- Что такое эпоксидная смола и как с ней работать? | Art Smola
- РАЗНИЦА МЕЖДУ ЭПОКСИДНОЙ СМОЛОЙ И ПОЛИУРЕТАНОМ | СРАВНИТЕ РАЗНИЦУ МЕЖДУ ПОХОЖИМИ ТЕРМИНАМИ — НАУКА
- Синтетические смолы (полимеры)
- Эпоксидные смолы
- Циклоалифатическая смола, способ ее получения и ее применение в высокоустойчивом покрытии
- Плотность эпоксидной смолы: расход и технологии применения
- Смолы эпоксидные: разновидности химических составов
- Основные потребительские свойства эпоксидной смолы
- Современные области применения эпоксидной смолы
- Изготовление эпоксидной смолы: дополнение к инструкции
- Эпоксидная смола для творчества: особенности, основные марки
- Изделия из дерева и эпоксидной смолы своими руками
- Плотность эпоксидной смолы: стандартные и фактические показатели
- Вредна ли для здоровья эпоксидная смола и насколько
- Свежая эпоксидная смола лучшего качества от полкило + сопутствующие товары.
- Эпоксидная смола — обзор | Темы ScienceDirect
- Обзор полимерного бетона на эпоксидной и полиэфирной основе и исследование полифурфурилового спирта в качестве полимерного бетона
- 1. Введение
- 2. Эпоксидный полимер и биокомпозиты
- 3. Эпоксидно-полимерный бетон
- 4. Полиэфирный полимер и биокомпозиты
- 5. Полиэфирно-полимерный бетон
- 6. Полифурфуриловый спирт
- 6.1. Предпосылки
- 6.2. Реакции отверждения
- 6.3. PFA Биопластики / Композиты
- 6.4. Механические свойства
- 6.5. Термические свойства
- 6.6. Водостойкость
- 6.7. Продукты, доступные из полифурфурилового спирта
- 7. Заключение и дальнейшие направления деятельности
- Конкурирующие интересы
- Произошла ошибка при настройке пользовательского файла cookie
- Epoxy Resin — (почти) универсальный полимер
- Эпоксидные смолы — Pham — — Основные справочные работы
- Смола или полимер? Какой сегодня наиболее популярный термин для обозначения пластиковых пакетов pac
- Разница между смолой и полимером
Что такое эпоксидная смола и как с ней работать? | Art Smola
Содержание статьиВы часто видите красивые изделия из эпоксидной смолы и думаете, что с этим материалом могут работать только профессионалы? В этой статье мы покажем вам, что работа с эпоксидной смолой – это не так уж и сложно, – достаточно лишь следовать некоторым правилам и запастись терпением 🙂
Что такое эпоксидная смола?Эпоксидная смола представляет собой двухкомпонентный термореактивный жидкий полимер.
Но, избегая непонятные для начинающих мастеров химические термины, можно сказать, что эпоксидная смола – это продукт, состоящих из двух жидких компонентов А и В (где “А” – смола, а “В” – отвердитель), смешивание которых в определённых пропорциях запускает процесс отвердевания с выбросом тепла.
Эпоксидная смола для бижутерииВ результате чего залитая в силиконовые формы, опалубки или поверх заготовок жидкая смола превращается в твёрдые как прочный пластик украшения, картины, подносы, подставки и даже столешницы.
Эпоксидная смола поистине многофункциональна, и область её применения ограничена лишь воображением творца. Но из главных направлений можно выделить следующие (причём для каждой задумки нужна определённая смола с определёнными свойствами).
Resin Art- Картина из эпоксидной смолы автора @tata_resinart
- Менажницы с рисунком из эпоксидной смолы от автора @sea_waves_decor
Resin Art (резинарт) – общее название для всех творений из эпоксидной смолы, но чаще всего под этим термином подразумеваются картины, панно, подносы, подставки, сервировочные доски, посуда и другие изделия, в процессе создания которых смола окрашивается в несколько цветов и выливается в широкую силиконовую форму или на основу-заготовку (арт-борд), может украшаться различным декором.
Для данного направления в основном требуется смола средней густоты или самая густая, например:
БижутерияЮвелирные украшения – название говорит само за себя, хоть и в данном случае не обрабатываются драгоценные камни и металлы, а создаётся их имитация или вовсе сотворяется нечто новое, не существующее в природе, что можно носить в качестве аксессуара: кольца, подвески, браслеты, серьги и тд.
Для их создания необходима жидкая смола, чтобы минимизировать количество пузырей воздуха в заливке:
- Стол из эпоксидной смолы и дерева
- Стол из эпоксидной смолы и дерева
Столы и мебель – тоже вполне понятное направление, но часто для реализации таких крупных проектов требуется много материала и опыта. Для создания мебели эпоксидную смолу в основном соединяют с другими материалами вроде древесины, металла и других наполнителей.
В данном случае не обойтись без жидкой смолы
- Покрытие лодок эпоксидной смолой
- Пол из эпоксидной смолы
Покрытие поверхностей – очень широкое течение, диапазон которого варьируется от создания прочного прозрачного слоя на фотографиях и готовых картинах до ремонта лодок, мебели и даже заливки полов, смола – это ещё и хороший клей-лак.
Для данных целей рекомендуем смолу для создания финишного слоя или термоустойчивого слоя с отличной защитой от царапин:
Есть и множество других уникальных техник работы со смолой, но определить их в конкретное направление довольно сложно или вовсе невозможно, – как мы уже сказали, всё зависит от воображения автора.
После отвердевания смола совершенно безвредна для контакта с кожей человека: вы спокойно можете носить украшения, сделанные из смолы, трогать их. Подробнее об этом вы можете прочитать в статье о безопасности нашей смолы: Насколько опасна эпоксидная смола?
Однако более деликатно дело обстоит с едой: сертификат на безопасный контакт с пищевыми (только холодными) продуктами имеют лишь некоторые смолы (к примеру, наша смола Art Pro 2.0):
Но в жидком виде смола Работа с эпоксидной смолой при смешивании и катализе (процесс отвердевания с выбросом тепла) должна происходить в хорошо проветриваемом/вентилируемом помещении и строго в средствах индивидуальной защиты: в маске-респираторе, очках, перчатках и тд, особенно если у человека есть склонность к аллергии на “химию”. Процесс работы со смолой по вредности можно сравнить с лакокрасочными работами.
Мы предлагаем следующий ассортимент средств защиты:
В каких условиях можно работать с эпоксидной смолой?Работа со смолой должна проводиться в отлично вентилируемом/проветриваемом помещении (вдали от кухонь и жилых комнат) с (важно!)
Если вы живёте в регионе с повышенной влажностью, то рекомендуем использовать нашу эпоксидную смолу Art Pro 2.0, имеющую хорошую защиту от влажности.
Как работать с эпоксидной смолой?Подготовка1. Работа со смолой начинается с подготовки рабочего места: его необходимо застелить защитной плёнкой/полиэтиленом/силиконовым ковриком (от них хорошо отлипает смола после отвердевания), в крайнем случае – бумагой/газетой, ведь в процессе вы точно накапаете материалом на любимый стол.
2. Для смешивания смолы потребуются некоторые аксессуары: тара, в которой вы будете смешивать смолу (2-3 пластиковых стаканчика или пара силиконовых), а также палочки для размешивания и салфетки, чтобы можно было быстро вытереть пролитый продукт. Смола смешивается только по весу (в граммах), поэтому электронные весы тоже будут очень кстати.
3. Не забывайте про средства защиты! Все те же маска-респиратор, перчатки и тд.
4. Также подготовьте основу (арт-борд, холст, силиконовую форму и тд), куда или на что вы будете выливать смолу. Чтобы окрасить смолу, потребуются жидкие красители или порошковые пигменты, – ни в коем случае не берите красители на водной основе, пользуйтесь специальными красителями для смолы. В качестве декора можно взять глиттер (блёстки), стеклянную крошку, кристаллы, сухие цветы, бусины, морские раковины и тд (всё зависит от вашей задумки).
Основная часть работы со смолойВ первом разделе мы упомянули, что эпоксидная смола – это двухкомпонентный продукт, состоящий из баночки со смолой (А) и баночки с отвердителем (В), которые смешиваются в определённых пропорциях. Эти пропорции не универсальны, и у каждой смолы – свои.
1. Для примера мы возьмём нашу эпоксидную смолу многофункциональную «Trasparente» с пропорциями к смешиванию 100:60 (все дальнейшие значения вроде 0,6 и 1,6 будут актуальны только для этой смолы). Для непосвящённых людей данная формулировка может показаться очень сложной, но всё довольно просто! Это означает, что компонент «А» относится к компоненту «В» как 100 частей и 60 частей: на каждые 1 гр компонента А приходится 0,6 гр компонента В. Из этого отношения можно вывести такую формулу: количество «А» умножить на 0,6 = количество «В». К примеру:
50 гр «А» х 0,6 = 30 гр «В», итого – 80 гр смеси компонентов.
Нужно определённое количество общей смеси? Тогда пользуйтесь такой формулой: общее кол-во = кол-во А умножить на 1,6. К примеру, нам нужно 50 гр общей смеси:
50 гр = кол-во А х 1,6
кол-во А = 50/1,6 = 31,25 (можно округлить до 32 гр)
Но это только количество компонента А, нам нужен ещё и компонент В, а формулу по его поиску мы уже знаем:
Кол-во В = 32 гр (А) х 0,6 = 19,2 (округляем до 19)
Итого: 32 гр «А» + «19» гр = 51 гр
К сожалению, не всегда получается получить ровно грамм в грамм именно то количество общей смеси, что мы задумали.
Но если математика даётся вам с трудом или вам не хочется тратить время на бесконечные расчёты, вы можете воспользоваться нашим калькулятором расхода смолы: Калькулятор.
2. После того, как вы отмерили по весам количество каждого компонента (в чистых тарах!), самое время их смешать: влейте «В» в тару с «А» (если позволяет объём) или влейте оба компонента в новую чистую тару (обязательно слейте весь материал, соскребая его со стенок и дна тар) и начните интенсивно мешать по и против часовой стрелке, также соскребая материал со дна и стенок тары. Мешайте в течение 3-5 минут тщательно, но аккуратно, избегая резких всплесков, – так в массу будет попадать меньше пузырей воздуха.
Мы крайне не рекомендуем смешивать (а точнее, оставлять в одной таре на долгое время) большое количество смолы за раз, иначе смола начнёт сильно нагреваться, «вскипит» и сразу застынет (весьма некрасиво). Если вам необходим большой объём, то после смешивания обязательно разлейте смесь на более мелкие объёмы.
3. После смешивания компонентов в смесь можно добавить жидкий краситель или пигмент. Если в вашей работе подразумевается несколько цветов, то сначала разлейте смесь по другим тарам, чтобы в каждую можно было добавить определённый цвет. Добавляйте не более 5 % красителя от общего кол-ва смолы (а лучше и вовсе по чуть-чуть, сразу размешивая и оценивая качество окрашивания), красители и пигменты бывают довольно концентрированными. Хорошо размешивайте краситель в смоле, поскольку его неразмешанные «сгустки» могут также повлиять на отверждение смолы.
На этом же этапе вы можете добавить в смолу блёстки и другой мелкий декор.
4. После проделанных действий мы наконец можем смело вылить смолу в силиконовую форму или на поверхность заготовки. И те и другие должны быть чистыми и полностью сухими. Всплывающие пузыри воздуха можно аккуратно убрать тонкой палочкой или использовать пламя ручной газовой горелки (строго на расстоянии 10-15 см, не задерживаясь на одном месте и не задевая сами заготовки/силиконовые формы). Оставляйте залитые заготовки в сухом, тёплом и тёмном месте (не лишним будет прикрыть их от пыли так, чтобы защитный материал не касался смолы) на время, которое обычно прописывается в инструкции, идущей вместе со смолой (обычно это 24-36 ч).
Если полученный результат вас не устраивает, изделие можно «подкорректировать». К примеру, если на картину из смолы упал мелкий ворс или пылинки во время отвердевания, поверхность можно покрыть дополнительным прозрачным слоем: смешиваете небольшое количество смолы и выливаете на поверхность, отправляя затвердевать по уже описанным правилам.
Для создания финишного слоя вы можете использовать смолу для заливок или продукт для создания термоустойчивого слоя с отличной защитой от царапин:
Другой вид коррекции – шлифовка и полировка. Данный вид обработки изделий не так прост и требует специального оборудования или, хотя бы, инструментов. Так, грубые погрешности можно шлифовать специальным шлифовальным станком или машиной или обычной наждачной бумагой вручную (переходя с крупной зернистости на более мелкую, чтобы поверхность получилась более гладкой). Для более кропотливого шлифования используются небольшие машинки – граверы.
- Шлифовка столешницы из эпоксидной смолы
- Ручная шлифовка изделия из эпоксидной смолы
Для шлифовки изделий мы можем предложить шлифовальные листы разной зернистости:
Однако после шлифовки изделие теряет глянец, который можно восполнить полировкой или лаком. Полируют изделия обычно с помощью специального средства – полироли, которую растирают по поверхности изделия тряпочками/губками для полировки или полировальным кругом. Но если вы решили вместо этого покрыть лаком – выбирайте хороший, нежелтеющий. Лак можно также заменить смолой, однако только в том случае, если есть возможность покрытия поверхности с помощью литья, ведь если наносить смолу кистью, она может лечь неравномерно.
- Полировка столешницы из эпоксидной смолы
- Полировка небольших изделий из эпоксидной смолы
К очень большому сожалению, да. Некоторые некачественные смолы могут пожелтеть уже спустя месяц после создания украшения, поэтому используйте только проверенные профессиональные эпоксидные смолы с хорошей защитой от пожелтения. К примеру, наши 🙂
Мы даём гарантию на то, что изделия из нашей смолы не будут желтеть в течение 4-5 лет, а если хранить их в дали от солнечного и уф-света, то этот срок может увеличиться до 10 лет!
- Пользуйтесь средствами индивидуальной защиты при работе со смолой: маска-респиратор, очки, перчатки и тд.
- Смешивайте эпоксидную смолу строго по пропорциям, используя точные весы.
Мешайте в течение 3-5 минут, соскребая материал со стенок и дна тары. Работайте в хорошо проветриваемом/вентилируемом помещении с низкой влажностью при температуре не ниже 20 и не выше 25-27 °C.
- При заливке эпоксидной смолы в формы или на заготовки, избегайте влажных поверхностей, не добавляйте в смолу красители на водной основе.
- Пузырьки воздуха, попавшие в смолу при смешивании, можно удалить с поверхности заливки с помощью маленькой палочки вручную или применяя пламя газовой горелки (строго по правилам).
Команда Арт Смолы всегда готова ответить на все интересующие вас вопросы в комментариях 🙂
РАЗНИЦА МЕЖДУ ЭПОКСИДНОЙ СМОЛОЙ И ПОЛИУРЕТАНОМ | СРАВНИТЕ РАЗНИЦУ МЕЖДУ ПОХОЖИМИ ТЕРМИНАМИ — НАУКА
В ключевое отличие между эпоксидной смолой и полиуретаном заключается в том, что эпоксидная смола содержит эпоксидные группы, тогда как полиуретаны содержат уретановые связи. С точки зрения применения
В ключевое отличие между эпоксидной смолой и полиуретаном заключается в том, что эпоксидная смола содержит эпоксидные группы, тогда как полиуретаны содержат уретановые связи. С точки зрения применения, основное различие между эпоксидной смолой и полиуретаном состоит в том, что эпоксидные смолы могут выдерживать умеренные температуры, в то время как полиуретаны могут выдерживать высокие температуры.
И эпоксидная смола, и полиуретан являются полимерными материалами. Полимер — это макромолекула, содержащая большое количество небольших повторяющихся звеньев (мономеров). Эти мономеры соединяются друг с другом с образованием полимера. Термин эпоксидная смола используется для обозначения эпоксидных смол, которые состоят из функциональных групп эпоксидной смолы в повторяющемся образце. Полиуретан также является полимерным материалом, содержащим уретановые связи.
1. Обзор и основные отличия
2. Что такое эпоксидная смола
3. Что такое полиуретан
4. Параллельное сравнение — эпоксидная смола и полиуретан в табличной форме
5. Резюме
Что такое эпоксидная смола?
Эпоксидная смола или эпоксидная смола — это класс полимерных материалов, состоящих из функциональных эпоксидных групп. Это форма полиуретана. Эти полимеры могут быть как низкомолекулярными, так и высокомолекулярными полимерами, по меньшей мере, с двумя эпоксидными группами.При производстве в промышленных масштабах главным источником эпоксидной смолы является нефтяное масло. Однако есть и некоторые источники растительного происхождения.
Эпоксидные смолы могут реагировать друг с другом посредством каталитической гомополимеризации и образовывать поперечные связи между собой. Или же эпоксидные смолы могут реагировать с некоторыми другими соединениями, такими как;
- Амины
- Кислоты
- Фенолы
- Спирты
- Тиолы
Это сореагенты. Некоторые другие названия этих сореагентов — отвердители или отвердители. Следовательно, реакции сшивания, которые эпоксидные смолы претерпевают с этими отвердителями, относятся к «отверждению». В процессе сшивания образуется термореактивный полимер, который имеет благоприятные химические и механические свойства.
Методика расчета конкретного количества эпоксидных групп, присутствующих в эпоксидной смоле, заключается в следующем:
- Соотношение между количеством эпоксидных групп и массой полимерного материала дает конкретное количество эпоксидных групп в эпоксидной смоле.
- Единица измерения — «моль / кг». Мы иногда называем этот термин «эпоксидным числом».
Бисфенол А эпоксидная смола
Этот тип эпоксидных смол является результатом комбинации эпихлоргидрина и бисфенола A. Эта комбинация дает диглицидиловые эфиры бисфенола A. Если мы увеличим количество бисфенола А (по сравнению с эпихлоргидрином), получится полимерный материал с высокой молекулярной массой. Этот полимерный материал является линейным и представляет собой полутвердые кристаллические материалы.
Бисфенол F эпоксидная смола
Здесь мы используем бисфенол F вместо бисфенола A, но способ образования полимера такой же, как и у эпоксидной смолы бисфенола A (как обсуждалось выше).
Новолачная эпоксидная смола
Новолачные эпоксидные смолы образуются, когда фенолы реагируют с формальдегидом и подвергаются гликозилированию эпихлоргидрином. В большинстве случаев этот полимерный материал показывает высокую химическую стойкость и стойкость к высоким температурам, но низкую гибкость.
Алифатическая эпоксидная смола
Эти полимеры образуются путем гликозилирования алифатических спиртов или полиолов. Этот полимерный материал имеет низкую вязкость при комнатной температуре.
Что такое полиуретан?
Полиуретан — это полимерный материал, имеющий уретановые связи (карбаматные связи). Изоцианаты и полиолы подвергаются полимеризации с образованием полиуретана. Хотя название полиуретан дает представление о том, что полимер состоит из мономеров уретана, на самом деле он состоит из уретановых связей, а не мономеров.
При использовании мономеров для производства полиуретанов изоцианаты должны иметь по крайней мере две функциональные группы, которые позволяют им подвергаться полимеризации. Более того, полиол также должен иметь по крайней мере две гидроксильные группы на молекулу. Реакции между мономерами в этой полимеризации представляют собой экзотермическую реакцию, при которой тепло отводится от реакционной смеси. Уретановая связь образуется, когда группа –N = C = O изоцианата реагирует с группами –OH спирта с образованием уретановой связи (-NH-C (= O) -O).
В чем разница между эпоксидной смолой и полиуретаном?
