамогранитной плитки практически полностью повторяет природный процесс образования камня глубоко в недрах земли.
Чтобы получилась плитка керамогранит, необходимо:
- Смешать два сорта высококачественной белой глины, кварцевый песок, полевой шпат и минеральный краситель, который был выбран дизайнером.
- Когда масса готова, из нее формируют плитки согласно дизайн-проекту, а затем отправляют их под гидравлический пресс.
- Каждая плитка сдавливается под прессом 500 кг/см2 и сразу отправляется в печь на обжиг при температуре 1300 °C.
В раскаленной печи спрессованная плитка моментально спекается, образуя твердый материал повышенной плотности, практически не способный к поглощению влаги. Таким образом, керамическая плитка керамогранит сильно выигрывает по прочности у обычной керамической плитки, которую запекают с температурой 1100 °C, предварительно подвергнув прессованию с вдвое меньшими показателями (250 кг/см2) °C.
Сложность производственной технологии керамогранитной плитки состоит в очень точном соблюдении пропорций при приготовлении смеси, а также точного соблюдения режима температур при обжиге прессованных заготовок. Если учесть, что в заводских условиях операции производятся не с килограммами, а с тоннами материала, становится понятной сложность этой кропотливой работы.
Для получения качественного керамогранита компоненты смеси очень тщательно приготавливаются. Печь обжига в длину составляет 150 метров. Делается это для того, чтобы исключить погрешность в температуре, потому что несколько в сторону нарушают геометрические параметры плитки, то есть создают брак. Чтобы получить керамогранит высокого качества при обжиге плитку необходимо нагревать постепенно, очень внимательно контролируя повышение температуры до нужных 1300°C.
Технические характеристики керамогранита
1. Низкий коэффициент поглощения влаги
Благодаря тому, что керамогранит – материал низкопористый (вспомните прессование), коэффициент влагопоглощения у него стремится к нолю (0,05%). Такая низкая поглощаемость влаги не свойственна ни обычной керамической плитке, ни натуральному камню. Поэтому керамогранитом активно облицовывают фасады, защищая их от влаги во всех климатических зонах.
2. Устойчивость к внешним воздействиям и стиранию
Среди всех видов керамической плитки, керамогранит обладает наивысшей степенью устойчивости к износу и инертностью к агрессивным веществам. Он не теряет цвет на солнце с течением лет. Оставить царапину на нем можно только корундом либо алмазом (твердость по шкале твердости минералов Мооса – 8 баллов, то есть на 2 позиции ниже алмаза). Поэтому керамогранит выбирают для облицовки общественных зданий с высокой проходимостью людей – аэропортов и вокзалов, крупных магазинов и дворцов искусств.
3. Механическая прочность и стабильность к температурам
Ударная прочность и индифферентность к высокому давлению на поверхность керамогранита позволяет выбирать его в качестве напольного покрытия в производственных цехах. Резкие температурные перепады в пределах 100 °C не влияют на свойства керамогранитной плитки, поэтому этот материал популярен и в составе вентилируемых фасадов.
Можно также повториться, что керамогранит содержит только натуральные компоненты и красители. Перед изготовлением смеси для прессования, все компоненты проверяются на наличие радионуклидов, поэтому прочих равных керамогранит не несет в себе естественной радиации, в отличие от натурального гранита.
Виды керамогранита
Керамогранит делается из глины, которая известна как материал для творчества. Действительно, дизайнеру есть из чего выбрать, когда речь идет о керамогранитной плитке. По видам керамогранит разделяют на следующие группы:
- Технический керамогранит, имитирующий натуральный необработанный гранит. Он относительно недорог за счет отсутствия дополнительной обработки после обжига.
- Глазурованный керамогранит – декоративная плитка плитка. После запекания на листы керамогранита наносят глазурь и снова отправляют в печь. Он более надежен, чем обычная плитка, но все же устанавливается там, где механические воздействия на него будут минимальными, так как нарядная глазурь со временем стирается и блекнет.
- Матовый керамогранит – не полированная поверхность плитки.
- Полированный керамогранит – отполированный до зеркального блеска и, соответственно, более дорогой, чем матовый, декоративный керамогранит. Его не стоит укладывать на пол, поскольку со временем полировка грубеет, и полированный керамогранит внешне не сильно отличается от матового.
- Структурированный керамогранит – декоративные плитки с рельефной поверхностью, которые воспроизводят структуру и вид натурального камня, кожи, тканей с рисунками. Методов обработки структурированного керамогранита так же много, как дизайнерских решений: иногда его даже покрывают сусальным золотом.
- Сатинированный керамогранит – плитки, на которые перед обжигом наносится слой минеральных солей, что придает поверхности легкий блеск. Этот декоративный керамогранит еще называют обработанным воском. Скользит он гораздо меньше, чем полированный керамогранит, однако не его красота не имеет большой устойчивости к нагрузкам.
Стандартные размеры керамогранитной плитки
По размерам керамогранитная плитка еще более разнообразна, чем по видам, поэтому с подбором керамогранита для облицовки определенной комнаты проблем не бывает. Шаг стандартных размеров керамогранитных плиток – от минимального 7,5х7,5 см до максимального 120х180 см.
По толщине стандартные размеры тоже разнятся – от 7 мм до 30 мм. Более тонкая керамогранитная плитка используется в качестве интерьерной, поскольку вес ее меньше, но и хрупкость выше. Впрочем, соблюдать все тонкости технологии укладки керамогранита с нею тоже не обязательно. Керамогранитная плитка 12-20 мм идет на облицовку полов, испытывающих повышенную нагрузку. Утолщенный до 30 мм керамогранит используется для износостойких ступеней.
Особенность укладки керамогранита
Больших существенных отличий в технологии укладки керамогранита и укладки обычной керамической плитки нет. Единственно важный момент – клеящий состав. Так, например, из-за малой пористости невозможно уложить керамогранит на цементный раствор. Из-за низкого показателя влагопоглощения, керамогранит не держится на клеях, содержащих воду. Для керамогранита нужен двухкомпонентный клей с высокой адгезией, приникающие свойства которого обеспечат хорошее сцепление керамогранита с поверхностью. Первый компонент такого клея – сухая цементно-песчаная смесь, второй акрил либо латекс. Такие безводные клеи очень эластичны и в процессе эксплуатации показывают высокую стойкость к ударам, морозоустойчивость и инертность к температурным изменениям.
www.proplitku.by
Производство керамогранита, технологии, циклы, этапы
Керамический гранит – популярный строительный материал, изготавливаемый из специальной мелкодисперсной смеси. Производство керамогранита осуществляется в несколько последовательных этапов. Простыми словами можно описать, как выполняется весь процесс и какими качествами наделяется готовый керамогранит.