Эпоксидная смола против полиуретана | |
Эпоксидная смола или эпоксидная смола — это класс полимерных материалов, которые состоят из функциональных эпоксидных групп. | Полиуретан — это полимерный материал с уретановыми связями.![]() |
Мономеры | |
Мономерами эпоксидных смол являются фенолы и эпихлоргидрин, но мономеры могут варьироваться в зависимости от типа эпоксидной смолы. | Мономерами полиуретана являются полиолы и изоцианаты. |
Сопротивление | |
Проявляют сравнительно низкую стойкость к органическим кислотам. | Обладает высокой устойчивостью к коррозии, неорганическим кислотам, щелочным растворителям, органическим щелочам и многим другим растворителям. |
Терпимость | |
Эпоксидные смолы устойчивы к умеренным температурам. | Полиуретаны выдерживают высокие температуры. |
Резюме — Эпоксидная смола против полиуретана
Эпоксидные смолы — это разновидность полиуретанов. Эти полимеры получили свое название из-за повторяющихся связей, присутствующих в полимерном материале вместо мономеров, используемых для производства. Разница между эпоксидной смолой и полиуретаном заключается в том, что эпоксидная смола содержит эпоксидные группы, тогда как полиуретаны содержат уретановые связи.
Синтетические смолы (полимеры)
Категория: Облицовка камнем
Синтетические смолы (полимеры)
По способу производства полимеры подразделяют на два класса: класс А — полимеры, получаемые цепной полимеризацией, и класс Б — полимеры, получаемые поликонденсацией и ступенчатой полимеризацией.
Полимеризационные полимеры (класс А). При полимеризации происходит соединение одинаковых или различных молекул. Получающийся полимер обладает молекулярной массой, равной сумме молекулярных масс реагирующих молекул мономера. Никаких побочных продуктов при полимеризации не образуется.
Полиэтиленовые смолы отличаются хорошей гибкостью, сохраняющейся при температурах до —60 °С, практически абсолютной водостойкостью и стойкостью к агрессивным средам. Полиэтиленовые смолы применяют при изготовлении гидроизоляционных пленок, водопроводных труб, трубопроводов для едких жидкостей и некоторых предметов санитарно-технического оборудования.
Полипропиленовые смолы получают полимеризацией пропилена СН3—СН = СН2, представляющего собой газ, получаемый при крекинге нефтепродуктов. Из пропилена изготовляют трубы, детали химической аппаратуры, антикоррозионные и декоративные материалы, паро- и газонепроницаемые пленки.
Поливинилхлоридные (полихлорвиниловые) смолы получают полимеризацией винилхлорида СНг = СНС1. При обычной температуре — это бесцветный газ с запахом эфира.
Поливинилхлоридная смола, полученная водосуспен- зионным способом, представляют собой гранулы крупностью 0,01—0,3 мм и плотностью 1,4 г/см3. Она обладает большой теплостойкостью, морозостойкостью и диэлектрическими свойствами. Поливинилхлорид применяют для изготовления линолеума, гидро- и газоизоляционных пленок.
Полиизобутиленовые смолы получают полимеризацией изобутилена СН2=С(СН3)2 при температуре около 100 °С в присутствии галоидных соединений бора, алюминия или титана.
Полиизобутилен представляет собой каучукоподоб- ный эластичный материал плотностью 0,91—0,93 г/см3. Он применяется в качестве антикоррозионного и как компонент гидроизоляционных материалов. Низкомолекулярный полиизобутилен используют для изготовления лака и мастик.
Полистирольные смолы получают полимеризацией стирола (углеводородвинилбензола — фенилэтилена) С6Н5СН = СН2.
Полистирольные смолы бесцветны, хорошо окрашиваются в разные цвета, легко формуются, но обладают хрупкостью, невысокой теплостойкостью.
Полистирольные смолы применяют для изготовления латексов, эмалей и гидроизоляционных пленок.
Поливинилацетатные смолы — полимер винилацета- га (сложный эфир уксусной кислоты) и винилового спирта СН2 = СН—ОН.
Винилацетат представляет собой бесцветную легкоподвижную жидкость. Поливинилацетат — это прозрачный бесцветный полимер, неустойчивый к действию кислот и щелочей, слабо набухает в воде, растворим в спиртах и сложных эфирах, ароматических углеводородах и т. д.
Поливинилацетатные смолы обладают высокой адгезией к камню, стеклу и т. д., поэтому их используют в производстве лаков и клеев, для приготовления эмульсий, полимербетонов и растворов, применяемых при внутренней отделке зданий.
Полиакрилатные смолы получают на основе производных акриловой СН2 = СН—СООН и метакриловой СН2= = С(СН3)СООН кислот. Они представляют собой бесцветную прозрачную стекловидную массу.
Полиакрилатные смолы применяют для изготовления гидроизоляционных пленок, придания водонепроницаемости бетону (раствору), а также в качестве грунтовок при внутренней отделке стен.
Инден-кумароновые смолы представляют собой смесь продуктов полимеризации кумарона и индена. Эти смо- си выпускают в виде кусков или чешуек плотностью 1,05—1,2 г/см3. При нагревании полимер дает своеобразный запах. Инден-кумароновые смолы применяют для производства латексов, красок, лаков и клеев.
Поликонденсационные полимеры (класс Б). Поликонденсацией называют процесс образования высокомолекулярного вещества при соединении большого количества одинаковых или разных полиреактивных молекул низкомолекулярных веществ, происходящий с выделением воды, хлористого водорода, аммиака и других веществ.
Фенолоформальдегидные смолы получают при взаимодействии фенолов с формальдегидами. К фенолам относят собственно фенол, крезолы и резорцин. Для совместной конденсации с фенолом и формальдегидом используют также анилин.
Фенолоформальдегидные смолы отличаются высокой прочностью и теплостойкостью. Применяют их в производстве древесностружечных и древесноволокнистых плит, слоистых пластиков, а также для изготовления лаков, клеев и мастик.
К фенолоформальдегидным полимерам относятся: – бакелитовый лак, применяемый для получения покрытий, стойких к действию кислот, солей и ряда растворителей; – полимер Б для горячего склеивания асбестоцемента и каменных материалов;
резорцинформальдегидный полимер ФР-12, используемый при изготовлении клея холодного отверждения для склеивания строительных конструкций.
Аминоформальдегидные смолы, из которых наиболее важны мочевиноформальдегидные, получают в результате гголиконденсации мочевины и меламина с формальдегидом в определенных, строго контролируемых условиях, в виде раствора полимера и сухого полимера.
Аминоформальдегидные смолы бесцветны, сравнительно дешевы и применяются для изготовления теплоизоляционных материалов, слоистых пластиков и клеев.
Полиуретановые смолы представляют собой высоко-плавкие линейные кристаллические полимеры, получаемые взаимодействием диизоцнанатов с многоатомными, чаще двухатомными, спиртами. Они отличаются низкой температурой плавления, незначительной гигроскопичностью, высокой атмосферостойкостью, устойчивостью к воздействию кислорода воздуха и озона, кислот и щелочей.
Полиуретаны на основе полиэфиров используют для изготовления клеев марок ПУ-2 и ПУ-2/10, применяемых для склеивания строительных конструкций и каменных материалов.
Кремнийорганические смолы представляют собой особую группу высокомолекулярных соединений, в которых совмещены свойства, присущие некоторым органическим и неорганическим веществам. Эти смолы содержат в своем составе кремний наряду с органической частью смолы.
Кремнийорганические смолы обладают высокой теплостойкостью и гидрофобностыо. Их прочность и другие физические и механические свойства в меньшей мере зависят от колебаний температуры по сравнению с обычными смолами.
Кремнийорганические смолы служат для получения различных изделий, стойких к действию повышенных температур (400—500 °С). Эти смолы применяют в качестве добавок в бетонные и растворные смеси и в виде защитных покрытий для известняка, мрамора, травертина, бетона и других природных и искусственных каменных материалов, чтобы повысить их долговечность. Пропитка оказывает защитное действие в течение 6—10 лет, после чего должна быть возобновлена.
Кремнийорганические соединения для поверхностной пропитки изделий из природного камня и других строительных конструкций известны под названием гидрофо- бизирующих жидкостей.
Эпоксидные смолы получают поликонденсацией эпихлоргидрина с фенолами, спиртами или аминами. Типичным представителем этих полимеров считают поли- эпоксиды, которые при малой плотности 1,14—1,25 г/см3 обладают высокой адгезией к металлам и каменным материалам, малой усадкой, хорошей кпслотостойкостыо и значительной прочностью.
Эпокеидно-диановые неотверждспные смолы (ГОСТ !0587 76) выпускают следующих марок: ЭД-22, ЭД-20, ЭД-16, ЭД-8. Обозначения: Э — эпоксидная, Д —дифе- пилпропановая; цифры указывают нижний предел нормы содержания эпоксидных групп.
Эпоксидные неотвержденные полимеры представляют собой термопластичные продукты от желтого до коричневого цвета консистенцией от вязкой жидкости до твердого хрупкого материала. Хорошо растворяются в сложных эфирах, диоксане и хлорбензоле. Растворы и расплавы этих полимеров можно хранить длительное время.
Отвержденные эпоксидные полимеры характеризуются неплавкостыо и нерастворимостью. Отвердителями служат различные полимеры (фенолоформальдегидные, полиамидные, мочевино-меламиноформальдегпдные), а также полиспирты, амины, карбоновые кислоты, дифенолы.
Эпоксидные полимеры служат для получения клеев, используемых при склеивании плит из природного камня, керамики, бетона и различных строительных конструкций, а также при изготовлении компаундов (композиция, состоящая из эпоксидного полимера, наполнителя и огвердителя), которые могут быть использованы при ремонте облицовок из природного камня.
Синтетические смолы представляют собой органические комолекулярные вещества. Высокомолекулярными назыв вещества с большой молекулярной массой, молекулы которы. разованы десятками и даже сотнями тысяч атомов. Поэтому кие вещества называются полимерами.
Смолы производят в виде порошков, гранул или вязких костей. Твердые смолы применяются при заводском изготовлении изделий, а жидкие как при заводском, так и непосредственно на строительной площадке для приготовления клеев, гидроизоляционных составов, полимербетонов и других строительных смесей.
Все смолы по своим физическим свойствам можно разделить на две большие группы: термопластичные, существенно изменяющие упругость под действием температуры вплоть до расплавления, и термореактивные, которые после полимеризации незначительно изменяют свои свойства под действием температуры.
Наибольшее применение в строительстве находят карбомид-ные и фенолформальдегидные смолы. Их применяют для изготовления бумажных пластиков, клеев, лаков, гидроизоляционных материалов.
Широко также применяются полистирол, полиэтилен, поли-УРетан, полиэфирные смолы. Из них изготавливают пленки, трубы, плитки, теплоизоляционные материалы, бумажные пластики, клеи, лаки, гидроизоляционные составы и т. п.
Такие смолы, как полипропилен, эпоксидные, применяют мень-Ше в виду их высокой стоимости. Эти смолы обладают большой Тепловой и коррозионной стойкостью. Они предназначены для изготовления стеклопластиков, клеев, защитных и гидроизоляционных составов.
Синтетические латексы и эмульсии представляют собой водные дисперсии синтетических смол. Смола находится в них в виде мельчайших частиц размером 0,05 до 5 мк. После нанесения ла-тексов на поверхность вода испаряется и образуется полимерная пленка. Латексы и эмульсии имеют небольшую вязкость, что позволяет вводить в них большое количество наполнителей.
Латексы применяются для получения герметиков, гидроизоляционных составов, в качестве добавки в бетон, для приготовления красок, приклеивающих мастик и т. д.
Облицовка камнем — Синтетические смолы (полимеры)
Эпоксидные смолы
Эпоксидные смолы
Эпоксидными смолами называются олигомерыОлигомеры (от греч. oligos – малый, немногочисленный и meros – часть) — полимеры с небольшим числом структурных (мономерных) звеньев и невысокой молекулярной массой., содержащие эпоксидные группы и способные под действием отвердителей (полиаминов и др.) образовывать пространственно сшитые полимеры.Наиболее распространённые эпоксидные смолы — продукты конденсации эпихлоргидрина и бисфенола А
Систематическое название бисфенола А:
2,2-бис(4-гидроксифенил)пропан.Нередко употребляется техническое название – дифенилолпропан. (дианаДиан – название бисфенола А, данное в честь русского химика Александра Дианина, впервые получившего это соединение (1891 г.).). Эти смолы часто называют эпоксидиановыми (англ. «epoxy-dian resins») в честь русского химика А.

- Эпихлоргидрин реагирует с дианом по типу нуклеофильного присоединения с раскрытием эпоксидного циклаНуклефильное присоединение
Нуклеофил — атом кислорода фенольного гидроксила.. Реакцию проводят в присутствии основанийОснования (например, HO– в составе NaOH) усиливауют нуклеофильные свойства фенольных ОН-групп, переводя их в анионы:~C6H4-OH + HO– → ~C6H4-O– + H2O (в щелочной среде). При соотношении эпихлоргидрин : диан = 2 : 1 образуется диэпоксид:
- Далее диан и диэпоксид, являясь бифункциональными соединениями, вступают в процесс поликонденсации, который идёт как последовательность реакций присоединения и не сопровождается выделением побочных продуктов (в отличие от большинства процессов поликонденсации, основанных на реакциях замещения).
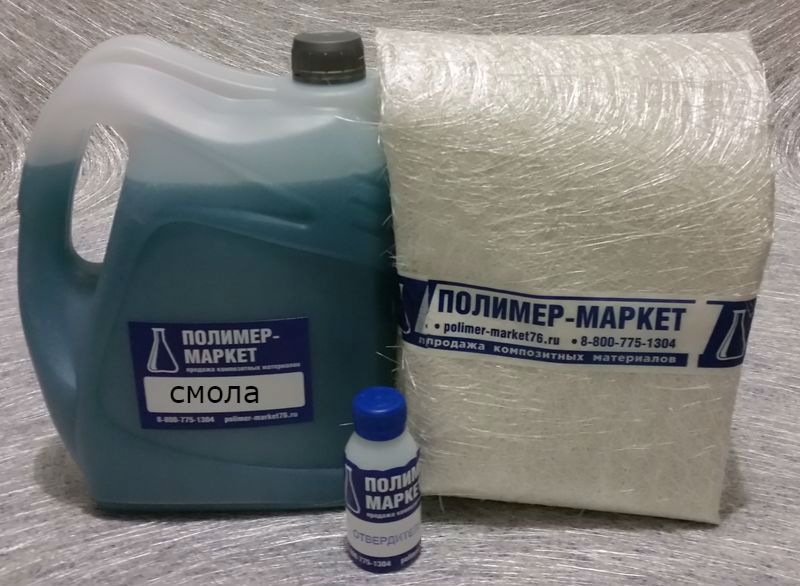
На заключительной стадии процесса образуется растворимая вязкотекучая эпоксидная смола c невысокой молекулярной массой (450-4000):
где
Для отверждения эпоксидиановой смолы обычно используют полиэтиленполиамины Н2N(СН2СH2NH)nH (где n=1-4) или гексаметилендиамин H2N(CH2)6NH2, которые, присоединяясь по эпоксидным группам, образуют трёхмерную сетчатую структуру:
Таким образом, после отверждения эпоксидная смола превращается в пространственно сшитый полимер и утрачивает способность к растворению и плавлению. Следует отметить, что процесс отверждения происходит по типу реакций присоединения, без выделения низкомолекулярных летучих веществ. Это является достоинством с точки зрения получения однородных монолитных материалов. По прочности продукты отверждения эпоксидных смол превосходят материалы на основе других синтетических смол и широко применяются в различных промышленных сферах (судостроение, авиастроение, ракетоостроение, автомобилестроение и т.

В композиции на основе эпоксидных смол перед отверждением обычно вводят различные наполнители — порошки, высокопрочные сплошные и рубленые волокна из ткани, стекловолокна и др. материалов. Композиции холодного отверждения (~20°С) используют в качестве клеев, герметиков, заливочных компаундов, эпоксидных лаков, эмалей и других защитных покрытий в случаях, когда по условиям эксплуатации нежелателен нагрев. Композиции горячего отверждения (100-300°С) применяют в качестве связующих для высокопрочных армированных пластиков, композиционных высокотемпературных материалов и др.
В последнее время стало популярным использование эпоксидных смол для изготовления: наливных полов, дизайнерской мебели, светильников, столешниц, бижутерии и т.п.
Циклоалифатическая смола, способ ее получения и ее применение в высокоустойчивом покрытии
Область техники, к которой относится изобретение
Настоящее изобретение касается синтеза циклоалифатической смолы, содержащей силаны с эпоксидными и алкокси-силанольными функциональными группами; и ее применения в композициях покрытия, особенно в атмосферостойких.
Уровень техники
Эпоксидные смолы хорошо известны своей прекрасной химической устойчивостью, характеристиками сцепления и твердости, так что они применяются в лакокрасочной промышленности главным образом в качестве грунтовок для новых сооружений или для технического обслуживания существующих сооружений. Также известно, что эпоксидные смолы, главным образом получаемые из эпихлоргидрина и бисфенола А, меняют блеск в глянцевых покрытиях при воздействии солнечного света, покрытия становятся желтыми вследствие окисления двойных связей в молекуле бисфенола, что приводит к явлению деградации поверхности, известному как «выцветание»; поэтому их редко применяют в качестве внутренних покрытий.
Успехи в области производства эпоксидных смол в последние годы сделали доступными гидрированные эпокси-циклоалифатические смолы, которые обладают высокой устойчивостью к солнечному свету, однако их реакционная способность в отношении аминных отвердителей намного ниже, чем у обычных ароматических смол. Существует также большое число силанов с эпокси-функциональными группами, которые работают аналогично эпокси-циклоалифатическим смолам, обеспечивая свойства химической устойчивости, гладкости и эластичности эпоксидных смол, а также атмосфероустойчивости, сравнимые с таковыми у силанов.
Полисилоксановые смолы применяются в покрытиях, устойчивых к высоким температурам, которые образуют очень жесткие, но очень хрупкие пленки с плохими декоративными характеристиками, помимо того, что они намного более дорогие, чем эпоксидные или алкидные смолы, применяющиеся в декоративных целях и в промышленности. С такими контрастными особенностями, оба типа смол недостаточно хороши для введения в идеальное покрытие, которое соответствует высоким эксплуатационным требованиям к твердости, гладкости, блеску и прочности, которые желательны в лакокрасочной промышленности; недавние исследования показали, что оба типа указанных контрастных смол дополняют друг друга при комбинировании в подходящих количествах и типах, при формировании гибридных эпокси-полисилоксановых смол.
В патенте США №4,250,074 (Raymond Е. Foscante et al., выдан в 1981) описана процедура гибридизации, где эпоксидные и силановые полимеры смешивают, они заканчивают свои реакции полимеризации одновременно, эпоксидный полимер реагирует с дифункциональным амином, и полисилоксан претерпевает внутреннюю реакцию по механизму гидролитической поликонденсации. Гибридный полимер представляет собой взаимопроникающую полимерную сетку (IPN), которая формирует пленку, устойчивую к воздействию УФ-облучения без выцветания и имеющую хорошую устойчивость блеска, но получаемая пленка хрупкая и имеет низкую ударопрочность и абразивостойкость.
В патенте США №5,618,860 (Norman R. Mowrer et al., выдан в 1997) описано применение эпокси-циклоалифатических смол, смешанных с гидролизованными силанами, которые реагируют с амино-силановым отвердителем и подходящим металлорганическим катализатором. Данный гибридный полимер дает пленку, имеющую более высокую твердость и атмосфероустойчивость, по сравнению с чистой эпоксидной пленкой, однако сохраняются проблемы с жесткостью, низкой эластичностью и ударопрочностью вследствие непрерывной реакционной способности остающихся радикалов.