Характеристики керамогранита
Смесь для керамогранита изготавливается из двух различных сортов глины, в состав которой входят минеральные кварцсодержащие материалы и природные пигменты-красители (например, окись железа, придающая кобальтовый оттенок материалу). Состав настоящего керамогранита во многом схож с природным камнем гранитом. Однако этот материал обладает одним преимуществом – в его составе нет никаких радиоактивных включений (как в натуральном граните), подбор компонентов раствора для производства керамического гранита тщательно контролируется. Смесь приготавливают посредством тщательного перемешивания и последующего прессования под большим давлением (около 500 кг/кв.см.) После того, как спрессованный камень немного просохнет, осуществляется обработка керамогранита методом обжига при высокой температуре (около 1200-1300 градусов).
В целом же производство керамогранита выполняется по тому же принципу, что и в природных условиях. Разница лишь в том, что процесс создания камня полностью контролируется мастером, что позволяет получить высококачественный декоративный материал. Керамогранит свойства свои приобретает благодаря правильному выполнению мастером всей технологии производства. Камень становится прочным, устойчивым к воздействию неблагоприятных факторов, имеет красивый внешний вид.

Отличительной особенностью керамогранитного камня является то, что узор у него на срезе и поверхности одинаков. Кроме глины (обычно применяют белую массу) в составе раствора для керамического гранита имеются минеральные компоненты, полевые шпаты и кварц. Покраска керамогранита выполняется на первом этапе изготовления, в процессе приготовления сырьевого раствора. В густую массу добавляют минеральный пигмент и хорошо размешивают. Такой подход позволяет равномерно распределить красящий состав по всей толще керамического гранитного камня. Кроме того, добавление пигмента в раствор исключает выцветание оттенка камня в процессе эксплуатации, под воздействием ультрафиолетовых солнечных лучей.


Одним из важных достоинств керамогранита является высокая износоустойчивость. Используемая технология изготовления керамогранита обеспечивает материалу хорошие показатели морозоустойчивости, стойкости к ультрафиолетовому излучению, большим сопротивлением неблагоприятным климатическим и механическим воздействиям.

Керамогранит, состав которого обеспечивает плотную структуру материалу, характеризуется низким уровнем водопоглощения. Он не подвержен воздействию щелочных материалов и кислот, может выдерживать огромные механические и ударные нагрузки, давление ветра и внутреннее напряжение, вызываемое резкими перепадами температур. Более того, технология керамогранита настолько качественна и хороша, что материал может успешно противостоять открытому огню (характеризуется отличными огнеупорными свойствами).


Внешний вид керамогранитного камня может быть разным, в зависимости от способа обработки. Матовый материал после обжига не обрабатывается вообще, сохраняя свой первоначальный природный облик. Рельефный керамогранит имеет на своей поверхности ярко выраженный узор. Полировка плитки керамогранит обеспечивает получение красивого материала с идеально гладкой, ровной глянцевой поверхностью. Полирование керамогранита осуществляется посредством срезания верхнего матового слоя после обжига материала. Изготовление керамогранита в производственных условиях позволяет получить и полуполированный камень. Его создают посредством частичного срезания верхнего слоя. В итоге поверхность керамогранита получается комбинированной, в ней есть и матовые, и глянцевые участки. Нормы расхода керамогранита (количество материала на 1 кв.м. площади помещения) определяются производителем в соответствии с техническими характеристиками готового изделия. В данном случае учитывается размер одного элемента и ширина швов между плитками.



Завод по производству керамогранита поставляет на строительный рынок глазурованный и не глазурованный декоративный камень. В первом случае внешний вид плитки более привлекателен, но её рекомендуется применять только для покрытия пола, на поверхность которого создаются небольшие нагрузки.

Страны, в которых сейчас действуют заводы по производству керамогранита:
- Россия
- Италия
- Испания
- Турция
- Китай
- США
Производство керамогранита (видео пример с итальянского завода) постоянно совершенствуется.
Изготовители этого строительного материала регулярно изменяют дизайн керамогранита, создавая всё новые и новые текстуры, оттенки и узоры.

Это важно! Правильно комбинируя между собой различные виды гранита керамического (камень должен иметь одинаковый размер), можно красиво украсить интерьер комнаты и создать уникальный дизайн стен или пола в помещении.

Технология изготовления керамогранита
Строительный материал керамогранит, технология производства которого имеет свои особенности, создаётся исключительно из природного натурального сырья (глины). Материал подвергается однократному обжигу, поэтому сырьё обязательно должно обладать огнеупорными характеристиками и содержать минимальное количество красящих элементов (титана или оксидов железа). Заводы производители керамогранита применяют в качестве сырья такие материалы, как полевой шпат, огнеупорные глины, кварцевый песок и каолин. Перед использованием каждый из этих материалов проходит тщательную проверку (входной контроль). Современное оборудование для производства керамогранита полностью компьютеризировано, и это позволяет мастерам проводить анализы и получать результаты высокой точности. После того, как сырьё проходит полноценный технологический контроль, его допускают (или не допускают) к дальнейшему производству.

Теперь расскажем, как делают керамогранит. Вся процедура осуществляется последовательно, в несколько этапов. Рассмотрим каждый из них в подробностях.

Выбор сырья и приготовление раствора
Производство керамогранита начинается с выбора сырья и приготовления на его основе раствора. Здесь нужно быть очень внимательным, ведь от качества исходного материала будет во многом зависеть качество готового изделия. Керамогранит, глина для которого подбирается мягкая и пластичная, окрашивается специальным пигментом (с основой в виде металлических окисей — хрома, кобальта, железа или марганца). Для того, чтобы готовый керамический черепок получился более прочным, в раствор во время приготовления добавляют полевой шпат и кварцевый песок. Для производства керамогранита ещё необходима глина малой пластичности, насыщенная каолином.

Подготовленное сырьё необходимо хорошо измельчить, используя специальное оборудование для керамогранита (мельница) и метод мокрого дробления. Такой подход обеспечивает раствору однородность, благодаря чему обожжённый черепок получается качественным и прочным. Когда состав хорошо измельчён, его подают в смесительную камеру мельницы, где происходит приготовление порошкообразной смеси. Далее из раствора выпаривают воду, поместив его в камеру с горячим воздухом (с температурой около 600 градусов). Получаемый состав полностью подготовлен к прессованию.

Прессование керамогранита
Качественное изготовление керамогранита возможно только при правильном подходе к прессовке подготовленной глиняной смеси. Гранулированный раствор с содержанием влаги не более 7% прессуется под давлением не менее 400 кг/см2. Такая процедура позволяет получить прочное изделие нужной формы, размера и фактуры.
Сушка сформированного изделия
Сушка следующий важный этап, применяемый при производстве керамогранита. Дело в том, что в процессе прессовки в материале остаётся определённый процент влаги (необходимой для формовки изделия). Главной задачей на этапе сушки является полное обезвоживание наполовину готового продукта. Завод керамогранита использует для качественной сушки материала специальные тепловые камеры с высокой температурой и горячим воздухом. Заготовки керамогранита укладываются туда, а весь процесс просушивания тщательно контролируется ответственными специалистами.

Обжиг
Устройство керамогранита на этапе обжига предполагает воздействие на подготовленный материал высокой температуры. В ходе температурной обработки керамогранит приобретает необходимую прочность. Глиняное сырьё, находясь под воздействием большой температуры, спекается, становясь монолитным. После остывания изделие становится невероятно прочным, с минимальным количеством пор и высокой стойкостью.
Совет. При обжиге керамогранита необходимо следить за уровнем температуры, поскольку от неё зависит оттенок готового строительного материала. Контроль особенно необходим в том случае, если камень покрывается глазурью. Чрезмерно высокая температура приведёт к пережогу поверхности, а если температурный режим будет меньше нормы, то изделие получится недожжённым, а значит, менее прочным.

Контроль качества продукции
За качеством готового изделия необходимо следить во время его выхода с автоматической линии. Каждый плиточный элемент проверяется при помощи компьютеризированного оборудования на предмет соответствия европейским стандартам.

Некачественная плитка сразу убирается из партии и впоследствии перерабатывается специальным механизмом. А вот качественный материал сортируется по цвету, сорту и калибру.

Изготовленный и отсортированный керамогранит (упаковка которого выполняется в автоматическом режиме в специальную тару), отправляется на оптовые склады. Реализаторам остаётся только сформировать ценник на керамогранит, доставка материала конечному потребителю осуществляется сразу же после поступления заказа на склад.