В более поздних изобретениях, таких как Заявка на Патент США 2007/0213492 (Norman R. Mowrer et al., опубликована 13 сентября 2007) (PPG), циклоалифатические смолы также применяют в гибридизации с силановыми интермедиатами, такими как метокси-функциональный DC-3074 от Dow. Другие примеры включают силанол-функционализированные смолы, такие как DC-840 и Z6018 также от Dow Corning, которые также претерпевают гидролитическую поликонденсацию, которой способствует предварительный гидролиз метокси-радикалов из интермедиатов и вода из атмосферного воздуха. В этом наиболее недавнем развитии темы, силановые интермедиаты требуют обязательного перемешивания с гидрированными эпоксидными смолами или силанами, имеющими эпоксидные функциональные группы.
Постоянно имеется потребность в защите камня, металла, дерева, пластика, цемента и других субстратов. Это требует применения покрытий, имеющих очень хорошую ударопрочность, жесткость, атмосфероустойчивость и устойчивость блеска, и гибридизация с эпоксидными или другими смолами, такими как акриловые, полиэфирные или полисилоксановые полимеры, позволяет достичь особых эксплуатационных характеристик и стоимости.
Краткое описание изобретения
Первой целью настоящего изобретения является разработка смолы, соответствующей высоким эксплуатационным требованиям по твердости, гладкости, блеску и прочности, имеющимся в лакокрасочной промышленности.
Другой целью настоящего изобретения является разработка покрытий, имеющих очень высокую ударопрочность, жесткость, атмосфероустойчивость и устойчивость блеска.
Другой целью настоящего изобретения является разработка покрытий, позволяющих проводить гибридизацию с эпоксидными или другими смолами, такими как акриловые, полиэфирные или полисилоксановые полимеры.
Всех поставленных целей удалось достичь посредством получения циклоалифатической смолы путем синтеза циклоалифатической смолы, содержащей продукт реакции гидрированного бисфенола и силанов с эпоксидными и алкокси-силанольными функциональными группами; и ее применения в композициях покрытия. Указанная циклоалифатическая смола позволяет избежать тройного смешивания эпоксидных смол с функциональными алкокси-силанами и функциональными силанолами, реагирующих с амино-силанами с получением гибридных смол для приготовления коррозионностойких покрытий для промышленного применения.
Подробное описание изобретения
В первом варианте осуществления настоящего изобретения описано получение циклоалифатической смолы, содержащей силаны с эпоксидными и алкокси-силанольными функциональными группами, реакцией гидрированного бисфенола и эпокси-функционального силана с концевыми метокси-, этокси- или пропокси-группами.
Циклоалифатическую смолу получают реакцией этерификации эпокси-функционального силана, имеющего общую формулу:
где каждый R1 независимо выбран из метила, метокси-, этокси- или пропокси-группы; ʺXʺ может представлять собой эпокси-циклогексильную или глицидокси-группу; и ʺnʺ представляет собой целое число от 1 до 6, с гидрированным бисфенолом, имеющим формулу
где R2 может представлять собой метил, этил или атом водорода.
Эпокси-функциональный силан составляет от 30 до 75%, предпочтительно от 50 до 65 вес. % от общего веса компонентов циклоалифатической смолы.
Гидрированный бисфенол составляет от 30 до 70%, предпочтительно от 35 до 65 вес. % от общего веса компонентов циклоалифатической смолы.
Предпочтительно, гидрированный бисфенол выбран из гидрированного бисфенола A или гидрированного бисфенола F.
Предпочтительно, эпокси-функциональный силан может представлять собой 3-глицидилокси-пропил-триметокси-силан, 3-глицидилокси-пропил-триэтокси-силан, γ-глицидокси-пропил-триэтокси-силан, 3-глицидилокси-пропил-трипропокси-силан, 3-глицидокси-пропил-метил-диэтокси-силан, 2-(3,4-эпокси-циклогексил)этил-триметокси-силан, β-(3,4 эпокси-циклогексил)этил-триэтокси-силан, более предпочтительно эпокси-функциональный силан представляет собой 3-глицидилокси-пропил-триметокси-силан.
Эпокси-функциональный силан содержит глицидильную функциональную группу на одном конце и метокси-, этокси- или пропокси — радикалы, связанные с атомом кремния эпокси-функционального силана. Реакцию проводят при низкой температуре в диапазоне от 90°C до 160°C, в присутствии металлорганического катализатора. В качестве продукта данной реакции образуется спирт, который соответствует типу применяемого эпокси-функционального силана, экстрагируется от 70 до 90% от ожидаемого стехиометрического выхода, метокси-функционализированный силаны предпочтительны вследствие более высоких получаемых выходов.
Циклоалифатические кольца гидрированного бисфенола придают молекуле улучшенные механические и химические свойства, когда комбинируются с эпокси-функциональным силаном путем алкоголиза между гидроксильными концевыми группами гидрированного бисфенола и концевыми метокси-, этокси- или пропокси-группами эпокси-функционального силана, формируя в молекуле оксирановую концевую группу, которая может реагировать с аминовыми или амино-силановыми отвердителями, и один или больше метокси- или этокси-фрагментов доступны для комбинирования с другими функциональными группами с образованием гибридов, например, с полисилоксанами, акриловыми соединениями или эпоксидами.
Реакцию этерификации можно проводить в молярном соотношении от 0. 7:1.0 до 2.5:1.0 между эпокси-функциональным силаном и гидрированным бисфенолом, предпочтительно один или два моля эпокси-функционального силана на моль гидрированного бисфенола; при использовании большего мольного количества эпокси-функционального силана доступно больше концевых групп, при этом формируется более плотное и сильное связывание с опцией формирования гибридов с другими типами смол.
Предпочтительно, эпокси-функциональный силан должен содержать по меньшей мере две доступные концевые метокси-, этокси- или пропокси-группы в молекуле, по меньшей мере одна из них может реагировать с гидроксильными группами гидрированного бисфенола. В этой реакции образуется спирт, который соответствует типу применяющегося эпокси-функционального силана, и образующийся спирт необходимо экстрагировать, т.к. реакция является обратимой.
Количество генерируемого спирта одинаково во всех случаях, поскольку оно зависит от количества гидроксильных концевых групп гидрированного бисфенола.
Реакция получения циклоалифатической смолы ускоряется металлорганическими катализаторами, такими как октоат цинка или лаурат олова.
Благодаря типу компонентов, применяемых в получении циклоалифатической смолы, добавление воды не требуется.
Необязательно можно добавлять алкил силикат во время процесса получения циклоалифатической смолы, где указанные алкил-силикаты содержат метальные, этильные, пропильные, бутильные или гидроксильные концевые группы, которые быстрее реагируют с непрореагировавшими концевыми метокси-, этокси- или пропокси-группами в реакции этерификации между гидрированным бисфенолом и эпокси-функциональным силаном.
Предпочтительно, алкил силикат выбран из группы, состоящей из тетраметил ортосиликата, тетраэтил ортосиликата, тетрапропил ортосиликата или тетрабутил ортосиликата, где алкил-силикаты могут быть гидролизованы или частично гидролизованы.
В этом случае циклоалифатическую смолу получают из:
(a) 30-60% гидрированного бисфенола, предпочтительно 35-50 вес. %, от общего веса компонентов циклоалифатической смолы;
(b) 30-70% эпокси-функционального силана, предпочтительно 30-65 вес. %, от общего веса компонентов циклоалифатической смолы;
(c) 10-40 вес. % алкил силиката, от общего веса компонентов циклоалифатической смолы, и
(d) до 5 вес. % металл органического катализатора, такого как октоат цинка или лаурат олова, от общего веса компонентов циклоалифатической смолы.
Механизм отверждения циклоалифатической смолы может работать с полифункциональными аминами или амино-силанами, которые могут реагировать с глицидилами, и по реакции непрореагировавших концевых метокси-групп с гидроксильными группами, образующимися при реакции эпокси-оксиранов с аминами. Данная циклоалифатическая смола обладает потенциалом к формированию эпокси-полисилоксанов, описанных выше, или ее можно смешивать с другими смолами, такими как эпоксидные смолы, главным образом для усиления ее химической устойчивости. Ее можно также модифицировать другими полимерами, такими как акриловые полимеры, в этом случае можно получить тройную гибридную акрило-эпокси-полисилоксановую смолу, имеющую высокую химическую и механическую устойчивость и высокую стабильность внешнего вида.
Во втором варианте осуществления настоящего изобретения описано двухкомпонентное полисилоксан-эпоксидное покрытие, как в случае смолы по первому варианту осуществления. Надлежащим образом полученное покрытие обладает ударопрочностыо, жесткостью, эластичностью, атмосфероустойчивостью и устойчивостью блеска, и данное покрытие содержит:
(a) 15-55 вес. % циклоалифатической смолы, полученной согласно первому варианту осуществления настоящего изобретения;
(b) 10-20 вес. % амино-полифункционального отвердителя или амино-силана с концевыми метокси- или этокси-группами;
(c) до 5 вес. % металлорганического катализатора, и
(d) пигменты и агрегаты.
Благодаря такому составу циклоалифатической смолы, не требуется добавление воды в композицию покрытия или в процессе его получения.
Отвердитель может представлять собой амино-полифункциональную молекулу, например алифатический амин, аминный аддукт, полиамидоамин, циклоалифатический амин, ароматические амины, являющиеся основаниями Манниха, которые могут быть полностью или частично замещены аминосиланами, имеющими следующую общую формулу:
где ʺZʺ может представлять собой алкил, гидроксиалкил, алкоксиалкил, где число атомов углерода меньше примерно шести; ʺуʺ представляет собой H(HNR)n, где ʺRʺ представляет собой арил, алкил, алкоксиалкил или циклоалкил, и ʺnʺ представляет собой целое число от 2 до 6. ʺRʺ может варьироваться в каждой молекуле ʺуʺ.
Металлорганический катализатор выбран из октоата цинка, лаурата олова или органотитанатов, предпочтительно дибутилтитаната.
Композиция может также содержать другие соединения, такие как модификаторы реологии, диспергирующие средства, смачивающие реагенты, пластификаторы, пеногасители и растворители, для придания целевых характеристик прочности и нанесения.
В третьем варианте осуществления настоящего изобретения описано двухкомпонентное покрытие, как в случае циклоалифатической смолы по первому варианту осуществления, с по меньшей мере одной неароматической эпоксидной смолой и/или по меньшей мере одним акриловым полимером. Данное покрытие имеет желаемые механические свойства, атмосфероустойчивость и устойчивость блеска.
Благодаря своим свойствам и композиции, циклоалифатическая смола по первому варианту осуществления настоящего изобретения может заменить смеси, описанные в патентах US 4,250,074; US 5,618,860 и US 6,639,025 (Haruji Sakugawa), где гидрированную эпоксидную и полисилоксановую смолу добавляют совместно в органо-оксисилановые смолы, и затем отверждают амино-силанами, где полисилоксановые и органо-оксисилановые смолы гидролизуют добавлением воды, и полученные силанолы поликонденсируются, формируя линейный комплексный полимер с эпоксидной смолой.
Благодаря такому составу циклоалифатической смолы, не требуется добавление воды в композицию покрытия или в процессе его получения.
Композиция покрытия по третьему варианту осуществления позволяет одновременно формировать два полимера, каждый из которых реагирует со своим соответствующим отвердителем, сшиваясь с образованием запутанной сетки химических связей, что в результате дает пленку с более высокой прочностью по сравнению с обычными эпоксидными пленками, а также она будет иметь большую химическую устойчивость и лучшие физические характеристики, такие как твердость, жесткость, эластичность, сцепление, устойчивость блеска, устойчивость к разрушению под действием ультрафиолетовых лучей от солнечного света, являющиеся следствием наличия циклоалифатических ядер, достаточного количества кремниевых групп для защиты сложной гибридной молекулы, а также формирования линейных полимеров циклоалифатических эпоксидных смол с полисилоксан-аминами.
Получают гибридное покрытие по третьему варианту осуществления настоящего изобретения, содержащее:
По меньшей мере одну неароматическую эпоксидную смолу и/или по меньшей мере один гидроксилированный акриловый полимер;
(a) Циклоалифатическую смолу, полученную по первому варианту осуществления настоящего изобретения;
(b) Отвердитель;
(c) Металлорганический катализатор, и
(d) Пигменты и агрегаты.
Описанная композиция может также содержать другие соединения, такие как модификаторы реологии, диспергирующие средства, смачивающие реагенты, пластификаторы, пеногасители и растворители, для придания целевых характеристик прочности и нанесения.
Неароматические эпоксидные смолы относятся к циклоалифатическому или алифатическому типу, содержат более одной, предпочтительно две эпокси-группы на молекулу, и предпочтительно должны быть жидкими и иметь эквивалентный вес на эпокси-группу от 150 до 2000, и предпочтительно от 150 до 500. Предпочтительными циклоалифатическими эпоксидными смолами являются даглицидиловый эфир гидрированного бисфенола А-типа и диглицидиловый эфир гидрированного бисфенола F-типа. Предпочтительные алифатические эпоксидные смолы относятся к типу, получаемому реакцией полипропиленгликоля с эпихлоргидрином. Предпочтительное содержание эпоксидной смолы находится в диапазоне от 15 до 45 вес. % от общего веса полимера, предпочтительное содержание составляет по меньшей мере 25 вес. %.
Отвердитель может представлять собой полифункциональный амин, например алифатический амин, аминовый аддукт, полиамидоамин, циклоалифатический амин, ароматические амины, являющиеся основаниями Манниха, которые могут быть полностью или частично замещены аминосиланом, имеющим следующую общую формулу:
где ʺZʺ может представлять собой алкил, гидроксиалкил, алкоксиалкил, где число атомов углерода меньше примерно шести; ʺуʺ представляет собой H(HNR)n радикал, где ʺRʺ представляет собой арильные, алкильные, алкоксиалкильные или циклоалкильные радикалы, и ʺnʺ представляет собой целое число от 2 до 6. ʺRʺ может варьироваться в каждой молекуле ʺуʺ.
Предпочтительно, по меньшей мере 0.7 эквивалентов амина на эквивалент эпокси-соединения может присутствовать в отвердителе, и амин может быть бифункциональным или полифункциональным.
Химические реакции отверждения покрытия, когда оно содержит по меньшей мере одну эпоксидную смолу и циклоалифатическую смолу по первому варианту осуществления, могут состоять в реакции присоединения эпоксидной смолы с аминами, оставляющими концевую гидроксильную группу в заместителе, которая может присоединяться к непрореагировавшим концевым метокси-, этокси- или пропокси-группам циклоалифатической смолы, присутствующим в смеси. Такая же реакция между эпоксидной смолой и аминосиланом может также осуществляться через оксирановый радикал циклоалифатической смолы.
В каждой комбинации амина с эпокси-радикалами может образовываться гидроксильная группа, которая в свою очередь комбинируется с метокси-, этокси- или пропокси-группой, генерируя при этом соответствующий спирт.
Покрытие по третьему варианту осуществления настоящего изобретения может содержать:
(a) 15-55 вес. % циклоалифатической смолы, полученной согласно первому варианту осуществления настоящего изобретения;
(b) 15-45 вес. % неароматической эпоксидной смолы, содержащей по меньшей мере две эпокси-группы на молекулу;
(c) 10-20 вес. % амино-полифункционального или амино-силанового отвердителя с концевыми метокси- или этокси-группами;
(d) до 5 вес.% металлорганического катализатора, и
(e) Пигменты и агрегаты.
Варианты и композиции по второму и третьему вариантам осуществления настоящего изобретения во всех случаях представляют собой двухкомпонентные системы смолистых покрытий, упакованные в два отдельных контейнера, которые необходимо смешать перед применением.
В третьем варианте осуществления, композиция покрытия также может содержать:
(a) 20-60 вес. % циклоалифатической смолы, полученной согласно первому варианту осуществления настоящего изобретения;
(b) 10-30 вес. % гидроксилированного акрилового полимера с эквивалентным весом в диапазоне от 600 до 1000 грамм на эквивалент гидроксила;
(c) 10-30 вес. % полиаминового или амино-силанового отвердителя;
(d) до 5 вес. % металлорганического катализатора, и
(e) 10-40 вес. % пигментов, наполнителей, добавок и растворителей.
В этом случае циклоалифатическая смола по первому варианту осуществления гидролизуется в комбинации с функциональным акриловым полимером, который химически реагирует с концевыми группами циклоалифатической смолы и/или с концевыми группами отвердителя.
Металлорганический катализатор промотирует реакции алкоголиза между циклоалифатической смолой и гидроксилированным акриловым полимером; металлорганический катализатор промотирует гидролитическую конденсацию силанольного радикального комплекса, который формируется при реакциях между амин-глицидило-гидроксильными радикалами функционального акрилового полимера и свободными гидроксильными радикалами алкил-силиката, и гидролиз завершается благодаря наличию влажности окружающего воздуха, которая превращает метокси-, этокси- и пропокси-группы в гидроксильные радикалы.
Металлорганический катализатор выбран из октоата цинка, лаурата олова или органотитанатов, предпочтительно дибутилтитаната.
Отдельными предпочтительными амино-силановыми отвердителями, благодаря своим характеристикам, являются: N-(3-(триметоксисилил)пропил)этилендиамин; N-(3-(триметоксисилил)пропил)диэтилентриамин; N,N-бис(3-(триметоксисилил)пропил)-1,2-этандиамин; N,N’-бис(3-(триметоксисилил)пропил)-1,2-этандиамин; бис(триметоксисилилпропил)амин; бис(3-триэтоксисилилпропил)амин; аминоэтиламинопропилтриметоксисилан; аминопропилтриметоксисилан; γ-аминопропилтриметоксисилан; 3-аминопропилтриметоксисилан; аминопропилтриэтоксисилан; 3-аминопропилтриэтоксисилан; γ-аминопропилтриэтоксисилан; триаминопропилтриметоксисилан; N(β-аминоэтил)-γ-аминопропилтриметоксисилан; N-2-аминоэтил-3-аминопропилтриметоксисилан; N(β-аминоэтил)-γ-аминопропилметилдиметоксисилан; 4-(амино)-3,3 (диметил-бутил)триметоксисилан; N-(2-аминоэтил)-3-аминопропилметилдиметоксисилан; N-(н-бутил)-3-аминопропилтриметоксисилан; 3-аминопропилметилдиэтоксисилан; N-бензил-N-аминоэтил-3-аминопропилтриметоксисилан-хлоргидрат; метокси-терминальные 3-(2-аминоэтил)аминопропил фенил силсесквиоксаны; полидиметилсилоксаны с аминоалкильными группами; силилированньгй полиазамид; раствор амино-функциональной метилфенил силиконовой смолы; олигомерный диамино-силан.
Аминопропилтриметоксисилан особенно предпочтителен по своим характеристикам функциональности, и в целом предпочтительны дифункциональные амино-силаны, поскольку в них комбинируется наличие двух водород-содержащих радикалов, реагирующих с оксирановыми радикалами неароматических эпоксидных смол в модифицированных формулах, или также с оксирановыми радикалами циклоалифатической смолы по первому варианту осуществления настоящего изобретения, с формированием линейных несшитых полимеров, демонстрирующих повышенную устойчивость к атмосферным факторам воздействия. Пример 1
Циклоалифатическую смолу получали следующей реакцией: примерно 150 грамм гидрированного бисфенола А растворяли примерно в 130 граммах глицидокси-пропил-триэтокси-силана, начинали нагревание и поддерживали его до тех пор, пока расплав гидрированного бисфенола А не достигал температуры примерно 140°С. В полученный прозрачный раствор добавляли 1.2 грамма октоата цинка, вызывая обильное образование метилового спирта. Экстрагировали образовавшийся спирт до получения примерно 28-30 грамм спирта. В этот момент времени реакцию считали завершенной и получали прозрачную смолу. Пример 2
Получали смолистое эпокси-силановое покрытие (главная цель настоящего изобретения). 530 грамм циклоалифатической смолы, полученной согласно Примеру 1; 2.65 грамм соли алкиламида с кислотными группами, в качестве диспергирующего соединения; 113 грамм диоксида титана; 50 грамм бутилацетата; 5.3 грамм дибутиллаурата олова и 5.3 грамм воды помещали в перемешиваемый сосуд. Смесь диспергировали до получения однородной смеси, после чего добавляли 4 грамма дибутил титаната и продолжали перемешивать еще 30 минут. Смесь отверждали добавлением 60 грамм амин-полиэфира, имеющего эквивалентный вес 230. Полученную смесь можно наносить при комнатной температуре обычным распылением, кистью или роликом; получая гладкую, блестящую и твердую пленку, с высокой устойчивостью к ультрафиолетовым лучам, без выцветания при воздействии солнечного света, и обладающую прекрасной эластичностью.