yaplitka.ru
Технология производства керамогранита
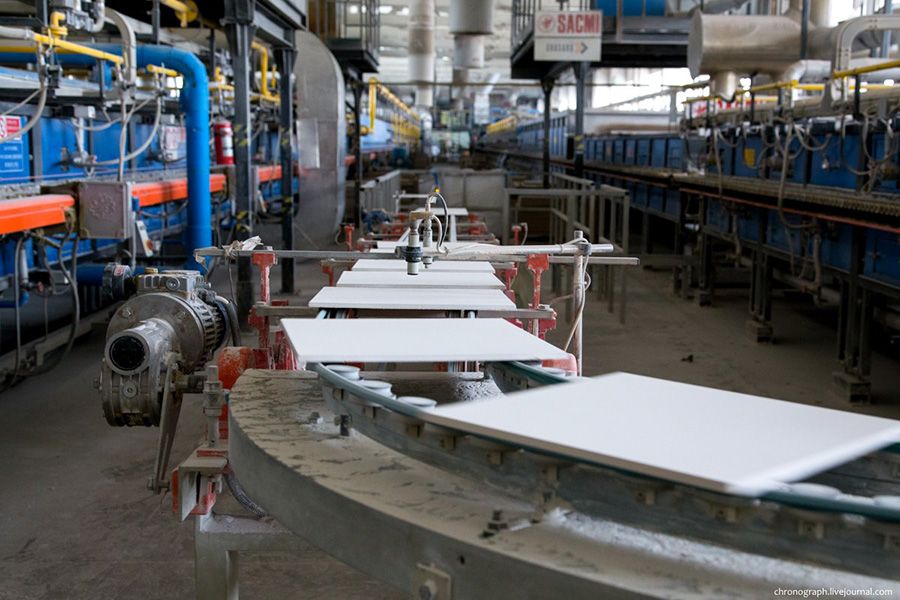
Керамогранит — исключительный по техническим качествам материал, поэтому необходимо, чтобы используемое для его производства сырьё было абсолютно чистым и обладало по возможности совершенной геохимической структурой. Итак, качество сырья является непреложным условием производства хороших изделий.
Процесс изготовления керамогранита начинается со складирования сырья, которое бывает трёх видов: глинистые, неглинистые и инертные материалы. Глинистое сырьё составляют каолиновые глины и каолины, придающие сырьевой основе связывающие свойства и пластичность, что впоследствии, после прессования, позволяет плитке сохранять свою форму. Неглинистые материалы — полевые шпаты — уменьшают пористость обожженных изделий, облегчая процесс спекания и придавая материалу прочность, компактность и стойкость.
Инертные материалы — это кварцевые пески; они образуют «остов» плитки. К сырьевым материалам относятся также пигменты, которые являются оксидами или смесями оксидов металла, почти все они изначально натурального происхождения, переработанные затем особым образом, используются для получения цвета, требуемого производством. После выгрузки и складирования сырья в специальные отсеки, в которых поддерживается постоянная температура, начинается технологический процесс, на первом этапе которого производится помол и окрашивание сырья, которое впоследствии составит основную сырьевую смесь. Сырьё загружается в приёмные бункера, откуда ленточные конвейеры подают его к соответствующим установкам.
Для начала сырьевые материалы, строго дозированные на весовых конвейерах, перемешиваются по заданной рецептуре, в результате чего получается основная сырьевая смесь. Эта смесь подвергается последующей обработке, призванной обеспечить абсолютную однородность массы по размеру и по влажности частиц материалов.
Итак, первый шаг — это достижение гранулометрической однородности. А достигается она в результате мокрого (т.е. в присутствие воды) помола материалов в мельницах, имеющих вид огромных стальных цилиндров, непрерывное вращение которых обеспечивается мощными электродвигателями. Внутри каждой мельницы имеются несколько сообщающихся камер, каждая из которых содержит определённое количество мелющих тел. Последние в результате вращения цилиндров падают одно на другое, измельчая частицы сырьевой смеси.
В качестве мелющих тел используются натуральные материалы (галька) или шары различных размеров из натуральных компонентов, переработанных специальным образом (например, из спечённого глинозёма). Результат — водная суспензия, частицы которой обладают достаточно мелкой и однородной величиной.
Внутри мельница состоит из нескольких сообщающихся камер, разделённых прорезиненными сетками. В каждой камере содержатся мелющие тела, уменьшающиеся по мере перемещения из одной камеры в другую. Смесь перемещается из одной камеры мельницы в другую, только когда зернистость материалов достигает нужных размеров. Получаемая масса — водная суспензия, частицы которой обладают достаточно мелкой и однородной величиной, чтобы можно было перейти к следующей стадии обработки. Эта суспензия называется шликером.
Полученный шликер поступает в огромные подземные бассейны, где, во избежание отстаивания (т.е. оседания составных частей), непрерывно перемешивается с помощью пропеллерной мешалки. Затем сырьевая смесь окрашивается, и получаются те тона, которые впоследствии составят смесь пресспоршка. Окрашивание осуществляется путём добавления в шликер приготовленных ранее красителей, система дозирования которых полностью компьютеризована.
Теперь шликер должен быть обезвожен до нужной степени. Данная операция производится в атомизаторе (башенном распылительном сушиле). Содержащийся в бассейнах шликер при помощи насосов подаётся в атомизатор. Это огромный стальной цилиндр, оснащённый газовой горелкой, которая доводит внутреннюю температуру до 550 градусов. Проходя под высоким давлением через форсунки, шликер распыляется внутрь сушила, где попадает под поток горячего воздуха. Вода быстро испаряется через верхнюю часть атомизатора, а высушенная смесь, пресспорошок, высыпается на транспортёр через его нижнюю часть, который доставляет его в бункера хранения. Цель атомизации — высушить шликер до получения материала, степень влажности которого идеальна для его прессованию.
Процент влажности полученного пресспорошка составляет около 6 %. Это идеальный показатель, обеспечивающий правильное выполнение прессования, в процессе которого плитки обретают форму. Пресспорошки являются главным ингредиентом смесей, которые будут подвергнуты прессованию. Перед прессованием порошки поступают в бункера хранения, где охлаждаются до температуры окружающей среды и становятся однородными по остаточной влажности.
Далее различные цвета извлекаются из бункеров и перемешиваются посредством автоматизированного оборудования в соответствии с формулой или рецептом. Количество цветовых сочетаний бесчисленно. На этом этапе возможно обогащение порошков другими материалами, в виде гранул, порошков или чешуек, придающими готовым изделиям особые эстетические и технические свойства. Полученные таким образом составы являются конечным результатом процесса обработки сырьевых материалов.
Этап прессования преследует три цели: формование плитки – придание пресспорошку установленной формы; трамбование пресспорошка — процедура, позволяющая сырой и ещё необожженной плитке выдерживать последующие нагрузки; уплотнение – предельное сокращение пористости плитки.
Этап формовки начинается с подачи пресспорошка к прессам. Прессование включает четыре стадии:
- Сначала форма наполняется пресспорошком, который подаётся из расходных бункеров, расположенных над прессами.
- Затем форма закрывается, и выполняется первичное прессование под небольшим давлением. В этом случае содержащийся в плитке воздух сжимается и удаляется при лёгком открывании формы.
- После этого имеет место вторичное прессование, которое и обусловливает создание сырой плитки.
- И в последнюю очередь плитка извлекается из формы, а одновременно идёт новая загрузка пресспорошка для последующего прессования.
www.keramogranit.ru
свойства, отличия от кафеля, укладка
На данный момент керамогранит считается одним из самых популярных отделочных материалов. В нашей статье опишем, что собой представляют такие изделия, обратим внимание на виды и размеры плиток, узнаем преимущества этого материала, а также особенности укладки.
Содержание статьи:
Что такое керамогранит
Под этим понятием скрываются искусственные отделочные изделия, выполненные в виде плитки различного размера и текстуры. Подобные материалы изготавливаются при высоком давлении (порядка 500 кгс/см2). В дальнейшем сформированная сырьевая масса поддаётся обжиганию при температуре около 1300 градусов Цельсия. Основными сырьевыми компонентами здесь считаются каолиновая и иллитовая глина. В базовый состав добавляются и другие компоненты для придания изделиям определённого цвета и особых технических характеристик. Ванная комната — идеальное помещение для такой плитки.
Первоначальной идеей разработчиков было использования плитки керамогранита для укладки в различных технических помещения, например в промышленных цехах или общественных зданиях. За последние несколько лет ассортимент отделочного материала значительно вырос. Теперь керамогранит используется не только в качестве напольного покрытия в местах с высокими механическими нагрузками (в кинотеатрах, магазинах, вокзалах, торговых комплексах и аэропортах), но и как отделочный стеновой материал. С помощью таких изделий проводится отделка бассейнов, кроме того плитку укладывают на пол в ресторанах, химических лабораториях, на автомойках и в гаражах.
Отличие керамогранита от керамической плитки
Рассматриваемые материалы изготавливаются из одного и того же сырья, каолиновой глины, поэтому основанным отличием керамогранита от керамической плитки считается технология производства. Как мы уже говорили, спекание сырьевых компонентов у керамического гранита происходит при температуре больше 1000 градусов, у кафеля температурные показатели гораздо ниже.
Керамические изделия, изготовленные по технологии двойного обжига, отличаются небольшой толщиной, имеют минимальные показатели прочности. В структуре такого материала присутствует множество пор, которые впитывают влагу. Через высокую гигроскопичность некоторые виды керамической плитки непригодны для использования во влажных помещениях. Кафель отличается от керамики значительной толщиной и весом, что повышает устойчивость к ударным нагрузкам. Подобные материалы отличаются от аналогов водонепроницаемостью и термостойкостью.
Керамическая плитка для туалета с неполированной поверхностью может использоваться может использоваться для обустройства ступенек крыльца, в ванной комнате или кухне, то есть в помещениях, где необходимо создать антискользящую поверхность. Это особенно важно, ведь небольшое количество воды может превратить пол в скользкий каток, что может привести до травм жильцов.
По технологии производства керамогранита сырьевая масса подвергается воздействию повышенного давления и температур. В конечном итоге это приводит к спеканию отдельных частиц и получению прочного, лишённого пор изделия. Основными характеристиками такой плитки считаются:
- Устойчивость к истирающим усилиям и повышенным механическим нагрузкам. Напольное покрытие под мрамор может выдерживать на себе до 500 килограммов веса без появления трещин и других разрушений.
- Минимальное водопоглощение. В плитке полностью отсутствуют поры, впитывание воды не превышает 0,05%. В связи с этим рассматриваемый материал можно использовать для отделки пола и стен во влажных комнатах.
- Устойчивость к резким колебаниям температур. Керамогранит может эксплуатироваться в диапазоне от -50 до +50 градусов без потери своих основных эксплуатационных характеристик.
- Отделанная поверхность не боится воздействия моющих средств и химических веществ.
Следует обратить внимание на один немаловажный факт. Дело в том, что структура керамогранита однородна по всей толщине, у керамической плитки декоративный слой уложен только на лицевой поверхности. В связи с этим места сколов и царапины на керамическом граните будут почти незаметными для прохожего.
Этот материал часто делают под камень, поэтому его внешний вид будет не худшим, чем у кафеля. Поверхность таких изделий бывает глазурованной полированной, рельефной или матовой. В строительных магазинах присутствует огромный выбор цветов и оттенков керамоплитки, чего не скажешь об аналоге.
Каким бывает керамогранит
В строительстве используются следующие виды керамогранита:
- Технический. Сравнительно дешёвые изделия, имитирующие натуральный гранит. Дешевизна таких изделий связана с отсутствием обработки их поверхностей.
- Глазурованный. Это плитка со специальной декоративной поверхностью. На поверхность такого материала после предварительного обжига наносят глазурь и обратно отправляют в печь. Глазурованный керамогранит отличается особой прочностью, но устанавливается в местах с минимальными механическими нагрузками.
- Матовые изделия имеют неполированный лицевой слой.
- Полированный керамогранит используется в качестве отделочного материала для стен. Он достаточно дорогой, по внешнему виду не сильно отличается от матового аналога.
- Изделия со структурированной поверхностью имитируют дерево, ткань, кожу. В некоторых случаях такая плитка покрывается слоем сусального золота.
Размеры
Одним из самых популярных размеров керамогранита считается 600*600 миллиметров или 60 на 60 сантиметров. Такие изделия используются для укладки напольного покрытия в больших торговых центрах и других помещениях, требующих высокой скорости укладки покрытия. Существуют и другие стандартные размеры материала, например 20 на 20 сантиметров, хотя самыми маленькими считаются габариты 5*5 сантиметров. Самые большие размеры керамогранитной плитки считаются 1,2*3,6 метра. Подобные материалы используются для отделки фасадов.
Внешний вид
Лицевая поверхность рассматриваемого материала может быть самой разнообразной. Далее рассмотрим самые популярные виды:
- моноколор. такие изделия имеют однотонную поверхность, чаще всего белая, зелёная, красная, серая или жёлтая;
- имитация структуры натурального камня, гранита или мрамора;
- изделия с особенной текстурой, под дерево или натуральный камень;
- однородный серый, бежевый, синий или розовый керамогранит с равномерно распределёнными по поверхности светлыми или тёмными точками.
Цвет поверхности плитки будет зависеть от количества пигментов, которые добавляют в процессе производства в базовый состав. Так самым дешёвым считается гранит с равномерно распределёнными вкраплениями. Самым дорогим изделием является моноколор для окрашивания которого используются редкие металлы (кобальт, цирконий или хром). Самыми сложными в изготовлении считаются плитки керамогранита, имитирующие натуральный камень. В данном случае необходимо сложное смешивание нескольких пигментов для получения необходимой текстуры.
Также рекомендуем посмотреть статью: Плитка для ванной комнаты — фото обзор с реальными интерьерами.
По месту применения
В зависимости от места применения керамогранит можно условно разделить на несколько основных видов:
- Для лестниц. Материалы с антискользящим покрытием и высокой износостойкостью. К таким следует отнести плитку с матовой поверхностью.
- Керамогранит для отделки полов. Подобные материалы применяются для укладки напольного покрытия как внутри так и снаружи помещений (на улице). Особенно часто такие изделия укладываются в торговых центрах промышленных цехах и других помещениях с высокой интенсивностью движения людей.
- Плиты, предназначенные для отделки стен.
- Фасадный керамогранит. Монтаж таких изделий проводится на металлический каркас между направляющими которого уложен слой утеплителя из пенополистирола или минеральной ваты. Далее устраивается воздушная прослойка толщиной в 5 сантиметров (предназначена для отвода выделяющейся влаги).
Преимущества использования керамогранита
При отделке пола керамогранитом можно получить несколько весомых преимуществ:
- Рассматриваемый материал не боится воздействия влаги, он характеризируется минимальным водопоглощением, не разрушается под воздействием отрицательных температур. В связи с этим плитка может эксплуатироваться даже на улице.
- Лицевая поверхность керамогранита обладает высоким уровнем износоустойчивости, не боится воздействия кислот и других химических веществ.
- Структура материала не разрушается под воздействием внешних агрессивных факторов, не выгорает на солнце. Керамогранит может использоваться в качестве напольного покрытия в местах с высокой проходимостью людей, например, в выставочных залах, торговых павильонах и др.
- Материал имеет высокие показатели твёрдости, резка керамогранита может проводиться только при помощи специального инструмента, например болгарки с абразивным кругом.
Особенности укладки
Процесс укладки керамического гранита почти ничем не отличается от аналогичных операций, проводимых с кафелем. Единственное, что необходимо учитывать в данном случае, это правильный подбор клеевой смеси (через минимальную пористость такой материал фактически невозможно уложить на цементно-песчаный раствор). Плитка плохо держится на обычном клее в составе которого присутствует вода. Для её надёжной фиксации нужен двухкомпонентный состав, обладающий высокой адгезией.
Подобную смесь можно приготовить и в домашних условиях. Первым компонентом здесь считается смесь цемента и песка, вторым акрил или латекс. Такой состав абсолютно безвреден, он обладает высокими показателями морозостойкости и ударостойкости. На вопрос о том, чем резать плиты керамогранита можно ответить просто – болгаркой с абразивным кругом или плиткорезом.
Полезная статья? Оцени и добавь к себе в закладки!
vashavannaya.ru
Укладка керамогранита на пол своими руками
Много ли найдется отделочных материалов, которые красивы, не боятся воды, морозов, жары, перепадов температур, стойких к механической нагрузке, не выцветающих, легких в уходе. Думается, не так уж и много. Один из них — керамогранит. Такое сочетание качеств способствует высокой популярности материала — его используют в наружной и внутренней отделке. Сложная система наружного крепления не дает возможности делать это самостоятельно, а вот укладка керамогранита на пол или стены внутри помещений — задача средней сложности и может быть выполнена своими руками, без привлечения специалистов.
Красиво, солидно, надежно