Пример 3
Получали гибридное покрытие следующим образом: смешивали 530 грамм циклоалифатической смолы, полученной согласно Примеру 1; примерно 480 грамм циклоалифатической эпоксидной смолы, имеющей эквивалентный вес 225, и примерно 300 грамм диоксида титана, диспергировали с получением смеси, используя соль алкиламида в качестве диспергирующей добавки, до достижения степени дисперсности по Хегману равной 6. Полученную пасту вводили в реакцию с 500 граммами амин-функциональной смолы, имеющей эквивалентный вес 230, и разбавляли добавлением 150 грамм бутилацетата для облегчения спреевого нанесения с получением толщины влажной пленки от 0.15 до 0.18 мм (6-7 мил). Высыхание до исчезновения отлипа достигалось примерно за 5 часов, а гладкую пленку с 98% единицами блеска по Гарднеру получали на следующий день. Определение твердости по карандашной шкале BYK-Гарднера дало значение твердости Н, и пленка обладала также прекрасной эластичностью. Сухая пленка с толщиной 0.10-0.13 мм (4-5 мил) обладала прекрасной ударопрочностью и устойчивостью к ультрафиолетовому свету.
Пример 4
Получали модифицированную силан-эпоксидную смолу. В перемешиваемую колбу, оснащенную системой конденсации экстракта помещали 250 грамм глицидокси-пропил-триэтокси-силана, после чего начинали перемешивать и нагревать. В течение 60 минут добавляли 140 грамм гидрированного бисфенола А и 2 грамма октоата цинка. Когда температура достигала 100-105°С, образовывался спирт, и гидрированный бисфенол А начинал растворяться в системе. Температура поддерживалась равной 150°С в течение 2 часов, после чего температура начинала расти, и образование спирта заканчивалось, было проэкстрагировано 64 грамма метилового спирта. В этот момент времени реакция была закончена. 40 грамм полученной смолы смешивали с 20 граммами гидроксилированного акрилового полимера, имеющего ОН-эквивалентный вес между 600 и 800 граммами, и затем полученную смесь наносили традиционным распылением, кистью или роликом на чистую металлическую пластину. Примерно после 2 часов сушки получали гладкую, прозрачную, эластичную и твердую пленку с прекрасной устойчивостью к свету, полученная силан-эпоксидная смола очень хорошо подходит для изготовления покрытия с высокой устойчивостью к атмосферным факторам воздействия и высокой температуре, обладая устойчивостью к температурам до 260°С.
Хотя настоящее изобретение было детально описано для определенных предпочтительных вариантов, возможны и другие варианты его осуществления. Поэтому суть и объем формулы настоящего изобретения не ограничиваются описанными в настоящем тексте предпочтительными вариантами.
Описанное изобретение может быть подвергнуто различным вариациям квалифицированным специалистом в данной области техники. Такие вариации не должны трактоваться как выход за рамки сути и объема настоящего изобретения, и все такие модификации, как будет понятно квалифицированному специалисту в данной области, рассматриваются как входящие в объем приведенной далее формулы изобретения.
Плотность эпоксидной смолы: расход и технологии применения
ПОДЕЛИТЕСЬ
В СОЦСЕТЯХ
Химия – наука сложная, и далеко не каждый владеет знаниями в этой области. Однако тот, кто работает с химическими составами и обеспечивает протекание в них определенных процессов, должен иметь представление об используемых веществах. Плотность эпоксидной смолы в готовом изделии будет высокой только в том случае, если правильно подобраны компоненты и созданы оптимальные условия для полимеризации состава.
Плотность эпоксидной смолы может отличаться в зависимости от соотношения компонентов
Смолы эпоксидные: разновидности химических составов
Применение эпоксидки давно и прочно вошло в нашу жизнь. В быту, где необходимо надежное соединение или твердый состав, это средство незаменимо. Эпоксидная смола – это один из видов синтетических смол, олигомер, содержащий эпоксидные группы. Вещество имеет сложную химическую формулу.
Любая эпоксидка состоит из основного компонента – смолы, а также отвердителя
В зависимости от состава, различают несколько видов смол:
- Эпоксидно-диановые. Имеют маркировки ЭД-10, ЭД-16, ЭД-20, ЭД-22, ЭП-СМ-ПРО. Активно используются в быту и в производственной сфере. Компаунды с функцией пропитки, наливной пол, клеевые составы – далеко не полный перечень применения данного вида полимеров.
- Эпоксидно-диановые, предназначенные для изготовления лаков и красок. Данные эпоксидки маркируются Э-40, Э-40 Р. С их помощью создаются прочные лакокрасочные покрытия.
- Эпоксидно-модифицированные (ЭПОФОМ-1,2,3). Используются для проведения ремонтных работ.
- Специальные эпоксидные смолы. Особенности составов (с хлором, резорцином и т. д.) позволяют применять их в особых условиях.
Любая эпоксидная смола состоит из двух компонентов – непосредственно смолы как основного вещества и отвердителя. Различные наполнители придают составу определенные качества.
Основные потребительские свойства эпоксидной смолы
Стоимость эпоксидной смолы довольно высокая. Приобрести небольшое количество для бытовых нужд вполне доступно, но значительные объемы требуют немалых финансовых затрат. Вместе с тем популярность вещества растет. Объяснить данный факт можно наличием хороших потребительских качеств данного полимера. Среди основных характеристик можно выделить следующие:
Эпоксидная смола характеризуется термостойкостью, водонепроницаемостью и прочностью
- Прочность. При высоком уровне технологичности процессов изготовления и применения застывшая смола может соперничать с отдельными марками бетона.
- Термостойкость. Эпоксидная смола может выдерживать воздействие температуры от 200 °С и выше.
- Водонепроницаемость. В твердом состоянии вещество не впитывает воду.
- Клеящие свойства. Высокий уровень адгезии и прочность соединений позволяют склеивать большие поверхности.
- Устойчивость ко многим агрессивным химическим веществам.
- Небольшой вес изделий.
Данные характеристики свойственны всем видам смолы. Эти качества могут проявляться в большей или меньшей степени в зависимости от добавок, использованных при приготовлении эпоксидки.
Полезный совет! Приобретая эпоксидную смолу, обязательно следует определить (самостоятельно на основании информации на упаковке или попросить специалиста продающей компании предоставить сведения о товаре) целевое назначение состава. Даже незначительное несоответствие может повлиять на итоговый результат.
Современные области применения эпоксидной смолы
Появление новых составов постоянно расширяет область применения эпоксидных смол. С помощью данных полимерных материалов можно не только склеивать предметы и создавать декоративные изделия, мебель, но и заменять значительных размеров металлические элементы конструкций и механизмов, сокращая их стоимость и снижая вес. К основным сферам применения эпоксидки можно отнести:
Эпоксидная смола активно применяется в ремонтных работах
- Производство композитных материалов. Используя способ пропитки синтетических тканей, изготавливают стеклопластик и углепластик. Материал получается легкий и прочный. Он активно применяется в моделировании, при создании машин, ракет, кораблей, самолетов.
- Изготовление мебели. Это варианты как поточные (в основном кухонные столешницы), так и эксклюзивные (столы из слэбов, столешницы – реки, карты, картины и т. д.).
- Создание электроизоляционных и гидроизоляционных материалов. Эпоксидная смола является диэлектриком, она влагонепроницаема.
- Производство бижутерии. Украшения из эпоксидки (кулоны, браслеты, броши и т. д.) недорогие и отличаются декоративностью и эстетичностью.
- Ремонтные работы. Можно залить эпоксидной смолой растрескавшуюся столешницу, сделать новый пол, устранить течь в лодке, отремонтировать автомобильный кузов, используя стеклоткань, и т. д.
- Изготовление различных поделок, сувениров, стендовых моделей.
Работать с эпоксидной смолой гораздо проще, чем, например, с металлом или керамикой.
Изготовление эпоксидной смолы: дополнение к инструкции
Эпоксидная смола всегда идет в комплекте с отвердителем, так как без него основная жидкость не застынет. Всю информацию о том, как изготовить эпоксидку, можно прочитать в инструкции к применению. Отдельные важные моменты изготовитель все же не освещает, поэтому стоит сказать о них отдельно:
Для разных видов работ выбирается свой состав и температурный режим смолы
- На качестве итогового продукта сказывается как недостаток, так и избыток отвердителя. При дефиците масса будет характеризоваться липкостью. Излишнее количество добавки ускорит процесс полимеризации, но приведет к растрескиванию материала.
- Размешивать компоненты необходимо предметом, не имеющим дополнительных элементов (лопастей, венчиков, изогнутостей и т. д.). Такие приспособления ускоряют протекание процесса отвердения.
- Токсичность эпоксидной смолы проявляется в жидком состоянии, но она незначительна, потому проветривания помещения вполне достаточно для создания безопасных условий.
- Нельзя допускать попадания сторонней жидкости как в отдельные компоненты, так и в готовый состав.
- Замешивать необходимо такое количество материала, которое можно успеть выработать до начала процесса отвердевания. Если все же эпоксидки приготовлено много, лучше разлить ее в небольших количествах в разные емкости – она дольше будет сохранять необходимую вязкость.
Полезный совет! При подготовке смолы для разных видов работ необходимо соблюдать определенную технологию, включающую правильный выбор состава, температурный режим, алгоритм действий и временные рамки.
Замешивать необходимо такое количество вещества, которое не успеет затвердеть до конца работы
Технологические тонкости работы с эпоксидной смолой
С момента приготовления смеси и до начала активного ее затвердевания есть 40 минут, за которые требуется успеть израсходовать состав. В ходе работы смола может быть использована в качестве клеящего вещества, для нанесения верхнего слоя на основание, для заливки полостей или специальных форм. Исходя из цели, должно замешиваться необходимое количество эпоксидной смолы.
При этом важно знать расход полимера. Особенно актуален точный показатель в тех случаях, когда заливаются значительные горизонтальные поверхности. Например, расход эпоксидной смолы на 1м² столешницы – 1 л (или 1,1 кг) при толщине слоя 0,1 см. Это количество без добавок. Значение среднее и может разниться в зависимости от производителя полимера.
Оптимальный для отвердевания слой эпоксидки – 1 см. Более толстое покрытие может трескаться в ходе застывания. Если требуется залить толстый слой ‒ 2 и более сантиметров, можно делать это поэтапно, нанося состав в несколько приемов. Для больших объемов можно подобрать эпоксидную смолу с отвердителем.
Важно правильно подготовить поверхность, на которую будет наноситься полимер:
Готовую эпоксидную смолу необходимо использовать в течение 40 минут
- Обеспылить.
- Обезжирить. Если для данных целей применялся растворитель, нужно удалить его и дождаться, пока испарятся остатки, то есть поверхность станет сухой.
- Деревянные части следует зачистить шкуркой. Это создаст шероховатости, которые увеличат площадь соприкосновения.
- Металлические поверхности нужно отшлифовать до блеска.
При склеивании частей необходимо стянуть конструкцию струбцинами.
Советы по изготовлению цветной эпоксидной смолы
Чтобы быть уверенным в результате окрашивания эпоксидной смолы, лучше приобретать специально для этого предназначенные средства. Найти их можно в магазинах и художественных салонах, торгующих соответствующей продукцией. Типы красок могут быть следующие:
- Однотонные. Придают эпоксидке определенный цвет (синий, красный, фиолетовый и т. д.).
- Флуоресцентные. Благодаря наличию в составе люминоформа изделия приобретают эффект свечения. Могут давать также дополнительный цветовой оттенок.
- С эффектом матовости. Поглощают глянец материала.
- Металлик. Изделия приобретают металлический блеск.
- С блестками. Застывшая эпоксидная масса переливается.
Для окрашивания эпоксидной смолы рекомендуется приобретать специальные красители
На фото эпоксидной смолы в интернете продемонстрированы как типы красителей, так и готовые изделия с их применением. Можно выбрать желаемый вариант цвета. Вид изделий во многом зависит от количества введенного красителя. Несколько капель сохранят прозрачность, придадут легкий оттенок. Увеличив количество красителя, можно получить более выразительный цвет. Чтобы добиться яркого, глубокого оттенка, следует сначала выкрасить состав в белый цвет, а потом добавить желаемый оттенок.
Полезный совет! Чтобы не возникло сложностей в работе с красителями, лучше приобрести средство того же производителя, который изготовил эпоксидную смолу.
Эпоксидная смола для творчества: особенности, основные марки
Одно из качеств эпоксидной смолы – прозрачность – позволяет применять данный материал для творчества. Подобные составы используют для изготовления 3D-картин, оригинальных столешниц, бижутерии, декоративных предметов интерьера. Как прекрасный заливочный состав эпоксидка применяется при создании гербариев и различных выставочных моделей природного материала. Цветы живые и сухоцветы, экзотические виды насекомых, образцы минералов приобретают дополнительную оригинальность и экзотичность под прозрачным полимерным слоем.
При выборе материала для творчества важен класс эпоксидной смолы. Самыми популярными прозрачными составами являются:
Эпоксидную смолу применяют для изготовления мебели, картин, украшений, декоративных предметов
- Resin Art. Вещество жидкой консистенции, применяется для рисования и выполнения различных оформительских работ. Состав придает объектам 3D-эффект, создает глянцевый слой.
- Magic Crystal-3D. Используется при изготовлении объемных предметов небольших размеров: бижутерии, ваз, подсвечников, брелоков, декоративных корпусов и т. д.
- Epoxy CR 100. Применяется для создания изделий, имеющих значительные объемы и поверхности, поэтому в продажу поступает большими упаковками.
- ЭД-20. Может использоваться как в строительной отрасли, так и для изготовления различных декоративных элементов.
- Aquaglass Citrus. Быстро застывает как в тонком слое, так и в более толстом ‒ до 2 см, удобно применять для выполнения покрытий.
- Diamant. Используется для создания ювелирных украшений, продается в небольших объемах.
Полезный совет! Приобретая смолу для творчества, необходимо быть уверенным, что она устойчива к пожелтению.
Изделия из дерева и эпоксидной смолы своими руками
В интернете размещено большое количество фото с изображениями изделий, изготовленных из эпоксидной смолы или с применением данного вещества. Значительное количество из них производится из дерева и смолы. Древесине довольно часто отдается предпочтение из-за высокого уровня экологичности и естественной декоративности. Даже необработанные поверхности могут являться прекрасными элементами интерьеров, а в случае применения дополнительных материалов их оформительская ценность увеличивается.
Для изделий с эпоксидной смолой древесина должна быть сухой
Любая деревянная поверхность, даже идеально отшлифованная, имеет поры, в которые проникает эпоксидка, создавая прочное соединение. Поэтому сочетание материалов является удачным для изготовления эксклюзивной мебели. Эпоксидка для заливки или склеивания деревянных поверхностей чаще применяется прозрачная. Она может также тонироваться в зависимости от дизайнерского замысла.
Самостоятельно изготовить изделие из дерева и эпоксидной смолы несложно. В качестве образца можно взять идею из интернета. О выборе и подготовке эпоксидного состава в статье сказано выше, но несколько советов домашним умельцам не будут лишними:
Статья по теме:
Прозрачная эпоксидная смола для заливки: материал для творчества и быта
Основные характеристики и технология применения. Изготовление состава своими руками. Изделия из эпоксидной смолы и дерева.
- для соединения с эпоксидкой допустимо использование только хорошо просушенной древесины;
- при заливке горизонтальных поверхностей необходимо выдерживать строгий уровень расположения изделия;
- большую механическую нагрузку на элементы с эпоксидными вставками можно допускать только на 4-5-й день после отвердения.
Значительно усиливает декоративность изделий из эпоксидной смолы и дерева наличие подсветок. О технике создания светящихся полимеров также есть информация в данной статье.
На сегодняшний день мебель из эпоксидной смолы и древесины очень популярна
Плотность эпоксидной смолы: стандартные и фактические показатели
Эпоксидная смола отличается устойчивостью к щелочам, галогенам и некоторым видам кислот. Это качество обеспечивается химическим составом и основными свойствами. Вещество в чистом виде, без отвердителей, имеет следующие показатели:
- упругость составляет 3000-4500 МПа;
- предел прочности достигает 80 МПа;
- плотность имеет значение 1,2 г/см³.
Основные единицы, которыми измеряют плотность эпоксидной смолы, – г/см³ (кг/м³). Показатель величины может зависеть от следующих факторов:
- От температуры. Изделия, полученные горячим способом отвердения, более плотные.
- От наличия воздуха. Пузырьки в составе эпоксидного слоя уменьшают плотность.
- От наличия пигментных добавок. Красители, придавая декоративность материалу, снижают его плотность.
- От качества отвердителей. При использовании кислотных добавок плотность материала выше, чем после применения щелочных.
Эпоксидная смола без отвердителя имеет плотность 1,2 г/см³
Плотность эпоксидной смолы (кг/м³ или г/см³) – один из основных показателей прочности отвердевшего материала. Если в ходе эксплуатации выполняемое из полимера изделие будет испытывать значительные механические нагрузки, необходимо уделять особое внимание данной величине.
Полезный совет! Определить плотность подготовленного к работе состава эпоксидной смолы в домашних условиях практически невозможно, для этого необходима лаборатория. Следовательно, добиться оптимальной величины можно только при соблюдении технологичности в процессе работы с полимером.
Технические показатели эпоксидной смолы ЭД-20: плотность, вязкость, температура
Широкое применение как на производстве, так и в быту получила эпоксидная смола ЭД-20. Она представляет собой жидкое вещество желтого или коричневого цвета, не имеющее добавок. Данную смолу можно соединять с различными отвердителями, в зависимости от целей и используемого объема применяют пластификатор. Изделия из ЭД-20 характеризуются следующими качествами:
- высокой плотностью и прочностью;
- стойкостью к механическим воздействиям;
- водонепроницаемостью, диэлектрическими свойствами;
- термостойкостью;
- высоким уровнем адгезии;
- малым весом.
Эпоксидная смола ЭД-20 характеризуется высокой прочностью и плотностью
Основные технические параметры данного вида смолы имеют такие показатели:
- плотность эпоксидной смолы ЭД-20, кг/м³ – 1110-1230 при холодном способе отверждения, 1200-1270 – при горячем;
- динамическая вязкость – 13-20 Па/сек.;
- температура размягчения – до 60 °С;
- время желатинизации – 8 ч.
Смола ЭД-20 – материал универсальный. Высокий уровень плотности позволяет применять его как для изготовления интересных ювелирных украшений, так и для создания машин, кораблей, самолетов. Входит данный полимер также в составы лакокрасочной продукции.
Важно! Хранить смолу ЭД-20 можно только в плотно закрытой емкости при температуре не выше 40 °С.
Полиэфирная смола: как работать, токсичность состава
В промышленном производстве применяется большое количество смол. В быту же наиболее приемлемые – эпоксидные и полиэфирные. Оба варианта – термореактивные пластмассы, после отвердевания их нельзя вернуть в жидкое состояние. Процесс полимеризации полиэфирных смол начинается еще на стадии их изготовления на производстве. Идущие в комплекте отвердители эту реакцию только ускоряют.
Чаще всего в быту применяются эпоксидные и полиэфирные смолы
Отсюда можно сделать вывод, что полиэфирная смола затвердеет и без добавки, но особую актуальность приобретает срок годности состава. Из основных достоинств полиэфирных смол можно выделить:
- невысокую стоимость;
- быстрое отверждение;
- отсутствие интенсивного изменения вязкости.
Уровень вредности полиэфирной смолы невысокий, хотя полимер имеет довольно выраженный запах. При длительном контакте и в закрытом помещении состав может вызвать раздражение верхних дыхательных путей и покраснение при попадании на кожу. Работать с полиэфирной смолой несложно. Отвердитель, или точнее ускоритель, необходимо вливать в рекомендуемых изготовителем пропорциях, размешивать неинтенсивно (это поможет избежать появления пузырьков) в течение 2 минут.
Отвердитель в полиэфирной смоле выполняет роль катализатора, то есть при его добавлении начинается выделение тепла, активизирующего процесс полимеризации. Можно не вносить добавок в данный вид смолы, а использовать внешние источники тепла.
Быстрое отверждение – одно из главных преимуществ полиэфирной смолы
Полезный совет! Не стоит наносить на эпоксидный слой полиэфирную смолу – вещества расслоятся.
Вредна ли для здоровья эпоксидная смола и насколько
Что касается эпоксидной смолы, постоянно используются слова «химический», «синтетический», «реакция», «полимеризация» и более сложные пугающие названия веществ. Ассоциации нетрудно угадать – сплошная химия, а значит, вредно. В содержании статьи уже были попытки осветить данный вопрос, но он настолько важен и актуален, что стоит остановиться на нем более основательно.
Еще раз хочется обратить внимание на то, что вредность эпоксидной смолы связана только с жидким ее состоянием. При вдыхании паров могут возникать дискомфорт в желудке, головная боль, кашель. Всего этого нетрудно избежать, если работать в помещении с вентиляцией, а еще надежнее – в респираторе. При нечастом контакте с составом проблем обычно не возникает. Те же, кто занят в промышленном производстве, максимально ограждены от воздействия вредных веществ.
При работе с эпоксидной смолой рекомендуется надевать респиратор
После отвердения эпоксидная смола нетоксична. Если ношение кулона или браслета вызвало определенную негативную реакцию, это, скорее всего, связано с индивидуальными особенностями организма, с аллергической реакцией на конкретные вещества. Чаще это материалы, на основе которых выполнено декоративное покрытие изделия, а не основная его часть.
Чтобы избежать попадания смолы на кожу, стоит работать в перчатках с резиновой или другой подобной пропиткой. Эпоксидная смола не вызывает ожогов, но удалить ее при попадании следует как можно скорее: из-за температуры тела она начнет застывать, и тогда убрать ее будет сложнее – понадобятся растворители, которые гораздо токсичнее смолы.
В определенной степени работа с эпоксидной смолой – метод проб и ошибок. В статье размещена информация, которая поможет хотя бы частично избежать проблем. Если желание дополнено правильной организацией рабочего процесса, знаниями особенностей используемых материалов, результат обязательно будет радовать.
Свежая эпоксидная смола лучшего качества от полкило + сопутствующие товары.
Дорогой друг!
Добро пожаловать на новый сайт нашего интернет-магазина! Наш магазин для тех, у кого «чешутся» руки, кто всё любит делать сам или хочет научиться что-то сделать своими руками!Сайт стал еще удобнее и понятнее, появилось больше информации о товаре, реальных фотографий и видео! Вы по-прежнему можете купить у нас всего полкилограмма эпоксидной смолы, метр стеклоткани или 100 грамм отвердителя, пигмента или другого материала.
Не забыли мы и об оптовых покупателях, практически всё, что мы продаем можно купить много и по «вкусной» цене. Для ремонта и строительства лодок у нас есть смола эпоксидная, отвердители, пластификаторы, стеклоткани, эмали. Для изготовления обвесов, бамперов есть стекломат, микросфера, аэросил, шпатлевка. Для моделирования стекловуаль, пигменты, а также смола для бижутерии.
Практически каждый месяц у нас появляются новинки — материалы, о которых вы часто спрашиваете! Все материалы мы тестируем на предмет качества и свежести.
ВНИМАНИЕ! Мы сами завозим посылки на склады транспортных компаний! Отправляем 5 дней в неделю Новой почтой, реже Деливери.
Чем мы лучше других?
Мы придерживаемся мнения «Клиент всегда прав», хотя, поверьте, не всегда так получается. Не каждый хочет взвешивать смолу или придерживаться технологий. У нас покупают, потому что:
- наш товар всегда свежий, он просто не залеживается
- весь товар можно купить в небольшом количестве
- на большие объёмы — скидки
- если вам что-то не подошло, товар можно вернуть или обменять
- мы даем консультации по товару и технологиям, о которых знаем сами
- если вы обнаружили недостачу, мы исправляем проблему за свой счёт
- упаковка и доставка посылок на склад перевозчика за наш счёт
- выписать счёт-фактуру или накладную для нас не проблема
Если по каким-либо причинам у вас не получается оформить заказ, выделите табличку вашего заказа, нажмите кнопки CTRL+C (скопировать) и вставьте в письмо, которое нужно создать в вашем почтовом клиенте нажав CTRL+V. Наш е-мейл внизу каждой страницы. Смайлик замените собачкой.
Товар в картинках
Эпоксидная смола — обзор | Темы ScienceDirect
6.3.1 Приготовление эпоксидной смолы, модифицированной лигнином
Эпоксидная смола имеет хорошую адгезию, небольшую усадку при отверждении, при отверждении не выделяется газ, имеет хорошую термостойкость, отличную стойкость к растворителям и ползучесть для получения широкого диапазона применений в области клея, красок и флюсов. Он также обычно используется в качестве матрицы из композитной смолы, армированной волокном. Когда лигнин добавляется в систему эпоксидной смолы, он может реагировать с различными типами реакций сшивания отвердителя.Затем в таком модифицированном лигнином эпоксидном материале могут образовываться нерастворимые неплавящиеся трехмерные сетки. Приготовление модифицированной лигнином эпоксидной смолы осуществляется тремя способами:
① Лигин непосредственно смешивается с обычными смесями эпоксидных смол, которые могут образовывать взаимопроникающие сетчатые полимерные структуры.
② Лигнин окисляется перед первой модификацией, а затем используется в качестве сырья для получения эпоксидных смол.
③ Функциональные группы, которые могут реагировать с эпоксидной смолой, вводятся в лигнин, а модифицированный лигнин затем используется для модификации эпоксидной смолы.
Пленку эпоксидной смолы, модифицированной сульфатным лигнином, получают методом литья из раствора следующим образом. Эпоксидную смолу бисфенол-А сначала смешивают с сульфатным лигнином, массовая доля которого составляет 10-40% (по массе смеси) при перемешивании. Также добавляется соответствующее количество отвердителя (высокая активность алифатического полиамина). Они отверждаются при 100 ° C в течение 2 часов или при комнатной температуре в течение 24 часов для формования. Исследования показывают, что лигнин может быть связан с сеткой эпоксидной смолы через непрореагировавшую аминогруппу отвердителя.Реакция протекает только при высокой температуре отверждения. Измеряя реакционную способность лигнина с отвердителями на основе амина, результаты показывают, что реакция лигнина и полиаминов не имеет способности реагировать с эпоксидными группами или первичными и вторичными аминами [25]. Нижний лигнин (BL), извлеченный из древесины, может быть модифицирован эпихлоргидрином для получения эпоксидных групп. Два материала эпоксидной смолы, модифицированной лигнином, получают с использованием 1- (2-цианоэтил) -2-этил-4-метилимидазола (2E4MZ-CN) и лигнина в качестве отвердителей соответственно.Механизм реакции между лигнином и эпихлоргидрином следующий: с тетрабутилбромидом (TBAB) катализатора межфазного переноса лигнин и эпихлоргидрин реагируют как реакция присоединения с открытым кольцом. Затем с помощью гидроксида натрия хлористый водород удаляется и эпоксидные группы реформируются [26]. Основываясь на идее, что лигнин может действовать как отвердитель эпоксидной смолы, лигнин может улучшить стабильность качества модифицированной эпоксидной смолы, регулируя количество группы и количество групп. Эти группы могут реагировать с эпоксидной группой посредством химической реакции.Гидроксильные группы ферментолизированного лигнина или его производных могут реагировать с ангидридом двухосновной кислоты и катализатором с образованием форполимеров. Затем они могут реагировать с глицидиловым эфиром с получением эпоксидной смолы полиэфирного типа, модифицированной ферментолизированным лигнином. Результаты показывают, что, когда содержание форполимера невелико, хотя эпоксидное число выше, плотность сшивки системы будет снижаться из-за наличия большего количества непрореагировавших мономеров диглицидилового эфира этиленгликоля. Присоединение эпоксидных групп диглицидилового эфира этиленгликоля к карбоксильным группам форполимера является более полным.Более того, количество свободного мономера диглицидилового эфира этиленгликоля будет постепенно уменьшаться. Плотность сшивки эпоксидной смолы значительно возрастет из-за синергетического эффекта лигнинового компонента, тем самым увеличивая прочность связи на сдвиг. Когда содержание форполимера (массовая доля) составляет 50%, адгезионная прочность на сдвиг модифицированной эпоксидной смолы достигает максимального значения [27]. До сих пор исследования только лигнина в качестве сырья для получения эпоксидной смолы относительно небольшие, и большая часть исследований посвящена введению лигнина в эпоксидную смолу посредством метода смешивания.Большинство материалов на основе эпоксидных смол, модифицированных лигнином, представляют собой органические растворители, и их недостатком являются низкие технологические характеристики. В настоящее время исследователи ищут позитивный и эффективный способ решения проблем.
Самым важным в процессе приготовления эпоксидной смолы, модифицированной лигнином, является выбор подходящего отвердителя. Его цель — согласовать скорость отверждения, температуру отверждения, время отверждения и другие параметры процесса и систему отверждения. Можно выбрать широкий спектр отвердителей, и те, которые обычно выбирают, можно разделить на две категории: полиаминовые отвердители и ангидридные отвердители.Полиамины могут отверждать эпоксидную смолу при комнатной температуре и подходят для крупногабаритного литья. Однако полиаминовые отвердители обладают большей токсичностью, поэтому более популярны менее токсичные отвердители на основе ангидрида кислоты. Кислые отвердители имеют более низкую скорость отверждения и обычно требуют нагревания в процессе отверждения. Их можно использовать для формования под низким давлением без образования побочных продуктов. Общие полиамины и отвердители на основе ангидрида кислоты приведены в Таблице 6.2 [28]. Тип отвердителя напрямую связан с характеристиками эпоксидной смолы, обычно из следующих аспектов, как принцип выбора отвердителя:
Таблица 6.2. Обычные отвердители аминного и ангидридного типов для эпоксидных смол, модифицированных лигнином, и их соответствующие контрольные дозировки и условия отверждения [28]
Тип | Название | Сокращение | MW | Контрольная дозировка /% | Условия отверждения |
---|---|---|---|---|---|
Аминный отвердитель | Этилендиамин | EDA | 60,1 | 6–8 | 25 ° C / 2–4 дня; 80 ° C / 3-5 ч |
Диэтилтриамин | DTA | 103.2 | 8–11 | 25 ° C / 4–7d; 150 ° C / 2–4 ч | |
Триэтилтетрамин | TTA | 146,2 | 9–12 | 25 ° C / 4–7 дней; 150 ° C / 2–4 ч | |
Тетраэтилпентамин | TPA | 189 | 12–15 | 25 ° C / 4–7d; 150 ° C / 2–4 ч | |
Полиэтиламин | PEDA | 14–16 | 25 ° C / 4–7d; 150 ° C / 2–4 ч | ||
Гексилендиамин | HDA | 116 | 15–16 | 25 ° C / 2–4 дня; 80 ° C / 3-5 ч | |
Дициандиамид | DICY | 84.1 | 6–7 | 145–165 ° C / 2–4 ч | |
М-фенилендиамин | MPD | 108,1 | 14–16 | 80 ° C / 3–4 ч; 150 ° C / 2 | |
M-ксилилендиамин | MXDA | 136,2 | 18–24 | 25 ° C / 1,5–2 дня; 80 ° C / 3–5 ч | |
β-гидроксиэтилэтилендиамин | 104,2 | 16–18 | 25 ° C / 7 дней; 80–100 ° C / 3 ч | ||
Триэтаноламин | ЧАЙ | 149.2 | 10–15 | 100–120 ° C / 4 ч | |
Отвердитель на основе ангидрида кислоты | Малеиновый ангидрид | MA | 98,1 | 30–40 | 160–200 ° C / 2–4 h |
Фталевый ангидрид | PA | 148,1 | 35–45 | 120 ° C / 1 ч; 150 ° C / 6 ч | |
Пиромеллитовый ангидрид | PMDA | 218 | Смешивание с MA и PA | 120 ° C / 1 ч; 150 ° C / 6 ч | |
Гексагидрофталевый ангидрид | HHPA | 154.2 | 65–80 | 80 ° C / 3d; 120 ° C / 3 ч |
① Выбирайте отвердители в соответствии с их характеристиками (такими как высокая температура, гибкость, коррозионная стойкость и т. Д.).
② Выбирайте отвердители в соответствии с условиями отверждения (например, система, соответствующая температуре отверждения, времени отверждения и т. Д.).
③ Выбирайте отвердители в соответствии с применимым периодом (промежуток времени между добавлением эпоксидной смолы в отвердитель и временем, когда ее нельзя использовать).Длительный период времени обычно соответствует отвердителю кислотно-ангидридного типа.
④ С точки зрения безопасности используйте менее токсичный отвердитель.
6.3.2 Структура и характеристики эпоксидной смолы, модифицированной лигнином
Композитная модификация — эффективное средство для улучшения комплексных характеристик эпоксидной смолы, таких как сопротивление растрескиванию, ударопрочность и устойчивость к влажному нагреву. Модифицированные лигнином эпоксидные смолы имеют высокую практическую ценность [29–31]. Функциональные группы множественного типа могут быть дополнительно модифицированы другими функциональными группами для участия в реакции отверждения эпоксидной смолы.Совместимость между компонентами может быть улучшена путем создания взаимопроникающей полимерной сети [32] для обеспечения лучшего эффекта модификации композита. Более того, молекулы лигнина содержат множество ароматических кольцевых структур и могут придавать эпоксидной смоле более высокую жесткость, термическую стабильность и устойчивость к растворителям. Максимальное количество компонентов лигнина в модифицированную систему эпоксидной смолы может быть добавлено до 60% [33]. Когда спекаемый лигнин и термореактивная эпоксидная смола смешиваются, прочность модифицированного материала значительно повышается, когда массовая доля лигнина достигает 30%.Когда массовая доля лигнина составляет 20%, совместимость является наилучшей, а прочность сцепления достигает максимума. Однако прочность модифицированного материала на сдвиг постепенно снижается после того, как массовая доля лигнина превышает 35%. T г модифицированного материала увеличивается с увеличением содержания лигнина и достигает максимума при содержании 40%. Материал, модифицированный 20 мас.% Лигнина, имеет только один T г , который увеличивается до двух, когда содержание составляет 25% или 40%.Это доказывает, что совместимость компонентов в модифицированном материале достигается наилучшим образом при содержании лигнина 20 мас.% [34]. В отсутствие отвердителя лигнин может также участвовать в реакции отверждения эпоксидной смолы путем смешивания. По мере увеличения содержания лигнина прочность композитного материала на изгиб постепенно снижается. Причем ударная вязкость сначала увеличивается, а затем уменьшается. Лигнин также может катализироваться для сшивки или реакции с эпоксидной смолой. Этот связывающий эффект способствует улучшению характеристик композита лигнин / эпоксидная смола.Кроме того, соединения лигнина и эпоксидных смол могут брать на себя роль отвердителей через взаимопроникающую полимерную сетку в форме высокой совместимости [35]. Например, щелочной раствор сульфатного лигнина смешивают с водорастворимым эпоксидным соединением и отвердителем для образования взаимопроникающей полимерной структуры. Межфазная совместимость лучше, а жесткость, прочность и прозрачность очевидны [36]. Модифицированная лигнином эпоксидная смола может эффективно улучшить прочность сцепления.Например, после того, как лигнин и эпоксидная смола смешаны и подвергнуты термообработке при 100 ° C в течение 2 часов, эффективность связывания значительно улучшилась на 78% по сравнению с немодифицированной смолой [37].
Тип лигнина и соответствующие химические свойства напрямую влияют на свойства модифицированной эпоксидной смолы и свойства материала. Высококипящий лигнин имеет высокую химическую активность и больше фенольного гидроксила, и его можно напрямую смешивать с эпихлоргидрином для получения эпоксидной смолы.Введение лигнина может улучшить термическую стабильность и стойкость эпоксидной смолы к растворителям, а также улучшить прочность на разрыв и гибкость материала. Эпоксидную смолу с эпоксидной эквивалентной массой 320 г / моль получают реакцией с лигнином и эпихлоргидрином. Этот эквивалентный вес выше, чем у эпоксидной смолы типа бисфенол-А, эпоксидный эквивалент которой составляет 175 г / моль. Более того, эти две смолы демонстрируют одинаковые характеристики термореактивности. Следовательно, ожидается, что метаноллигнин заменит бисфенол-А в качестве сырья для приготовления эпоксидных смол, а полученные материалы подвержены биоразложению [38].Реакция эпоксидирования протекает тяжело для лигнина и его производных с низким содержанием фенольных гидроксилов, таких как лигносульфонат кальция (содержание фенольных гидроксилов составляет 1,56%). Следовательно, они сначала нуждаются в модификации, такой как химическая модификация лигнина, для улучшения реакционной способности. Например, содержание фенольных гидроксильных групп и реакционная способность лигносульфоната кальция в качестве сырья могут быть улучшены посредством фенольной модификации фенол-сернокислотным методом. Затем его можно использовать для более легкого приготовления эпоксидной смолы, а показатель эпоксидной смолы продукта может достигать 0.47 мес. 1/100 г [39].
Обзор полимерного бетона на эпоксидной и полиэфирной основе и исследование полифурфурилового спирта в качестве полимерного бетона
Термореактивные смолы на основе эпоксидной смолы и полиэфира на нефтяной основе могут использоваться для производства высококачественного полимерного бетона. Однако ресурсы на основе нефти ограничены, и это потребовало разработки термореактивных биореактивных смол для использования в качестве полимербетона. Фурфуриловый спирт (FA), термореактивный биореактивный полимер, получают из лигноцеллюлозной биомассы, и он может быть полимеризован в полифурфуриловый спирт (PFA) в присутствии кислотного катализатора.Высокоэкзотермические реакции полимеризации, включающие превращение FA в PFA, могут быть использованы для изготовления бетона на основе PFA с каменной структурой. Полимербетон на основе PFA предлагает самый широкий диапазон химической стойкости к кислотам и щелочам по сравнению со всеми другими типами полимербетона, которые основаны на различных термореактивных полимерных системах. В этой обзорной статье мы обсудили составы (включение заполнителей, наполнителей и смолы) и свойства (особенно при сжатии и изгибе) полимербетона на основе эпоксидной смолы и полиэфира.В другом разделе мы привели свойства механической, термической и водостойкости биополимера на основе PFA, биокомпозитов, нанокомпозитов и полимербетона. Наконец, мы попытались выяснить, можно ли успешно использовать PFA в качестве биополимерного бетона или нет.