Виды керамогранита
Самое широкое распространение получил у нас полированный керамогранит, еще встречается матовый и полуполированный. Но это далеко не все виды этого материала. Есть еще несколько интересных вариаций, о которых знают пока немногие. Разберемся со всеми видами и их основными характеристиками.
- Полированный и полуполированный (отличается степенью полировки и блеска). Этот вид имеет наиболее эффектный вид. И, хотя стоит дороже остальных видов, используется достаточно часто. Но стоит иметь в виду, что в процессе эксплуатации полировка становится тусклее и со временем поверхность становится матовой. Есть полированного керамогранита еще один недостаток — полировка открывает закрытые ранее поры. В результате пролитая жидкость впитывается, остаются следы. Потому многие производители покрывают плитки керамогранита лаком. Если такого покрытия нет, его надо нанести после укладки. Еще один неприятный момент: если на такую поверхность попадает жидкость, пол становится очень скользким.
Полированный керамогранит уложен без шва, создавая ощущение монолита - Глазурованный. Внешне он похож на керамическую плитку, но отличается повышенной прочностью. На плитку керамогранита нанесли глазурь, затем обожгли в печи. Если этот материал использовать в местах с большой нагрузкой, тонкий декоративный слой протрется, отделка потеряет свой вид.
- Матовый. Это сформованные плиты без дальнейшей обработки. Поверхность из матового керамогранита не столь эффектна, как из полированного, но зато этот вид отделки нескользкий даже в мокром состоянии и его можно использовать и в кухнях и в ванных.
Матовый можно использовать во влажных помещениях - Технический. Самый дешевый материал из данной группы. Чем-то напоминает натуральный гранит, не очень декоративен, но очень прочен. Служить может более десяти лет даже в местах с высокой механической нагрузкой. Использовать можно на полу в технических помещениях, на верандах, террасах, выкладывать дорожки на участке.
- Сатинированный (сатиновый). Очень декоративный и необычный вид у этого керамогранита. Поверхность напоминает сатин, имеет мягкий блеск, но не выдерживает значительных нагрузок, и потому больше используется для отделки стен.
Поверхность сатинированного керамогранита очень необычно - Структурированный. Этот вид имеет рельефную поверхность разного типа. Есть просто интересные рельефы, а есть имитирующие кожу, натуральный камень, древесину. Более популярен из этой группы керамогранит под дерево(керамический паркет).
Структурированный керамогранит может быть разным