1. Введение
Полимербетон — это мономеры, которые полимеризуются in situ в присутствии других компонентов. Полимеризация in situ происходит под действием тепла, катализаторов или излучения. После полимеризации мономер можно использовать в качестве связующего компонента, и он не требует воды для схватывания или затвердевания.Полимербетон состоит из полимерного связующего, отвердителя и заполнителя. Взаимодействие между этими компонентами полностью зависит от химических и физических реакций. С конца 70-х годов эпоксидный и акриловый полимерный бетон стали заменять традиционные материалы благодаря быстрому отверждению и отличной адгезии к цементному бетону [1–3]. Saljé et al. сообщили о сравнительных свойствах станков, изготовленных из полимербетона и металлического железа [4]. Из-за высоких механических свойств имеются сообщения об использовании компонентов из полимербетона в станках [5, 6].Метилметакрилат, ненасыщенная полиэфирная смола, эпоксидные смолы, фурановые смолы, полиуретановые смолы, карбамидоформальдегидная смола и смеси полиэфир / стирол обычно рассматриваются как системы полимербетона [7, 8]. Преимущества использования полимерной смолы заключаются в том, что она обладает высокой механической прочностью, долговечностью и стойкостью к химическому воздействию [9].
Бетон, пропитанный полимером, представляет собой другой тип полимербетона, в котором гидравлическое вяжущее полностью заменено полимерным материалом.В бетоне, пропитанном полимером, мономер проникает в матрицу бетона на конечную глубину. Еще одна категория — полимерцементный бетон, который представляет собой смесь обычного гидравлического цементного бетона и высокомолекулярных полимеров. Поливинилацетат, полиакрилаты, поливинилхлорид, стирол-бутадиен и поливинилиденхлорид — это полимеры, которые были исследованы в качестве полимерцементного бетона. Основываясь на приведенном выше вводном абзаце, можно сказать, что полимербетон отличается от типичного портландцементного бетона, полимерцементного бетона и бетона, пропитанного полимером.Полимерцементный бетон широко используется в качестве ремонтного материала.
Характеристики полимерного бетона зависят от различных факторов, таких как свойства полимера, тип наполнителей и заполнителей, температура отверждения и дозировка компонентов. Выбор конкретного типа смолы зависит от таких факторов, как стоимость, желаемые свойства и химическая / атмосферостойкость. Температура отверждения связана с термореактивными смолами, которые можно использовать в качестве полимербетона, и существует несколько литературных источников по температуре отверждения термореактивных полимеров в журналах по химии полимеров и химии материалов.
Заполнители и наполнители составляют около 75–80% объема полимербетона. Агрегаты обычно инертны по своей природе и могут быть диспергированы по полимерной матрице. По размерам агрегаты могут быть крупными (состоящими из материала размером более 5 мм) и мелкими агрегатами (размером менее 5 мм). Заполнители, используемые в полимерном бетоне, могут представлять собой силикаты [10], переработанный полиэтилентерефталат [11], отходы щебня, кварц, гравий, известняк, известняк, гранит, глина и т. Д. [12].Документировано использование заполнителей и наполнителей в эпоксидных композитах, армированных натуральным волокном [13, 14]. Кроме того, имеются сообщения об использовании заполнителей из вторичного бетона (RCA) [15]. RCA доступны после сноса старых дорог и зданий, и если они не используются надлежащим образом, они считаются отходами. Возле агрегата очень важен наполнитель. Наполнители добавляются для уменьшения содержания пустот в смеси заполнителя и тем самым повышения прочности полимербетона.В качестве наполнителей могут использоваться различные типы мелкодисперсных материалов, например летучая зола, микрокремнезем, фосфор-гипс, шлак и т. Д. [16, 17]. Микронаполнитель представляет собой мелкодисперсный порошок с размером частиц менее 80 микрон, поэтому микронаполнитель немного отличается от наполнителя по размеру.
Летучая зола, побочный продукт сжигания угля на электростанциях, используется в качестве наполнителя из-за ее доступности. Сообщается, что его использование в полимербетоне дает лучшие механические свойства, а также снижает водопоглощение.Добавление летучей золы также улучшает удобоукладываемость свежей полимербетонной смеси, в результате чего получаются продукты с превосходной отделкой поверхности [18]. Сообщалось, что для изготовления полимербетона с мелким заполнителем необходимо использовать более высокую дозировку смолы. Это объясняется большой площадью поверхности этих материалов [19–21]. Ребеиз и др. сообщили о производстве полимербетона путем добавления летучей золы [22, 23]. Различные исследователи рекомендовали, чтобы влажность заполнителя не превышала 0.От 1% до 0,5% для улучшения механических свойств полимербетона [24, 25].
В дополнение к грубым и мелким заполнителям, микронаполнители, как обсуждалось выше, добавляются в систему полимербетона в основном с целью заполнения микропустот. Полимербетон также может быть армирован различными видами синтетических и натуральных волокон для улучшения его механических свойств [26]. Серия полимербетона различного состава с использованием оптимизированной пропорции смеси заполнителя с наименьшим содержанием пустот сообщается на основе концепции дизайна смеси при планировании экспериментов [27].
Ненасыщенные полиэфирные смолы и эпоксидные смолы являются наиболее часто используемыми системами смол для полимербетона из-за их низкой стоимости, доступности и хороших механических свойств [28]. Эпоксидный бетон имеет лучшие свойства, чем полиэфирный бетон, но свойства полиэфирного бетона можно улучшить до того же уровня путем добавления микронаполнителей [29]. Фенольная смола широко используется в качестве полимерцементного бетона. Однако в этой обзорной статье мы не обсуждаем бетон на основе фенольной смолы.Фурановые смолы широко используются в качестве полимербетона в европейских странах [30]. Но очень мало сообщений об использовании первичного или армированного полифурфурилового спирта (PFA) в качестве полимербетона. Это связано с тем, что реакции отверждения PFA из фурфурилового спирта имеют взрывоопасный характер. Но с акцентом на биополимеры или биорезины в 21 веке, важно переосмыслить использование PFA в качестве полимербетона, контролируя взрывной характер реакций отверждения.
2. Эпоксидный полимер и биокомпозиты
Эпоксидные смолы получают реакцией сочетания, которая содержит по крайней мере два активных атома водорода с эпихлоргидрином. Дегидрогалогенирование происходит в промежуточном продукте с образованием эпоксидной смолы (см. Схему 1).
Почти все эпоксидные смолы превращаются в твердые, неплавкие и нерастворимые трехмерные термореактивные сетки для их использования путем отверждения с помощью сшивающих агентов. Соединения с аминовыми функциональными группами и соединения с карбоксильными функциональными группами широко используются для отверждения эпоксидных смол.Конечные свойства отвержденных эпоксидных смол зависят от типа эпоксидных смол, отвердителя и процесса отверждения [31]. Исследователи пытаются сократить время отверждения эпоксидной смолы, потому что короткое время отверждения повысит эффективность процесса. В этом отношении Zhang et al. сообщили о предварительном нагреве формы и других добавках, используемых в эпоксидной смоле во время изготовления материала на основе эпоксидной смолы [32]. Температура стеклования () стандартной эпоксидной смолы составляет от 135 до 140 ° C, а для высокоэффективной эпоксидной смолы — от 170 до 180 ° C.Об этом сообщает Kasemsiri et al. что в жидкой эпоксидной смоле, содержащей скорлупу орехов кешью, использовались двухступенчатые процессы отверждения вместо одностадийного обычного процесса отверждения [33]. Об этом сообщает Pan et al. Этот анимированный лигнин увеличивал эффективность отверждения эпоксидной смолы из-за наличия значительного количества реакционноспособных аминогрупп [34]. Johnston et al. сообщили, что использование микроволн для отверждения эпоксидных смол не повлияло и на химические свойства полученной эпоксидной смолы.Фактически, скорость отверждения увеличивалась по сравнению с термическим отверждением, когда в качестве источника отверждения использовалось микроволновое излучение [35].
Биокомпозиты на основе эпоксидного полимера и натуральных волокон вызвали широкий исследовательский и технический интерес в последнее десятилетие. Натуральное волокно нельзя использовать непосредственно в качестве армирующего материала, но его необходимо обрабатывать щелочью, чтобы удалить лигнин и другие примеси [36]. Fiore et al. использовали обработанные гидроксидом натрия волокна кенафа для производства армированных волокном кенафа эпоксидных композитов с более высокими модулями по сравнению с чистой эпоксидной смолой [37].Rwawiire et al. разработаны биокомпозиты на основе зеленой эпоксидной смолы и биоразлагаемой коры ткани. Прочность при растяжении и изгибе зеленой эпоксидной смолы составляла 33 МПа и 207 МПа соответственно [38]. Bisaria et al. изготовили армированные джутовым волокном эпоксидные композиты, взяв джутовое волокно разной длины (5, 10, 15 и 20 мм). Они обнаружили, что свойства при растяжении и изгибе максимальны при длине джутовых волокон 15-16 мм [39]. С появлением нанотехнологий исследователи также исследуют нанокомпозиты с эпоксидной смолой в качестве матрицы и в одном отчете; Schilde et al.включили углеродные нанотрубки (УНТ) для изготовления композитов УНТ-эпоксид [40].
3. Эпоксидно-полимерный бетон
Реакция отверждения в эпоксидной смоле является экзотермической по своей природе, но имеет небольшую величину. Следовательно, его можно глубоко заливать в форму без перегрева во время приготовления полимербетона на основе эпоксидной смолы. Эпоксидно-полимерный бетон демонстрирует высокую физическую прочность, а также хорошее сцепление с бетонными и металлическими поверхностями. Благодаря этим свойствам его можно использовать во многих областях, где присутствуют большие нагрузки, сильные удары и химическое воздействие.Типичные применения эпоксидного полимербетона включают (i) покрытие полов, (ii) траншеи, (iii) отстойники, (iv) быстрый ремонт разрушенных полов из кислого кирпича, (v) профили из сборного полимербетона. свойства эпоксидно-полимерного бетона, а также эпоксидно-полимерцементного бетона.
Эпоксидно-полимерный бетон был приготовлен с использованием эпоксидной смолы и микрокремнезема в качестве наполнителя с различными размерами частиц и измельченных заполнителей разных размеров (0,4 мм и 0,8 мм) [42]. Плотность микрокремнезема, определенная в опубликованной литературе, варьировалась от 2100 до 2250 кг / м 3 .В приготовленный эпоксидно-полимерный бетон, помимо наполнителя и заполнителей, также был добавлен отвердитель. Прочность на сжатие, изгиб и прочность на разрыв были определены для эпоксидного полимербетона с 0,4 и 0,8 мм дробленых заполнителей. Предел прочности на сжатие для эпоксидно-полимерного бетона с заполнителями 0,4 мм и 0,8 мм оказался соответственно МПа и МПа. Значения прочности на изгиб для эпоксидно-полимерного бетона с заполнителем 0,4 мм варьировались в пределах 12.7 МПа и 9,32 МПа, а значения прочности на изгиб для 0,8 мм заполнителей варьировались от 17,57 МПа до 14,81 МПа. Значения прочности на разрыв для агрегатов 0,4 мм и 0,8 мм составили 12,1 МПа и 7,67 МПа, соответственно. Авторы заявили, что вышеуказанные механические свойства были получены при использовании 24% эпоксидной смолы (масса всего образца). Приведенные выше значения указывают на то, что заполнители большего размера снижают прочность на сжатие и прочность на разрыв эпоксидного полимербетона.
В другом отчете было приготовлено несколько образцов эпоксидно-полимерного бетона с использованием 15% эпоксидной смолы (вес всего образца) на основе бисфенола А [43]. В опубликованной работе тетраамин-3-этилен использовался в качестве отвердителя, а соотношение смола: отвердитель при использовании составляло 2: 1. Удельные веса отвердителя и смолы при 25 ° C, как сообщалось, составляли 1,07 и 1,18 г / см 3 соответственно. Мелкодисперсный, средний и крупный порошок кремнезема со средним размером частиц 50-60 мкм, мкм, 600 мкм, мкм и 1100 мкм, мкм, соответственно, использовался в качестве наполнителя при приготовлении эпоксидно-полимерного бетона.В качестве заполнителя использовался доломит с размером частиц менее 4,75 мм. Прочность на сжатие полученного эпоксидно-полимерного бетона была довольно высокой (128,9 МПа) по сравнению со значением 32,5 МПа для обычного бетона. Golestaneh et al. предсказал, что максимальная плотность заполнителя и наполнителя в смеси, вероятно, была причиной такого высокого значения для эпоксидно-полимерного бетона. Сообщается, что максимальное значение прочности на изгиб составляет 22,5 МПа. И снова это значение было примерно в 5 раз больше, чем прочность на изгиб обычного бетона.
Новый тип полимербетона на основе эпоксидной смолы с жидким силиконовым каучуком или порошком из шинных отходов был исследован для ремонта взлетно-посадочной полосы [44]. Механические характеристики эпоксидно-полимерного бетона с порошком из отходов шин были выше, чем у силиконовой резины. Elalaoui et al. сообщили, что эпоксидно-полимерный бетон также можно использовать при более высоких температурах. Они сообщили о механических и физических свойствах эпоксидно-полимерного бетона, подвергнутого воздействию температуры менее 250 ° C в течение 3 часов [45]. Когда эпоксидный полимерный бетон подвергался воздействию температур выше 150 ° C, он демонстрировал значительную потерю прочности, в основном из-за термоокислительной деструкции эпоксидного полимера и нарушения сцепления между заполнителями и связующим.С другой стороны, бетон на основе цемента имел более низкие механические свойства по сравнению с полимербетоном, когда он подвергался воздействию высоких температур.
Haidar et al. изготовили эпоксидную смолу, армированную смесью крупнозернистого и мелкого песка, называемой микрополимерным бетоном (MPC) [46]. Сообщается, что бетон MPC, разработанный с содержанием полимера 9%, показал самые высокие физико-механические характеристики, такие как прочность и жесткость. Также для образования ПДК количество взятой эпоксидной смолы было немного меньше, чем для обычного эпоксидно-полимерного бетона.
Эпоксидно-полимерный бетон, армированный натуральными и синтетическими волокнами, описан Рейсом и Феррейрой [47]. Они использовали кокосовый орех, жмых сахарного тростника и банановые волокна для изготовления полимербетона на основе эпоксидной смолы [13]. Результаты изгиба у полимербетона, армированного кокосовым волокном, были выше, чем у других полимербетонов из натуральных волокон, и также наблюдалось увеличение по сравнению с неармированным полимербетоном. Эпоксидно-полимерный бетон, армированный рубленым углеродом и стекловолокном (длиной 6 мм), также исследовали Рейс и Феррейра [47].Кремнеземный песок в качестве заполнителя смешивали с эпоксидной смолой. Авторы предварительно обработали стекловолокно силаном, чтобы улучшить адгезию между волокнами и смолой. Вязкость разрушения полимербетона, армированного углеродным волокном, увеличилась до 29%, в то время как полимербетон из стекловолокна увеличился до 13% по сравнению с эпоксидным неармированным полимерным бетоном.
Отходы становятся неотъемлемой частью нашей жизни. Отходы могут использоваться для армирования полимербетона на основе эпоксидной смолы. Летучая зола и твердые отходы красного шлама использовались при приготовлении полимербетона для улучшения физических свойств и механической прочности полимербетона [48].Для приготовления композитов использовалось от 8 до 12% золы, от 12 до 25% красного шлама и 30–35% эпоксидной смолы. Использовали около 10–15% наполнителя в виде порошка кремнезема. Литой полимерный бетон с 35% смолы, 25% летучей золы и 15% микрокремнезема был исследован на их прочность на изгиб. Сообщенное значение прочности на изгиб составило 21,53 МПа. Мраморные отходы смешивали с коммерческой эпоксидной смолой для изготовления эпоксидно-полимерного бетона [49]. Было замечено, что введение частиц отходов обработки мрамора увеличивает 10% -ную температуру разложения чистой эпоксидной смолы на 5–50 ° C.Композиты, армированные отходами обработки мрамора — пемза, показали увеличение модуля упругости примерно на 10%, тогда как композиты, армированные отходами обработки мрамора, сепиолитом или цеолитом, показали увеличение модуля упругости примерно на 76,67–143,33% по сравнению с матрицей из чистой эпоксидной смолы. Таким образом, механические свойства эпоксидно-полимерного бетона улучшаются при добавлении отходов на основе мрамора или глины.
Эпоксидные смолы используются не только как полимербетон, но и как полимерцементный бетон.Эпоксидная эмульсия была приготовлена путем эмульгирования эпоксидной смолы на основе диглицидилового эфира бисфенола А и отвердителя на основе аминоамида в воде с использованием неионогенного поверхностно-активного вещества, чтобы ее можно было использовать в качестве полимерцементного бетона [50]. Образцы бетона на основе эпоксидного полимерного цемента были приготовлены путем варьирования соотношения полимерцемент от 0% до 30% по массе цемента. Прочность на сжатие немодифицированного образца раствора, отвержденного водой, увеличилась с 39,5 МПа через 28 дней до 45,0 МПа через 90 дней отверждения. Было замечено, что как через 28, так и через 90 дней прочность раствора на сжатие увеличивалась с увеличением соотношения полимер-цемент.Прочность на изгиб немодифицированного раствора, отверждаемого водой, составляла 7,8 МПа. Прочность на изгиб образцов полимерно-модифицированных строительных смесей, отвержденных на воздухе, была меньше, чем у образцов немодифицированных растворов, отвержденных водой. Однако для обеих полимерных систем прочность на изгиб была лучше, чем у контрольных образцов, отвержденных водой, при соотношении полимер-цемент 30%. При соотношении полимер-цемент 30% прочность на изгиб образцов раствора, модифицированного эпоксидной смолой, была примерно на 10% выше, чем у образцов, отвержденных во влажном состоянии. Это показало, что добавление полимера к цементному раствору улучшает удобоукладываемость и увеличивает прочность на изгиб и сжатие.Также было заявлено, что строительный раствор на основе эпоксидной эмульсии может использоваться для ремонтных работ во влажных и промышленных средах.
4. Полиэфирный полимер и биокомпозиты
Реакция отверждения полиэфира проходит в две стадии. На первой стадии при 100 ° C и выше реакции гликолей с ангидридами двухосновной кислоты, такими как фталевый и малеиновый ангидриды, проводят в инертной атмосфере. Поскольку реакция 1-й стадии является экзотермической по своей природе, температура реакционной системы повышается до более 150 ° C.На этом этапе половина сложных эфиров конденсируется в полимеры с выделением воды в качестве побочного продукта. Поскольку реакция полиэтерификации обратима по своей природе, удаление воды на последней стадии процесса реакции имеет важное значение:
Мониторинг реакций отверждения при полиэтерификации осуществляется с помощью дифференциальной сканирующей калориметрии (ДСК) [51]. Исследователи также пытаются производить полиэфиры из возобновляемых источников. Это в значительной степени уменьшит углеродный след. Dai et al.синтезировали три ненасыщенных полиэфира на биологической основе из итаконовой кислоты и различных диолов, полученных из возобновляемых источников [52].
Чистая полиэфирная смола показывает предел прочности и модуль упругости ~ 68 МПа и ~ 3,1 ГПа. Прочность на изгиб и модуль упругости при изгибе чистых полиэфирных смол составляют около 110 МПа и 3,44 ГПа соответственно. Обработанные гидроксидом натрия беспорядочно ориентированные бамбуковые волокна, армированные полиэфирными биокомпозитами с более высокой прочностью на растяжение и сжатие по сравнению с неармированной полиэфирной смолой, были изготовлены Manalo et al.[53]. Подобным образом обработанные щелочью полиэфирные биокомпозиты, армированные жмыхом, были изготовлены Naguib et al. [54]. В этом отчете реакция сшивания проводилась с использованием пероксида метилэтилкетона в качестве катализатора и октоата кобальта в качестве ускорителя. Джутовое волокно длиной 5-6 мм было использовано Gopinath et al. для изготовления биокомпозитов на основе эпоксидных смол [55]. Стекловолокно широко используется в качестве армирующего агента для композитов на основе полиэфира. Полиэфирная смола, армированная стекловолокном, показала предел прочности и модуль упругости ~ 110 МПа и 5.5 ГПа соответственно. Прочность на изгиб и модуль упругости при изгибе полиэфирной смолы, армированной стекловолокном, составляли около 193 МПа и 5,86 ГПа соответственно. Смеси натуральных и синтетических волокон, таких как сизаль-джут-стеклянные волокна, использовались для изготовления полиэфирных композитов [56]. Ojijo и Ray в своей обзорной статье сообщили о нанокомпозитах, приготовленных из алифатических полиэфиров и наноглины [57].
5. Полиэфирно-полимерный бетон
Полиэфирный бетон используется в строительстве более 20 лет.Этот тип полимербетона может выгодно заменить традиционный портлендский бетон в ситуациях, когда требуется быстрое уплотнение материала. Строительный материал из полиэфирного полимербетона демонстрирует превосходную химическую стойкость и физические свойства, такие как высокая прочность и относительно низкая усадка. Изобретение, упомянутое в патенте США 4371639A, было направлено на отверждаемые полимербетонные композиции, особенно подходящие для строительных изделий, содержащие (1) полиэфирную композицию, (2) смесь заполнителей, содержащую песок, а также летучую золу и (3) инициатор. [58].Эти композиции особенно подходят для использования при изготовлении труб, настилов мостов, водосбросов плотин, строительных панелей и футеровки резервуаров.
Полиэфирный бетон стоит дорого, и это связано с тем, что заполнители, используемые в рецептуре, необходимо сушить перед их включением в полимерную матрицу. Игнасио и др. использовали различные системы отверждения (метакриловая кислота и малеиновый ангидрид) для проверки гипотезы о том, что введение кислотных функциональных групп в ненасыщенные полиэфиры на основе изофталевой кислоты может как ограничить пагубное влияние влаги в процессе отверждения, так и улучшить межфазные взаимодействия даже в полиэфирном бетоне, содержащем влажные агрегаты [59].Механические свойства полученного полиэфирного бетона оценивались испытаниями на сжатие. Результаты показали, что метакриловая кислота и малеиновый ангидрид, при использовании в качестве отвердителей, привели к производству полиэфирного бетона, имеющего более высокие механические свойства как в сухом, так и во влажном состоянии, чем обычный полиэфирный (на основе изофталевой кислоты) бетон [59].
Полимербетонные смеси на основе полиэфирной смолы в качестве органического связующего, летучей золы и речного песка в виде мелких заполнителей и гранита в качестве крупных заполнителей были приготовлены Варугезе и Чатурведи [18].Летучая зола использовалась вместо речного песка, который обычно использовался при строительстве обычных цементобетонных систем. Такие свойства, как время отверждения, прочность на изгиб и сопротивление водопоглощению, были изучены путем изменения уровня летучей золы. Варугезе и Чатурведи отметили, что летучая зола может использоваться в качестве мелкозернистого заполнителя для частичной или полной замены обычного речного песка в полимербетонных системах. При более высоком уровне летучей золы свойства полиэфирного полимербетона ухудшаются из-за увеличения количества смолы в смеси.Время отверждения, прочность и устойчивость к водопоглощению полимербетона, наполненного летучей золой, с использованием ненасыщенного полиэфира в качестве связующего для смолы, могут быть дополнительно улучшены [18].
Пористый полимерный бетон был разработан корейскими учеными с использованием ненасыщенной полиэфирной смолы в качестве связующего, переработанного заполнителя в качестве крупного заполнителя, а также летучей золы и доменного шлака в качестве наполнителя для проницаемого покрытия [60]. Были исследованы механические свойства полимербетона, которые составили более 18 МПа.Hwang et al. заменил наполнитель (карбонат кальция) и мелкий заполнитель (речной песок) летучей золой и быстроохлаждаемым стальным шлаком (RCSS), которые были получены из промышленных побочных продуктов для производства полиэфирного полимербетона [61]. Было обнаружено, что они эффективны для улучшения прочностных характеристик и долговечности, а также экономической эффективности полимербетона. Как сообщалось, разработанный продукт успешно снизил потребность в полимерном связующем на 21,3% по сравнению с обычным продуктом, что, в свою очередь, позволило сократить общие затраты на материалы на 18.5%. Однако использование RCSS показало снижение производительности в условиях повышенной температуры.
Сообщалось о влиянии гамма-излучения и размеров частиц мрамора на сжимающие свойства полимербетона с целью разработки полимербетона для несущих нагрузок [62]. Результаты показали, что деформация сжатия и модуль упругости зависят от комбинации размеров частиц мрамора и применяемой дозы облучения. Комбинация частиц среднего и большого размера обеспечивает самый высокий модуль упругости, а также высокие дозы облучения вызывают большее количество диспергированных частиц в единице объема, что обеспечивает большее сопротивление распространению трещин [62].Сообщалось, что характеристики полиэфирного полимербетона можно также улучшить за счет армирования полиэфира, армированного сталью и армированными волокнами полимерными стержнями, а также порошковыми отходами стекла [63, 64]. Переработанные пластиковые отходы полиэтилентерефталата (ПЭТ) использовались для приготовления полимербетона с использованием ненасыщенной полиэфирной смолы [11, 65]. Сообщалось, что смолы на основе переработанного ПЭТ могут быть использованы для производства высококачественного полимерного бетона для сборных железобетонных изделий, таких как компоненты коммунальных служб, транспортные компоненты, основания машин и компоненты зданий.Важно отметить, что использование переработанного ПЭТ в полимербетоне помогло снизить стоимость материала.
Было проведено сравнительное исследование влияния термических эффектов на прочность на изгиб двух различных композиций связующих полимерных строительных смесей. Для этого образцы ненасыщенных полиэфирных и эпоксидно-полимерных растворов подвергали воздействию большого диапазона температур от -20 до + 100 ° C, а затем испытывали на изгиб. Отчетливо наблюдалось снижение прочности [21].
Сообщалось о влиянии возраста на прочность на сжатие и изгиб рециклированного ненасыщенного полиэфирного полимерного бетона [66]. Полимербетон на основе переработанных ненасыщенных полиэфирных смол достиг более 80% своей 28-дневной прочности за семь дней. Благодаря высокой прочности на сжатие, переработанный полимерный бетон на основе ненасыщенной полиэфирной смолы может использоваться в более тонких секциях сборных элементов. С введением содержания монтмориллонита (от 1% до 5%) прочность на сжатие переработанного ненасыщенного полиэфирного полимербетона увеличилась примерно на 12%.Однако при 8% монтмориллонита прочность образцов снизилась.
Также сообщалось о влиянии температуры на прочность на сжатие и изгиб рециклированного ненасыщенного полиэфирного полимерного бетона [66]. Переработанный ненасыщенный полиэфирный полимерный бетон теряет прочность при повышении температуры с 20 ° C до 30 ° C. Несмотря на потерю прочности при высоких температурах, переработанный ненасыщенный полиэфирный полимерный бетон показал высокую прочность на сжатие по сравнению с бетоном из портландцемента.
Химическая стойкость полимербетона на основе полиэфира была испытана в семи различных кислотных средах, которые часто являются причиной коррозионных процессов в промышленных средах [67]. Ни одна из композиций не показала признаков физических изменений поверхности или потери веса. Было снижение прочности на изгиб образцов, подвергшихся воздействию коррозионных агентов, и этот эффект был более выражен в композициях с более низкими концентрациями наполнителя. Анализ растровой электронной микрофотографии также показал, что химическая атака произошла на границе раздела полимерная матрица-агрегат.Горнински и др. также сравнили механические свойства полимербетона по сравнению с бетоном из портландцемента [68].
6. Полифурфуриловый спирт
6.1. Предпосылки
Смола PFA — это 100% смола биологического происхождения, которая отверждается из фурфурилового спирта (FA) с образованием термореактивного полимера [69]. Производство PFA начинается с фурфурола, полученного в результате гидролиза сельскохозяйственных отходов, богатых гемицеллюлозой. Затем фурфурол восстанавливается до FA, которая полимеризуется до смолы PFA.Мономеры FA могут быть смешаны с новой системой заполнителей для получения полимербетона с улучшенными химическими и физическими характеристиками [70]. Полимеры фурана нашли широкое применение при формировании литейных стержней, в которых смешивались мелкие заполнители (песок). Все крупногабаритные заполнители были исключены в рецептурах полимербетона на основе PFA. В Соединенных Штатах были проведены исследования систем полимербетона с использованием фурановых полимеров. Было обнаружено, что на характеристики полимербетона значительное влияние оказал выбор заполнителя для производства фуранового полимербетона с диапазоном прочности на сжатие от 5000 до 15000 фунтов на квадратный дюйм.В полимербетоне на основе эпоксидной смолы и полиэфира авторы также использовали заполнители разных размеров, и, следовательно, выбор заполнителей важен в рецептурах полимербетона [18, 42].
Полимерный бетон, описанный в патенте США 4373058, был образован из смеси мономера FA и кислотного отвердителя, смешанных с системой минеральных заполнителей. Мономер FA полимеризовали in situ в смеси с получением сильно сшитого смолистого полимерного бетона, в котором минеральные агрегаты были диспергированы или связаны в полимерном связующем.Полимербетон, образованный из фурановых полимеров, обладал широчайшим диапазоном химической стойкости, о которой сообщалось, и был также полезен для производства годного к употреблению бетонного продукта из-за относительно низкой вязкости, простоты обращения, смешивания, уплотнения, текучести и отделки, а также быстрого отверждения при температурах окружающей среды. Из-за выгодной доступности сырья и экономичности по сравнению с другими органическими связующими мономер на основе фурана был использован в полимерном бетоне.
Кукачка и Сугама разработали полимербетон на основе FA для всепогодного ремонта бетонных и асфальтовых поверхностей [71].Для этого применения были установлены следующие критерии: (i) Высокая прочность при выдержке в один час. (Ii) Размещение материалов возможно во время сильных осадков при температурах от -32 до 52 ° C. (Iii) Химические составляющие низкая стоимость и долговременная стабильность при хранении. Этим требованиям удовлетворяет состав, состоящий из мономера FA, α , α , α -трихлортолуола, пиридина, силана, хлорида цинка, кремнеземного наполнителя и крупного заполнителя.
6.2. Реакции отверждения
Исследования смол PFA начались давно, но из-за сильно экзотермических реакций существует очень мало литературы, относящейся к смолам PFA [72, 73]. Также смолы PFA смешивают с термореактивными смолами на основе фенола для получения модифицированных смол [74]. Активными катализаторами для получения смол PFA являются серная кислота, бисульфат натрия, пара-толуолсульфоновая кислота (PTSA), алкансульфоновая кислота, имеющая от 2 до 14 атомов углерода, и пара-толуолсульфонилхлорид. При кислотном катализе Бренстеда или Льюиса ФА полимеризуется в ПФА [75, 76].Инертные материалы, такие как сульфат бария, диоксид кремния, углерод и асбест, также использовались с активным катализатором. Было отмечено, что после добавления PTSA к ЖК начинается полимеризация, которая носит медленный характер [77, 78]. Смола конденсационного типа, отверждаемая кислотой, состоящая из PFA или смесей PFA с другими смолами, отверждаемыми кислотой, также использовалась для обработки песчаных стержней или форм [79]. Этот продукт можно рассматривать как первый шаг к приготовлению бетона на основе PFA. В этом отчете диоксид серы был введен в формовочную композицию вместе с окислителем, который повлиял на окисление диоксида серы внутри литейной формы или стержневой композиции.Окислитель представлял собой органический пероксид, который вводили в песок или вводили в смолу. В US 4448234 изобретатели использовали тот же пероксид, но разные кислотные катализаторы для изготовления песчаных стержней и форм. В качестве кислот использовались фосфорная кислота, фторборная кислота или плавиковая кислота [80]. В схеме реакции отверждения смол PFA указано, что на первой стадии гидроксиметильная группа FA конденсируется в положении C5 другого фуранового кольца, что приводит к линейным олигомерам, связанным метиленовыми связями [81].На втором этапе эти линейные олигомеры были сшиты в разветвленные черные материалы, и это было продемонстрировано с помощью экспериментов ЯМР [72].
Недавно был предложен более экологичный и устойчивый каталитический путь для замены опасных кислотных катализаторов [41]. Органически модифицированный монтмориллонит (Org-MMT) и, для сравнения, MMT натрия (Na-MMT) использовали для оценки каталитического эффекта на полимеризацию FA в PFA. Катион октадециламмония (ODA) также использовался в качестве гомогенного кислотного катализатора, чтобы подчеркнуть особую роль этого межслойного катиона, присутствующего в Org-MMT.Как сообщается в этой статье, FA / Org-MMT полимеризуется быстрее, чем FA / ODA, но начало полимеризации слегка сдвигается в сторону более высокой температуры из-за начального интеркалирования между слоями MMT (Рисунок 1). Реологическое и хемореологическое поведение смолы PFA было изучено Домингесом и Мадсеном с целью разработки процесса отверждения [82].
6.3. PFA Биопластики / Композиты
Недавно PFA были объединены с изолятом соевого белка (SPI) для производства биопластиков [83].Биопластики были приготовлены физически путем адсорбции нерастворимых в воде PFA на SPI. В этом методе раствор моногидрата PTSA по каплям добавляли к FA при комнатной температуре, чтобы катализировать FA. Затем пленки SPI были погружены в катализированную FA на различные интервалы времени, и по истечении заданного времени пленки SPI были удалены и охарактеризованы.
Поглощение катализированной FA на SPI увеличилось с 18% до 26% с увеличением времени погружения SPI с 24 до 60 часов, и это было связано с гидрофильной природой катализированной FA.На следующем этапе пленки SPI с абсорбированной FA были отверждены в воздушной печи в течение 2 часов при 145–150 ° C для получения пленок SPI, адсорбированных PFA. Вес PFA, адсорбированного на пленке SPI, зависел от времени погружения. Морфология поверхности показала присутствие физически адсорбированных FA и PFA на поверхности SPI (рисунки 2 и 3).
Биокомпозиты PFA, армированные льняным волокном, были также получены Кумаром и Анандживала [84]. В этом методе PTSA растворяли в FA. Перед использованием смолы выдерживали в течение 10 дней при низкой температуре (10–15 ° C), не мешая получению частично отвержденной и вязкой смолы PFA.10 слоев тканого льняного волокна были отдельно погружены в смолы PFA и уложены друг над другом. Льняное волокно, смоченное смолой PFA, помещали в сушильный шкаф при 100 ° C примерно на 5 ч для приготовления препрегов. После этого препреги подвергали прессованию при 170 ° C в течение 2 часов, чтобы получить образцы биокомпозита толщиной около 4 мм. Соотношение PFA: ткань в отвержденных биокомпозитах составляло 60: 40. Биокомпозиты PFA / волокна агавы также были приготовлены путем включения различных массовых фракций микроволокна в матрицу PFA [85].
Сообщалось о синтезе упорядоченных мезопористых композитов ПФА-диоксид кремния с помощью органосилана с использованием ТЭОС, 3- (триэтоксисилил) фурана и фурфурилового спирта в качестве предшественников и триблок-сополимера F127 в качестве структурно-регулирующего агента через процесс EISA [86 ]. Зарбин и др. сообщили о получении стеклоуглерода путем пиролиза PFA внутри пор стекла Vycor, которое использовалось в качестве темплата [87]. Получены нанокомпозиты стекло / полимер. Эти нанокомпозиты обрабатывали HF для удаления фракции кремнезема.О создании бионанокомпозитов путем включения нитевидных волокон целлюлозы в PFA сообщили Прангер и Танненбаум [88].
Супергидрофобные пленки композитов ПФА / многослойные углеродные нанотрубки были получены с использованием модифицированных фторуглеродом МУНТ (MWNT-OOCC 7 F 15 ), PFA и PTFE [89]. Образованные многомасштабные структуры шероховатости и более низкая поверхностная энергия в этих нанокомпозитах сыграли важную роль в создании супергидрофобных поверхностей композитов PFA / MWNTs.
6.4. Механические свойства
Сообщается, что прочность на разрыв и модуль Юнга чистого PFA составляют МПа и ГПа соответственно [78]. Однако удлинение при разрыве было слишком низким [78]. Чтобы увеличить удлинение при разрыве, изолят соевого белка был включен в PFA для изготовления пленки SPI-PFA [83]. Механические характеристики пленок абсорбированного / адсорбированного соевого белка (ат.% Относительной влажности) показали предел прочности на разрыв около 20 МПа и модуль Юнга 0,5 ГПа.
Натуральные волокна, такие как лен и агава, использовались для улучшения механических свойств материалов на основе PFA [84, 85].Поведение биокомпозитов на основе ПФА, армированных льняным волокном, при растяжении было изучено путем проведения испытаний на растяжение. В этом случае PFA показал предел прочности на разрыв 15,65 МПа, а введение льняного волокна не повлияло на прочность биокомпозитов на разрыв, так как значение практически не изменилось, то есть 15,53 МПа [84]. Однако удлинение при разрыве увеличивалось с введением льняного волокна. Произошло снижение прочности на разрыв с 15,53 МПа до 10,07 МПа и дальнейшее увеличение относительного удлинения при разрыве для образцов ПФА, армированных влажным льняным волокном.Подобная тенденция в механических свойствах наблюдалась для композитов PFA, армированных агавой, с различной загрузкой микроволокон агавы [85].
Образцы из чистого PFA показали более высокую прочность на изгиб 60,2 МПа и модуль упругости при изгибе 3,2 ГПа. Введение льняного волокна снизило прочность на изгиб с 60,2 МПа до 23,2 МПа, а также модуль упругости с 3,2 ГПа до 2,4 ГПа [84]. Произошло дальнейшее снижение модуля упругости при изгибе с 2,4 ГПа до 2,2 ГПа для влажных композитных образцов. Свойства изгиба также показали тенденцию к снижению с увеличением загрузки волокон агавы в PFA [85].Включение льняного волокна в PFA показало снижение ударной вязкости с 30,4 Дж м -1 до 24,9 Дж м -1 [84]. Далее оно уменьшилось до 14,8 Дж · м -1 для влажных образцов биокомпозита. Уменьшение растягивающего и изгибного напряжения, а также энергии удара для влажных образцов было связано с водопоглощающей способностью льняного волокна. В композитах миграция воды через полимер может привести к нарушению границы раздела волокно / полимер, что снижает общую прочность композита.Сообщалось, что в случае армирования льном это могло быть еще более драматичным, поскольку лен имеет тенденцию впитывать довольно большое количество воды при воздействии на него.
6.5. Термические свойства
PFA изначально имел очень высокую термическую стабильность с высоким выходом полукокса и (представляет собой температуру, при которой потеря массы максимальна). PFA показал потерю массы около 0,5% при 200 ° C, а для образцов сухого биокомпозита она увеличилась до 5% (рис. 4). Увеличение потери массы ниже 200 ° C было связано с гидрофильной природой льняного волокна, включенного в PFA [84].Точно так же было замечено, что пленки абсорбированного / адсорбированного PFA арилированного соевого белка показали более высокую термическую стабильность, чем пленки нативного SPI [83]. Пленки SPI-PFA показали две значимые потери массы в температурном диапазоне, обозначенные как в диапазоне температур 200–300 ° C и в диапазоне температур 300–400 ° C. Потеря массы на первом этапе объяснялась потерей абсорбированной / адсорбированной влаги. Потеря массы на втором этапе была связана с деградацией материалов SPI в PFA.
Огнестойкость PFA и PFA, армированного льняным волокном, оценивалась коническим калориметром [84].Параметры, обычно доступные в эксперименте с коническим калориметром, включали скорость тепловыделения (HRR) и особенно его пиковое значение (PHRR), общее тепловыделение (THR), объем образовавшегося дыма, скорость потери массы, время до возгорания и время до пикового нагрева. скорость выпуска. Волокна льна показали очень низкое время воспламенения (5 сек). Введение PFA в льняное волокно увеличивало время воспламенения с 5 до 105 с. Это показало, что термостойкость материалов PFA, армированных натуральным волокном, увеличилась.