Это тоже керамогранит
Имитация поверхности камня подойдет для укладки на террасе или открытой веранде
Это — вариант » под камень» для стен
Как видите, выбрать есть из чего — под разные требования, для разных задач, интерьеров и помещений. Каждый из видов бывает в десятках цветов и оттенков, очень широк размерный ряд. Минимальный размер плитки керамогранита 5*5 см, максимальный — 120*360 см (это фасадный). Самые популярные размеры для отделки помещений 30*30 см, 45*45 см и 60*60 см. Различной бывает и толщина — от 3 мм до 30 мм. Кстати, стоит сказать, что правильно уложенный керамогранит (на ровную поверхность без пустот) толщиной 3 мм выдерживает такие же нагрузки, как и 3 см.
Рассчитывается количество керамогранита просто: по площади, но требуется еще, как минимум, запас в 10%. Это страховка на случай ошибки в измерениях и на подрезку, которая неизбежна.
На что обратить внимание при выборе
Выбирая керамогранит, надо обращать внимание не только на внешний вид, но и на качество. Перед оформлением покупки сначала осмотрите несколько образцов, желательно из разных пачек. По внешним признакам можно с высокой степенью достоверности сказать, насколько качественный перед вами материал.
- Измерьте размеры плитки. Они на несколько миллиметров могут отличаться от заявленных. Если вы не собираетесь их комбинировать с керамогранитом другого размера, это, может и нестрашно, но знать об этом надо. Хуже, если плитки из разных пачек будут разного размера — укладка керамогранита превратиться в сложную задачу. От такого материала лучше отказаться.
- Посмотрите на торец плитки керамогранита. Если это не структурированная и не сатиновая разновидность, боковая поверхность должна выглядеть также, как и лицевая.
Кроме внешнего вида обращаем внимание на геометрию - Осмотрите заднюю часть. Тут должны быть сформированы ромбы или квадраты. Оптимальный размер ячейки 1,5-2 см, высота выступа — 2-3 мм. Если квадраты больше 3 см и больше, а выступы высокие, перед вами керамогранит низкого качества.
- При покупке проверьте геометрические нескольких плиток, взятых из разных коробок. Измерьте несколько плиток. В идеале разбега в размерах быть не должно. Также проверьте, ровные ли края, не выгнута/вогнута ли поверхность, нет ли «пропеллера».
Если все тесты пройдены успешно, керамогранит можно брать. Но при этом есть еще несколько моментов. Проконтролируйте, чтобы все пачки были одного размера и толщины. Достаньте плитки и сравните оттенки. Часто встречаются достаточно заметные отличия, которые потом при укладке керамогранита бросаются в глаза.
Подготовка основания под укладку керамогранита
Как и большинство отделочных материалов, этот укладывают на ровную, чистую, загрунтованную поверхность. Лучшее основание — бетон или цементнопесчаная стяжка. Перепад высот на 1 квадратный метр не должны быть больше 1 см. Если разница более значительная, заливают выравнивающую стяжку толщиной не менее 3 см.
Качественная укладка керамогранита возможна на идеально ровном основании

Если перепады в рамках допустимого, поверхность сначала очищают от старого покрытия, если таковое было. Заделываются трещины, выбоины и сколы. Затем наносится грунтовка (глубокого проникновения) для лучшей адгезии (сцепления).
На что класть
Так как керамогранит имеет очень низкую гигроскопичность, класть его на обычный цементно-песчаный раствор — зря тратить время и деньги. Вода в поверхность данного материала не впитывается, и плитка практически не держится. Именно при таком клеящем составе отделка «отскакивает». Адгезии с раствором почти нет.
Укладку керамогранита лучше делать на специальный клей

Для тяжелых облицовочных материалов делают специальный клей с большим количеством полимерных добавок. Этот состав имеет в разы большую адгезионную способность, так что даже при очень низкой гигроскопичности хорошо держит керамогранит. Использовать для укладки цементно-песчаный раствор не стоит. В этом случае велика вероятность того, что во время эксплуатации плитки отделятся от пола или стен. Придется из вынимать, выдалбливать раствор, грунтовать и садить керамогранит уже на специальный клей.
Укладка керамогранита своими руками
Перед укладкой надо плитку осмотреть. Многие производители на заводе покрывают лицевую сторону защитным слоем — техническим парафином. Он предотвращает появление царапин при транспортировке. Перед укладкой парафин надо удалить. Счищается он легко — шпателем. Затем поверхность моется мыльной водой (с любым моющим средством), после чего керамогранитную плитку высушивают. Мочить ее пред укладкой запрещено.
Немного об условиях, в которых должны производиться работы. Минимальная температура, при которой можно класть керамогранит — это +5°C, оптимальная +18-20°C. Если он кладется на пол с подогревом, подогрев необходимо выключить не позднее чем за 36 часов до начала работ, а включать можно только через 3-4 суток после окончания укладки.
Способы укладки
Керамогранит можно класть по любым схемам, которые только вам нравятся. Можно комбинировать разные размеры, цвета, встраивать декоративные элементы.
Простые схемы укладки керамогранита

Кроме выбора схемы укладки, необходимо определиться с шириной шва. Она может быть от 0 мм до 10 мм. Бесшовная укладка чаще всего применяется с полированным материалом. Тогда создается эффект сплошной поверхности. Этот вариант совсем не подходит для теплых полов — он не позволяет компенсировать тепловые расширения.
В случае с укладкой со швами, их выдерживают при помощи специальных вставок, традиционно использую пластиковые крестики нужного размера. После схватывания клея, швы заполняют специальной пастой — затирают. Цвет пасты может подбираться «в тон» или быть контрастным.
Варианты комбинирования нескольких цветов

Монтаж на пол
Далее, по инструкции разводится клей (не ошибитесь с объемами, так как застывает он быстро). На прогрунтованый пол, обычным шпателем наносят слой клея. За раз обычно укладывают примерно квадратный метр — больше не успеть и состав начнет твердеть.
Толщина стоя клея зависит от того, насколько ровное основание, от габаритов плитки и свойств клея. Потому говорить в общем сложно. Но по опыту можно сказать, что при укладке на идеально ровный пол плиток керамогранита размерами до 60 см можно брать зубчатый шпатель 8 или 10 и им распределять клей. При осадке фактический слой получается 3-4 мм. Этого вполне достаточно. Если вам нужна более полная информация, ее можно найти на официальном сайте производителя клея.
Начинать кладку надо из центра помещения. Чтобы проще было ориентироваться, на полу малярным мелованным шнуром отбивают две линии, которые в пересечении дают центр. Относительно этого центра и ведется в дальнейшем укладка, двигаясь в одну и другую сторону к стенам.
В центре может находится угол плитки (как на фото ниже) или его середина — зависит от схемы. Вообще, чтобы оценить как будет у вас смотреться выбранная схема раскладки, стоит выложить ее «насухую». Кроме того, что вы сможете реально увидеть, хорошо ли будет все смотреться, и поменять при необходимости схему клади, еще вы будете четко представлять, где какие подрезы нужны и когда какую плитку класть.
Укладка ведется относительно центра помещения

Итак укладка керамогранита происходит в такой последовательности:
- Нанесли клей на пол размерами примерно в 1 кв.м.
- Зубчатым шпателем снимаем излишки, формируя рельеф.
Нанесли клей, сформировали рельеф - Берем сухую плитку керамогранита, укладываем в нужное место. Ее надо хорошенько придавить и подвигать туда-сюда или с круговым смещением.
- Фрагмент ставят на место, вставляют крестики (если укладка со швом).
Поставить плитку, придавить, подвигать - Берут второй, укладывают также.
При кладке часто в швах выступает клей, иногда он попадает на лицевую поверхность. То, что клей выступает — это хорошо, значит под плиткой нет пустот. Но его надо тут же вытирать влажной губкой, затем сухой тряпкой. На поверхности не должно оставаться даже малейших следов: если клей засохнет удалить его практически невозможно.
Вариант укладки керамогранита под дерево

Процесс установки плитки повторяется снова и снова, пока не заполнится все пространство. При этом надо следить за плоскостями, чтобы швы были ровными и одинаковой толщины, а края плитки находились в одной плоскости. Все это проверяется строительным пузырьковым уровнем. При укладке керамогранита своими руками стоит помнить, что откорректировать положение плитки вы можете только на протяжении 4-5 минут после укладки раствора. Далее он схватиться, и ничего вы сделать не сможете. Потому проверяйте плоскости и швы регулярно.
При укладке надо постоянно контролировать плоскость

Обратите внимание, что под плиткой не должно быть пустот, даже минимальных. Тогда отделка будет держаться долго и без проблем. При наличии пустот керамогранит в этом месте может треснуть или отскочить.
Особенности укладки на стену
При монтаже керамогранита на стену используют тоже специальный клей. Особенность состоит в том, что укладку начинают снизу, причем со второго ряда. По периметру стены отмечают линию, где будет заканчиваться первый ряд керамогранитной плитки (с учетом шва). По этой линии прибивают деревянную планку (обязательно ровную) или профиль для гипоскартона. На этой планке будет «стоять» второй и последующий ряды. Это необходимо, так как вес даже одного элемента достаточно солидный, а с клеем получиться и того больше. Если такую плитку просто установить на клей, скорее всего, она поплывет — сдвинется вниз. Потому и необходима эта опора.
При укладке на стену требуется опора — брусок или профиль

Снимают планку после того, как уложен самый верхний ряд, а затем кладут первый. К этому времени второй ряд уже давно «схватился» и сдвинуть его не получится, так что работать можно смело.
Затирка швов
Выбранную пасту разводят по инструкции, которая есть на упаковке. Должна получиться консистенция, близкая к сметане, может, чуть гуще. Берут резиновый шпатель, зачерпывают небольшое количество затирки. Движениями наискосок по отношению к шву, наносят пасту, затем подбирают излишки, проведя шпателем вдоль шва.
Затирка швов керамогранита