6.6. Водостойкость
Чистые пластмассы на основе PFA полностью не растворимы в воде по своей природе. Однако включение натуральных волокон в биокомпозиты на основе PFA показало тенденцию к водопоглощению из-за гидрофильной природы волокон [84, 85]. Пленки SPI, абсорбированные / адсорбированные PFA, показали максимальное водопоглощение 50% при полном погружении в воду на 24 часа с хорошей стабильностью размеров. Это было связано с наличием водопоглощающего материала, то есть SPI [83].
6.7. Продукты, доступные из полифурфурилового спирта
В приведенной выше литературе исследуются возможности использования биопластов на основе PFA или материалов, армированных натуральным волокном, в новых и отремонтированных конструкциях путем замены традиционных армированных волокном полимеров и кирпича.Материал на основе PFA будет недорогой, легкой, прочной и устойчивой биокомпозитной или нанокомпозитной строительной системой на основе панелей, профилей, каркасов и многослойных структур (рис. 5).
В одной из публикаций было проведено сравнение между цементными кровельными листами, армированными асбестовыми волокнами, слоновой травой и остатками сахарного тростника на основе некоторых физико-механических свойств и производных затрат. Листы из травяного волокна оказались наиболее привлекательным выбором для кровли [90].Многие другие натуральные волокна также были исследованы для изготовления биоразлагаемых композитов [91]. Панели на основе биокомпозитов из PFA и льняного волокна были успешно отформованы под давлением путем армирования PFA 10 слоями тканого льняного полотна [84]. Kukacka et al. сообщили о приготовлении водосовместимого полимерного бетона на основе фурфурилового спирта, содержащего 8% воды по массе заполнителя, с прочностью на сжатие> ~ 2000 фунтов на квадратный дюйм (> 13,78 МПа) в возрасте 1 часа при 24 ° C [92].
7. Заключение и дальнейшие направления деятельности
Бетон является основным компонентом строительного сектора.Как правило, значительная часть бетона используется для изготовления тротуаров, несущих конструкций зданий и оборудования. Составы бетона основаны на смеси мелких и крупных минеральных заполнителей и пасты портландцемента и воды. Но проблема в том, что эти ресурсы ограничены, поэтому через несколько сотен лет портландцемент уже не будет в изобилии.
Другой вариант — полимербетон на основе термореактивных смол на полиэфирной и эпоксидной основе. Рахман и Ислам сообщили об использовании эпоксидной смолы для приготовления полимерцементного раствора и полимерного раствора.Результаты показали увеличение механической прочности как полимерцементного раствора, так и полимерного раствора с добавлением эпоксидной смолы [93]. О бетоне, модифицированном латексом, также сообщили Jamshidi et al. [94]. Настоящая обзорная статья дает представление о полимербетоне на основе эпоксидной смолы и полиэфира с улучшенными физическими свойствами по сравнению с обычным портландцементным бетоном. Было заявлено, что этот полимербетон может использоваться для самых разных целей, таких как покрытия, покрытия и ремонт, а также для приложений в тяжелых промышленных средах, в которых требуются прочность, гибкость и химическая стойкость.Хорошо известно, что прочность на сжатие и прочность на изгиб полимербетона зависят от содержания термореактивной смолы. Однако оптимальное содержание термореактивной смолы для конкретной системы полимербетона также зависит от природы заполнителя, используемого в системе. Опять же, следует отметить, что и эпоксидные, и полиэфирные смолы являются синтетическими по своей природе, поэтому полимербетон на основе этих двух полимеров относится к категории ограниченных ресурсов.
Полимербетон на основеPFA может быть ответом на оба вышеуказанных вопроса, поскольку он получен из возобновляемых источников и может использоваться в качестве полимербетона вместо обычного портландцементного бетона.Сообщалось, что для применения в тяжелых промышленных условиях требуется более химически стойкий полимерный бетон, и тогда возможность использования полимербетона на основе фурана возрастает.
Из обзора литературы можно сделать следующие выводы: (i) Прочность на изгиб эпоксидно-полимерного бетона, армированного натуральным волокном, составляет около 18 МПа. Включение золы и красного шлама в эпоксидную и полиэфирную смолу показало прочность на изгиб 21,3 и 18 МПа.5 МПа, соответственно, и были лучше, чем у портландцементного бетона. (Ii) Прочность на изгиб и модуль упругости при изгибе композитов PFA, армированных натуральным волокном, составляли МПа и ГПа, которые были сопоставимы с таковыми для композитов, армированных натуральным волокном, эпоксидной смолы или композитов, армированных полиэфиром. (iii) Прочность на сжатие (МПа) полимербетона на основе PFA была ниже, чем у эпоксидно-полимерного бетона (МПа). (iv) Биополимерный бетон имел сравнимые механические свойства с полимером на основе эпоксидной смолы и полиэфира, а также источники сырье было экологически чистым и биологическим.
Наконец, мы можем заявить, что биополимерный бетон будет предлагать опорные конструкции и перегородки с полной экологической проверкой. Рисунок 6 дает нам представление о формировании полимербетона на основе PFA с каменной структурой или гладкой структурой в зависимости от скорости отверждения, которая зависит от температуры. Можно успешно изготавливать полимербетон на основе PFA, но бетон на основе полимера стоит дорого, и продукт подвергается размерной усадке после отверждения.
Конкурирующие интересы
Автор заявляет об отсутствии конкурирующих интересов.
Произошла ошибка при настройке пользовательского файла cookie
Этот сайт использует файлы cookie для повышения производительности. Если ваш браузер не принимает файлы cookie, вы не можете просматривать этот сайт.
Настройка вашего браузера для приема файлов cookie
Существует множество причин, по которым cookie не может быть установлен правильно. Ниже приведены наиболее частые причины:
- В вашем браузере отключены файлы cookie. Вам необходимо сбросить настройки вашего браузера, чтобы он принимал файлы cookie, или чтобы спросить вас, хотите ли вы принимать файлы cookie.
- Ваш браузер спрашивает вас, хотите ли вы принимать файлы cookie, и вы отказались. Чтобы принять файлы cookie с этого сайта, используйте кнопку «Назад» и примите файлы cookie.
- Ваш браузер не поддерживает файлы cookie. Если вы подозреваете это, попробуйте другой браузер.
- Дата на вашем компьютере в прошлом. Если часы вашего компьютера показывают дату до 1 января 1970 г., браузер автоматически забудет файл cookie. Чтобы исправить это, установите правильное время и дату на своем компьютере.
- Вы установили приложение, которое отслеживает или блокирует установку файлов cookie. Вы должны отключить приложение при входе в систему или проконсультироваться с системным администратором.
Почему этому сайту требуются файлы cookie?
Этот сайт использует файлы cookie для повышения производительности, запоминая, что вы вошли в систему, когда переходите со страницы на страницу. Чтобы предоставить доступ без файлов cookie потребует, чтобы сайт создавал новый сеанс для каждой посещаемой страницы, что замедляет работу системы до неприемлемого уровня.
Что сохраняется в файле cookie?
Этот сайт не хранит ничего, кроме автоматически сгенерированного идентификатора сеанса в cookie; никакая другая информация не фиксируется.
Как правило, в файле cookie может храниться только информация, которую вы предоставляете, или выбор, который вы делаете при посещении веб-сайта. Например, сайт не может определить ваше имя электронной почты, пока вы не введете его. Разрешение веб-сайту создавать файлы cookie не дает этому или любому другому сайту доступа к остальной части вашего компьютера, и только сайт, который создал файл cookie, может его прочитать.
Epoxy Resin — (почти) универсальный полимер
Держите эпоксидную смолу в своем арсенале среди других клеев…
Хотя мы рекламируем универсальность эпоксидной смолы, ей есть свое время и место. У этого чудесного клея так много применений для склеивания, нанесения покрытия и герметизации; он предназначен для образования очень стойкого твердого покрытия. Широко используется для рукоделия, изготовления и ремонта мебели, а также для множества поделок; хорошо иметь под рукой и другие клеи и адгезивы.
Ежедневные проекты и ремонт требуют правильного инструмента для работы. И есть несколько факторов, которые следует учитывать при выборе правильного клея, включая тип проекта или ремонта, задействованные материалы, а также время закрепления, высыхания и (полного) отверждения. В разделе «Выбор лучшего клея для работы» на сайте «Сделай сам» Instructables.com; Клеи, которые удобно иметь под рукой, делятся на три группы:
- Базовый — суперклей и универсальный клей
- Ориентированные на применение — клеи для дерева и резины, горячий клей, силикон и эпоксидная смола
- Специальные клеи — пластик Клей Cement & Gorilla Glue
Базовые клеи недороги, быстро сохнут и отлично подходят для множества мелких домашних ремонтов и фиксации различных предметов.Некоторые прикладные клеи предназначены для особых целей, например, для дерева и резины. Силикон — это больше герметик, например, для окон, он остается гибким и водонепроницаемым. Горячий клей часто используется мастерами для изготовления универсального клея. Эпоксидная смола обеспечивает превосходное сцепление, является отличным наполнителем, а также имеет преимущества покрытия и герметизации. Специальные клеи отлично подходят для работы с пластмассами.
Производство эпоксидных смол
Клеи бывают разных типов, и не все они предназначены для приклеивания ко всем материалам.У каждого из них есть свои преимущества и недостатки, поэтому при нанесении клея важно учитывать, какие требования предъявляются к вашему проекту. Например, эпоксидные смолы часто используются при создании печатных плат для компьютерной и электронной промышленности. К другим отраслям применения относятся авиационная, автомобильная и морская отрасли, где требуются прочные связи, а также устойчивость к влаге, химическим веществам и ударам.
На личной клейкой записке; недавно оторвалась любимая пара обуви, и поход к сапожникам казался нужным.Семейный местный сапожник был закрыт в праздничные выходные, поэтому я немного поработал над тем, что они будут использовать для ремонта. Оказывается, клей для обуви доступен в Интернете, он обеспечивает превосходное сцепление, но остается гибким. И вуаля! Не нужен сапожник или новая пара обуви!
Эпоксидные смолы — Pham — — Основные справочные работы
Эпоксидные смолы представляют собой реакционноспособные промежуточные продукты, используемые для производства универсального класса термореактивных полимеров. Они характеризуются наличием трехчленной циклической простой эфирной группы, обычно называемой эпоксидной группой, 1,2-эпоксидом или оксираном.Наиболее широко используемые эпоксидные смолы — это диглицидиловые эфиры бисфенола A, полученные из бисфенола A и эпихлоргидрина. Выдающиеся эксплуатационные характеристики термореактивных материалов, полученных из эпоксидных смол на основе бисфенола А, в значительной степени передаются за счет части бисфенола А (прочность, жесткость и характеристики при повышенных температурах), эфирных связей (химическая стойкость), а также гидроксильных и эпоксидных групп (адгезивные агенты). Помимо бисфенола А, для производства специальных смол используются другие исходные материалы, такие как алифатические гликоли и фенол, а также новолаки с или -крезолом.Эпоксидные смолы могут также включать эпоксидсодержащие соединения на основе ароматического амина, триазина и циклоалифатических скелетов.
Было описано множество реагентов для перевода жидких и твердых эпоксидных смол в отвержденное состояние, которое необходимо для достижения конечных свойств конечного использования. Отвердители или отвердители делятся на каталитические или ядерноактивные. Каталитические отвердители инициируют гомополимеризацию смолы, катионную или анионную, как следствие использования кислоты или основания Льюиса в процессе отверждения.Активные отвердители представляют собой полифункциональные соединения, обычно содержащие активные атомы водорода, которые используются в стехиометрических количествах с эпоксидными смолами. Важные классы активных отвердителей включают многофункциональные амины и их амидопроизводные, полифенолы, полимерные тиолы, поликарбоновые кислоты, ангидриды, фенолформальдегидные новолаки и резолы, а также аминоформальдегидные смолы.
Эпоксидные смолы широко используются на рынке защитных покрытий, где важны высокая коррозионная стойкость и адгезия к основанию.Эпоксидные смолы получили широкое распространение в защитных покрытиях, а также в электротехнике и конструкциях благодаря их исключительному сочетанию таких свойств, как ударная вязкость, адгезия, химическая и термическая стойкость, а также хорошие электрические свойства.
Смола или полимер? Какой сегодня наиболее популярный термин для обозначения пластиковых пакетов pac
?Более популярный термин для сырого пластикового упаковочного материала с самого начала стал лидером нашего опроса и остался там, хотя и с меньшим отрывом, поскольку откликнулось все больше профессионалов в области упаковки.Но причины, по которым люди предпочитают один термин другому, в любом случае довольно убедительны.
Чуть более половины (51%) респондентов поддерживают термин «смола». Почему? Похоже, от старых привычек трудно избавиться, так как многие участники опроса высказывали похожие комментарии, как и этот человек: «Вот как я этому научился в школе упаковки».
И, находясь в Риме, делайте то же, что и они, как говорят эти респонденты:
«Это то, что я узнал первым, и то, что я слышу чаще всего».
«Чаще используется нашими поставщиками и пользователями.
Другие указали на более технические причины, почему они склоняются к «смоле»:
«Хотя термин смола вызывает мысли о растительной« слизи », такой как янтарь, это гораздо более практичный термин для использования в индустрии пластмасс. по сравнению с полимером. Полимер описывает материал на макромолекулярном уровне, тогда как смола описывает материал в объемной форме ».
«Смола может включать добавки и состоять из более чем одного типа полимера. Например, «смола» АБС имеет в качестве компонентов полимер акрилонитрил и полимер бутадиена.
Сторонники полимеров
Но люди, хорошо демонстрирующие упаковку (42%), говорят, что они считают «полимер» лучшим описателем — во многих случаях по научным причинам:
«Смола, похоже, не подходит. охватывают также весь спектр используемых материалов ».
«Полимер заставляет меня думать о готовой упаковке, а смола для меня означает сырье. Я работаю в готовой упаковке, так что «Полимер» мне подходит. К тому же, когда вы добавляете к полимеру слово «матрица», это звучит очень круто.Матрица из смолы просто не течет, как полимерная матрица ».
«Поскольку я ученый-полимер по образованию, я предпочитаю термин« полимер », поскольку для меня он представляет собой ключевой функциональный компонент. Для меня смола — это полимер плюс добавки ».
«Это более точный термин для описания семейства материалов, которые экструдируются в жесткую и гибкую упаковку».
Лишь горстка людей (4% для каждого варианта) говорят, что они либо «не знают», либо выберут что-то другое.Например, этот респондент объясняет, почему он / она выбрал категорию «Другое»: «Я думаю о смоле как о чем-то, что не находится в ее окончательном физическом состоянии. Что касается сырья, я думаю о полимере как о чем-то, что уже целое, но просто подвергается процессу термоформования, чтобы изменить свою форму ».
Ясно, что профессионалы в области упаковки приветствуют разнообразие фраз так же, как и разнообразие мыслей. Это одна из причин, по которой мне нравится освещать такую динамичную и инновационную отрасль.
Это результаты неофициального онлайн-опроса, проведенного агентством Packaging Digest с 19 февраля по 7 марта 2016 г., когда мы получили 132 ответа.
______________________________________________________________________
Ознакомьтесь с множеством новых идей в пластиковой упаковке на выставке EastPack 2016, 14–16 июня, в Нью-Йорке.
______________________________________________________________________
Разница между смолой и полимером
Ключевое различие между смолой и полимером состоит в том, что смолы имеют малую молекулярную массу, тогда как полимеры имеют большую молекулярную массу.
Мономеры — это строительные блоки полимеров. Это либо простые, либо сложные молекулы с двойными связями или другой функциональной группой, такой как –OH, -NH 2 , –COOH и т. Д. Ненасыщенные двойные связи или функциональные группы необходимы в процессе полимеризации, когда несколько мономеров связываются с образованием полимер. Эти полимеры бывают натуральными или синтетическими. Синтетические соединения производятся для имитации природных соединений, и теперь они широко используются. Смола — это природное мономерное соединение, которое также имеет синтетический аналог.
СОДЕРЖАНИЕ
1. Обзор и основные отличия
2. Что такое смола
3. Что такое полимер
4. Сравнение бок о бок — смола и полимер в табличной форме
5. Резюме
Что такое смола?
Смола — это органический материал, который естественным образом образуется в растениях. Это вязкая жидкость прозрачного или темно-коричневого цвета. У некоторых растений сок растений содержит смолы. Хотя это жидкости и вязкие, они могут затвердеть при обработке химикатами. Уровень жесткости зависит от растения, производящего смолу.Этот материал не растворяется в воде, но растворяется в спирте. Существуют разные классы смол, и их химический состав различается.
В основном смолы содержат летучие терпены. Из-за терпенов смолы приобретают характерный запах. Чаще всего бициклические терпены встречаются в таких смолах, как альфа-пинен, бета-пинен, дельта-3 карен и сабинен. Кроме них, существуют также моноциклические (лимонен) и трициклические терпены (сесквитерпены, лонгифолен).
Рисунок 01: Смола в сосне
Кроме того, в небольших количествах содержатся нелетучие твердые вещества, которые делают смолу густой и липкой.Мы можем разделить эти отдельные соединения в смоле фракционной перегонкой.
Смолы находят множество применений. Люди использовали растительные смолы тысячи лет. Например, они полезны как компонент духов, лаков, лаков, украшений и т. Д. Теперь ученые нашли способ производить смолы также синтетическим путем. Синтетические смолы важны как мономер для производства полимеров. Синтетические смолы более стабильны и однородны, чем натуральные. Они полезны при производстве пластмасс и красок; они также могут производить предметы, которые производятся с использованием натуральных смол.
Что такое полимер?
Полимеры — это большие молекулы с повторяющимися структурными единицами мономеров. Эти мономеры связываются друг с другом ковалентными связями с образованием полимера. Они имеют высокую молекулярную массу и состоят из более чем 10 000 атомов. Процесс их синтеза, который мы называем полимеризацией, включает образование более длинных полимерных цепей.
Существует два основных типа полимеров в зависимости от методов их синтеза. Если мономеры имеют двойные связи между атомами углерода, в результате реакций присоединения мы можем получить полимеры.Эти полимеры называются аддитивными полимерами. В некоторых реакциях полимеризации, когда два мономера соединяются друг с другом, небольшая молекула, такая как вода, удаляется. Такие полимеры представляют собой конденсационные полимеры.
Полимеры имеют очень разные физические и химические свойства, чем их мономеры. Более того, в зависимости от количества повторяющихся звеньев в полимере их свойства различаются. В окружающей среде присутствует большое количество полимеров, и они играют очень важную роль.
Рисунок 02: Пластик — это полимер
Синтетические полимеры также широко используются для различных целей.Полиэтилен, полипропилен, ПВХ, нейлон и бакелит — это некоторые синтетические полимеры. При производстве синтетических полимеров процесс всегда должен строго контролироваться, чтобы получить желаемый продукт. Синтетические полимеры важны как клеи, смазки, краски, пленки, волокна, пластмассовые изделия и т. Д.
В чем разница между смолой и полимером?
Смола — это органический материал, который естественным образом образуется в растениях, в то время как полимеры представляют собой большие молекулы с повторяющимися структурными единицами мономеров.Ключевое различие между смолой и полимером заключается в том, что смолы имеют малую молекулярную массу, тогда как полимеры имеют большую молекулярную массу. Кроме того, смола представляет собой вязкую жидкость прозрачного или темно-коричневого цвета, в то время как полимеры могут быть твердыми или жидкими.
Резюме — Смола против полимера
Смола и полимер — это органические материалы. Ключевое различие между смолой и полимером заключается в том, что смолы имеют малую молекулярную массу, тогда как полимеры имеют большую молекулярную массу.
Артикул:
1. Джонсон, Тодд. «Эпоксидная смола.» ThoughtCo, май. 23 января 2019 г., доступно здесь.
Изображение предоставлено:
1. «Résine» (CC BY-SA 3.0) через Commons Wikimedia
2. «1061731» (CC0) через Pixabay