Обработав некоторый кусок 1-1,5 квадрата, остатки пасты подтирают чистой влажной губкой. Удалять пасту тоже надо тщательно, она прилипает немногим хуже клея.
Как и чем резать
Керамогранит большой толщины режут на специальном оборудовании с водяным обдувом. Но такой для отделки пола в квартире или доме используется очень редко. Обычно толщина напольной плитки из керамогранита 4-8 мм. Очень редко берут более толстую: слишком затратно, да и вес приличный — сильно нагружать перекрытия без надобности не стоит. Такие экземпляры можно резать хорошим плиткорезом или болгаркой. Диски, если найдете, берите специальные, по керамограниту, если не нашли, можно пробовать диски по камню.
Плиткорез должен быть качественным, с массивной станиной. Очень важно чтобы режущий элемент (ролик или стержень) был хорошего качества.
Ходить по облицованному полу можно через трое суток после укладки.
Фото-примеры отделки помещений керамогранитом
Кухонный фартук — удобно, красиво, надежно

Интересный способ укладки со смещением
Наконец-то дерево может быть и в ванной тоже, правда, из керамики
Шикарный интерьер ванной с использованием полированного керамогранита
Практичный пол на кухне
Интересная коллекция для стен
Лестница с уложенным керамогранитом будет красивой и удобно, за ней легко ухаживать
Вариации на тему природного камня в ванной
Широкие контрастные швы — элемент дизайна
kak-sdelano.ru
Состав, виды, типы и технология производства керамической плитки.
Эмалированная керамическая плитка, предназначенная для облицовки стен внутри помещений. Эмаль придает плитке блеск и позволяет отобразить рисунок любого дизайна, а также защищает керамическое тело плитки от проникновения влаги. Основные форматы производства плитки: 20х20 см, 20х25 см, 25х33,3 см. Внешне бикоттуру можно отличить по: относительно небольшой толщине; красно-коричневой глиняной основе; небольшому весу; глянцевой блестящей эмали. Бикоттура обычно изготавливается коллекциями, состоящими из нескольких цветов: более светлого — чаще всего базового в серии и дополнительных – более темных и с большим количеством декорированных элементов.
Бикоттура применяется для облицовки стен в интерьерах, иногда для покрытия пола (если выбранная серия рекомендована к такому применению), но лишь в тех помещениях, которые не пересекаются напрямую с улицей и где нет риска повредить эмаль механическими частицами (например, песок, пыль).
Это эмалированная керамическая плитка, предназначенная как для облицовки стен, так и для укладки плитки на пол. Некоторые ее виды являются морозостойкими и, соответственно, позволяют применять данную серию снаружи и внутри помещений.
Основные отличия бикоттуры от монокоттуры:
— большая твердость материала;
— наличие серий с низким водопоглощением;
— морозостойкие качества;
— более толстая и прочная основа плитки;
— более твердая, износостойкая эмаль.
Монокоттура используется для облицовки всех типов поверхностей в интерьерах, а особо стойкие виды этой плитки могут применяться как напольное покрытие в общественных местах с не очень интенсивной проходимостью.
Керамический гранит, прокрашенный по всей массе — это неэмалированная керамическая плитка одинарного обжига, изготовливаемая из светлых сортов глины. По типу поверхности керамический гранит разделяют на несколько основных видов:
- Матовый — плитку с такой поверхностью после выхода из печи не обрабатывают дополнительно, поэтому она имеет естественный вид.
- Полированный — необработанную поверхность греса ровно срезают, а затем осветляют. В результате плитка становится сверкающей. После полировки на изделие наносится состав, который закрывает микропоры и делает поверхность менее восприимчивой к загрязнению.
- Полуполированный (лаппатированный – от итальянского lappato – притертый, заглаженный) керамогранит — получают посредством срезания меньшего верхнего слоя греса по технологии поверхностной шлифовки. Обычно таким образом обрабатывают неровную плитку, в результате получается эффектное сочетание полированных и матовых участков. Поверхность лаппатированного керамического гранита легче очищается от загрязнений.
- Большое распространение получил смальтированный керамический гранит (gres porcelanato smaltato). Технология его изготовления очень схожа с производством монокоттуры — нанесенная эмаль, определяющая цвет и фактуру поверхности, обжигается вместе с плиткой в результате одинарного обжига, но при этом материал обладает такими же высокими прочностными и морозоустойчивыми показателями, как керамогранит.
- Еще одной технологией обработки керамического гранита является ретификация. Ретификация — это дополнительная механическая обработка уже готового материала, заключающаяся в срезании боковых кромок с каждой стороны как матовой, так и полированной плитки на специальных станках (при помощи алмазных кругов), для придания всем без исключения плиткам в серии единого размера в каждом формате и одинаково ровных краев изделия. Эта операция позволяет укладывать плитки разных размеров, а также сочетать матовые и полированные плитки одной серии с минимальными швами от 1мм, что является дополнительным преимуществом и практически невозможно для неретифицированных плиток.
Керамогранит, прокрашенный в массе предназначен для облицовки всех типов поверхностей, как внутри помещений, так и на улице. Это могут быть и частные интерьеры, и рестораны, и аэропорты, и бассейны, и тротуарные дорожки и т. д.
Это, как правило, неэмалированная керамическая плитка одинарного обжига. Она изготавливается из красной глины путем экструзии – продавливания через квадратную, прямоугольную или, например, шестиугольную форму. Котто применяется в основном для отделки полов. Метод экструзии позволяет получать плитку самой причудливой конфигурации. Наиболее ходовые размеры: 25×25, 30×30, 20×40 и 40×60 см.
Клинкер — это керамическая плитка одинарного обжига с уплотненной основой, при изготовлении которой применяют метод экструзии, а также технологию прессования (например, у фабрики Paradyz). Иногда ее эмалируют или покрывают так называемой «солью» – тонким слоем прозрачного стекла. Обычно клинкеры используют для облицовки полов как внутри, так и снаружи, а также при строительстве бассейнов — в отделке цоколей, уголков, водостоков, ступеней и различных соединительных элементов.
Крупнопористая плитка с цветной основой и лицевой поверхностью, как правило, покрытой непрозрачной глазурью, на которую нанесен яркий рисунок. Из-за пористой основы майолика легко впитывает воду, поэтому может быть использована только для отделки внутренних стен в сухих помещениях. Несмотря на ограниченную область использования и энергоемкий двойной обжиг, майолика пользуется устойчивым спросом благодаря высоким декоративным достоинствам, прочно ассоциирующимся со стариной.
www.kayros.biz